Prototype Injection Molding: An Efficient Product Process
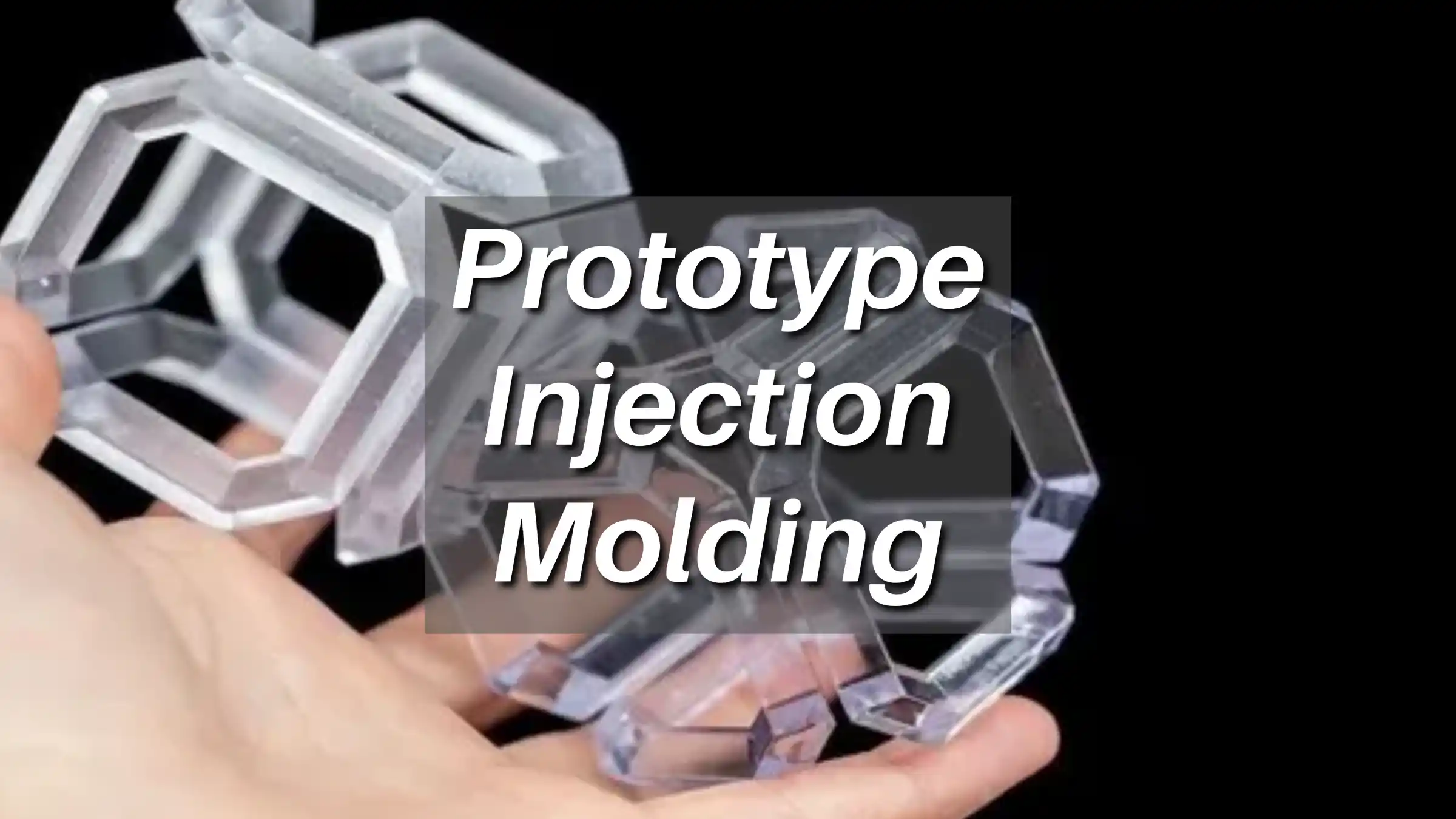
Prototype injection molding is a critical process in product development, enabling manufacturers to create preliminary versions of parts and products before mass production.
Introduction
Prototype injection molding is a process used to create sample parts and products to evaluate design, fit, function, and manufacturability.
