Yield Strength of Steel: A Comprehensive Guide
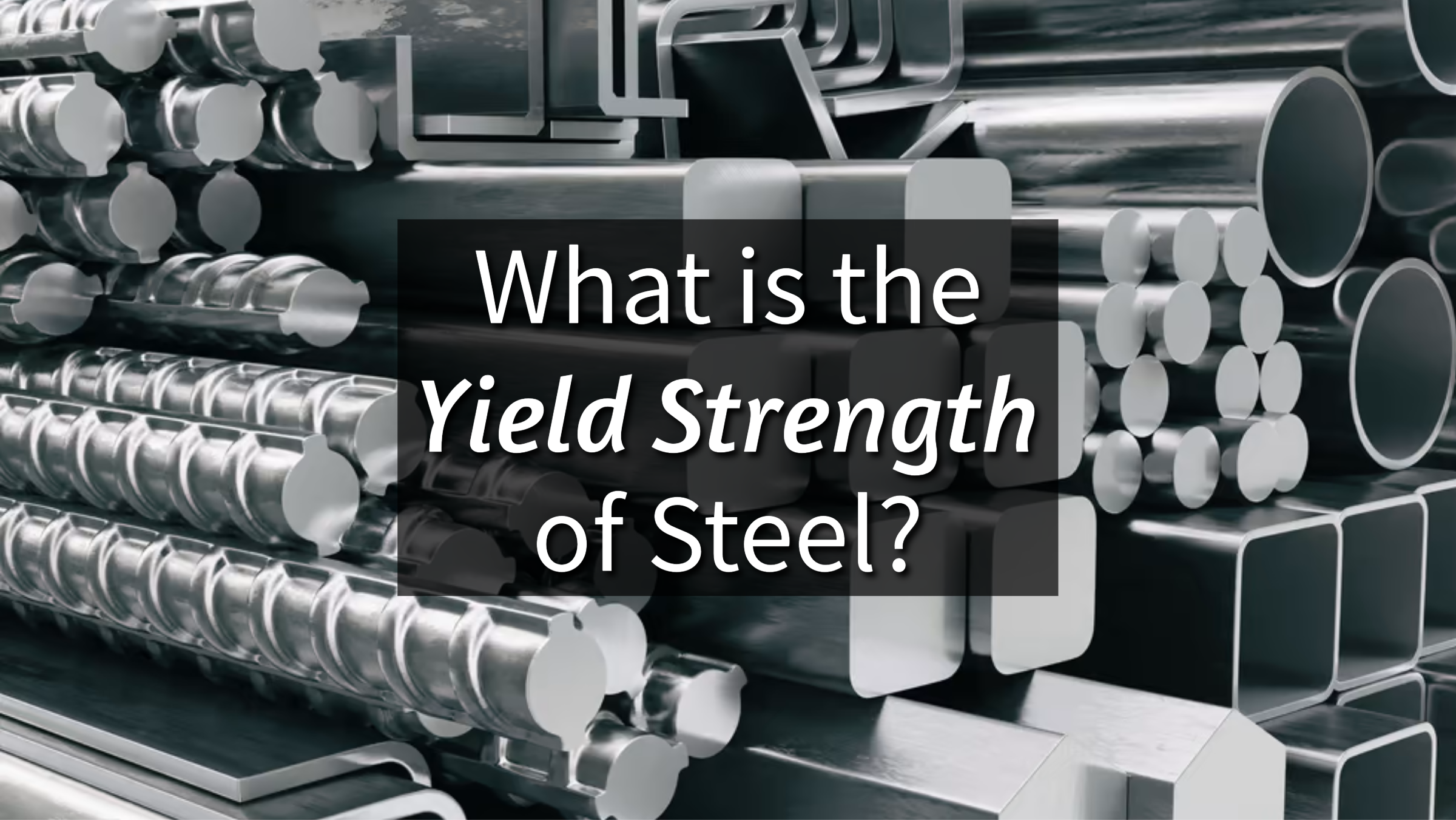
What is the yield strength of steel, and why does it matter? This guide explains what yield strength means and explores the different ranges found in various steel materials.
