Polycarbonate Injection Molding: Everything You Need to Know
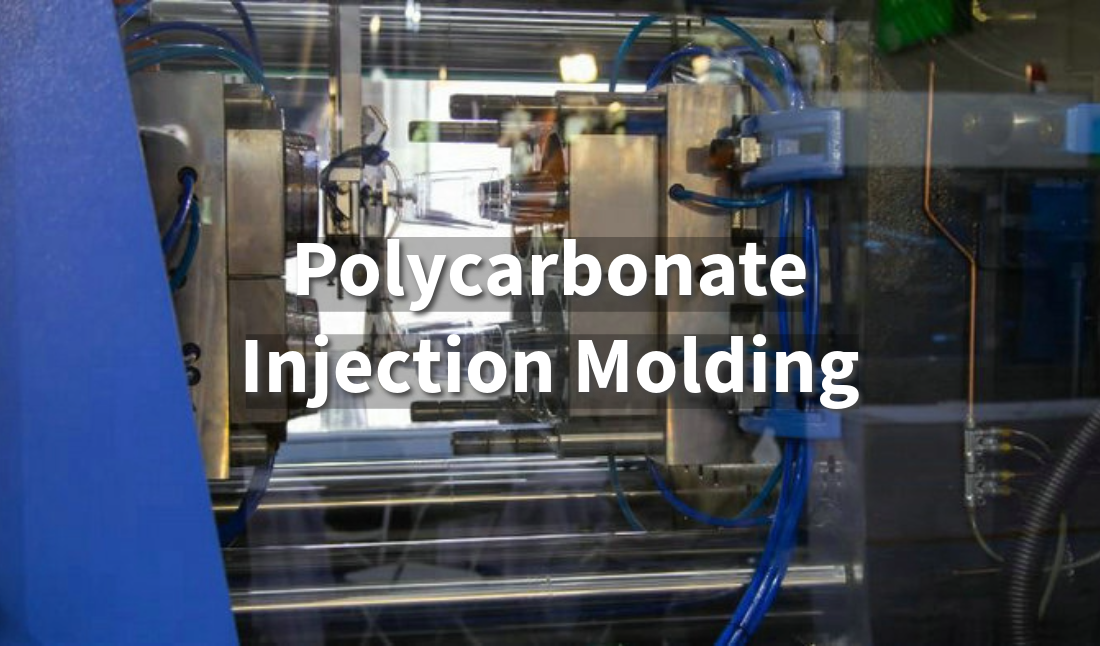
Discover how polycarbonate injection molding works, its benefits, and why it's perfect for producing high-quality, durable plastic components
Introduction to Polycarbonate Injection Molding
Polycarbonate as a Material
Polycarbonate is a type of thermoplastic known for its high impact resistance, optical clarity, and durability. It is often used to create products that need to be tough, lightweight, and transparent, such as safety glasses, electronic components, and automotive parts.
Importance of Injection Molding for Polycarbonate Products
Injection molding is a key manufacturing method used to produce polycarbonate products. This process involves injecting molten polycarbonate into a mold, where it cools and solidifies into the desired shape. Injection molding is highly efficient, allowing for the mass production of polycarbonate parts with consistent quality. It is especially useful for making complex shapes with high precision, making it an ideal choice for various industries, including automotive, electronics, and medical devices.
What is Polycarbonate Injection Molding?