By using this method, engineers and designers can produce accurate prototypes that closely resemble the final product.
This allows for thorough testing and validation before proceeding to mass production.
Prototype Injection Molding Process
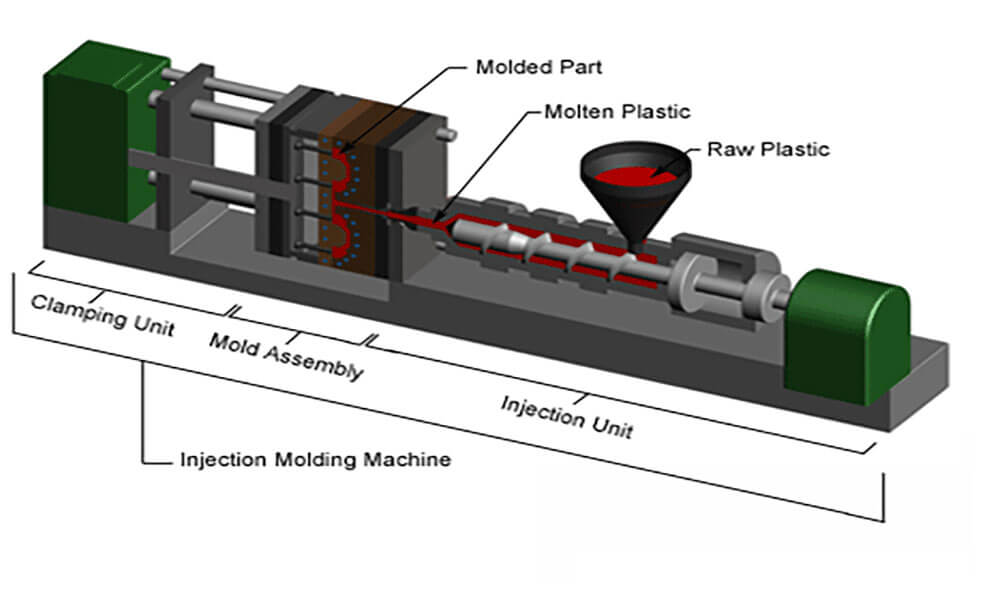
Source: hollyplasticparts.com
Design and CAD Modeling
The first step in prototype injection molding is creating a detailed design of the part or product using Computer-Aided Design (CAD) software.
This digital model provides a precise blueprint for the mold and helps in visualizing the final product.
Mold Fabrication
Types of Molds
There are various types of molds used in prototype injection molding, including aluminum molds, steel molds, and soft tooling.
Each type has its advantages and is chosen based on the requirements of the prototype.
Rapid Tooling
Rapid tooling involves the quick fabrication of molds using techniques like 3D printing and CNC machining.
This approach significantly reduces lead times and costs, making it ideal for prototype development.
Material Selection
Choosing the right material is crucial for prototype injection molding. Materials must be selected based on their properties, such as strength, flexibility, and thermal resistance, to ensure the prototype meets the desired specifications.
Injection Molding Setup
Machine Calibration
Proper calibration of the injection molding machine is essential to ensure accurate production. This involves setting up the machine parameters, such as temperature, pressure, and injection speed, to match the material and mold requirements.
Process Parameters
Setting the correct process parameters, including injection pressure, holding pressure, and cooling time, is vital for achieving high-quality prototypes. These parameters must be optimized to prevent defects like warping, sink marks, and incomplete fills.
Prototype Production
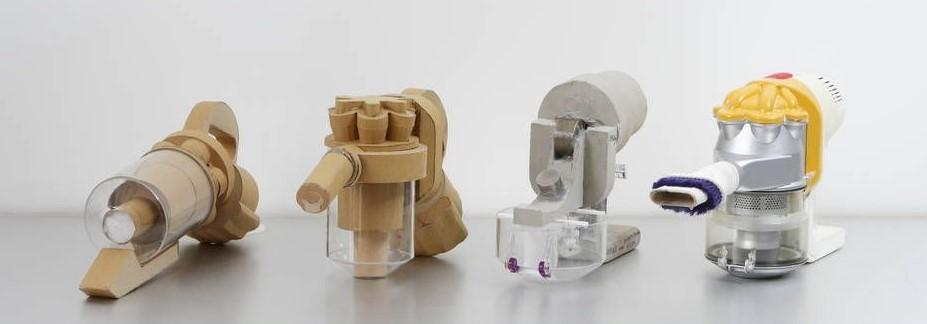
Source: dyson.com
Injection Process
In this step, the selected material is melted and injected into the mold cavity under high pressure.
