Selective Laser Melting: The Power of Metal 3D Printing
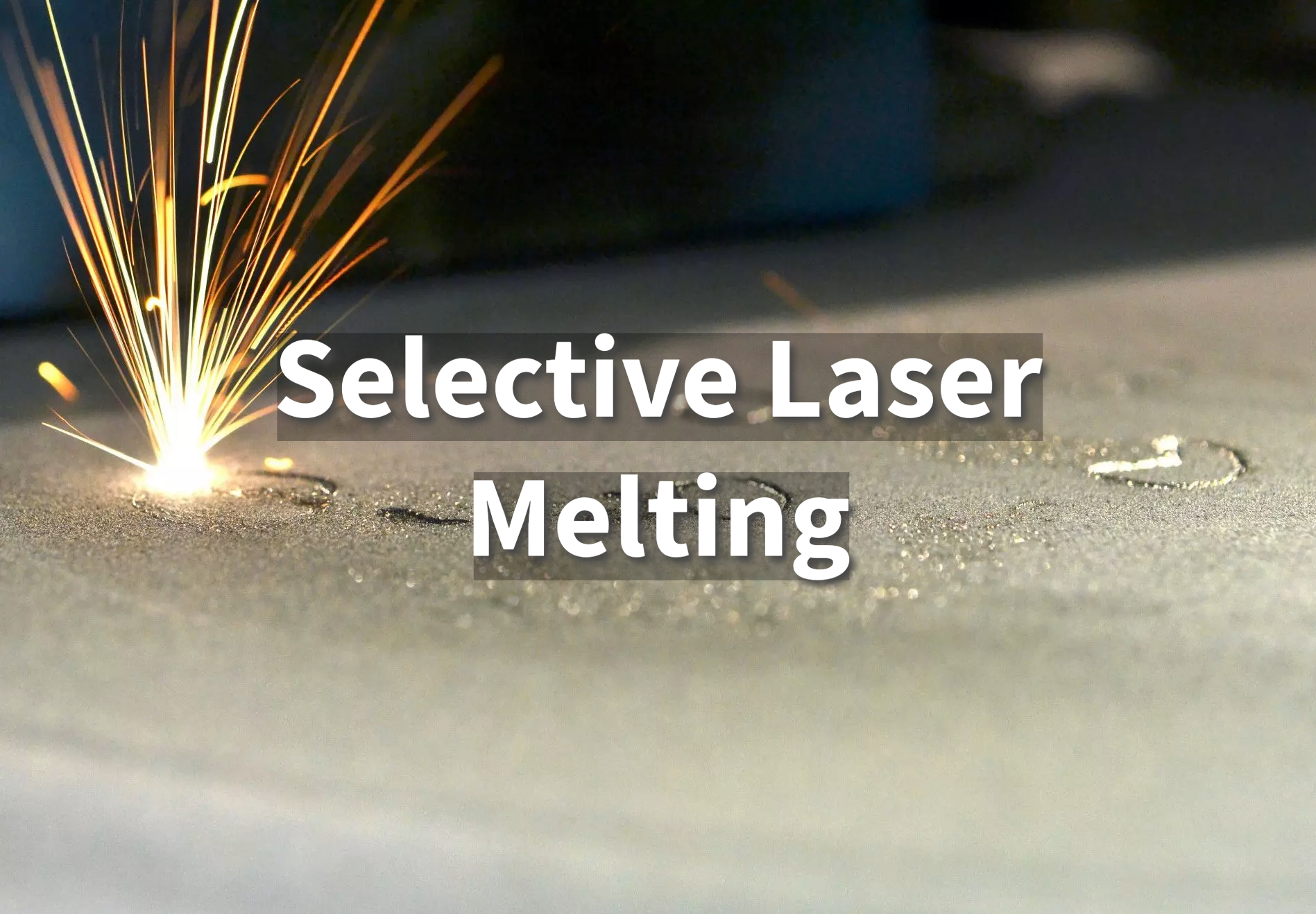
Selective laser melting (SLM) allows manufacturers to 3D print highly intricate metal parts with precision, strength and efficiency.
