Low Volume Injection Molding: A Comprehensive Guide
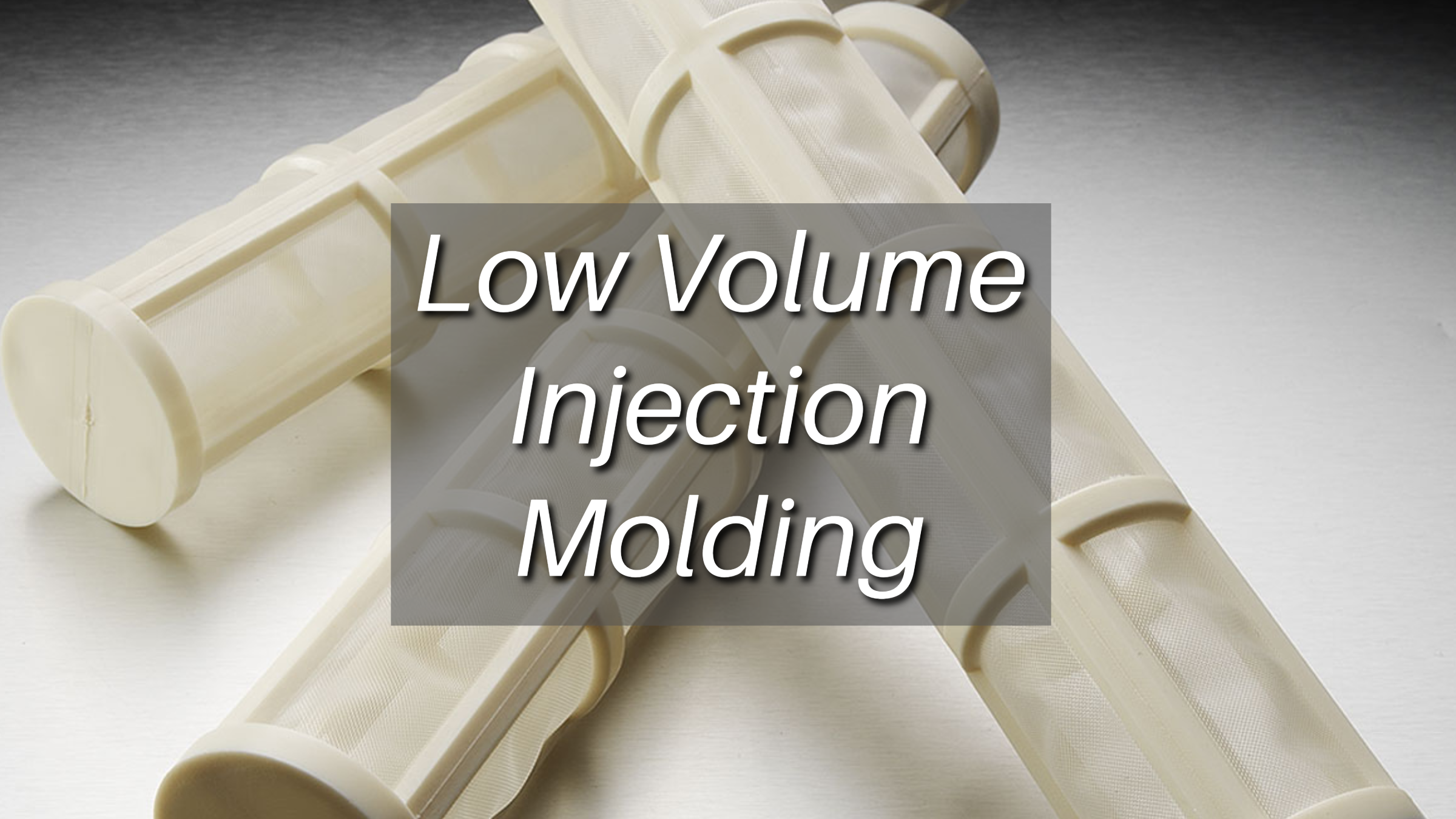
Discover how low volume injection molding helps businesses develop new products and tap niche markets on their budget and schedule.
Introduction
Low volume injection molding is a plastic production technique well-suited for small batches. It serves as a bridge between prototyping and large-scale manufacturing by allowing the creation of plastic parts in limited quantities. This makes the process ideal for developing products by allowing prototypes to be produced, testing new designs, and serving niche markets with short production runs.
