Swiss Machining: The Power of Precision and CNC Technology
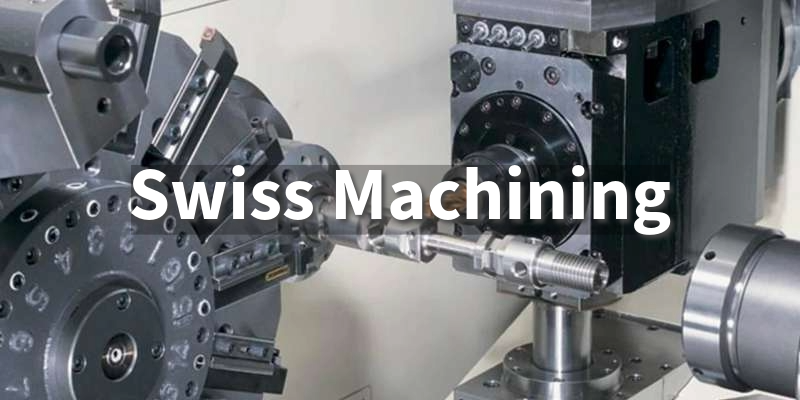
Explore the innovative process of Swiss machining and how CNC Swiss machines deliver unmatched precision.
Introduction to Swiss Machining
Precision is crucial in many industries that manufacture components and tools. Swiss machining enables the production of parts with extremely tight tolerances through the use of computer numerical control (CNC) technology.
In this blog post, we will explore the basics of Swiss machining and how it allows for highly precise manufacturing.
What is Swiss Machining?
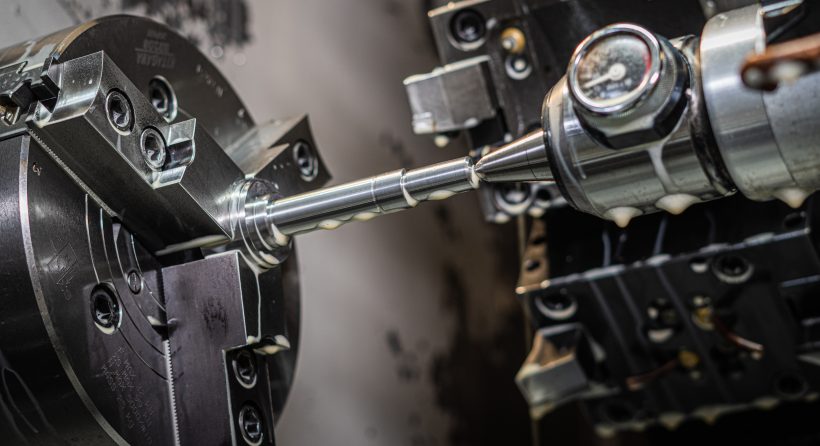
Source: amfg.ai
Swiss machining is a specialized metal cutting process developed in Switzerland to accurately produce small, intricate parts through precise lathe operation.
It originated in the late 19th century to manufacture the miniature components found in mechanical watches. The development of Swiss machining was crucial to enable the mass production of watch parts that were previously hand-crafted by skilled artisans.
Several characteristics define Swiss machining: It utilizes lathes equipped with multiple spindle heads containing very sharp cutting tools. These cutting tools can rotate as well as move linearly, allowing them to precisely carve complex 3D shapes into workpieces. Automated tool changes and synchronized spindle motions facilitate efficient, repetitive machining cycles.
Through a process called “Swiss precision machining”, components like gears, springs, and jewels can be cut directly from metal stock within tolerances as tight as a few millionths of a meter.
How CNC Swiss Machines Work
CNC, or computer numerical control, enables the high levels of automation, efficiency, and precision achieved through modern Swiss machining. At the core of CNC Swiss machines are multifunctional lathes integrated with sophisticated automation technology.
