The Essential Guide to CNC Fixtures
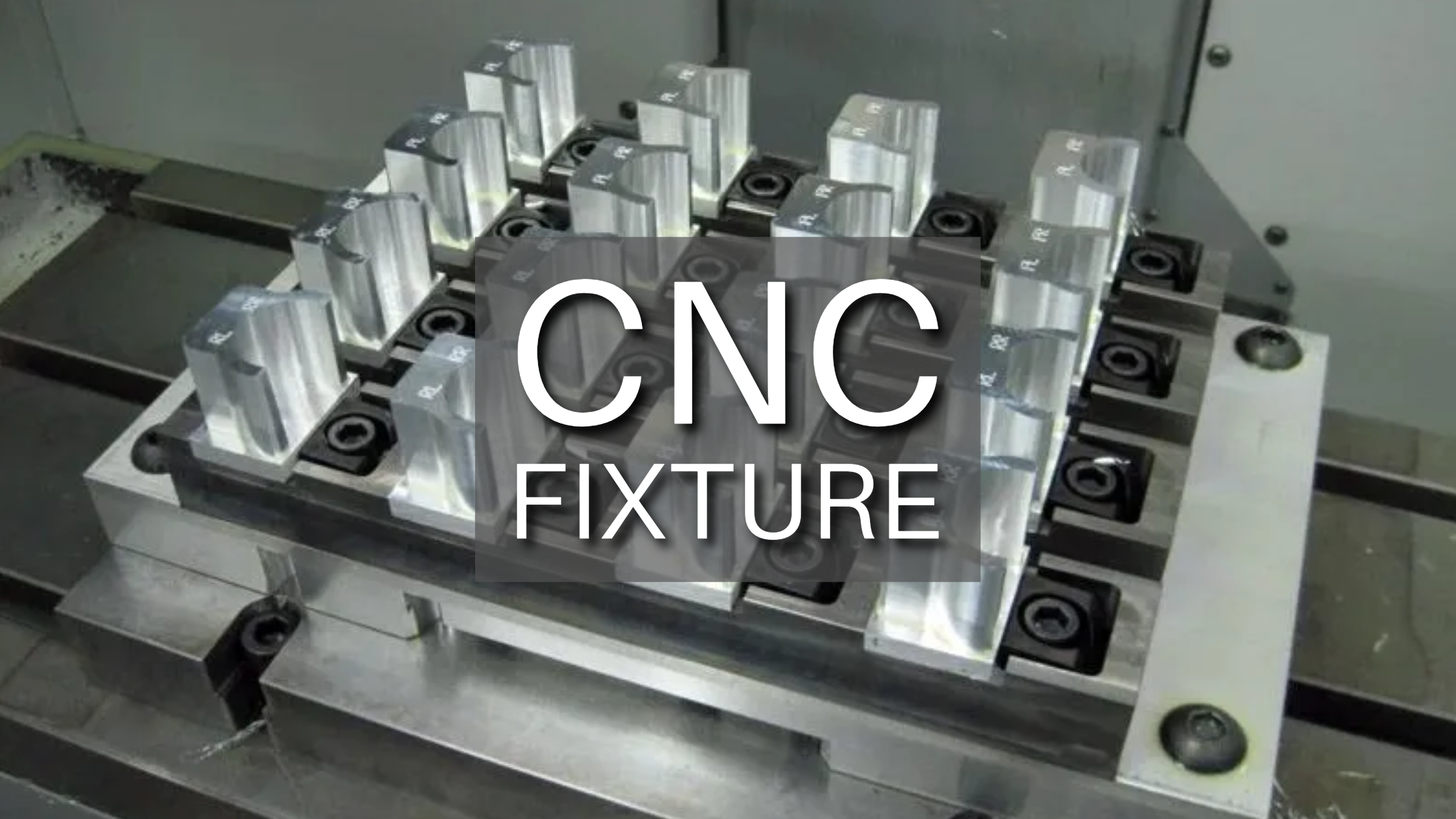
This comprehensive guide explores CNC fixtures, offering insights into their definition, types, mechanism and role in manufacturing processes.
Introduction
Computer Numerical Control (CNC) fixtures are crucial tools in the manufacturing industry, providing support and precision for machining operations.
They enhance efficiency, accuracy, and safety, making them indispensable in various sectors.
Fundamentals of CNC Fixture
Purpose and Functionality
- Ensuring Accurate Positioning: Fixtures provide a stable location, achieving high precision in operations. For instance, in the automotive industry, they ensure accurate drilling and milling of engine blocks.
