Understanding Draft Angle in Injection Molding
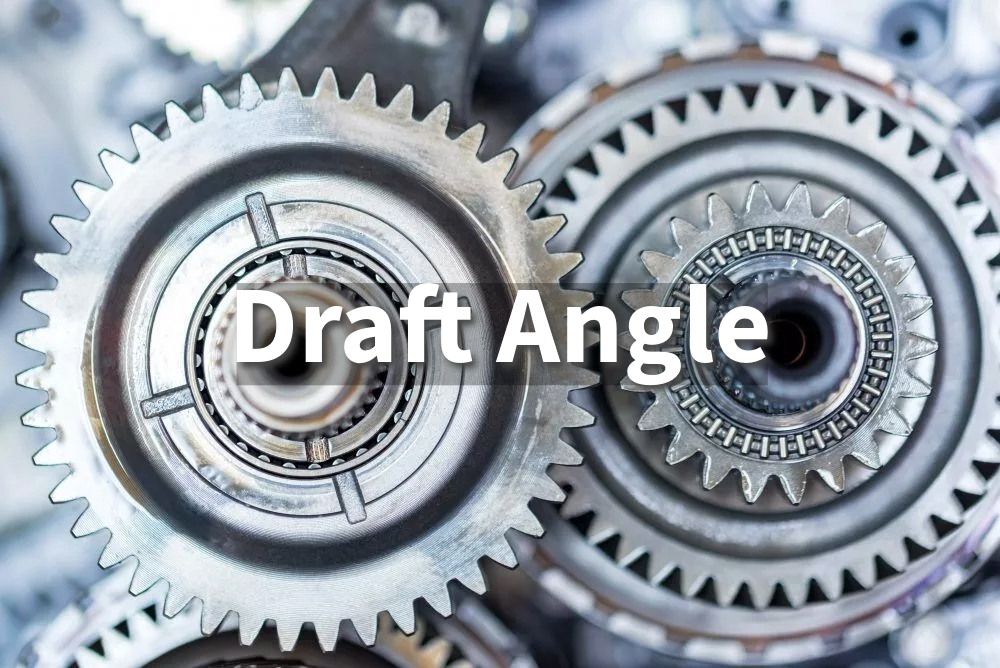
Explore the significance of draft angle in injection molding and tips on how to use it effectively.
What is Draft Angle in Injection Molding?
Definition of Draft Angle
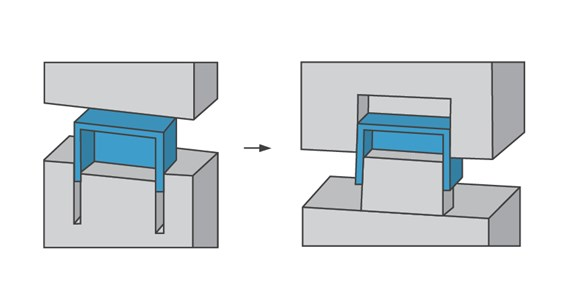
Source: FacFox.com
A draft angle is a specific angle added to the vertical surfaces of a mold used in injection molding.
Instead of being perfectly straight up and down, these surfaces are tilted slightly, typically ranging from 1 to 5 degrees, depending on the type of material and part complexity.
This design feature is essential for the efficient production of molded parts.
Role in Part Design and Mold Release
Part Design
In part design, incorporating a draft angle is critical for ensuring that the part can be manufactured successfully.
The angle allows for smoother transitions between surfaces, which can help in achieving desired geometric features without compromising the integrity of the part.
It also aids in minimizing stress concentrations that could lead to defects during cooling.
Mold Release
The primary function of the draft angle is to facilitate mold release. When a molded part cools, it can shrink and create a tight fit against the mold.
A draft angle reduces the friction between the part and the mold walls, making it easier to remove the part without damage.
Properly designed draft angles help ensure that the parts can be ejected smoothly and efficiently, reducing production time and costs.
Importance of Draft Angle in Injection Molding
How It Improves Part Ejection
The primary importance of the draft angle lies in its ability to enhance part ejection from the mold. By incorporating a slight slope on the mold surfaces, the molded part can slide out more easily after cooling.
