Inconel 3D Printing: A Complete Guide
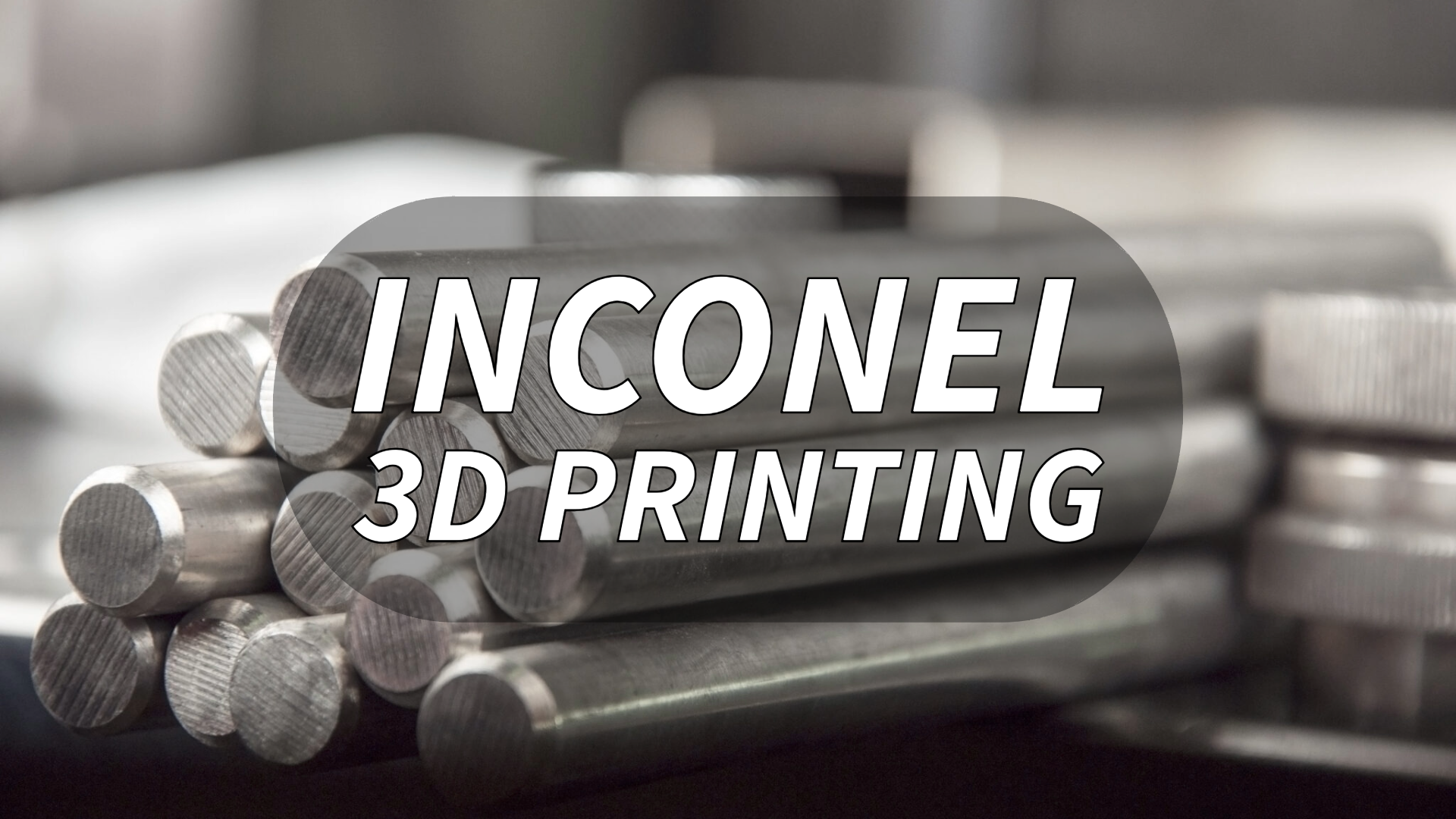
Discover the basics of inconel, including its type, price, and advantages in 3d printing, and explore how it is applied across industries.
