Unionfab’s Affordable SLM Printing [+Cost Calculator]
Explore Unionfab’s SLM success stories across various industries and use our free cost calculator to estimate your 3D printing costs.
Introduction
Selective Laser Melting (SLM) is a powder bed fusion technique that utilizes a laser beam to selectively melt and bond metallic powders, building each layer according to a CAD model. It stands out for its ability to create highly precise and durable metal components that traditional manufacturing techniques can’t.
In this article, we will highlight the advantages of SLM, compare the costs of SLM with other metal part manufacturing methods, and display Unionfab's SLM cases across various fields.
If you're not yet familiar with what SLM is while reading this article, feel free to check out our SLM blog section to quickly get up to speed!
Why Choose Selective Laser Melting?
1. Create Complex Designs Easily
Traditional manufacturing struggles with intricate geometries due to tooling and mold limitations. SLM overcomes this by building parts layer by layer from digital models, enabling complex designs like:
Internal cooling channels
Honeycomb structures
Topology-optimized shapes This technology allows for design freedom, creating more innovative products.
2. Enable Small-batch Production
SLM is ideal for small-batch or customized production where traditional methods are costly or impractical.
Efficient for one-off or low-volume (1-1000) parts
Perfect for prototyping and personalized designs
It minimizes costs while delivering the flexibility needed for unique projects.
3. Save Materials and Costs
Traditional methods, such as CNC machining, waste significant material, especially with expensive metals like titanium. SLM only uses the required powder for each layer, thus
Reducing material waste
Lowering long-term costs
4. Faster Development Without Molds
With SLM, there’s no need for mold design or tooling. Parts are directly printed from CAD models, which:
Shortens development cycles
Allows quick design adjustments
Speeds up responses to market or customer needs
5. High-precise, high-strength and Lightweight Designs
SLM creates high-performance metal parts that meet strict strength and precision demands while enabling lightweight structures through optimized geometries.
Improved efficiency with reduced weight
Enhanced reliability for aerospace and medical applications
6. 7/24 Response via Digital Platform
SLM leverages digital platforms for seamless support:
Upload designs online
Get instant quotes