Introduction
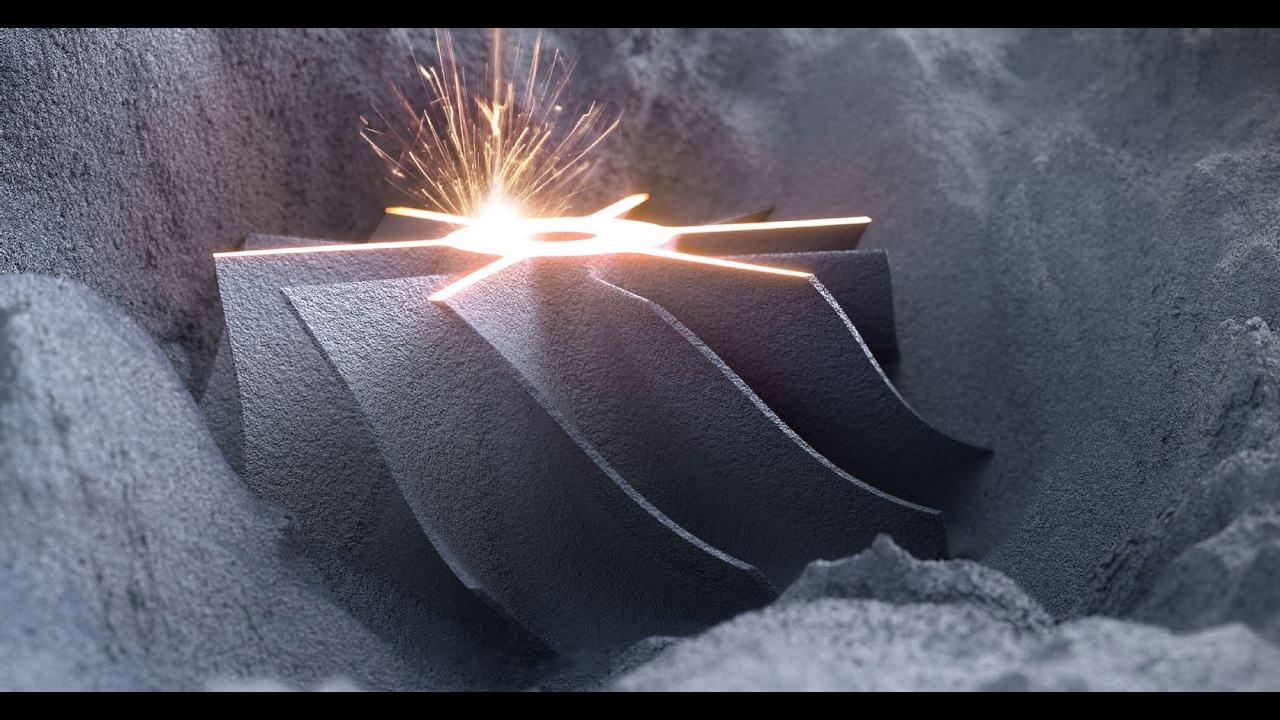
Source: kdmfab.com
Additive manufacturing, or 3D printing, has transformed modern production, with Selective Laser Melting (SLM) leading the way.
Unlike some 3D printing technologies that produce parts with porosity or partial density, SLM creates parts with mechanical properties comparable to those made using conventional methods like CNC machining or casting.
Materials such as stainless steel, titanium, aluminum, cobalt-chromium, and nickel-based superalloys are commonly used in SLM, providing excellent strength-to-weight ratios and durability, which are crucial for mission-critical applications.
The Advantages of SLM Technology
With its capability to produce lightweight structures, reduce material waste, and offer design flexibility, SLM is revolutionizing the way industries approach metal manufacturing.
It enables engineers to optimize designs for performance, such as lattice structures for weight reduction, internal channels for heat management, and intricate surface details that would be difficult to machine.
What is Selective Laser Melting?