TL;DR: Head straight to the "Conclusion" section for a comparative table of yield strengths😉
Introduction
Definition of yield strength
Yield strength is used to define a material’s resistance to permanent deformation under stress. It’s the maximum stress a material can withstand before it begins to deform plastically.
In simpler terms, it's the point at which an elastic material (one that springs back after being bent) becomes a plastic material (one that retains the bent shape).
Yield strength is measured in units of force per unit area, commonly expressed in pounds per square inch (psi) or megapascals (MPa).
Yield Strength of Steel
Yield strength for different steel types can ranges from as low as 200 MPa (30,000 psi) for mild steel to over 2000 MPa (290,000 psi) for high-strength alloy steels.
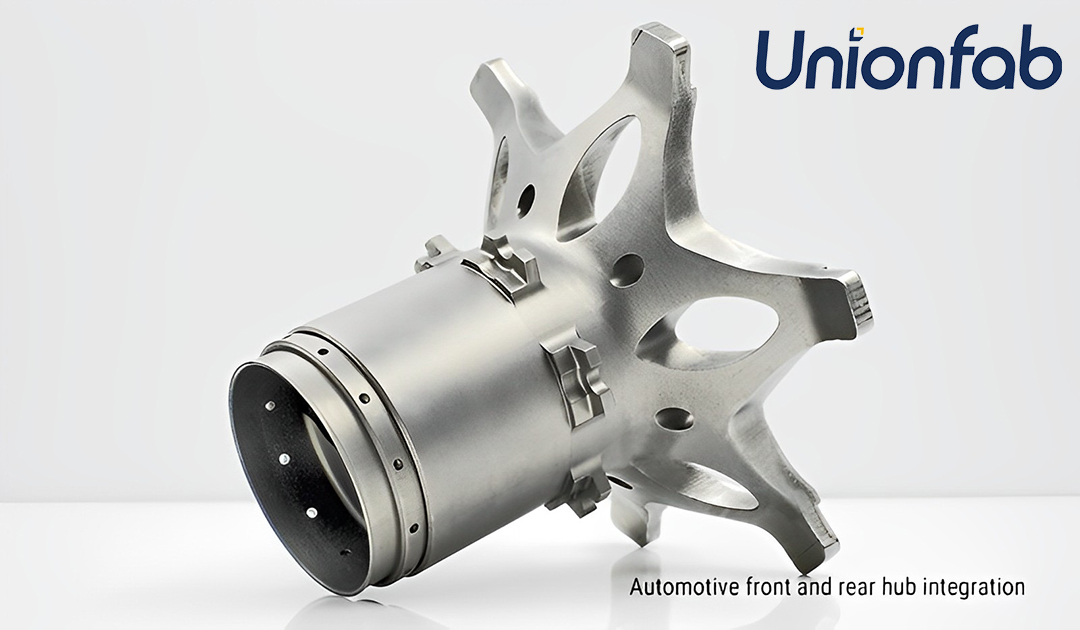
Source: Unionfab
Steel properties vary based on composition and processing. Different formulations and manufacturing methods produce steels with a spectrum of characteristics, including yield strength.
For example, increasing the carbon content raises the yield strength. Additional alloying elements such as manganese can provide further enhancements.
Yield Strength of Different Steel Types
The yield strength of steels varies greatly from around 200 MPa to over 2000 MPa.
Mild steel demonstrates lower yield, while high-strength versions exhibit significantly higher stresses before deformation.
Yield Strength of Stainless Steel
Stainless steels are known for their excellent corrosion resistance, but their yield strength also varies depending on the specific type:
Austenitic Stainless Steels like Stainless Steels 304 and 316 offer good corrosion resistance but have a moderate yield strength, typically around 200-300 MPa (30,000-45,000 psi).
