Rapid Tooling Explained: Faster Prototyping, Efficient Production
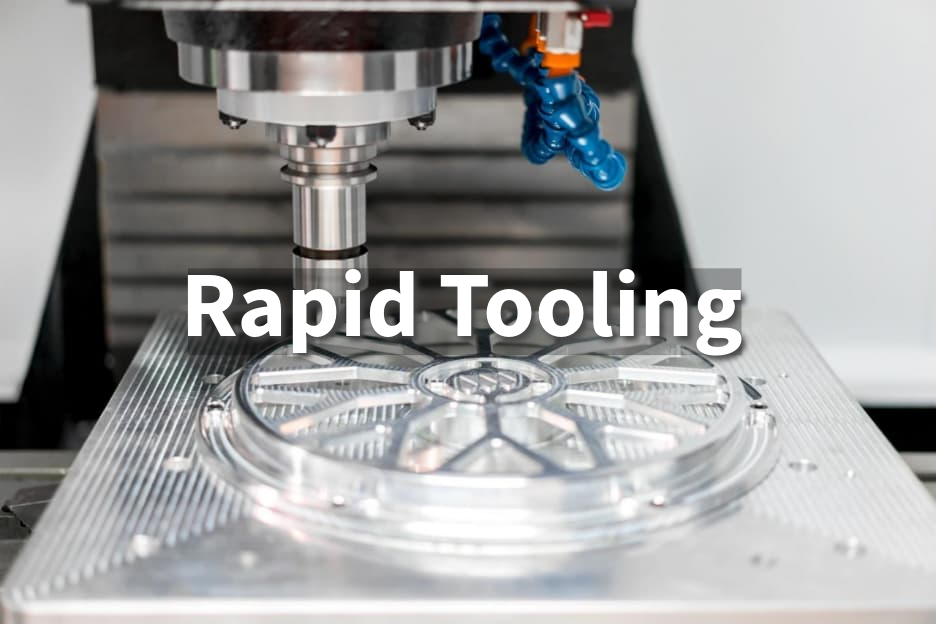
Explore how 3D printing transforms rapid tooling by providing quick, cost-effective manufacturing solutions for high-performance and complex designs.
Introduction to Rapid Tooling
Rapid tooling refers to a group of manufacturing methods that use 3D printing technologies to quickly produce tooling, molds, and prototypes. With rapid tooling, companies can minimize the time required to fabricate tooling and get new products to market faster compared to traditional tooling methods.
What is Rapid Tooling?
Rapid tooling involves using 3D printing processes like stereolithography, multi-jet fusion, and metal binder jetting to build tooling like injection molds, compression molds, and casting dies in just days or weeks. This is much faster than the months typically required to machine tooling from raw materials through conventional methods.
There are a few main types of rapid tooling:
Prototype Tooling: Used to test initial designs and produce very low volumes (10-100 parts) of prototypes. Materials include various photopolymers and plastics.
Hard Tooling: Can produce volumes from hundreds to tens of thousands of parts. Materials include nylons, elastomers, and metal alloys printed using binder jetting.
Production Tooling: Capable of high volume production runs like injection molding. Materials include tungsten carbide infiltrated with cobalt for strength and wear resistance.
The speed and shortened development cycles of rapid tooling allow companies to test new product designs more quickly and get customized or low-volume parts to customers faster.
How Rapid Tooling Works
Overview of the Process
There are several basic steps involved in the rapid tooling process:
A 3D CAD model of the final part is created along with any necessary draft angles, parting lines, ejector pin locations, etc.
The CAD model is sliced into 2D layers and 3D printing occurs, layer by layer.
Once printing is complete, any support material is removed in a process like acid baths.
Post-processing may include infiltration, machining of surfaces, or adding inserts.
The finished rapid tool can then be used for tasks like prototype molding, casting, or injection molding.
Common Materials and Techniques
Some materials often used in rapid tooling include plastic photopolymers printed via stereolithography for soft molds, nylon powders printed by multi-jet fusion for hard tooling, and tungsten carbide infiltrated with cobalt for durable injection molds.
Specific 3D printing methods employed contain stereolithography, multi-jet fusion, and binder jetting of metal powders.