Understanding Selective Laser Melting
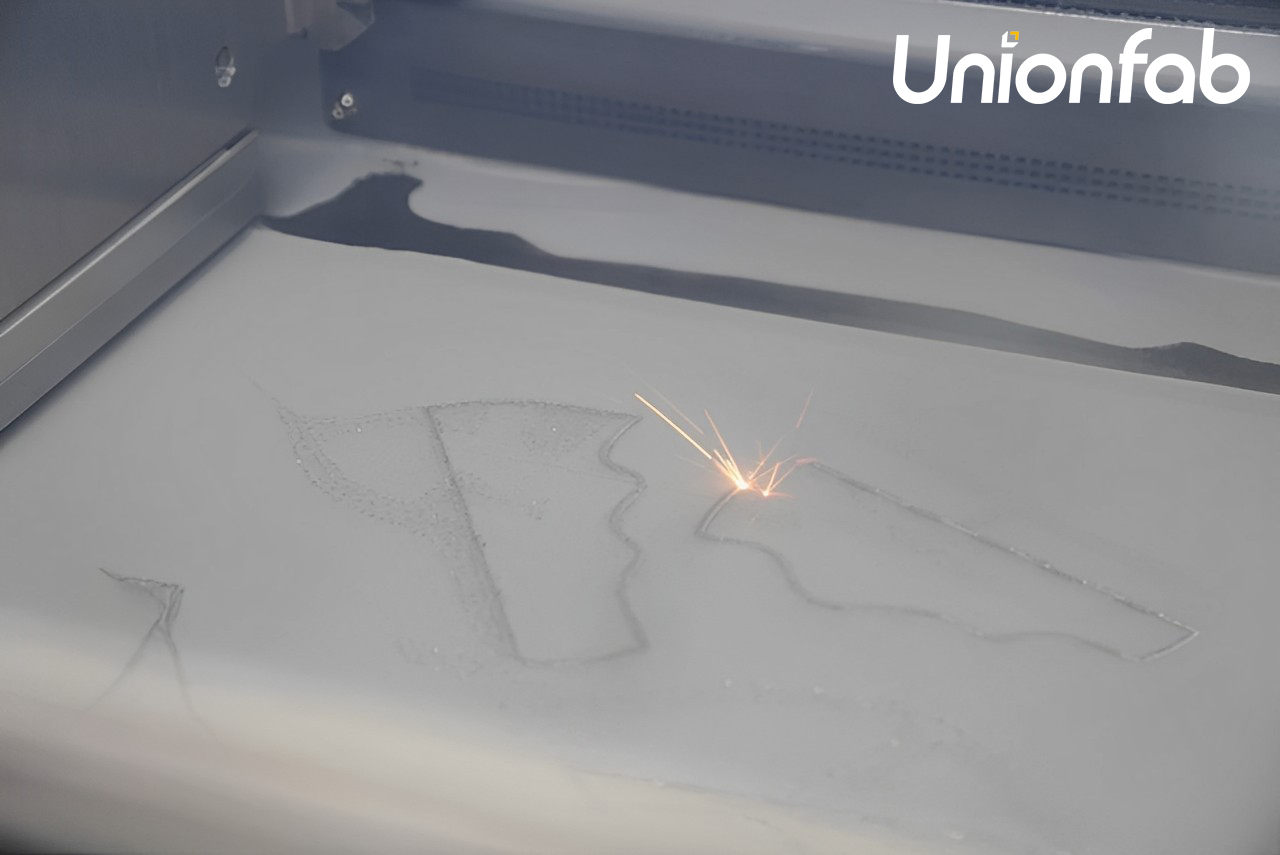
Selective Laser Melting (SLM) is a highly advanced additive manufacturing technique that utilizes a high-energy laser to selectively melt and fuse metal powders, layer by layer, to create three-dimensional objects.
This process differs from other popular 3D printing methods, such as Direct Metal Laser Sintering (DMLS), Selective Laser Sintering (SLS), and Binder Jetting, in several key ways.
