Sheet Metal Prototyping: A Definitive Guide
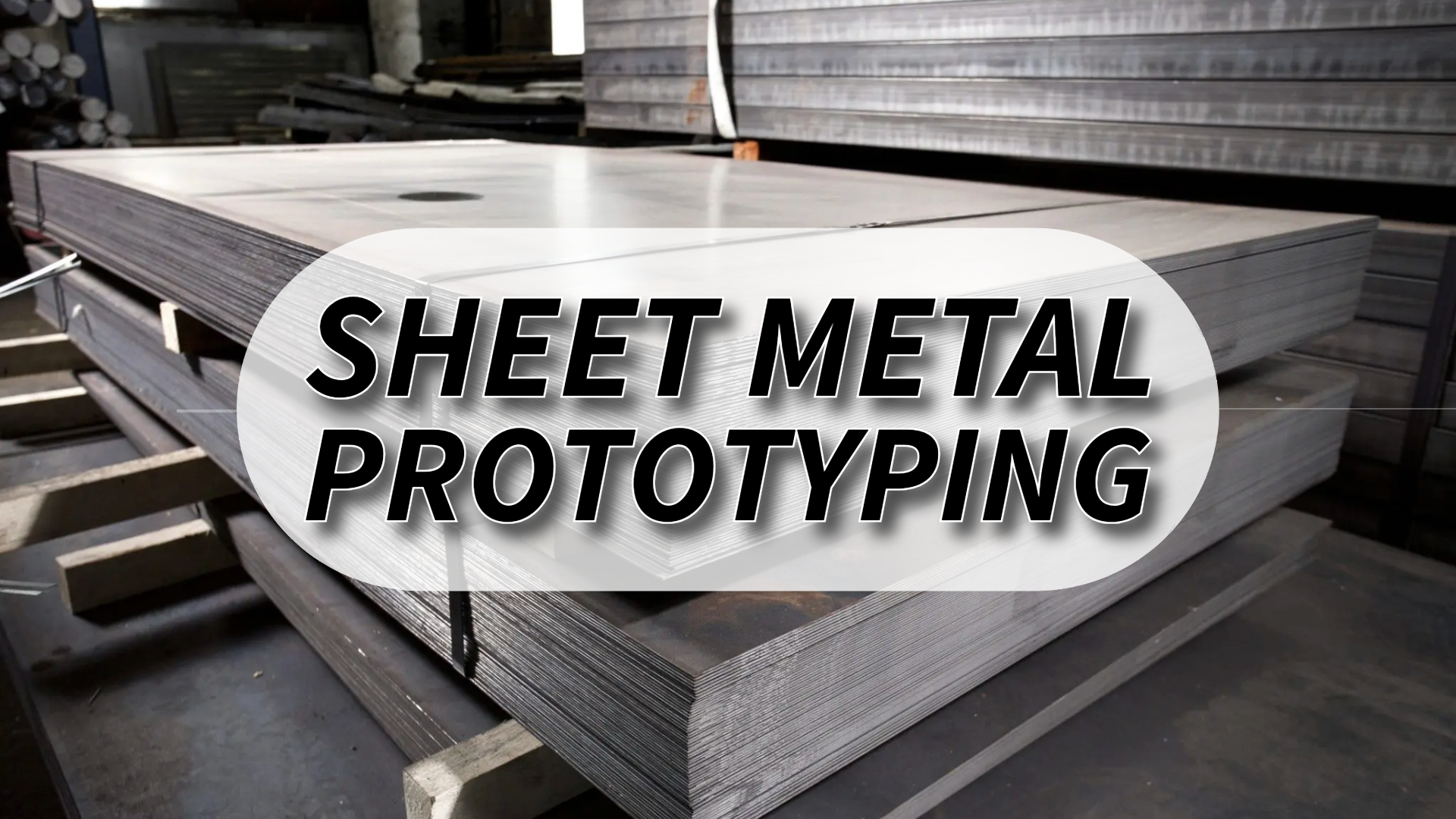
Explore the basics of sheet metal prototyping, its forming processes, materials, tolerances, benefits, and applications within one guide.
Introduction
Sheet metal prototyping is a crucial process that enables the creation of functional prototypes, closely resembling final products in both shape and usability. Widely used across industries like automotive, aerospace, and electronics, it allows for quick design iterations and practical testing before full production.