Comparison to Traditional Tooling
Unlike slow subtractive machining of tools from solid blocks, rapid tooling is an additive process where materials are selectively joined. This allows building complex interior cavities and enables tools to be finished in days rather than months.
While rapid tools have more limited lifespan, the accelerated design cycles allow getting ideas to market much faster.
Common Rapid Tooling Techniques
3D Printing
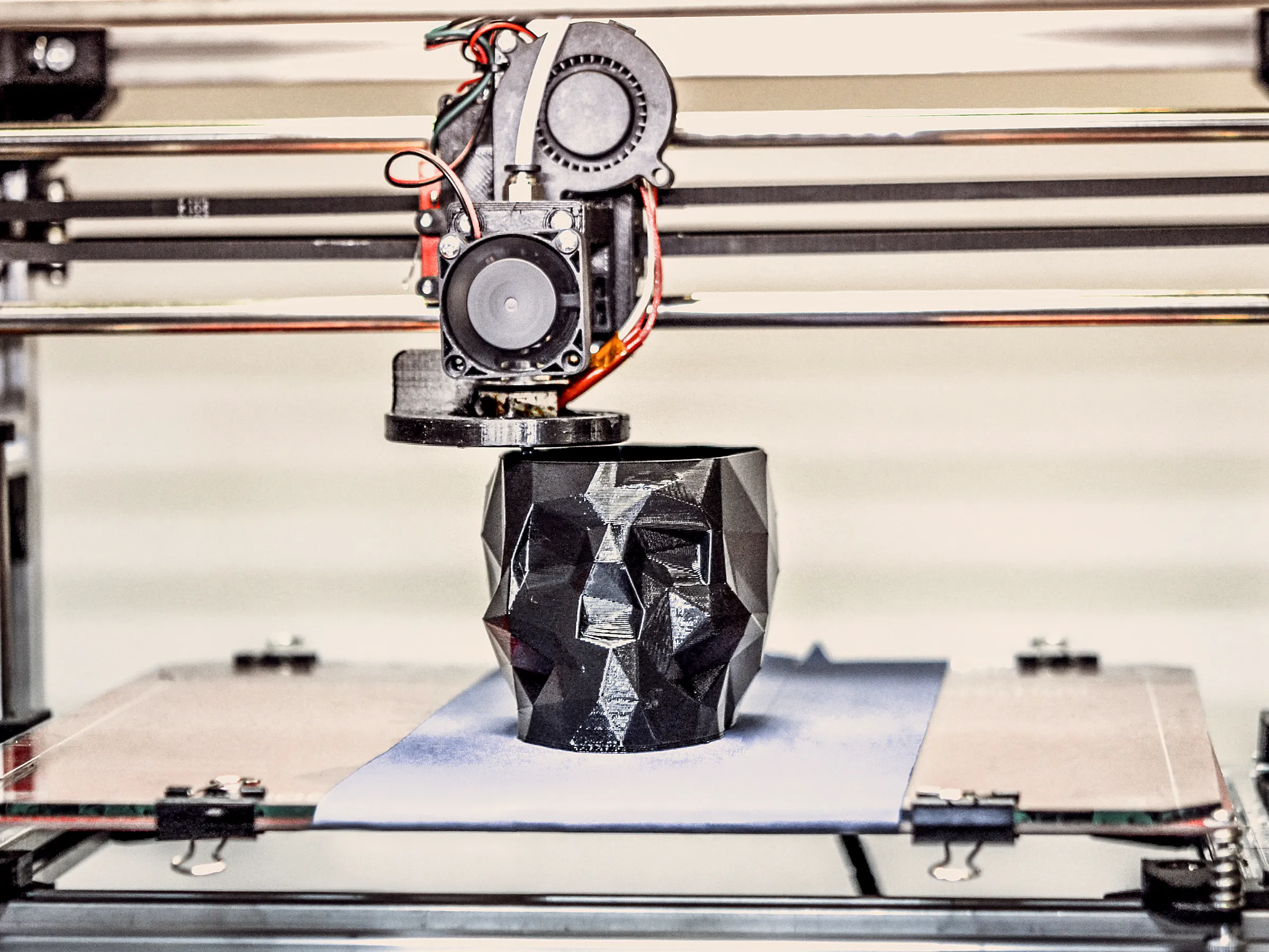
Source: wired.com
Additive manufacturing processes like stereolithography, multi-jet fusion and binder jetting allow building tools layer-by-layer directly from 3D CAD files. This enables quick design changes and complex internal features.