The Science Behind SLM
Step 1: Prepare the Metal Powder
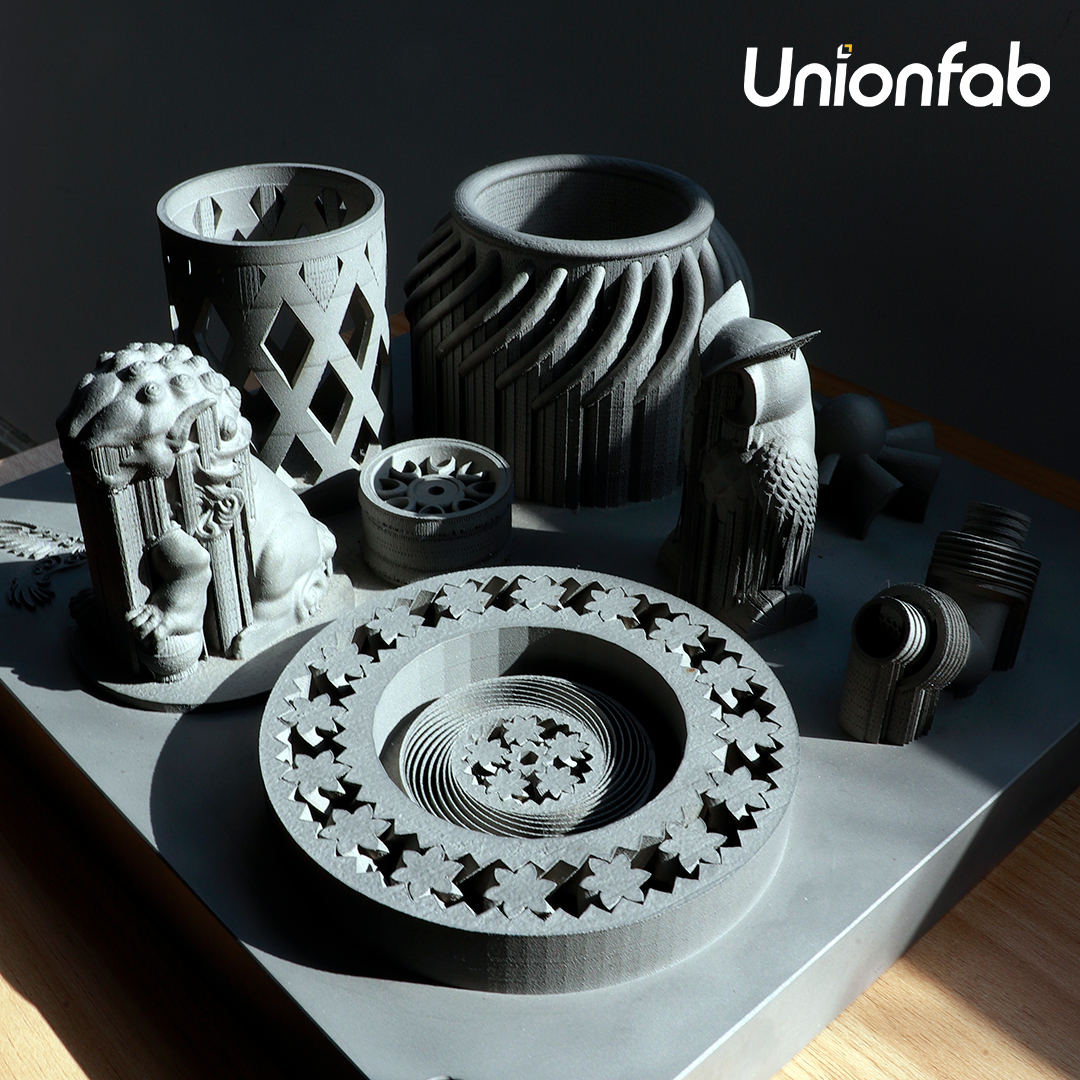
Start with a bed of fine metal powder, typically sized between 20 to 50 microns in diameter. This powder serves as the raw material for the SLM process.
Step 2: Laser Melting
A high-energy laser, such as a fiber or direct diode laser, is precisely directed to selectively melt the powder in a predetermined pattern. This fuses the powder particles together layer by layer.
Step 3: Layering
Once a layer is completed, the build platform lowers, and a new layer of powder is spread over the previous layer. The melting process is then repeated for the new layer.
Step 4: Achieving Full Metal Density
SLM achieves full metal density by completely melting the powder, resulting in parts with superior mechanical properties and precision. This distinguishes SLM from other methods like Direct Metal Laser Sintering (DMLS), Selective Laser Sintering (SLS), and Binder Jetting, which do not achieve the same level of density.
