Anodized Blue: A Comprehensive Guide
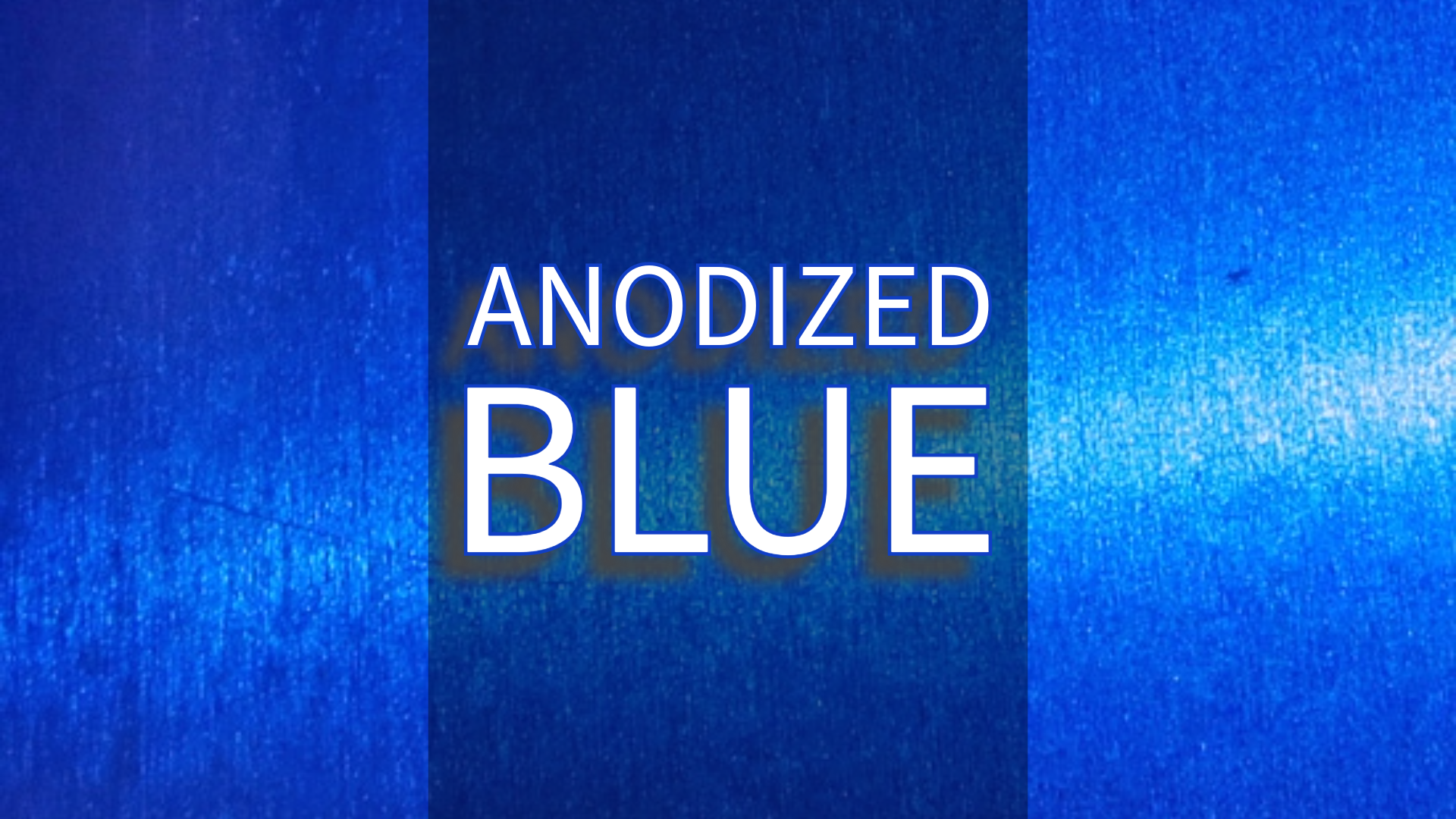
Discover the process behind anodized blue and explore various applications and advantages of this great finishing.