This article covers the basics of sheet metal prototyping, the forming processes and materials involved, its tolerances, benefits, and applications, offering a comprehensive guide to this versatile manufacturing approach.
Sheet Metal Basics
What is sheet metal?
Sheet metal is a versatile, thin, flat piece of metal formed into various shapes and sizes, widely used in manufacturing due to its durability, malleability, and ease of fabrication. Known for its strength and lightweight properties, sheet metal is commonly used to create everything from structural components to precision parts across industries.
Two Ways of Producing Original Sheet Metal: Hot-Rolled and Cold-Rolled
Hot-Rolled Sheet Metal: Hot-rolled sheet metal is produced by heating metal to a high temperature and then rolling it into thin sheets. This process gives the metal a rough finish but is cost-effective and ideal for larger, less precise components.
Cold-Rolled Sheet Metal: Cold-rolled sheet metal is processed at or near room temperature, resulting in a smooth, polished finish with tighter tolerances. Cold-rolled sheets are typically stronger and used for applications requiring precision and a finer appearance.
Check the video below to tell the differences between hot-rolling and cold-rolling.
Different Thicknesses of Sheet Metal
Sheet metal is available in a range of thicknesses, which influence its flexibility and strength. Thickness is commonly measured in gauge (the higher the gauge, the thinner the metal) or millimeters:
Leaf: a few atoms to 0.025mm (0.001in)
A thin sheet, often of precious metal. The most common example might be gold leaf.
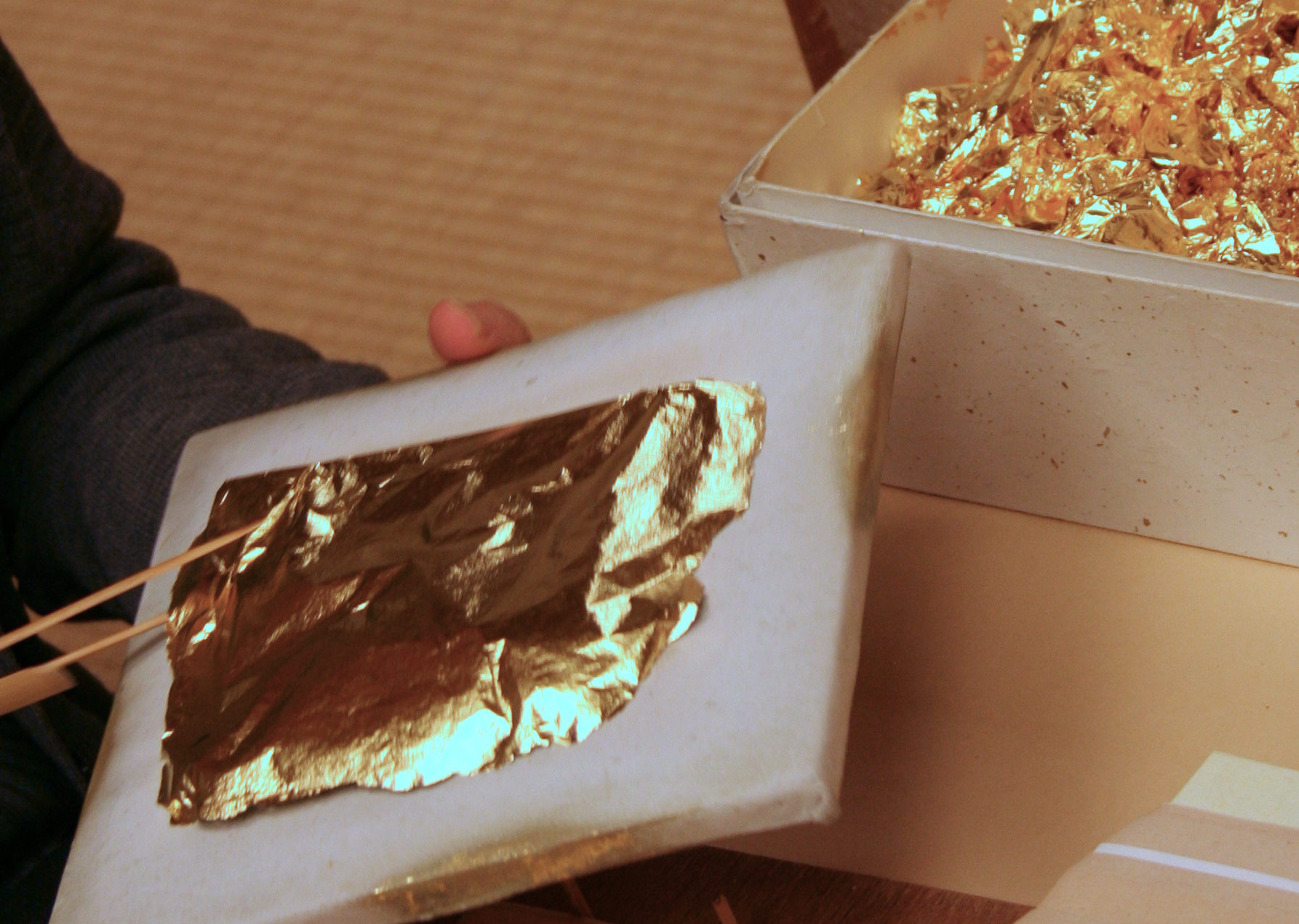
Source: By Eckhard Pecher - Own work, CC BY 2.5
Foil: 0.025mm (about 0.001in) to 0.15mm (0.060in)
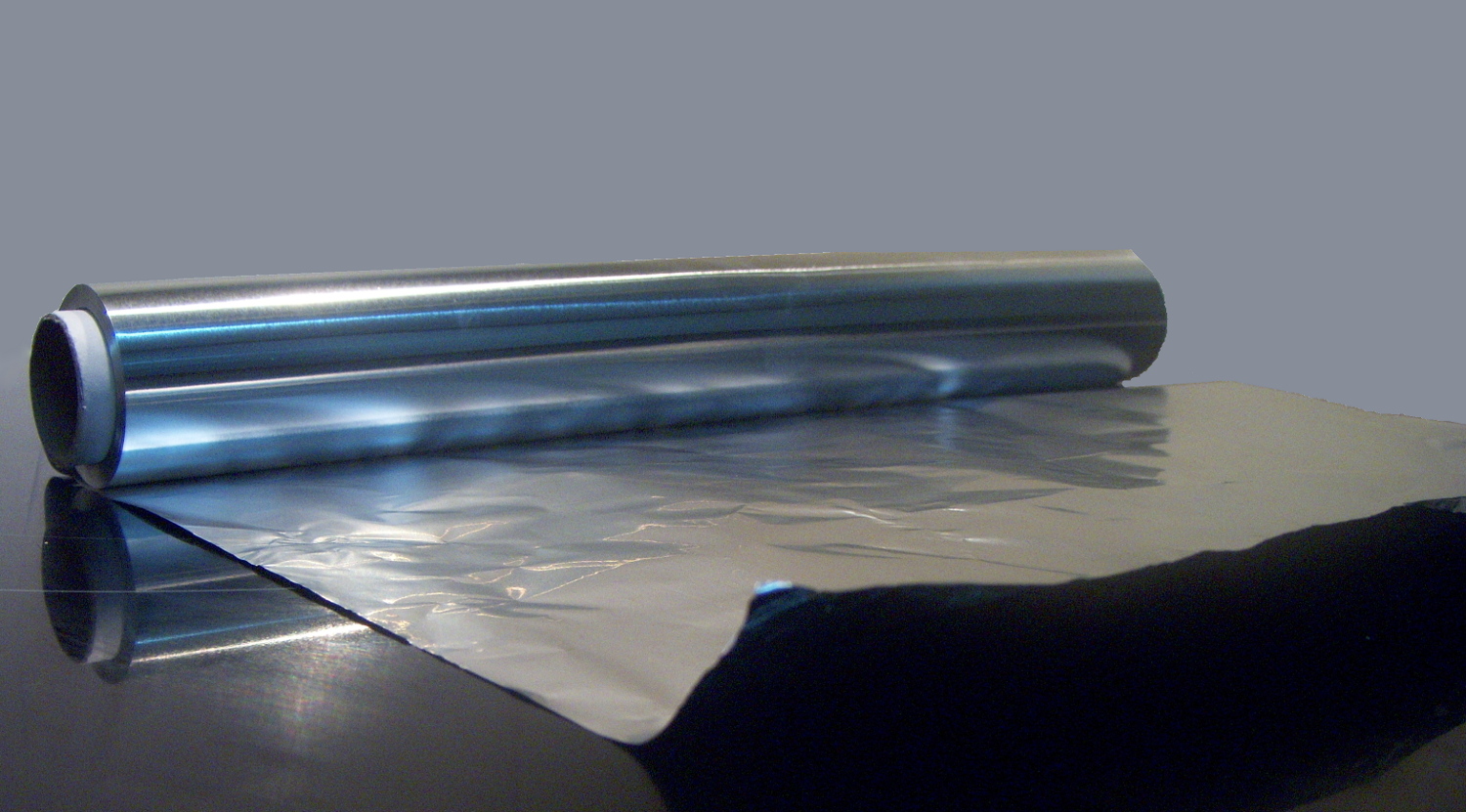
Source: en.wikipedia.org
A thin sheet, thicker than leaf and thinner than sheet. Foil is typically available in the precious metals – gold, silver, platinum and palladium – as well as other semi-precious metals such as copper and brass. Other, more commonly available metals such as aluminium are often used as foils, for example baking foil.
