Polycarbonate vs. ABS: What Is the Difference?
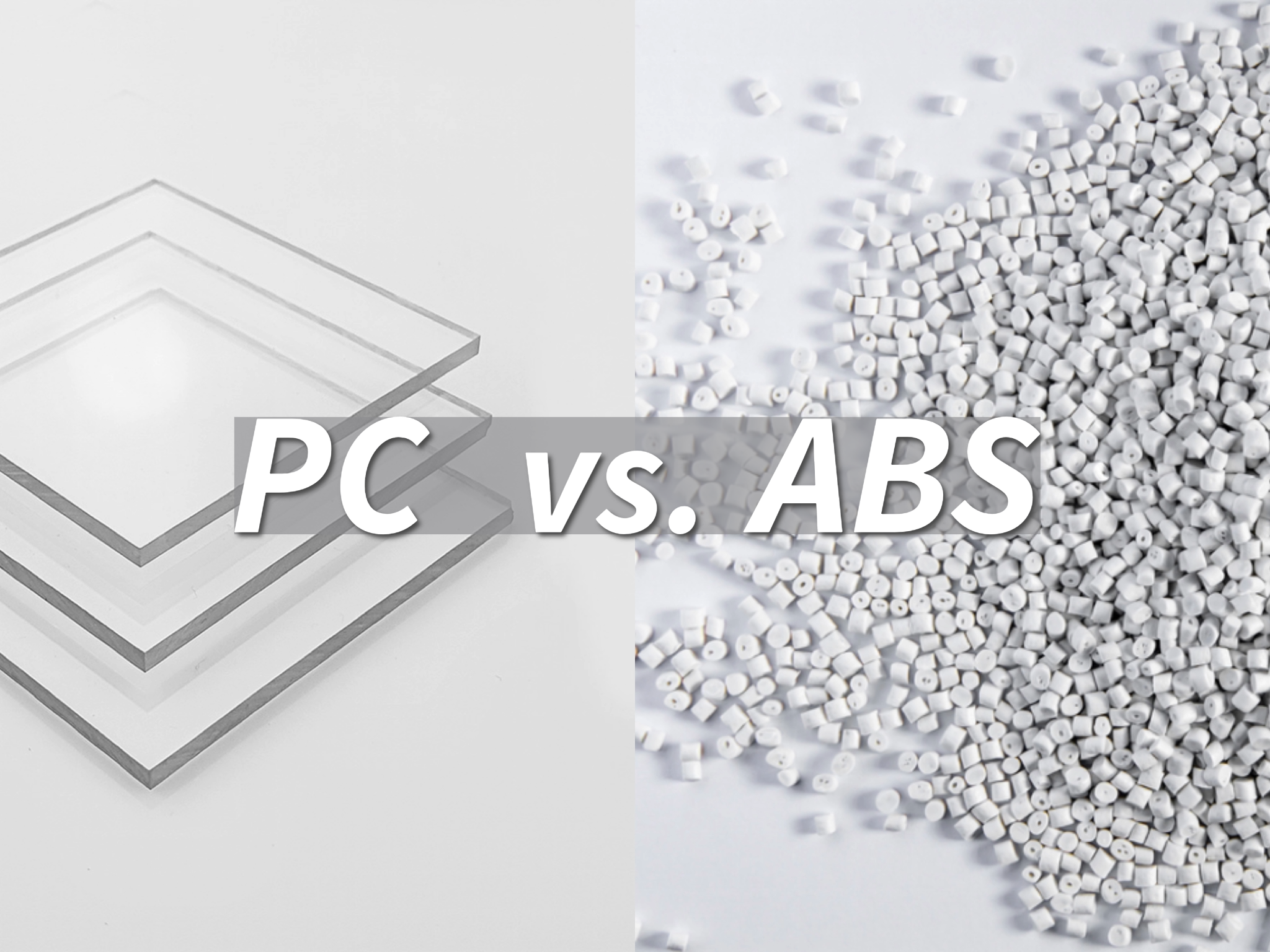
Polycarbonate and ABS are two types of plastic. PC is stronger and more heat-resistant, while ABS is cheaper and easier to mold.