Introduction
Anodized blue is a specialized finishing process that imbues metal surfaces with a vibrant blue color while enhancing their durability and resistance to corrosion.
In this comprehensive guide, we delve into the intricacies of anodized blue, exploring its properties, the science behind its formation, the process involved, its advantages, applications, and more.
Understanding Anodized Blue
What is Anodized Blue
Anodized blue is a finishing technique that uses an electrochemical process called anodization to create a vibrant blue hue on metal surfaces.
Through immersion in an electrolytic solution and the application of an electric current, a protective oxide layer forms on the metal, which is then dyed blue. This enhances both the aesthetic appeal and performance of the metal.
Properties of Anodized Blue
Anodized blue surfaces exhibit several desirable properties that make them highly sought after in various industries:
Corrosion Resistance: The protective oxide layer formed during anodization acts as a barrier against corrosion, protecting the underlying metal from environmental elements such as moisture, chemicals, and salt spray.
Durability: Anodized blue coatings are exceptionally durable, and capable of withstanding abrasion, wear, and impact better than many other surface finishing options. This durability ensures the longevity of the metal object, even in demanding applications.
Visual Appearance: The vibrant blue color of anodized coatings adds a striking visual element to the metal surface, enhancing its aesthetic appeal and making it stand out among other finishes.
Comparison with Other Finishes
Comparison Aspect | Anodized Blue | Traditional Methods |
---|---|---|
Penetration and Bonding | Penetrates, Strong Bond | Surface Coating |
Durability and Resilience | Highly Durable, Resilient | Prone to Wear, Corrosion |
Environmental Considerations | Environmentally Friendly, Minimal Waste | Hazardous Chemicals, More Waste |
Anodized Blue Compare with Other Finishes
Penetration and Bonding: Unlike traditional coatings that merely sit atop the metal surface, anodized blue penetrates the metal's oxide layer, creating a strong bond that is resistant to fading, chipping, and peeling. This ensures that the blue color remains vibrant and intact for an extended period.
Durability and Resilience: Anodized blue coatings are more durable and resilient than many paint or powder coat finishes. The oxide layer formed during anodization provides an additional layer of protection against corrosion and wear, resulting in a longer-lasting finish.
Environmental Considerations: Anodized blue coatings are also more environmentally friendly than some traditional painting methods, as they produce minimal waste and utilize non-toxic materials. This makes them a preferred choice for eco-conscious consumers and industries.
Overall, anodized blue stands out as a superior finishing option for metal objects, offering unparalleled durability, color retention, and aesthetic appeal compared to traditional coating methods.
Science Behind Blue Anodized Coatings
Anodization Process
Anodization involves immersing a metal substrate in an electrolytic solution and passing an electric current through it. This electrical current stimulates an oxidation reaction at the metal's surface, resulting in the formation of a thin, protective oxide layer. This oxide layer is crucial for both the durability and coloration of the finished product.
Chemical Composition and Color Formation
The vibrant blue color in anodized coatings is achieved through the application of organic or inorganic dyes during the anodization process. These dyes are carefully selected for their ability to bond with the porous oxide layer formed on the metal's surface. By impregnating the oxide layer with these dyes, a rich and long-lasting blue hue is achieved.
Role of Oxide Layers
The oxide layer formed during anodization plays a dual role in the coloring process. Firstly, it acts as a protective barrier, shielding the underlying metal from corrosion and environmental damage. Secondly, the porous nature of the oxide layer allows the applied dyes to penetrate and bond with the metal substrate. This ensures that the blue coloration is deeply integrated into the surface, providing both colorfastness and durability over time.