Low volume injection molding lets manufacturers gauge feedback on their designs before committing to high-volume manufacturing, perfect for refinement based on customer response in the product development phase.
Understanding Injection Molding
Definition of Injection Molding
Injection molding is a formative manufacturing process as it forms plastic parts.
The process involves injecting melted plastic into a hollow mold cavity under high pressure. As the plastic cools and hardens inside the mold, it takes on the precise shape of the interior cavity. Once sufficiently solidified, the newly formed part can then be removed from the mold, having been molded into the intended design during the precise injection molding process.
By forcibly injecting melted plastic into a mold and allowing it to set under pressure, intricate plastic components can be efficiently mass produced.
Process of Injection Molding
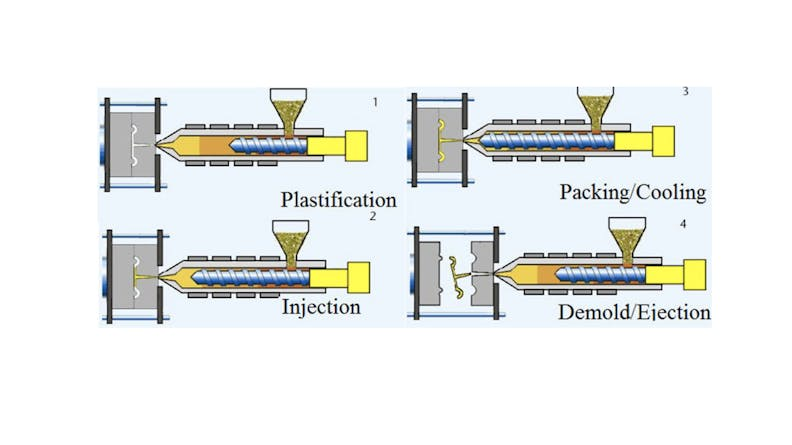
Source: xometry.com
Clamping: The two mold halves are pressed together tightly.
Injection: Melted plastic is forced into the mold cavity under pressure and fills all parts of the mold.
Packing and Holding: More pressure keeps the plastic filling the mold as it cools to account for shrinkage.
Cooling: A coolant circulates in the mold to rapidly harden the plastic.
Ejection: When set, the mold opens and ejector pins pop out the finished part.
Repeat: The mold automatically clamps shut again to make another part.
Injection Molding Types
Conventional Injection Molding
The most common type, conventional injection molding uses a two-piece mold that opens to eject the molded part once solidified.
Overmolding
This technique involves injecting plastic over an existing substrate. Overmolding is often used to impart textures, improve grip, or provide extra protection to a part.
Insert Molding
Insert molding places metal inserts inside the mold cavity prior to plastic injection. This allows for parts with higher strength requirements or specific electrical properties where metal components are desirable.
Gas-Assisted Injection Molding (GAIM)
Gas-assisted injection molding injects an inert gas like nitrogen into the molten plastic stream. This creates a hollow cavity within the part, lowering material needs, cycle times, and weight while enhancing dimensional stability.
Liquid Silicone Injection Molding (LIM)
Suitable for flexible medical and food-grade components, liquid silicone injection molding molds liquid silicone rubber (LSR), which offers biocompatibility as well as heat and flexibility advantages over rigid plastics.
Advantages of Injection Molding
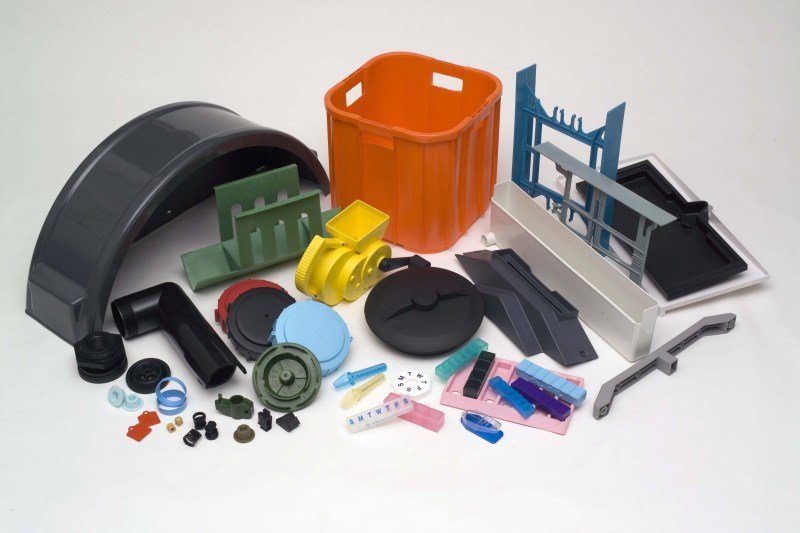
Source: KUZMA Industrial Group
High-precision and Repeatability: Injection molding produces parts with high dimensional accuracy and consistent quality throughout the production run.