The molten material fills the mold, taking its shape to form the prototype.
Cooling and Ejection
After the material has filled the mold, it is cooled to solidify. Once cooled, the mold opens, and the prototype is ejected.
The cooling process is critical as it affects the dimensional accuracy and surface finish of the prototype.
Iteration
After the initial prototype is produced, it undergoes testing and evaluation. Based on the feedback, design modifications are made, and the mold is adjusted if necessary. This process is repeated until the prototype meets all specifications and performance criteria.
Design Considerations for Prototype Molding
Material Compatibility
Ensuring the chosen material is compatible with the intended application is crucial. Different materials have varying shrinkage rates, thermal properties, and mechanical strengths that must be considered during the design phase.
Shrinkage Rates: Different materials shrink at different rates as they cool and solidify. For example, polypropylene has a higher shrinkage rate compared to ABS plastic. If not properly accounted for, this can lead to dimensional inaccuracies in the final prototype.
Thermal Properties: The heat resistance of materials varies significantly. For instance, a prototype intended for an automotive part near the engine must be made from a heat-resistant material like polyphenylene sulfide (PPS) rather than a less heat-tolerant material like polyethylene.
Mechanical Strength: Some applications require materials with high tensile strength or impact resistance. For example, a prototype for a heavy-duty tool handle would need to be made from a durable material like polycarbonate, whereas a less demanding application might only require polystyrene.
Tolerances and Precision
Prototypes must be designed with appropriate tolerances to account for material behavior during molding.
High precision is necessary to ensure that the prototype meets the functional and aesthetic requirements.
Tight Tolerances: A prototype for a medical device must have very tight tolerances to ensure all parts fit together seamlessly and function correctly. This might involve tolerances of ±0.05 mm or less.
Adjusting for Material Behavior: Materials can expand or contract during molding and cooling. For instance, if creating a prototype for a snap-fit part, the design must account for the slight expansion and contraction of materials like nylon to ensure a proper fit.
Surface Finish and Texture
The surface finish and texture of the prototype can affect its appearance and performance.
Mold design and material selection play a significant role in achieving the desired surface quality.
Aesthetic Requirements: A prototype for a consumer electronics case might require a smooth, glossy finish to match the final product. This would involve polishing the mold to achieve the desired surface quality and selecting a material that can support such a finish, like ABS or polycarbonate.
Functional Textures: In contrast, a prototype for a grip handle might require a textured surface for better ergonomics. This could involve designing the mold with a textured finish and selecting a material like thermoplastic elastomer (TPE) that can replicate the desired texture.
Structural Integrity
The prototype must have sufficient structural integrity to withstand testing and real-world use.
This involves considering factors such as wall thickness, reinforcement, and material strength during the design process.
Wall Thickness: Uniform wall thickness is crucial to avoid issues like warping or sinking. For a plastic housing component, maintaining a consistent wall thickness of around 2-3 mm can help ensure structural integrity without causing molding defects.
Reinforcements: Adding ribs or gussets can enhance the strength of the prototype. For instance, a prototype for a plastic bracket might include ribbing to increase stiffness without significantly increasing weight or material costs.
Material Strength: The choice of material directly impacts the prototype's durability. For a load-bearing prototype, selecting a material with high tensile and impact strength, such as fiberglass-reinforced nylon, is essential to prevent failure during testing and use.
In conclusion, in prototype injection molding, careful consideration of material compatibility, precise tolerances, surface finishes, and structural integrity is essential. Addressing these factors ensures that the prototype performs reliably and meets both aesthetic and functional requirements.
Challenges and Solutions of Injection Molding Prototyping
Mold Design Limitations
Complex designs can pose challenges in mold fabrication. Utilizing advanced mold-making techniques and materials can help overcome these limitations. For instance:
Advanced Techniques: Utilizing techniques like multi-cavity molds or hot runner systems can facilitate the production of complex geometries with high precision.