Definition of Injection Molding
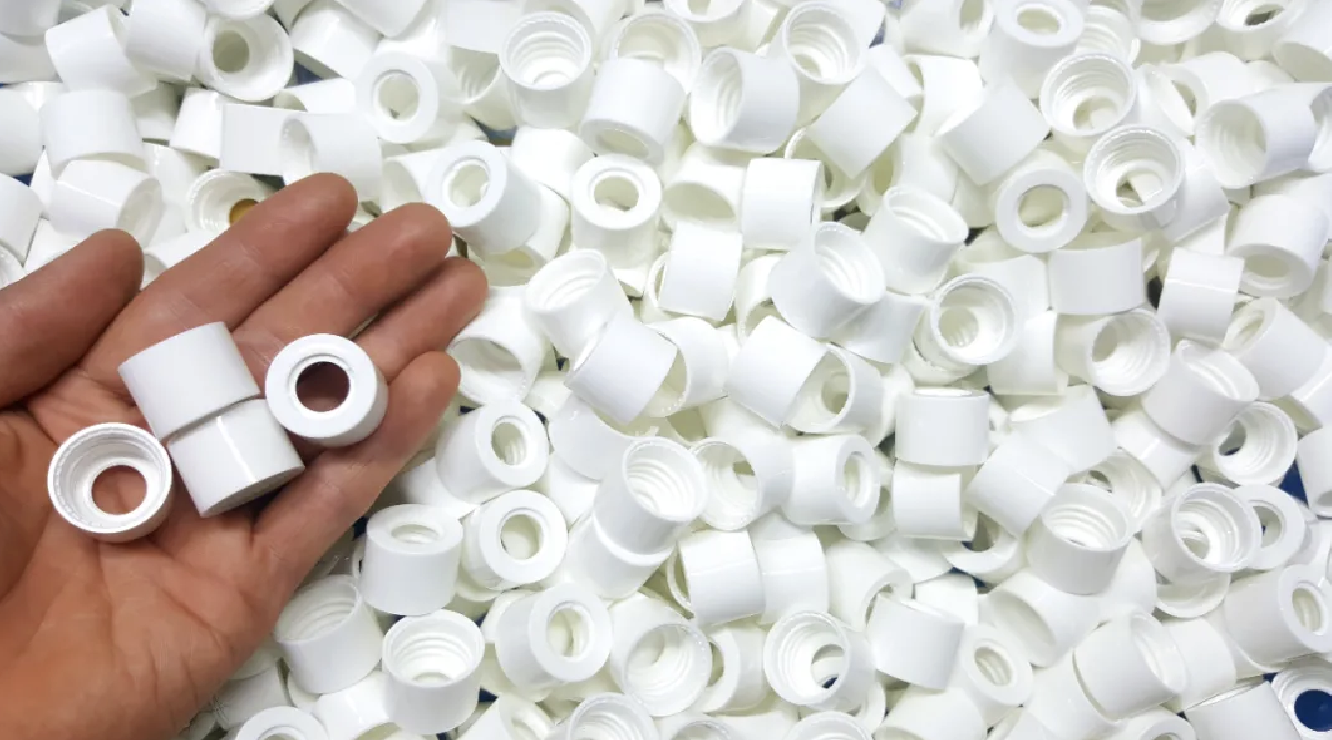
Source: Unionfab
Injection molding is a manufacturing process used to produce parts by injecting molten material into a mold. The material, usually a thermoplastic like polycarbonate, is heated until it becomes liquid, then forced into a specially designed mold where it takes the shape of the mold cavity. Once cooled, the material solidifies, creating a finished part.
Benefits of Using Polycarbonate for Injection Molding
Key Properties of Polycarbonate
Polycarbonate has several key properties that make it an excellent material for injection molding. These include:
Strength: Polycarbonate is known for its high tensile strength, making it resistant to breakage and ideal for applications requiring durability.
Transparency: The material is naturally transparent, which makes it perfect for products that require optical clarity, such as lenses and protective barriers.
Impact Resistance: Polycarbonate has excellent impact resistance, meaning it can withstand significant force without cracking or breaking.
Benefits in Manufacturing
Using polycarbonate in injection molding offers several benefits:
Durability: Polycarbonate parts are long-lasting and can handle high levels of wear and tear, making them suitable for demanding environments.
Heat Resistance: Polycarbonate can withstand high temperatures without deforming, making it ideal for applications where heat resistance is important.
Versatility: The material is versatile and can be used to create a wide range of products, from consumer goods to industrial components. Its adaptability makes it a popular choice for various industries.
