Infill 3D Printing: A Comprehensive Introduction
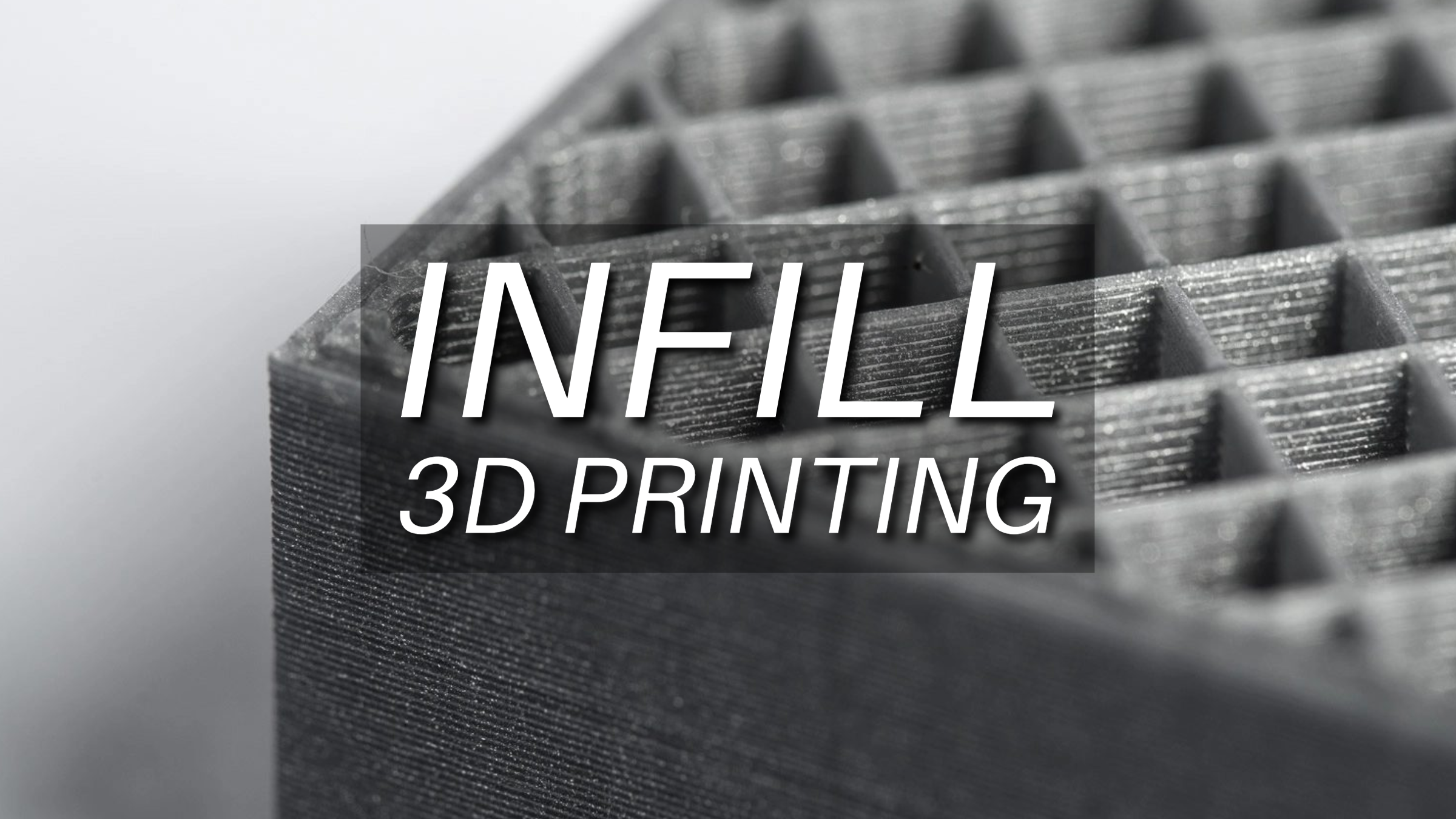
Learn about different types of infill 3d printing, their applications, and advancements shaping the future of additive manufacturing.
Introduction
Infill 3D printing is a crucial aspect of additive manufacturing that plays a significant role in determining the structural integrity, strength, and overall performance of printed objects.
This comprehensive guide explores the concept of infill 3D printing, including its definition, various patterns, benefits, applications, and advanced techniques shaping its future.