Step 5: Control of Parameters
The process requires careful control of laser energy to ensure complete melting and fusion of the powder. This helps prevent excessive thermal distortion or residual stresses in the final part, necessitating a deep understanding of material properties, laser parameters, and the physics involved in melting and solidification.
SLM vs. Other 3D Printing Techniques
SLM vs. Direct Metal Laser Sintering (DMLS)
DMLS is similar to SLM in that it also utilizes a high-energy laser to fuse metal powders. However, the key difference lies in the melting process.
While SLM completely melts the powder to achieve full metal density, DMLS relies on a sintering process, where the powder particles are only partially fused together.
This results in parts with slightly lower mechanical properties compared to SLM, but DMLS can generally be more cost-effective for certain applications.
SLM vs. Selective Laser Sintering (SLS)
Selective Laser Sintering is another additive manufacturing technique that uses a laser to fuse powdered materials, but it is typically used for polymers rather than metals.
In SLS, the laser selectively sinters the polymer powder, creating a solid structure. SLS is known for its ability to produce complex, intricate parts but may not offer the same level of mechanical performance as SLM for metal-based applications.
SLM vs. Binder Jetting
Binder Jetting is a unique additive manufacturing process that uses a liquid binder to selectively join powdered materials, such as metals or ceramics, together.
Unlike SLM and DMLS, which rely on laser-based melting, Binder Jetting utilizes a printing head to deposit the binder onto the powder bed, layer by layer.This approach can be more cost-effective for certain applications, but the resulting parts may not have the same level of strength and durability as those produced by laser-based techniques.
Materials for Selective Laser Melting