Introduction
Inconel is a high-performance nickel-chromium alloy known for its strength, heat resistance, and corrosion resistance, making it ideal for demanding industries like aerospace and energy. In 3D printing, Inconel enables the creation of complex, durable parts that traditional methods find challenging.
This article will cover the types of Inconel alloys for 3D printing, its cost, comparisons with other materials, suitable printing technologies, design guidelines, and the key benefits and applications of using Inconel in 3D printing.
Types of Inconel Alloys for 3D Printing
Inconel 718 vs. Inconel 625
In 3D printing, the most widely used types of Inconel are Inconel 718 and Inconel 625. These alloys are popular due to their excellent performance and are widely used in high-demand industries like aerospace, energy, and automotive. Below is a table comparing the main characteristics and applications of these two alloys.
Inconel 718 | Inconel 625 | |
---|---|---|
Chemical Composition | Nickel (50-55%), | Nickel (58%), |
Density | 8.19 g/cm³ | 8.44 g/cm³ |
Ultimate Tensile Strength | 1,250 MPa | 930 MPa |
Yield Strength | 1,035 MPa | 480 MPa |
Fatigue Strength | 620 MPa | 400 MPa |
Hardness | Rockwell C (RC) 30-40 | Rockwell C (RC) 20-30 |
Melting Point | ~1,330°C (2,426°F) | ~1,350°C (2,462°F) |
Operating Temperature | Up to 700°C (1,300°F) | Up to 980°C (1,800°F) |
Corrosion Resistance | Excellent, especially against oxidation and stress-corrosion | Excellent, especially in harsh environments like saltwater |
Applications | Aerospace (turbine blades, engine parts), energy, automotive | Marine (saltwater applications), chemical processing, aerospace |
Other Common Inconel Alloys
Beyond Inconel 718 and 625, additional alloys like Inconel 600, Inconel 601, and Inconel 825 offer specific benefits for 3D printing.
Inconel 600 is known for its excellent oxidation resistance and is frequently used in chemical processing equipment.
Inconel 601 offers enhanced resistance to oxidation and is used in high-temperature applications such as furnace components.
Inconel 825 stands out for its high resistance to both corrosion and oxidation, making it suitable for handling acids and other aggressive chemicals.
Particle Size of Inconel Alloys and Its Effects
Particle Size of Inconel Alloys
