Discover the Strongest 3D Printer Filaments for Ultimate Strength
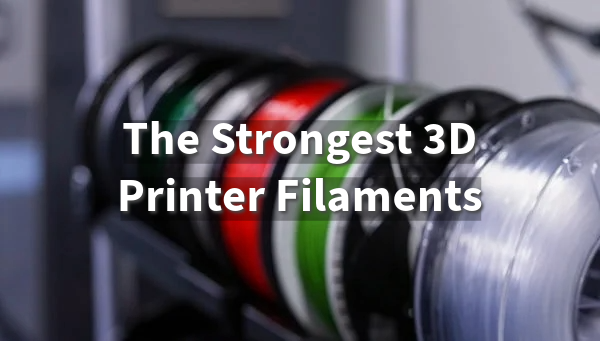
Explore the strongest 3D printer filaments with our insightful guide. Ideal for tough, industrial-grade projects.
Introduction
Whether you are designing functional prototypes or parts for industrial applications, the strength of the 3D printer filament you choose is an important consideration.
In this blog post, we will explore some of the strongest filament materials currently available for FDM/FFF 3D printing.
Understanding your strength requirements and an application's demands can help you select a filament optimized for durability.
What Makes a 3D Printer Filament Strong?
There are a few key factors that determine the strength of a 3D printer filament:
Material Composition
Filaments made from thermoplastic polymers like polycarbonate, nylon, and ABS can withstand more stress than lower-grade plastics due to their molecular structure. They are engineered at the microscopic level for resilience.
Tensile Strength
How much weight a printed part can bear before the material begins to pull apart or deform under load. Tensile strength is measured in pounds per square inch (psi) or megapascals (MPa). Higher numbers indicate greater tensile strength.
Impact Resistance
The ability to resist cracking or breaking when struck. Impact strength is important for parts that may face occasional drops, vibrations, or other forces leading to sudden stresses.
Materials like nylon and polycarbonate have higher toughness.
Testing Strength
Filament strength is tested using standardized methods. Tensile strength involves stretching a sample to failure, while impact tests use a tiny dart or weight swung at set speed. Strict testing ensures the rating accurately reflects real-world performance under stress.
The Strongest 3D Printer Filaments
Polycarbonate (PC)
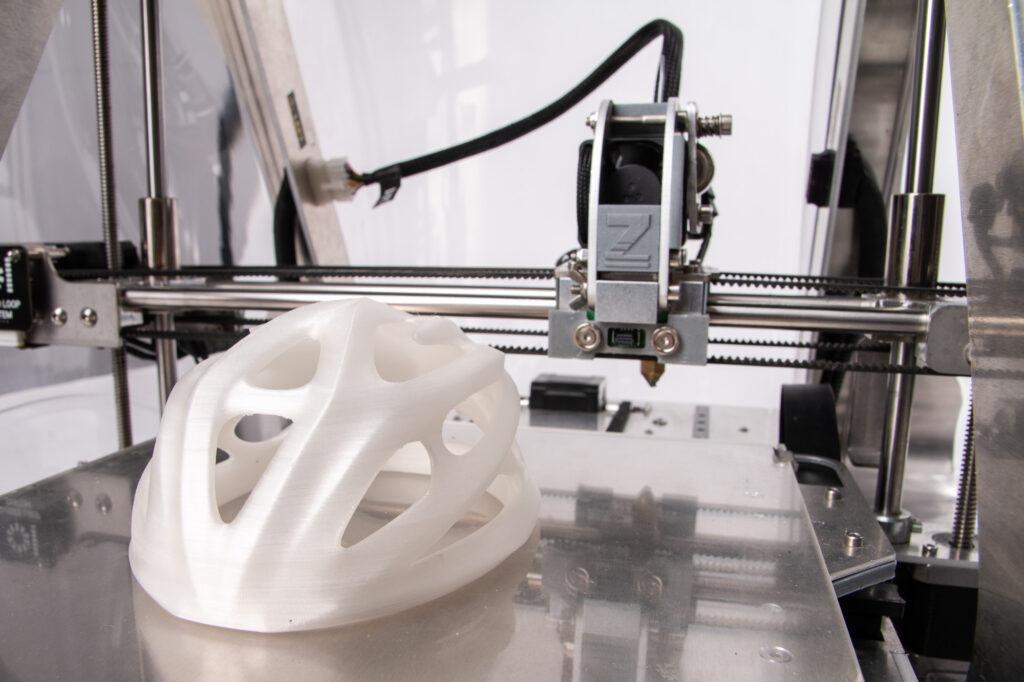
Source: zmorph3d.com


PC has one of the highest tensile and impact strengths of common 3D printing materials. It is heat resistant and durable for withstanding knocks.
