Types of Rivets: A Complete Overview
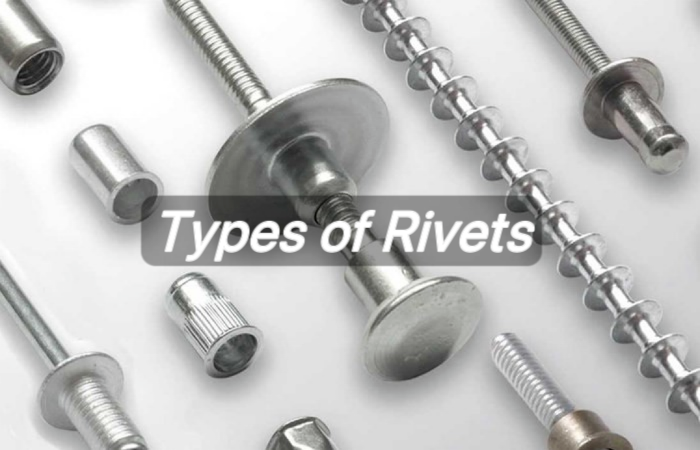
This guide explains the different types of rivets and how they are used. From working processes to common uses, learn everything you need to know.
Introduction
Rivets work by being squeezed or clenched after a hole is drilled, securely joining materials to prevent joints from failing under stress or vibration.
This blog will give a clear overview of the different types of rivets and their common uses.
Overview of Rivets
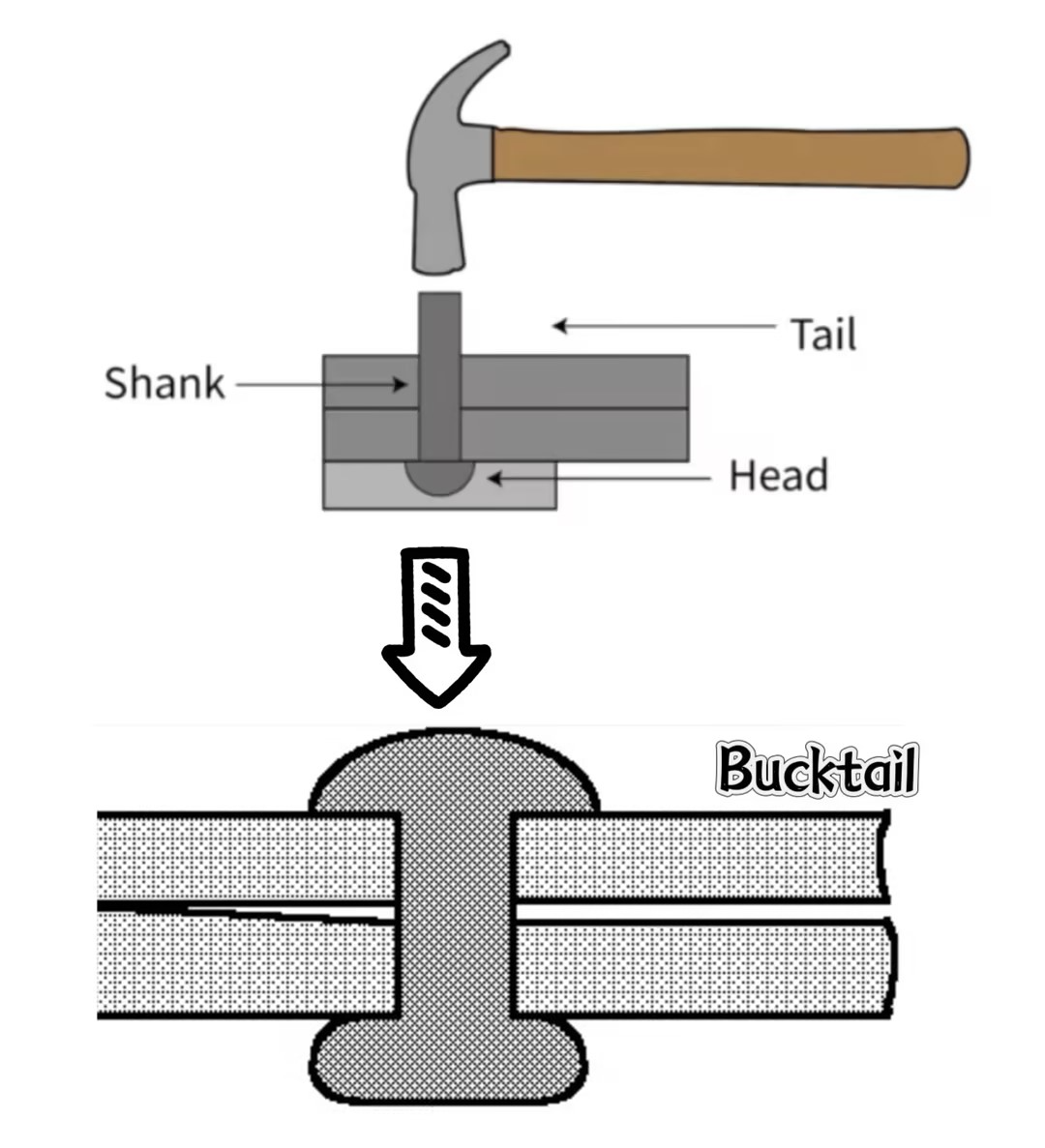
Source: capablemachining.com
Rivets are cylindrical fasteners used to join materials together by fitting through holes and being secured in place. The basic components of a rivet include:
The shank: This is the cylindrical main body of the rivet that passes through the materials.
