Cost-Effective CNC Steel Machining: Tips and Tricks
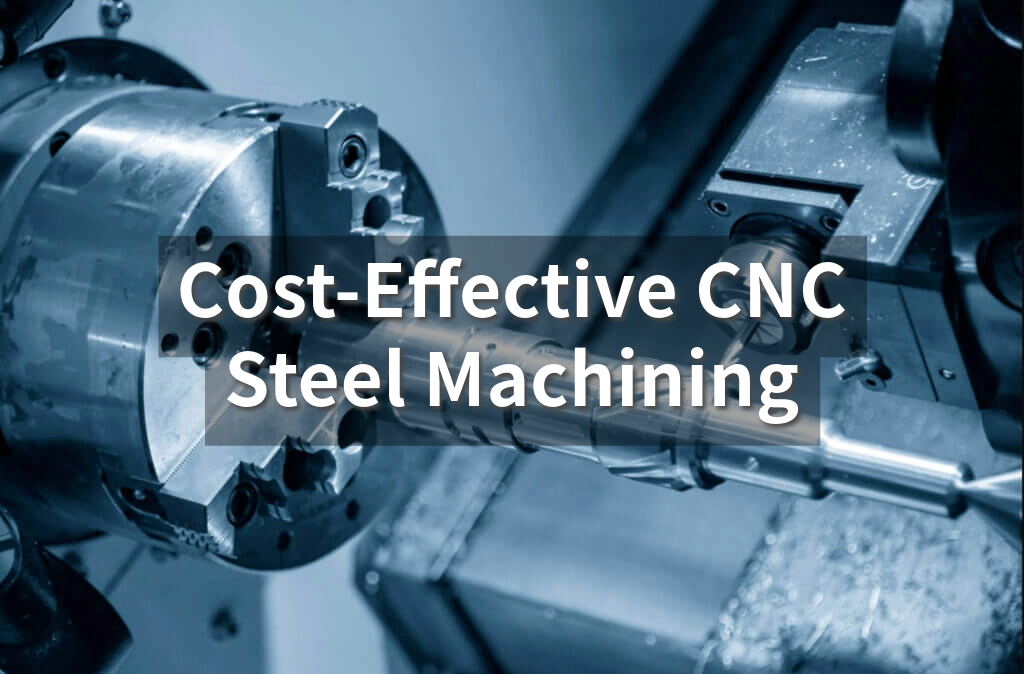
Make your CNC steel machining projects more affordable. Explore our tips and tricks for cost-effective machining.
Introduction
CNC steel machining is a precision manufacturing process that employs computer numerical control to shape steel into desired components. It’s widely used in various industries due to its versatility and accuracy. However, the costs involved in CNC machining can be substantial.
This blog post will delve into practical strategies to optimize your CNC steel machining operations, focusing on cost-efficiency without compromising quality.
What Factors Determine CNC Machining Cost?
The price tag of CNC steel machining is influenced by several factors. Understanding these elements can help you make informed decisions when budgeting for your project.
Labor Costs
The skilled operators who run the CNC machines are a significant expense. Their expertise, experience, and the time spent on each part directly impact the overall cost.
Machine Setup and Calibration
Before production starts, CNC machines require careful setup and calibration. This process involves adjusting machine settings to ensure precision and accuracy. These tasks consume time and resources, contributing to the final cost.
Programming and Software Expenses
CNC machines operate based on detailed instructions created by specialized software. Developing these programs requires skilled programmers and can be time-consuming. Additionally, the cost of software licenses and maintenance adds to the overall expense.
Material Costs
The type and quantity of steel used in the machining process significantly affect the cost. Some steel grades are more expensive than others due to their properties and availability.
Overhead Costs
Beyond direct labor and material costs, there are additional expenses involved in running a CNC machining operation. These include electricity consumption, machine maintenance, facility rent, and other operational costs, collectively known as overhead costs.
Material Selection for CNC Steel Machining
Different types of steel possess varying properties, which impact their machinability, durability, and ultimately, price.