Martensitic Stainless Steels like Stainless Steels 410 prioritize strength and hardness, achieving yield strengths in the range of 400-600 MPa (60,000-90,000 psi). However, their corrosion resistance is lower than austenitic types.
Duplex Stainless Steels combine the corrosion resistance of austenitic steels with the higher yield strength of martensitic steels, typically reaching 500-700 MPa (70,000-100,000 psi).
Yield Strength of Carbon Steel
Yield Strength of Mild Steel (Low-Carbon Steel)
Mild steel, also known as low-carbon steel, is widely used due to its affordability, good formability (ease of shaping), and weldability. However, its yield strength is relatively low, typically around 200-300 MPa (30,000-45,000 psi).
Applications of mild steel often prioritize formability and cost-effectiveness over high strength. Examples include:
Building structures (non-load-bearing components)
Automotive body repair
Ductwork
Pipes
Mild steel is also often used in general fabrication, such as in frames, brackets, and supports, where moderate strength and good weldability are required.
Medium Carbon Steel (e.g., AISI 1045)
Yield Strength: Around 350-450 MPa (50,000-65,000 psi).
Used for applications like shafts, gears, and axles where higher strength is needed.
High Carbon Steel (e.g., AISI 1095)
Yield Strength: Around 600-700 MPa (87,000-102,000 psi).
Typically used in cutting tools, springs, and high-strength wire.
Very High Carbon Steel
Yield Strength: Can exceed 700 MPa (102,000 psi).
Used in specialized applications like knives, springs, and high-strength cables.
Maximum Yield Strength of Steel
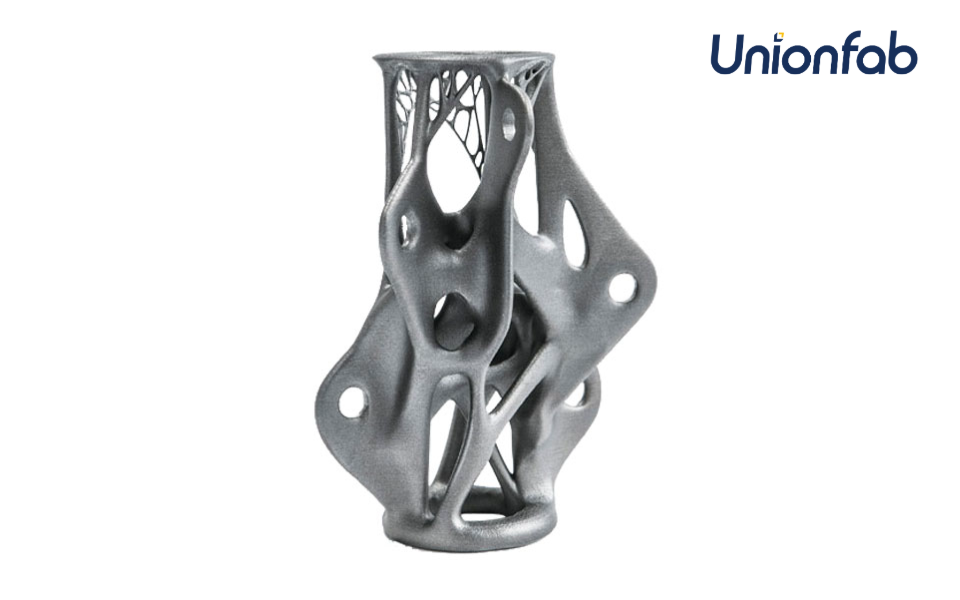
Source: Unionfab
While there’s no single “maximum” yield strength for steel, some alloy steels can achieve remarkably high values:
Maraging Steels: These steels are known for their very high yield strength, often exceeding 2000 MPa. They are used in applications like aerospace components and tooling.
Ultra-High-Strength Steels (UHSS): These include steels like martensitic steel and dual-phase (DP) steel, which can have yield strengths above 2000 MPa. They are often used in automotive and defense applications.