Process of Anodized Blue Paint
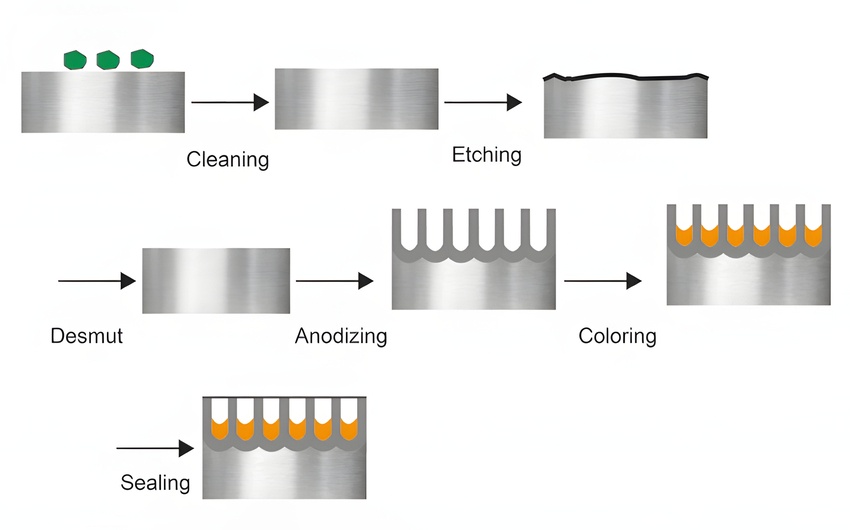
Source: at-machining.com
Preparation of Metal Surface
Before anodization, meticulous preparation of the metal surface is essential. Any impurities or contaminants must be thoroughly removed through cleaning and pre-treatment processes. This ensures optimal adhesion of the subsequent oxide layer and promotes uniform coloration during the anodizing process.
Anodizing
During the anodizing stage, the prepared metal substrate is immersed in an electrolytic bath and subjected to an electric current. This electrical current triggers an oxidation reaction at the surface of the metal, leading to the formation of a thin but resilient oxide layer. This layer serves as the foundation for the subsequent coloring process.
Coloring
Once the oxide layer has been established, the metal is ready for coloring. It is immersed in a dye solution, specially formulated to bond with the porous structure of the oxide layer.
The dye penetrates deeply into the oxide layer, ensuring a vibrant and long-lasting blue hue. This step is crucial for achieving the desired aesthetic appearance of the finished product.
Sealing
The metal undergoes a sealing process to enhance durability and longevity. A sealing agent, like hot water or chemicals, closes pores within the oxide layer, protecting against corrosion and abrasion. This maintains the vibrant color and appearance of the anodized blue finish.
Advantages of Anodized Blue
Durability and Corrosion Resistance
Anodized blue coatings offer exceptional protection against corrosion, weathering, and abrasion. This ensures the longevity and performance of the underlying metal substrate, making anodized blue ideal for applications where durability is paramount.
Environmental Sustainability
The anodization process is inherently environmentally friendly. It produces minimal waste and utilizes non-toxic materials, reducing its impact on the environment. Additionally, the durability of anodized coatings decreases the need for frequent maintenance or replacement, further minimizing environmental strain.
Design Flexibility
Anodized blue coatings provide designers and manufacturers with a wide range of color options, enabling creative expression and customization while preserving the inherent qualities of the metal substrate. This versatility allows for the creation of visually striking and unique products across various industries.
Visual Effects
The vibrant blue color of anodized coatings adds visual appeal to a diverse array of products and applications. This enhances their aesthetic value and marketability, making them stand out in the marketplace and appealing to consumers seeking visually striking and attractive products.
Low Maintenance Requirements
Thanks to their exceptional durability and resistance to fading or chipping, anodized blue coatings require minimal maintenance. This saves both time and resources over the lifespan of the finished product, making anodized blue a cost-effective and practical choice for a wide range of applications.
Applications of Anodized Blue
Anodized blue coatings find widespread use across various industries, owing to their durability, aesthetic appeal, and corrosion resistance. Some prominent applications include:
Consumer Electronics
In the realm of consumer electronics, anodized blue coatings are utilized in a myriad of products such as mobile devices, laptops, and appliances. The vibrant blue finish adds a touch of sophistication and modernity to these devices, enhancing their visual appeal and distinguishing them in a competitive market.