Importance of Choosing the Right Steel Grade for Cost-Effectiveness
Selecting the appropriate steel grade is essential for optimizing costs.
A steel that is too strong or resistant to machining for your specific application will increase processing time and tool wear, driving up expenses. Conversely, using steel that is not robust enough for the intended purpose might lead to part failure and costly rework.
Understanding Steel Grades
Steel is classified into different grades based on its composition and properties. The grade of steel you choose will significantly impact the final product's strength, durability, and cost.
Carbon Steel: This is the most common type of steel, known for its strength and affordability. It's widely used in various applications.
Stainless Steel: Resistant to corrosion and heat, stainless steel is ideal for outdoor or wet environments. However, it's generally more expensive than carbon steel.
Example: Stainless Steel 316: Renowned for its exceptional resistance to corrosion and high temperatures, Stainless Steel 316 is ideal for applications in harsh environments. However, its superior properties come at a higher cost compared to other steel grades.
Tool Steel: Designed for high wear resistance, tool steel is used for cutting tools and molds. It's very hard and durable but also more costly.
Tips for Sourcing Affordable Steel Materials
To further reduce material costs, consider the following strategies:
Optimize material usage: Design your parts to minimize material waste.
Explore alternative steel grades: Evaluate if a less expensive steel grade can meet your project requirements.
Source materials from multiple suppliers: Compare prices and availability to find the best deals.
Consider purchasing in bulk: Buying larger quantities of steel can often lead to cost savings.
Recycle scrap steel: Whenever possible, reuse steel scraps to reduce material expenses.
Optimizing CNC Machining Processes for Steel
To maximize cost-efficiency in CNC steel machining, it's essential to optimize the production process itself. Let’s explore some key strategies.
Efficient Toolpath Strategies for Steel Machining
The path the cutting tool takes, known as the toolpath, significantly impacts machining time and tool wear. Optimized toolpaths can drastically reduce costs. Key strategies include:
High-speed machining: Using higher cutting speeds and feed rates when possible can increase productivity.
Toolpath smoothing: Creating smooth toolpaths reduces vibrations and extends tool life.
Optimized cutting parameters: Selecting the right cutting speed, feed rate, and depth of cut for the specific steel and tool combination is crucial.
Techniques to Reduce Machine Downtime with Steel
Machine downtime, when the CNC machine is idle, translates to lost production time and increased costs. To minimize downtime:
Preventive maintenance: Regular inspections and maintenance of the machine and its components help prevent breakdowns.
Efficient tool management: A well-organized tool storage system and a reliable tool presetting process can reduce tool change time.
Quick tool change systems: Investing in quick tool change systems can significantly reduce downtime between tool changes.
Methods to Minimize Waste and Scrap in Steel Machining
Reducing material waste is a direct path to cost savings. Effective strategies include:
Material optimization: Designing parts to maximize material utilization and minimize scrap.
Scrap recycling: Implementing a system to collect and recycle steel scrap can generate additional revenue.
Process control: Implementing quality control measures to reduce defects and rework can also minimize waste.
Advanced Steel Machining Techniques
To stay competitive in the manufacturing industry, it's essential to embrace advanced machining techniques. Let's explore how these technologies can improve efficiency and reduce costs.
High-Speed Machining Techniques for Steel and Their Cost Benefits
High-speed machining involves running CNC machines at significantly higher speeds and feed rates than traditional methods.
Key Elements of High-Speed Machining
Higher Spindle Speeds: HSM utilizes significantly higher spindle speeds compared to conventional machining. This results in faster material removal rates and improved surface finish.
Increased Feed Rates: By employing higher feed rates, the cutting tool removes more material per tooth, leading to reduced machining time.
Rigid Machine Tools: HSM requires highly rigid machine tools to withstand the increased cutting forces and vibrations.
Utilization of Multi-Axis Machines for Complex Steel Parts(3-axis, 4-axis, 5-axis)Multi-axis machines have the ability to move cutting tools in multiple directions simultaneously. This capability is invaluable for creating complex steel parts with intricate geometries.