- Enhancing Operational Efficiency: Streamlined setups minimize alignment time, leading to increased productivity. Dedicated fixtures are known to significantly reduce setup times, resulting in notable efficiency improvements.
- Enhancing Repeatability and Precision: Consistent use of fixtures ensures parts are machined to the same specifications, minimizing variations. In aerospace, fixtures maintain tolerances within microns for critical components like turbine blades.
Key Components
- Base Plate: Provides a stable foundation and attaches to the CNC machine table, ensuring the fixture stays in place during machining.
- Clamps and Hold-Downs: Secure the workpiece to prevent movement. These can be mechanical, hydraulic, or pneumatic, crucial for maintaining machining integrity. In medical device manufacturing, precise clamping ensures exact specifications for surgical instruments.
- Locating and Positioning Elements: Ensure precise alignment of the workpiece. Elements like pins and bushings guide the workpiece into position, ensuring accuracy. In aerospace, they help achieve the required precision for complex components like turbine blades.
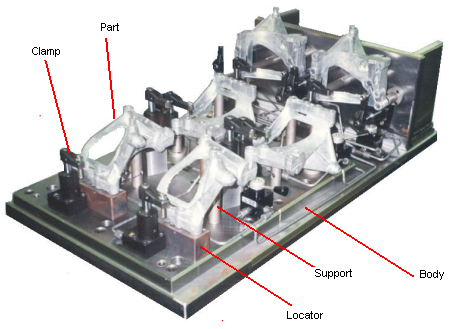
Source: cnctimes.com
Types of CNC Fixture
Modular Fixtures
- Flexibility: Easily adaptable for different workpieces, suitable for small batches and prototyping.
- Quick Adjustments: Allows for rapid reconfiguration to accommodate new part designs, minimizing downtime.
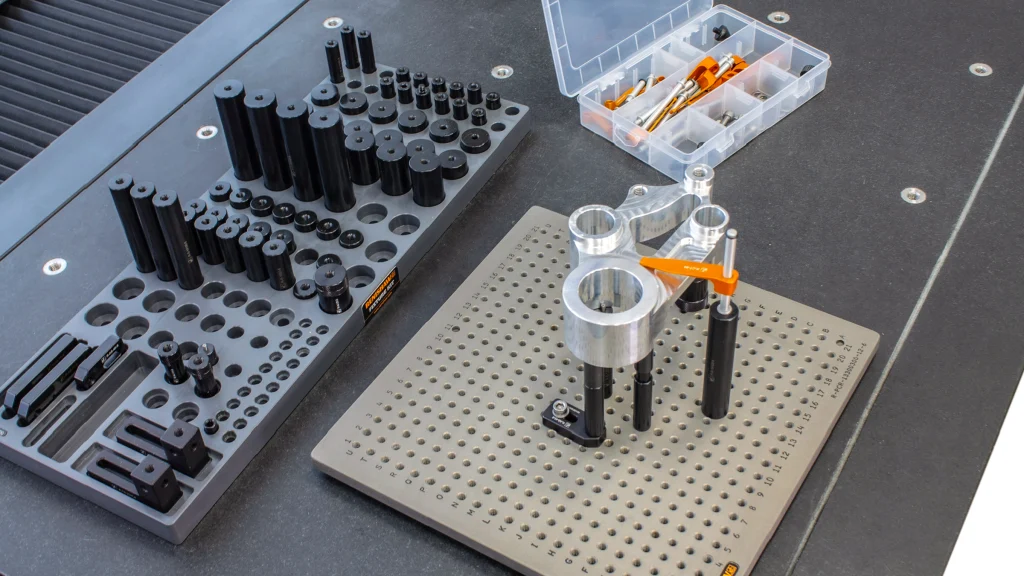
Source: metrology.news
Dedicated Fixtures
- Precision and Efficiency: Customized for specific parts or operations, offering high precision and efficiency.
- Application Examples: Commonly used in automotive machining for tasks such as engine block machining, improving throughput significantly.
