Guide to Stainless Steel 3D Printing[+Free Cost Calculator]
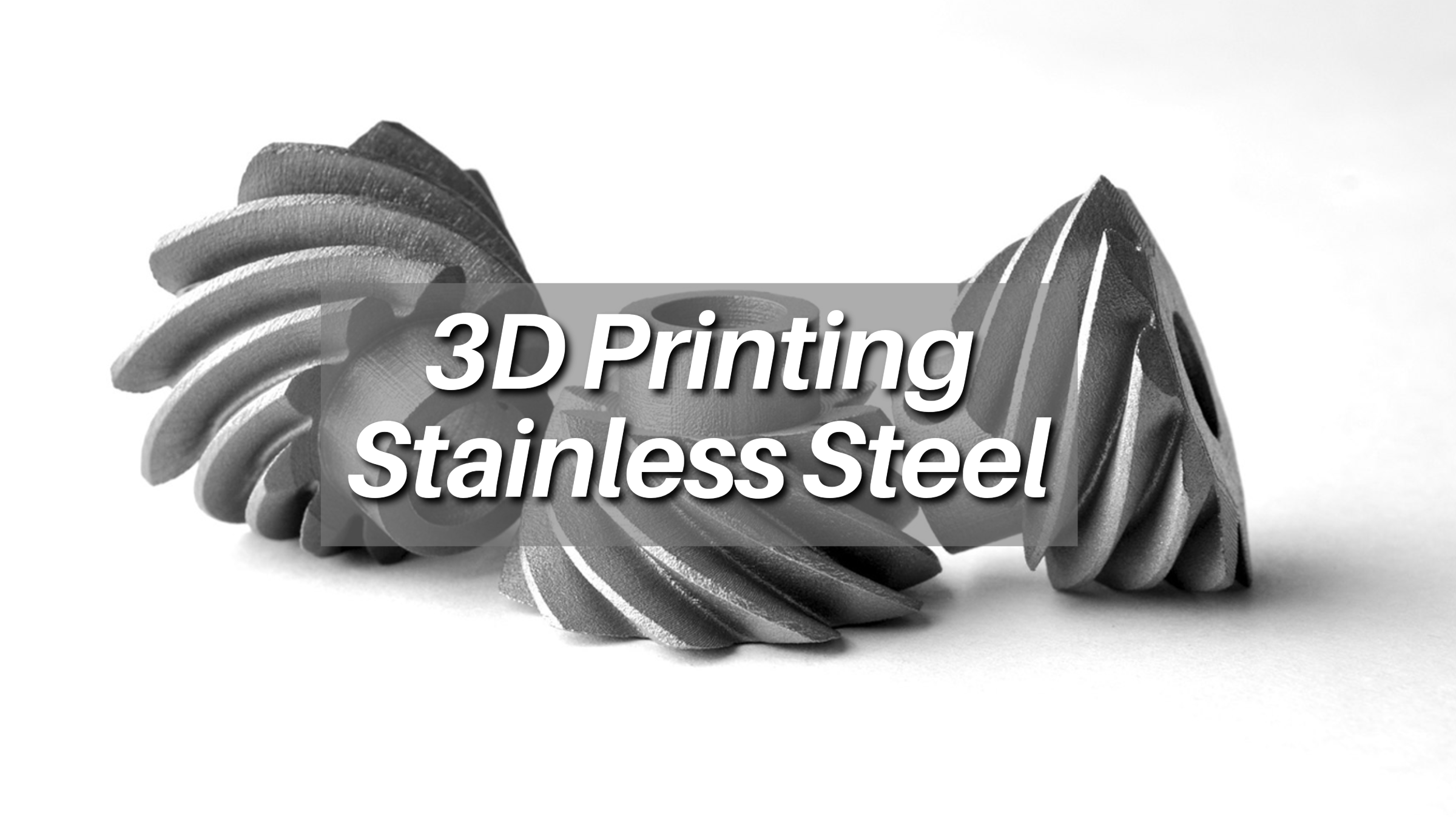
This informative article serves as both a knowledge guide to stainless steel 3D printing and a buying guide to help customers select the most suitable service provider.
Introduction
Stainless Steel(SS) is valued across industries for excellent mechanical properties, corrosion resistance, and durability. Unlike other metals, SS can withstand extreme temperatures, high pressure, and harsh environments, making it ideal for aerospace, medical, automotive, and consumer applications.
Now with advancements in manufacturing, 3D printing has revolutionized stainless steel fabrication. Compared to traditional casting, machining, and welding, it offers greater design flexibility, minimal material waste, and precise production of complex geometries. These advantages open new possibilities for industries requiring custom, lightweight, and high-performance stainless steel components.
Understanding 3D Printing Stainless Steel
Basics of Additive Manufacturing
Additive Manufacturing (AM), also known as 3D printing, builds objects layer by layer from a digital design. For stainless steel, this typically involves a metal powder and a high-powered laser. Here's a breakdown of the process:
Powder Preparation: Fine stainless steel powder is spread onto a platform.
Laser Melting: A high-powered laser selectively melts the powder particles according to the design blueprint.
Layer by Layer: The platform lowers, and a new layer of powder is deposited. The laser then melts the fresh powder, fusing it to the previous layer.
Support Removal: Once complete, the part is removed from the machine, and any support structures used during printing are removed.
Advantages of 3D Printing Over Traditional Methods in Making Stainless Steel Parts
Compared with traditional methods like casting, molding and machining, 3d printing has several unique advantages in making stainless steel parts as follows:
Design Freedom
Traditional manufacturing limits complexity. 3D printing enables intricate geometries, internal channels, and lightweight structures without extra cost.
Faster Production
No need for molds or setups—get functional stainless steel parts in days, perfect for rapid prototyping and small-batch production.
Cost-Effective for Low to Medium Volumes
No tooling costs**, making 3D printing affordable for prototypes, custom parts, and limited production runs.
Minimal Material Waste
Uses only the necessary material, reducing scrap compared to machining.
Strong, Integrated Parts
Fewer weak points—complex assemblies can be printed as a single durable component.
On-Demand Manufacturing
No need for large inventories—print only what you need, when you need it.
Stainless Steel 316L vs. 17-4 PH vs. 304L vs. 15-5 PH
After understanding the advantages of 3D printing for stainless steel, the next step is choosing the right material for your specific application.