This reduces the force required for ejection, minimizing the risk of jamming or sticking, and allows for quicker cycle times in the manufacturing process.
Preventing Damage to Molded Parts
Draft angles also play a crucial role in preventing damage to molded parts. When parts are ejected without sufficient draft, they may experience excessive friction against the mold walls.
This can lead to scratches, surface imperfections, or even breakage. By using an appropriate draft angle, manufacturers can ensure that parts are removed gently, preserving their quality and integrity.
Enhancing Mold Life
Incorporating draft angles can significantly enhance the lifespan of molds. When parts are ejected smoothly, there is less wear and tear on both the mold and the ejection mechanisms.
This reduced stress helps to maintain the mold's precision and functionality over time, leading to fewer repairs and lower production costs. A well-designed draft angle not only improves part quality but also contributes to the overall efficiency and longevity of the manufacturing equipment.
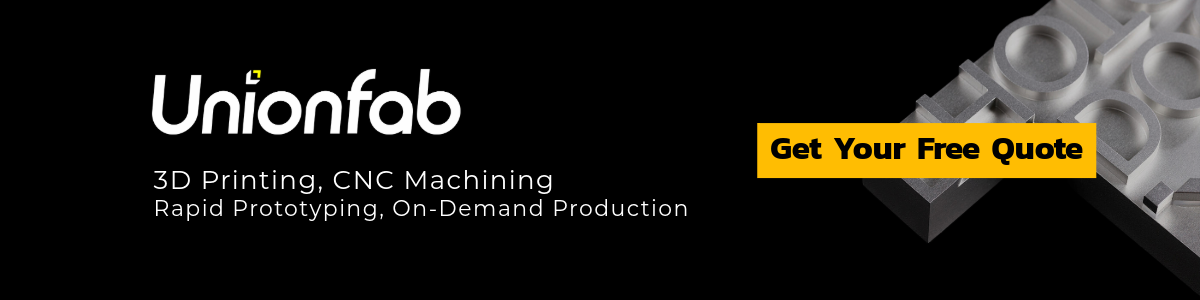
How to Calculate the Right Draft Angle
General Guidelines for Choosing Draft Angles
When determining the appropriate draft angle for injection molding, several factors should be considered. Here are some general guidelines:
Material Type: Different materials have varying shrinkage rates and properties. Softer materials, like PLA, may require a smaller draft angle (around 1-2 degrees), while harder materials, like ABS, might benefit from a larger angle (2-5 degrees).
Part Geometry: The complexity of the part also influences the draft angle. Simple shapes require less draft, while intricate designs with deep features or undercuts may need larger angles to facilitate easier ejection.
Production Volume: For high-production runs, optimizing draft angles can reduce cycle times and improve efficiency. A slightly larger draft angle can be beneficial in these cases.
Mold Design: Consider the overall mold design and how the draft angle will interact with other features. Ensure that the draft angle does not interfere with the functionality of the part or the mold itself.
Draft Angle for Different Materials
The following table provides a quick reference for common materials and their recommended draft angles.
Material | Recommended Draft Angle | Notes |
---|---|---|
PLA | 1-2 degrees | Lower shrinkage, easier release |
ABS | 2-5 degrees | Moderate shrinkage, good durability |
PETG | 2-3 degrees | Good balance of strength and ease |
Polycarbonate | 3-5 degrees | Higher strength, larger angles may help |
Nylon | 2-4 degrees | Flexible, requires careful design |
Additional Considerations
Surface Finish: A smoother finish may allow for smaller draft angles, whereas rougher surfaces may necessitate larger angles to prevent sticking.
Ejection Methods: The type of ejection mechanism (e.g., mechanical or pneumatic) can also impact the required draft angle.
Impact of Draft Angle on Injection Mold Design
Mold Complexity
Simplified Design: By adding draft angles, the mold can be designed with simpler shapes that facilitate easier part ejection. This reduces the need for intricate features or complex ejection mechanisms, which can complicate the mold.
