Titanium vs. Aluminum: Which is Best for You?
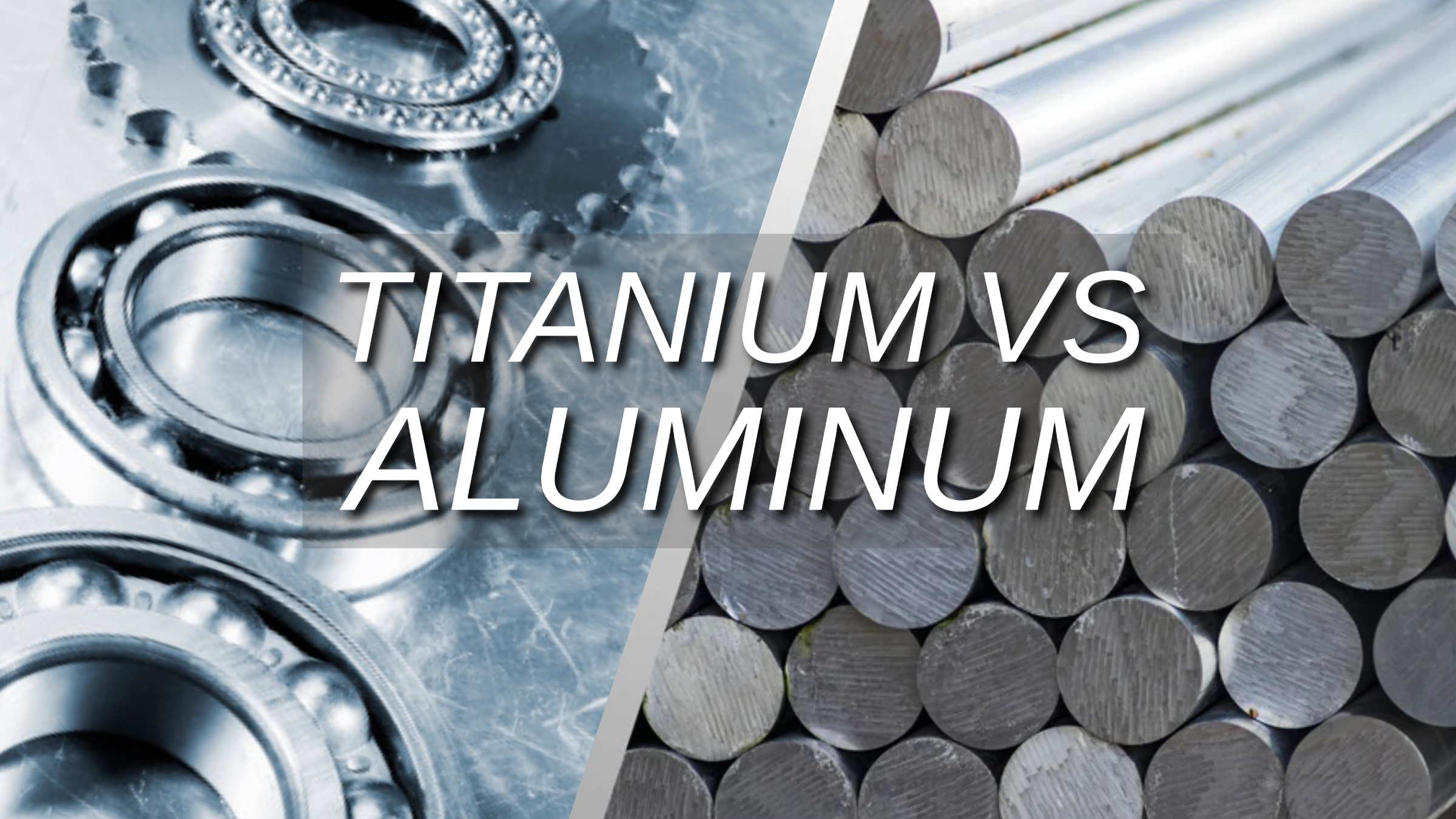
This article compares the pros and cons of titanium and aluminum, to help select the best material for industrial projects.
Introduction
The lightweight metals titanium and aluminum are famous for their strength-to-weight ratios, making them suitable for applications requiring a lightweight design.
However, beneath their comparable densities lies an opposition in their properties - titanium possesses remarkable strength and resistance to corrosion, whereas aluminum offers affordability and simplicity of use. Selecting one over the other depends on project requirements.
Titanium vs. Aluminum: Composition and Properties
Both titanium and aluminum are popular choices for applications requiring a lightweight yet strong material. However, their internal makeup and resulting properties differ significantly.