The common particle size of metal powder varies depending on specific 3D printing technologies and application requirements. Generally, the particle size for metal powder used in 3D printing ranges from 15 to 150 microns (μm). Below are some common particle size ranges.Effects of Different Particle Sizes
Inconel is usually processed into metal powder for 3D printing. The particle size of the powder has a big impact on Inconel’s physical properties, especially during 3D printing.
Particle Size Range (micron/µm) | Application and Characteristics |
---|---|
15–45 µm | Suitable for high-precision 3D printing, such as Selective Laser Melting (SLM) and Electron Beam Melting (EBM); |
45–75 µm | Commonly used in general industrial 3D printing, with a good balance for Selective Laser Melting (SLM) and Direct Metal Laser Sintering (DMLS). |
75–100 µm | Suitable for larger parts with lower precision requirements; |
100–150 µm | Primarily for large parts manufacturing and repair; |
Generally, as the powder particle size increases:
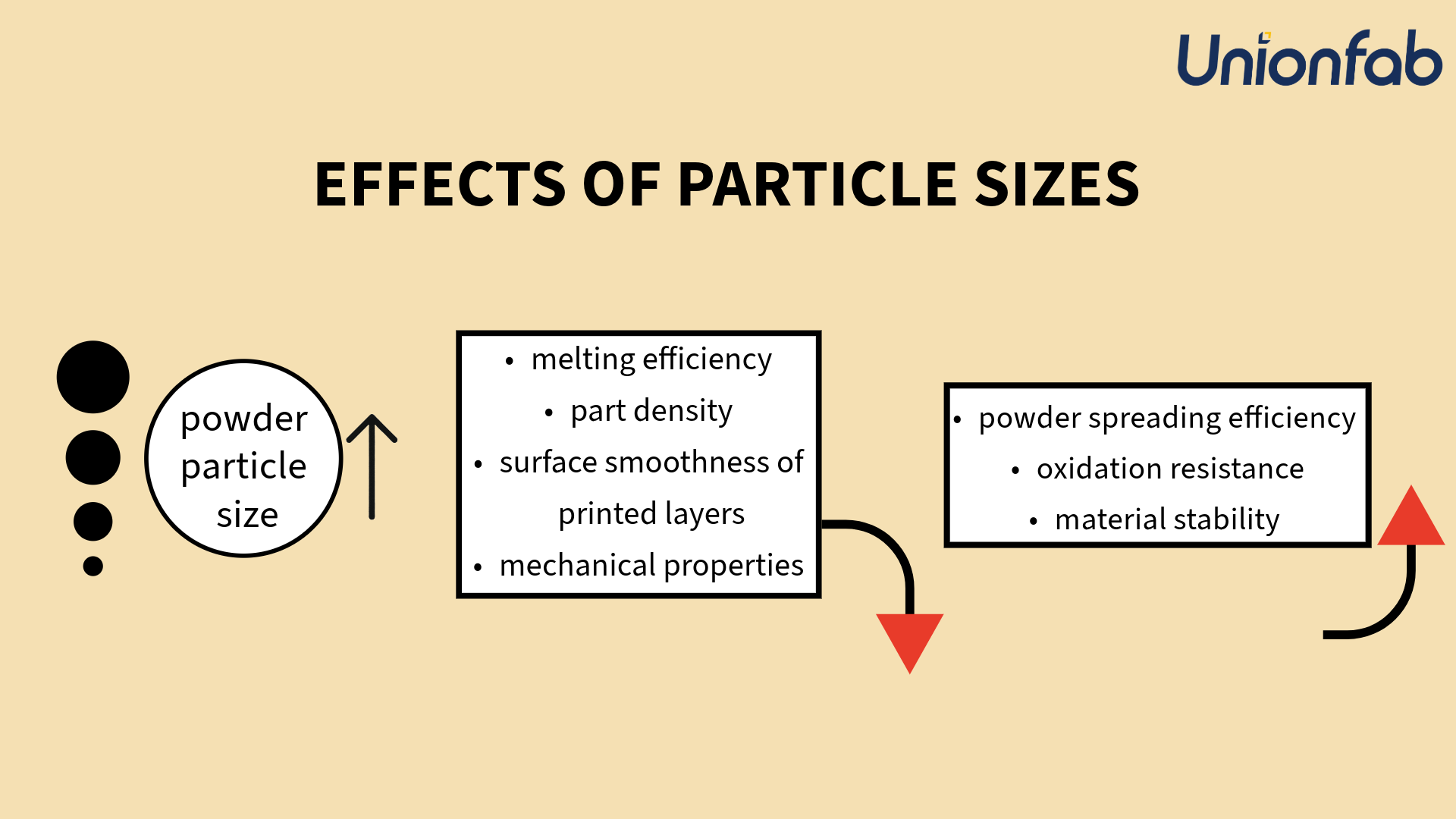
The melting efficiency, part density, surface smoothness of printed layers, and mechanical properties tend to decrease.
Flowability, powder spreading efficiency, oxidation resistance, and material stability improve.
The followings explain how it impacts.
Melting Efficiency & Density
Small Particles: Have a larger surface area, absorb heat easily, and melt uniformly. This helps create a dense, consistent final product with fewer voids and stronger corrosion resistance.
Large Particles: Don’t melt as thoroughly, which can lead to pores or uneven areas, lowering the density and strength of the part. ⠀
Surface Smoothness of Layers
Small Particles: Produce a smoother, more even surface and better print resolution. This is especially useful for high-precision parts, as they spread evenly across each layer.
Large Particles: May not achieve the same smooth finish, making them less ideal for parts that require detailed surfaces. ⠀
Flowability & Powder Spreading
Small Particles: Can sometimes clump together, disrupting flow and slowing down printing. They’re great for detail but can be tricky to spread evenly.
Large Particles: Flow smoothly, which speeds up the spreading process. However, they may sacrifice detail and precision. ⠀
Oxidation & Stability
Small Particles: With their larger surface area, they’re more prone to oxidation, which can impact Inconel’s corrosion resistance and stability. To prevent this, they should be stored in an inert gas environment.