PC parts work well for prototypes, housings, and other applications that require high strength at higher temperatures. Downsides are its price and tendency to warp easily during printing.
Nylon
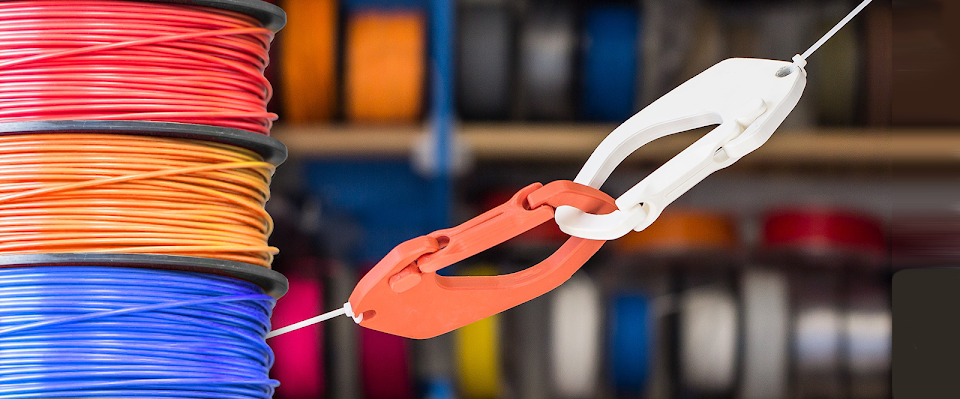
Source: matterhackers.com
Nylons like PA12 and PETG are very strong and flexible. They absorb impacts well without snapping. Nylon is suitable for functional models, snap-fit parts, and anything moving or bearing loads.
However, nylon can be difficult to print with and requires an enclosure to prevent warping.
PEEK
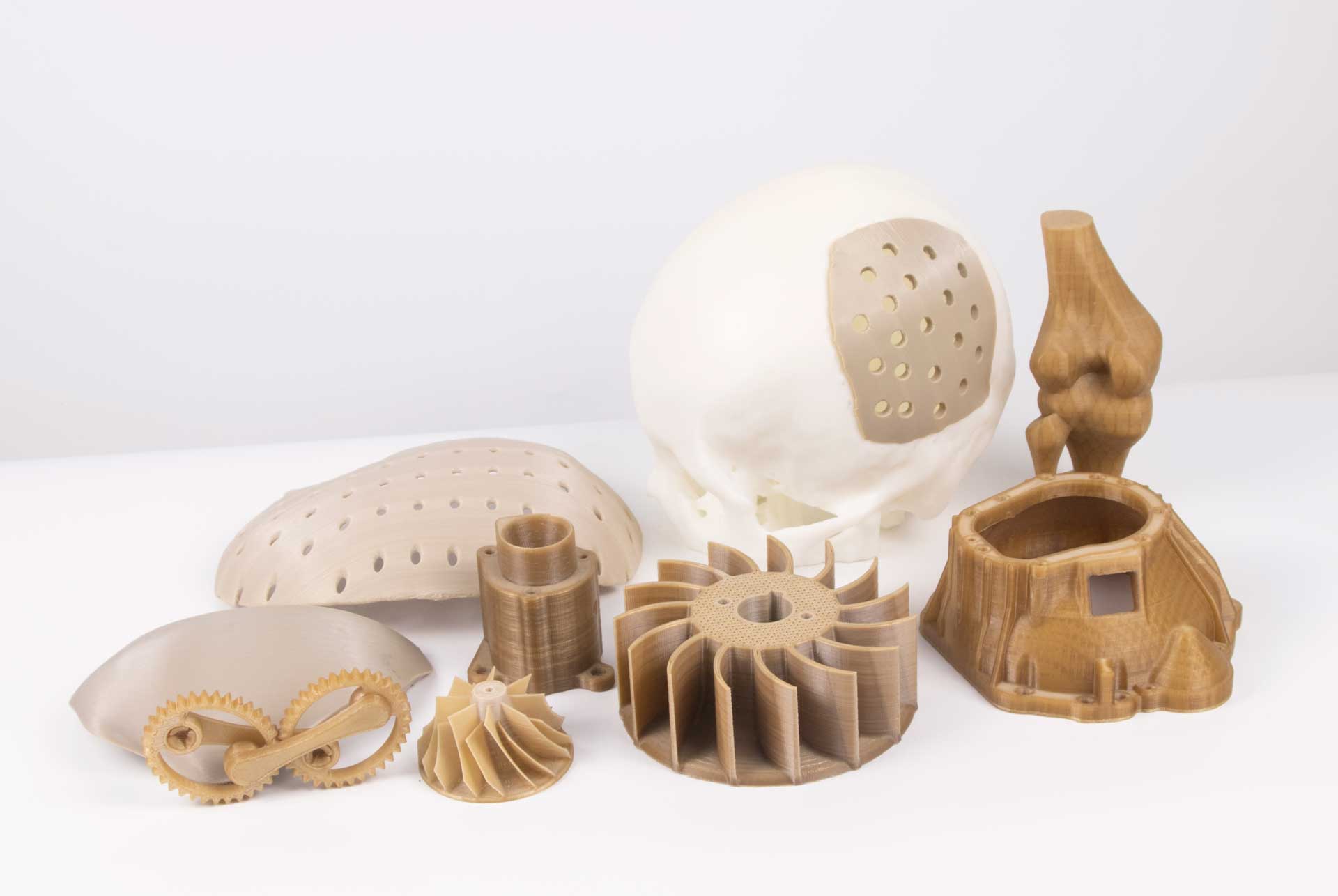
Source: iemai3d.com