In 3d printing, the common types of stainless steel include 316L, 17-4 PH, 304L and 15-5 PH. Below is a comparison table of them to help you make a choice.
Property | 304L | 15-5 PH | ||
---|---|---|---|---|
Tensile Strength (MPa) | 485–620 | 1000–1200 | 485–620 | 1000–1100 |
Yield Strength (MPa) | 170–310 | 850–1000 | 170–310 | 860–1050 |
Elongation | 40–50 | 10–20 | 40–45 | 10–20 |
Hardness (Brinell) | 146–190 | 330–400 | 146–190 | 330–370 |
Density (g/cm³) | 7.9 | 7.75 | 7.9 | 7.75 |
Corrosion Resistance | ★★★★☆ | ★★★☆☆ | ★★★☆☆ | ★★★☆☆ |
Thermal Conductivity | 15–16 | 16–17 | 16.2 | 16–17 |
Post-Processing | Stress relieving | Solution treatment & aging | Stress relieving | Solution treatment & aging |
Cost | $$ | $$$ | $ | $$$ |
Key Takeaways:
Mechanical Properties: 17-4 PH and 15-5 PH have higher strength but lower ductility than 316L and 304L.
Corrosion Resistance: 316L excels in chloride environments, while the others offer good but lower resistance.
Thermal Properties: All grades have similar thermal conductivity.
Density: 316L and 304L are slightly denser than 17-4 PH and 15-5 PH.
Post-Processing: 17-4 PH and 15-5 PH require solution treatment and aging, while 316L and 304L need stress relieving.
Cost: 304L is the cheapest, 316L is moderate, and 17-4 PH and 15-5 PH are the most expensive.
To get more details about the properties of stainless steels, download Unionfab’s data sheets.
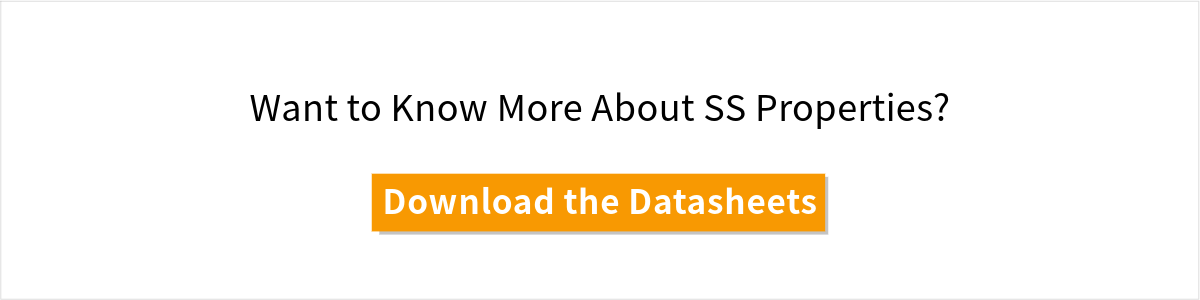
How to Choose the Right Technology to 3D Print Stainless Steel
The technologies used in metal 3d printing include SLM(Selective Laser Melting), BJ(Binder Jetting), EBM (Electron Beam Melting), DED(Directed Energy Deposition), WAAM(Wire Arc Additive Manufacturing), and Cold Spray.
How do they work?
Selective Laser Melting (SLM) 3D Printing
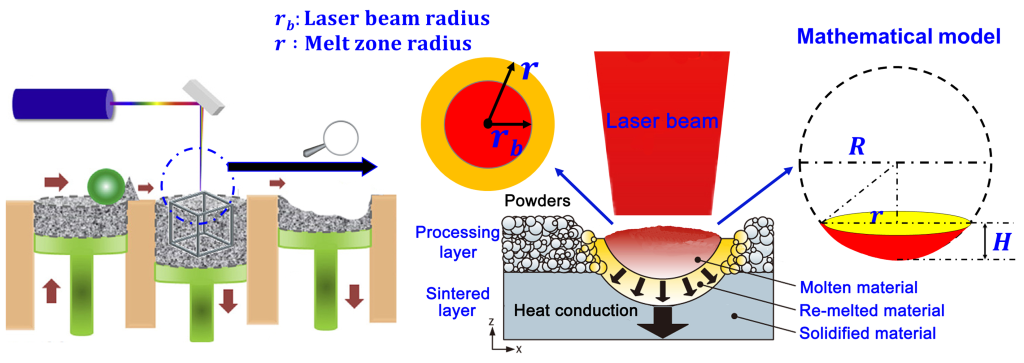
Source: wikipedia.org
SLM, also known as Direct Metal Laser Sintering (DMLS), is the most widely used technique for 3D printing stainless steel.
Process: A high-powered laser beam selectively melts thin layers of metal powder, fusing them together to create the desired part layer by layer.
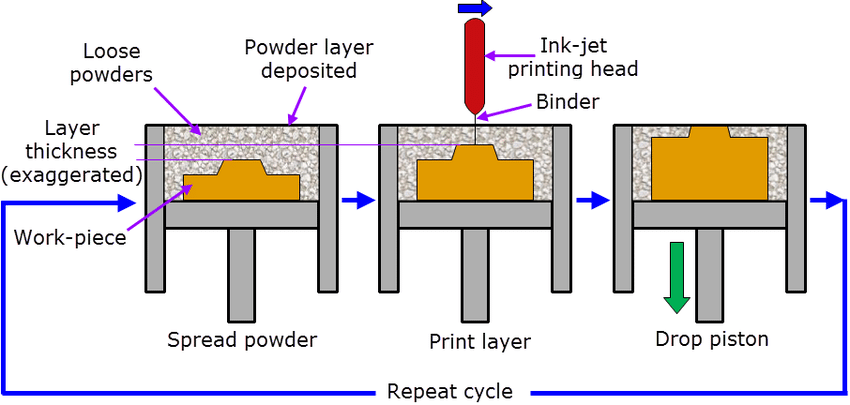
Source: oceanproperty.co.th
Process: A print head jets a binder solution onto specific areas of the powder bed, adhering the powder particles together. Once a layer is complete, a new layer of powder is deposited, and the process repeats. Finally, the entire part is infiltrated with a bonding agent to create a solid structure.
Electron Beam Melting (EBM)
Uses an electron beam to melt metal powder layer by layer in a vacuum chamber. It is similar to SLM, but uses an electron beam instead of a laser.