Materials: Choosing mold materials with superior hardness and heat resistance, such as tool steel or aluminum alloys, can enable the fabrication of intricate molds capable of producing complex parts.
3D Printing: Incorporating additive manufacturing processes like 3D printing can allow for the fabrication of intricate mold inserts or prototype parts directly, bypassing some traditional mold design limitations.
Material Shrinkage and Warping
Materials can shrink and warp during cooling, leading to dimensional inaccuracies. Proper mold design and process control can minimize these effects. Considerations include:
Mold Design: Designing the mold with uniform cooling channels and appropriate venting can help control cooling rates and minimize shrinkage and warping.
Material Selection: Choosing materials with low shrinkage rates or adding fillers and reinforcements can mitigate shrinkage and improve dimensional stability.
Process Optimization: Implementing precise control over process parameters such as temperature, pressure, and cooling time can minimize shrinkage and warping effects during molding.
Ensuring Consistent Quality
Maintaining consistent quality across multiple prototypes can be challenging. Implementing rigorous quality control measures and iterative adjustments can help ensure uniformity. Strategies include:
Quality Control Measures: Implementing stringent inspection protocols at various stages of production can identify and rectify quality issues early on, ensuring consistency across prototypes.
Material Testing: Conducting material testing to evaluate properties such as viscosity, flow behavior, and mechanical strength can ensure consistent performance across different batches of prototypes.
Process Monitoring: Employing real-time monitoring systems to track key process parameters can help identify deviations and maintain consistent quality throughout production runs.
Iterative Adjustments
Prototyping often requires several iterations to achieve the desired outcome. Rapid tooling and flexible design modifications facilitate quick adjustments and improvements. Consider the following:
Rapid Tooling: Utilizing rapid tooling techniques such as aluminum or soft steel molds can expedite the production of prototype molds, enabling faster iterations and design modifications.
Flexible Design: Designing prototypes with features that allow for easy modification, such as interchangeable inserts or modular components, facilitates quick adjustments and iterations.
Digital Prototyping: Leveraging digital prototyping tools and simulations allows for virtual testing and optimization of designs before physical production, reducing the need for extensive iterations and physical modifications.
Benefits of Prototype Injection Molding
Cost-Effectiveness
Prototype injection molding is more cost-effective than traditional manufacturing methods, particularly for small production runs and complex designs. Here's how:
Reduced Tooling Costs: Compared to traditional manufacturing methods like CNC machining, the cost of tooling for injection molding prototypes is generally lower. This is especially advantageous for small production runs where amortizing tooling costs over a limited number of parts is more feasible.
Material Efficiency: Injection molding processes typically generate less material waste compared to subtractive manufacturing methods like milling or turning. This efficiency translates into cost savings, particularly when working with expensive materials.
Economies of Scale: While prototype injection molding may have higher initial setup costs compared to additive manufacturing methods like 3D printing, it becomes more cost-effective for larger production volumes due to lower per-unit costs.
Time Efficiency
Rapid tooling and quick turnaround times enable faster product development cycles, reducing time-to-market. Consider the following:
Shorter Lead Times: Injection molding prototypes can be produced relatively quickly once the tooling is prepared, allowing for rapid iteration and design refinement.
Faster Iterations: The ability to quickly modify molds and produce new prototypes accelerates the iteration process, enabling design changes to be implemented and tested rapidly.
Streamlined Development: By reducing the time required for each iteration, prototype injection molding helps streamline the product development process, allowing companies to respond more swiftly to market demands and stay ahead of competitors.
Design Validation and Iteration
Creating prototypes allows for thorough testing and validation of designs, leading to improved final products. Iterative prototyping helps identify and resolve design flaws early in the process. Here's how it benefits:
Early Detection of Issues: Prototyping enables designers to identify potential design flaws or performance issues before investing in full-scale production. This early detection minimizes the risk of costly design changes later in the development process.
Iterative Improvement: Through successive iterations, designers can refine and optimize the product design based on real-world testing and user feedback. This iterative approach results in products that better meet customer needs and performance requirements.
Validation of Concepts: Prototyping allows designers to validate design concepts and feasibility, providing valuable insights that inform subsequent iterations and final production decisions.
