How to Create 3D Models for Printing?
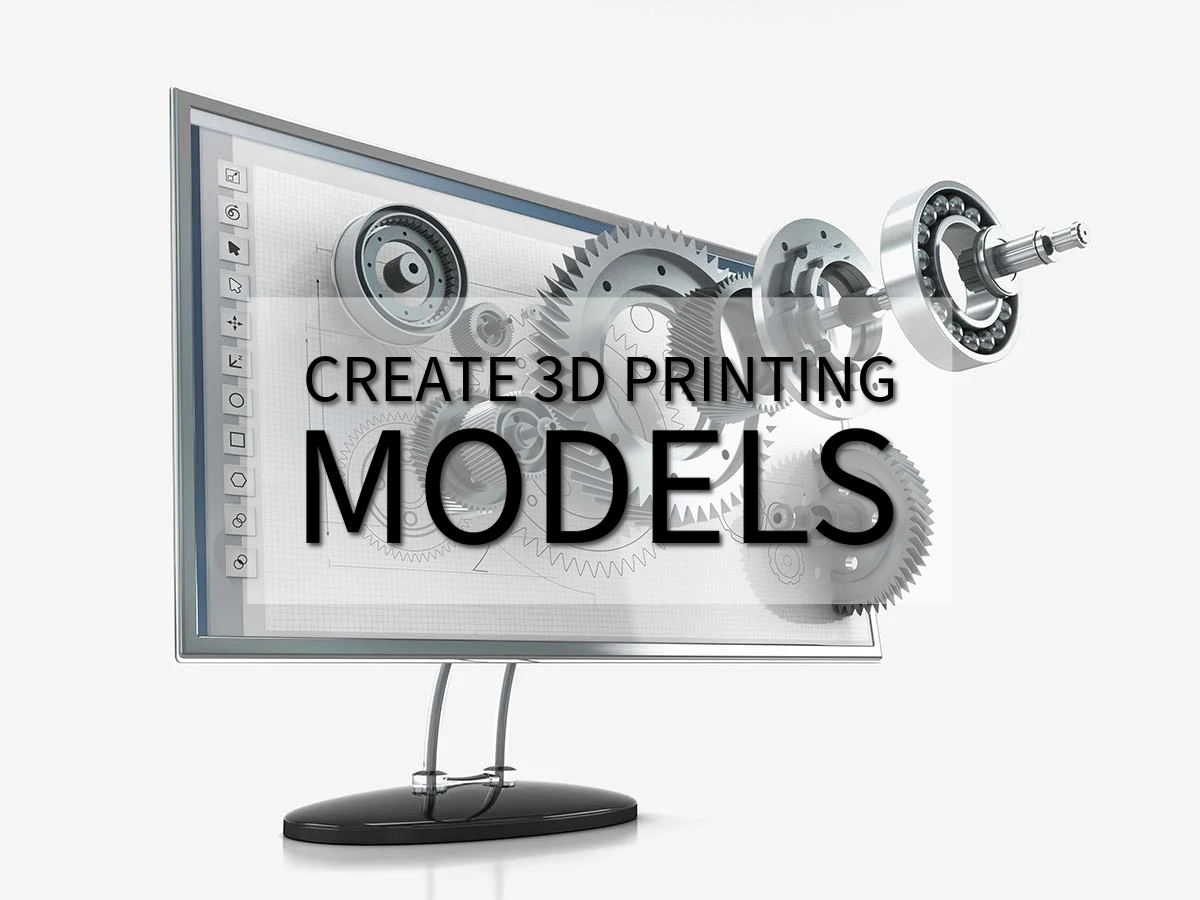
Learn the basics, choose the right software, and prepare your designs for flawless 3D printing results.
Introduction
Creating 3D models for printing is the first and most crucial step in bringing your creative ideas into the physical world. Whether you’re designing prototypes, art pieces, or functional parts, mastering 3D modeling is essential for successful 3D printing.
This guide will walk you through the fundamentals of creating 3D models, helping beginners take their first steps into the world of 3D design.
What is 3D Modeling?
3D modeling is the process of creating a three-dimensional representation of an object or scene using specialized software. These digital models can be manipulated and modified to visualize ideas, concepts, and designs in a virtual environment. It involves several techniques, such as polygon modeling, sculpting, and parametric modeling, each suited for different types of designs.
By mastering 3D modeling, you can turn creative ideas into tangible realities, whether for personal projects or professional endeavors.