Introduction
PC, or Polycarbonate, is a strong and light plastic. It does not break easy and can stand high heat. People use polycarbonate for applications like eyeglass lenses, sports gear, and electronics casings as it protects things well.
ABS, or Acrylonitrile butadiene styrene, is another handy plastic. Because of its strength and stability, ABS is suitable for light-duty applications. Common items include phone cases, prototype tools, and casual household goods.
What is Polycarbonate?
Polycarbonate is a tough, clear plastic. It is light but hard to break. Its molecules are made of carbonate groups connected by bisphenol-A pieces.
It is used in:
Car headlights: Cars use polycarbonate for headlights because it is transparent and doesn't easily crack.
Gadgets: Things like phones, TVs and tablets have polycarbonate screens since they stay in one piece.
Device screens: Mobile phones, tablets and TVs rely on polycarbonate screens that won't shatter like glass if dropped. This protects the display.
Doctor tools: Doctors choose polycarbonate for tools since it's easy to clean and won't break if it falls.
Medical tools: In healthcare settings, polycarbonate equipment is chosen since it withstands wear and impacts while allowing easy disinfection.
Eye gear: Makers of eyeglasses, helmets and shields pick polycarbonate because it's difficult to smash.
Eyewear/headgear: Products like eyewear, helmets and face shields select polycarbonate for its combination of clarity and strength, helping to prevent injury from hits or falls.
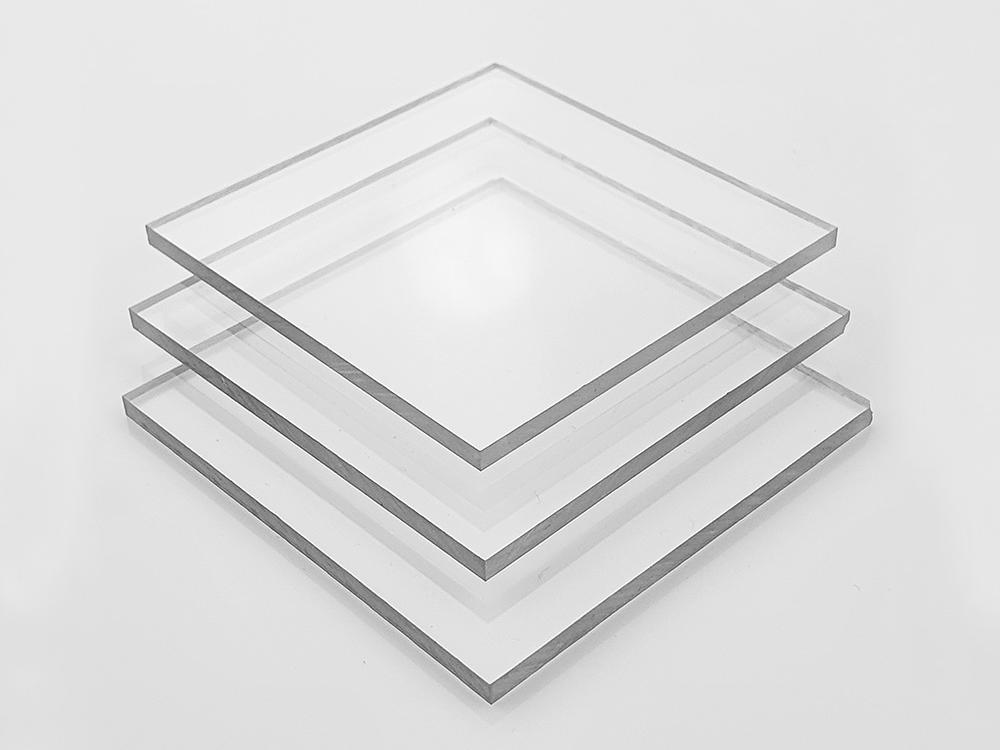
Source: cutplasticsheeting.com
What is ABS?
ABS is a strong plastic. It is made of acrylonitrile, butadiene and styrene stuck together.
