Living Hinge: Creating Flexible Parts
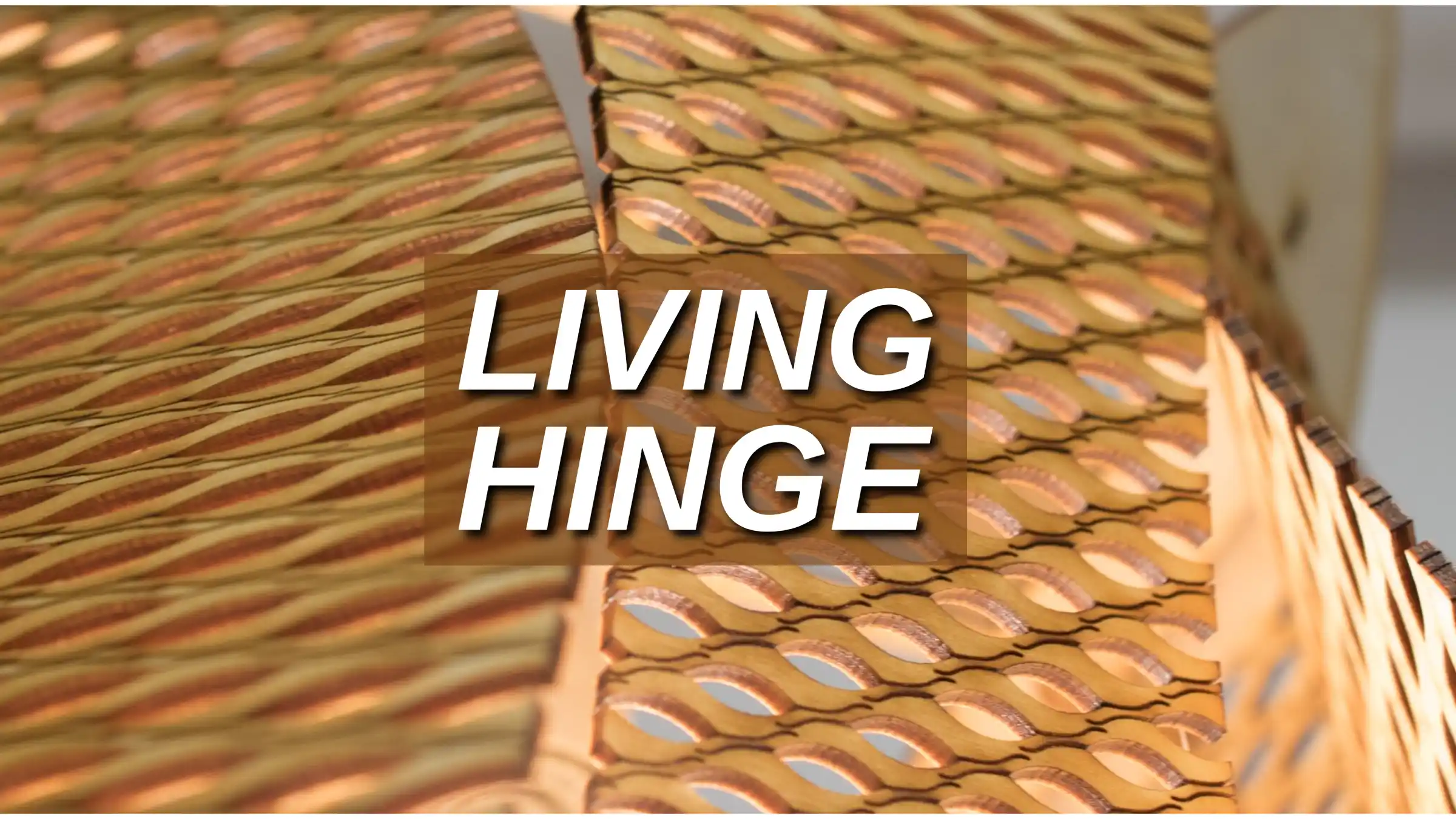
This article explores the concept of living hinges, including their design principles, benefits and applications.