Chemical Composition:
Titanium: A pure element (Ti) on the periodic table. It's naturally occurring but rarely found in its pure form. Typically, it's extracted from minerals like ilmenite (FeTiO3) and rutile (TiO2).
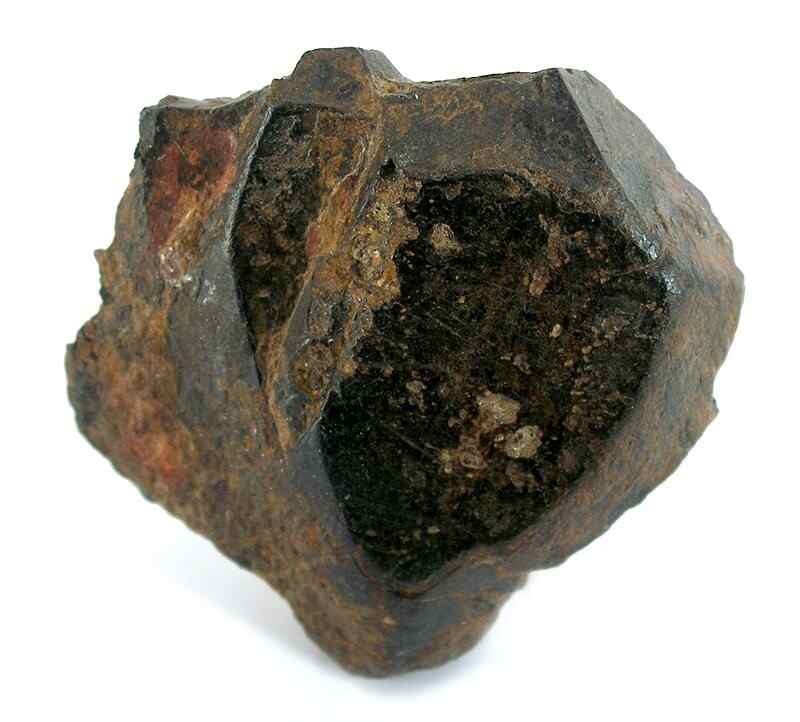
Source: wikipedia.org
Aluminum: Another element (Al), also not readily available in its pure state. It's extracted from bauxite ore (Al2O3) and then alloyed with other elements like copper, magnesium, or silicon to enhance its properties.
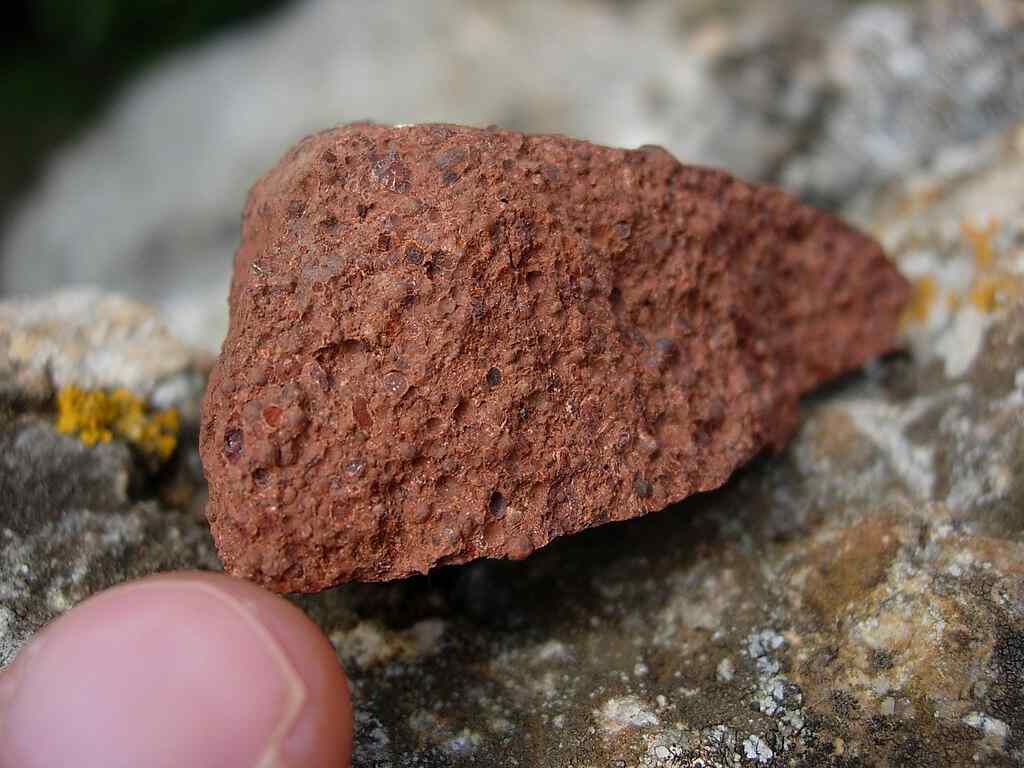
Source: wikipedia.org
Physical Properties:
Density Both titanium and aluminum have lower densities than steel, making them attractive alternatives. However, titanium is denser (around 4.5 g/cm³) than aluminum (around 2.7 g/cm³).