Automotive Industry
Within the automotive industry, anodized blue coatings are employed for trim, accents, and custom detailing. Whether adorning exterior components or accentuating interior features, the striking blue hue adds a touch of elegance and personality to vehicles, making them stand out on the road.
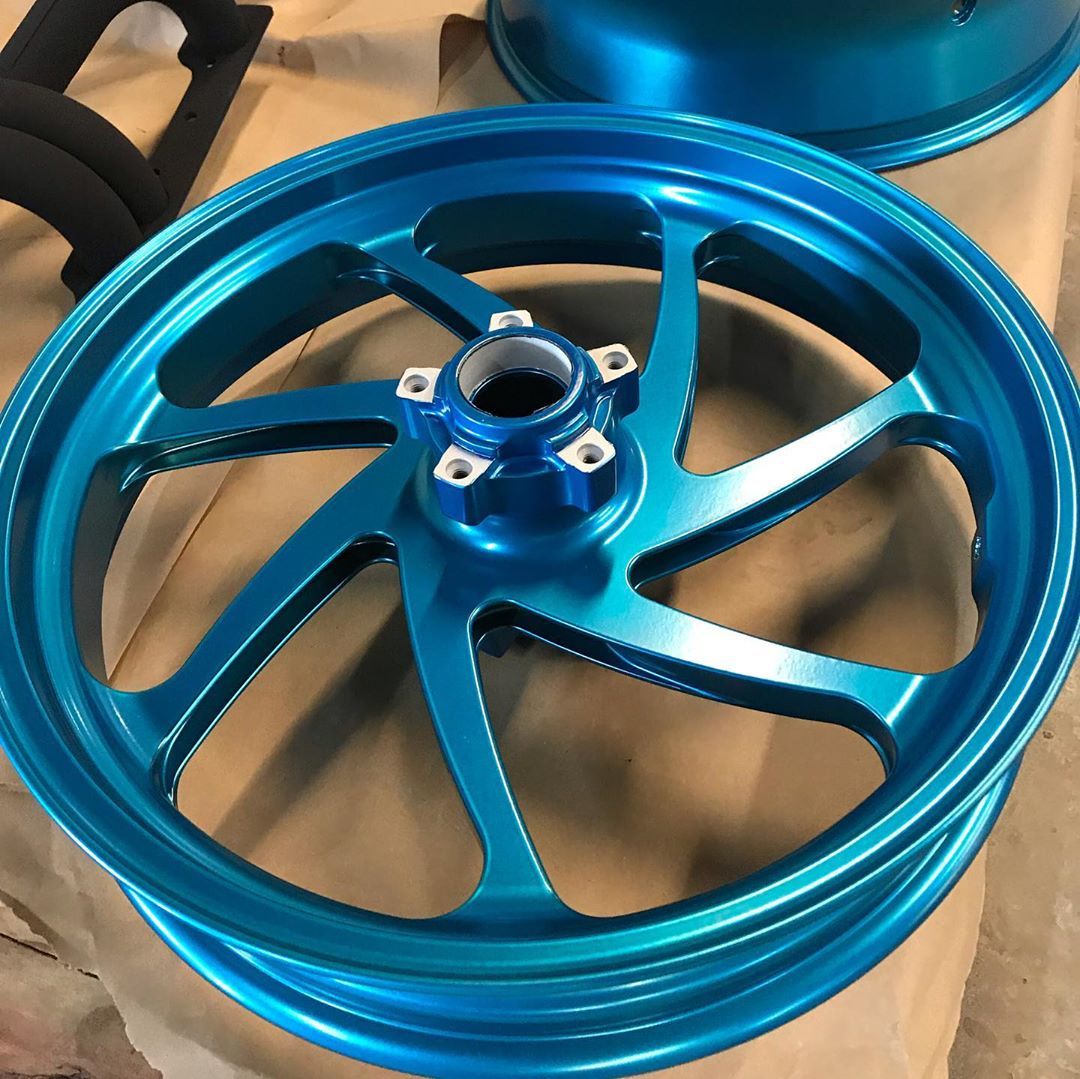
Source: tobegoodov.shop
Architectural Uses
Anodized blue coatings play a vital role in architectural applications, where they are used for building facades, window frames, and decorative elements. The durable and weather-resistant nature of these coatings makes them ideal for enhancing the aesthetic appeal and longevity of architectural structures.