Tool Steel: Tool steels exhibit a broad range of yield strengths, typically from 500 MPa to over 2,000 MPa, depending on their type and treatment. For example, general-purpose tool steels like O1 may have yield strengths around 500 to 1,200 MPa, while high-performance steels like H13 Tool Steel and M2 High-Speed Steel can reach 1,300 to 2,200 MPa.
However, steels with the highest yield strengths are often more expensive and require specialized fabrication techniques.
Stress-Strain Curve and Yield Strength
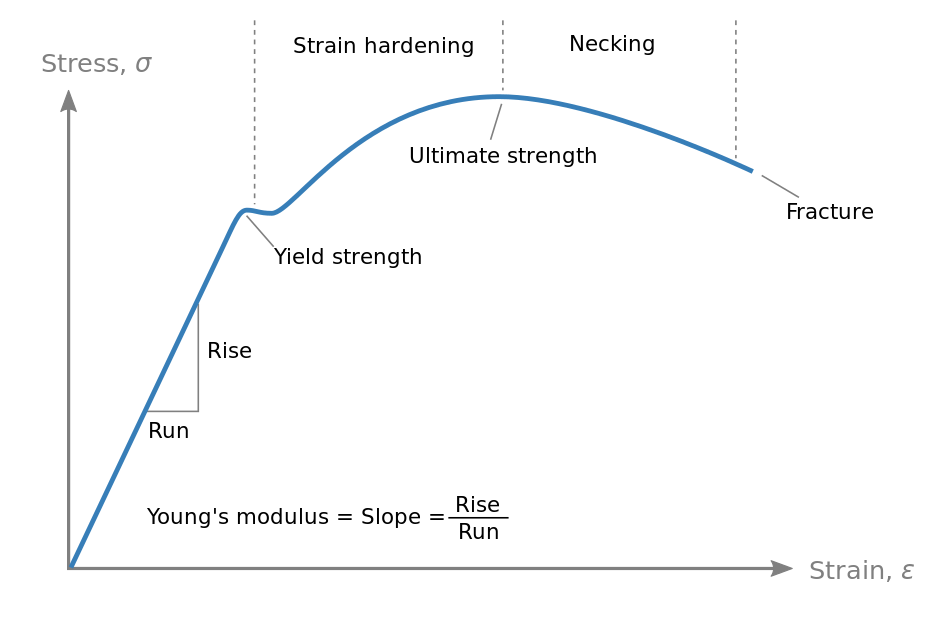
Source: Wikipedia
Imagine bending a metal spoon. Up to the yield strength, the spoon will bend but spring back to its original shape once you release. However, if you bend it past the yield strength, the spoon will stay bent permanently.
The stress-strain curve is a valuable tool for understanding yield strength. Here's how they relate:
The curve starts with a linear region where stress is proportional to strain (deformation). This region represents elastic behavior.
At the yield point, the curve deviates from linearity. This signifies the onset of plastic deformation. The stress required to reach this point is the yield strength.
Beyond the yield point, the material enters the plastic deformation zone. Here, the amount of deformation increases significantly with relatively small increases in stress.
Essentially, the higher the yield strength, the greater the stress a material can endure before it starts to deform permanently.
Importance of Yield Strength in Material Selection
Yield strength is critical when choosing a material for an application:
Structural Integrity: In structures like bridges or buildings, materials need to withstand specific loads without permanent deformation.
Safety: Yield strength plays a vital role in safety-critical components. For example, car parts like frames and axles experience significant stress during operation.
Performance: Depending on the application, a material might need to maintain its original shape under stress. For instance, a machine tool needs to resist deformation to ensure precise operation.
By understanding yield strength, engineers and designers can select materials that are:
Strong enough to handle the anticipated loads without permanent deformation.
Safe for the intended application.
Able to perform their function effectively.
Tensile vs. Compressive Yield Strength of Steel
In this guide, the terms “yield strength” refers to “tensile yield strength” rather than "compressive yield strength".
