Injection Molding Defects Explained: Prevention and Solutions
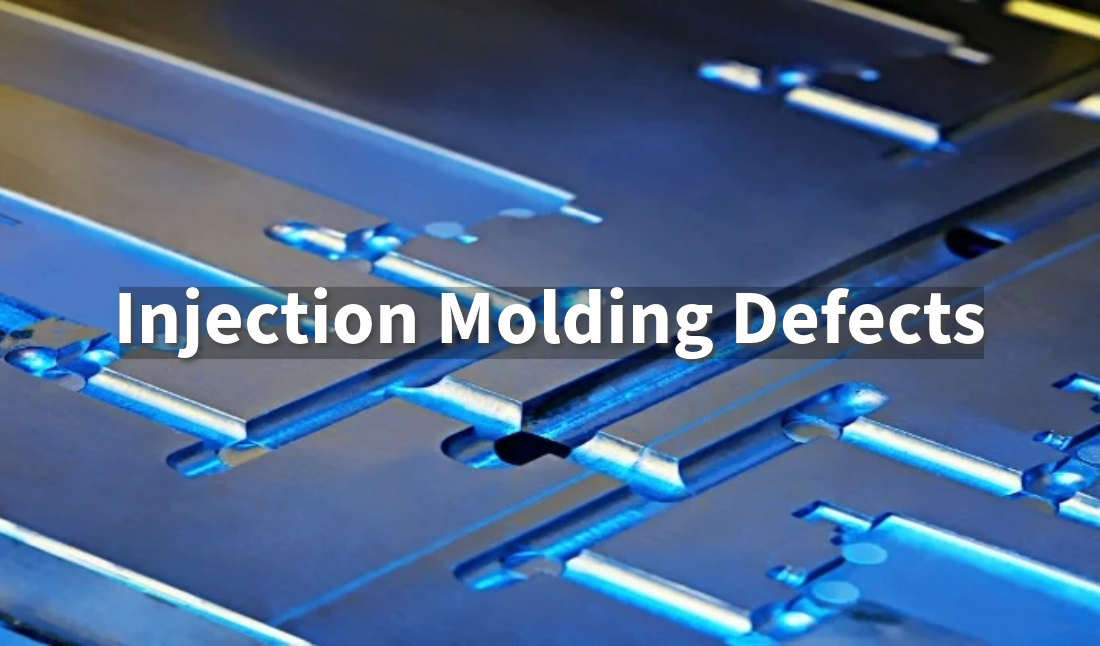
Learn about common injection molding defects and effective strategies to prevent them.
Introduction
Injection molding is an important way to make plastic parts. It works by injecting melted plastic into a mold, which then cools down and forms the final shape. This process allows companies to make lots of items quickly, which is why it is used in many industries from making toys to car parts.
However, sometimes defects can happen during injection molding. They can make the products look bad or even weaken them. In this blog, we will explain some common injection molding defects, why they happen, and how they can be fixed to make the best quality products.
Common Injection Molding Defects
Warping: Warping happens when parts of the molded item cool at different rates, causing the product to twist or bend out of shape. This can happen because of uneven cooling or a poor mold design.
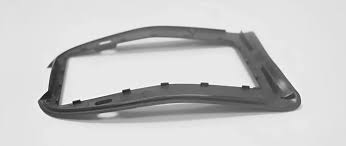
Source: prototool.com
Sink Marks: Sink marks are small dents or dips on the surface of the molded part. They happen when the plastic inside the mold shrinks unevenly, often because of low pressure or not enough cooling time.
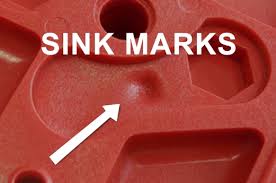
Source:moldplasticinjection.com
Flow Lines: Flow lines are streaks or patterns that appear on the surface of the molded part. They are usually caused by changes in the speed or direction of the melted plastic as it moves through the mold. Incorrect temperature or injection speed can cause these lines.
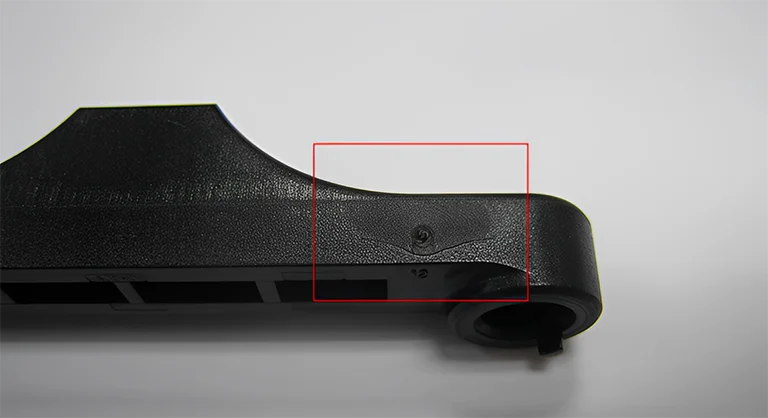
Source: prototool.com
Burn Marks: Burn marks are dark spots on the molded part. They are usually caused by trapped air or the plastic getting too hot, which can burn the material.