The head: Rivets have one head attached to the exposed end after assembly. Head styles indicate rivet type.
The bucktail: This refers to the end of the rivet that is deformed after installation to secure it in place, sometimes called a "clenched end".
Historically, rivets have been used for thousands of years, finding applications in structures as early as Ancient Egypt.
However, it was not until the Industrial Revolution that riveting truly came into widespread use. Advances in manufacturing allowed for mass production of rivets out of stronger metals like steel and aluminum.
Materials Used for Rivets
Rivets can be made from a variety of metals depending on the intended application and required properties. The most common materials used for rivets include:
Aluminum - Aluminum rivets are lightweight and corrosion-resistant. They are often used in applications like aircraft construction where weight is critical.
Stainless Steel - Stainless steel rivets are highly durable and resistant to saltwater corrosion. They see wide use in marine and offshore applications.
Copper - Pure copper rivets have excellent resistance to corrosion from water, air or soil contact. This makes them suitable for applications involving alloys or where corrosion is a concern.
Steel - As one of the strongest metal materials, steel rivets are very durable and can withstand heavy stresses. They are commonly used for structural and mechanical works.
Brass - A copper-zinc alloy, brass rivets have good strength properties while being moderately priced. They work well for general purpose applications or where corrosion resistance is needed.
The material used depends on factors like the operating environment, loads imposed, cost constraints, and appearance or color requirements.
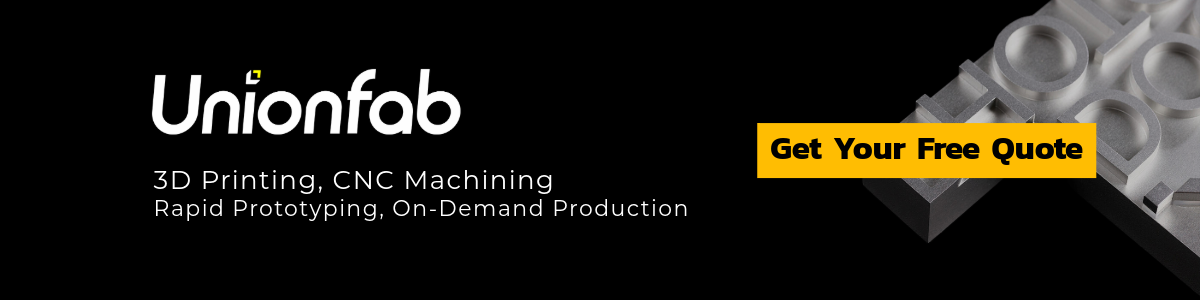
Types of Rivets
Solid rivets have a round head on one side and the shank passes all the way through both materials.
To install, the shank is inserted through holes and then a tool called a rivet setter is used to buckle/form the other end of the shank tightly against the material.
Common examples are used heavily in shipbuilding, bridges and construction equipment where high strength connections are required.
Blind Rivets (Pop Rivets)
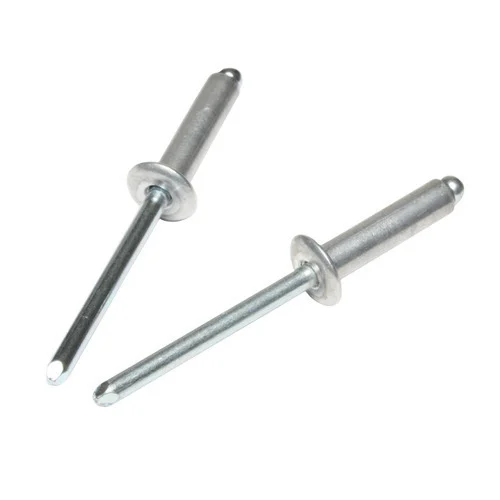
Blind rivets are hollow and have a round head on one side, unlike solid rivets they do not stick out the back.
