Medical Device Prototyping: A Comprehensive Introduction
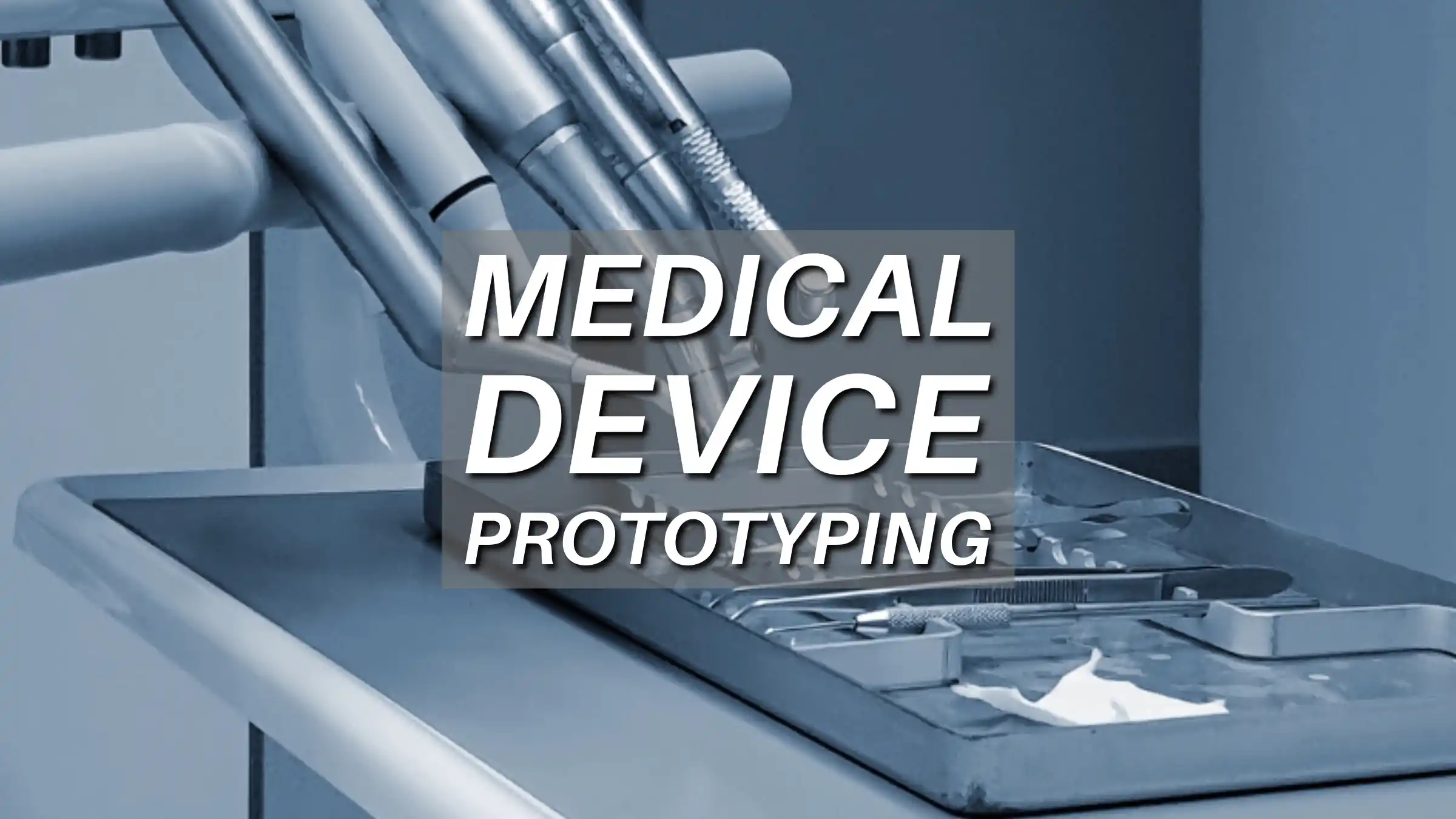
This article provides an introductory overview of medical device prototyping, explaining its material, technology, process, and benefits.
Introduction
Medical device prototyping is the creation of physical models to test and refine the design of a new medical instrument, implant, or equipment.
By creating a tangible representation, engineers and medical professionals can assess the device's functionality, ergonomics, and user experience to ensure that the final product is safe, effective, and user-friendly.
Understanding Medical Device Prototyping
What is Prototyping?
Prototyping, in general, is the creation of a preliminary version of a product to test its features, usability, and functionality.
In the context of medical devices, prototypes can range from low-fidelity, basic models made with readily available materials to high-fidelity, near-production versions that closely resemble the final product.
Why Medical Device Prototyping is Important?
Early Identification of Issues
Prototypes allow engineers and medical professionals to identify and address design flaws early on. This saves time and money compared to fixing problems after large-scale manufacturing has begun.