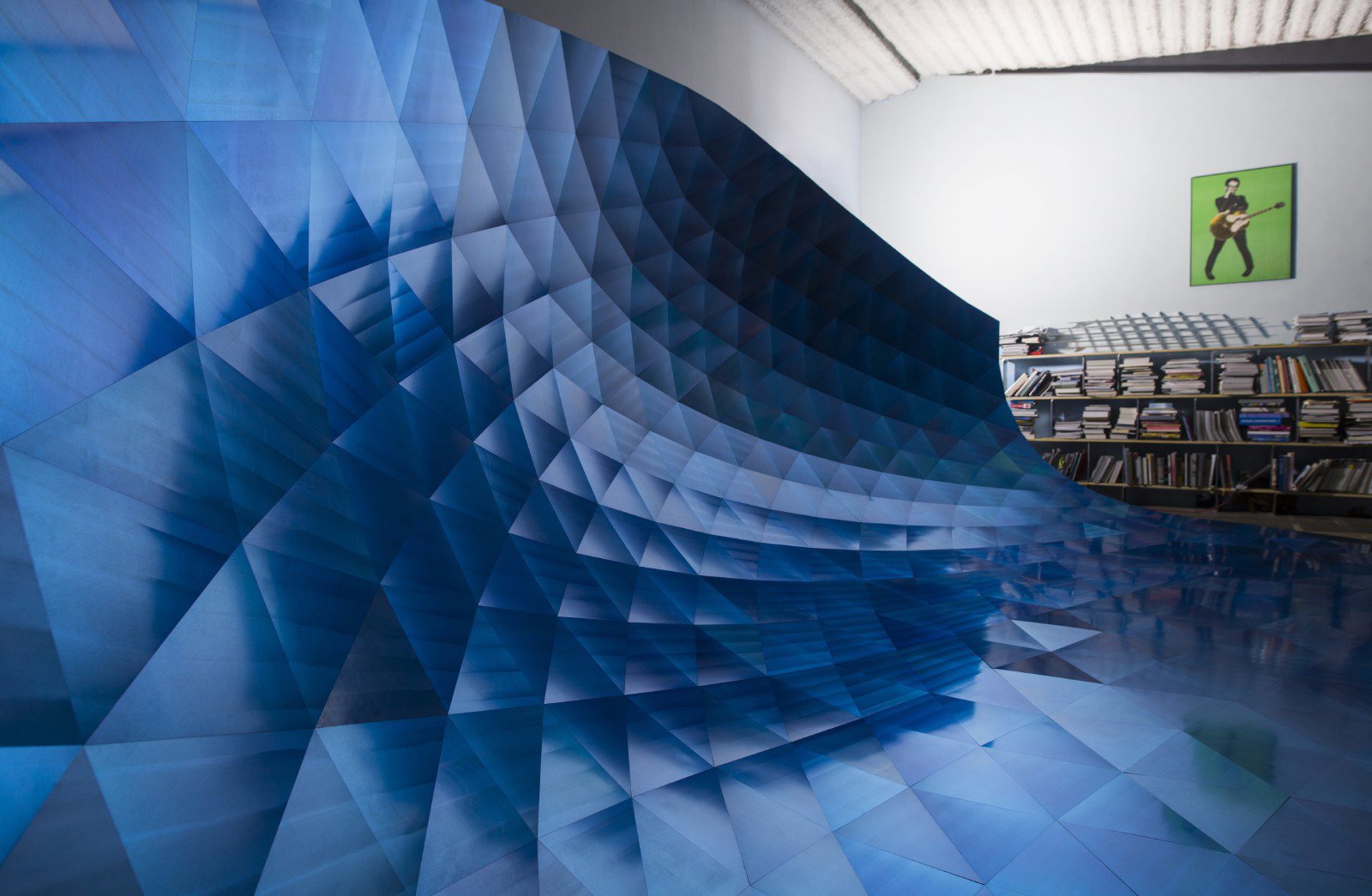
Source: shapesbyhydro.com
Sporting Goods
In the realm of sporting goods, anodized blue coatings are employed in the manufacturing of bicycles, firearms, and recreational equipment. The vibrant blue finish not only enhances the visual appeal of these products but also provides a durable and corrosion-resistant surface that withstands the rigors of outdoor activities.