Main Applications
3D models consist of vertices, edges, and faces that define the shape of the object. They can be used for a variety of applications, including:
3D Printing: Converting digital designs into physical objects by layering materials.
Animation: Creating animated characters and scenes for movies, video games, and virtual reality.
Architectural Visualization: Designing and visualizing buildings and environments before construction.
Product Design: Developing prototypes and visual representations of consumer products.
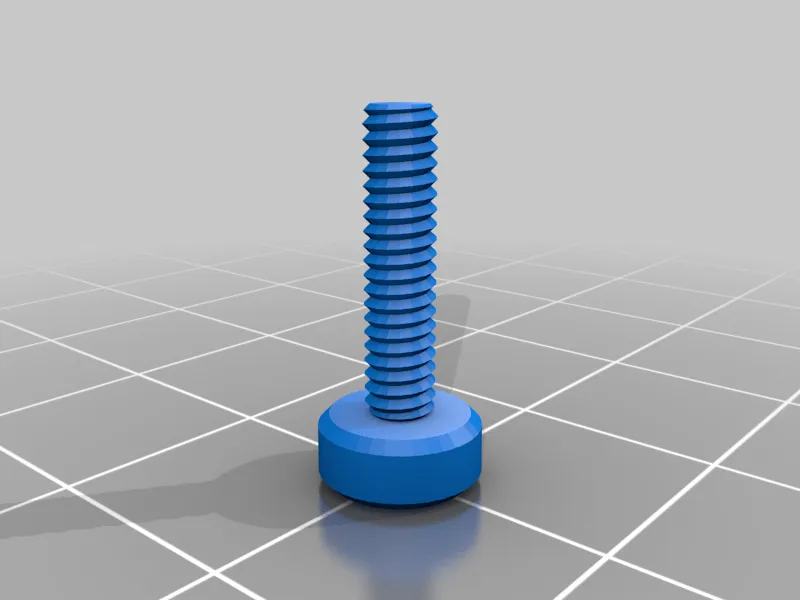
Source: medium.com
Choosing the Right 3D Modeling Software
Selecting the right software is critical to your success in 3D modeling. Here are a few popular options suitable for beginners and experienced users alike:
TinkerCAD
A web-based tool ideal for beginners, TinkerCAD offers a user-friendly interface and simple drag-and-drop functionality.
SketchUp
Known for its intuitive design, SketchUp is great for architectural designs and other projects requiring precision.
Blender
Blender is a robust, open-source software that offers advanced tools for modeling, animation, and rendering, making it ideal for users who want to delve into more complex designs.
Fusion 360
Fusion 360 is a professional CAD software that provides parametric modeling capabilities, making it ideal for designing intricate mechanical parts and prototypes.
ZBrush
ZBrush is a digital sculpting tool for creating detailed models and textures. It lets users sculpt shapes like clay, offering various brushes and tools for intricate designs. ZBrush is widely used in the film and game industries for character and creature modeling.
The Step-by-Step Process to Create 3D Models
Creating a 3D model can be an exciting and rewarding process. Here’s a step-by-step guide to creating 3D models:
Step 1: Conceptualize Your Design
Brainstorm Ideas: Start by sketching your ideas on paper or using digital tools. Think about the purpose of your model and what it should look like.
Gather References: Collect reference images or materials that inspire you. This could include photographs, drawings, existing 3D models, or even concepts created with an image generator to help visualize your design.
Step 2: Choose Your Software
Select a 3D modeling software that fits your needs and skill level. Popular options include TinkerCAD for beginners, Blender for versatile projects, and Fusion 360 for engineering-focused designs.
Step 3: Create a Basic Shape
Start with Simple Geometry: Use basic shapes (cubes, spheres, cylinders) to block out the overall form of your model. This helps establish proportions and layout before adding details.
Use Extrusion and Manipulation: Modify the basic shapes by extruding, scaling, and rotating them to match your design.
Step 4: Refine Your Model
Add Details: Once the basic shape is in place, begin refining your model by adding more complex details. Use tools like beveling, sculpting, or modifiers to enhance features.
Use Reference Images: Refer back to your gathered images to ensure accuracy in details, proportions, and textures.
Step 5: Texture and Material Application
UV Unwrapping: If your model requires textures, unwrap the UVs to create a flat representation of the model’s surface. This allows you to apply textures accurately.
Apply Materials: Use the software’s material editor to add colors, patterns, and surface properties. Experiment with different materials to achieve the desired look.