Track production in real-time
Most traditional methods can’t support online quoting or even need in-person meetings. While this streamlined process is location-independent and hassle-free.
Cost of Common Metal Powder for SLM 3D Printing
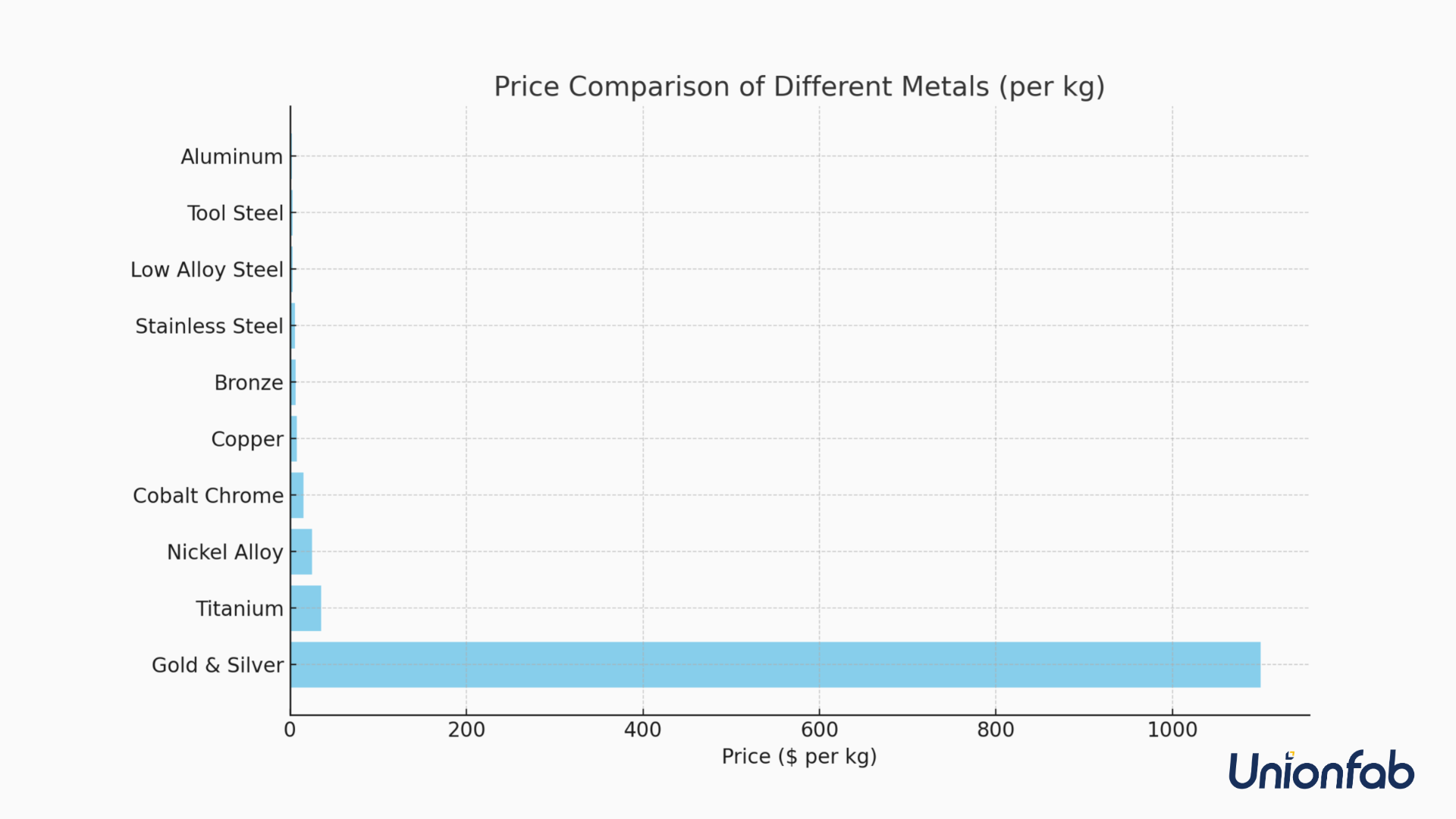
For SLM 3D Printing, materials are usually processed as powder for better precision control, and material efficiency. Here we have compared the common metal powder of SLM 3D Printing in terms of their cost, key characteristics and applications.
Metal Type | Approximate Cost, per kg (ascending) | Key Characteristics | Specific Applications |
---|---|---|---|
|
|
| Aircraft parts (wings, fuselages), car engine components, beverage cans. |
|
| Strong | Bridges, building frames, pipelines, and ship hulls. |
|
|
| Cutting tools, molds for plastic injection, and dies for metal stamping. |
|
|
| Kitchenware, medical instruments, automotive exhaust systems. |
|
|
| Sculptures, marine propellers, and decorative hardware. |
|
| Conductive | Electrical wiring, heat sinks, and plumbing pipes. |
Cobalt Chrome | $10 - $20 | Biocompatible | Dental crowns, hip implants, and turbine blades. |
Nickel Alloy | $15 - $30 | Corrosion-resistant Heat-resistant | Jet engines, chemical processing equipment, and submarine parts. |
|
| High strength-to-weight ratio | Aircraft landing gears, bone implants, and sports equipment (bike frames). |
|
|
| Jewelry, circuit boards, and high-end electronics (smartphones, watches). |
Key Takeaways
If you prioritize cost, metals like aluminum, low alloy steel, and stainless steel provide excellent value for general applications.
If you prioritize performance, premium metals like titanium, nickel alloys, and cobalt chrome deliver advanced properties for specialized uses.
If you're unsure about which material to use for 3D printing, feel free to contact our experts for detailed advice!
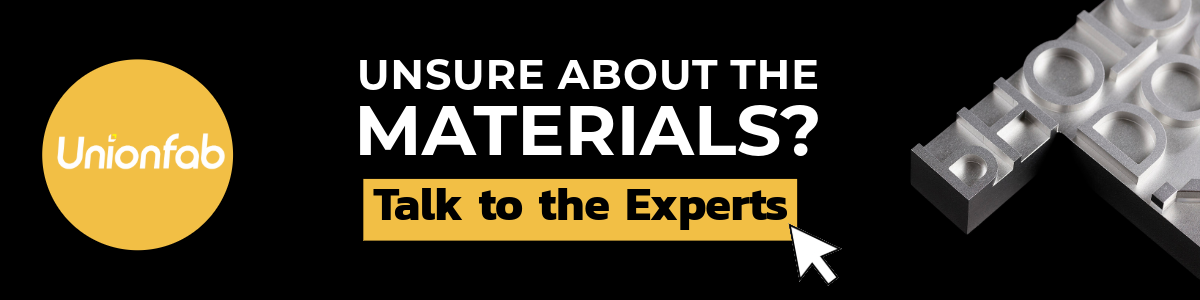
Cost Comparison Between SLM and Other Metal Manufacturing Methods
To help understand the cost dynamics, let’s break down the costs of SLM versus traditional methods (e.g., casting, CNC machining) by key factors:
Manufacturing Method | Initial Setup Cost | Material Efficiency | Small Batch Cost | Design Complexity |
---|---|---|---|---|
Casting | $$$$$ | $$ | $$$$$ | Low |
CNC Machining | $$$ | $$$ | $$$ | Moderate |
SLM 3D Printing | $ | $$$$ | $$ | High |
Initial Setup Costs:
Traditional Methods (e.g., Casting): High tooling and mold costs; best suited for large-scale production.