Scalability: The process can be easily scaled up for mass production by building additional molds and machines.
Wide Material Range: A vast variety of plastic materials can be used, offering a broad range of properties for different applications.
Complex Shapes: Injection molding can create intricate and complex shapes with good surface finishes.
Techniques in Low Volume Injection Molding
Material Selection
While a wide range of plastics can be used in injection molding, low volume applications often focus on materials that balance cost, performance, and processability. Commonly used options include:
ABS (Acrylonitrile Butadiene Styrene): Offers a good balance of strength, rigidity, and impact resistance.
PP (Polypropylene): Lightweight, chemical resistant, and cost-effective, but with lower strength compared to ABS.
PC (Polycarbonate): High strength, clarity, and good heat resistance, but can be more expensive.
Nylon: Offers excellent wear resistance and mechanical properties, but requires specific drying procedures to prevent moisture-related issues.
Aside from the type of plastic, several properties need to be considered when selecting a material for low-volume injection molding:
Shrinkage: Different plastics have varying shrinkage rates as they cool. Molds need to be designed to account for this shrinkage to ensure parts meet dimensional specifications.
Flowability: The material's ability to flow easily within the mold cavity is crucial. Low-volume processes might benefit from materials with good flow characteristics to avoid issues like filling problems or uneven cooling.
Heat Resistance: The chosen material should be able to withstand the processing temperatures involved in injection molding.
Cost: Material cost plays a more significant role in smaller production runs compared to high-volume scenarios.
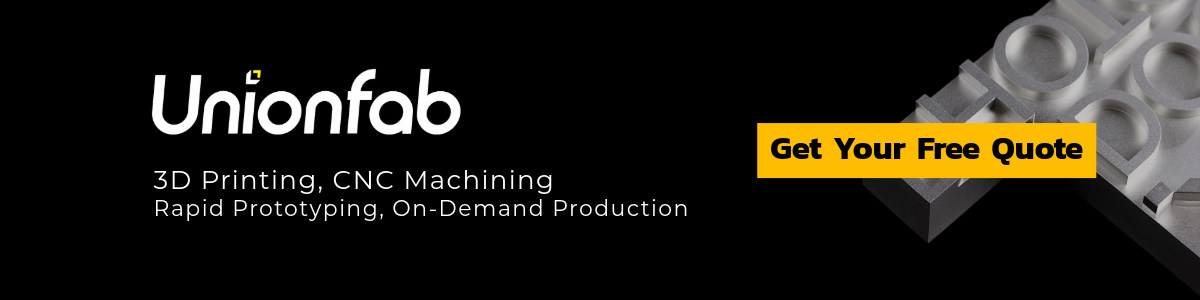
Mold Design
Designing for Efficiency
Single Cavity Molds: These are most common for low volumes, as they are quicker and cheaper to produce.
Parting Lines: Optimize parting line placement to minimize post-processing and finishing needs.
Wall Thickness: Maintain uniform wall thickness throughout the part to ensure consistent cooling and prevent warping.
Draft Angles: Include slight draft angles on the sides of the part to facilitate easier removal from the mold.
Prototyping and Iteration
Low-volume processes often benefit from rapid prototyping techniques to validate the mold design before final production.
Techniques like 3D printing can be used to create test molds for functional testing and design iteration before committing to a final steel mold.
Injection Process
Machine Settings
Melt Temperature: The temperature at which the plastic is melted needs to be precisely controlled to ensure proper flow and avoid material degradation.
Injection Pressure: The force used to push the melted plastic into the mold needs to be sufficient to fill the mold without causing defects.
Cooling Time: How long the plastic cools inside the mold affects the cycle time and part quality.
Benefits of Low Volume Injection Molding
Cost-Effectiveness
Reduced Tooling Costs
Compared to traditional high-volume injection molding, which utilizes steel molds, low-volume processes can significantly reduce tooling costs.