Strength Despite the lower density, aluminum can achieve impressive strength levels through alloying. However, titanium is unmatched in pure, unadulterated strength. Titanium alloys boast even higher strength-to-weight ratios, making them ideal for applications demanding high strength without excessive weight.
Corrosion Resistance Titanium forms a passive oxide layer (TiO2) that shields it from corrosion, even in harsh saltwater environments. Aluminum also forms an oxide layer (Al2O3), but it's not as robust. In salty or highly acidic conditions, aluminum can corrode.
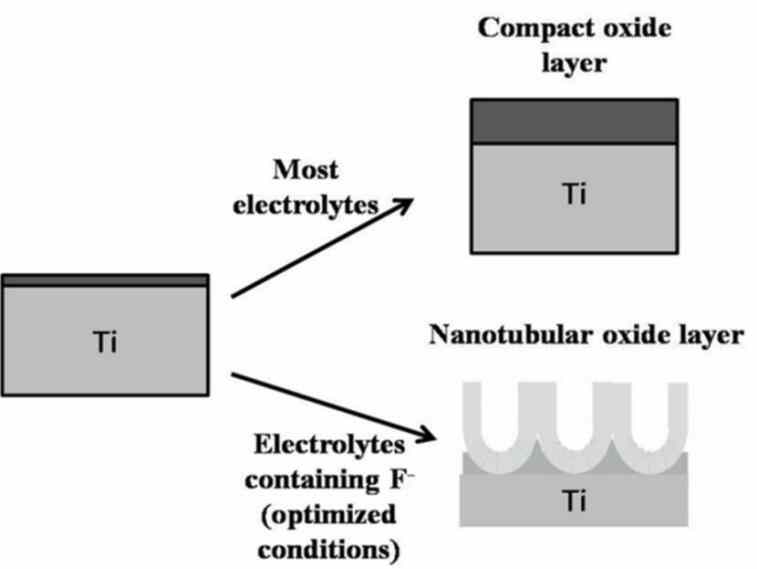
Source: researchgate.net
Machinability Titanium's superior strength comes at a cost – it's tougher to machine. Aluminum's softer nature makes it easier to shape and fabricate.
Melting Point Titanium melts at a much higher temperature (around 1668°C) compared to aluminum (around 660°C). This makes titanium suitable for applications exposed to extreme heat.
Cost Due to its abundance and ease of processing, aluminum is significantly cheaper than titanium. Titanium's extraction and processing are complex, leading to a higher price tag.
Titanium vs. Aluminum: Strength
When it comes to strength, both titanium and aluminum hold their own, but their capabilities differ in specific areas.
Property | Titanium | Aluminum |
---|---|---|
Tensile Strength | 230 MPa - 1400 MPa | 90 MPa - 690 MPa |
Flexibility | Low | High |
Ductility | Low | High |
Impact Resistance | Varies by alloy | Can be surprisingly high for weight (alloy dependent) |
Fatigue Strength | Generally superior, especially at high temperatures | Good |
Titanium vs. Aluminum: Pros and Cons
When choosing between titanium and aluminum, it's crucial to understand the advantages and disadvantages of each metal.
Titanium's Pros:
Unmatched Strength Boasts superior tensile strength, making it ideal for applications demanding high loads without excessive weight (e.g., aerospace components, bicycle frames).
Exceptional Corrosion Resistance Forms a protective oxide layer that shields it from rust and degradation, even in harsh environments like saltwater (e.g., marine equipment, medical implants).
High-Temperature PerformanceWithstands extreme heat due to its high melting point, making it suitable for applications exposed to intense temperatures (e.g., jet engine components, high-performance brakes).
Biocompatible Non-toxic and readily accepted by the human body, making it ideal for medical implants (e.g., artificial joints, bone screws).
Low Maintenance Requires minimal upkeep due to its exceptional corrosion resistance.