Introduction
Living hinges are thin, flexible sections of material, typically plastic, that connect two rigid parts, allowing them to bend or flex without breaking.
These hinges are integral to the part, eliminating the need for separate hinge components, making them a popular choice in various industries.
Understanding Living Hinge
Definition of Living Hinge
A living hinge is a thin, flexible hinge made from the same material as the adjoining rigid parts, enabling repeated bending and flexing without failure. Typically manufactured from plastic, living hinges are designed to last through thousands of cycles without breaking.
This integral hinge is created during the molding process, resulting in a seamless and continuous piece that includes both the hinge and the rigid sections it connects.
Advantages and Challenges of Living Hing
Advantages
Flexibility and Elasticity: An effective living hinge must bend repeatedly without fracturing, made possible by materials with high elongation properties. This flexibility ensures the hinge can stretch and bend while returning to its original shape, maintaining functionality throughout its lifespan.
Durability: Living hinges should endure thousands to millions of flex cycles without significant wear or failure. This durability is essential for applications that require frequent use, ensuring long-lasting performance.
Uniform Thickness: Consistent thinness across the hinge ensures even stress distribution during bending, reducing the risk of cracking or failure. This uniformity is crucial for the hinge's structural integrity and reliability.
Cost-Effective and Simplified Assembly: Living hinges eliminate the need for additional components, reducing material and assembly costs. Their integral design streamlines the manufacturing process and simplifies assembly, particularly advantageous in high-volume production.
Compact Design: Living hinges require minimal space compared to traditional mechanisms, enabling more streamlined and aesthetically pleasing product designs. This compactness is especially beneficial in applications where space is limited.
Challenges
Material Limitations: Not all materials are suitable for forming effective living hinges. The choice of material is crucial, as it must possess the necessary flexibility, durability, and elasticity. Commonly used materials include polypropylene and polyethylene.
Design Constraints: Designing a living hinge requires precise consideration of various factors, including thickness, radius, and material properties. Improper design can lead to premature failure, making it essential to follow best practices in hinge design.
Load Bearing: Living hinges are typically limited to applications with minimal load requirements. They are not suitable for bearing significant weight or stress, which restricts their use to specific types of products and applications.
Fundamentals of Living Hinge Design
Basic Principles of Living Hinge Design
Effective living hinge design relies on understanding stress distribution and material properties, with key principles including:
Uniform Thickness: Consistent thickness ensures even stress distribution, crucial for preventing weak points prone to cracking or failure. Typically, living hinges range from 0.2 to 0.5 mm thick, tailored to specific materials and applications.
Radiused Corners: Rounded corners mitigate stress concentration, enhancing hinge durability. Adding a radius at the hinge base disperses stress evenly, improving overall performance.
Length and Width: Hinge dimensions impact flexibility and strength. Longer hinges distribute stress more evenly but may compromise part stiffness, while wider hinges handle more stress but sacrifice flexibility.
Material Selection: Choosing materials with high elongation and fatigue resistance is vital. Common choices like polypropylene (PP), polyethylene (PE), and acetal (POM) ensure durability and longevity under repeated flexing.
Material Considerations in Living Hinge Design
Material selection is critical for the success of a living hinge. Ideal materials include:
Polypropylene (PP): Known for its high flexibility and fatigue resistance, polypropylene is one of the most common materials used for living hinges. It offers excellent durability and can withstand many flex cycles.
Polyethylene (PE): Polyethylene, particularly high-density polyethylene (HDPE), offers good elongation and flexibility. It is suitable for applications requiring moderate hinge performance.
Acetal (POM): Acetal, also known as polyoxymethylene, provides good wear resistance and mechanical properties.It is used in applications where higher strength and stiffness are required, along with flexibility.