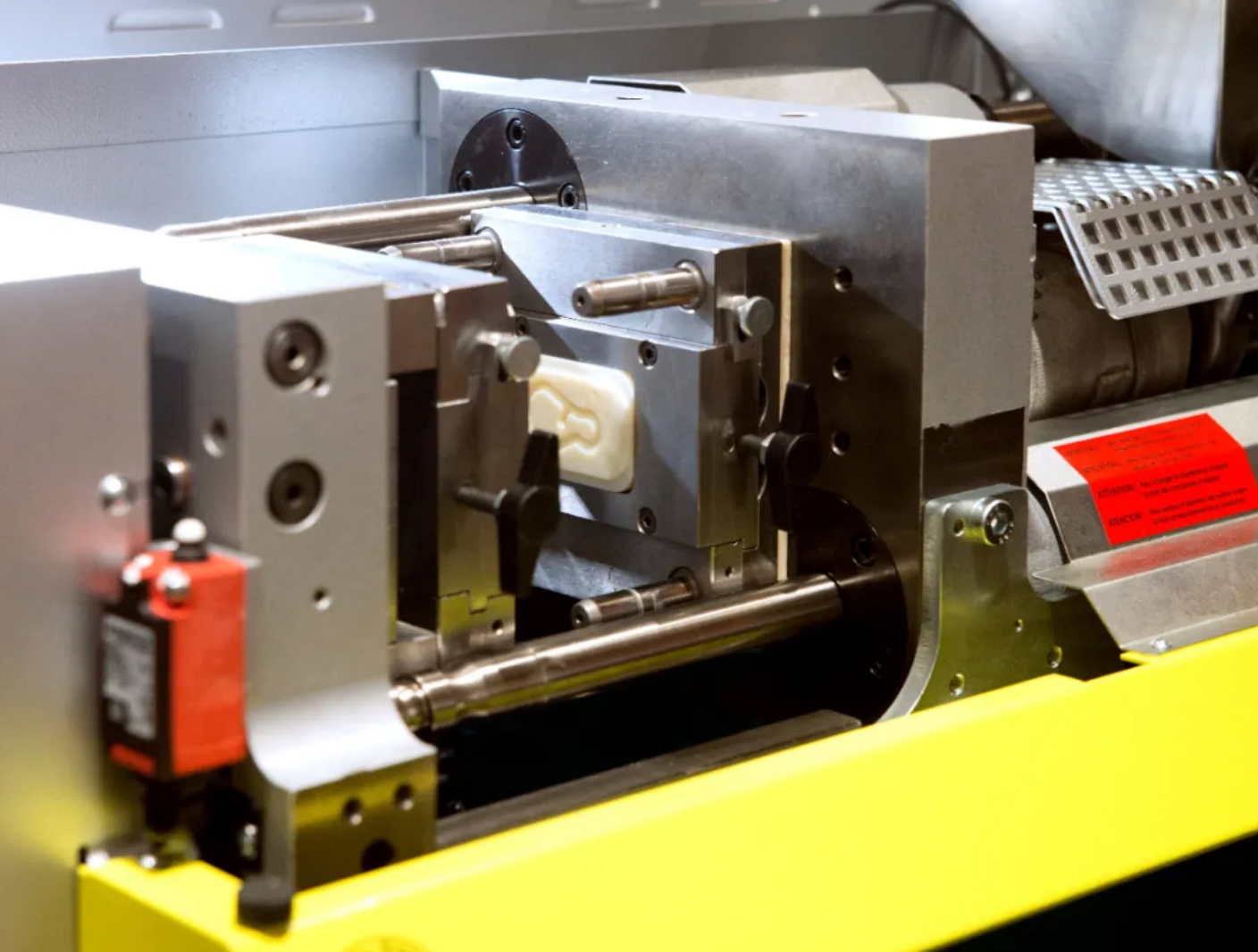
Source: Unionfab
Techniques like aluminum molds or even 3D printed molds offer faster turnaround times and lower upfront investment.
Minimized Waste
Small production batches minimize wasted plastic. Less material is thrown out since fewer parts are made. This cuts costs to throw away scrap plastic. It also makes the process better for the environment by reducing waste.
Flexibility
Quick Turnaround Times
Low-volume molds can be made quicker than large batch molds. This speeds up how fast new parts are ready.
Adaptability to Design Changes
Design changes are easier with low volume production. Fewer molds are used compared to high volume production.