One of the key advantages of Selective Laser Melting (SLM) is the wide range of materials that can be processed using this technology. Unlike traditional manufacturing methods,
SLM allows for the production of parts from a diverse array of metals, each with its unique properties and applications.
Common Metals Used in SLM
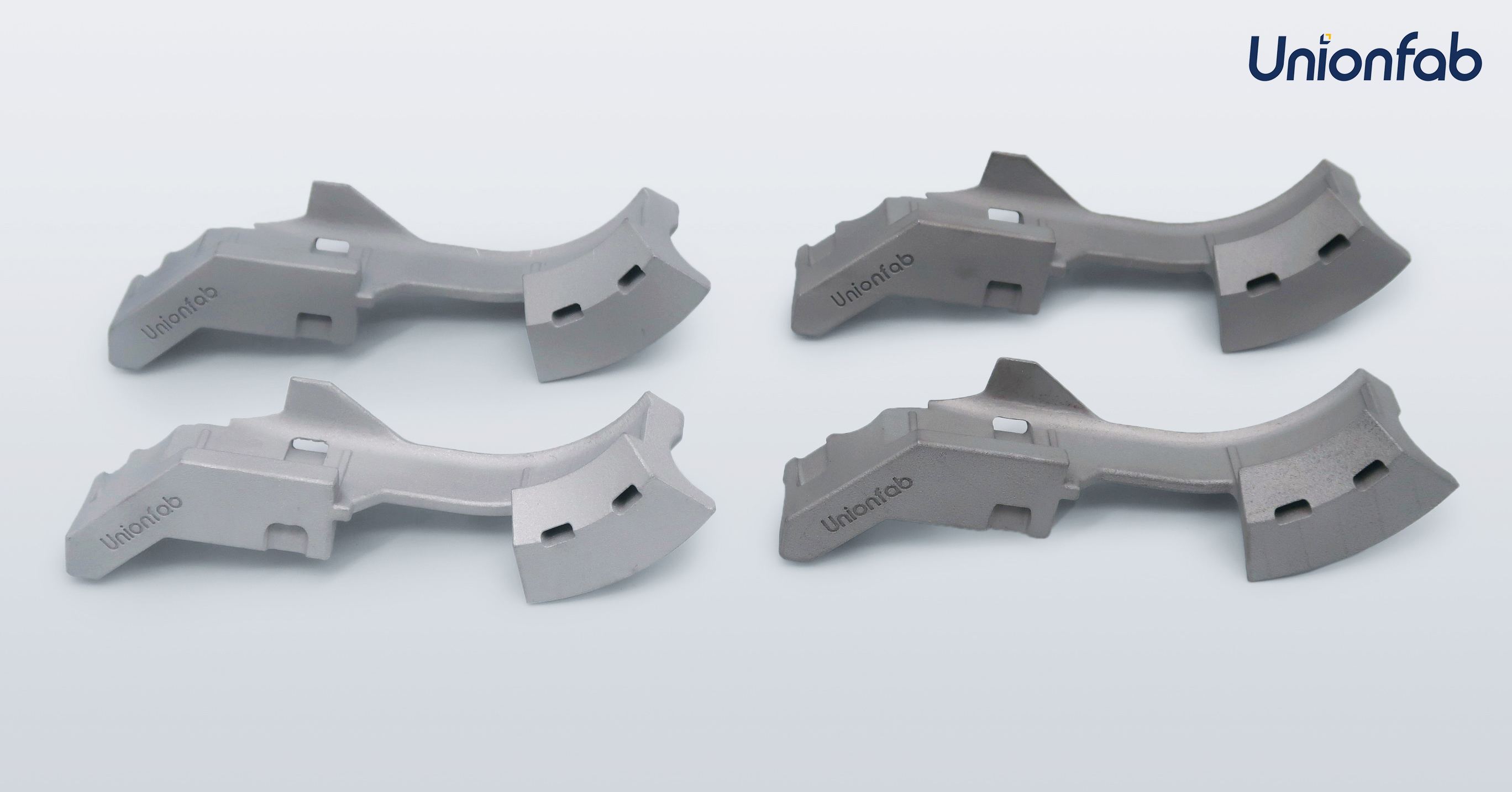
Titanium: Titanium is a popular choice for SLM due to its exceptional strength-to-weight ratio, corrosion resistance, and biocompatibility. These properties make titanium parts ideal for applications in the aerospace, medical, and automotive industries.
Aluminum: Aluminum is another material that is widely used in SLM. Lightweight and highly conductive, aluminum parts produced through SLM are often used in the electronics and transportation sectors.
Stainless Steel: Stainless steel is a versatile material that can be readily processed using SLM. Parts made from stainless steel offer high strength, corrosion resistance, and durability, making them suitable for a wide range of industrial and commercial applications.
Cobalt-Chromium: Cobalt-chromium alloys are commonly used in the medical and dental industries due to their biocompatibility, strength, and wear resistance. SLM enables the production of highly intricate and customized cobalt-chromium implants and prosthetic devices.
Material Properties and Their Impact
The specific properties of the metals used in SLM, such as melting point, thermal conductivity, and coefficient of thermal expansion, play a crucial role in the final quality and performance of the printed parts.
Metals with lower melting points need precise laser control to avoid excess warping from heat. Materials that disperse heat quickly may need different cooling to control internal stresses and bending.
For instance, higher thermal conductivity materials can retain heat longer. Strategies like specialized platforms, air knives or chill plates help draw out residual heat more quickly for dimensional accuracy.