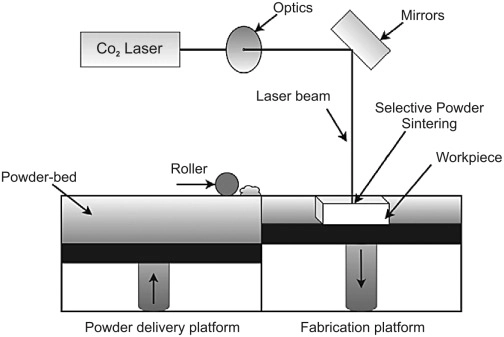
Source: 3dprintingindustry.com
Direct Energy Deposition (DED)
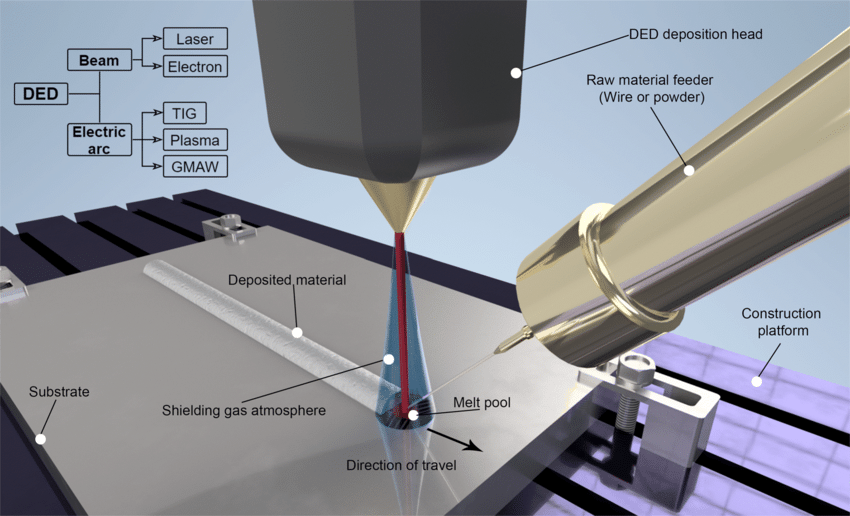
Source: additec3d.com
Uses a focused energy source (laser, electron beam, or plasma arc) to melt metal powder or wire, which is directly deposited onto a substrate. This technique is ideal for repairs or adding material to existing parts.
WAAM (Wire Arc Additive Manufacturing)
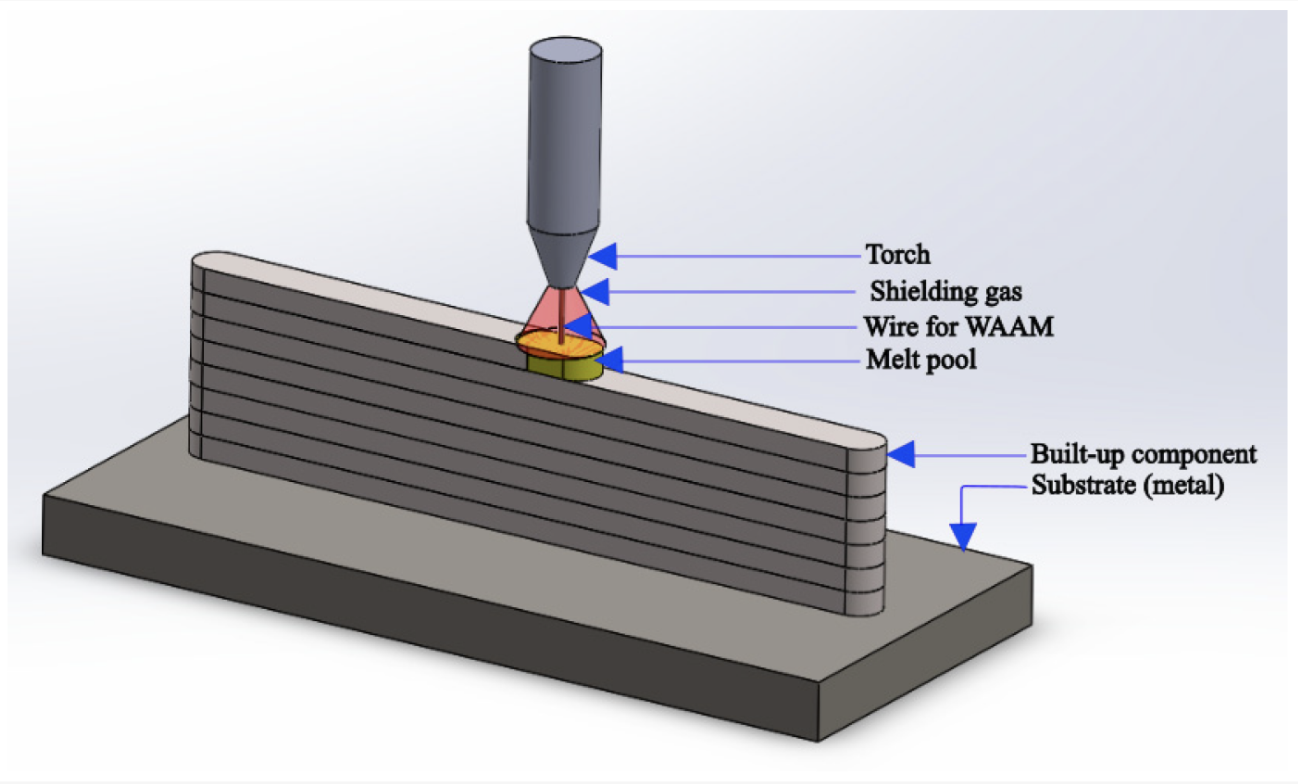
Source: mdpi.com
Uses an electric arc to melt metal wire, depositing it layer by layer onto the substrate. It’s similar to DED but typically uses metal wire instead of powder.
