Compression Molding vs Injection Molding: Ultimate Comparison Guide
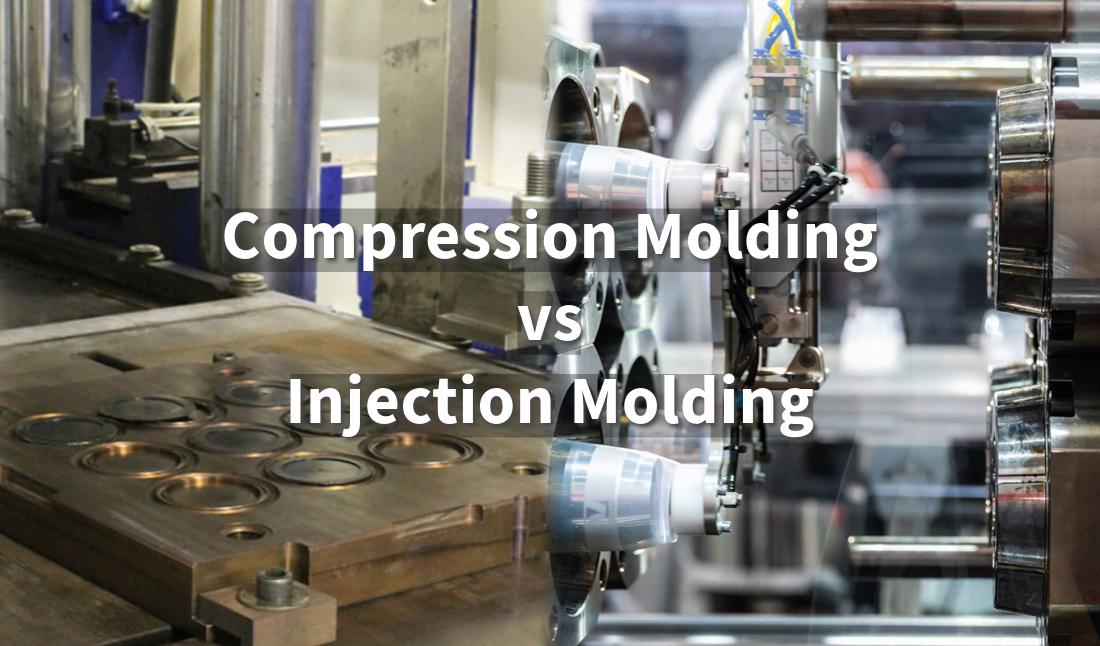
Compression and injection molding each have unique benefits. Find out which method is ideal for your manufacturing needs, budget, and design.
Introduction
Molding is a process used in manufacturing to create all kinds of products we use every day. It involves shaping materials, usually plastics, into specific forms by using molds. Two common types of molding are compression molding and injection molding. Each has its own advantages and is good for different situations.
Choosing the right molding technique is important to make high-quality products quickly and at a good cost. The choice between compression molding and injection molding depends on things like the type of material, how many parts you need, and how complex the design is. Understanding these methods can help you make better choices for your project.
What is Compression Molding?
Compression molding is a process where a material, usually a preheated plastic, is placed into an open mold. The mold is then closed, and pressure is applied to shape the material. Heat and pressure are kept until the material takes the shape of the mold.
Source: grinding.com
Materials commonly used in compression molding include plastics like phenolic, epoxy, and polyester. These materials are chosen because they can handle high temperatures and pressure.
Compression molding is often used to make large, strong parts like car parts, electrical insulators, and kitchenware. Its main advantages are low tooling costs, the ability to make complex parts, and being suitable for strong materials.
What is Injection Molding?
Injection molding is a process where melted material, usually plastic, is injected into a mold under high pressure. Once the material cools and hardens, the mold is opened, and the finished part is removed. This process is often automated, which makes it good for making lots of identical parts quickly.
Source: 3erp.com
Materials commonly used in injection molding include plastics like polyethylene, polypropylene, polystyrene, and ABS. These materials are popular because they are strong and easy to use.
Injection molding is used to make a wide range of products, including consumer goods, medical devices, and car parts. Its advantages include fast production, the ability to make detailed parts, and little material waste.
Compression Molding vs Injection Molding: Key Differences
Cost-effectiveness: Compression molding usually has lower tooling costs, which makes it better for smaller production runs. Injection molding has higher tooling costs, but it becomes more cost-effective for large-scale production because of its speed.
Production speed and scalability: Injection molding is faster and better for making large quantities. Compression molding has slower cycle times, so it is less ideal for high-volume production.
Design flexibility and material compatibility: Injection molding allows for more complex designs and a wide range of materials. Compression molding works well for simpler, larger parts and is good for materials that need high strength.
Environmental impact and waste: Injection molding produces less waste because of its precise control. Compression molding may produce more waste, but it can often use recycled materials, which helps reduce its environmental impact.
Choosing the Right Method for Your Project
Factors to consider: When deciding between compression molding and injection molding, think about factors like production volume, budget, part complexity, material type, and what properties you need for the product. Each of these factors will affect which method is more efficient and cost-effective.
When to choose compression vs injection molding: Compression molding is best for projects that need large, strong parts with simple designs, especially when using certain types of plastics. It is also a good choice for smaller production runs because of its lower tooling costs. Injection molding is better for making lots of parts, especially when the design is complex. It works well with a wide range of plastics and is great for mass production.
Conclusion
Both compression molding and injection molding have their own advantages and are suitable for different projects. Compression molding is good for smaller production runs, strong materials, and simple designs. Injection molding is better for large-scale production of complex, detailed parts.
Get Expert Molding Solutions with Unionfab
Not sure which molding method is right for your project? At Unionfab, we specialize in both compression and injection molding solutions and can guide you to make the best choice for your needs.
Contact us today to discuss your needs, and let us bring your designs to life with the highest quality and reliability. Trust Unionfab for all your molding needs.