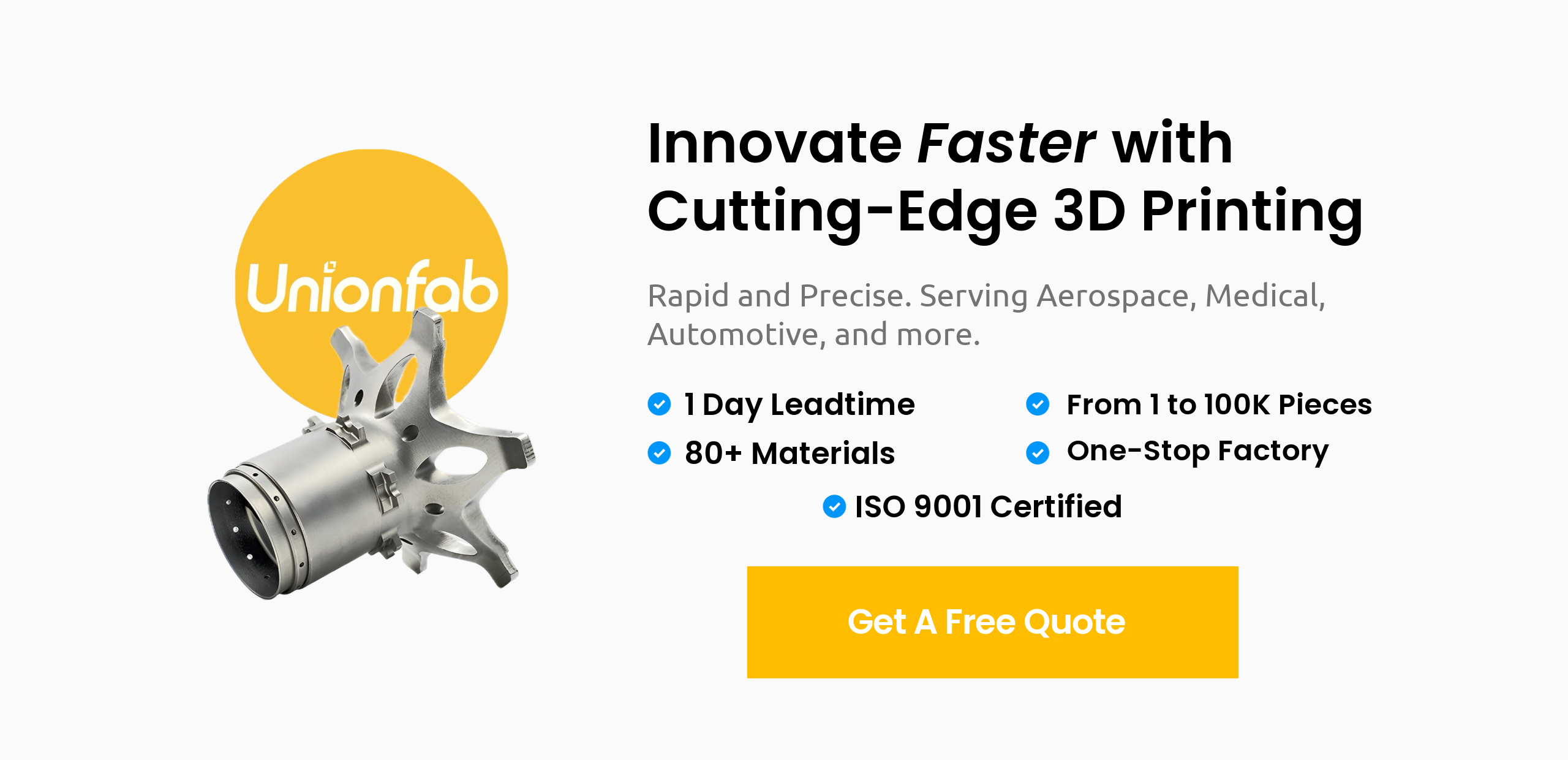
Key Benefits of SLM 3D Printing
From unparalleled design freedom to enhanced sustainability, SLM has revolutionized the way manufacturers approach metal fabrication.
High Precision and Design Freedom
One of the most compelling advantages of SLM is its ability to produce parts with an exceptionally high degree of precision and geometric complexity.
The layer-by-layer approach of this additive manufacturing technique allows for the creation of intricate designs that would be virtually impossible to achieve through traditional subtractive manufacturing methods.
This design freedom empowers engineers, designers, and innovators to push the boundaries of what's possible, unlocking new opportunities for innovation.
Stronger, Lighter, and More Complex Metal Parts
The SLM process, with its ability to completely melt and fuse metal powders, results in parts with superior mechanical properties.
These parts are often stronger and lighter than their conventionally manufactured counterparts, as the fusion process produces a denser and more uniform material structure.
This makes SLM-produced parts ideal for applications in industries such as aerospace, automotive, and medical, where weight, strength, and performance are critical factors.
Minimal Waste and Sustainability Advantages
Compared to traditional manufacturing methods, SLM offers significant sustainability benefits. The additive nature of this technology means that material is only used where it is needed, resulting in minimal waste and efficient use of resources.
Additionally, the ability to produce parts on-demand and reduce the need for extensive tooling and inventory can lead to substantial reductions in energy consumption and carbon footprint throughout the production lifecycle.
Applications
Selective Laser Melting (SLM) has found widespread applications across a diverse range of industries, each capitalizing on the unique benefits this additive manufacturing technology can offer.