The Injection Molding Process for Polycarbonate
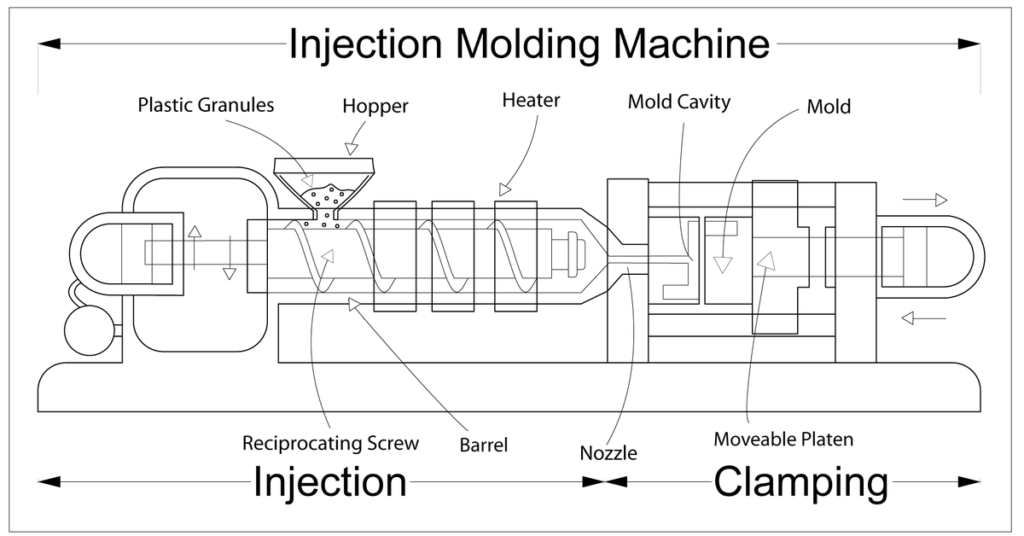
Source: weetect.com
Step-by-Step Explanation of the Process
Heating: Polycarbonate pellets are fed into an injection molding machine, where they are heated until they melt and become a thick, flowable liquid.
Injection: The molten polycarbonate is injected into a pre-designed metal mold under high pressure. The pressure ensures that the material fills every part of the mold cavity, creating the desired shape.
Cooling: Once the mold is filled, it is cooled to allow the polycarbonate to solidify. Proper cooling is crucial to avoid defects and ensure that the final part maintains its intended shape and strength.
Ejection: After the polycarbonate has cooled and solidified, the mold opens, and the finished part is ejected. The part may undergo further processing, such as trimming or surface finishing, depending on the application.
Key Parameters to Control
Temperature: The temperature of the polycarbonate must be carefully controlled to ensure it melts evenly. Too high a temperature can degrade the material, while too low a temperature can lead to incomplete filling of the mold.
Pressure: High pressure is needed to ensure that the molten polycarbonate fills the entire mold cavity. Insufficient pressure can result in voids or incomplete parts.
Cooling: Proper cooling is essential to prevent defects like warping or internal stress. Cooling must be uniform to maintain the integrity of the part.
Challenges with Polycarbonate and How to Address Them
Bubbles and Voids: Bubbles can form if the material is not heated evenly or if air is trapped during the injection process. To prevent this, precise temperature control and proper venting of the mold are necessary.
Warping: Warping can occur if the cooling process is uneven, leading to internal stresses. To minimize warping, ensure uniform cooling and avoid sudden temperature changes.
Discoloration: Overheating polycarbonate can cause discoloration. To avoid this, maintain the correct processing temperature and avoid excessive residence time in the injection molding machine.
Applications of Polycarbonate Injection Molding
Common Industries and Products
Polycarbonate injection molding is used in a wide range of industries due to the material's strength, durability, and optical clarity. Common industries include:
Electronics: Polycarbonate is widely used in electronic housings, connectors, and other components due to its excellent electrical insulation and impact resistance.
Automotive: The automotive industry uses polycarbonate for headlamp lenses, interior components, and other parts that require high durability and heat resistance.
Medical Devices: In the medical field, polycarbonate is used for items such as surgical instruments, fluid reservoirs, and protective housings because of its clarity, strength, and resistance to sterilization processes.
Examples of Successful Products Made Using Polycarbonate
Safety Glasses: Polycarbonate's impact resistance and transparency make it an ideal material for safety eyewear, providing both protection and clear vision.