Installation uses a special rivet gun which pulls the inner mandrel of the rivet while simultaneously flaring/forming its back end.
Often used for internal assemblies like inside of vehicles or equipment cabinets where only one side is accessible.
Semi-Tubular Rivets
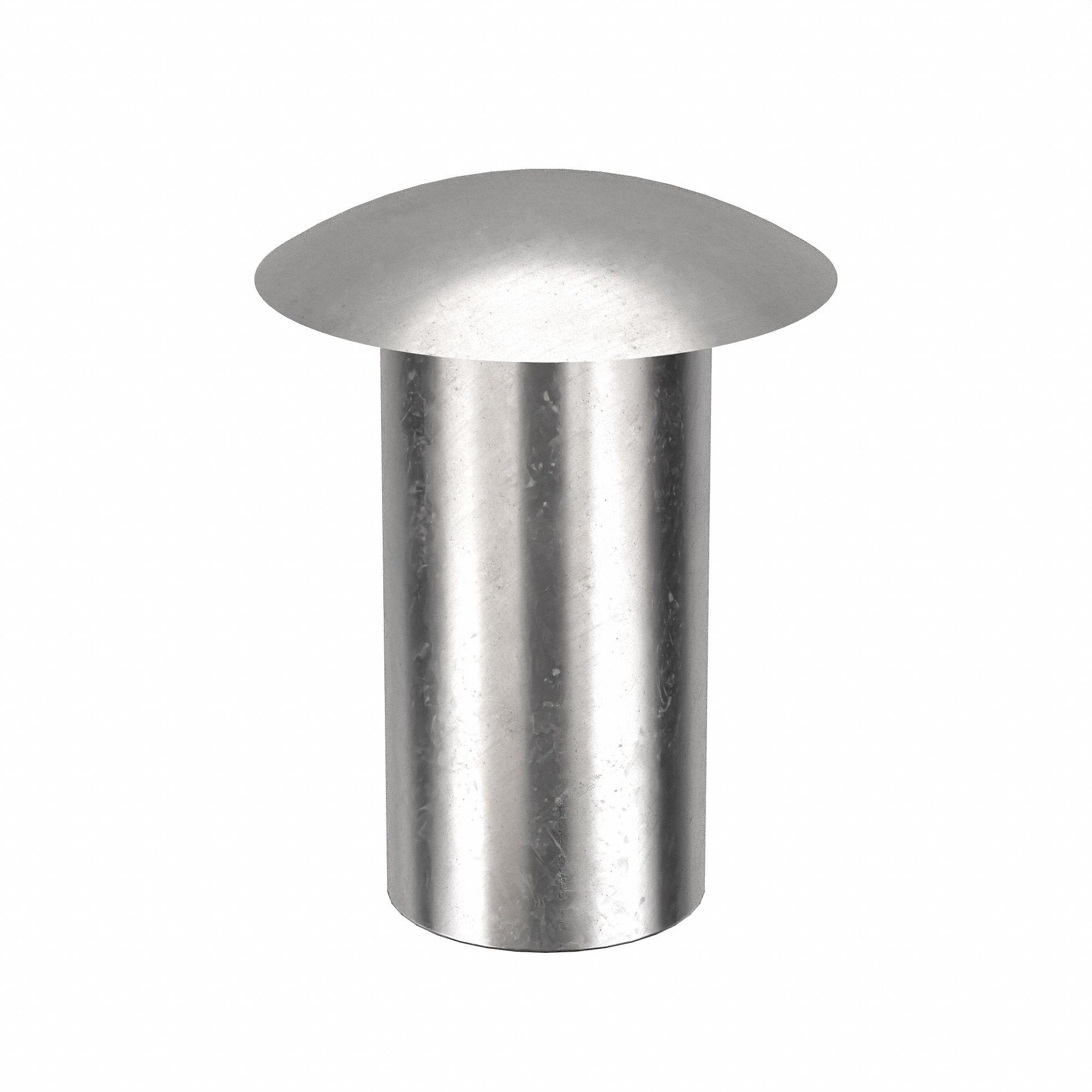
Similar head design to solid rivets but have a hollow shank that can be flared on both ends.
Squeezed into place using a hammer on one end and riveting tool on the other to flare shank.
Common in ductwork, roofing and areas requiring rapid or field installation.