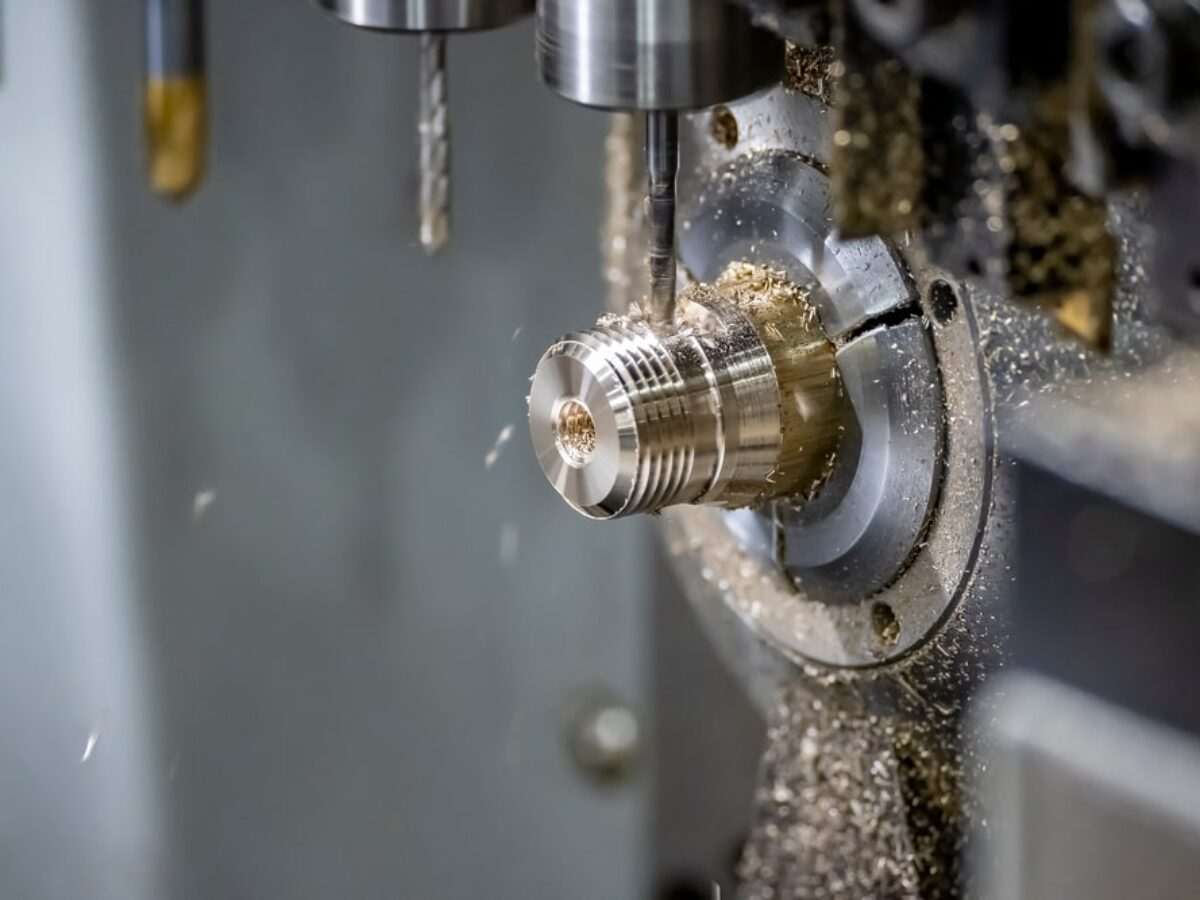
Source: sybridge.com
These advanced lathes contain multiple spindle heads, each fitted with an array of indexable cutting tools. The spindles can rotate these tools as well as move them linearly through precision-guided ways.
Numerical control dictates the two-dimensional motions of each spindle and tool driven by servo motors. Coupled with automated tool changers, this dual-axis motion capability facilitates highly complex 3D contouring and profiling of workpieces directly from metal stock.
Computer control synchronizes the coordinated movements of all spindles and tool components. Machining processes such as drilling, boring, milling, and gear cutting are automated through programmed CNC routines. This increases efficiency by reducing non-cutting time compared to manual machining. Further, CNC eliminates human errors and variations, ensuring exact replication of digital part designs down to the micrometer scale.