Cold Spray
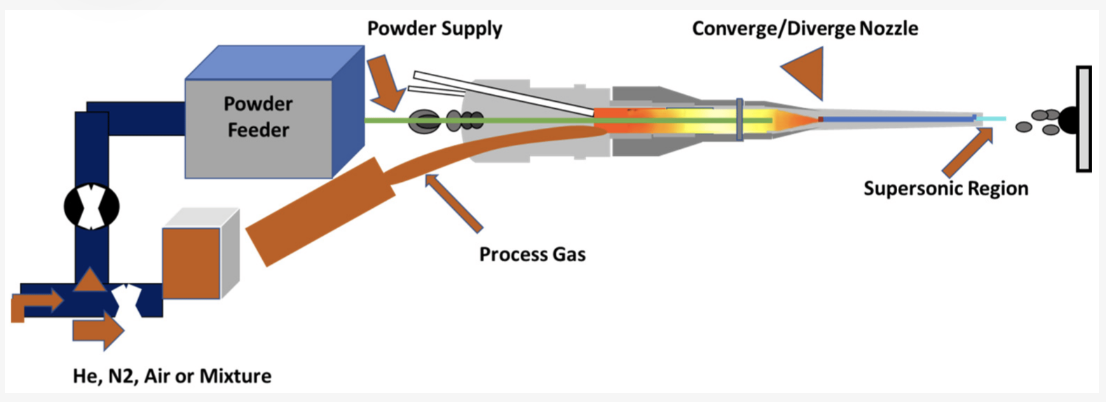
Source: mdpi.com
Uses high-pressure gas to accelerate metal powder particles to supersonic speeds, which impact and bond them onto a substrate without melting. It is ideal for surface coating and repair applications.
SLM vs. BJ vs. EBM vs. DED vs. WAAM vs. Cold Spray
Here's a comparative analysis of SLM, BJ, EBM, DED, WAAM, and Cold Spray for stainless steel printing across the specified dimensions:
Dimension | SLM | BJ | EBM | DED | WAAM | Cold Spray |
---|---|---|---|---|---|---|
Part Complexity | ⭐⭐⭐⭐⭐ | ⭐⭐⭐⭐ | ⭐⭐⭐⭐ | ⭐⭐⭐ | ⭐⭐ | ⭐⭐ |
Desired Strength | ⭐⭐⭐⭐⭐ | ⭐⭐⭐ | ⭐⭐⭐⭐ | ⭐⭐⭐⭐ | ⭐⭐⭐ | ⭐⭐ |
Surface Finish | ⭐⭐ | ⭐⭐⭐⭐ | ⭐⭐ | ⭐⭐ | ⭐ | ⭐⭐ |
Cost | ⭐⭐ | ⭐⭐⭐⭐ | ⭐⭐⭐ | ⭐⭐⭐⭐ | ⭐⭐⭐⭐ | ⭐⭐⭐ |
Speed | ⭐⭐⭐ | ⭐⭐⭐⭐ | ⭐⭐⭐ | ⭐⭐⭐⭐ | ⭐⭐⭐⭐⭐ | ⭐⭐⭐⭐ |
Post-Processing Complexity | ⭐⭐ | ⭐⭐⭐ | ⭐⭐ | ⭐⭐⭐ | ⭐⭐⭐⭐ | ⭐⭐⭐⭐ |
Sustain-ability | ⭐⭐⭐ | ⭐⭐⭐⭐⭐ | ⭐⭐⭐ | ⭐⭐⭐ | ⭐⭐⭐⭐ | ⭐⭐⭐ |
Batch Production Potential | ⭐⭐⭐ | ⭐⭐⭐⭐⭐ | ⭐⭐ | ⭐⭐⭐ | ⭐⭐⭐⭐ | ⭐⭐ |
Technology Maturity | ⭐⭐⭐⭐⭐ | ⭐⭐⭐ | ⭐⭐⭐⭐ | ⭐⭐⭐ | ⭐⭐ | ⭐⭐ |
Key Takeaways
SLM: Best for high-strength, complex parts with tight tolerances (e.g., medical implants).
Binder Jetting: Optimal for low-cost, high-volume production of less critical parts.
EBM: Balances strength and high-temperature performance (e.g., aerospace components).
DED: Best for repairing, large parts, and functional components that require high strength and fast deposition, but with lower surface finish and precision.
WAAM: Ideal for large, low-cost structures where surface finish is secondary.
Cold Spray: Specialized for repairs, coatings, or hybrid manufacturing.
Cost-saving Design Tips
Optimize Wall Thickness
Avoid Excessive Thickness: Keep walls at 1-2 mm to reduce material usage and printing time.
Uniform Thickness: Ensure consistent thickness to prevent warping or stress.
Minimize Support Structures
Design Self-Supporting Geometries: Use angles >45 degrees to reduce support material and labor.
Hollow Structures: Use hollow or lattice designs to save material while maintaining strength.
Simplify Complex Features
Reduce Overhangs/Undercuts: Simplify designs to minimize additional supports and post-processing.
Combine Parts: Print assemblies as a single part to cut fasteners and assembly time.
Use Tolerances Wisely
Avoid Tight Tolerances: Use standard tolerances to reduce printing time and avoid extra machining.
Account for Shrinkage: Design with shrinkage in mind to avoid reprints.
Reduce Post-Processing Needs
Smooth Surfaces: Design with smooth transitions to minimize sanding or polishing.
Avoid Small Features: Simplify intricate details to reduce finishing work.
Leverage Software Tools
Topology Optimization: Remove unnecessary material while maintaining strength, resulting in lighter, cost-effective parts.
Simulation Software: Use tools like finite element analysis (FEA) to test and optimize designs before printing, reducing failure risks.
If you want to calculate the 3d printing cost of your model, Unionfab’s free cost calculator is a good helper.