PEEK is one of the strongest engineering thermoplastics available for advanced 3D printers. It is heat resistant up to 327°C and has excellent mechanical properties for high-stress applications.
PEEK provides high strength even in harsh environments but requires an expensive high-temperature 3D printer.
Carbon Fiber Composites
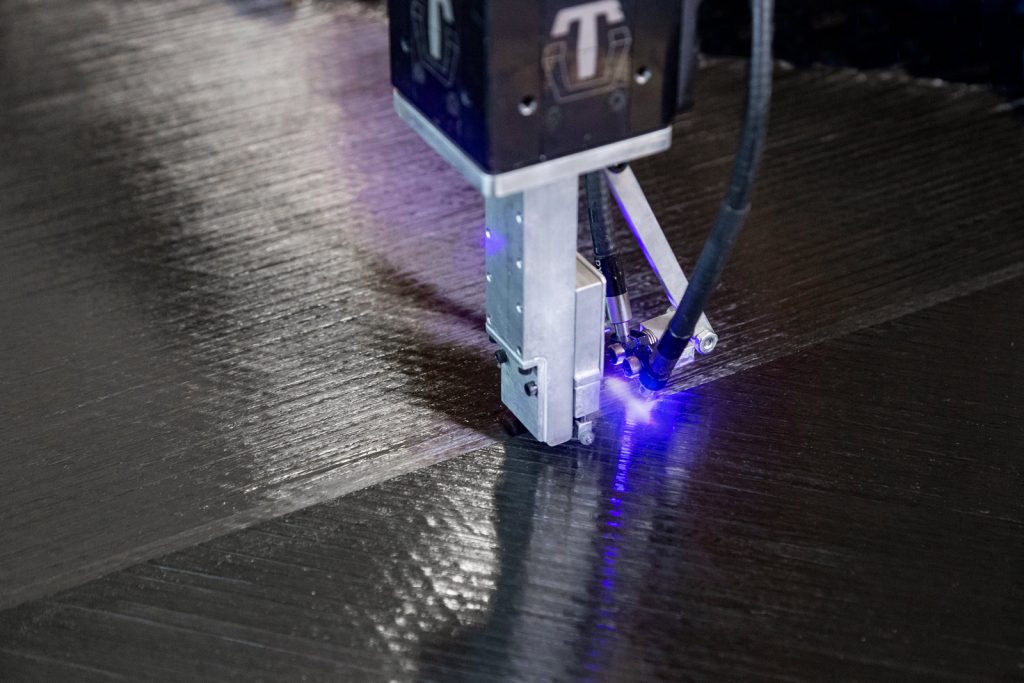
Source: amfg.ai
Fiber-filled composite filaments add carbon fiber or glass fiber strands for strength far beyond regular plastics. The fiber reinforcement provides high tensile strength, stiffness, and temperature resistance.