Design Parameters and Specifications for living hinge
Hinge Thickness
The thickness of the hinge significantly impacts its flexibility and durability. Typically ranging from 0.2 to 0.5 mm, thinner hinges offer greater flexibility but may sacrifice durability, while thicker ones prioritize durability over flexibility.
Hinge Length
Longer hinges distribute stress more evenly, reducing the risk of failure.
However, excessively long hinges may compromise the overall part's rigidity.
Balancing stress distribution and structural integrity is crucial for optimal performance.
Hinge Width
The width of the hinge affects its stress-handling capability.
Wider hinges can withstand more stress but may sacrifice flexibility.
Optimization based on expected load and required flexibility is necessary for optimal performance.
Radius
Incorporating a radius at the base of the hinge reduces stress concentration and enhances durability.
While a larger radius provides better stress distribution, it may necessitate more space in the design.
Careful consideration of these parameters ensures the creation of effective and durable living hinges tailored to specific application requirements.
Plastic Living Hinges
Common Types of Plastics Used for Living Hinges
Polypropylene (PP) and Polyethylene (PE): The two materials are consistent with the previous context, and will not be reiterated here.
Nylon: Nylon provides a balanced mix of flexibility and durability, with superior strength and wear resistance compared to polypropylene and polyethylene. This makes it suitable for demanding applications, including industrial components and robust consumer products.
Benefits of Using Plastic for Living Hinges
Cost-Effective: Plastics are generally less expensive to produce than metals, and the integral hinge design reduces the need for additional components and assembly steps, further lowering manufacturing costs.
Lightweight: Plastic materials are significantly lighter than metals, which is beneficial in applications where weight reduction is important, such as in automotive and aerospace industries.
Corrosion-Resistant: Plastics do not corrode like metals, making them suitable for use in environments where exposure to moisture, chemicals, or other corrosive elements is a concern.
Moldable: Plastics can be easily molded into complex shapes, allowing for greater design flexibility. This characteristic enables the creation of intricate hinge designs that integrate seamlessly into the final product.
3D Printed Living Hinges
Definition of 3D Printed Living Hinges
3D printed living hinges are created using additive manufacturing techniques, where the hinge is printed layer by layer, allowing for complex and customized designs. This method enables the production of flexible hinges directly integrated into a single printed part, offering significant advantages in terms of design freedom and prototyping speed.
Advantages of 3D Printing for Living Hinges
Rapid Prototyping: 3D printing allows for the quick production of prototypes and iterations, enabling designers to test and refine hinge designs rapidly. This accelerates the development process and reduces the time to market.
Customization: Additive manufacturing enables the creation of tailored designs for specific applications. Each hinge can be customized in terms of size, shape, and material properties to meet unique requirements.
Complex Geometries: Traditional manufacturing methods often struggle with intricate hinge designs. 3D printing can produce highly complex geometries that would be challenging or impossible to achieve with conventional techniques.
Reduced Waste: 3D printing is an additive process, meaning material is only deposited where needed, resulting in minimal waste. This efficient use of material not only reduces costs but also contributes to more sustainable manufacturing practices.
Material Options for 3D Printed Living Hinges
Flexible Filaments: TPU (Thermoplastic Polyurethane) stands out for its exceptional flexibility and durability, rendering it an ideal material for 3D printed living hinges. Its ability to withstand repeated bending and flexing without fracture makes it a reliable choice for such applications.
Resins: Specialized resins used in stereolithography (SLA) and digital light processing (DLP) 3D printing can produce durable and flexible parts.These resins are formulated to provide a good balance of flexibility and strength.
Nylon: The materials remain consistent with the preceding context and won't be reiterated here.
Design Flexibility and Customization
3D printing enables unique and intricate hinge designs not achievable through traditional methods. Designers can experiment with diverse geometries and material properties to enhance hinge performance. Key aspects of design flexibility and customization include:
Variable Thickness: Designers can vary the thickness of the hinge along its length to control flexibility and strength precisely. This level of control enables the creation of hinges with optimized performance for specific applications.