Aerospace Industry
The aerospace sector has been a significant beneficiary of SLM technology. The ability to produce lightweight, yet highly durable components is crucial for the aviation industry, where reducing weight is key to improving fuel efficiency and performance.
SLM-manufactured parts, such as engine brackets, heat exchangers, and interior fittings, have been instrumental in helping aerospace companies achieve their design and sustainability goals.
Automotive Industry
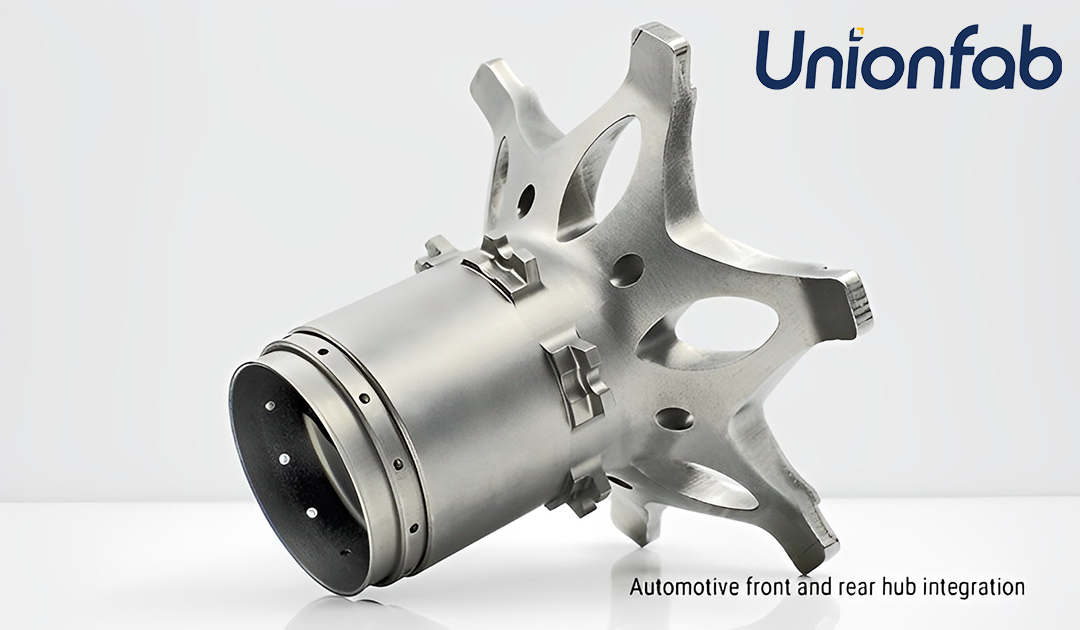
In the automotive industry, SLM has enabled the creation of enhanced performance parts that were previously challenging to produce using traditional methods.
From complex engine components to customized interior features, SLM allows for the fabrication of intricate designs that can improve vehicle efficiency, handling, and aesthetics.
Challenges and Limitations
While SLM has revolutionized additive manufacturing, it faces some challenges:
Material Costs: The specialized metal powders required can be expensive, limiting wider adoption. Ongoing R&D aims to reduce costs.
Production Speed: The layer-by-layer process can be slower than traditional methods. Researchers are exploring ways to increase efficiency, such as higher-power lasers.
Residual Stresses: Thermal cycling can cause distortion and impact part integrity. Advanced control systems and post-processing techniques are being developed.
Surface Finish: Additional post-processing may be needed to achieve desired surface quality. Optimizing process parameters can improve as-built finishes.
Conclusion
As a leading 3D printing company, we have experienced firsthand the numerous benefits that Selective Laser Melting (SLM) technology can offer our customers.
From the exceptional precision and geometric complexity enabled by SLM to the superior mechanical properties and sustainability benefits, this technology has proven to be a game-changer across a wide range of industries.
Partner with Unionfab for SLM 3D Printing
At Unionfab, we are dedicated to pushing the boundaries of manufacturing through advanced selective laser melting (SLM) technology.
Our expertise in metal 3D printing allows us to create high-precision, durable metal components tailored to your unique specifications.
Don’t settle for ordinary—get an instant quote by uploading your model, and launch your next creation from file to finish!