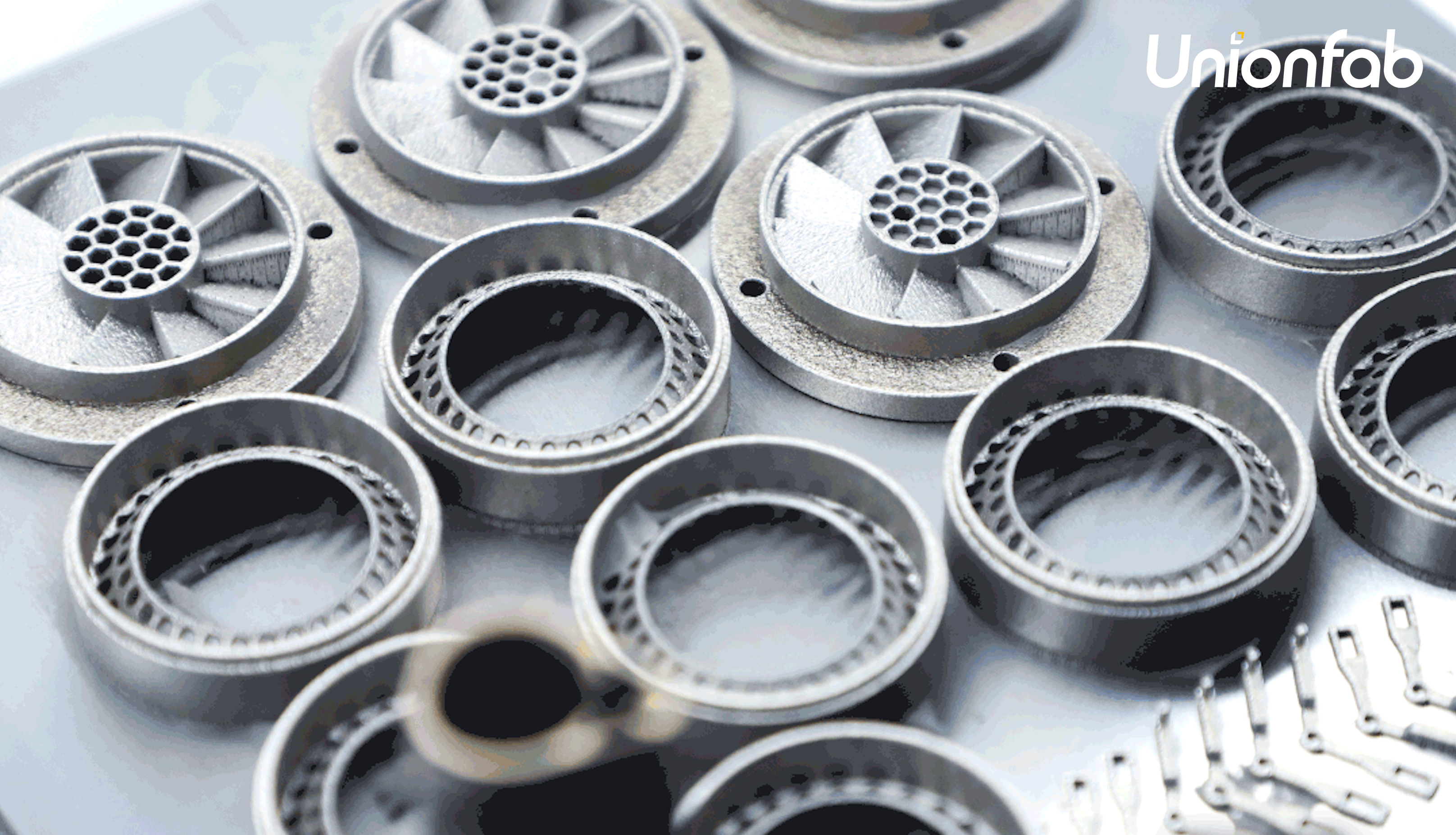
Source: Unionfab
Why the Difference?