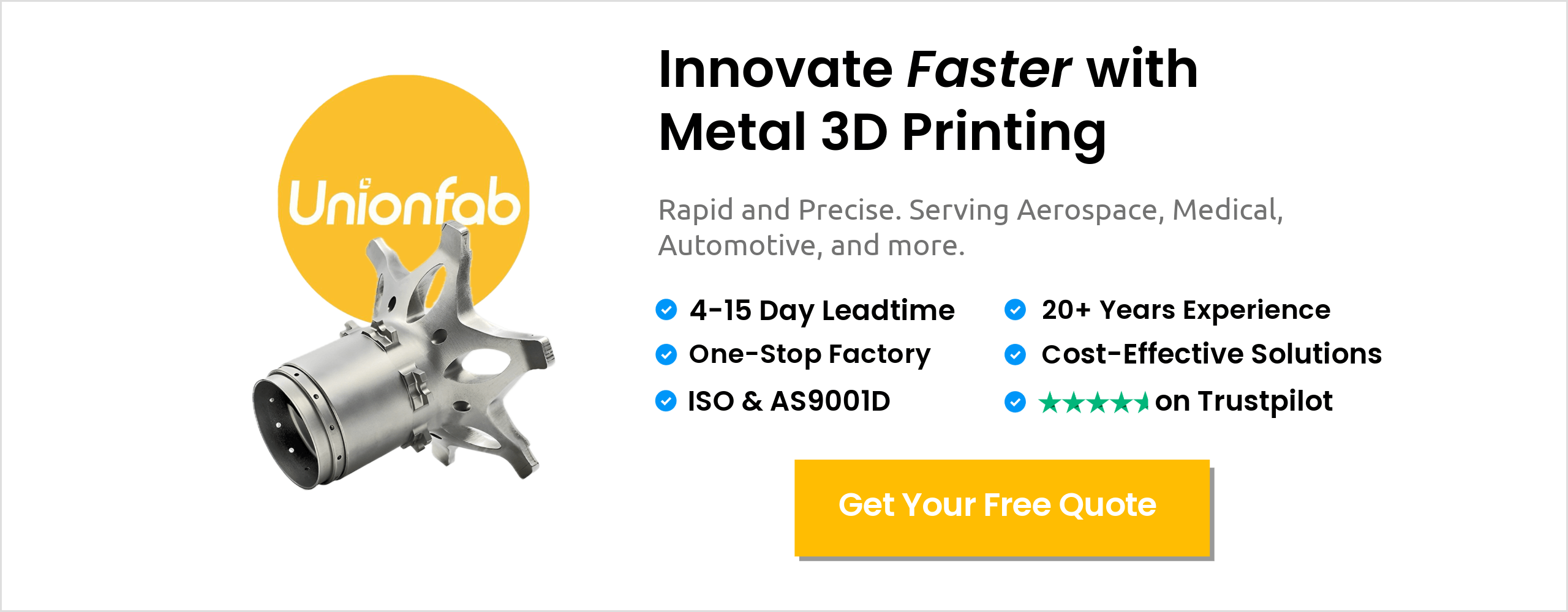
Industry-specific Applications of Stainless Steel 3D Printing
In 3D printing, stainless steel is applied across various industries thanks to its diverse performance advantages. Below, we will highlight its key application areas and explore the reasons for its widespread use in these fields.
1. Aerospace & Automotive
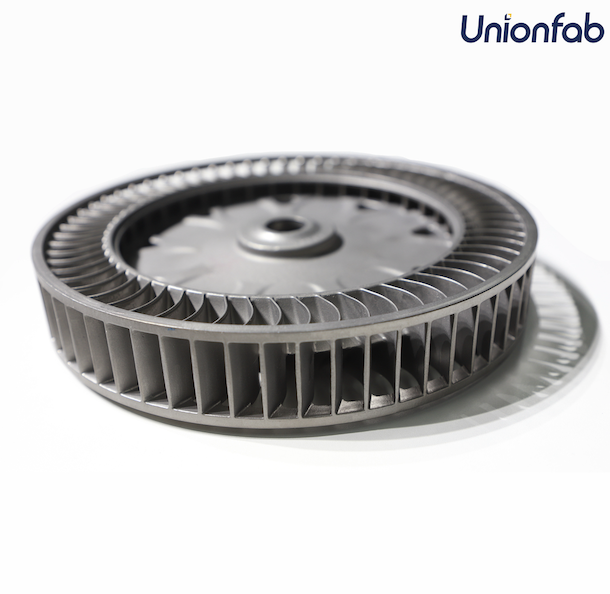
Key Properties: High strength-to-weight ratio, temperature and corrosion resistance.
Applications:
Aerospace: Engine components (turbine blades, fuel nozzles), structural parts (brackets, mounts), tooling (jigs, fixtures).
Automotive: Engine and exhaust components (manifolds, valves), custom parts (brackets, connectors), prototyping.
Why It’s Suitable: Stainless steel's strength and heat resistance are essential in both aerospace and automotive industries. 3D printing allows for the creation of intricate, lightweight designs, rapid prototyping, and reduced production costs.
2. Medical & Healthcare
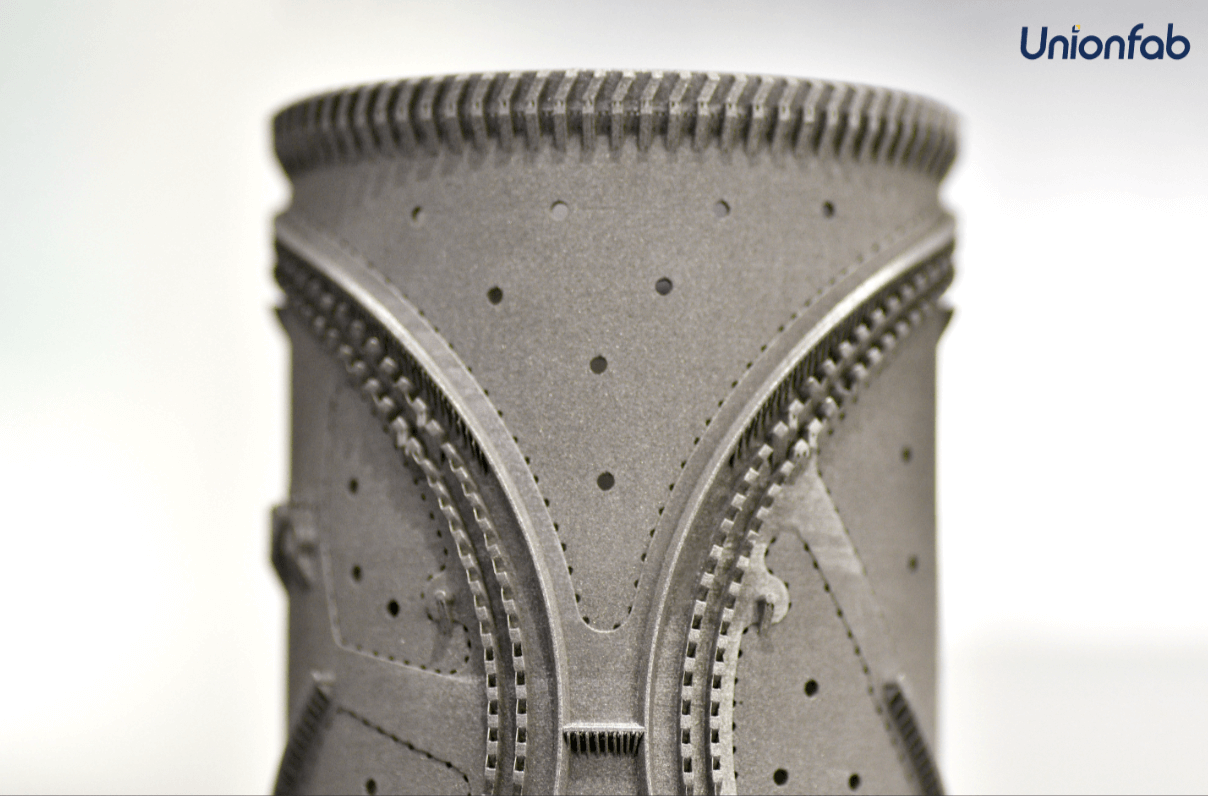
Key Properties: Biocompatibility, corrosion resistance, ease of fabrication.