Material Testing
Prototyping provides an opportunity to test different materials and assess their performance in real-world conditions. This helps in selecting the best material for the final product. Considerations include:
Material Compatibility: Testing multiple materials during the prototyping phase allows designers to evaluate their suitability for the intended application in terms of mechanical properties, durability, and environmental factors.
Performance Evaluation: Prototyping enables designers to assess how different materials behave under specific conditions, such as temperature variations, chemical exposure, or mechanical stress. This empirical data guides material selection for the final product.
Cost-Benefit Analysis: By comparing the performance and cost of various materials in prototype testing, designers can make informed decisions about which material offers the best balance of performance, cost, and manufacturability for the final product.
Overall, prototype injection molding offers significant advantages in terms of cost-effectiveness, time efficiency, design validation, and material testing, making it a valuable tool for accelerating product development and ensuring the successful launch of high-quality products to market.
Applications of Prototype Injection Molding
Automotive Industry
Component Testing: Prototype injection molding is used to create prototype parts like dashboards, bumpers, and interior components. These prototypes are tested for fit, form, and function to ensure they meet performance, aesthetic, and safety standards.
Design Validation: By producing prototype parts, designers can identify and correct potential design flaws early in the development process, reducing the risk of costly changes later and optimizing the design for manufacturing.
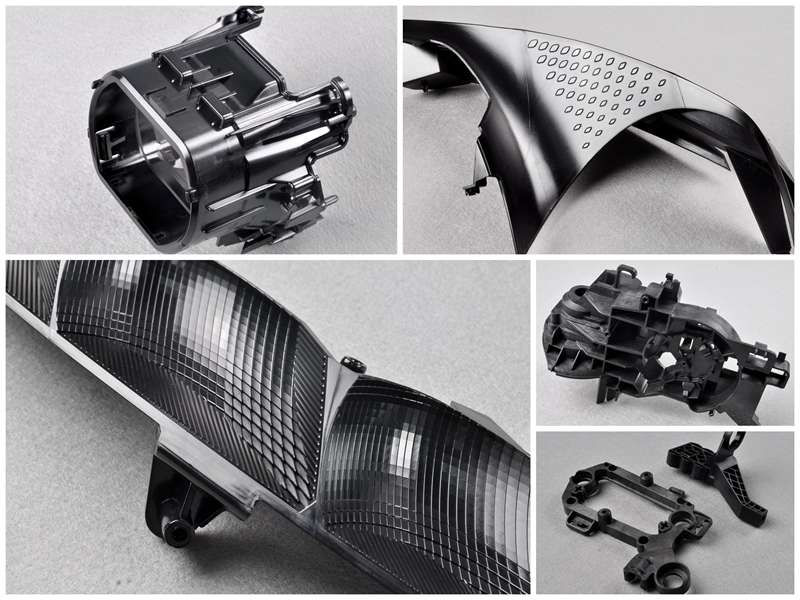
Source: autoprotoway.com
Consumer Electronics
Ergonomic Testing: Prototype injection molding allows for the creation of physical models of products such as smartphones, tablets, and wearable devices. These prototypes can be tested for comfort, usability, and aesthetics to ensure they are user-friendly.
Functional Prototyping: Creating accurate representations of final products enables functional testing of the assembly and interaction of parts, ensuring that complex components fit and work together as intended.
Medical Devices
Precision and Accuracy: Prototype injection molding ensures that medical devices, such as surgical instruments and diagnostic equipment, meet exact specifications and perform reliably under medical conditions.
Regulatory Approval: Prototyping allows for rigorous testing and validation to meet stringent regulatory standards, ensuring that medical devices can be approved by bodies like the FDA before full-scale production.