CNC Machining
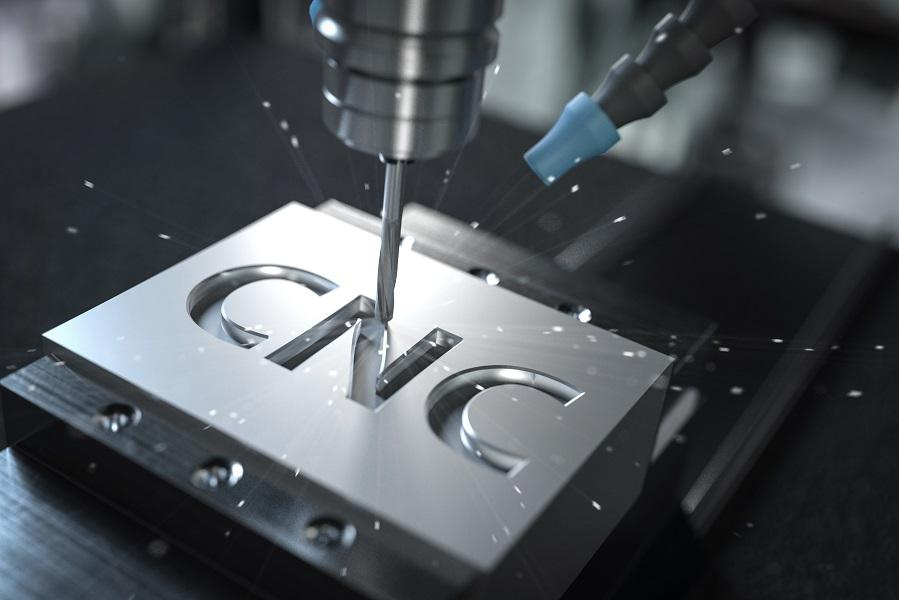
Source: stuermer-maschinen.de
Computer numerical control machining utilizes subtractive methods to precisely cut geometries in pre-fabricated tooling blocks. While slower than 3D printing, it achieves very high precision and surface quality.
Silicone Molding
A 3D printed or CNC'd mold cavity is filled with liquid silicone rubber that hardens into a flexible mold. This allows low-cost prototype parts in plastics or metals to be cast.
Reaction Injection Molding
A rapid urethane tool produces molds used for reaction injection, where liquid components react and cure inside the mold without high pressures.
Electroplating
Thin metal like nickel can be electroplated over a 3D printed mandrel or mold to create a durable shell. This enables functional metal prototypes.
Rapid Tooling Types: Soft Tooling vs Hard Tooling
Soft Tooling
Made from plastic photopolymers using stereolithography 3D printing.
Used for design validation with very low volumes under 100 units.
Materials are flexible and less durable, good for conceptual models.
Printing is fast but parts have low strength and wear out quickly.
Hard Tooling
Manufactured using multi-jet fusion or binder jetting of nylon or metal powders.
Capable of medium runs from hundreds to tens of thousands of parts.
Materials like nylon and infiltrated metals provide structure and durability.
Tools have a longer usable life than soft but take slightly longer to print.
Comparison Table:
Soft Tooling | Hard Tooling | |
---|---|---|
Material | Plastic | Nylon or metal |
Purpose | Rapid design testing | Higher production volumes |
Characteristics | Flexible | Strong and long-lasting |
Usage | Prototypes under 100 units | Medium runs from hundreds to thousands |
Common process | Stereolithography | Multi-jet fusion or binder jetting |
Lifespan | Short | More durable |
Common Materials Used in Rapid Tooling for 3D Printing
Plastics
Photopolymers: Cured by UV light, used for prototype parts and soft tooling inserts with stereolithography (SLA).
Polyamides: Nylon powders like PA 12 for multi-jet fusion (MJF) give tough but flexible properties ideal for hard tooling.
