Injection Molding Materials: A Comprehensive Guide
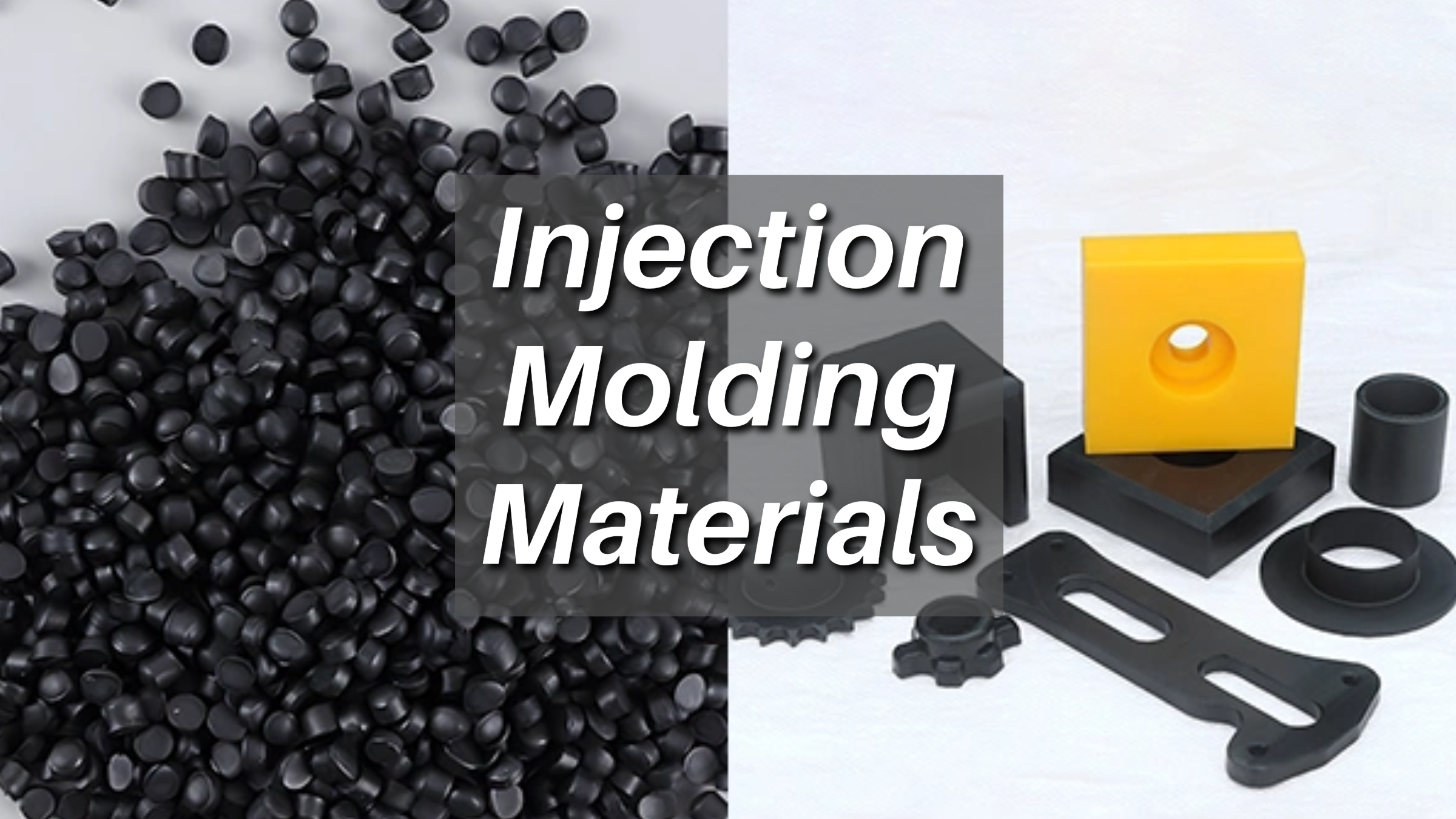
Explore the significance of injection molding materials, from understanding the injection molding process and navigating material types to optimizing efficiency.
