All About Vertical Milling: Key Insights and Practical Tips
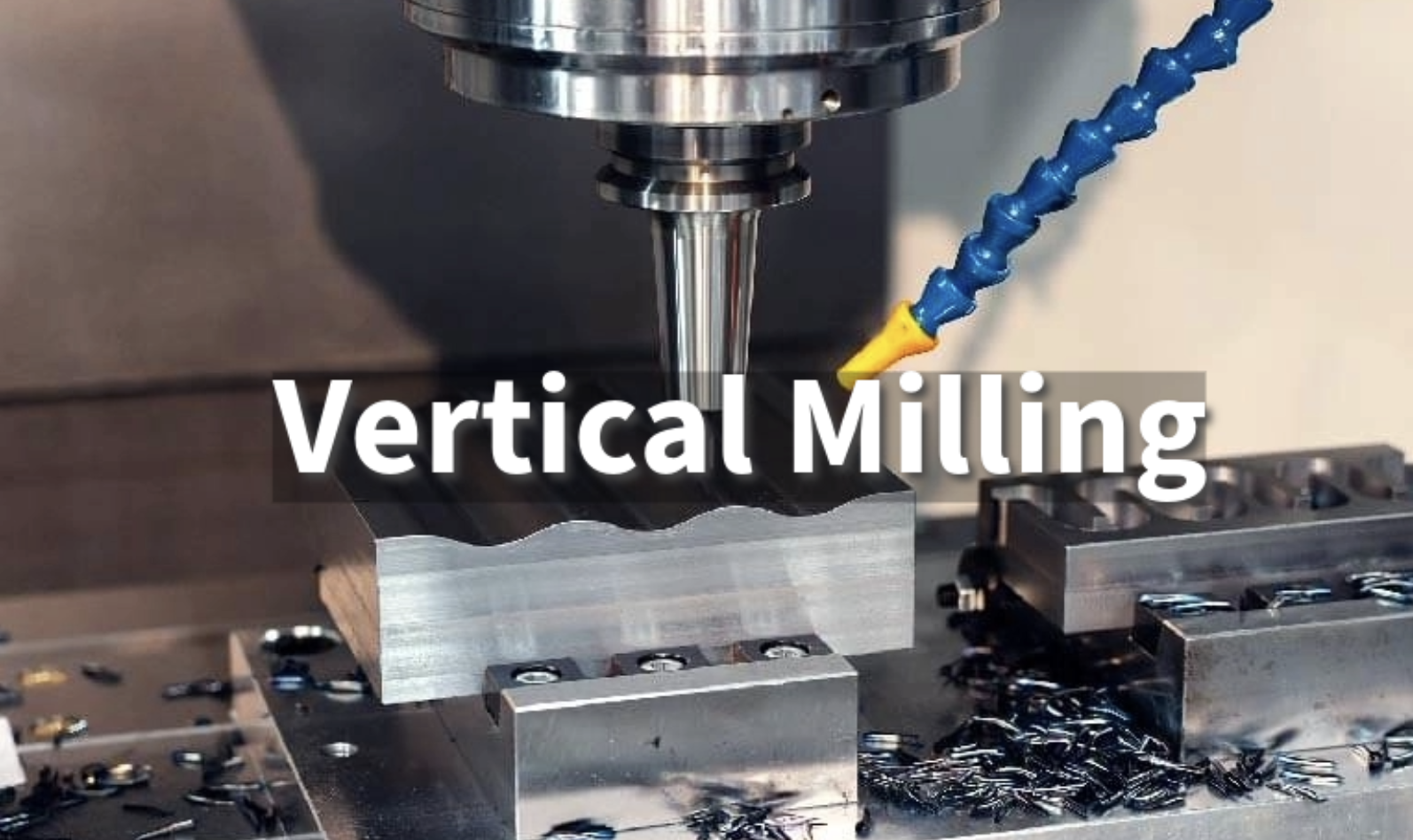
Explore the fundamentals of vertical milling, from advantages to essential applications, and learn how it enhances precision machining for your projects.