Integrated Features: 3D printing allows for the integration of additional features directly into the hinge design, such as locking mechanisms, reinforcement ribs, or textured surfaces, without the need for separate components.
Complex Geometries: With 3D printing, hinges can be designed with complex geometries, including curved shapes, intricate patterns, and multi-material constructions. This capability expands the possibilities for innovative and functional hinge designs.
Tailored Material Properties: By selecting and combining different materials, designers can tailor the mechanical properties of the hinge to match the specific requirements of the application. This includes varying the flexibility, strength, and durability of the hinge.
Applications of 3D Printed Living Hinges
3D printed living hinges find applications in various industries due to their customization and rapid prototyping advantages. Some common applications include:
Consumer Products: Prototyping and producing custom hinges for items like foldable electronics, toys, and household gadgets.
Medical Devices: Creating custom-fit enclosures and components for medical instruments and devices that require precise hinge functionality.
Automotive: Developing prototypes and low-volume production parts for interior components such as glove compartments and console lids.
Electronics: Manufacturing battery covers, access panels, and flexible connectors for electronic devices.
3D printed living hinges offer design flexibility, rapid prototyping, and material efficiency, making them increasingly popular for various applications. Leveraging 3D printing capabilities, designers create customized hinge solutions that enhance product performance.
Applications of Living Hinges
Consumer Products
Toothbrush Cases
Living hinges are commonly used in toothbrush cases to create a flexible, durable hinge that can withstand repeated opening and closing cycles.
The integral design reduces the number of parts and assembly steps, making the case lightweight, cost-effective, and reliable for daily use.
Remote Controls
Hinged battery compartments in remote controls often utilize living hinges.The hinge allows easy access to batteries while ensuring a secure closure. This design reduces the risk of losing small parts and simplifies the overall construction of the remote.
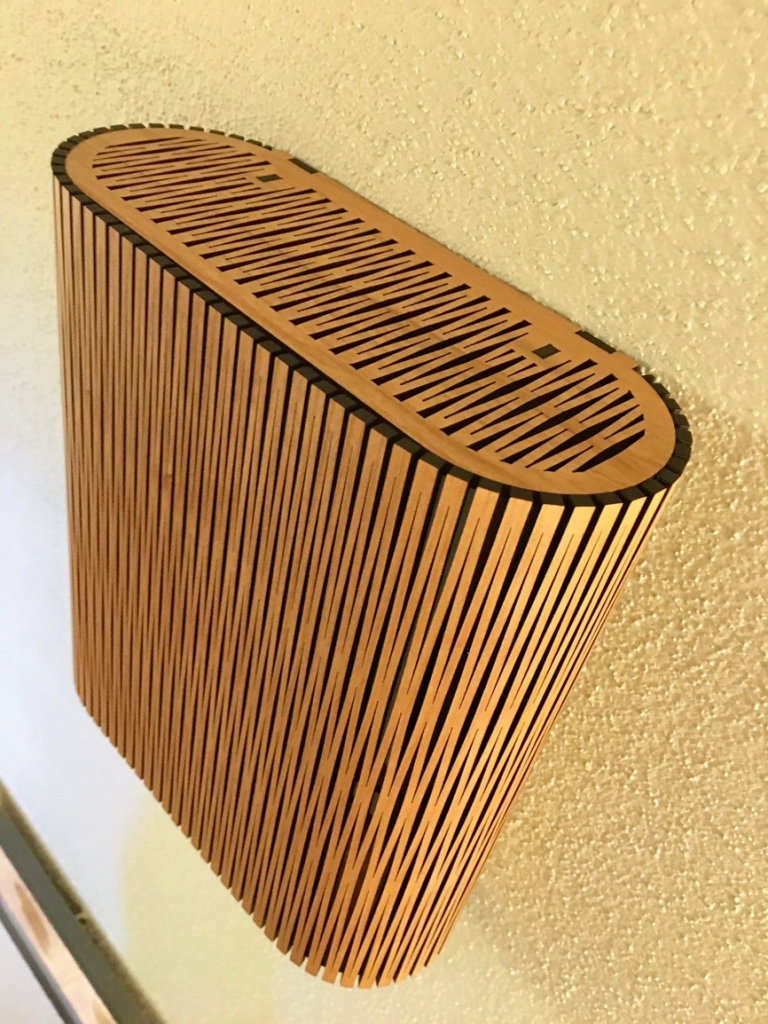
Source: community.glowforge.com
Medical Devices
Pill Dispensers
Living hinges are used in pill dispensers to provide secure and easy access to medication. The hinge ensures that the dispenser can be opened and closed repeatedly without breaking, enhancing user convenience and maintaining the integrity of the medication.