Introduction
Injection molding relies on a vast array of materials, each offering unique advantages for the final product. From the crystal-clear clarity of acrylic to the high-strength resilience of nylon, the chosen material impacts everything from visual appeal to mechanical performance.
Understanding Injection Molding Materials
Explanation of Injection Molding Process
Injection molding is a high-volume formative manufacturing process that creates precise plastic parts. The injection molding process invovles the following steps.
Material Selection: This is the first step. Factors like part strength, heat resistance, and chemical compatibility are considered.
Mold Design and Creation: A steel mold with a cavity matching the desired part shape is designed and manufactured.
Material Preparation: Plastic pellets are fed into a hopper and heated until molten.
Injection: The molten plastic is injected into the mold cavity under high pressure.
Cooling and Ejection: The plastic cools and solidifies within the mold. Once cooled, the part is ejected.
Finishing (Optional): Depending on the application, parts may undergo additional processes like trimming, deburring, or surface finishing.
Types of Injection Molding Materials
Thermoplastics
ABS (Acrylonitrile Butadiene Styrene): Offers a good balance of strength, impact resistance, and affordability. Used in car parts, toys, and electronics.
Nylon (Polyamide): Strong, abrasion-resistant, and versatile. Used in gears, bearings, and housings.
Polycarbonate (PC): Highly transparent, impact-resistant, and dimensionally stable. Used in lenses, medical devices, and electronic components.
Polyethylene (PE): Lightweight, flexible, and chemically resistant. Used in bottles, films, and packaging.
Polypropylene (PP): Strong, lightweight, and heat-resistant. Used in food containers, textiles, and automotive parts.
Thermosets
Epoxy: Strong adhesive properties and good chemical resistance. Used in electrical components and composite materials.
Phenolics: Excellent heat and chemical resistance. Used in electrical components and automotive parts.
Elastomers
Silicone: High heat resistance, flexibility, and biocompatibility. Used in medical devices, gaskets, and food-grade applications.
Nitrile Rubber: Excellent oil and abrasion resistance. Used in hoses, seals, and gaskets.
Common Injection Molding Materials
ABS (Acrylonitrile Butadiene Styrene)
ABS is a tough, lightweight, and dimensionally stable thermoplastic known for its good impact resistance and scratch resistance.
It also boasts excellent insulating properties, making it suitable for electrical applications. Additionally, its low melting temperature (around 40-80°C) makes it ideal for injection molding.
ABS is used in various commercial products, including car parts (interior trims, dashboards), toys (building blocks), electronics casings, and household appliances.
Nylon (Polyamide)
Nylon is a versatile material known for its strength, making it a popular choice for mechanical parts like gears, bearings, and bushings.
It's also lightweight compared to metal alternatives, contributing to weight reduction and potentially lower production costs.
However, nylon tends to absorb water, limiting its suitability for marine applications.
HDPE (High-Density Polyethylene)
HDPE is a cost-effective, stiff plastic material with high strength.
It's widely used for manufacturing plastic bottles, shampoo bottles, toys, recycling bins, and even flower pots.
While affordable and strong, HDPE has some drawbacks. It's highly flammable and not biodegradable, posing environmental concerns. Additionally, it cannot be easily painted or bonded and has poor weather resistance.
LDPE (Low-Density Polyethylene)
LDPE is another commonly used injection molding material known for its moisture and chemical resistance.
It's also low-cost and food-grade safe, making it suitable for food packaging applications like bottles, plastic bags, and wraps.
However, LDPE shares some limitations with HDPE, including flammability, poor resistance to high temperatures, and difficulty in bonding. It also weathers poorly.
PC (Polycarbonate)
Polycarbonate (PC) is a high-performance, transparent thermoplastic with excellent strength and impact resistance.
It can withstand higher temperatures due to its relatively high melting point (155°C). Additionally, PC has good dimensional stability and high density (1.2 – 1.22 g/cm3).
Thanks to these strengths, it’s a preferred material for safety-critical products like helmets and bulletproof glass—often recommended or supplied by safety solutions providers. It's also used in equipment housing, automotive parts, electrical connectors, and insulators.