Sheet Metal: 0.15mm (0.06in) to 6mm (0.24in)
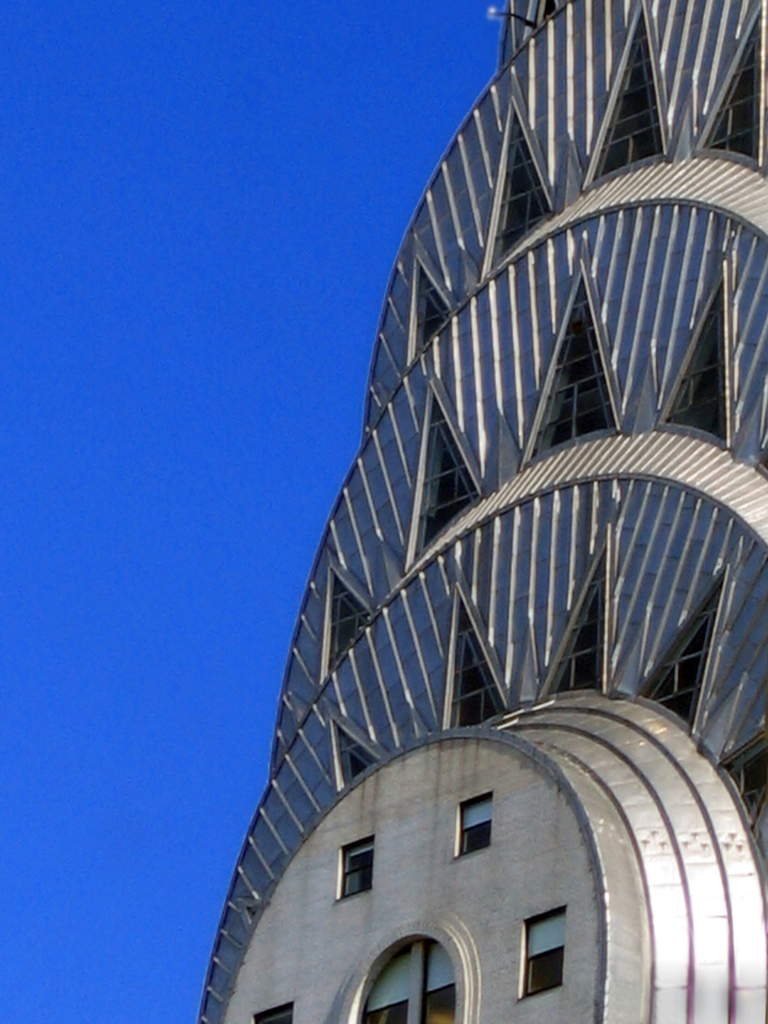
Source: en.wikipedia.org
Thinner sheets (0.15mm to 1.2mm) are often used for lightweight applications like enclosures and electronics.
Medium-thickness sheets (1.2mm to 3mm) are common in automotive and general manufacturing.
Thicker sheets (3mm to around 6mm) provide greater strength, used in applications like construction and machinery.
Plate Metal: Above 6mm
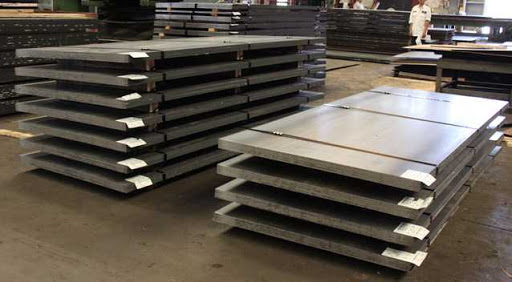
Source: www.hvrmagnet.com
Used in heavy-duty industrial applications, such as shipbuilding, bridges, large machinery, and construction. Plate metal provides the highest strength and rigidity.