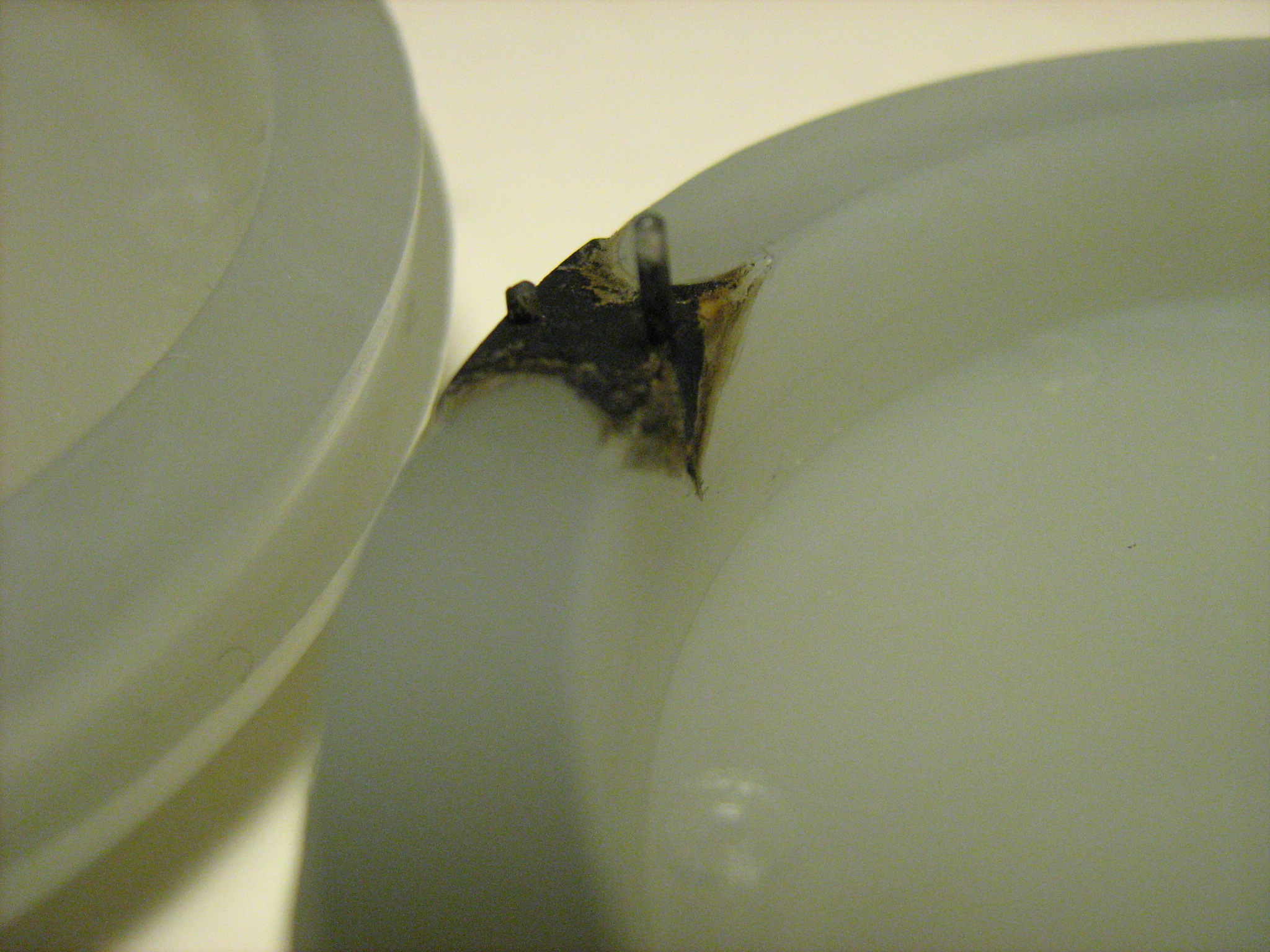
Source: nanomoldcoating.com
Weld Lines: Weld lines happen where two or more flow fronts meet during the molding process. These lines can make the part weaker and are often caused by low temperatures or incorrect injection speeds.