However, PC is susceptible to damage from certain chemicals and has low fatigue tolerance. It can also turn yellow over time with UV exposure, and its mechanical properties degrade in hot water.
Factors Influencing Injection Molding Materials Selection
While the properties of the material itself are crucial, several other factors influence the selection process for injection molding.
Application-Specific Requirements
This is all about ensuring the chosen material can handle the job it's designed for.
Strength and Durability
For parts experiencing high stress or loads, consider materials like:
Nylon: Gears, bearings (exceptional strength, wear resistance)
PC (Polycarbonate): Automotive parts, safety equipment (high strength, impact resistance)
Flexibility
If flexibility is crucial, choose materials like:
LDPE (Low-Density Polyethylene): Squeeze bottles, toys (flexibility, affordability)
Polyurethanes (TPUs): Shoe soles, hoses (excellent flexibility, durability)
Heat Resistance
Parts exposed to high temperatures may benefit from:
PC (Polycarbonate): Electronics components (high melting point, dimensional stability)
PPS (Polyphenylene Sulfide): Engine components, pump housings (exceptional heat resistance)
Transparency
For clear parts, materials like:
PC (Polycarbonate): Safety glasses, lenses (high clarity, impact resistance)
PMMA (Polymethyl Methacrylate - Acrylic): Display cases, signs (excellent clarity, lightweight)
Production Volume and Scalability
This factor considers how efficiently the material translates into production.
Low Volume
For small production runs, costlier but unique materials like:
PEEK (Polyetheretherketone): Medical implants, aerospace components (excellent strength, high-temperature resistance)
ABS (Acrylonitrile Butadiene Styrene): Versatility allows for smaller production runs with good properties.
High Volume
Affordability and efficient molding are key. Consider:
HDPE (High-Density Polyethylene): Bottles, containers (cost-effective, good flow properties)
PP (Polypropylene): Food containers, textiles (affordable, good processing characteristics)
Regulatory Compliance and Certifications
Food Contact
Materials that meet food safety regulations are essential, like:
PP (Polypropylene): Food containers, reusable straws (food-grade safe)
High-density PE (HDPE): Food storage containers (food-grade safe)
Medical Devices
Materials requiring biocompatibility and sterilization:
PEEK (Polyetheretherketone): Medical implants (biocompatible, high-performance)
PC (Polycarbonate): Syringe barrels (chemical resistance, sterilizable)
Environmental Sustainability
Biodegradable or Recyclable Materials
Consider options like:
PLA (Polylactic Acid): Compostable packaging materials (biodegradable, good clarity)
Bio-based PE (Polyethylene): Bottles, containers (made from renewable resources)
Reduced Material Waste
Materials with good flow properties for minimal waste:
PP (Polypropylene): Good flow characteristics, recyclable
ABS (Acrylonitrile Butadiene Styrene): Relatively low waste during molding, recyclable
Material Optimization Techniques
Beyond selecting the right material, manufacturers can further optimize the injection molding process through various techniques.
Material Flow and Viscosity Management
Material Selection: High-viscosity materials might require adjustments to mold features or processing parameters to ensure proper flow.
Mold Design Optimization: Sharp corners, thin walls, and unnecessary changes in thickness can hinder material flow. Streamlining the mold design for smooth flow can improve material usage.
Melt Temperature Control: Temperatures that are too low can lead to poor flow and incomplete filling, while excessively high temperatures can cause degradation and waste.
Mold Design Considerations
Gate Design and Placement: The gate, the entry point for molten plastic into the mold cavity, plays a significant role. The size, shape, and location of the gate can influence flow patterns and minimize waste.
Runner System Design: The runner system channels the molten plastic from the sprue (injection point) to the gates. Optimizing runner size and layout can minimize material used in the runner system itself, reducing overall waste.
Venting: Proper venting allows trapped air to escape the mold cavity during filling. Inadequate venting can lead to incomplete filling, surface defects, and wasted material.
Temperature and Pressure Control
Precise Melt Temperature: Maintaining the optimal melt temperature for the chosen material allows for good flow while minimizing degradation. Overheating can lead to material breakdown, discoloration, and potential part defects.