However, composites are costly and need modified print settings for the added abrasiveness.
In general, PC, nylon, and carbon fiber composites offer the highest strengths while being suitable for most 3D printers. The material you choose depends on your specific strength and durability needs as well as printing constraints.
Applications of Strong 3D Printer Filaments
Industry Use
Polycarbonate, nylon, and composite materials are commonly used in 3D printing for industries like:
Aerospace: PC and nylon allow 3D printed prototyping of aircraft and spacecraft parts that withstand high impact stresses. For example, Polymaker has supplied PC filament to NASA to print prototype components.
Automotive: Carbon fiber composites provide strength and heat resistance for functional 3D printed car and racing parts like engine mounts that require high strength-to-weight ratios.
Prototyping and Functional Parts
Strong thermoplastics are well-suited for 3D printed prototypes and final functional parts:
Durable prototypes: PC and nylon withstand extensive testing and remain dimensionally stable through multiple design iterations.
Snap-fit components: Nylon's flexible strength allows complex assemblies with interlocking parts like electronics housings.
Load-bearing designs: Carbon composite gives parts like drone frames the rigidity to handle heavy payloads or repetitive stresses.
Industrial tools: PEEK provides heat resistance and durability for functioning prototypes of molds, jigs, and other industrial tooling.
The right filament enables 3D printing real-world components and prototypes that undergo stresses mimicking final applications. This advances product development cycles.
Factors to Consider When Choosing a Strong Filament
When selecting the strongest filament for your needs, it's important to consider:
Printing Temperature
Materials like PEEK and carbon fiber require high temperature printers. Be sure your machine can reach 250°C/490°F or higher as needed.
Printer Compatibility
Check for any special tips or modifications needed like hardened steel nozzles for abrasives. Compatibility issues can reduce print quality.
Cost vs. Performance
Options like PC, nylon and PETG provide high strength at lower cost than exotics. Judge if you truly need maximum strength or if a good material will suffice.
Tips for Printing with Strong Filaments
To fully utilize a strong filament's mechanical properties, it's important to use the proper print settings. Here are some tips:
Optimal Temperature: Higher temperatures like 245°C for nylon and 265°C for PC aid layer bonding for maximum strength.
Print Speed: Slower speeds of 30-50mm/s allow thorough melting for better layer adhesion than faster prints.
Nozzle Size: Larger 0.6mm nozzles speed printing but reduce strength slightly from lower pressure. 0.4mm improves strength.
Cooling: Active part cooling aids layer bonding, while an enclosure prevents warping for materials like PC and nylon that change shape easily.
Adhesion: A brim or raft provides additional surface area to help large prints adhering to stay on the bed under pressure.
Post-Processing: Letting prints fully cool before handling prevents heat warping, while light sanding removes blemishes for a smooth finish.
Proper settings during 3D printing maximize the true strength potential of durable filaments for even the most demanding application requirements. At Unionfab, we ensure optimal profiles for our range of materials.
Conclusion
In conclusion, the ability to 3D print durable parts using high-strength thermoplastics like polycarbonate, nylon and carbon fiber composites has expanded the capabilities of additive manufacturing for real-world functional prototypes and production components.
With the appropriate strong material matched to the intended stresses and environmental conditions, along with optimized printing parameters, 3D printing delivers functional elements able to withstand heavy loads, impacts and repeat stresses.
Discover High-Strength Filaments at Unionfab
Get an instant quote or contact us today to discuss prototyping or production needs! Our experienced team of engineers can help you select filaments optimized for your applications.
Let Unionfab be your trusted partner for high-performance 3D printing.