Think of it like this:
3-axis: A robot arm moving forward, backward, left, right, and up and down.
4-axis: The arm can also spin around its base.
5-axis: The arm can spin both at its base and at its wrist.5-axis machines are the most flexible, able to create almost any shape you can imagine.
Automation in CNC Steel Machining to Enhance Efficiency
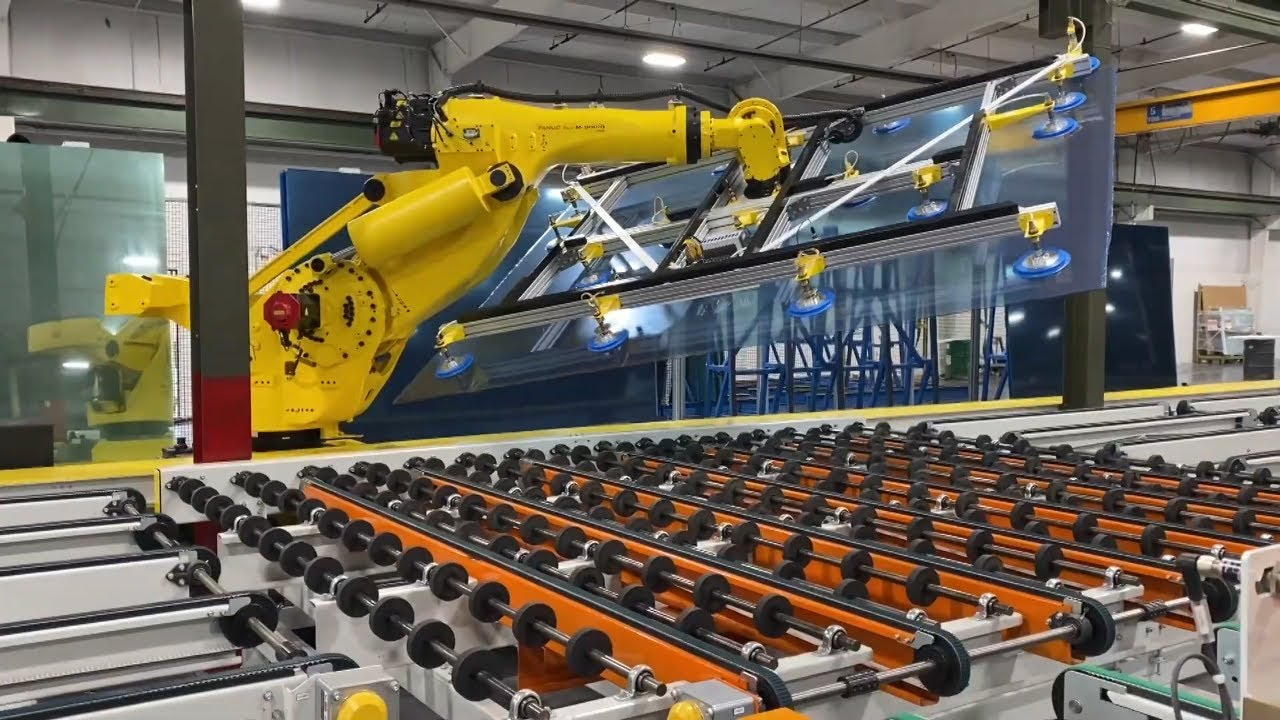
Source: youtube.com>Glassline Corporation Key Technologies
Automation, particularly through the use of robotic arms, has revolutionized CNC steel machining, significantly enhancing efficiency and precision.
Supporting Robotic Automation:
CNC Controllers: Advanced CNC controllers provide precise control over robot movements.
Vision Systems: Cameras and sensors enable robots to perceive their surroundings and make real-time adjustments.
Programming Software: User-friendly software simplifies the programming and operation of robotic systems.
Energy and Resource Management in Steel Machining
In today’s environmentally conscious world, it's crucial for businesses to operate sustainably. Let's explore strategies to reduce energy consumption and waste in CNC steel machining.