Optimized Injection Pressure: Using the appropriate injection pressure ensures complete filling of the mold cavity without excessive pressure that can cause warping or flash (excess material seeping out of the mold).
Holding Pressure and Packing: Precise control of holding pressure and packing time allows for proper material packing and compensation for shrinkage during cooling, minimizing sink marks.
Strategies for Minimizing Material Waste
Runner and Sprue Design: Optimizing runner and sprue sizes can minimize the amount of material wasted during each injection cycle. These leftover materials can often be reground and reused for future molding.
Cold Runner Systems: These systems use heated molds and a cooled runner to solidify plastic only in the sprue and runner channels, minimizing waste compared to hot runner systems where the entire runner remains molten.
Regrind and Reprocessing: Regrinding sprues and runners allows for a portion of the leftover material to be reused in subsequent molding cycles, reducing overall material waste.
Quality Assurance of Injection Mold Materials
Defect Reduction Through Proper Material Selection
Matching Material Properties to Application
Selecting a material with the necessary strength, heat resistance, and chemical compatibility for the intended use helps prevent defects like cracking, warping, or discoloration.
For instance, using a high-temperature resistant material like PEEK (Polyetheretherketone) for engine components reduces the risk of heat deformation.
Material Purity and Consistency
High-quality, contaminant-free materials minimize imperfections like bubbles or streaks.
Inconsistency in material properties can lead to unpredictable shrinkage or warping. For example, using virgin PP (Polypropylene) with consistent properties ensures minimal surface imperfections in food containers.
Moisture Control
Hygroscopic materials like nylon absorb moisture, leading to surface blemishes or internal stresses that cause warping or cracking.
Proper drying techniques ensure consistent material properties and prevent these defects.
Surface Finish Considerations
Material Selection
Different materials offer varying surface finishes. For instance, PP (Polypropylene) has a naturally matte finish, while PMMA (Polymethyl Methacrylate - Acrylic) offers a high-gloss finish.
Mold Surface Quality
The surface finish of the mold directly impacts the part's surface quality. A polished mold creates a smooth surface on the part, while a textured mold replicates its texture onto the part.
Process Optimization
Optimizing processing parameters like melt temperature, injection pressure, and cooling time can minimize surface defects like sink marks, flow lines, or blemishes.
Dimensional Accuracy
Mold Design and Manufacturing
A precisely designed and manufactured mold ensures the final parts meet the desired dimensions.
Material Shrinkage
All materials experience some shrinkage upon cooling. Understanding the material's shrinkage rate allows for adjustments in mold design to compensate and achieve accurate part dimensions.
Process Control
Maintaining consistent processing parameters throughout production minimizes dimensional variations in the molded parts.
Tolerance Levels
Part Design and Functionality
The intended use of the part determines the tolerance levels required for its dimensions.
Material Selection
Certain materials inherently offer better dimensional stability than others.
Choosing a material like PC (Polycarbonate) with good dimensional stability helps maintain tolerance levels for parts requiring precise dimensions.
Process Control and Monitoring
Continuously monitoring and adjusting processing parameters like injection pressure and holding time ensures parts stay within the specified tolerances.
Post-Processing Methods
Trimming and Deburring
Removing excess material from sprues and gates, trimming flash (excess material around the part), and deburring sharp edges ensures clean and dimensionally accurate parts.
Surface Finishing
Some applications may require additional surface finishing techniques like polishing, painting, or plating to achieve the desired aesthetics or functionality.
Importance of Injection Molding Materials
Backbone of the Injection Molding Process
The chosen material dictates the success of the entire injection molding process.
Flow Efficiently: Materials with good flow properties, like PP (Polypropylene), fill the mold cavity completely, minimizing defects and ensuring part consistency.
Solidify Properly: The material's solidification rate significantly impacts cycle time. Materials that solidify quickly, like HDPE (High-Density Polyethylene), allow for faster production cycles.
Possess Necessary Properties: The material's inherent properties like strength, heat resistance, and flexibility need to match the final part's application. For instance, using a high-strength nylon gear in a power tool ensures it can handle the torque and stress.