Introduction to Vertical Milling
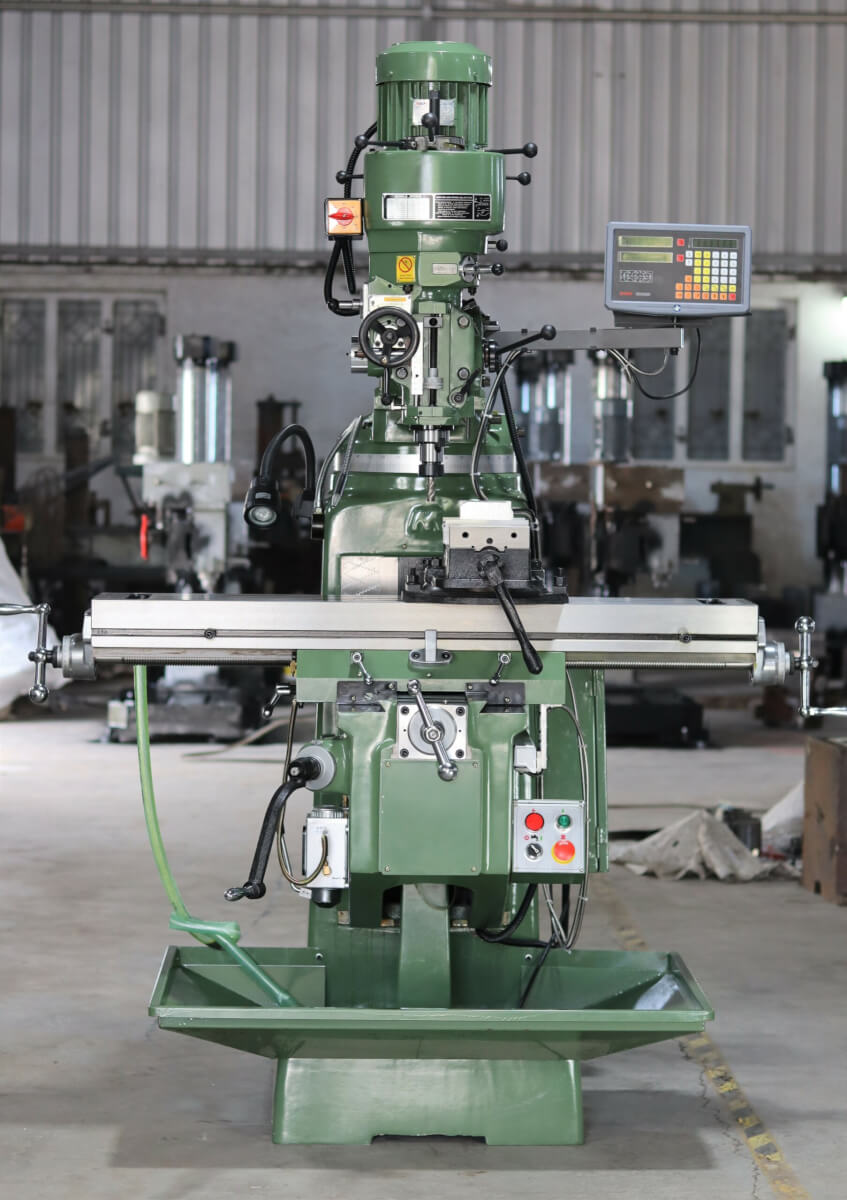
Source: ravimachines.com
Brief Overview of Milling in CNC
Milling is a basic CNC (Computer Numerical Control) process where a rotating tool cuts material away from a workpiece to create a desired shape. It is widely used in manufacturing to make precise and complex parts.
Definition and Purpose of Vertical Milling
Vertical milling is a type of milling where the cutting tool is attached to a spindle that is oriented vertically. This type of milling is used to create detailed shapes and features on different materials like metal, plastic, or wood by moving the tool up and down.
What is Vertical Milling?
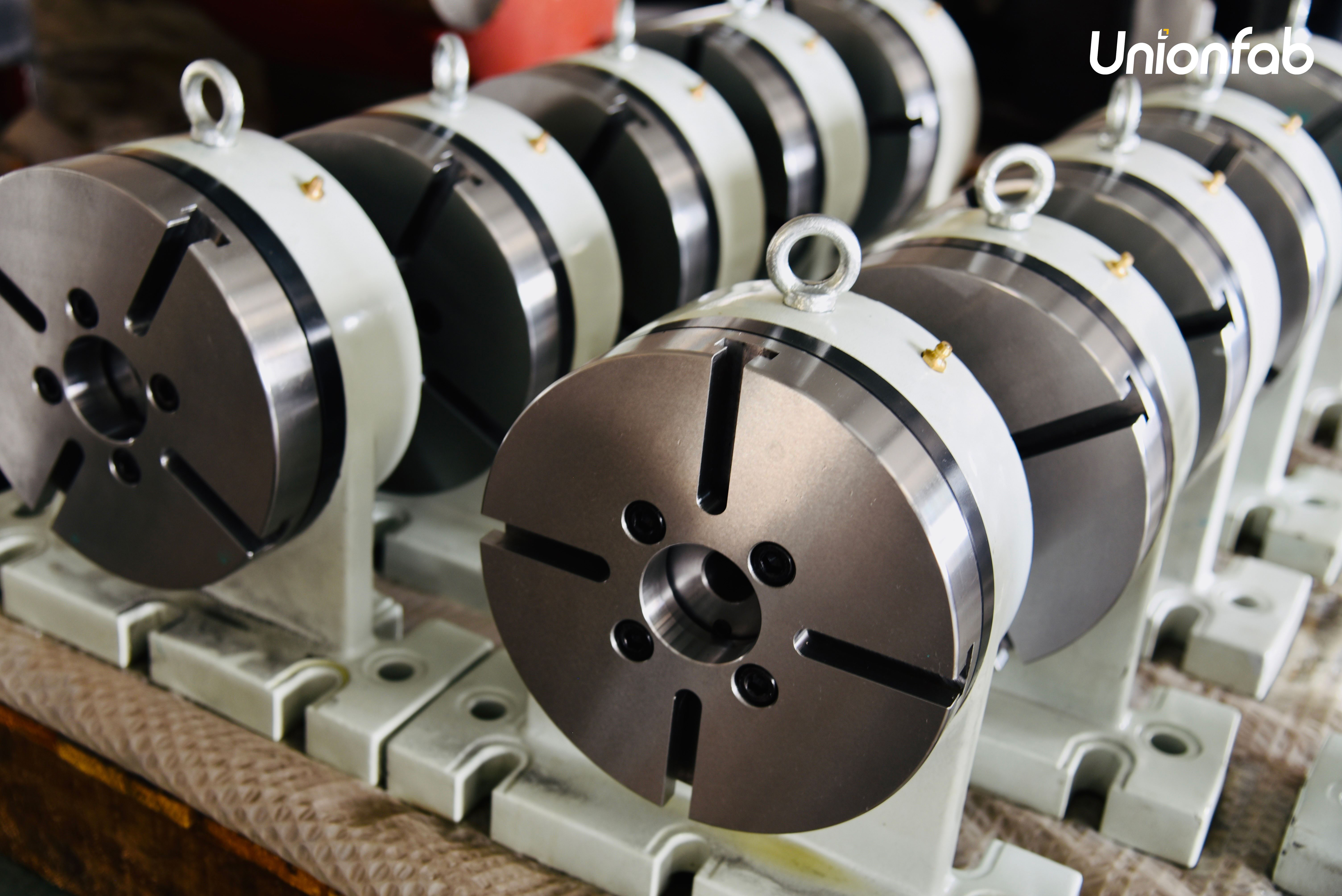
Source: Unionfab
Vertical milling is a machining process where a spinning tool removes material from a solid piece to shape it. The cutting tool is attached to a vertical spindle, which moves up and down to create precise shapes. The tool can also move side to side and front to back, allowing for a variety of operations.
How Vertical Milling Works
Basic Working Principle