Improved Functionality
Through testing with prototypes, developers can refine the device's functionality, ensuring it effectively addresses the intended medical need.
Enhanced User Experience
Prototypes allow for user testing, which provides valuable insights into the device's usability and ergonomics.
This can lead to a more user-friendly design that is easier and safer for patients and healthcare professionals alike.
Regulatory Compliance
Medical devices need to meet stringent regulatory requirements to ensure safety and efficacy. Prototyping helps ensure the final product meets these requirements by allowing for early testing and documentation.
Material Selection
Choosing the right materials is a fundamental aspect of medical device prototyping. The materials used impact not only the device's functionality but also its safety and regulatory compliance.
Importance of Biocompatibility
Biocompatibility refers to a material's ability to coexist peacefully with the human body. In medical device prototyping, this is paramount.
Cytotoxicity
The material should not harm or kill living cells in the body.
For a prototype syringe needle, stainless steel or a biocompatible plastic like PEEK (polyetheretherketone) would be preferable to avoid cytotoxicity concerns.
Immunogenicity
The material should not trigger an immune response, such as inflammation or allergic reactions.
Silicone is a commonly used material in catheters due to its low immunogenicity.
However, for a prototype of a long-term heart valve implant, a material with even higher biocompatibility like biocompatible titanium might be chosen.
Genotoxicity
The material should not damage a cell's genetic material.
Biocompatible plastics like polyetherimide (PEI) are often used in prototypes due to their excellent biocompatibility and suitability for various sterilization methods.
Implantation Site
Different parts of the body have varying biocompatibility requirements. For example, materials used in long-term implants need to be highly biocompatible to minimize rejection risks.
A prototype bone screw might utilize a biocompatible metal like titanium alloy, while a prototype tongue scraper could be made from a medical-grade silicone that is gentler on soft tissue.
Criteria for Material Selection
Beyond biocompatibility, several other factors influence material selection in medical device prototyping.
Mechanical Properties
The material needs to possess the necessary strength, flexibility, and other mechanical properties to perform its intended function.
A prototype gripper for surgical instruments might need a strong and rigid material like ABS plastic, while a prototype breathing mask would require a flexible material like silicone to ensure a comfortable fit.
Sterilization Compatibility
The material needs to withstand the sterilization techniques used (e.g., autoclaving, radiation) without degradation.
For example, polycarbonate (PC) is a common choice for prototypes requiring sterilization with gamma radiation.
Imaging Compatibility
For devices used in conjunction with imaging techniques (e.g., X-rays), the material should not interfere with image quality.
For a prototype stent used in angioplasty procedures, a radiopaque material like Nitinol (nickel-titanium alloy) would be preferred as it shows up clearly under X-rays.
Manufacturability
The chosen material should be compatible with the chosen prototyping technique (e.g., 3D printing) and allow for efficient and cost-effective production.
For example, Polylactic Acid (PLA) is a popular choice for 3D-printed prototypes due to its biodegradability and ease of printing, while a complex prototype with intricate features might require a more specialized material like a high-resolution resin for stereolithography (SLA) printing.
Balancing Durability and Cost
Medical device prototyping often involves a balancing act between material durability and cost.
Durability
For certain prototypes, particularly high-fidelity models used for rigorous testing, durability becomes crucial.
A prototype for a surgical instrument used in multiple procedures might benefit from a durable material like stainless steel, while a low-fidelity prototype for a disposable diagnostic tool could utilize a less expensive material like ABS plastic.
Cost
Prototyping is an iterative process, and multiple iterations might be necessary. Here, cost-effective materials are essential for keeping development costs manageable.
Early design explorations for a new catheter design might use a low-cost material like foam core for initial user feedback on ergonomics.
As the design progresses, a more biocompatible and sterilizable material like a medical-grade thermoplastic elastomer (TPE) could be used for functional testing.
Prototyping Technologies
3D Printing
3D printing is an additive manufacturing technique that builds objects layer by layer from digital files. This allows for the creation of complex geometries and intricate features.
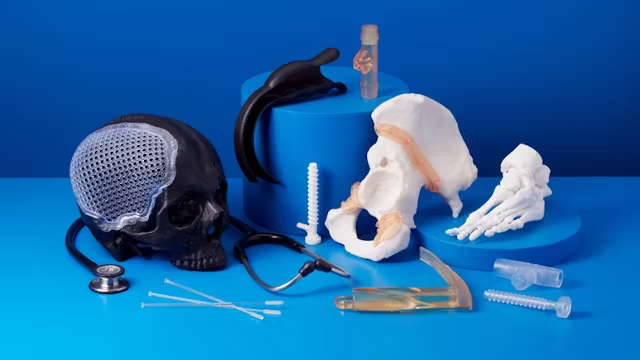
Source: machinedesign.com
Advantages in Medical Device Prototyping
Versatility: A wide range of materials can be used in 3D printing, from biocompatible plastics to metals and even bioresorbable materials. This allows for the prototyping of devices with varying properties.