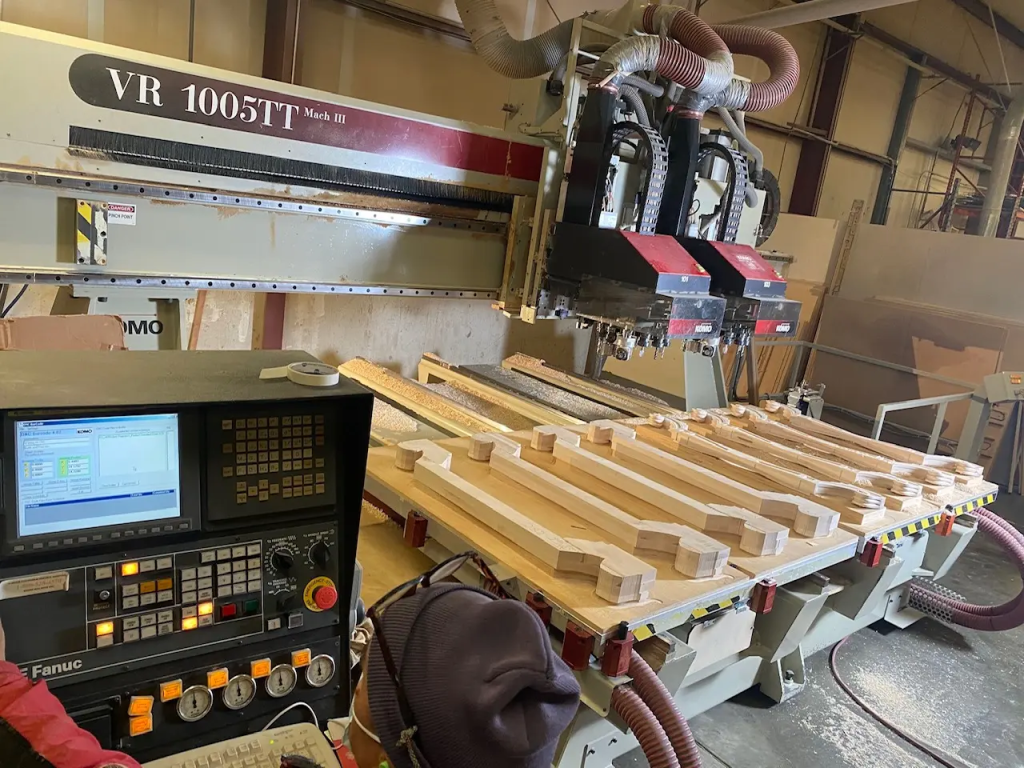
Source: allstarcnc.com
Hydraulic Fixtures
- Strong Clamping Force: Hydraulic pressure ensures secure clamping, particularly important for heavy-duty machining.
- Stability for Large Workpieces: Ideal for aerospace applications, providing stability when machining large components and reducing machining time.
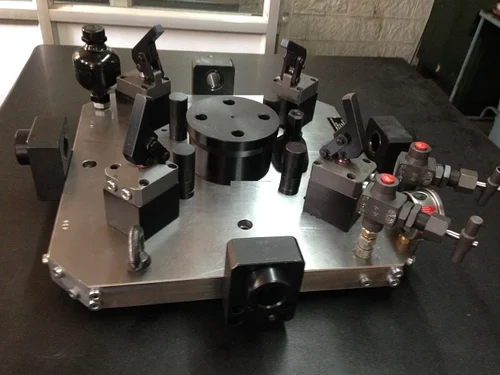
Source: smkturnkey.com
Pneumatic Fixtures
- Fast Clamping: Compressed air clamps workpieces swiftly, suitable for automated environments.
- Speeding up Assembly: Used in electronics manufacturing to expedite assembly processes, reducing cycle times.
Design Considerations for CNC Fixtures
Material Selection
- Durability and Strength Impact: Material choice affects fixture durability and ability to withstand machining forces.
- Example: Steel fixtures suit heavy-duty machining for their strength, while aluminum is preferred for rapid prototyping due to its lightweight nature and corrosion resistance.
Rigidity and Stability
- Preventing Deflection and Vibration: Rigidity ensures precise cutting and consistent part dimensions.
- Example: Fixtures with reinforced structures and solid base plates reduce deflection, improving surface finish quality.
Accessibility for Tooling
- Facilitating Easy Tool Access: Easy access to tools streamlines setup and operation, enhancing productivity.
- Example: Open designs or removable panels simplify tool installation and adjustment, reducing setup time and maintenance tasks.
Minimizing Interference
- Reducing Obstructions: Minimizing interference with machining processes and tooling prevents collisions and inaccuracies.
- Example: Clearance zones and avoidance of overhanging features minimize interference, ensuring smooth machining operations.