SLM: No tooling required; lower initial costs for prototyping and small batches.
Material Usage:
Traditional Methods: Material waste can be significant, e.g., chips from CNC machining or excess in molds.
SLM: Powder-based system allows for recycling unused material, making it highly efficient.
Labor Costs:
Traditional Methods: Requires skilled operators for setup, machine operation, and quality checks.
SLM: High automation reduces labor involvement and costs.
Small Batch Costs:
Traditional Methods: High unit costs due to tooling amortization.
SLM: Ideal for small batches as there are no tooling or mold costs.
Key Takeaways
For small batches and complex designs, SLM is more cost-effective.
Traditional methods are more economical for large-scale production and simple geometries.
Unionfab’s Free Cost Calculator
As we’ve mentioned before, 3D printing can support online instant quoting now, which is one of its advantages that set it apart from many traditional manufacturing methods.
So, if you already know which material to choose and have a 3D model ready, try our free instant quoting system to see if 3D printing your product could save you money!
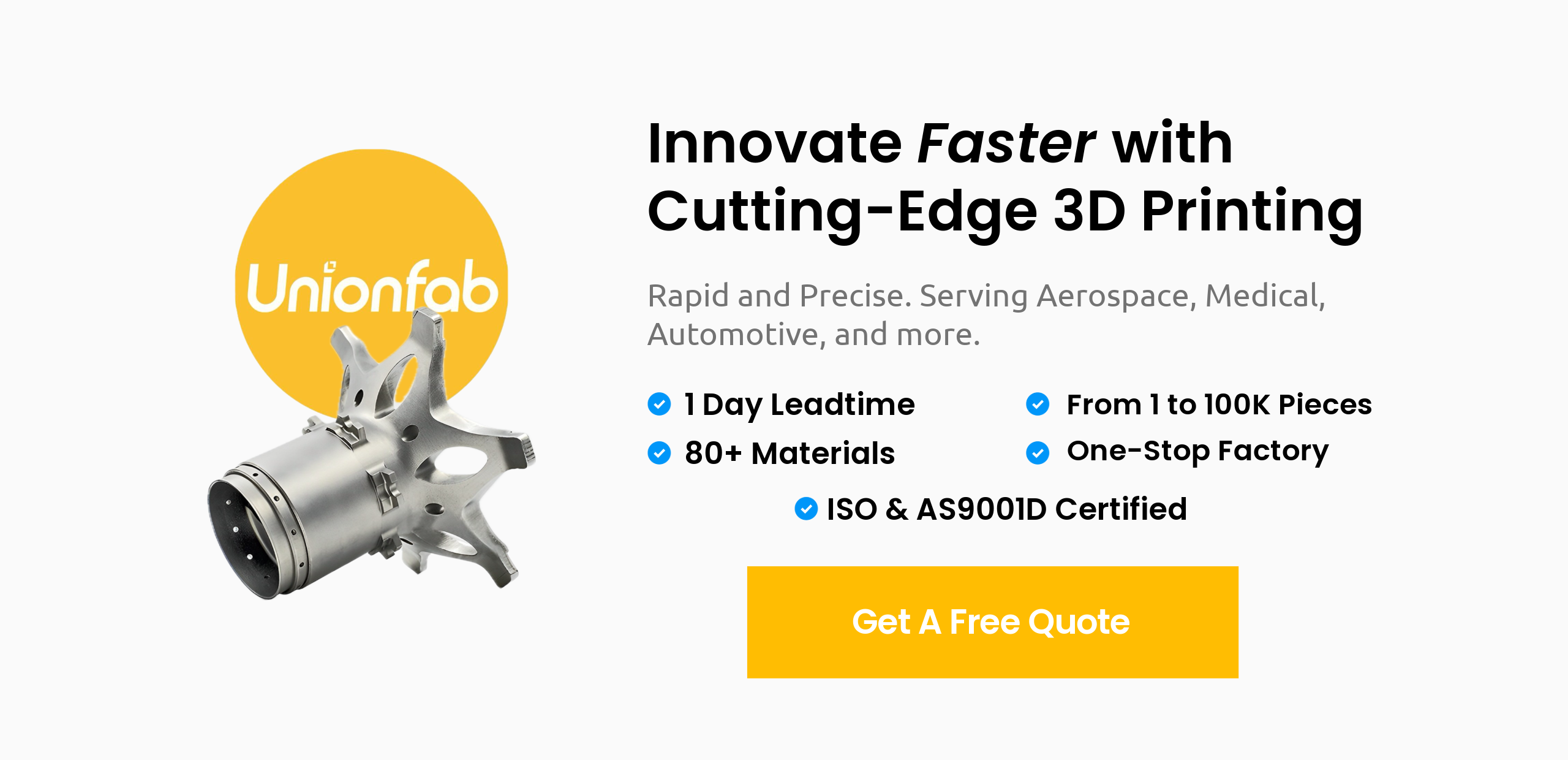
Unionfab’s SLM Service
Certification
At Unionfab, we pride ourselves on delivering high-quality SLM services backed by globally recognized certifications:
ISO 9001: Ensures quality management across all processes.
AS 9001D: Meets the stringent requirements of the aerospace industry.
ISO 13485: Demonstrates our commitment to producing medical-grade components that meet international standards.
These certifications underscore our dedication to precision, reliability, and excellence in every project we undertake.
Equipment
Unionfab boasts state-of-the-art equipment that empowers us to handle diverse and demanding 3D printing needs:
1,000+ advanced 3D printers: A robust infrastructure to manage projects of all sizes and complexities.
