ABS Injection Molding: Everything You Need to Know
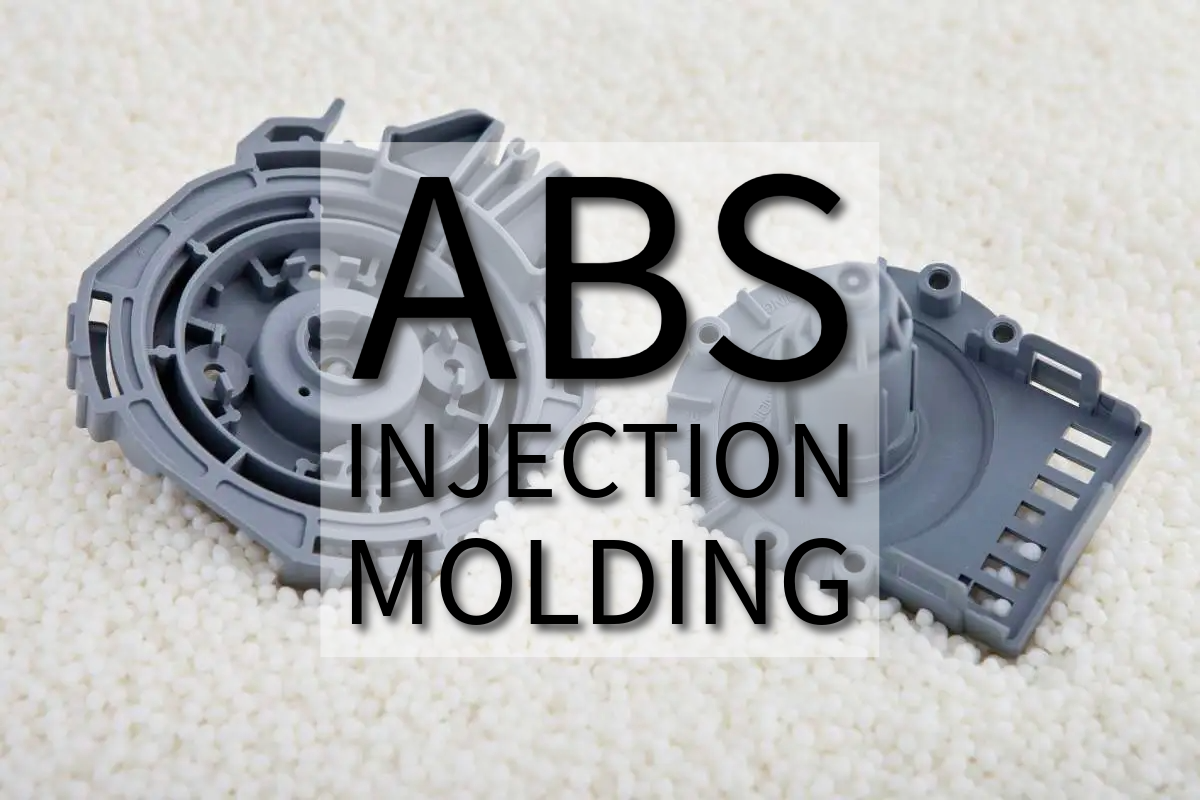
Learn why ABS is the material of choice for injection molding, its applications, and how to optimize the process for high-quality parts.
Introduction
ABS is one of the most commonly used thermoplastics in injection molding due to its unique properties like toughness, durability, and ease of processing.
This guide will walk you through the ABS injection molding process, its advantages, limitations, and considerations for achieving optimal results.
What is ABS Injection Molding?
ABS Injection Molding is a manufacturing process that involves injecting molten ABS plastic into a mold to create complex shapes and components.
ABS is a versatile material known for its strength, impact resistance, and heat stability, making it ideal for a range of industrial and consumer products.
ABS injection molding is a widely used manufacturing process for creating a variety of products, including automotive components, consumer electronics, toys, plumbing fixtures, and household appliances.