Step 6: Lighting and Rendering Setup
Set Up Lighting: Position lights in your scene to highlight your model’s features. Consider using different light sources (ambient, point, directional) for depth.
Render the Scene: Once your model is complete and properly lit, render it to produce a high-quality image. Adjust rendering settings for resolution and quality.
Step 7: Review and Iterate
Evaluate Your Model: Take a step back and assess your work. Look for any areas that need improvement or adjustment.
Gather Feedback: Share your model with peers or mentors to receive constructive criticism. Use their feedback to make necessary changes.
Step 8: Prepare for 3D Printing (If Applicable)
Check Printability: If you intend to 3D print your model, ensure it meets the printer’s requirements. Check wall thickness, overhangs, and ensure there are no holes in the mesh.
Export the Model: Save your model in a compatible file format for 3D printing, typically STL or OBJ.
Slicing Your Model for Printing
After finalizing your 3D model, the next step is to slice it for printing. Slicing breaks your model into thin layers and generates G-code, which instructs the 3D printer on how to build the object layer by layer.
Choosing Slicing Software
There are several slicing software options available, each with unique features. Some popular choices include:
Cura: Open-source and user-friendly, suitable for both beginners and advanced users.
PrusaSlicer: Designed for Prusa printers, this software offers advanced settings for various materials.
Simplify3D: A paid option that provides detailed control over the slicing process, including customizable supports and layer settings.
Polydevs: an advanced and intuitive platform for controlling and optimizing industrial 3D printing processes, offering precise control and enhanced productivity.
Repetier-Host: A versatile tool that includes slicing capabilities and can manage multiple printers.
Key Settings to Adjust
When using slicing software, focus on these important settings:
Layer Height: Controls the thickness of each layer. Thinner layers provide finer details but take longer to print.
Infill Density: Determines how much material is used inside your model. Higher densities offer more strength but use more material and increase print time.
Print Speed: Affects how quickly the printer operates. Slower speeds generally lead to better quality.
Temperature Settings: Set the correct extrusion and bed temperatures based on your material to avoid issues like warping.
Support Structures: Add supports for overhangs or intricate features to prevent sagging during printing.
Brim and Raft Options: Improve bed adhesion for models with small bases. A brim adds material around the base, while a raft creates a foundation layer.
Tips for Optimizing 3D Models for Better Printing
Tips | Goals |
---|---|
Simplify Geometry | Keep designs simple to improve accuracy. |
Check Wall Thickness | Ensure walls are thick enough (at least twice the nozzle diameter). |
Evaluate Overhangs | Minimize overhangs to enhance printability. |
Test Scale | Print a smaller version to check proportions. |
Use Fillets and Chamfers | Add rounded edges to improve strength. |
Optimize Orientation | Position the model to reduce overhangs. |
Repair Model Errors | Check and fix common errors before slicing. |
Prepare for Supports | Design efficient supports for easier removal. |
Common Mistakes to Avoid
Ignoring Design Limitations: Always consider the limitations of your 3D printer when designing your model, including build volume and material properties.
Neglecting Model Checks: Use your modeling software’s tools to check for non-manifold edges, holes, or other issues that may cause printing errors.
Skipping Slicing Settings: Don't overlook the importance of slicing settings; take time to understand how they affect your print.
Conclusion
Creating 3D models opens up countless possibilities for innovation and creativity. By following this guide, you can gain the skills and knowledge needed to turn your ideas into reality. With practice and experimentation, you will become proficient in 3D modeling and ready to tackle more complex projects.
Quality 3D Printing Solutions at Unionfab
Unionfab is here to support you on your 3D printing journey. We offer professional services and high-quality 3D printing solutions tailored to your needs. Contact us to learn more!
FAQs
Is it expensive to print 3D models?
The cost of 3D printing depends on factors like printer type, material, model complexity, printing time, and service provider. For hobbyist-level prints, costs are typically lower, with affordable materials like PLA or ABS ranging from $20 to $50 per kilogram. However, industrial 3D printing using materials like metal, Nylon 12, or resin, and more complex processes such as SLS or SLA, can be more expensive.
Can you 3D print from just a picture?
Yes, but it requires additional steps and software to convert the 2D image into a 3D model. The accuracy and quality will depend on the image and the techniques used. Upload your 2D drawing here and get an instant quote from us!
How long does it take to 3D print something?
Printing time depends on factors like model size, complexity, layer height, infill density, and printer speed. Printing can take anywhere from a few hours to several days. For more details, read this article.