Compatibility with CNC Machine
- Seamless Integration: Compatibility with CNC machine specifications ensures optimal performance.
- Example: Standardized mounting interfaces and alignment features ensure proper integration, reducing setup time and operational errors.
In summary, when designing CNC fixtures, material selection, rigidity, accessibility for tooling, interference minimization, and compatibility with CNC machines are pivotal considerations. Thoughtful attention to these factors optimizes fixture performance, enhances productivity, and ensures precision in machining operations.
Using CNC Fixtures Effectively
Proper Fixture Setup and Alignment
- Achieving Precision and Consistency: Ensuring correct setup and alignment results in precise machining, maintaining consistent production quality.
- Minimizing Errors and Rework: Proper alignment reduces machining errors, leading to lower scrap rates and saving time and resources.
Optimizing Clamping and Holding Techniques
- Preventing Workpiece Movement: Effective clamping techniques stabilize the workpiece, improving machining accuracy and surface finish.
- Preserving Workpiece Integrity: Proper clamping maintains workpiece integrity, particularly important for delicate or complex parts, and enhances dimensional accuracy.
Monitoring and Adjusting During Machining Process
- Maintaining Precision: Regular monitoring maintains high precision levels, facilitating prompt error detection and correction.
- Enabling Timely Corrections: Continuous adjustments prevent defects, ensuring consistent product quality and enhancing productivity.
Ensuring Safety Measures for Operators and Equipment
- Preventing Accidents: Implementing safety measures protects operators and equipment, minimizing downtime and ensuring efficient operation.
- Extending Equipment Lifespan: Following safety protocols prolongs fixture and machine lifespan, reducing downtime and improving overall efficiency.
In summary, effective utilization of CNC fixtures ensures precision, minimizes errors, and enhances safety. By prioritizing proper setup, monitoring, and safety measures, manufacturers can optimize production quality and efficiency while safeguarding both personnel and equipment.
Applications of CNC Fixtures
Automotive Manufacturing
- Consistent Part Production: CNC fixtures ensure precise machining, critical for maintaining the quality and reliability of automotive parts.
- Examples: Used for machining engine components like cylinder heads and blocks, as well as transmission parts, ensuring uniformity in production quality.
Aerospace Industry
- Complex Component Machining: CNC fixtures provide the stability and accuracy required for machining intricate aircraft parts with tight tolerances.
- Examples: Used for machining aircraft structural parts, such as fuselage sections and wing components, and turbine blades, meeting stringent performance and safety standards.
Medical Device Fabrication
- High Accuracy and Precision: CNC fixtures enable the production of intricate medical device components with exceptional precision.
- Examples: Employed in manufacturing surgical instruments, implants, and prosthetic devices, ensuring adherence to strict regulatory standards for safety and effectiveness.
Mold and Die Making
- Reproducible Tooling Production: CNC fixtures are essential for fabricating accurate molds and dies used in various manufacturing processes.
- Examples: Utilized in creating injection molds and stamping dies, ensuring consistent, high-quality parts production in large quantities.
Conclusion
CNC fixtures play a vital role in modern manufacturing, enhancing efficiency, precision, and safety. By understanding their types, design considerations, and applications, manufacturers can optimize their machining processes.
Unionfab: A Trustworthy Partner in Manufacturing
Unionfab provides comprehensive manufacturing solutions including high-quality CNC, ensuring precision and efficiency in every project.
Furthermore, we provide a wide range of essential services, including finishing, to meet various needs. For further information, don't hesitate to contact us through our Contact Us page.
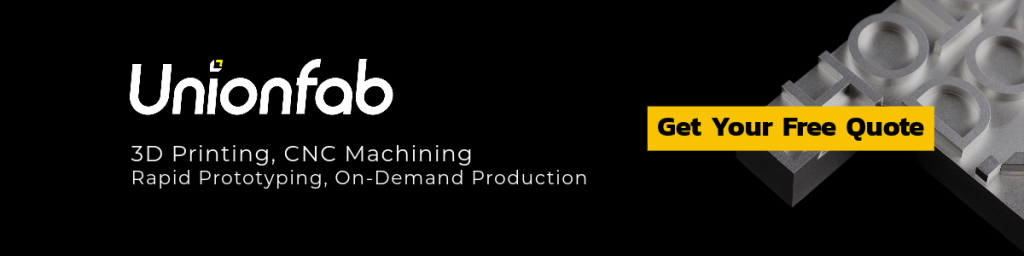