It is used in:
Cars: ABS is used for control panels and trim pieces because it maintains its shape even on hot, sunny days inside vehicles.
Electronics: Phones, game consoles and other devices have ABS casings since it stays solid in your hands.
Toys: ABS lets toy makers create durable toys that kids can play with without them breaking.
Home stuff: Appliances’ like microwave ovens and 3D printers choose ABS because it won't soften or melt from higher operating temperatures.

Source: asanform.com
Polycarbonate vs ABS: A Comparison
These two plastics are commonly used. But how do they differ?
Strength and Hardness
Polycarbonate is very tough and can withstand heavy impacts without cracking or breaking. It is stiffer and more durable than ABS.
ABS also has good impact strength but is more prone to flexing or warping over time under stress.
Physical Properties
Polycarbonate is a clear, glossy material while ABS comes in various opaque colors and textures. PC is denser and heavier than ABS.
Both plastics can be easily molded, formed or 3D printed.
Chemical Resistance
Most acids, bases and solvents do not affect polycarbonate.
ABS is vulnerable to chemicals like acetone that can cause it to warp or dissolve over time.
UV Resistance
ABS breaks down faster when exposed to ultraviolet sunlight compared to more durable polycarbonate. ABS will yellow and degrade outdoors quicker.
Cost
Virgin polycarbonate pellets are more costly than ABS plastic filament to produce parts. ABS proves the more affordable option.
Environmental Impact
Neither fully biodegrades quickly. But ABS recycling is relatively common while PC recycling facilities are still developing. Both can be reused to make new products.
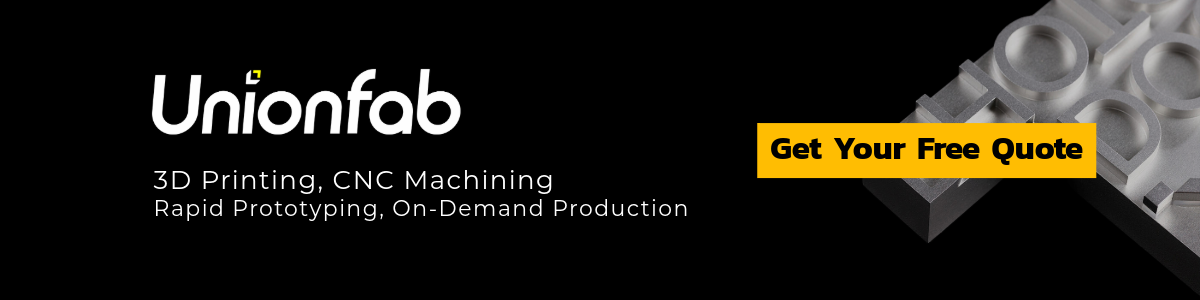
Polycarbonate vs ABS: Manufacturing Method
Polycarbonate and ABS are two common thermoplastics used in a variety of applications, from consumer goods to industrial components. While both materials offer unique properties, their manufacturing processes can differ significantly.
3D Printing: Layer-by-Layer Creation
3D printing, or additive manufacturing, has become increasingly popular in recent years. This process involves building a part layer by layer, using a variety of techniques.
Polycarbonate: Polycarbonate is commonly used in 3D printing, especially with fused deposition modeling (FDM) technology.
ABS: ABS is another common material for 3D printing, especially for FDM. Its layer adhesion properties and ease of printing make it a popular choice.
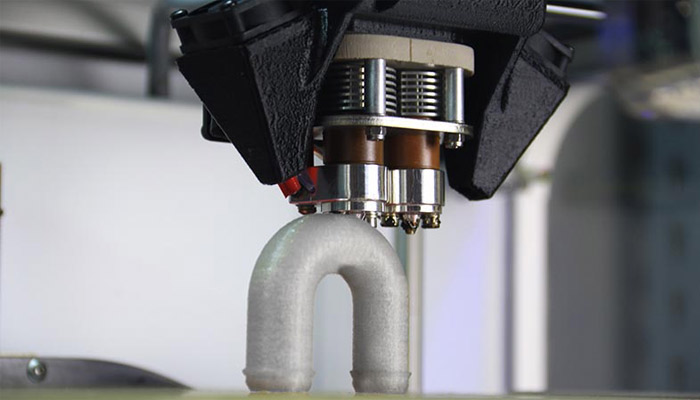
Source: airwolf3D.com
Injection Molding: A Common Method
Injection molding is perhaps the most widely used method for both polycarbonate and ABS. In this process, molten plastic is injected into a mold cavity, where it cools and solidifies. The mold is then opened, and the finished part is ejected.