What is Infill 3D Printing
Definition and Explanation of Infill 3D Printing
Infill 3D printing refers to the process of creating a supportive internal structure within a 3D printed object, often using a lattice pattern, filling the empty spaces between its outer shells or perimeters.
This internal structure, known as infill, provides strength, stability, and support to the object while reducing material usage and print time compared to solid structures. The role of infill is crucial in achieving the desired mechanical properties and optimizing the performance of 3D printed parts.
Role of Infill in the 3D Printing Process
Infill plays a vital role in determining the mechanical properties and performance of a 3D printed object. It provides internal support, enhances strength, and prevents warping or deformation during printing.
Difference Between Solid and Infill Structures
Aspect | Solid | Infill |
---|---|---|
Strength | Max | Adeq |
Material Usage | High | Reduced |
Print Time | Longer | Shorter |
Applications | Load | Protos |
Strength
- Solid: Solid structures provide maximum strength and rigidity due to their dense and continuous material composition. This makes them ideal for applications where structural integrity is critical and subjected to heavy loads or stress.
- Infill: Infill structures maintain adequate strength for many applications while using less material. They achieve this by creating internal lattice or honeycomb-like patterns, which provide support and reinforcement while reducing overall material usage.
Material Usage
- Solid: Solid structures require a significant amount of material to fill the entire volume of the object being printed. This leads to higher material consumption, increased waste, and elevated material costs.
- Infill: Infill structures conserve material by creating internal patterns that occupy only a portion of the object's volume. This reduces material consumption, minimizes waste, and lowers material costs, making infill structures more cost-effective and sustainable.
Print Time
- Solid: Printing solid structures takes longer compared to infill structures due to the higher volume of material being deposited layer by layer. The printer must lay down material for the entire object, resulting in a slower printing process.
- Infill: Printing infill structures is faster because they require less material to be deposited. The printer can build the internal lattice or honeycomb-like patterns more quickly, resulting in shorter print durations and increased printing efficiency.
Applications
Solid: Solid structures are commonly used in applications where maximum strength, durability, and rigidity are required. These include load-bearing components, structural parts, and objects subjected to high mechanical stress or impact.
Infill: Infill structures are versatile and suitable for various applications where strength, efficiency, and lightweight characteristics are desired. These include prototypes, lightweight components for aerospace and automotive industries, consumer goods, and objects where material conservation is important.
Infill 3D Printing Patterns
Basic Concepts of Infill in 3D Printing
In 3D printing, infill means adding internal structures to objects to support them without filling the entire volume. It saves material and time while maintaining strength and integrity. Infill prevents warping and enhances layer adhesion, crucial for efficient printing.
Common Infill 3D Printing Patterns and Their Characteristics
- Rectilinear: This pattern consists of parallel lines arranged in a grid-like formation. It offers good strength and reliability, making it suitable for various applications. Its simple structure ensures ease of printing and provides uniform support throughout the object.
- Honeycomb: Featuring hexagonal cells arranged in a honeycomb-like layout, this pattern offers an excellent strength-to-weight ratio. It provides strong support while minimizing material usage, making it ideal for lightweight components and structures where both strength and weight are crucial.
- Triangular: Comprising interconnected triangles forming a lattice structure, this pattern provides good strength and efficiency. Its triangular arrangement offers stability and uniform support, making it suitable for a wide range of applications, including lightweight structures and parts requiring strength and durability.
- Gyroid: The gyroid pattern, with its complex, interconnected strands, offers optimal strength, flexibility, and material efficiency. Its geometry provides strong support while minimizing material usage and weight, making it ideal for complex objects.
Comparison of Infill Density and Patterns in 3D Printing
Infill density and pattern selection depend on the object's purpose. Higher densities offer stronger but heavier prints, while lower densities save material but are less strong. Different patterns balance strength, flexibility, and efficiency. Customizing these factors helps optimize for load-bearing needs, weight, and print time.
Benefits of Infill 3D Printing
Structural Integrity and Strength Enhancement
Infill patterns serve to reinforce the internal structure of 3D printed objects, enhancing their mechanical properties and durability. By creating a lattice or honeycomb-like pattern within the object, infill distributes forces more evenly, reducing the likelihood of failure or deformation.
Material and Cost Efficiency
Infill 3D printing reduces material waste and production costs by using less material compared to printing solid structures. This efficiency not only conserves resources but also lowers material expenses, making infill printing a more economical option for manufacturing various parts and prototypes.