Applications:
Medical Devices: Surgical instruments (scalpels, forceps), implants (orthopedic implants, dental crowns), diagnostic equipment components.
Why It’s Suitable: 316L stainless steel's biocompatibility and corrosion resistance make it ideal for medical applications. 3D printing provides the flexibility to create custom, patient-specific devices efficiently.
3. Oil, Gas & Industrial Manufacturing
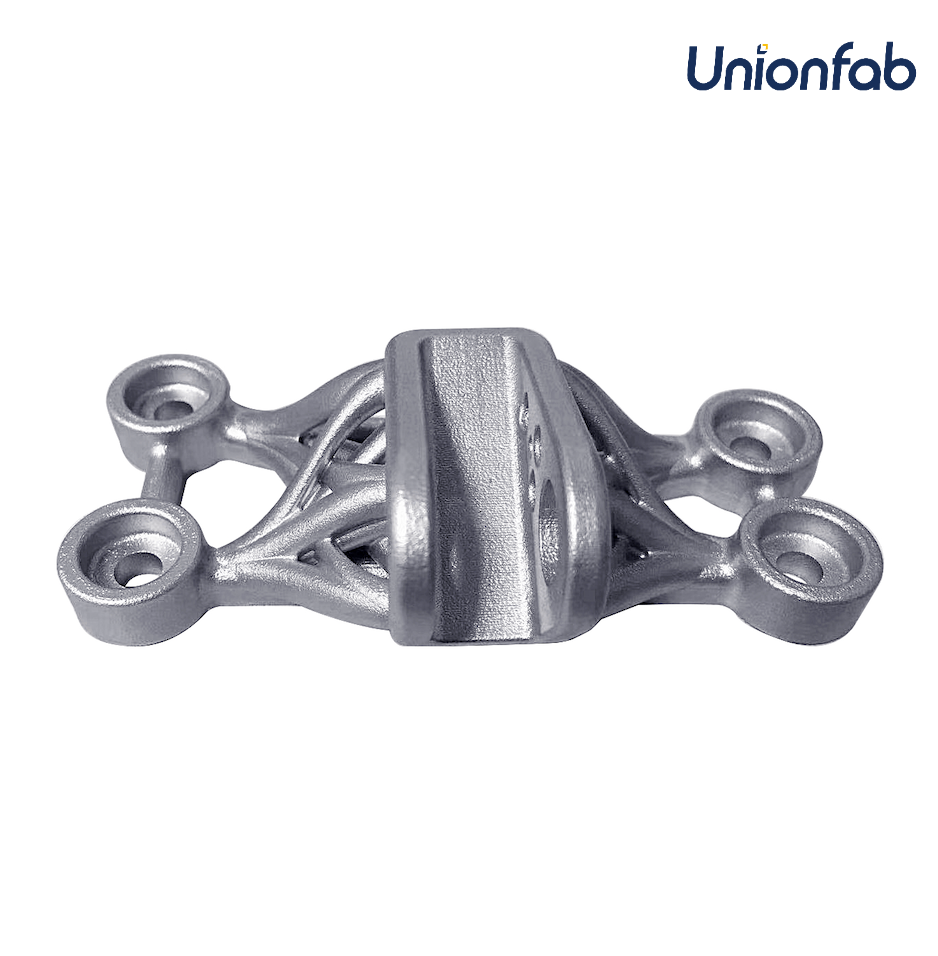
Key Properties: Corrosion resistance, strength, wear resistance.
Applications:
Oil & Gas: Drilling equipment (valves, pumps), pipeline components (fittings, connectors), tooling (wear-resistant tools).
Industrial Manufacturing: Machinery components (gears, bearings), tooling (molds, jigs), wear-resistant parts (conveyor belts, cutting tools).
Why It’s Suitable: Stainless steel's durability in harsh environments ensures reliability in oil, gas, and industrial manufacturing. 3D printing enables the production of custom parts on-demand, improving efficiency, reducing downtime, and cutting inventory costs.
4. Food, Beverage & Consumer Goods
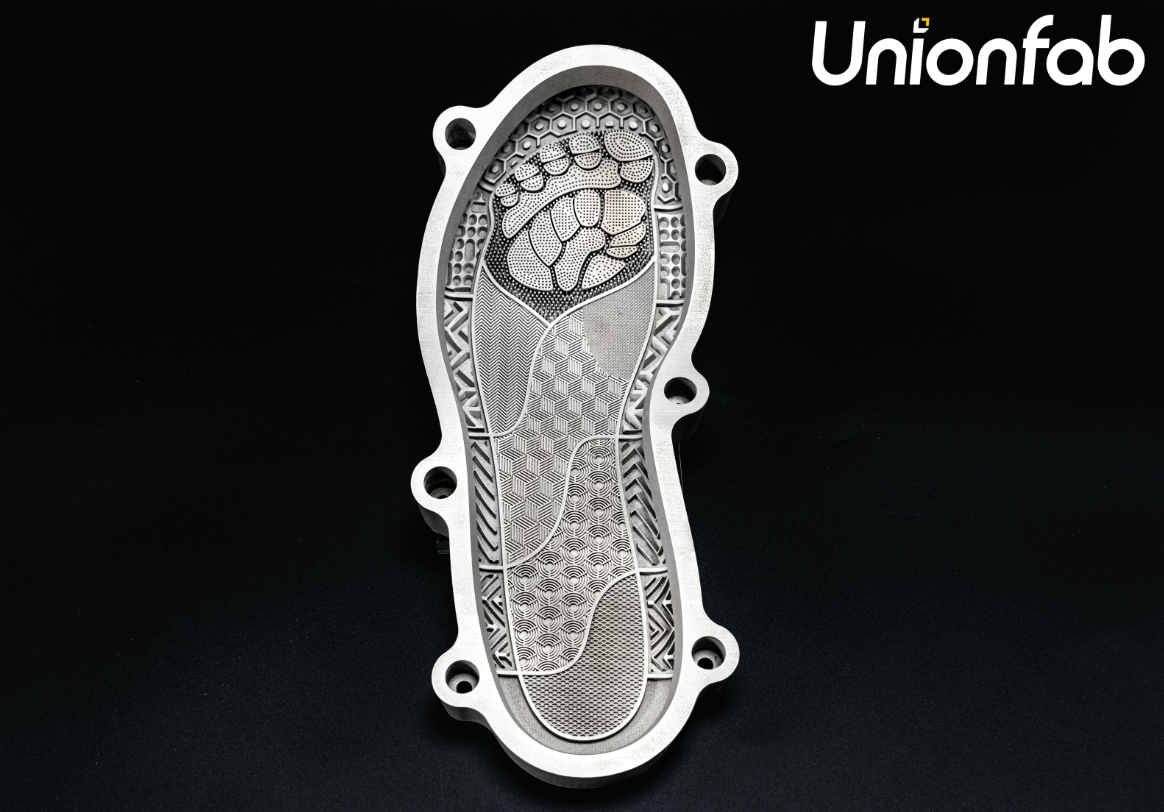
Key Properties: Corrosion resistance, ease of cleaning, strength.
