Acrylic CNC Cutting Explained: How to Achieve Flawless Results
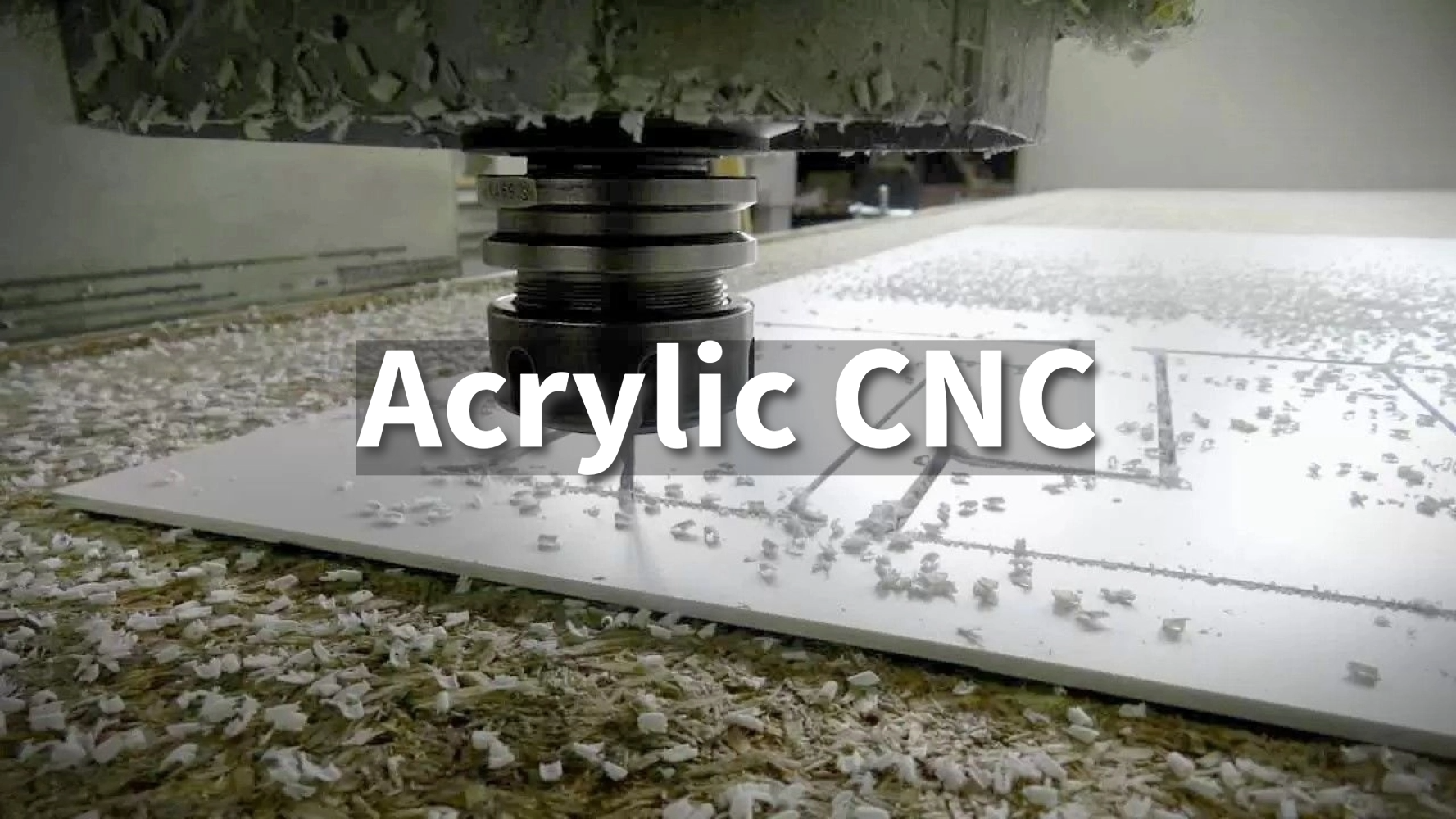
Explore the process of CNC acrylic machining, the benefits of using acrylic in custom projects, and tips for achieving perfect cuts every time.
Introduction
Computer numerical control (CNC) machining is a manufacturing process where a computer uses code to control machine tools like routers and mills. This allows for precise and repeatable cutting of a wide range of materials into complex shapes and designs.
Acrylic, also known as plexiglass, is a thermoplastic material that is light, durable, and produces clear finishes - making it a very popular choice for CNC machining.
In this blog post, we will explore some best practices for CNC machining of acrylic materials. By understanding factors like tool selection, speed and feed settings, cutting strategies, and post-processing techniques.
What is CNC Acrylic Cutting?
CNC acrylic cutting is a manufacturing process that involves using a computer-controlled router or milling machine to cut acrylic material according to a programmed toolpath. The CNC machine follows digital cutting instructions coded from a 3D model or technical drawing to precisely carve the acrylic into the final desired shapes and contours.