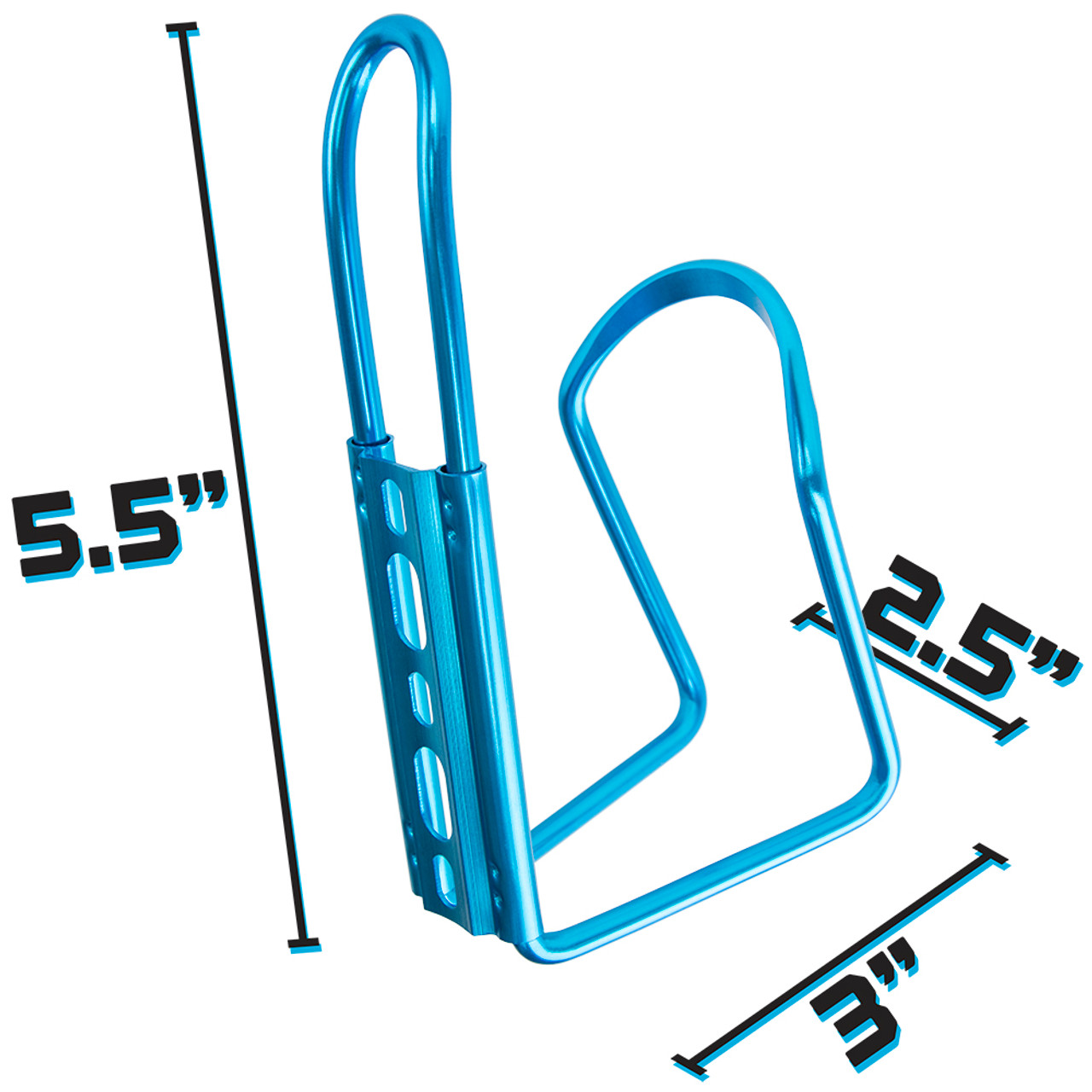
Source: hobbymonsters.com
Aerospace Industry
Within the aerospace industry, anodized blue coatings find application in aircraft components, interior fittings, and structural elements. The corrosion resistance and lightweight properties of these coatings make them well-suited for aerospace applications, where durability and performance are critical considerations.