Customization: 3D printing is ideal for creating customized prototypes tailored to specific needs.
Rapid Iteration: Prototypes can be produced quickly, enabling rapid design changes and testing cycles.
Applications
3D printing is suitable for a wide range of medical device prototypes, from initial concept models to functional prototypes for testing.
Examples include surgical instruments, prosthetics, implants, and drug-delivery devices.
CNC Machining
CNC (Computer Numerical Control) machining is a subtractive manufacturing technique that uses computer-controlled machines to remove material from a solid block to create a desired shape.
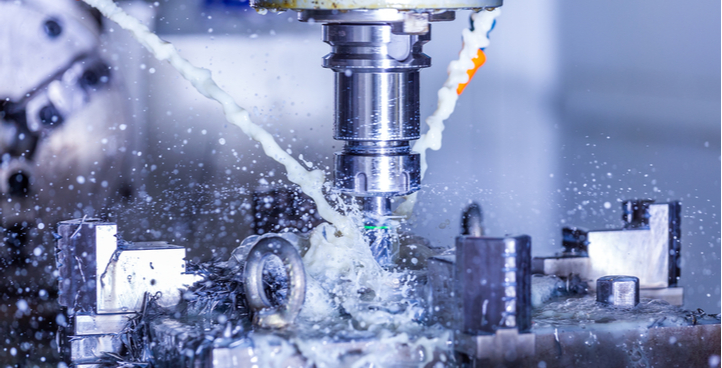
Source: robersontool.com
Advantages in Medical Device Prototyping
High Precision: CNC machining offers exceptional dimensional accuracy and surface finish, ideal for creating high-fidelity prototypes.
Strength and Durability: A wide range of materials can be machined, including metals, plastics, and even ceramics. This allows for the creation of prototypes with the necessary strength and durability for functional testing.
Applications
CNC machining is well-suited for prototyping complex metal parts and devices requiring tight tolerances. Examples include surgical instrument handles, orthopedic implants, and microfluidic devices.
Injection Molding
Injection molding is a high-volume manufacturing technique that creates identical plastic parts by injecting molten plastic into a mold cavity.
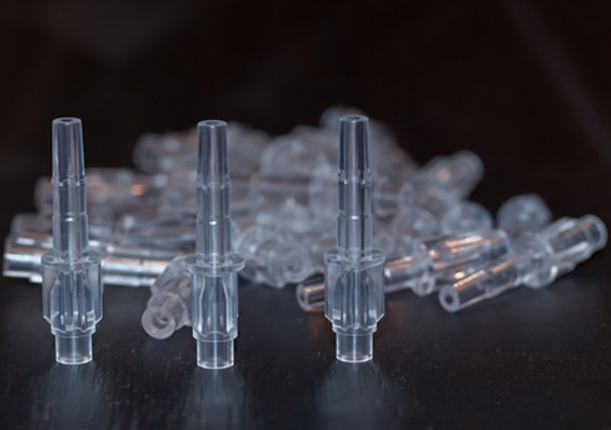
Source: rjcmold.com
Benefits
Cost-Effectiveness: For larger quantities, injection molding becomes a cost-effective way to produce identical prototypes.
High Quality: Injection molding produces parts with high dimensional accuracy and surface finish.
Applications
Injection molding can be used to prototype plastic components intended for mass production, such as disposable medical devices, casings for medical equipment, and drug delivery devices.
Laser Cutting
Laser cutting utilizes a laser beam to precisely cut shapes from a sheet of material.
Benefits of Medical Device Prototyping
Speed and Precision: Laser cutting offers fast and accurate cutting of various materials, ideal for creating flat prototypes or parts with intricate details.
Material Versatility: Laser cutting can handle a variety of materials, including plastics, wood, and some metals.
Applications
Laser cutting is suitable for creating low-fidelity prototypes, stencils for forming parts, and gaskets or seals for prototypes requiring specific shapes.
Prototyping Stages
Medical device prototyping is an iterative process, meaning it involves multiple cycles of design, creation, testing, and refinement.
Creating the Initial Prototype
This stage focuses on translating the initial concept into a physical model. The complexity of the prototype depends on the stage of development and the intended purpose.
Low-fidelity prototypes might be created using readily available materials like cardboard or foam core. These prototypes are quick and inexpensive, allowing for early user feedback on basic form and function.
Mid-fidelity prototypes might utilize 3D printing or CNC machining to create more realistic models with some functional elements. This allows for testing of user interaction and basic functionality.
Functional Testing and Iteration
Once the initial prototype is built, it's time for rigorous testing. This stage involves evaluating the device's performance against its intended purpose.