Drive Rivets
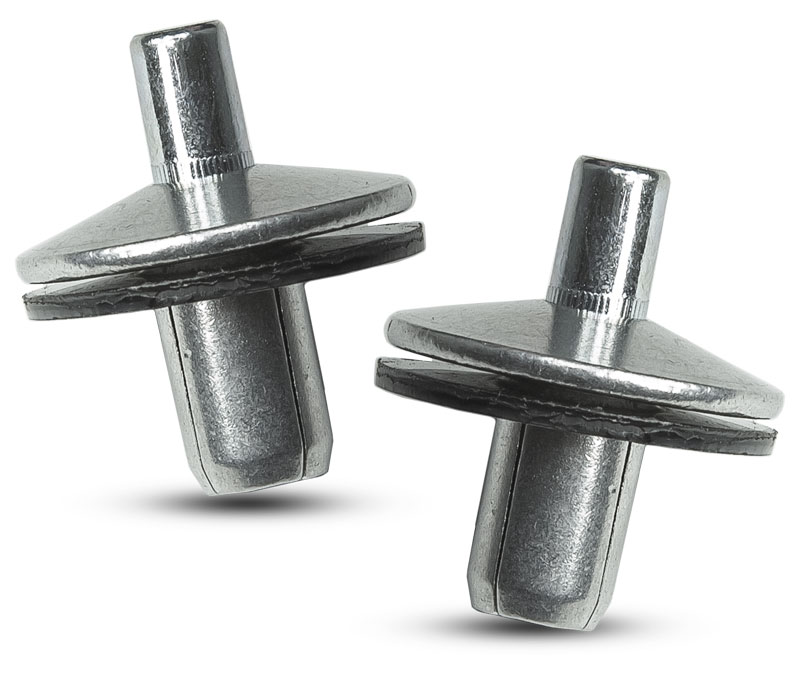
Cylindrical rivets that can be hammered into place without bulky setting tools.
Simply hammered through both materials which flares/spreads shoulders on rivet to lock in place.
Often used for temporary attachments or where tool access poses issues.
Choosing the Right Rivet
There are several factors to consider when selecting the best rivet for the job:
Factors to Consider
Factor | Considerations |
---|---|
Material | Metal type for strength, corrosion resistance etc. As described earlier |
Size | Diameter and length depends on thickness of materials and loads |
Strength | Shear vs tensile strengths based on forces (blind vs solid) |
Application | Permanent or temporary, accessibility, aesthetics |
Tips for Selection
Consider environmental conditions and choose a rivet material suitable for the atmosphere
Match the rivet size to the thickness of materials being joined so it can provide adequate holding power
For load-bearing applications, select rivets with proper tensile or shear strength ratings
Evaluate accessibility and choose rivet types that can be installed from one or both sides
Blind rivets are suitable when only one side is accessible while solid are good for strength
Temporary uses may require drive or snap rivets for quick installation without bulky tools
Flush rivets provide a smooth surface for applications like vehicles where visuals are important
Selecting the proper rivet type upfront can help ensure a reliable and durable fastening solution for the intended application.
Riveting Techniques
Tools and Equipment
Rivet sets - Used to buckle solid rivets and flare shanks on semi-tubular rivets.
Rivet guns - Leveraged tool used to install blind rivets and pop the mandrel out.
Hammers - Used to manually drive rivets like solid and drive types during installation.
Safety and Best Practices
Wear eye protection like safety glasses during installation due to metal debris.
Use a rivet gun properly by following safety instructions for the model.
Ensure rivet sizes match predrilled hole diameters for secure fitting.
Lubricate rivet shanks with oil for easier installation and reduce friction/damage.
Buckle rivets all the way to fully seat them but avoid excessive deformation.
Check blind rivets protrude slightly after setting to confirm proper sealing.
Proper tools, following safety measures and applying best practices helps install rivets efficiently while minimizing risks like injury or improper fastening.
Conclusion
In closing, this overview has examined the important role that rivets play across many industries as a common mechanical fastening method. We explored the basic components and history of rivets, as well as the different materials they can be made from like aluminum, steel and brass.
The major types of rivets - solid, blind, semi-tubular and more - were defined along with their unique installation processes and common applications. Factors to consider when selecting the right rivet type for a job like material, strength and accessibility were also highlighted.
Finally, essential riveting techniques including necessary tools, safety practices and installation tips were reviewed. Following these guidelines will help ensure reliable, durable fastening results on any project.
Unionfab: Your Manufacturing Ally
At Unionfab, we have the advanced 3D printing and CNC capabilities to provide fully customized manufacturing solutions for your unique application requirements.
Use our online tool to receive an instant quote for your next production project. If you have any questions or would like to speak with a Unionfab representative, please don't hesitate to reach out.
We're committed to delivering high-quality, cost-effective manufacturing support to help bring your ideas to life.