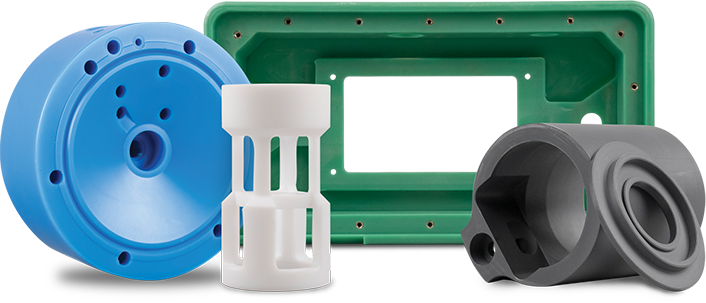
Source: jacoproducts.com
ABS Injection Molding Process
The ABS injection molding process consists of several key steps to ensure high-quality parts:
Material Preparation: ABS pellets are dried to remove moisture, as any trapped water can cause defects in the final part.
Molding Machine Setup: Machine settings such as temperature, pressure, and injection speed are calibrated based on ABS’s specific characteristics.
Injection Phase: The molten ABS is injected into the mold cavity under controlled pressure to fill all the intricate details of the mold.
Cooling and Solidification: Cooling rates are carefully controlled to allow the material to solidify evenly, which helps in achieving structural integrity.
Ejection: Once the part has cooled and solidified, it is ejected from the mold using ejector pins or other mechanical methods.
Post-Processing: Additional processes like trimming excess material, painting, or applying surface finishes are done to achieve the desired aesthetic or functional qualities.
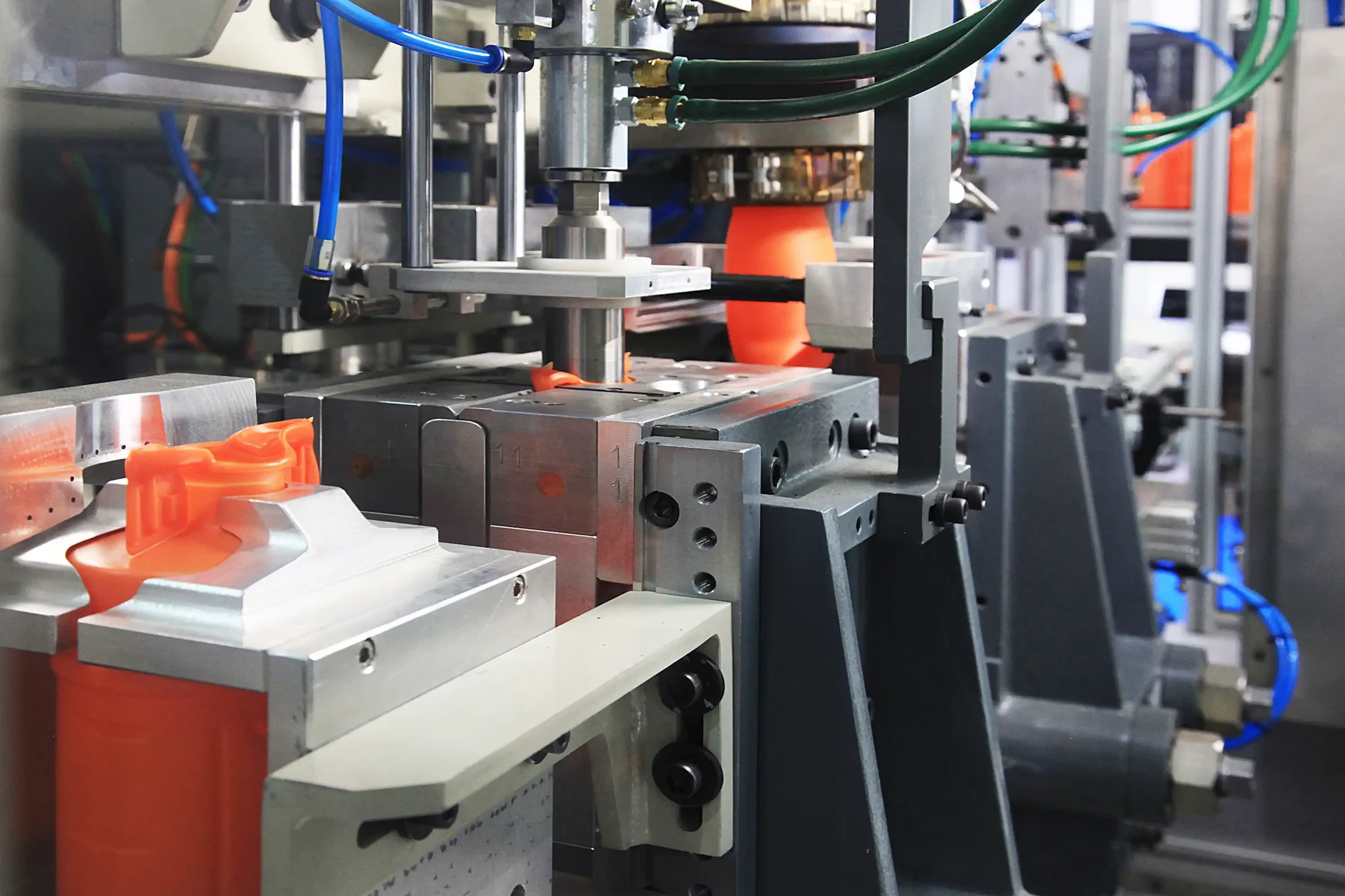
Source: acomold.com
Common Applications of ABS Injection Molding
The common applications of ABS injection molding span various industries:
Automotive Parts
ABS is widely used in automotive manufacturing for parts like dashboards, interior trim, mirror housings, and body panels because of its strong impact resistance and durability.