Applications:
Food & Beverage: Processing equipment (mixers, conveyors), custom fixtures (nozzles, molds), tooling (maintenance parts).
Consumer Goods: Wearables (watch cases, jewelry), electronics housings (custom enclosures), custom tools (household gadgets).
Why It’s Suitable: Stainless steel's resistance to corrosion, ease of cleaning, and aesthetic appeal make it ideal for both food-grade applications and consumer goods. 3D printing allows for the rapid creation of custom components with high precision.
Comparison of Key Stainless Steel 3D Printing Service Providers
To help you choose the most suitable service provider based on your needs, we have listed a table to compare several key stainless steel 3D printing service providers as follows.
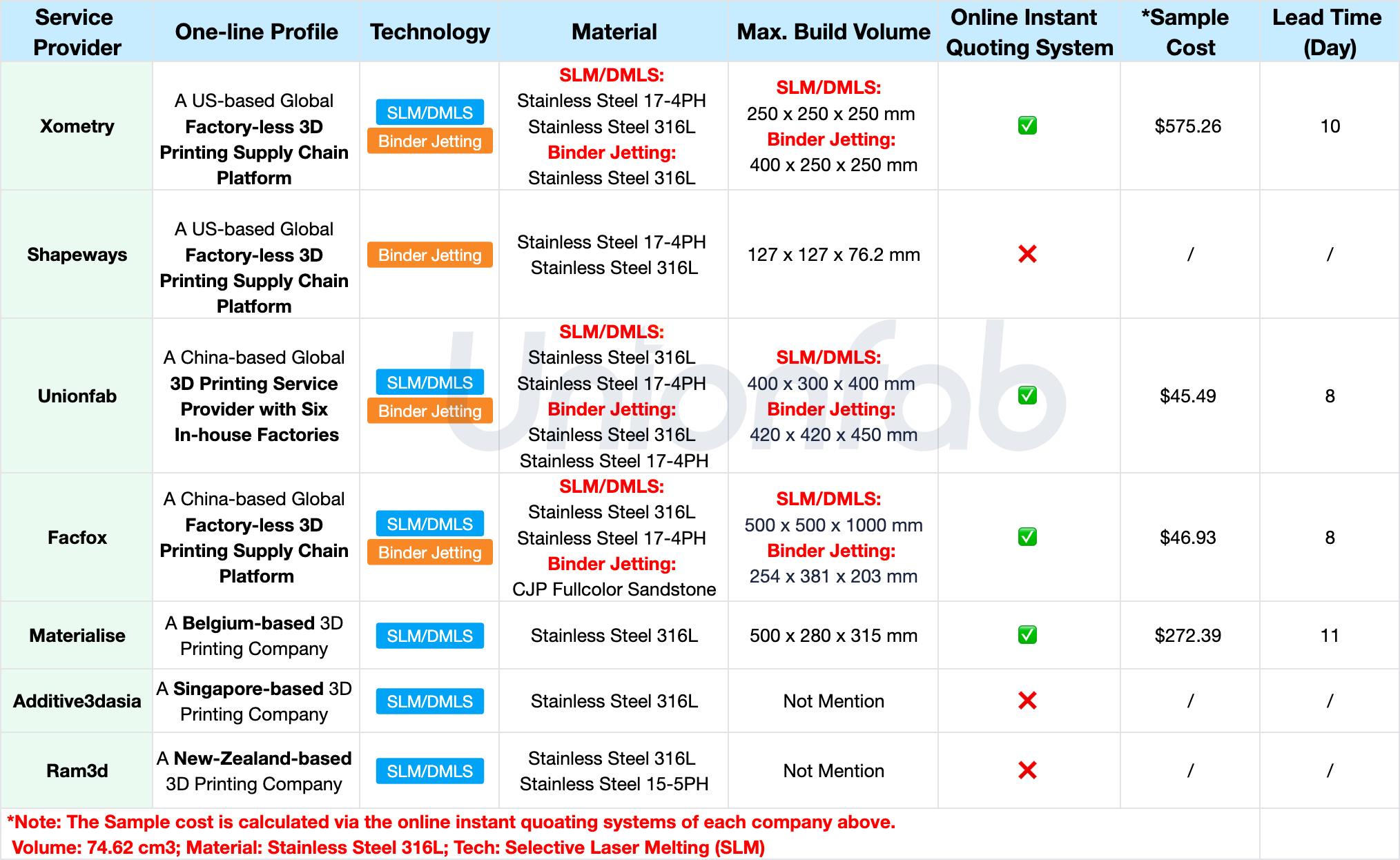
In summary,
Xometry, Unionfab and Facfox provide both SLM and Binder Jetting technologies, as well as richer materials compared to others competitors.
Facfox provides the largest build volume using SLM, while Unionfab provides the largest build volume using Binder Jetting.