For the gauge table, please refer to the file: Sheet-Steel-Gauges-and-Thicknesses
Common Materials Used in Sheet Metal Prototyping
Material | Types | Properties | Applications |
---|---|---|---|
Steel | Carbon, stainless, galvanized | Strong, durable, versatile; stainless steel is corrosion-resistant. | Automotive, appliances, construction, medical |
Aluminum | 5052, 6061, 3003 alloys | Lightweight, corrosion-resistant, high strength-to-weight ratio, easy to form | Aerospace, automotive, electronics |
Copper | Pure, copper alloys (e.g., brass) | High electrical/thermal conductivity, corrosion-resistant, attractive appearance | Electronics, HVAC, plumbing, decorative items |
Brass | Copper-zinc alloy | Corrosion-resistant, easy to shape, gold-like color, good acoustic properties | Decorative parts, musical instruments, fittings |
Titanium | Pure, titanium alloys | Strong, lightweight, corrosion-resistant, biocompatible | Aerospace, medical devices, high-end automotive |
Magnesium | Pure, magnesium alloys | Extremely lightweight, good strength-to-weight ratio, requires proper treatment for durability | Aerospace, automotive |
Forming Processes of Sheet Metal Prototyping
Cutting Processes
Laser Cutting: Uses a high-powered laser to cut precise shapes in sheet metal, ideal for intricate designs.
Water Jet Cutting: Employs high-pressure water mixed with abrasive particles to cut metal without heat, suitable for heat-sensitive materials.
Plasma Cutting: Utilizes a high-temperature plasma jet to cut thicker metals quickly, though it may lack the precision of laser cutting.
Shearing: A mechanical process that cuts metal sheets along a straight line, effective for basic shapes and straight cuts.
Punching: Involves using a punch press to create holes or specific shapes in metal by removing a portion of the material.
Perforating: Creates a series of holes in a pattern on the metal, often used for ventilation, filtration, or decorative purposes.
Bending Processes
Bending: A basic process where the sheet metal is bent to a specific angle, forming various shapes like brackets and frames.
Curling: Rolls the edges of metal sheets into a curved shape to remove sharp edges or improve rigidity.
Rolling: Uses rollers to form the metal sheet into curved or cylindrical shapes, often for creating tubes or curved parts.
Forming Processes
Hydroforming: Applies high-pressure hydraulic fluid to shape metal sheets over a mold, useful for complex geometries with uniform thickness.
Press Brake Forming: Involves pressing sheet metal into a mold using a press brake machine, suitable for creating sharp bends and precise angles.
Incremental Sheet Forming: Gradually deforms the sheet into complex shapes by applying small incremental forces, often used for prototyping.
Roll Forming: Passes the sheet metal through a series of rollers to form continuous shapes with a consistent profile, like channels or rails.
Spinning: Rotates the metal on a lathe while applying pressure to form it into round or conical shapes, suitable for symmetrical parts.
Stamping: Uses dies and presses to shape the sheet metal through processes like punching, bending, and embossing, ideal for high-volume production.
Expanding Processes
Deep Drawing: Pulls the metal into a die to create deep, hollow shapes like cups or cans, commonly used for cylindrical items.
Expanding: Stretches the metal sheet to increase surface area or create a mesh pattern, often used for filters, guards, and grilles.
3D Printing and Sheet Metal Prototyping
Integrating 3D printing with sheet metal prototyping is a powerful approach in modern manufacturing. Although traditionally applied to plastic or resin materials, 3D printing techniques have evolved to work with metal powders and hybrid materials, allowing for unique applications in sheet metal prototyping. Here’s how 3D printing enhances sheet metal prototyping:
Rapid Tooling and Molds
3D printing can quickly create custom tooling, molds, or jigs used in sheet metal forming processes. This allows manufacturers to test and refine designs without waiting for conventional tooling, reducing lead times and costs.
Complex Geometries
3D printing enables the creation of intricate designs that would be challenging or impossible with traditional sheet metal techniques alone. Components like internal cooling channels or lattice structures can be combined with sheet metal parts, offering advanced functionality without additional assembly.