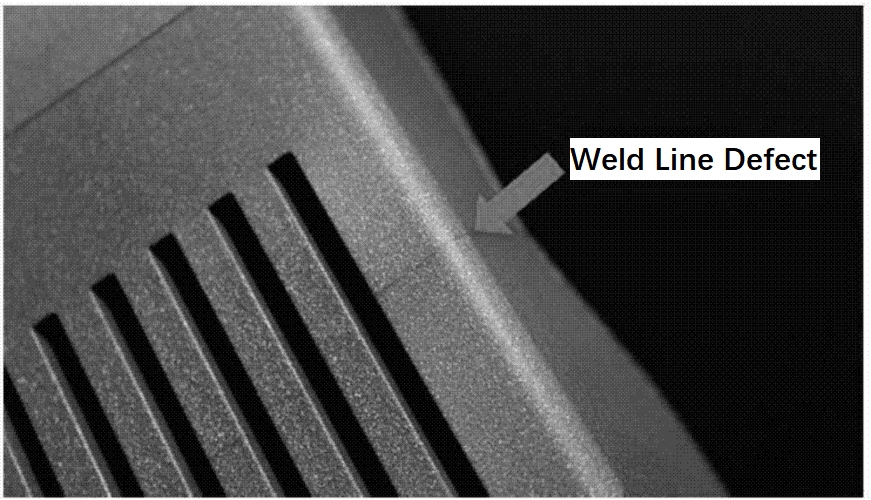
Source:ipqcco.com
Short Shots: Short shots happen when the mold is not filled completely with plastic, leading to incomplete parts. This can be due to low injection pressure or blockages in the mold.
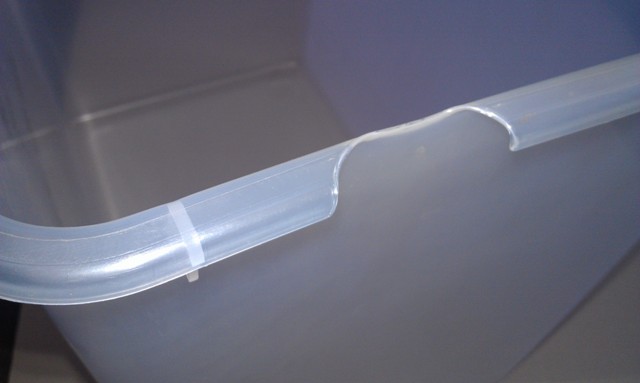
Source: improve-your-injection-molding.com
Flash: Flash is extra plastic that seeps out of the mold, creating a thin layer on the edges of the part. This can happen if the mold is not clamped tightly enough or if there is too much injection pressure.
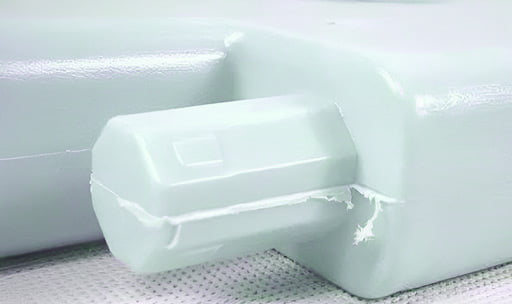
Source: madearia.com
Prevention and Solutions
Warping: To prevent warping, make sure the cooling rate is even throughout the part. This can be done by improving the mold design, using even wall thickness, and adjusting cooling times and temperatures. Choosing the right material can also help reduce warping.
Sink Marks: To prevent sink marks, increase the pressure and time during the injection process. Make sure the mold is designed to allow even cooling and consider using materials that shrink less.
Flow Lines: Flow lines can be reduced by optimizing the injection speed and temperature. Increasing the mold temperature and keeping a steady flow rate can help eliminate these lines. Ensuring the mold design allows for smooth flow paths can also help.
Burn Marks: Burn marks can be prevented by making sure the mold has proper venting so that trapped air can escape. Reducing the injection speed and temperature can also help avoid overheating the plastic.
Weld Lines: To avoid weld lines, increase the temperature of the mold and the melted plastic to ensure better fusion where the flow fronts meet. Adjusting the injection speed and pressure can also help strengthen the weld areas.
Short Shots: Short shots can be prevented by increasing the injection pressure and making sure the mold is free from blockages. Proper venting and maintaining the correct temperature can also help fill the mold completely.
Flash: To prevent flash, make sure the mold is clamped tightly and there are no gaps. Reducing the injection pressure and making sure the mold is aligned correctly can help avoid extra plastic from leaking out.
Regular Maintenance: Regular maintenance of machines is important to prevent defects. Making sure molds, injection machines, and other equipment are in good condition can reduce the risk of defects. Quality checks during and after production are also important for finding and fixing problems early, ensuring high-quality products.