Xometry, Unionfab and Facfox have higher ratings on Trustpilot where real customer feedbacks can be found.
Make Your Design a Reality with Unionfab
With 20+ years of expertise, 1,000+ industrial 3D printers, and 6 cutting-edge factories, Unionfab, certified with ISO 9001, ISO 13485, and AS 9001D, is committed to delivering high-quality, cost-effective 3D printing services. The followings are the details of our stainless steel 3d printing service.
SLM/DMLS | Binder Jetting | |
---|---|---|
Equipment | 100+: BLT; SLM; EOS; EXONE | 10+: HP S100 |
Materials | Stainless Steel 316L Stainless Steel 17-4PH | Stainless Steel 316L |
Max Part Size | 400 x 300 x 400mm | 420 x 420 x 450mm |
Layer Thickness | 0.035 mm | 0.035 mm |
Tolerance | ±0.2 mm | ±0.2 mm |
Min. Wall Thickness | 0.5 mm | 0.5 mm |
Min. Reference Unit Price | SS 316L: $0.4/g | SS 316L: $0.4/g |
Pass Rate | 99.5% | 99.5% |
Lead Time | 8 Days | 8 Days |
On-time Delivery Rate | 98% | 98% |
*The actual unit price is subject to real-time inquiry.
Post Processing
We not only provide cost-effective stainless steel 3d printing but also a range of post-processing options below, including sandblasting, electroplating, and polishing etc., to improve surface quality, durability, and aesthetics of the prints, ensuring the perfect fit for your diverse needs.
![]() | ![]() | ![]() | ![]() | ![]() |
---|---|---|---|---|
![]() | ![]() | ![]() | ![]() | ![]() |
![]() | ![]() | ![]() | ![]() | ![]() |
QA Report
In addition to delivering cost-effective prints, we also offer quality assurance services and can send the QA report with the shipment. Btw, if you haven’t used Unionfab’s 3d printing service yet, sign up now to get a 10% discount on your first order!
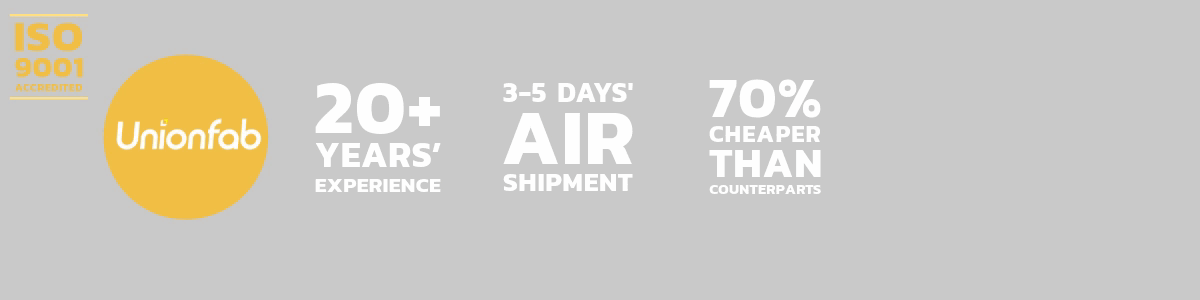
Customer Review
See real customer review from Trustpilot:
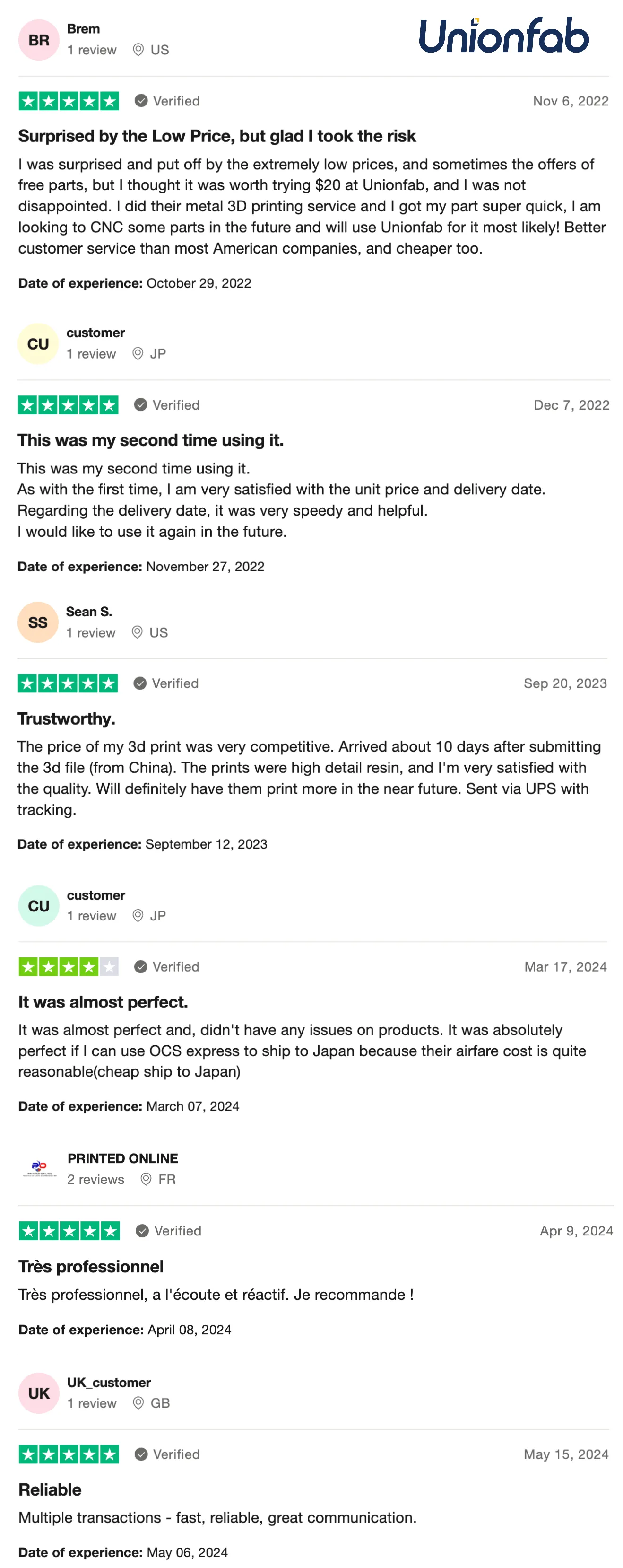