Weight Reduction
Infill structures are inherently lightweight due to their sparse internal patterns. This makes them ideal for applications where weight is a concern, such as aerospace and automotive industries. By reducing the overall weight of printed objects, infill printing enables the creation of lighter components without compromising on strength or structural integrity.
Less Print Time
Infill patterns contribute to shorter print times compared to printing solid structures. Since infill structures require less material to be deposited, the printing process is faster, resulting in reduced production times. This enables faster prototyping and production, allowing for quicker turnaround times and increased efficiency in additive manufacturing processes.
Applications of Infill 3D Printing
Aerospace
Infill 3D printing is extensively used in aerospace for producing lightweight components and structural parts for aircraft and spacecraft. The ability to create intricate internal structures with optimized infill patterns allows for the fabrication of lightweight yet durable parts, contributing to fuel efficiency and overall performance.
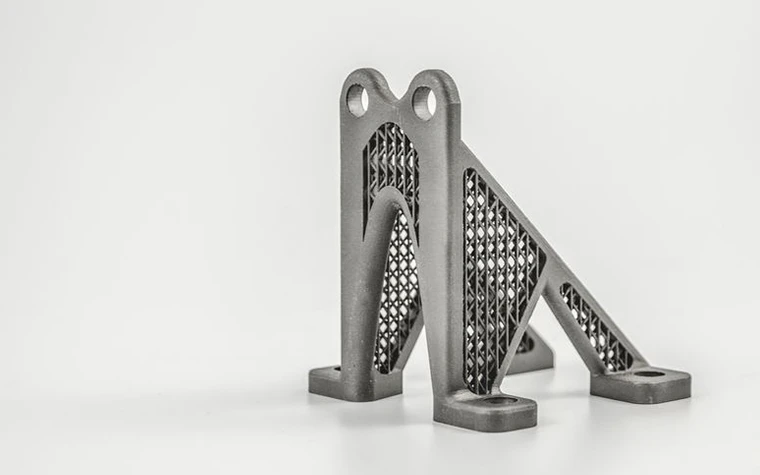
Source:materialise.com
Automotive
Infill 3D printing plays a crucial role in the automotive industry, where rapid prototyping and manufacturing of functional parts with reduced weight and material usage are essential.
By utilizing infill structures, automotive manufacturers can produce lightweight components that meet stringent performance requirements while minimizing material waste and production costs.
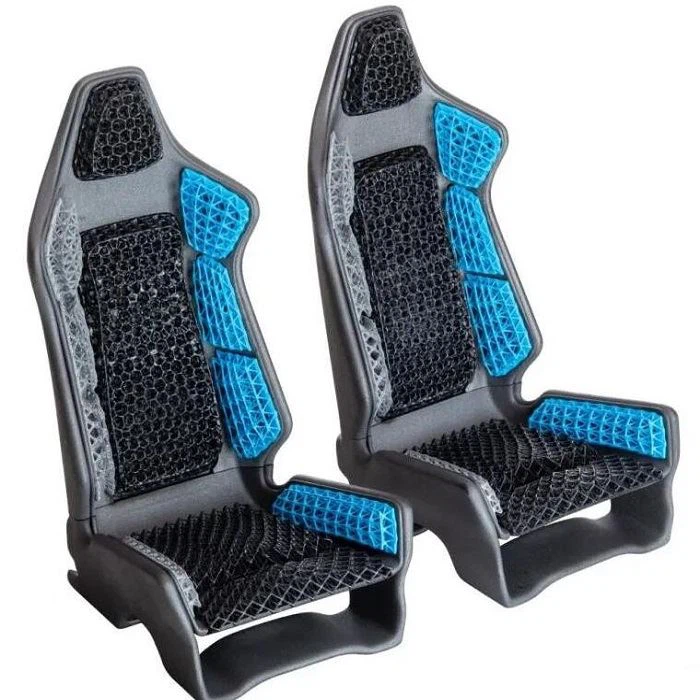
Source:china-3dprinting.com
Medical
Infill 3D printing is widely employed in the medical field for fabricating prosthetics, medical devices, and patient-specific implants. Customized infill patterns can be tailored to optimize the performance and functionality of medical devices, ensuring a perfect fit and enhancing patient outcomes.
Additionally, infill structures allow for the creation of lightweight yet durable prosthetic limbs and implants, improving comfort and mobility for patients.