Consumer Electronics
ABS is a popular material for cases and enclosures for phones, laptops, computer keyboards, and other electronic devices.
Its ability to be molded into intricate shapes with a smooth finish makes it ideal for this application.
Household Appliances
Many kitchen and home appliances like vacuum cleaners, mixers, and washing machine parts are made using ABS due to its toughness and resistance to wear and tear.
Toys
ABS is widely used in the toy industry because it is safe, lightweight, and can withstand rough handling. LEGO bricks, for example, are made from ABS plastic.
Medical Devices
ABS is used to create enclosures and components for medical instruments and devices, as it is easy to sterilize and mold into precise shapes.
Industrial Equipment
ABS is also used in various industrial machinery components due to its mechanical strength and resilience.
3D Printing Filaments
ABS is one of the most common materials used for 3D printing, valued for its strength, flexibility, and the ease with which it can be shaped.
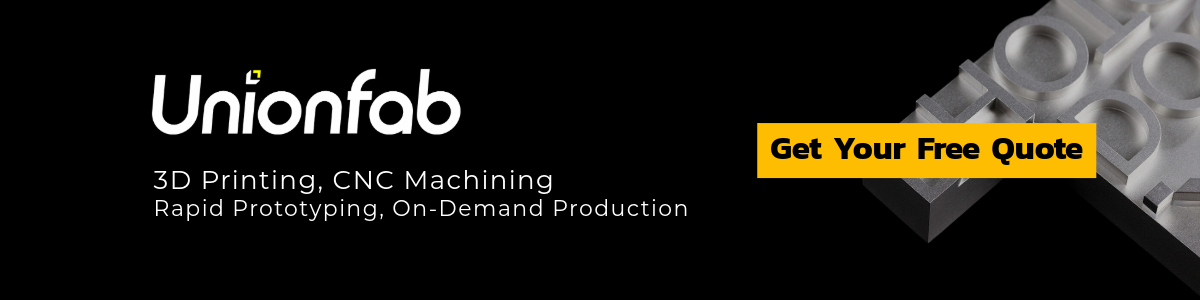
Benefits of ABS Injection Molding
ABS molding offers several benefits over alternative fabrication methods:
Durability: ABS is known for its toughness and ability to withstand mechanical stress, making it ideal for applications requiring strength and impact resistance.