Steel, like many materials, can withstand higher stresses in compression before yielding than in tension. This is due to the different ways materials fail under tension (where they are pulled apart) versus compression (where they are squeezed together).
Tensile Yield Strength of Steel
Refers to the stress at which a material begins to deform plastically under tension.
For M2, this is typically around 2,200 MPa.
Compressive Yield Strength of Steel
Refers to the stress at which a material begins to deform plastically under compression. Materials often exhibit higher yield strengths under compression than in tension.
For M2, this is typically around 3250 MPa (471,000 psi) when tempered at 300°F (149°C).
Factors Influencing Yield Strength
Several factors play a crucial role in determining the yield strength of steel:
Alloy Composition
Carbon Content: As mentioned before, higher carbon content strengthens steel. Carbon atoms act like roadblocks within the steel’s crystal structure, making it harder for the material to deform.
Alloying Elements: Adding elements like manganese, chromium, nickel, or molybdenum can significantly enhance yield strength. Each element brings its own strengthening mechanisms:
Manganese: Refines grain size and improves hardenability.
Chromium: Increases strength and corrosion resistance.
Nickel: Enhances strength and toughness, especially at lower temperatures.
Molybdenum: Improves high-temperature strength.
Additionally, finer grain sizes generally lead to higher strength.
Heat Treatment and its Impact on Yield Strength
Heat treatment processes can dramatically alter the microstructure and, consequently, the yield strength of steel. Here are two key techniques:
Quenching: Rapidly cooling the steel from a high temperature traps a metastable microstructure called martensite. Martensite is very hard and brittle, leading to a significant increase in yield strength. However, it can also be quite brittle.
Tempering: Reheating quenched steel to a lower temperature helps to relieve some of the internal stresses introduced by quenching and improve toughness without sacrificing too much strength. The specific tempering temperature determines the final balance between strength and toughness.
Conclusion
Understanding yield strength empowers engineers to create reliable, safe, and efficient designs across various engineering applications. The yield strength of steel varies depending on the type:
Carbon Steel: Yield strength increases with carbon content.
Alloy Steel: Alloying elements further enhance strength.
Tool Steel: Prioritizes high hardness and wear resistance.
Stainless Steel: Yield strength varies based on the specific type (austenitic, martensitic, duplex).
Steel Type | Carbon Content | Alloying Elements | Heat Treatment | Yield Strength Level | Yield Strength (MPa) |
---|---|---|---|---|---|
Mild Steel (Low Carbon Steel) | Low | None | Low | Weak | [200, 350] |
Medium Carbon Steel | Medium | None | Medium | Medium | [350, 450] |
High Carbon Steel | High | None | Medium to High | Strong | [600, 700] |
Stainless Steel | Low | Chromium (Cr), Nickel (Ni), Molybdenum (Mo) (depending on type) | Medium | Medium | [200, 700] |
Tool Steel | High | Chromium (Cr), Tungsten (W), Vanadium (V), Molybdenum (Mo), etc. | High | Strong | [500, 2200] |
Maraging Steel | Very Low | Nickel (Ni), Cobalt (Co), Molybdenum (Mo), Titanium (Ti), etc. | Very High | Extremely Strong | [1400, 2400] |
Unlock Your Manufacturing Potential at Unionfab
Whether you need high-performance metal that can withstand rigorous conditions, or ultra-fine resins for complex designs with intricate details, Unionfab's vast materials library allows you to bring any project to life.
Unleash creativity and innovate with speed and precision by working with Unionfab. We have the solution.
Get an Instant Quote
Use our online tool to get an Instant quote for your 3D printing or CNC project. Our team will review the details and follow up with a personalized proposal tailored to your needs.
Contact Us
If you'd prefer to discuss your needs with a Unionfab expert, contact us to connect with a representative. We're committed to delivering high-quality, cost-effective manufacturing support to help bring your ideas to life.