Titanium's Cons:
High Cost: Extraction and processing are complex, leading to a significantly higher price tag compared to aluminum.
Difficult to Machine: Its rigidity makes it challenging and time-consuming to shape and fabricate.
Heavy Compared to Aluminum: While still lightweight compared to steel, it's denser than aluminum, adding weight to the final product.
Brittle Under Certain Conditions: Can be prone to cracking under extreme bending or impact, depending on the specific alloy.
Aluminum's Pros:
Affordable: Abundant and readily available, making it a cost-effective choice for various applications.
Lightweight: One of the lightest structural metals, ideal for situations where weight reduction is crucial (e.g., aircraft parts, beverage cans).
Good Strength-to-Weight Ratio: Through alloying, aluminum can achieve impressive strength levels while remaining lightweight.
Machinable: Its softer nature makes it easier to shape and fabricate compared to titanium.
Recyclable: A significant portion of aluminum is recycled, making it an environmentally friendly option.
Aluminum's Cons:
Lower Strength: Compared to titanium, aluminum offers lower tensile strength, limiting its use in high-load applications.
Susceptible to Corrosion: While it forms an oxide layer, it's not as robust as titanium's. Aluminum can corrode in salty or highly acidic environments.
Lower Melting Point: Melts at a significantly lower temperature than titanium, making it unsuitable for applications exposed to extreme heat.
Not Biocompatible: Not readily accepted by the human body, limiting its use in medical implants.
Property | Titanium | Aluminum |
---|---|---|
Strength | Unmatched | Lower |
Cost | High | Affordable |
Corrosion Resistance | Exceptional | Susceptible |
Weight | Heavy Compared to Aluminum | Lightweight |
Machinability | Difficult | Machinable |
High-Temperature Performance | High | Lower Melting Point |
Biocompatible | Yes | No |
Recyclable | No | Yes |
Titanium vs. Aluminum: Applications
The unique properties of titanium and aluminum make them suitable for a wide range of applications.
Aerospace Industry
Titanium: Its exceptional strength-to-weight ratio, high-temperature resistance, and corrosion resilience make it a go-to material for aircraft parts (e.g., landing gear, engine components) where weight reduction and durability are crucial.
Aluminum: While not as strong as titanium, some high-strength aluminum alloys find use in non-critical aircraft parts (e.g., fuselage panels, wing components) due to their affordability and lightweight nature.
Automotive Sector
Titanium: Primarily used in high-performance vehicles due to its cost. However, its strength and weight reduction benefits can be seen in components like connecting rods, exhaust systems, and some luxury car body panels.
Aluminum: The metal of choice for most car bodies due to its affordability, lightweight properties, and good formability. Alloys with varying strengths are used depending on the specific component (e.g., engine blocks, wheels).
Medical Applications
Titanium: Due to its biocompatibility and exceptional corrosion resistance, it's widely used for medical implants like artificial joints, bone screws, and dental implants.
Aluminum: Limited use in medical applications due to biocompatibility concerns. However, some sterilized aluminum alloys can be found in specific medical equipment housings.
Consumer Electronics
Titanium: Primarily seen in high-end electronics like premium laptops or smartphone frames due to its sleek aesthetics, strength, and scratch resistance. However, the cost is a significant factor.
Aluminum: The dominant material for most consumer electronics (e.g., laptops, smartphones) due to its affordability, lightweight nature, and good heat dissipation properties.
Titanium vs. Aluminum iPhone
Apple recently introduced the iPhone 15 with a titanium frame, a shift from the traditional aluminum body used in previous models.
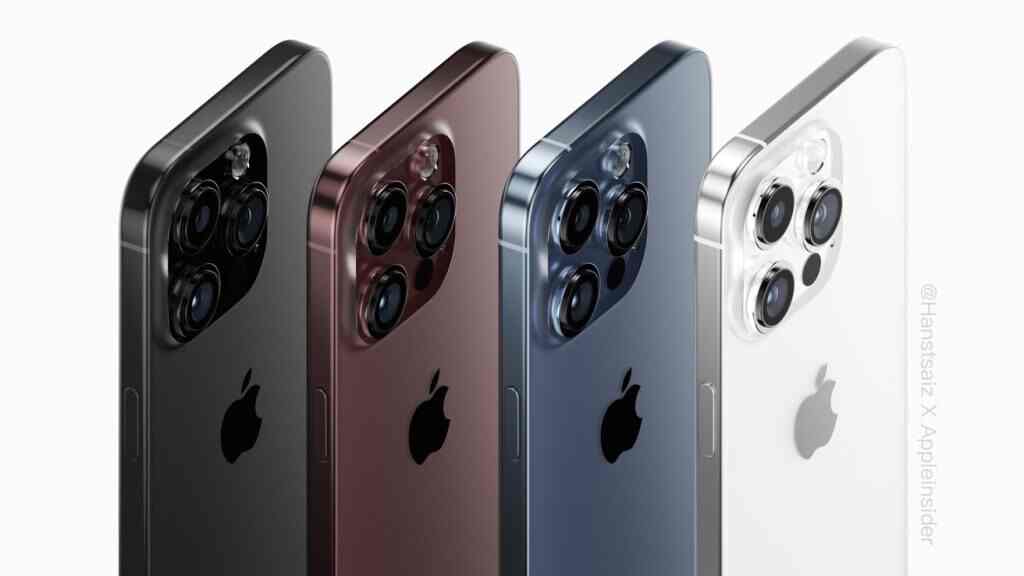
Source: appleinsider.com
Pros of Titanium iPhone:
Lighter than stainless steel frames used in some Pro models.