Polycarbonate: Due to its high heat resistance and toughness, polycarbonate can be injection molded at higher temperatures and pressures than ABS.
ABS: ABS is also well-suited for injection molding and is often used for complex parts with intricate details.
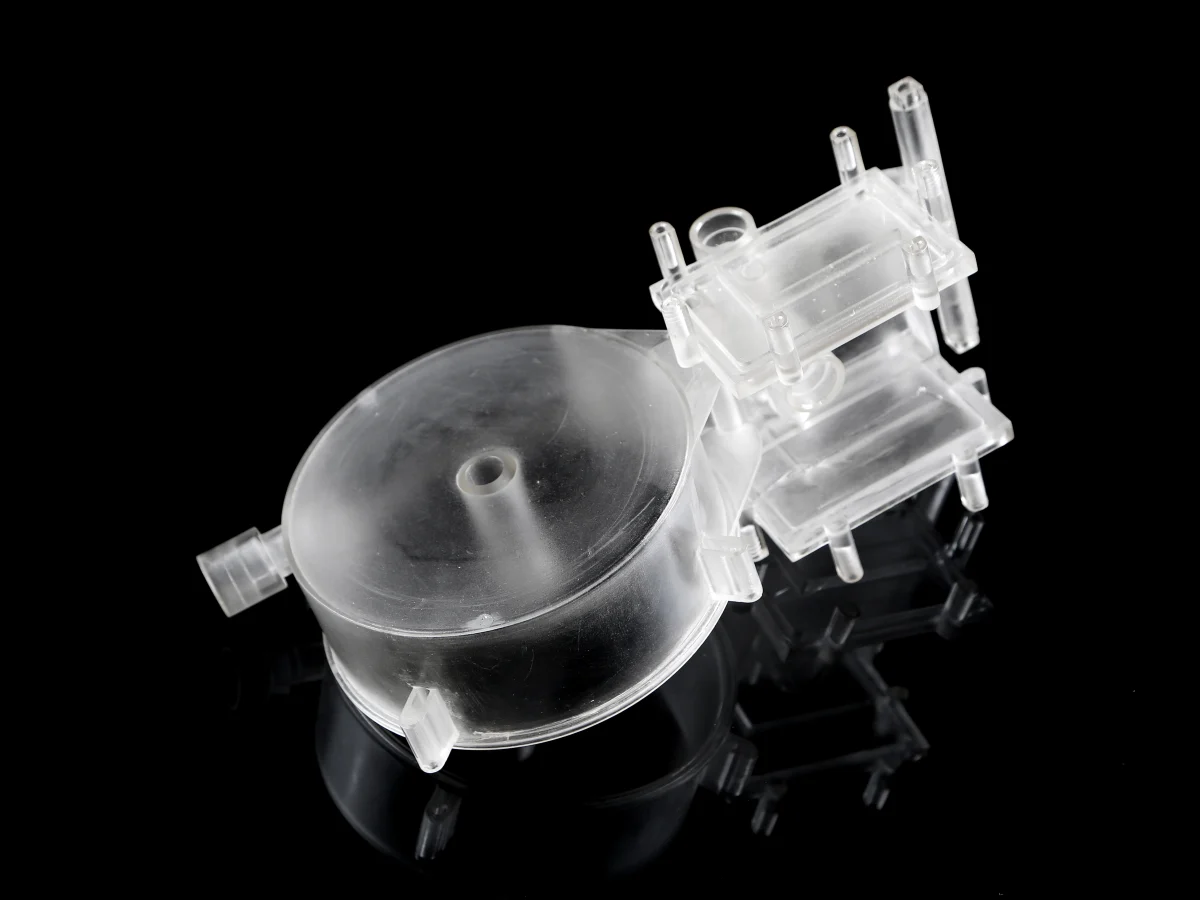
Source: hubs.com
Blow Molding: For Hollow Structures
Blow molding is primarily used for creating hollow plastic parts, such as bottles and containers. In this process, a heated plastic parison (a tube of plastic) is placed into a mold, and air is blown into it to expand the plastic against the mold walls.