Usability testing: This involves observing users interacting with the prototype to identify any ergonomic or usability issues.
Functional testing: This assesses the device's ability to perform its intended function effectively.
Safety testing: This ensures the prototype doesn't pose any risks to users or patients.
Based on the test results, the design is iterated upon. This might involve modifying features, changing materials, or even going back to the drawing board for a more significant redesign.
Refining and Optimizing the Design
Through multiple rounds of testing and iteration, the prototype is gradually refined and optimized. This stage involves:
Incorporating user feedback: Feedback from users and healthcare professionals is crucial for improving the device's usability and functionality.
Material selection: As the design progresses, more biocompatible and durable materials might be chosen for functional testing and regulatory compliance.
Detailed engineering: Detailed engineering drawings and specifications are created to ensure the final product can be manufactured consistently and meet quality standards.
Testing and Validation
Mechanical and Electrical Testing Procedures
Mechanical Testing
These tests evaluate the device's ability to withstand various physical stresses and strains it might encounter during use.
This could involve testing for tensile strength, compression strength, fatigue resistance, and wear resistance.
For example, a surgical instrument prototype might undergo testing to ensure it can withstand the forces applied during surgery.
Electrical Testing
For devices with electrical components, rigorous electrical testing is essential.
This might involve evaluating electrical safety, electromagnetic compatibility (EMC), and functionality of electrical components.
For instance, a pacemaker prototype would undergo extensive electrical testing to ensure it delivers electrical pulses safely and reliably.
Ensuring Compliance with Regulatory Standards
Regulatory bodies: Depending on the location, regulatory bodies like the US Food and Drug Administration (FDA) or the European Medicines Agency (EMA) set the standards for medical devices.
Consulting with regulatory experts: Seeking guidance from experts can help navigate the regulatory landscape and ensure compliance throughout the development process.
Following established design control procedures: These procedures document design decisions, testing results, and risk assessments, creating a clear audit trail for regulatory bodies.
Material Selection: By selecting biocompatible materials during prototyping, developers can ensure the final product meets biocompatibility standards.
The Role of Clinical Trials and User Feedback
While testing on prototypes plays a crucial role, it doesn't replace the need for clinical trials.
Clinical trials involve testing the device in a controlled setting with actual patients. This provides valuable data on the device's safety and effectiveness in a real-world environment.
User feedback gathered throughout the prototyping process remains crucial. This feedback, from both healthcare professionals and potential patients, helps refine the device's design and ensure it addresses user needs effectively.
Benefits of Medical Device Prototyping
Accelerating Time-to-Market
Prototyping allows for early identification and correction of design flaws. This prevents costly delays that can occur if problems are discovered later in the development process.
By enabling rapid iteration and testing cycles, prototyping helps bring innovative medical devices to market faster.
Reducing Development Costs
Prototyping allows for catching and fixing design issues early on when they are inexpensive to address.
This prevents costly rework later in the development process when changes might require retooling or restarting production runs.
Enhancing Product Quality and Safety
Prototyping facilitates rigorous testing of the device's functionality, user experience, and safety. This allows for identifying and addressing potential problems before the device goes into full production.
By ensuring a high degree of safety and user-friendliness, prototyping ultimately contributes to a higher-quality medical device that delivers optimal patient care.
Conclusion
Medical device prototyping is an essential process that translates promising concepts into tangible models for rigorous testing and refinement.
By creating physical models, engineers and medical professionals can refine designs, identify and address issues early on, and ensure the final product is not only functional but also safe, user-friendly, and meets regulatory requirements.
This iterative process ultimately leads to better medical devices, faster development times, and improved patient care.
Unionfab Provides Professional Products for Various Industries
Unionfab offers a comprehensive range of technology services and materials options.
By leveraging our knowledge of various materials, manufacturing techniques, and quality control processes, Unionfab helps companies across numerous industries seeking reliable prototyping and development solutions.
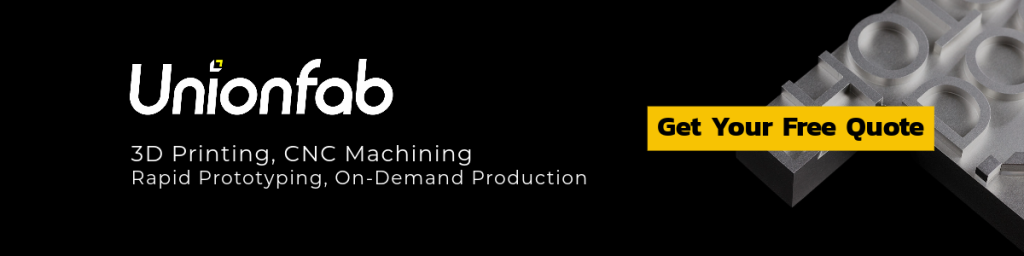