Impact on Manufacturing Efficiency
Material selection significantly influences production efficiency:
Faster Cycle Times: Materials with good flow properties and optimal processing parameters, like ABS (Acrylonitrile Butadiene Styrene), enable faster cycle times, leading to higher production output.
Reduced Waste: Materials with minimal shrinkage and good flow characteristics, like PP (Polypropylene), minimize material waste during the injection process.
Minimal Rejects: Materials with consistent properties and proper drying techniques, like nylon for automotive parts, minimize the risk of defects and part rejects, reducing rework and production delays.
Cost Considerations
Material Selection vs. Processing Costs: While a lower-cost material like LDPE (Low-Density Polyethylene) might seem appealing, it may require additional processing steps to achieve desired properties. This can negate the initial cost advantage.
Balancing Performance and Cost: Selecting a material that offers the necessary performance at a reasonable cost is crucial. For instance, a food container might prioritize a cost-effective material like PP, as long as PP meets the required strength and food-safe standards.
Quality Assurance and Product Integrity
The material selection directly impacts the quality and integrity of the final molded parts:
Material Properties and Defects: Choosing a material with the necessary strength and heat resistance, like PC (Polycarbonate) for safety glasses, minimizes the risk of defects like cracking or warping, ensuring product safety and functionality.
Dimensional Accuracy: Materials with predictable shrinkage rates, like ABS, allow for precise mold design, leading to dimensionally accurate parts. This is crucial for parts with tight tolerances, like gears or medical devices.
Long-Term Performance: Material selection considers how the part will perform over time. Using a UV-resistant material like PC for outdoor applications ensures the part doesn't become brittle or discolored due to sun exposure.
Conclusion
Injection molding relies on a diverse array of materials, each offering unique advantages and limitations.
Selecting the right material goes beyond just functionality; it impacts factors like production efficiency, cost, and even the final product's environmental footprint.
Unionfab: Your Reliable Partner in Manufacturing
Unionfab offers a wide range of services beyond injection molding, including 3D printing for prototyping, CNC machining for complex geometries, and various finishing techniques. This allows for seamless project management and efficient production.
Contact us today to discuss your project. Together, we can turn your vision into reality!
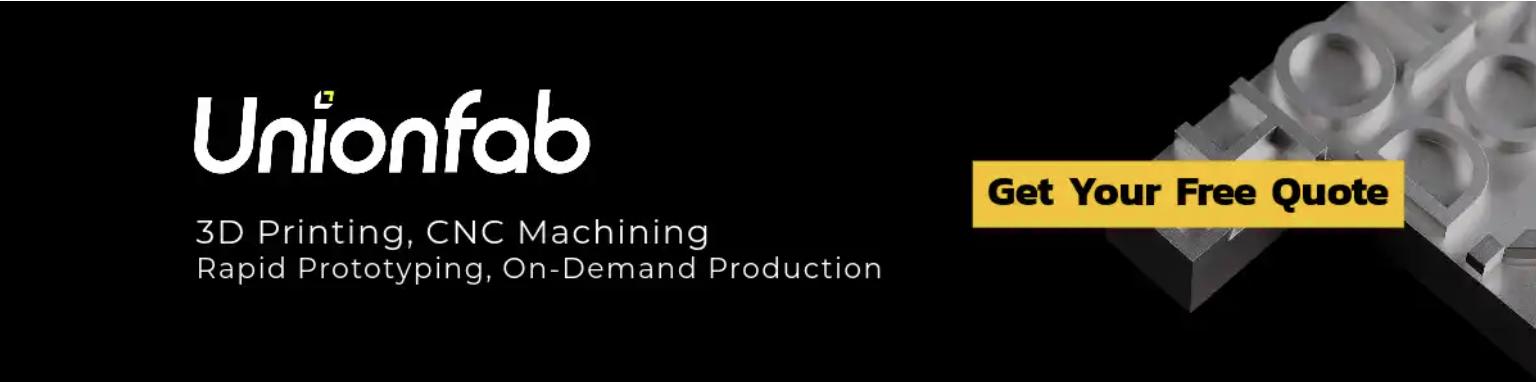