Source: waykenrm.com
Acrylic is well-suited for CNC machining due to its properties. It is a lightweight yet durable thermoplastic that can be easily cut without chipping or cracking. Different finishes like smooth, matte, or frosted can be achieved depending on the tool and feeding rate used. Acrylic is also transparent, coming in clear or colorful variations, making it suitable for signage, displays, and parts where visibility is important.
Its versatility means acrylic can be cut into complex geometric forms for applications like prototype enclosures, display stands, lighting fixtures, and more. The cut edges maintain a clean appearance without additional sanding required. Perhaps most valuable of all is the consistency and repeatability of CNC cutting. Identical acrylic parts can be machined time after time without variation in dimensions or quality.
Key Tools and Techniques
The most common CNC machines for cutting acrylic are routers and laser engravers. Routers use mechanized cutting tools while lasers rely on a focused light beam. For cutting thick acrylic, a router is best as it can handle larger material removal rates. Laser engraving works well for finer detail on thinner sheets.
Regardless of the machine, choosing the right tooling is paramount. For routers, a single-flute or spiral-flute acrylic bit cuts clean edges without chipping or melting. Maintain tool sharpness for best results. Laser cutting requires the appropriate lens and power setting matched to the material thickness.
Proper speeds and feeds are also important. Too fast and the acrylic may melt or blacken the cut edge. Too slow wastes time. As a general guideline for routers, start at 1500-3000 RPM for the bit and feed rates between 100-300 inches/minute. Always run tests on scrap material first.
Finally, using a coolant aids productivity and finish. Mist-type coolants like WD-40 help flush away melt residue from the cut kerf. This prevents buildup on tools and leaves a smooth, transparent edge on clear acrylic. Take breaks to refresh the coolant as needed.
Applications of CNC Acrylic Cutting
Thanks to its versatility and finishing capabilities with CNC, acrylic finds usage across several industries:
Signage and display industries use acrylic for precise lettering, logos, and graphics on signs, window clings, and vehicle/building wraps. Complex channel letters and façade designs are easily achieved.
Trade show exhibits and display cases employ acrylic to creates modular and durable casework and booth structures with clear views. CNC ensures consistent graphics and fittings.
Electronics/telecom rely on acrylic for protective covers, housings, and consumer electronic components through multi-part assemblies machined with close tolerances.
Examples of CNC Acrylic Cutting: Consumer Electronic Components
Source: sybridge.comLighting applications leverage acrylic for lens panels, lamp shades, and architectural cove lighting with intricate gradations. Diffuse finishes are attainable.
Prototyping fabricators cut acrylic sheets into enclosure parts, brackets, and testing apparatuses as a durable, transparent alternative to wood/metal.
Medical manufacturers produce examination light hoods, instrumentation panels, surgical guides and teaching models where visibility and sterilization are essential.

Source: sybridge.com
Acrylic's ease of machining thanks to CNC yields a wide range of useful end products across these high-technology industries where seeing through or protecting delicate components is a necessity.
Tips for Perfect Acrylic CNC Cuts
Always use sharp, acrylic-specific cutting tools made of carbide or diamond. Dull tools can melt the plastic.
Properly secure the acrylic sheet with clamps or hold-downs. Vibration from an unsecured sheet leads to chipping.
Test feed speeds and spindle speeds on scrap material first. Go slowly until you find optimal parameters to minimize melting or burrs.
Periodically pump a misting coolant onto the cut line. This washes away melt pool residue and hardened plastic for a flawless edge.
Cut profiles from outside to inside for best chip evacuation where possible. Interior slots may collect debris.
For keyslot or fancy profile cuts, increase clearance between tool and sheet from 0.05-0.125" for clean evacuation of chips.
Consider routing a perimeter sheet edge first if cutting completely separate internal shapes.
Lightly sand or polish the cut edge afterwards if necessary to remove microscopic burnishing for maximum transparency.
Keep tools and machinery well-lubricated per manufacturer recommendations for longevity.
Adhering to best tooling, machine parameter, and sanding practices garnered from experience ensures perfect, chip-free CNC cuts on acrylic projects of any scale or complexity.
Conclusion
CNC technology has opened many doors for precision acrylic fabrication that simply wouldn't be possible through manual means.
Whether it's intricate signage, medical models, or lighting components, the ability to reliably cut complex and accurate acrylic parts on demand has applications across industries.
Following the guidelines discussed - such as using the proper consumables, machine settings, and cooling techniques - empowers CNC operators to efficiently produce flawless acrylic cuts time after time.
Parameters that were once found through costly trial and error can now be replicated with ease. This ultimately lays the foundation for bringing high quality engineered acrylic products to market.
Transform Your Ideas at Unionfab
At Unionfab, we understand the importance of accuracy and quality in every project.
Unionfab delivers exceptional quality and fast turnaround times. Whether you're creating functional prototypes, stylish acrylic parts, or eye-catching displays, we're here to help.
Contact us today to discuss your project requirements and receive a quote. Let’s make your next project a reality with precision CNC machining at Unionfab!