This allows more flexibility to refine designs before bigger production runs. You can make changes and try different versions more easily.
Quality and Precision
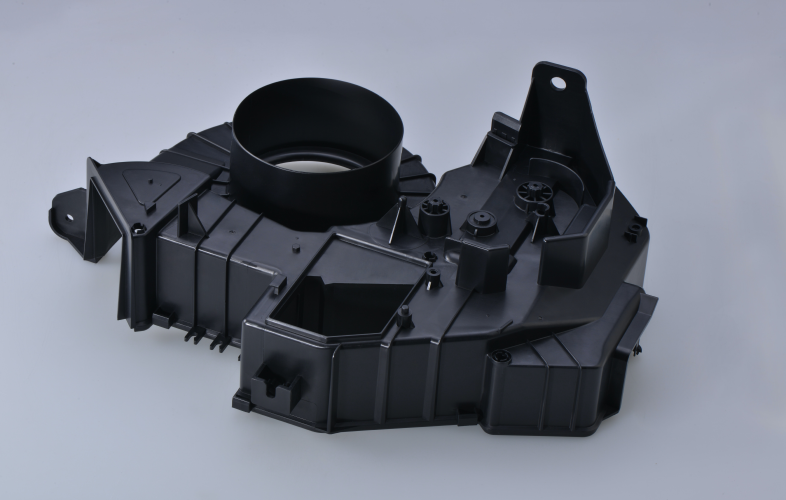
Source: Zeal3D
Consistent Part Quality
Injection molding makes parts the same way each time. Even when making few parts, it can create shapes that are very accurate and the same quality from start to finish. This repeatable process keeps parts uniformly good.
Detailed and Complex Geometries
Injection molding can create intricate and complex shapes with good surface finishes. This allows you to produce parts with detailed features even in low quantities.
Applications of Low Volume Injection Molding
Medical Devices
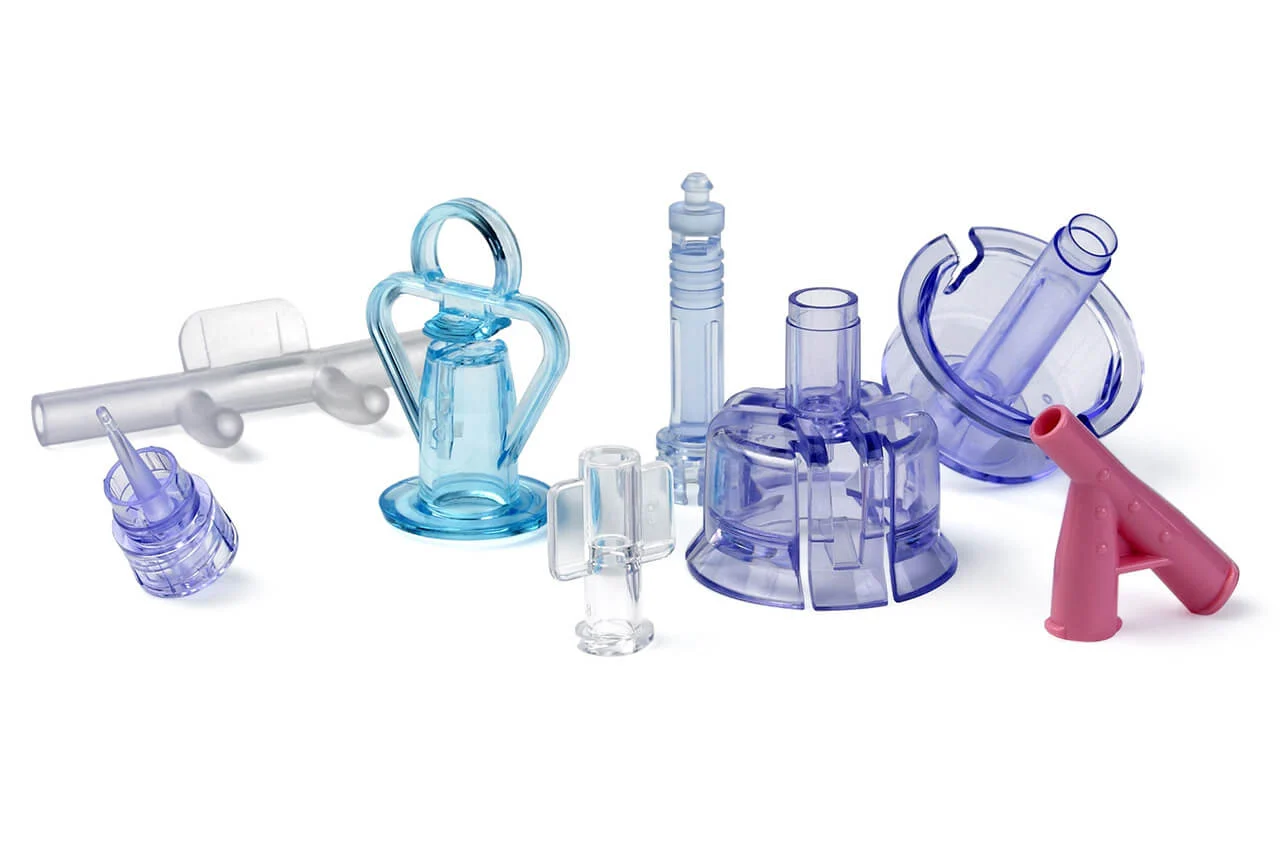
Source: Husky Technologies
Low-volume injection molding is ideal for creating prototypes of new medical devices for testing and development. This could include syringe bodies and plungers for new drug delivery systems, customizable inhaler components for patients with specific needs and prototype housing for a new diagnostic device.
This technique is also suitable for creating personalized medical equipment or components tailored to specific patient needs.
Consumer Products
Low-volume molding caters to niche markets where demand might not justify high-volume production. Examples include phone cases with custom engravings or designs, limited-edition color variations of popular consumer electronics and personalized water bottles or mugs with names or logos.