Polycarbonate: Polycarbonate's high impact strength and clarity make it a popular choice for blow molding applications, especially for food and beverage containers.
ABS: While ABS can be used for blow molding, it is less common due to its lower heat resistance and potential for warping.
Extrusion: For Continuous Profiles
Extrusion is used to produce continuous profiles of plastic, such as sheets, pipes, and rods. In this process, molten plastic is forced through a die, shaping it into the desired form.
Polycarbonate: Polycarbonate can be extruded to produce various profiles, including sheets for glazing and optical applications.
ABS: ABS is commonly extruded to produce pipes, fittings, and housings for electronic devices.
Thermoforming: Heating and Shaping Sheet Plastic
Thermoforming involves heating a sheet of plastic to make it pliable and then forming it into a desired shape using a mold.
Polycarbonate: Polycarbonate can be thermoformed to produce a variety of products, including automotive parts and medical devices.
ABS: ABS is also well-suited for thermoforming and is often used for packaging and consumer goods.
Polycarbonate vs ABS:which is better?
There are several important factors to examine:
Application Requirements
Will it be used indoors or outdoors? Polycarbonate withstands sun/heat better.
Does it need impact/shatter resistance? Then polycarbonate's strength and clarity are better.
Does color/aesthetics matter? ABS makes colored, opaque parts.
Manufacturing Requirements
Which forming processes will be used - injection molding, 3D printing etc.? Consider material properties.
Does product require machining or assembly later? ABS machines easier than polycarbonate.
Cost
Polycarbonate material costs more per unit than ABS plastic.
Upfront costs for manufacturing tools/molds affect price of each part.
Environmental Impact
How will plastic scrap/waste be disposed of? ABS recycling facilities are more available.
Does product require durability outdoors? UV-resistant polycarbonate is better long-term.
Careful assessment of all factors like product use, production process, expenses and sustainability will help pick the right plastic
for your specific application needs. Both materials have pros and cons to weigh.
Alternative Materials
While PC and ABS offer excellent properties, there are circumstances where alternative materials might be more suitable. Here are three potential alternatives:
Nylon: Nylon is tougher than ABS and can withstand more dents and crashes. It works well for parts on machines that need to last. Nylon stays sturdier than ABS in cold weather and does not crack or chip as easy when it's chilly out.
Polyethylene Terephthalate (PET): PET looks clear like polycarbonate and holds its shape without breaking apart. It can be recycled lots of times compared to other plastics. That's why water bottles and drink containers often use PET.
High Impact Polystyrene (HIPS): HIPS costs less to make than ABS but keeps its hardness and absorption of impacts the same. It provides an affordable option to test out designs for products, sample models and packaging where money matters. Things like appliances that need to stay on a low budget can use HIPS plastic.
Conclusion
In summary, this article discussed and compared polycarbonate and ABS plastics. Polycarbonate is stronger, more heat-resistant and clear like glass. However, it is also more expensive than ABS plastic. ABS provides color options and works better for low-cost items.
By considering the differences in properties, cost and sustainability, engineers can determine whether polycarbonate or ABS suits their needs the most.
Unionfab: Ensure You Pick the Right Plastic for Your Project
At Unionfab, we have extensive experience molding, machining, printing and finishing both PC and ABS. Tired of wasting time and money on failed prototypes? Let our engineers consult with you to maximize material selection.
Contact us today for quotes - we strive to deliver high quality solutions within your budget and timeline.
View our full capabilities at unionfab.com and turn your visions into realities.