Surgical Instruments
Disposable surgical instruments, such as scissors and clamps, may incorporate living hinges.The use of living hinges in disposable instruments reduces manufacturing costs and ensures reliable performance during medical procedures. The integral hinge design minimizes contamination risks associated with multiple parts
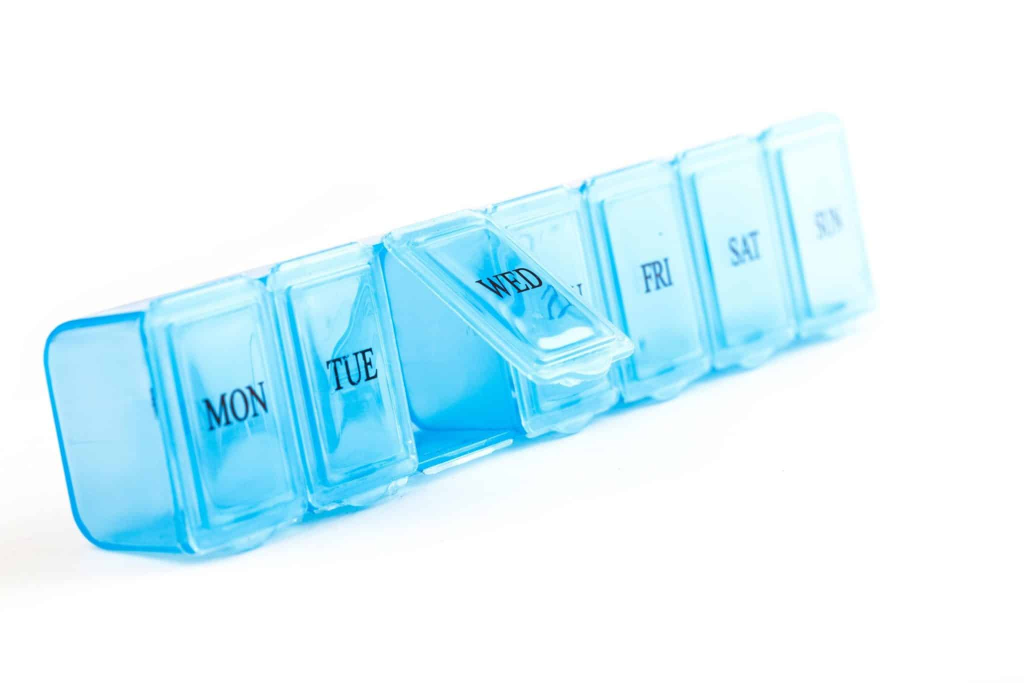
Source: jiga.io
Packaging Solutions
Flip-Top Caps
Flip-top caps for bottles and containers frequently use living hinges for their opening mechanism.These caps provide easy access to the contents while ensuring a secure seal when closed. Living hinges in flip-top caps enhance user convenience and maintain product freshness.