Largest build volume: 2100 × 700 × 800 mm: Perfect for producing large-scale components without compromising on quality.
Multi-color 3D printing capabilities: Adds aesthetic and functional versatility to your designs, whether for prototyping or final production.
With our cutting-edge technology, we ensure that our customers enjoy the benefits of faster production cycles, superior quality, and design freedom.
SLM 3D Printed Cases by Unionfab
Automotive: Lightweight SLM Wheel Hub
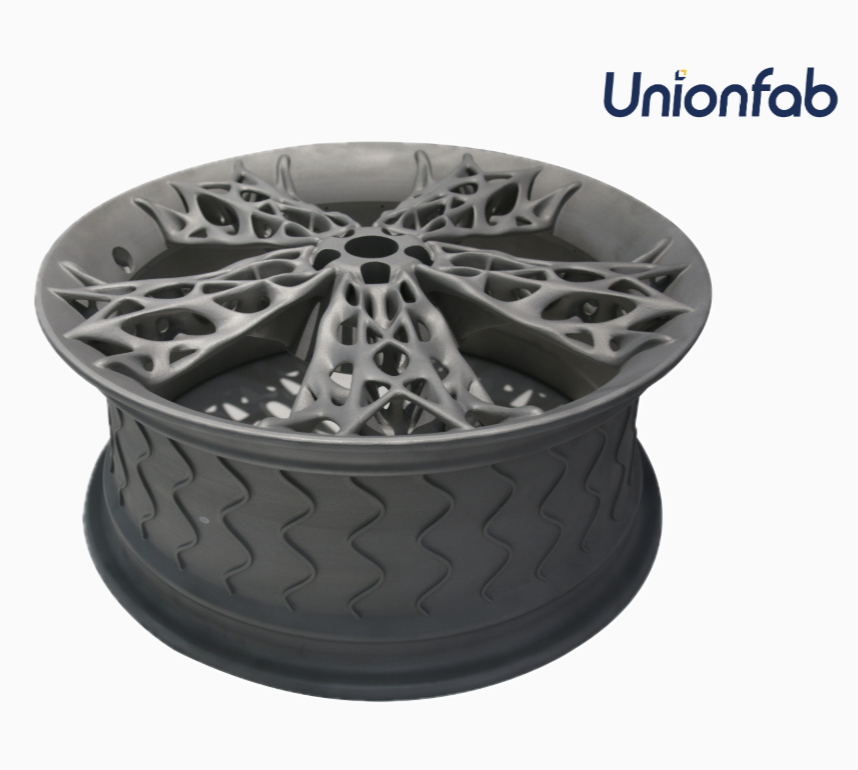
Material: Aluminum alloy for its lightweight and durable properties
Size: 485mm × 210mm
Weight Reduction: Achieved an 8% weight reduction by incorporating Topological Design and Hollow Internal Structure
Design: Colorful SLM Terracotta Warriors
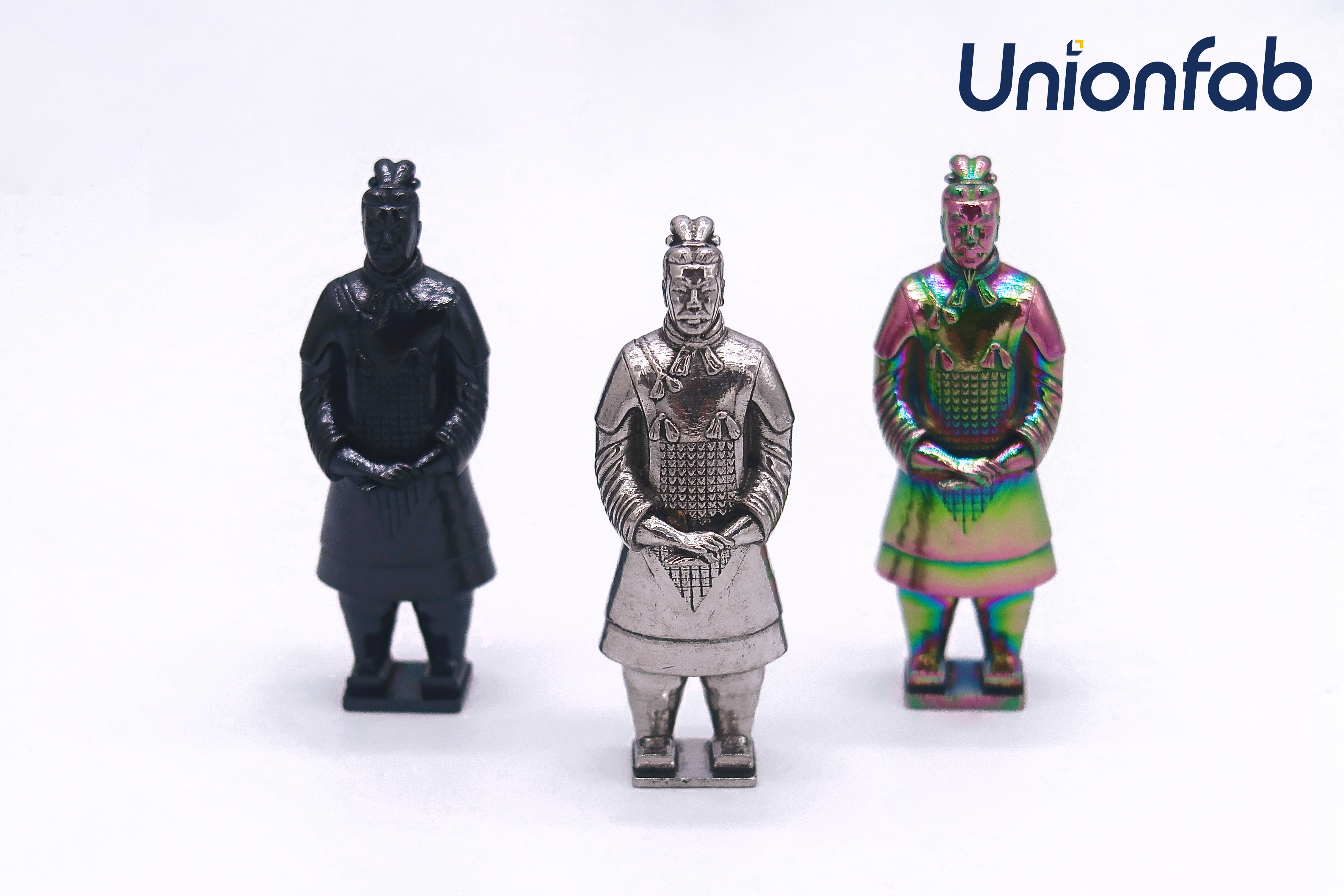
Material: Metal Alloys
Size: Each warrior stands approximately 5cm tall
Post-Processing Techniques:
Black Oxidation: For a classic, aged finish.