Fewer Undercuts: Draft angles help minimize undercuts, which are areas where the part could get stuck in the mold. Reducing undercuts simplifies the mold design and helps avoid the need for slide mechanisms that add complexity.
Cost
Lower Manufacturing Costs: A simpler mold design typically costs less to manufacture. This is due to reduced machining time and fewer components needed for the mold.
Efficiency in Production: Molds designed with appropriate draft angles can lead to faster cycle times. This means more parts can be produced in less time, ultimately lowering production costs.
Reducing the Need for Secondary Operations
Properly implemented draft angles can significantly reduce the need for secondary operations, which are additional processes required after the initial molding.
Minimized Finishing Work: With adequate draft angles, parts are more likely to come out of the mold with a smooth finish. This reduces the need for sanding, polishing, or other finishing operations that add time and expense.
Fewer Repairs and Adjustments: Parts with well-designed draft angles are less prone to defects like warping or surface flaws. This consistency reduces the need for rework or adjustments after the molding process.
Increased Efficiency: Reducing the need for secondary operations allows manufacturers to streamline their production processes, leading to quicker turnaround times and improved overall efficiency.
In summary, the incorporation of draft angles in injection mold design has a significant impact on mold complexity and cost, while also minimizing the need for secondary operations.
This leads to more efficient and cost-effective manufacturing processes, enhancing the overall quality and productivity of injection-molded parts.
Common Draft Angle Mistakes to Avoid
Undercuts
Undercuts occur when a feature of the molded part prevents it from being easily ejected from the mold. This can happen when the design does not account for adequate draft angles.Mistake to Avoid: Failing to incorporate draft angles in areas with potential undercuts can lead to complex mold designs, which are costly and time-consuming to produce.
Insufficient Angles
An insufficient draft angle is one that is too small to allow for smooth ejection of the part.
Mistake to Avoid: Using draft angles that are less than the recommended range (typically less than 1 degree for many materials) can result in parts sticking to the mold, leading to production delays and increased wear on the mold.
Consequences of Poor Draft Design on Part Quality
Surface Defects
Parts that get stuck in the mold may suffer from scratches or other surface imperfections during ejection. This negatively affects the aesthetic quality and functionality of the final product.
Part Breakage
If a part is forced out of the mold due to insufficient draft angles, it may break or deform, leading to waste and the need for additional production runs.
Reduced Mold Lifespan
Consistently struggling to eject parts can cause excessive wear on the mold, reducing its lifespan and increasing maintenance costs.
By avoiding these common mistakes related to draft angles, manufacturers can enhance the quality of their molded parts, reduce costs, and improve overall production efficiency.
Proper planning and design considerations are essential for successful injection molding.
Best Practices for Designing with Draft Angle
Tips for Incorporating Draft Angles Early in the Design Process
1. Start with a Design Review
Q: When should I consider draft angles in my design?
A: Incorporate draft angles during the initial design phase. This allows for seamless integration and helps avoid costly modifications later.
2. Use CAD Software
Q: How can CAD software help with draft angles?
A: Many CAD programs have features that allow you to visualize and apply draft angles easily. Use these tools to ensure angles are applied consistently throughout your design.
3. Test with Prototypes
Q: Should I prototype my design before finalizing?
A: Yes, creating prototypes can help identify potential issues with draft angles and part release. Adjust designs based on feedback from testing.
4. Collaborate with Mold Designers
Q: How can I ensure my draft angles are effective?
A: Work closely with mold designers and engineers early in the process to get insights into best practices for draft angles based on their experience and expertise.
Conclusion
Draft angles facilitate easier part ejection, prevent damage to molded parts, and enhance mold lifespan.
Properly calculating and incorporating draft angles from the start of the design process can help avoid common mistakes, such as undercuts and insufficient angles.
Ultimately, effective draft angle design leads to higher-quality products and a more efficient manufacturing process.
Optimize Your Injection Molding Design with Unionfab
At Unionfab, we understand the importance of precision in injection molding. Whether you're looking to improve part quality, reduce production time, or streamline mold design, Unionfab has the expertise and technology to bring your vision to life.
Contact us today to discuss your project and experience the difference of working with industry-leading professionals!