Metal Prototypes and Hybrid Parts
With metal additive manufacturing, parts can be printed directly in metal or created in hybrid form, where 3D-printed parts are incorporated with traditional sheet metal components. This approach allows for lightweight structures and complex forms while maintaining durability.
Reduced Waste
3D printing minimizes waste by building up only the necessary material. This contrasts with subtractive sheet metal processes, like cutting, which may produce scrap material. Reducing waste contributes to sustainability and cost-effectiveness.
Customization and Small Batch Production
For low-volume production, custom designs, or highly specialized components, 3D printing combined with sheet metal offers flexibility in meeting unique specifications without costly retooling.
By combining the strengths of 3D printing and sheet metal prototyping, manufacturers can achieve high levels of customization, precision, and efficiency, opening new possibilities across industries.
Using 3D Printing to Empower Your Product Innovations
For more information about 3d printing, feel free to contact Unionfab, China's largest 3D printing manufacturing company, offering expertise in rapid prototyping and on-demand production to meet evolving industry needs.
With over 20+ years' experience, 1000+ industrial 3D printers and the ISO 9001 certification, we deliver cost-effective and quality services that are 70% cheaper than counterparts and ensure rapid air shipments in 3-5 days via DHL Express and FedEx.
Post-processings
Decambering
Purpose: Used to straighten sheet metal that may have warped or bent during earlier processes like cutting or stamping.
Process: A force is applied to the metal to correct bends and restore flatness. Decambering is essential for parts requiring high precision and flatness.
Ironing
Purpose: Often used on deep-drawn sheet metal parts to ensure a consistent wall thickness.
Process: Pressure is applied to thin and even out the metal’s thickness across the piece. This is commonly used for thin-walled containers like beverage cans and battery casings.
Wheeling
Purpose: A method for creating smooth, complex curves on sheet metal, often for automotive or aerospace parts.
Process: Using an "English wheel" or similar tool, the metal is gradually shaped by rolling it, which allows for precise, smooth curvatures.
Hemming and Seaming
Purpose: Used to fold or roll the edges of sheet metal to create seams or strengthened edges, often for safety, durability, or to connect pieces.
Process: The edge of the sheet metal is folded over itself or another piece to create a smooth, reinforced edge. This process is frequently seen in car doors and appliance exteriors.
Flanging
Purpose: Increases edge strength or provides an interface for connecting parts by bending the edge of the sheet metal.
Process: The edge of the metal is bent up or outwards to form a flange. This added edge strength is useful for mounting and connecting metal parts securely.
Finishes
Painting / Powder Coating
Painting: A liquid paint coating applied to metal surfaces for color, protection, and aesthetic enhancement. It provides corrosion resistance and can be applied in various finishes (matte, gloss, etc.).
Powder Coating: A dry powder coating is electrostatically applied and then cured under heat, creating a durable, uniform finish. It’s highly resistant to chipping, scratching, and fading, ideal for outdoor applications.
Electroplating
Electroplating involves depositing a thin layer of metal (such as nickel, chrome, or zinc) onto the surface of a sheet metal component through an electric current. This coating enhances corrosion resistance, adds a decorative finish, and increases surface hardness.
Anodizing
Anodizing is an electrochemical process that creates a protective oxide layer on aluminum and other metals. It increases corrosion resistance, wear resistance, and allows for color customization. Anodized finishes are often seen in consumer electronics and architectural elements.
Brushing
Brushing involves using an abrasive belt or brush to create a fine, linear texture on the metal surface. This finish reduces surface reflections, provides a uniform appearance, and hides minor scratches, commonly used in stainless steel appliances and hardware.
Polishing
Polishing smoothens the metal surface to a high-gloss finish, enhancing reflectivity and appearance. Often used on decorative or high-visibility parts, it provides an aesthetic appeal and can help reduce surface imperfections for applications like mirrors or hardware.
Galvanizing
Galvanizing involves coating the metal, typically steel, with a protective layer of zinc to prevent rust and corrosion. This is achieved through hot-dip galvanizing or electro-galvanizing, commonly used for structural and outdoor applications where durability is crucial.
Tolerances in Sheet Metal Prototyping
Achieving precise tolerances in sheet metal prototyping is essential for ensuring that parts fit together correctly and function as intended. Common tolerance guidelines for sheet metal parts include:
General Tolerances
Standard tolerances for most sheet metal parts range from ±0.5mm to ±1.0mm.