More scratch-resistant than aluminum.
May offer a more premium feel.
Cons of Titanium iPhone:
Likely more expensive than aluminum models.
May be slightly heavier than aluminum.
Not as strong as stainless steel in terms of impact resistance.
Titanium vs. Aluminum: Choosing the Right Material
Choosing between titanium and aluminum requires careful consideration of several factors.
Performance Requirements
Strength
If application demands the absolute highest tensile strength, titanium is better. However, for moderate strength needs, some aluminum alloys might suffice.
Weight
If minimizing weight is paramount, aluminum wins due to its lower density. However, titanium's high strength-to-weight ratio can be advantageous in situations where weight reduction needs to be balanced with some degree of strength.
Corrosion Resistance
For applications exposed to harsh environments like saltwater or acidic conditions, titanium's exceptional corrosion resistance is unmatched. Aluminum can corrode in such environments.
High-Temperature Performance
If application encounters extreme heat, titanium's high melting point makes it a better choice than aluminum, which melts at a significantly lower temperature.
Biocompatibility
When human body compatibility is crucial (e.g., medical implants), titanium's biocompatible nature is essential. Aluminum is generally not suitable for such applications.
Material Availability and Sourcing
Titanium
Less readily available than aluminum, and its extraction and processing are complex. This can lead to longer lead times and higher costs.
Aluminum
Abundantly available and easily sourced, making it a more readily obtainable material.
Longevity and Maintenance
Titanium
Exceptionally corrosion-resistant, requiring minimal maintenance over its lifespan.
Aluminum
Susceptible to corrosion in harsh environments, potentially requiring more frequent maintenance or replacement.
Cost
Titanium
Significantly more expensive than aluminum due to its scarcity and complex processing.
Aluminum
A cost-effective material, making it a budget-friendly choice for many applications.
Environmental Impact
Titanium
Extraction and processing can be energy-intensive, leading to a higher environmental footprint.
Aluminum
More readily recycled, making it a more environmentally friendly option compared to virgin titanium.
Conclusion
Titanium offers unmatched strength and corrosion resistance, ideal for demanding applications like aerospace and medical implants, but it's expensive.
Aluminum is the affordable and lightweight choice for electronics and car parts, but trades strength and corrosion resistance for budget-friendliness.
In the end, the champion depends on your needs: ultimate performance (titanium) or affordability and weight savings (aluminum).
We Know Materials at Unionfab
From 3D printing to traditional techniques, Unionfab puts the power of creation in your hands.
Choose from our extensive range of high-quality materials, including Aluminum (Alsi10Mg) and Titanium (TC4), to perfectly match your design vision.
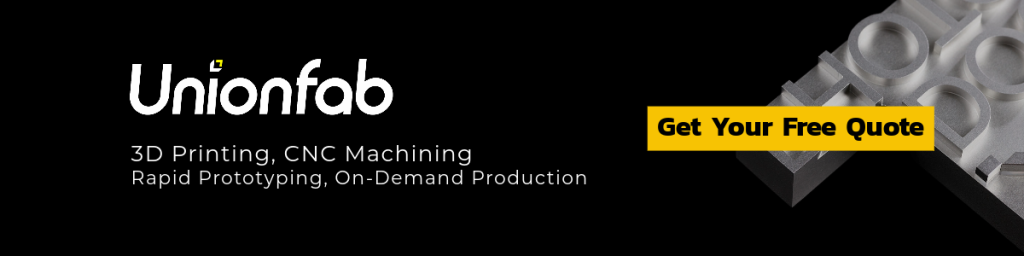