Automotive Industry
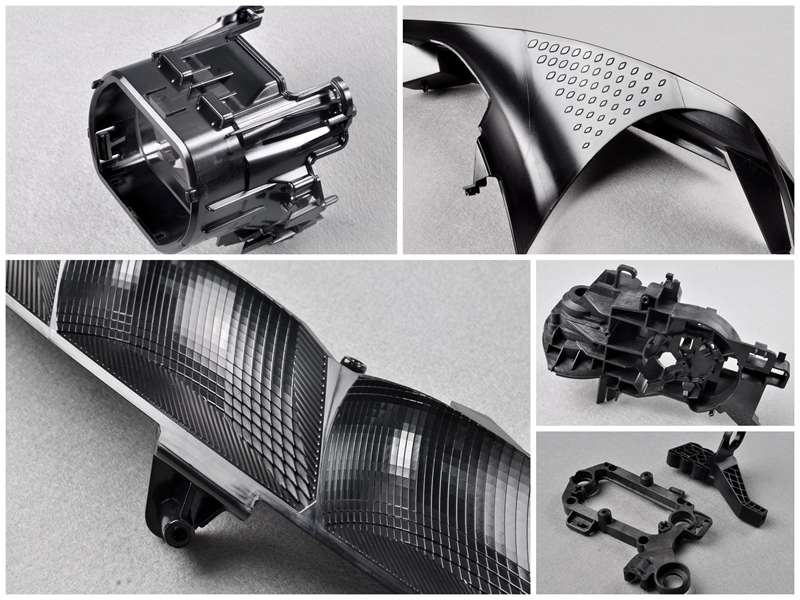
Source: autoprotoway.com
The automotive industry heavily relies on prototyping for new vehicle designs and components. Low-volume injection molding allows for the rapid creation of prototypes for testing and validation.
Besides, certain car parts might only be required in small quantities for specific models or performance upgrades. Low-volume molding provides a cost-effective way to manufacture these parts.
Electronics
Low volume injection molding works well for prototypes of things like phone and tablet cases, smartwatch and home device enclosures, and unique electronics gadget casings during the design process.
Conclusion
low volume injection molding offers a compelling option for businesses seeking high-quality plastic parts in smaller quantities. It provides a cost-effective alternative to traditional high-volume production, with faster turnaround times and greater flexibility for design changes.
From prototyping medical devices to producing limited edition consumer goods, low volume injection molding plays a vital role in bridging the gap between initial concepts and full-scale manufacturing.
Unionfab: Excelling at Different Levels of Production
Unionfab offers flexible parts manufacturing for any quantity, from prototypes to production runs of 100,000 pieces. We're your one-stop factory!
Get your instant quote now or contact us for specific needs.