Strategies to Reduce Power Consumption in CNC Steel Operations
CNC machines are power-hungry, so reducing energy consumption is vital for cost-efficiency and environmental responsibility. Some effective strategies include:
Energy-efficient equipment: Invest in CNC machines with energy-saving features like variable speed drives and efficient motors.
Optimized machine settings: Fine-tuning machine parameters like spindle speed and feed rate can significantly reduce energy consumption without compromising part quality.
Idle mode and sleep functions: Utilize machine settings to automatically enter low-power modes during idle periods.
Compressed air management: Optimize compressed air systems to reduce energy consumption.
Lighting and HVAC efficiency: Improve the energy efficiency of the machining facility by using LED lighting and optimizing heating and cooling systems.
Recycling and Reusing Steel Materials to Cut Costs
Recycling and reusing steel materials not only benefits the environment but also offers significant cost savings. Consider these practices:
Scrap metal recycling: Implement a robust scrap metal recycling program to recover the value of steel shavings and cuttings.
Material optimization: Design parts to minimize material waste and maximize material utilization.
Second-life materials: Explore opportunities to use recycled steel for specific applications where performance requirements are not critical.
Implementing Sustainable Practices in Steel Machining
Adopting sustainable practices is essential for long-term success. Here are some key considerations:
Environmental impact assessment: Evaluate the environmental impact of your machining operations and identify areas for improvement.
Waste reduction: Continuously seek ways to minimize waste generation throughout the machining process.
Water conservation: Implement water-saving measures in coolant and cleaning processes.
Employee training: Educate employees about sustainable practices and encourage their involvement in environmental initiatives.
Compliance with regulations: Stay informed about environmental regulations and ensure compliance.
Methods to Find Cost-Effective CNC Steel Machining Services
Locating the right CNC steel machining service provider is crucial for achieving cost-effectiveness without compromising quality. Let's explore key strategies.
Strategies for Finding Affordable CNC Steel Machining Services
Identifying potential service providers can be done through various channels:
Online directories: Utilize online platforms that list CNC machining companies.
Industry associations: Connect with industry associations to find reputable service providers.
Referrals: Seek recommendations from trusted colleagues or business partners.
Trade shows and exhibitions: Attend industry events to network with potential suppliers.
Comparing Prices from Different Service Providers
Obtaining quotes from multiple service providers is essential for identifying the best value. When comparing prices, consider the following:
Detailed specifications: Provide clear and detailed part specifications to ensure accurate quotes.
Quantity: Indicate the desired quantity of parts to determine potential volume discounts.
Material: Specify the exact steel grade required for accurate pricing.
Tolerances and finishes: Clearly communicate desired tolerances and surface finishes to avoid misunderstandings.
Hidden costs: Inquire about any additional fees, such as tooling, shipping, or setup charges.
Evaluating Manufacturing Capabilities and Quality
It's essential to assess a service provider's capabilities and quality standards:
Certifications: Verify if the company holds relevant certifications (e.g., ISO 9001) to ensure quality management systems.
Equipment: Inquire about the types of CNC machines and their capabilities.
Experience: Evaluate the company's experience in steel machining and relevant industries.
Quality control: Understand the service provider's quality control processes.
Customer references: Request references from previous clients to assess their satisfaction.
Assessing Turnaround Times and Reliability
Timely delivery is crucial for many projects. Consider the following factors:
Lead times: Inquire about typical lead times for different order quantities.
Production capacity: Assess the service provider's ability to handle your project's volume.
Emergency orders: Determine if the company can accommodate rush orders if needed.
On-time delivery record: Investigate the service provider's history of meeting deadlines.
Considering Additional Services and Support
Beyond the core machining services, consider the following:
Design assistance: Evaluate if the service provider offers design support or optimization suggestions.
Prototyping: Determine if prototyping services are available for testing and refinement.
Finishing services: Assess if additional finishing options (e.g., coating, heat treatment) are offered.