Metals
Stainless Steel: Durable metal for binder jetting processes like binder jetting of tooling exposed to heat, force or moisture.
Cobalt Chrome: Used for electron beam melting (EBM) of high-strength, biocompatible medical prototypes and production tools.
Composites
Silicone Rubbers: Flexible material for soft tooling allows easy removal of prototype parts without damage.
Infiltrated Metals: Tungsten carbide strengthened with nickel or cobalt binder creates abrasion-resistant, precision surfaces for injection molds.
Benefits of Rapid Tooling
Speed
Rapid tooling allows the quick fabrication of molds, dies and prototypes in just weeks rather than months.
This greatly reduces the time needed to iterate designs, obtain user feedback, and accelerate manufacturing startups.
Cost-Effectiveness
By compressing design-to-production cycles, rapid tooling cuts costs associated with storage, equipment rental and lengthy machining times of conventional tooling.
It may also reduce the need for extensive physical prototyping.
Flexibility
Additive techniques provide flexibility to easily modify tool designs on the fly.
Changes can be made in software and reprinted, versus expensive reworks of subtractively machined tools. Late stage adjustments are simpler.
Quality
While often used for prototypes, advances in materials like infiltrated tungsten carbide ensure rapid tools can produce accurate production-level parts in medium volumes.
Output quality remains high and consistent.
Applications of Rapid Tooling
Automotive
Rapid tooling allows building molds for interior/exterior prototyping and low-volume production parts.
Real-World Example:Ford*Ahead of this year’s launch of its first European-built, all-electric model, Ford is using a new 3D printing centre to increase efficiency and quality in production processes.*Twelve 3D printers print tools and fixtures for Cologne vehicle production and are also capable of printing components for pilot and small series vehicles

Source: media.ford.com
Aerospace
Critical flight hardware can be tested using rapid injection molds before committing to expensive tooling.
Real-World Example:AirbusAirbus evaluates jet engine blades through investment cast prototypes from rapid urethane molds to catch design issues.
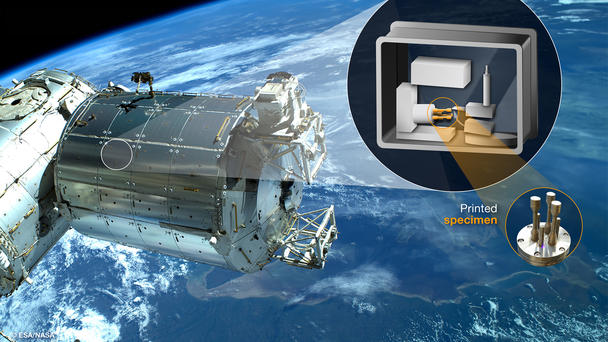
Source: airbus.com
Challenges and Limitations
Potential Downsides
Surface finish on early printed tools may not compete with machined quality.
Limited lifespan - additive tools can fail sooner than conventional tooling.
High initial costs - 3D printers and materials represent a major investment.
Strategies to Overcome Challenges
Post-processing like machining or polishing enhances surfaces without compromising speeds.
Combining 3D printing with traditional methods like CNC milling utilizes each technique's strengths.
Outsourcing to specialized rapid tooling service providers offers equipment access without large upfront expenses.
Factoring shorter tool lifespan, rapid manufacturing still reduces total costs through fast design cycles and iterations.
Conclusion
In summary, rapid tooling has transformed the way companies approach product design, prototyping and manufacturing.
By utilizing 3D printing and additive techniques, tools can now be fabricated in a fraction of the time required by conventional methods. This has allowed greater design flexibility and the ability to iterate concepts rapidly through testing with realistic form and function prototypes.
With refinements on the way, 3D printing and hybrid techniques will continue enhancing rapid tooling's positive impact on iterations, testing and manufacturing.
Unionfab: Your Rapid Tooling Helper
Whether you need prototype development, design validation or production solutions, our team of experts has the 3D printing technologies and expertise to deliver results.
We invite you to contact us today to discuss how we can assist with your next rapid tooling project. Our consultants are ready to provide recommendations on the best approach, materials and lead times possible.