Large Particles: Are less likely to oxidize, making them more stable for storage and use. ⠀
Mechanical Strength
Small Particles: Create a dense structure, which boosts strength and toughness, making the final part more durable.
Large Particles: Can lead to tiny defects, reducing tensile strength and making the part more susceptible to wear over time.
Inconel vs Other Metals in 3D Printing
Inconel vs Titanium
Inconel and titanium are strong and heat-resistant but suit different needs in 3D printing.
Inconel can handle extremely high temperatures (up to 980°C), making it ideal for aerospace and energy applications where parts face intense heat and corrosion.
Titanium, while also strong, is lighter and used in areas needing weight reduction, like medical implants and automotive parts. When choosing Inconel vs titanium, Inconel works best for extreme temperatures, while titanium is preferred for lightweight strength.
Inconel vs Stainless Steel
Inconel offers greater corrosion and heat resistance than stainless steel.
Inconel performs well in extreme environments, like chemical plants and aerospace, due to its high resistance to oxidation and stress.
Stainless steel is more cost-effective for general use where moderate corrosion resistance suffices. In high-stress, high-temperature scenarios, Inconel vs stainless steel comparisons usually favor Inconel.
Inconel vs Hastelloy
Hastelloy and Inconel both resist heat and corrosion. Choosing between them depends on the environment: Hastelloy for heavy corrosion, Inconel for intense heat.
Inconel excels in high-heat settings such as jet engines.
Hastelloy is best for highly corrosive environments like chemical processin.
What’s worth noting is that inconel, mainly made of rare, costly nickel and chromium, is pricier than other 3D printing metals. While ideal for aerospace due to its high quality, more affordable metals like stainless steel or aluminum are often better for everyday uses like automotive and electronics.
Want to know more about 3d printing using stainless steel, aluminum, or other cost-effective metals, feel free to contact Unionfab, China's largest 3D printing manufacturing company.
With over 20+ years' experience, 1000+ industrial 3D printers and the ISO 9001 certification, we deliver cost-effective and quality services that are 70% cheaper than counterparts and ensure rapid air shipments in 3-5 days via DHL Express and FedEx.
3D Printing Technologies Suitable for Inconel
The most common 3D printing technologies for Inconel are powder bed fusion (PBF, mainly SLM/DMLS) and direct energy deposition (DED). Here we have compared these 3 processes.
Technology | Process | Lead Time | Cost | Key Benefits | Limitations | Common Applications |
---|---|---|---|---|---|---|
Uses a high-powered laser to melt Inconel powder layer by layer | ★★★☆☆ | ★★★★☆ | Produces precise, dense parts with high detail | Expensive and slow; requires controlled environment | Aerospace (engine components, turbine blades), Energy (heat exchangers, valves), Medical (implants) | |
Directed Energy Deposition (DED) | Feeds Inconel powder or wire into a laser or energy source to build layers | ★★☆☆☆ | ★★★☆☆ | Ideal for large parts or repairs; faster than SLM | Lower precision; rougher finish | Aerospace (repairing turbine blades, coating parts), Industrial (repairing and reinforcing large parts) |
Binder Jetting | Uses a liquid binder to fuse layers of Inconel powder, then sinters in a furnace | ★★☆☆☆ | ★★☆☆☆ | Faster and more cost-effective for large batches; good for complex parts | Lower density; requires post-processing and sintering | Automotive (exhaust manifolds, turbocharger components), Industrial (complex fittings, tooling) |
For the design guideline of inconel 3d printing, you can refer to the article: https://www.materialise.com/en/academy/industrial/design-am/inconel-718
Advantages of Using Inconel in 3D Printing
High-Temperature ResistanceInconel withstands temperatures up to 980°C, ideal for aerospace, automotive, and energy parts exposed to extreme heat.
Excellent Corrosion ResistanceResistant to oxidation and corrosion, Inconel performs well in harsh environments, like marine and chemical applications.
Strength and DurabilityWith high strength and fatigue resistance, Inconel parts endure heavy loads and stress over time, making them reliable for critical uses.
Complex GeometriesInconel’s compatibility with 3D printing allows for intricate, lightweight designs that traditional methods can’t easily achieve, crucial for aerospace.