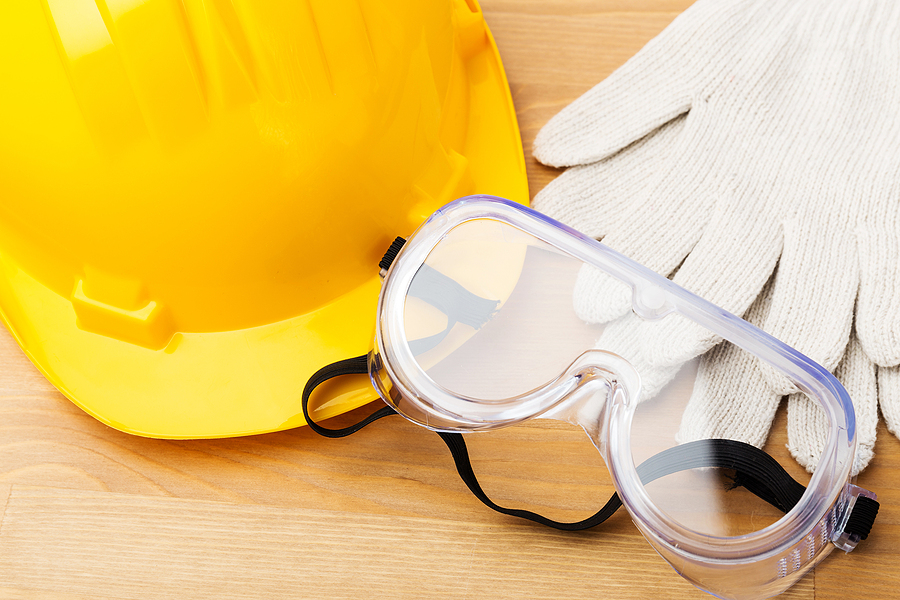
Source: midstatemold.com
Automotive Headlights: Polycarbonate is commonly used for automotive headlight lenses due to its durability and ability to withstand extreme temperatures and impact.
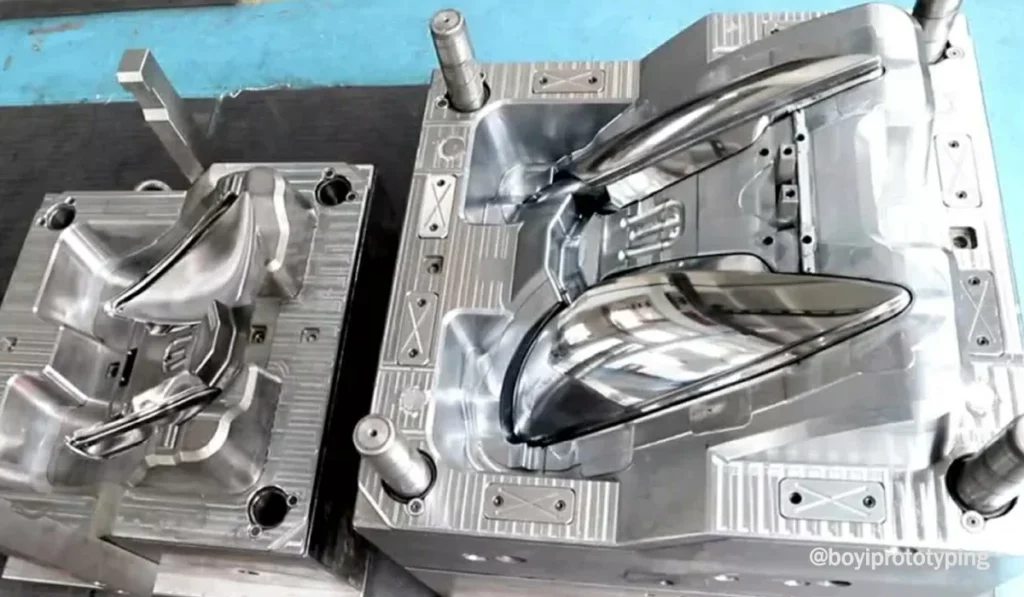
Source: boyiprototyping.com
Consumer Electronics: Products like laptop covers, smartphone cases, and electrical connectors are often made from polycarbonate due to its strength and insulating properties.
Tips for Successful Polycarbonate Injection Molding
Optimizing Molding Parameters
Control Temperature Precisely: Maintaining the correct temperature throughout the process is crucial. The polycarbonate must be evenly heated to ensure proper flow and avoid defects like bubbles or incomplete filling.
Maintain Adequate Pressure: Applying the right injection pressure ensures that the molten polycarbonate fills the entire mold cavity, avoiding defects like voids or surface flaws.
Uniform Cooling: Ensuring that the mold cools uniformly helps prevent issues like warping or internal stresses. Gradual and consistent cooling is key to achieving a stable part.
Avoiding Common Defects
Prevent Warping: To avoid warping, ensure the cooling process is even and gradual. Sudden temperature changes can create internal stresses that lead to deformation.
Minimize Bubbles: Prevent bubbles by thoroughly venting the mold and controlling the heating process to avoid air entrapment. Even melting of the polycarbonate helps ensure a smooth final product.
Prevent Discoloration: Avoid overheating the polycarbonate, as this can cause discoloration. Proper temperature management and minimizing residence time in the machine will help maintain the material's natural clarity.