Advanced Techniques for Defect Control
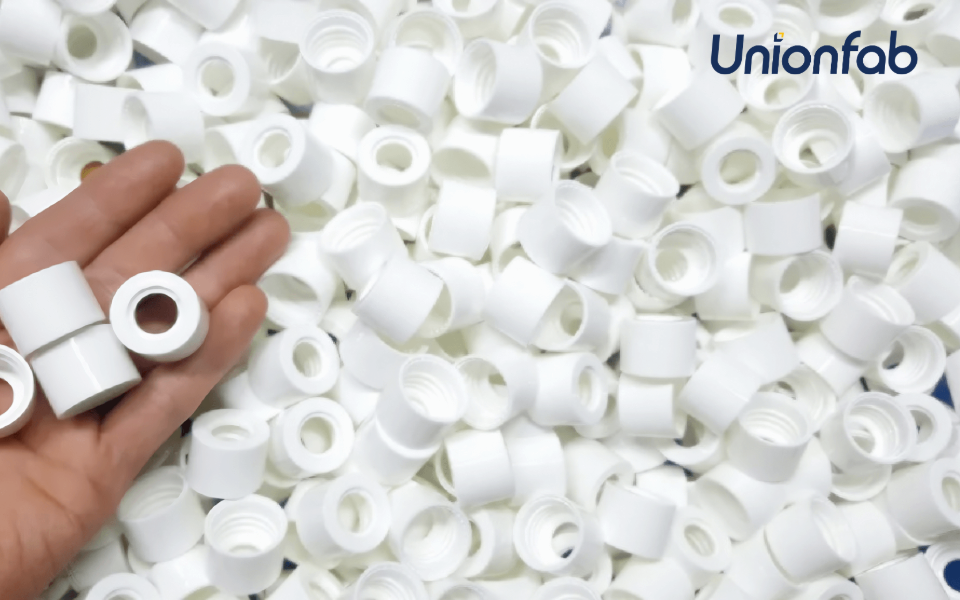
Automation and Sensors: Using automation and sensors in the injection molding process can help detect defects in real-time. These technologies can find issues like uneven filling or trapped air early, allowing for quick adjustments to prevent defects.
Quality Control: Quality control is very important for reducing defects. Using strict quality control procedures, including regular checks and monitoring throughout production, helps find and fix problems before they affect the final product.
Conclusion
Injection molding is a powerful way to make products, but defects can affect the quality of the final parts. Understanding the common defects, their causes, and how to prevent them is key to making high-quality products.
Regular maintenance, quality control, and using advanced technology are important for reducing defects and making sure production is defect-free. By focusing on quality assurance, manufacturers can save money, stay efficient, and deliver great products to their customers.
Unionfab: Quality Injection Molding
At Unionfab, we are committed to providing high-quality injection molding services that help you avoid common defects and ensure your products are the best they can be.
Contact us today to learn more about our advanced manufacturing solutions and how we can help with your next project.
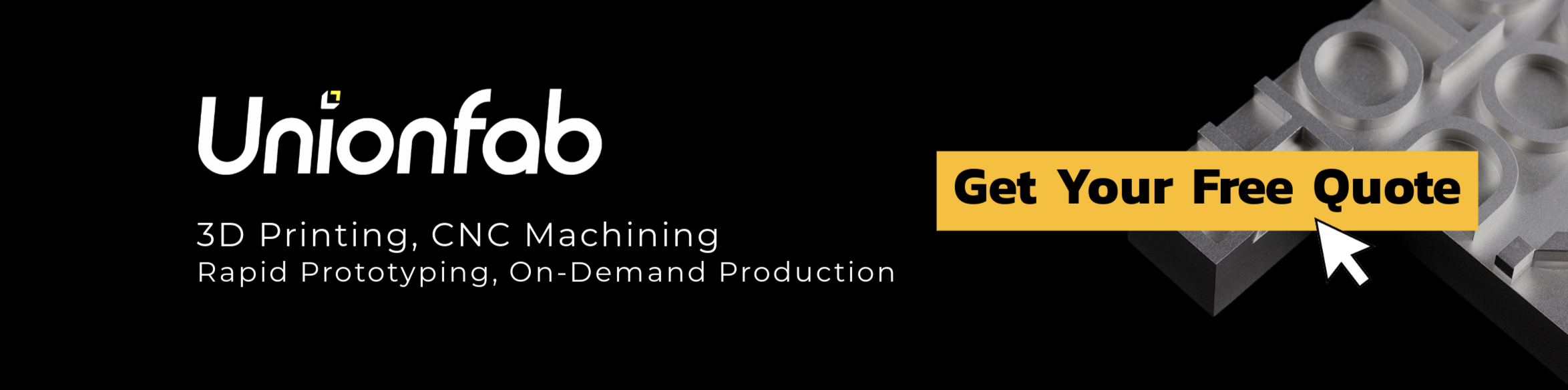