Reduced Material Waste3D printing Inconel builds parts layer-by-layer, minimizing material waste and making production more efficient.
Applications of Inconel 3D Printing
AerospaceInconel is widely used to produce high-strength, heat-resistant components like turbine blades, engine parts, and exhaust systems. Its durability under extreme conditions makes it ideal for aerospace applications.
Inconel 718 Turbine Blades
Source: researhgate.netAutomotive
In the automotive industry, Inconel 3D printing is applied in high-performance parts like turbocharger housings and exhaust manifolds, where resistance to heat and corrosion is essential.
Inconel 625 Fiesta Manifold
Source: waltonmotorsport.comEnergy
Inconel is used to create parts for power generation, such as heat exchangers, valves, and pumps that need to withstand high temperatures and pressure.
Inconel Alloy 600/625 Heat Exchanger
Source: steeltubes.co.inMarine
Due to its corrosion resistance, Inconel is valuable in marine applications, producing parts like propeller blades and equipment that encounter saltwater and harsh conditions.
Inconel Marine Turbo Heat Shield
Source: ppepower.comChemical Processing
Inconel’s resistance to acids and corrosive chemicals makes it ideal for 3D printing parts like reactor components, pipes, and fittings used in chemical processing.
Schematic Diagram of An Inconel X-750 Spacers
Source: researchgate.net
Conclusion
Inconel’s unique properties make it an outstanding material for 3D printing in demanding industries. Its heat resistance, strength, and corrosion resistance enable the creation of durable, high-performance parts in aerospace, automotive, and energy sectors.
Despite its higher cost and machining difficulty, Inconel remains invaluable where extreme conditions require reliable, long-lasting components. With advances in 3D printing technologies, Inconel’s applications will continue to expand, meeting the evolving needs of high-stress environments.
FAQs
Is Inconel Magnetic?
Inconel is generally non-magnetic. Although it contains nickel, which is usually magnetic, its specific alloy structure makes it mostly non-magnetic, especially in high-temperature applications.
How is inconel produced?
Inconel is produced by melting nickel, chromium, and other alloying elements like molybdenum and niobium. The molten alloy is then cast and subjected to processes like forging, rolling, and heat treatment to enhance its mechanical properties.
Is inconel hard to machine?
Yes, Inconel is difficult to machine due to its hardness, strength, and heat resistance. It tends to work-harden, which means it becomes harder as it’s being machined, requiring specialized tools, cooling methods, and slower machining speeds to avoid tool wear and overheating.
Why inconel is so expensive?
Inconel’s high cost comes from its expensive raw materials (mainly nickel and chromium), a complex production process, and difficulty in machining. These factors, combined with its specialized use in industries with extreme requirements, contribute to its high price compared to other metals.
What are the disadvantages of inconel?
High Cost
Inconel is expensive due to its costly raw materials (nickel and chromium) and complex manufacturing process, making it less budget-friendly than other metals. As of recent data, Inconel 625 is priced at approximately $52.5/kg in the USA and $36.9/kg in Europe. In contrast, stainless steel prices are significantly lower at around $3 per kilogram.
Difficult to Machine
Inconel’s hardness and heat resistance make it challenging to machine. It requires specialized tools, slow cutting speeds, and cooling to prevent tool wear, increasing production time and cost.
Heavy Weight
Inconel is dense, making it heavier than materials like titanium or aluminum. This limits its use in applications where weight reduction is critical, such as certain aerospace and automotive components.
Limited Availability
Due to its specialized applications, Inconel is not as widely available as more common metals, which can lead to longer lead times for procurement.
Oxidation at Extremely High Temperatures
While Inconel resists oxidation very well, at extremely high temperatures (above its maximum rated limit), it may still oxidize, limiting its use in certain ultra-high-temperature environments. These factors mean that while Inconel is excellent for specific high-stress applications, it’s not always the best choice for general use or cost-sensitive projects.
What is stronger, titanium or inconel?
Inconel is generally stronger than titanium at very high temperatures. Inconel maintains its strength and stability under extreme heat, while titanium is lighter and strong but loses strength at lower temperatures compared to Inconel. Therefore, Inconel is often chosen for high-heat applications, while titanium is favored for applications requiring a strong yet lightweight material.