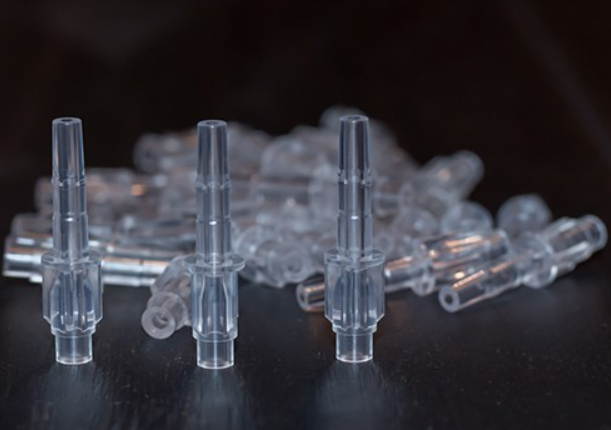
Source: rjcmold.com
Industrial Components
Durability Testing: Prototype injection molding is used to create industrial components such as gears, housings, and enclosures. These prototypes are tested for durability and performance to ensure they can withstand harsh environments.
Design Optimization: Prototyping helps optimize designs for manufacturability, ensuring that industrial components can be produced efficiently and cost-effectively while fitting seamlessly with existing machinery.
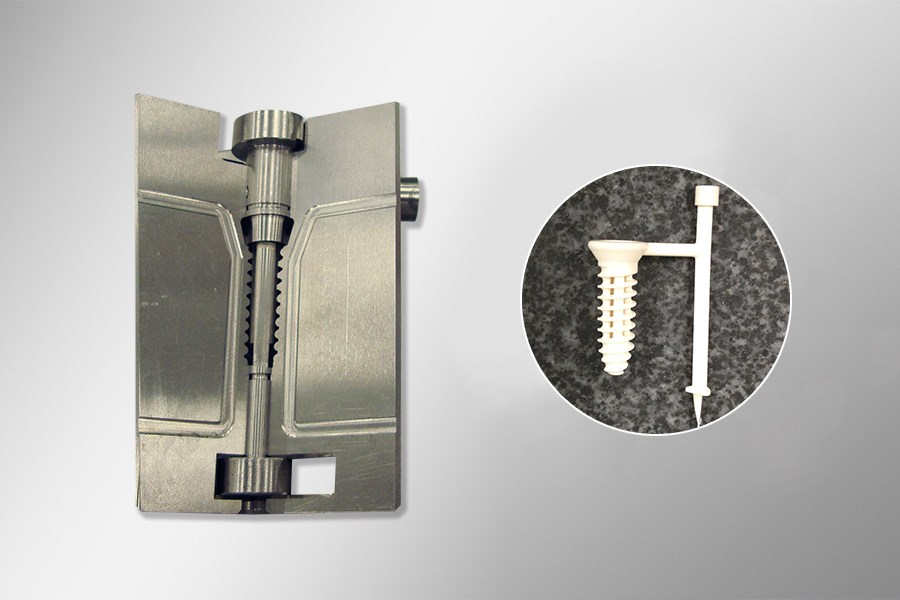
Source: spectrumplastics.com
Conclusion
Prototype injection molding is a crucial process in product development, offering numerous benefits such as cost savings, time efficiency, and the ability to validate and refine designs before mass production.
By addressing design considerations and overcoming challenges, manufacturers can create high-quality prototypes that pave the way for successful final products.
Unionfab Provides Efficient Manufacturing
Unionfab delivers integrated manufacturing solutions across a spectrum of industries, encompassing automotive injection molding among others. Moreover, our suite of services, including 3D printing and CNC machining, caters to diverse requirements.
For further details, please don't hesitate to reach out to us via our Contact Us page.
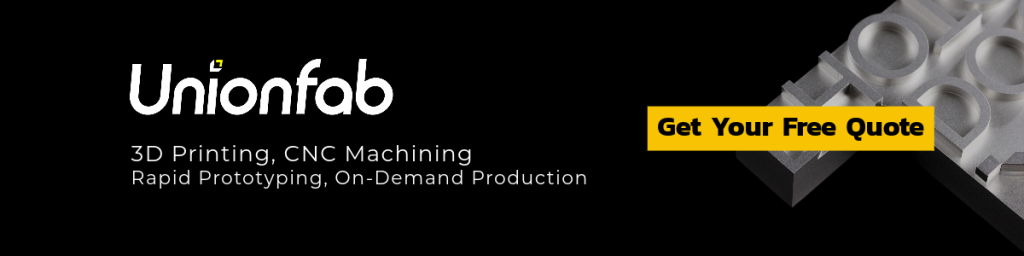