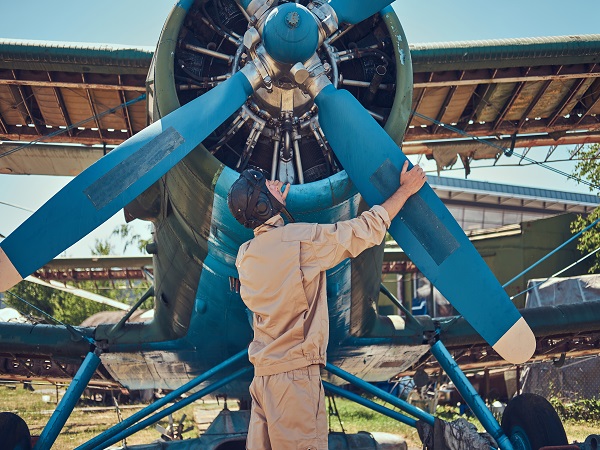
Source: hpipro.com
Conclusion
Anodized blue coatings offer a winning combination of aesthetic appeal, durability, and performance, making them an ideal choice for a wide range of applications.
Whether in consumer electronics, automotive design, architecture, sports equipment, or aerospace technology, anodized blue provides a flawless finishing touch that stands the test of time.
Achieve Flawless Finishing at Unionfab
For impeccable anodized blue coatings and expert finishing services, trust Unionfab to deliver superior results that meet your exacting standards.
Contact us today to learn more about our comprehensive range of metal finishing solutions.
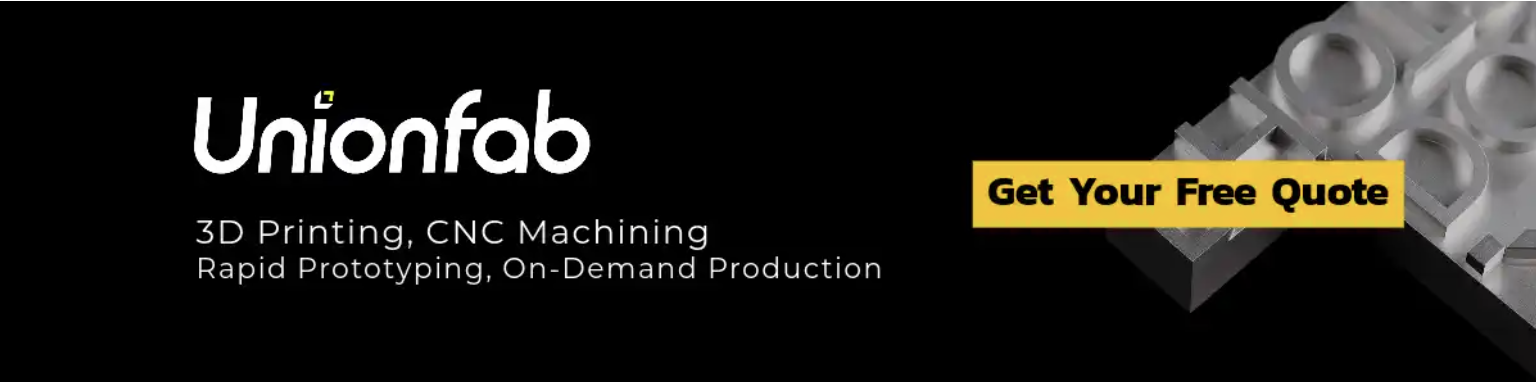