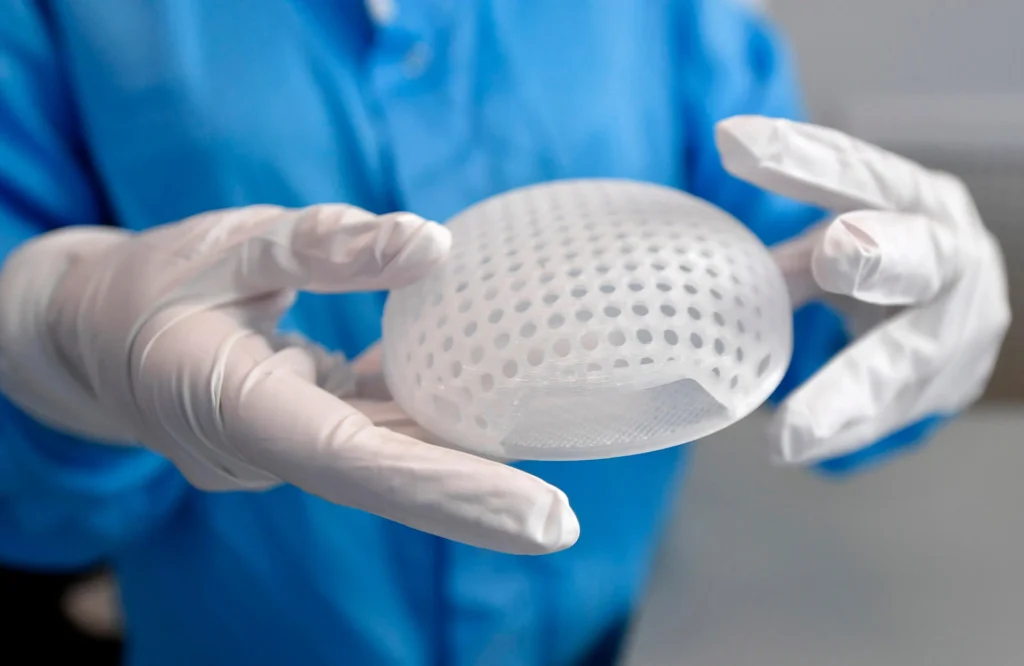
Source:3devo.com
Consumer Goods
Infill 3D printing is used in the consumer goods industry to create customized, durable products. It enhances household items and industrial equipment by improving strength, reducing weight, and enhancing performance. Customized infill patterns allow for personalized products tailored to individual preferences, offering flexibility and versatility in design and manufacturing.
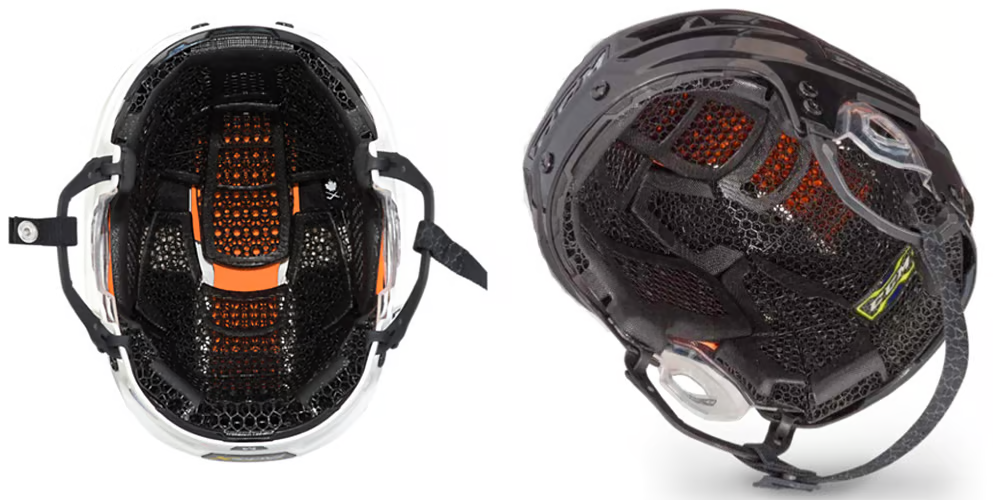
Source:all3dp.com
Advanced Infill 3D Printing Techniques
The field of 3D printing has seen significant advancements in infill techniques, which are crucial for optimizing the balance between material usage, print time, and structural integrity. Here are detailed explanations of recent advancements in infill 3D printing techniques:
Variable Infill Density
Variable infill density involves adjusting the density of the infill in different parts of the printed object based on specific requirements. This technique helps in optimizing the strength-to-weight ratio and reducing material usage. For example:
- High Stress Areas: Areas that need to bear more load can have a higher infill density to enhance strength.