Clamshell Packaging
Clamshell packaging, often used for electronics, toys, and consumer goods, utilizes living hinges to connect the two halves of the packaging.The hinge allows the packaging to be opened and closed repeatedly without losing integrity, providing both security and ease of access. This type of packaging is also often reusable.
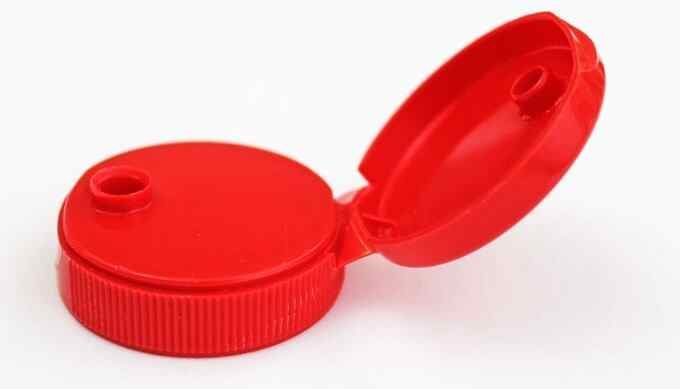
Source: rapidsrepro.com
Automotive Components
Glove Boxes
Living hinges are used in automotive glove boxes to create hinged access panels.The hinge provides a smooth and durable opening mechanism that can withstand frequent use. It also contributes to the aesthetic and functional design of the vehicle's interior.
Cup Holders
Hinges in automotive cup holders allow for flexible and durable components that can adapt to different cup sizes and shapes.Living hinges enable the cup holders to be more versatile and user-friendly, enhancing the convenience and functionality of the vehicle's interior.
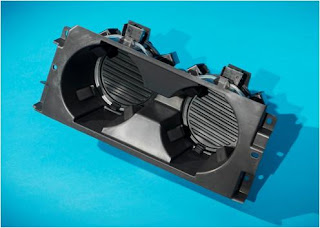
Source: plasticscar.blogspot.com
Electronics Enclosures
Battery Doors
Living hinges are commonly used in battery doors for electronic devices. The hinge allows easy access to batteries while providing a secure closure. This design helps maintain the device's compactness and reduces the risk of losing small parts.
Access Panels
Access panels in electronic enclosures often use living hinges to allow repeated opening and closing.The durable hinge design ensures that the panel can be opened and closed multiple times without breaking, providing reliable access to internal components for maintenance and repairs.
Living hinges excel across various industries, offering cost-effective, durable solutions for products needing repeated bending. Through material selection and hinge design optimization, manufacturers enhance functionality and user satisfaction.
Conclusion
Living hinges provide a cost-effective, durable, and flexible solution for various applications across industries.
By understanding the fundamentals of living hinge design and material considerations, designers can create products that benefit from the unique properties of living hinges.
Unionfab: Bring your Design to Living
Unionfab offers advanced solutions for incorporating living hinges into your designs, leveraging the latest materials and 3D printing technologies to bring your concepts to life.
For further details, please feel free to reach out to us via our Contact Us page.
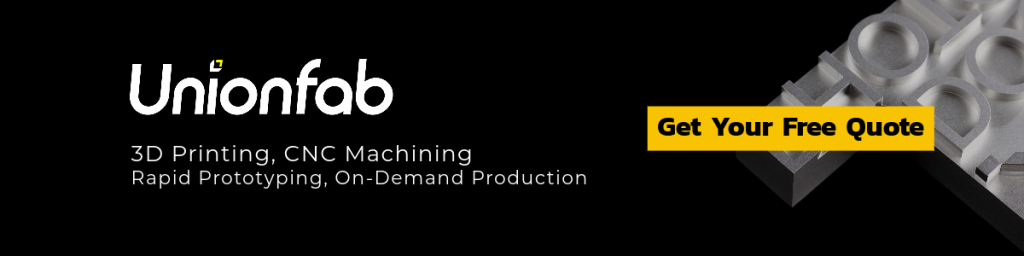