Ease of Processing: ABS has excellent flow characteristics, allowing it to be easily molded into complex shapes with fine details. This makes it suitable for intricate designs and components.
Aesthetic Flexibility: ABS can be easily colored, painted, or textured to create visually appealing products. It also supports various surface finishes, from matte to high gloss.
Cost-Effectiveness: Compared to other engineering plastics, ABS is relatively affordable while providing a good balance of strength and aesthetic quality. This makes it a cost-efficient option for high-volume production.
Chemical Resistance: While not as chemically resistant as some other plastics, ABS can withstand exposure to a range of common substances, including acids and alkalis.
Recyclability: ABS can be recycled, making it an environmentally-friendly choice for many manufacturers looking to reduce waste.
Limitations of ABS Injection Molding
While ABS injection molding provides manufacturing advantages, the material does have some limitations:
Lower heat deflection: ABS has a heat deflection temperature of only around 90°C, limiting its use in high-heat applications.
Prone to stress cracks: ABS can develop surface cracks if subjected to permanent bending stresses over a period.
Poor chemical resistance: ABS degrades when exposed to certain petroleum-based solvents and chlorinated hydrocarbons.
Moisture absorption: ABS absorbs up to 2% moisture when exposed to humid environments.
High mold wear: The abrasive fillers in ABS wear out molds faster than other plastics like PVC.
Difficult to glue and weld: Joining molded ABS parts requires special adhesives unlike applications with PVC or nylon.
Tips for Optimizing the ABS Injection Molding Process
Here are the key tips for optimizing the ABS injection molding process:
Proper Material Drying: Dry the ABS pellets thoroughly before molding to prevent moisture-related defects.
Precision Mold Design: Design molds with proper draft angles, wall thickness, and venting to avoid common defects like warping, short shots, or flash.
Temperature Control: Precisely control barrel and mold temperatures for smooth melting and filling without burning or voids.
Injection Speed and Pressure: Adjust injection speed and pressure for defect-free filling of fine details at an even flow front.
Cycle Time: Efficient cycle times are key to maximizing productivity, but need to be balanced with cooling rates to maintain part quality.
Cooling Rate Optimization: Control cooling evenly to prevent warping or shrinkage from uneven stresses within the part.
Shrinkage Management: Understanding the material's shrinkage helps design the mold cavity to ensure accurate final product dimensions.
Quality Control Checks: Conduct quality checks throughout to quickly find and fix issues for consistency.
ABS Injection Molding vs. Other Plastics
ABS is often compared to other plastics like polypropylene (PP), nylon, and PVC that are also widely used in injection molding.
PP is less dense and more flexible than ABS. It has better chemical resistance but lower impact strength. PP is cheaper than ABS and preferred for non-structural parts.
Nylon has better mechanical properties, rigidity and dimensional stability than ABS but is more expensive. It is more suitable than ABS for applications requiring heat resistance or strength.
PVC is lighter and more flexibly than ABS. It has good resistance to acids and alkalis but poor performance at low and high temperatures. PVC parts tend to wear quicker than ABS.
Conclusion
ABS injection molding is a effective manufacturing process that offers many benefits, particularly for industries requiring durable and detailed parts.
By understanding the material’s properties and optimizing the molding process, manufacturers can produce high-quality ABS parts consistently and efficiently.
Unionfab
Unionfab provides expert solutions for ABS injection molding, with a focus on delivering high-quality, precise, and durable parts for a wide range of applications.
FAQs
What is ABS Injection Molding used for?
ABS is used in automotive, electronics, toys, and medical devices, among other industries.
How durable is ABS compared to other plastics?
ABS is highly durable and impact-resistant, making it suitable for products that undergo mechanical stress.
What are the common challenges in ABS injection molding?
Common challenges include managing shrinkage, ensuring a consistent cooling rate, and achieving smooth surface finishes.
How can I improve the surface finish of ABS molded parts?
Improving the surface finish can involve post-processing techniques like sanding, polishing, or applying specialized coatings.