For smaller parts or high-precision applications, tolerances can be reduced to ±0.2mm or less, though achieving this requires advanced machinery and careful setup.
Bend Tolerances
Bend tolerance affects the accuracy of angles and is often defined as ±1 degree for most applications.
Variations may occur due to material thickness, bend radius, and tool wear. Larger angles generally have looser tolerances compared to tighter, smaller angles.
Flatness and Straightness Tolerances
Flatness tolerances ensure that parts lay flat without excessive warping, typically within 0.5mm per 300mm of material.
Straightness is essential for parts with long, straight edges and is often kept within 0.3mm per 100mm.
Hole and Slot Tolerances
Tolerances for holes, slots, and cutouts generally range from ±0.1mm to ±0.25mm, depending on the diameter and function of the hole.
For precision-aligned holes or assembly purposes, tighter tolerances can be achieved with specialized cutting methods like laser cutting.
Thickness Tolerance
Variations in sheet thickness can impact bending and other forming processes. Standard thickness tolerance for most metals is ±10% of the material thickness.
For critical applications, more stringent tolerances are required, which may impact material cost and machining time.
Tips for Managing Tolerances in Sheet Metal Prototyping
Use CAD and CAM Tools: Precise modeling and programming can help manage tolerances by simulating dimensions and machining paths.
Choose the Right Process: Processes like laser cutting and CNC bending provide tighter tolerances than manual methods.
Inspect Regularly: Perform dimensional inspections at each stage to catch deviations early, minimizing waste and rework.
Benefits of Sheet Metal Prototyping
Cost-Effective: Enables affordable design testing and iteration before large-scale production, reducing costly errors. ⠀
Fast Turnaround: Modern cutting and forming tools allow quick prototype creation, speeding up project timelines. ⠀
Design Flexibility: Supports complex shapes and easy adjustments, accommodating a range of design needs. ⠀
Realistic Testing: Prototypes closely mimic final products in durability and functionality, ideal for performance testing. ⠀
Material Options: Offers choices like steel, aluminum, and titanium, allowing selection based on specific properties needed.
Seamless Scalability: Easy transition to mass production, ensuring consistency between prototypes and final products.
Aesthetic Finishing: Allows for surface finishes like painting and anodizing, giving an accurate look and feel for the final product.
Applications of Sheet Metal Prototypes
Automotive Industry
Used to develop and test components like chassis, brackets, and body panels, ensuring parts meet safety and durability standards before mass production.
Automotive Sheet Metal Parts
Aerospace and Defense
Prototypes for components such as airframes, enclosures, and structural supports allow for testing under extreme conditions, ensuring performance and compliance with strict regulations.
Sheet Metal Aircraft Parts
Source: kdmfab.com
Electronics
Sheet metal prototypes are used for cases, frames, and mounting brackets in devices, helping refine designs for thermal management, durability, and assembly.
Extruded Aluminum Heat Sink
Source: customthermoelectric.com
Medical Devices
Prototyping enables precise design of equipment enclosures, brackets, and mounts, ensuring functionality and sterilizability, essential for medical applications.
Medical Sheet Metal Parts
Source: protolabs
Consumer Goods
Helps in the design of products like kitchen appliances, furniture, and lighting fixtures, where aesthetics and durability are key.
Sheet Metal Prototype of a Built-in Kitchen Oven
Source: prototek.comConstruction and Infrastructure
Prototypes of structural components, such as supports, brackets, and panels, are tested for strength and stability, allowing for quality assurance in building projects.
L-Bracket
Source: worthyhardware.com
Industrial Equipment
Used to create parts for machinery, such as enclosures, hoods, and safety guards, enabling functional testing to confirm that designs withstand industrial demands.
Machine Guard Enclosures
Source: totalshield.com
Conclusion
Sheet metal prototyping is an essential tool in modern manufacturing, providing a cost-effective and efficient way to create and test functional designs across industries.
It allows for precise testing and real-world application evaluations before full-scale production. By integrating forming processes, advanced materials, and even 3D printing, manufacturers can achieve a high level of customization and quality.
Whether for durability, flexibility, or aesthetics, sheet metal prototyping ensures that every component meets exacting standards, paving the way for innovative and reliable products.