Polycarbonate vs Other Materials in Injection Molding
Comparison with Other Commonly Used Materials
Polycarbonate is often compared with other thermoplastics such as ABS and Nylon when considering materials for injection molding:
Polycarbonate vs ABS: ABS is a popular thermoplastic known for its good impact resistance and cost-effectiveness. However, polycarbonate offers superior strength, optical clarity, and heat resistance compared to ABS. While ABS is less expensive and easier to process, polycarbonate is preferred for applications that require higher durability and transparency.
Polycarbonate vs Nylon: Nylon is known for its excellent wear resistance, chemical resistance, and toughness. However, polycarbonate provides better optical clarity and impact resistance, making it more suitable for applications like lenses and protective covers. Nylon is often used in applications where friction and wear are significant concerns, whereas polycarbonate is chosen for its transparency and resilience.
Why Choose Polycarbonate Over Alternatives?
Polycarbonate is selected over other materials when the application demands:
High Impact Strength: Polycarbonate's impact resistance makes it ideal for safety equipment and protective components that need to withstand physical force.
Optical Clarity: Unlike materials like ABS or Nylon, polycarbonate is naturally transparent, making it the material of choice for products requiring clear visibility, such as lenses and display panels.
Heat Resistance: Polycarbonate can tolerate higher temperatures compared to many other thermoplastics, making it suitable for applications exposed to heat, such as automotive and electrical components.
Versatility: The combination of strength, transparency, and durability makes polycarbonate a versatile choice for a wide range of industries, from consumer electronics to automotive and medical devices.
Conclusion
Polycarbonate injection molding offers significant advantages due to the material's strength, transparency, impact resistance, and heat tolerance. These properties make polycarbonate an ideal choice for a wide variety of applications, ranging from safety glasses and automotive parts to medical devices and consumer electronics. The injection molding process allows for efficient mass production of high-quality parts with complex shapes and excellent durability.
If you need a material that combines toughness, versatility, and optical clarity, polycarbonate is an excellent choice. Its use in injection molding ensures consistent, high-quality results, making it suitable for products that require durability and precision. Consider polycarbonate for your next project to benefit from its exceptional properties and manufacturing advantages.
Unionfab for Your Polycarbonate Injection Molding Needs
Ready to bring your ideas to life with polycarbonate injection molding? Contact Unionfab today for expert assistance in manufacturing high-quality, durable polycarbonate parts. Let Unionfab help you achieve the perfect solution for your project needs.
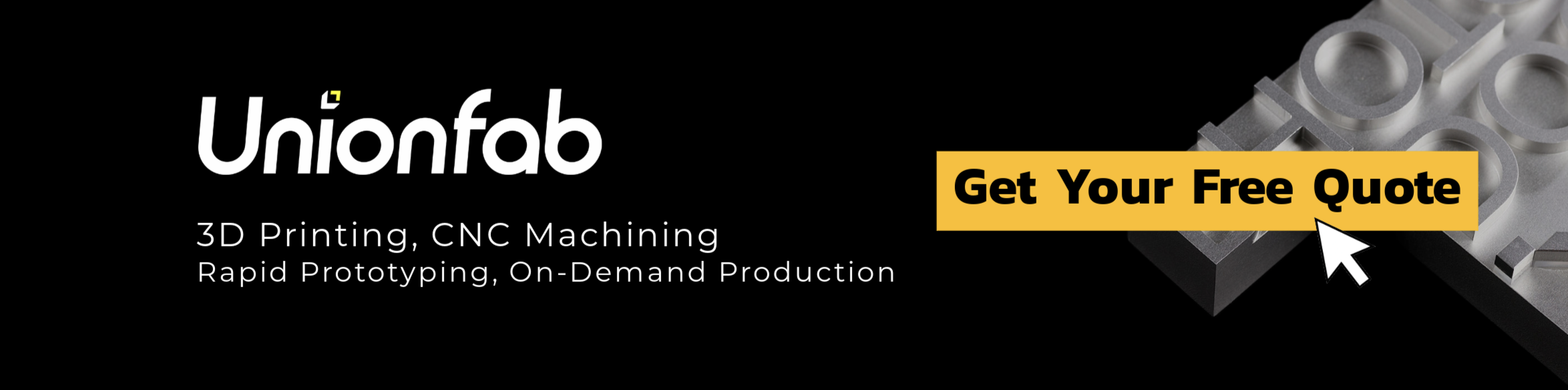