Customer support: Evaluate the responsiveness and helpfulness of the service provider's customer support team.
Industry-Specific Tips for Steel Machining
Automotive: Cost-Effective Machining for Steel Components
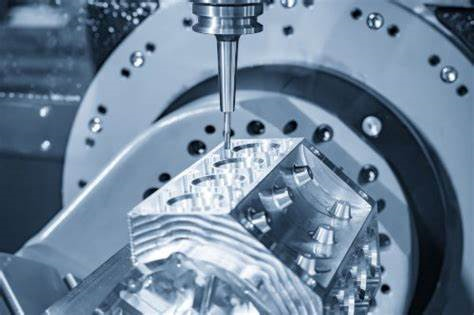
Source: china-machining.com
The automotive industry demands high-volume production of steel components while maintaining stringent quality standards and cost controls. Here are some tips:
Lean manufacturing principles: Implement techniques like just-in-time inventory, standardized work, and continuous improvement to optimize production flow and reduce waste.
Material optimization: Careful selection of steel grades and design for manufacturability can significantly impact costs.
Tool management: Effective tool management, including proper selection, maintenance, and storage, can extend tool life and reduce downtime.
Automation: Invest in automation technologies for repetitive tasks to increase productivity and reduce labor costs.
Aerospace: Precision and Cost Management in Machining Advanced Steel Alloys
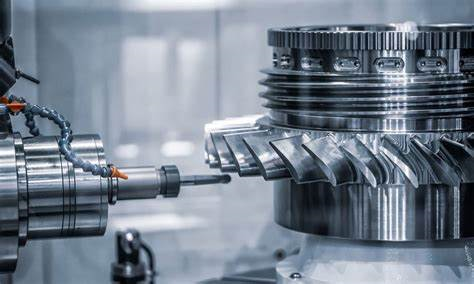
Source: rapiddirect.com
The aerospace industry requires exceptional precision, reliability, and lightweight components. Here are some tips:
Advanced machining techniques: Utilize high-speed machining, five-axis machining, and other advanced technologies to achieve complex geometries and tight tolerances.
Material certification: Ensure that all steel materials used meet stringent aerospace standards and certifications.
Non-destructive testing: Implement thorough non-destructive testing procedures to verify part integrity and safety.
Cost-benefit analysis: Carefully evaluate the cost-benefit of different machining processes and materials to optimize performance and affordability.
Consumer Electronics: Efficient Machining of Steel Parts and Components
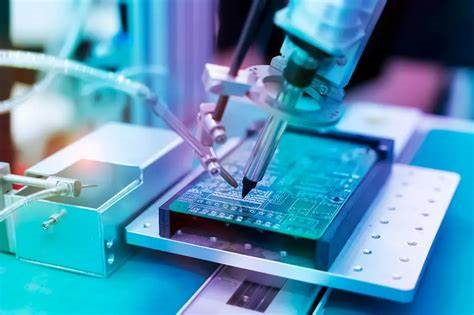
Source: cncpartsxtj.com
The consumer electronics industry demands high-volume production of small, precise steel components with attractive finishes. Here are some tips:
Miniaturization: Focus on miniaturization techniques to reduce material usage and costs.
Surface finishing: Invest in surface finishing processes to enhance the appearance and durability of steel components.
Rapid prototyping: Utilize rapid prototyping to accelerate product development and reduce time-to-market.
Supply chain management: Establish strong relationships with suppliers to ensure consistent material quality and delivery.
Conclusion
By carefully considering factors such as material selection, machine optimization, and industry-specific practices, businesses can significantly enhance the cost-effectiveness of their CNC steel machining operations.
A strategic approach to energy and resource management, coupled with the selection of the right service provider, is essential for long-term success.
By implementing the strategies outlined in this guide, companies can achieve substantial cost savings while maintaining or improving product quality.
Unionfab: Discover Your CNC Steel Machining
Ready to optimize your CNC steel machining process and achieve significant cost savings?
Let Unionfab be your partner in achieving manufacturing excellence.
Contact us today for a free consultation and quote.