Mirror Polishing: To achieve a sleek, reflective surface.
Plating: To add a premium metallic sheen.
Medical: SLM N95 Mask Mold
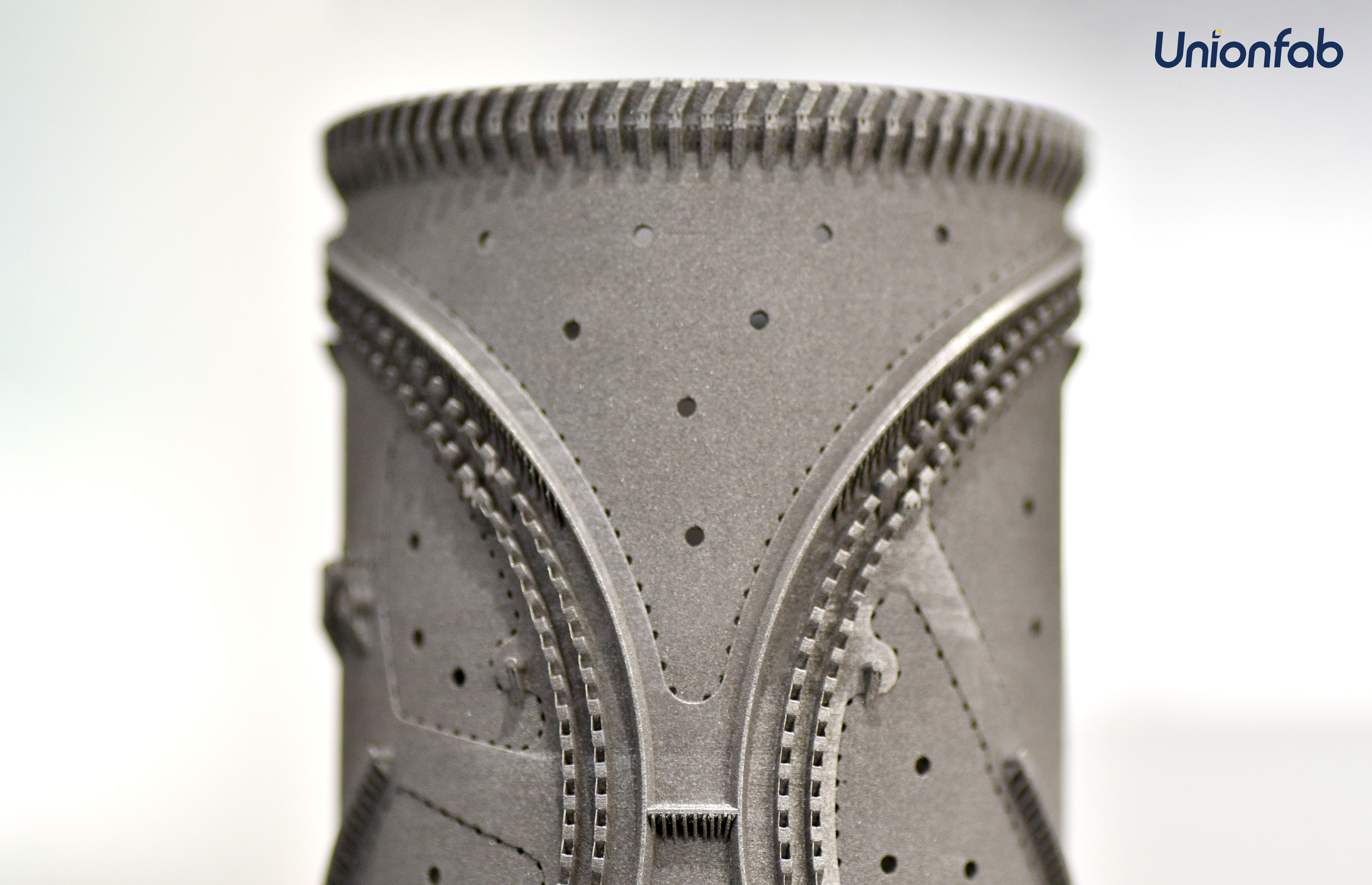
Material: Stainless Steel 316/L for excellent durability
Size: 79mm × 140mm
Machine Time: 15 hours
Turnaround Time: 3 Days
Interested in collaborating with Unionfab and using our 3d printing services ? Sign up to get the 10% off coupon for your first order!
"Editor's note: This post was originally published in November 2022 and has been updated to included more cases by Unionfab."