Industries like medical devices, timepieces, aerospace and semiconductor fabrication rely heavily on CNC Swiss machining for its unique ability to mass-produce small, complex engineered components with the highest precision. From orthopedic implants to aircraft engine parts to computer chips, CNC Swiss machines play an integral role in manufacturing the miniature yet mission-critical pieces essential to modern technology.
Swiss Screw Machines: A Key Player in Precision
A staple of Swiss machining is the Swiss screw machine due to its specialized capabilities. Commonly known simply as a "screw machine", this tool stands out for its multi-spindle design optimized for producing intricate, small-diameter components.
Unlike traditional lathes with one spindle head, Swiss screw machines house multiple independent turret-style spindle assemblies in a compact footprint. Each spindle is outfitted with indexable tooling and can rotate bidirectionally under numeric control. The ability to simultaneously operate diverse cutting motions across several spindles enables innovative machining functions unique to screw machines.
One such function is single-point forming and threading. Through synchronized spindle motions, screw machines can precisely form threads and contours on a workpiece directly from bar stock using just one cutting tool on each spindle. This eliminates threading taps and simplifies production of intricately profiled screws, fasteners, and cylindrical parts as small as a fraction of a millimeter in diameter.
Other specialized capabilities include multi-start threading for fast cycle times and built-in tool grinding to extend cutting edge life. Moreover, screw machines support automated production through integrated bar feeding, part inspection, and handling systems.
Industries like timekeeping, medical devices, aerospace and electronics depend heavily on the efficiency and small-scale precision afforded by screw machines' multi-spindle design. They remain a cornerstone technology for manufacture of tiny yet application-critical threaded components.
Applications of Swiss Machining
The biomedical sector has greatly benefited from the precision of Swiss machining. Orthopedic and dental implants crafted through Swiss lathing utilize complex internal geometries and mating surfaces that require micron-level tolerances. Tiny implant screws, bone anchors and millimeter-small artificial joints are routinely manufactured on CNC Swiss machines.
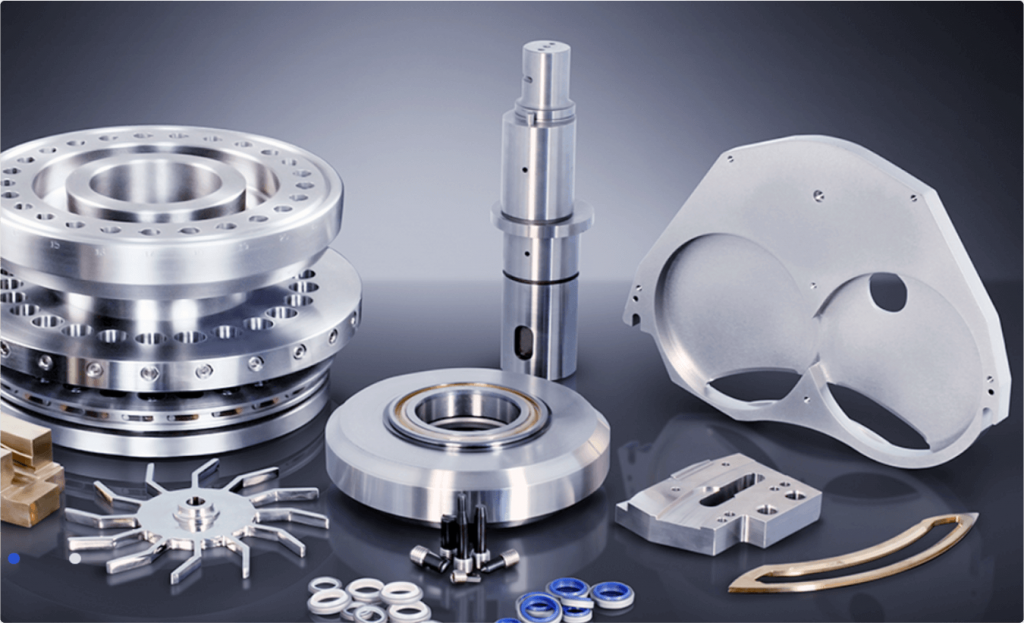
Source: zintilon.com
Aerospace also relies on Swiss machining for critical engine and structural components. Threaded fasteners, fuel nozzles, hydraulic fittings and turbine blades are just some of the miniature yet mission-essential parts produced with Swiss accuracy. For example, aircraft brake calipers containing dozens of minuscule ports and contours are produced as single units through multi-spindle Swiss lathing.