- Low Stress Areas: Areas with less structural demand can have a lower infill density to save material and reduce weight.
- Applications: This is particularly useful in automotive and aerospace industries where weight reduction without compromising strength is critical.
Adaptive Infill Algorithms
Adaptive infill algorithms dynamically adjust infill patterns during the printing process to improve performance and efficiency. These algorithms analyze the geometry of the object and modify the infill pattern accordingly:
- Optimized Path Planning: They optimize the path of the print head to minimize print time and material waste.
- Enhanced Structural Properties: By analyzing stress distribution, these algorithms can place more material where it's needed most, improving the overall strength of the object.
- Efficiency: Adaptive algorithms can lead to significant time savings, especially in large prints, by reducing redundant infill.
Smart Infill
Smart infill incorporates advanced materials or sensors within the infill structure to achieve specific functionalities:
- Embedded Sensors: Sensors can be embedded within the infill to monitor the structural integrity of the printed object in real-time or over its lifespan.
- Responsive Materials: Smart materials that change properties in response to environmental conditions (e.g., temperature, humidity) can be integrated within the infill to create adaptive structures.
- Applications: This technique is used in creating smart medical implants, responsive architectural elements, and IoT-enabled objects.
Integration with Multi-Material Printing
Combining different materials within infill structures allows for the creation of complex geometries and functional gradients:
- Gradient Structures: Different materials can be used in varying ratios within the infill to create a gradient of properties (e.g., transitioning from a hard exterior to a softer core).
- Hybrid Objects: Objects that require different properties in different areas (e.g., flexibility in one part and rigidity in another) can benefit from multi-material infill.
- Complex Geometries: This integration enables the production of objects with complex internal structures that would be difficult or impossible to achieve with a single material.
- Applications: This is particularly advantageous in medical prosthetics, robotics, and custom consumer products.
Practical Applications
- Medical Devices: Customized implants and prosthetics can be optimized for weight and strength, with smart infill providing real-time monitoring capabilities.
- Aerospace and Automotive: Lightweight yet strong components can be produced, improving fuel efficiency and performance.
- Consumer Goods: Multi-material infill allows for personalized products with varying tactile and structural properties, enhancing user experience.
In conclusion, these advanced infill techniques are pushing the boundaries of what is possible with 3D printing, enabling more efficient, strong, and functional printed objects. As technology progresses, the integration of AI and advanced materials will likely lead to even more sophisticated and capable 3D printed products.
Conclusion
Infill 3D printing revolutionizes additive manufacturing by offering a balance between strength, efficiency, and customization.
With its wide range of patterns, benefits, and applications, infill 3D printing continues to drive innovation and advancement in various industries, shaping the future of manufacturing.
Unionfab: Your Professional Partner in 3D Printing
Discover the future of manufacturing with Unionfab's advanced 3D printing capabilities and innovative solutions. Our comprehensive range of 3D printing services at Unionfab is designed to cater to a diverse array of industries and applications.
Contact us for professional assistance and expertise in additive manufacturing.
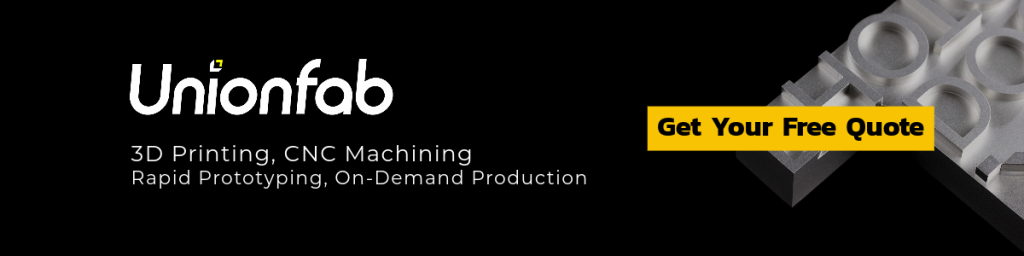