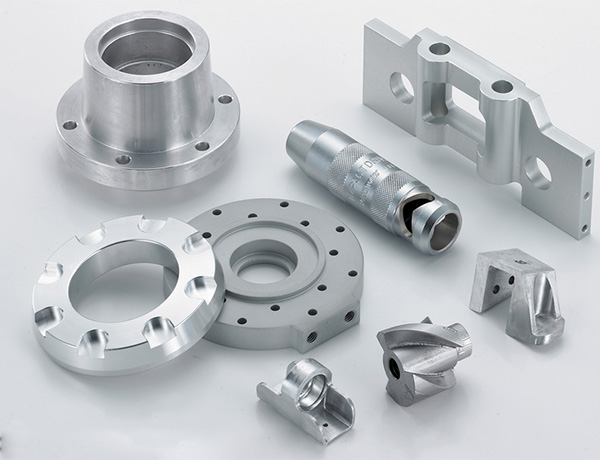
Source: exportersindia.com
In electronics, Swiss machining creates the minuscule parts that enable modern technologies. Thread-forming on screw machines yields hundreds of compass-point fine threaded standoffs per minute for circuit boards. Components like computer CPU heat sinksPattern with intricate etched cooling channels and threaded mounting holes are cut directly from metal stock on CNC Swiss lathes.
Beyond medical, aerospace and electronics, Swiss machining benefits numerous other industries. Timepiece manufacturers still machine watch gears as precise as a dust mote through Swiss screw machining. Optics rely on Swiss lathing for intricate lens mounting rings. Even the packaging sector uses Swiss-machined minuscule vial caps and dispensers. Through masterful precision, Swiss machining continues empowering innovation wherever micro-dimensioned components are mission-critical.
Benefits of Swiss Machining
Swiss machining boasts several benefits that make it indispensable across manufacturing industries demanding the highest levels of precision.
Precision
CNC Swiss lathes can hold tolerances within microns, enabling components to be machined to extremely tight specifications. This precise control achieves proper fit and function even for minute parts.
Efficiency
CNC automation and the multi-spindle designs of Swiss screw machines maximize efficiency. Fast automatic tool changes and synchronized cutting motions minimize non-productive time to maximize throughput.
Cost-Effectiveness
The speed and precision of Swiss machining allows production volumes sufficient to lower per-unit costs. Intricate one-piece components challenge assembly costs yet are competitively manufactured using Swiss production techniques.
Repeatability
Digital control ensures exact replication of designs. Complex components are identically reproduced part after part, reducing waste and improving quality consistency.
Durability
Smooth coordinated motions prevent vibration and tool breakage compared to conventional lathes. This extends cutting tool life, minimizing production downtime from replacing worn inserts.
Versatility
Multifunction CNC Swiss machines capably tackle diverse processes such as milling, threading and drilling beyond simple turning. This one-stop machining capability minimizes hand-off defects and delays.
Overall, Swiss machining enhances manufacturing competitiveness through consistent production of small yet critical components with unparalleled precision, efficiency, and cost-effectiveness. No other technique matches its excellence for micro-scale metalworking.
Conclusion
Through innovative CNC Swiss technology, precision component manufacturing has been taken to new heights. Swiss machining continues empowering critical innovations across numerous industries by solving the challenge of producing small, intricate parts with micron-level tolerances.
Advanced CNC Swiss lathes synchronized with automated multi-spindle screw machines now achieve previously unimaginable levels of miniature part complexity, quality and throughput.
Computer control unleashes the full potential of Swiss machining's two-axis motions, synchronized tooling platforms and live tooling to tackle an expanding range of high-value component machining applications.
Unlock Unmatched Precision with Unionfab
At Unionfab, precision is at the core of everything we do. Our team of experts is ready to collaborate with you on achieving the highest level of accuracy for your custom parts and components
Get an instant quote or contact us now for a free consultation, and discover how we can elevate your business.