In vertical milling, the workpiece is held on a table that can move side to side (X direction) and front to back (Y direction). The cutting tool is mounted on a vertical spindle that moves up and down (Z direction). By controlling these movements, the machine shapes the workpiece with accuracy. The speed of the spindle, depth of cut, and feed rate are adjusted to create the desired part.
Key Components
Spindle Orientation: The spindle is vertical, allowing the cutting tool to move up and down, which is great for making detailed features.
Cutting Tools: Different tools, like end mills and drills, can be used to cut, drill, and tap materials.
Workpiece Positioning: The workpiece is fixed on the table, which moves in the X and Y directions, allowing precise shaping by combining table and spindle movements.
Parts of a Vertical Milling Machine
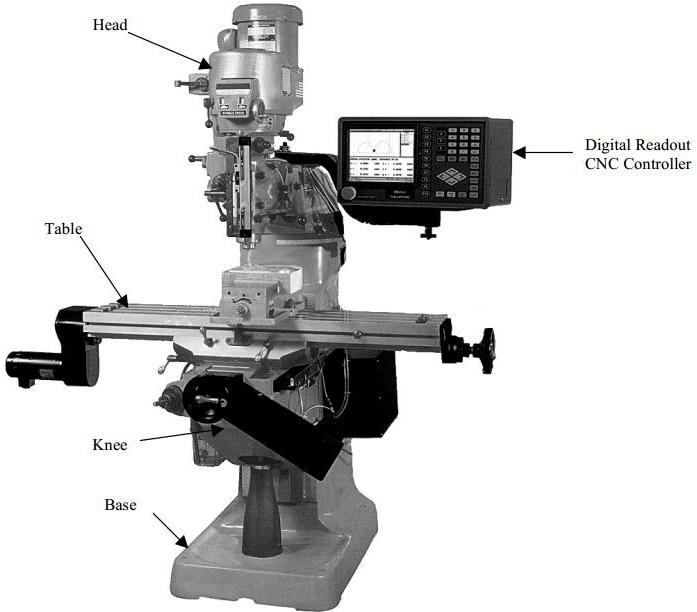
November 2013, International Journal of Advanced Trends in Computer Science and Engineering 2(6):129-135
Spindle: Holds the cutting tool and spins it to remove material.
Table: Supports and moves the workpiece in different directions.
Saddle: Moves the table front to back (Y direction).
Knee: Supports the saddle and table, allowing vertical movement.
Base: Provides stability to the machine and supports all other components.
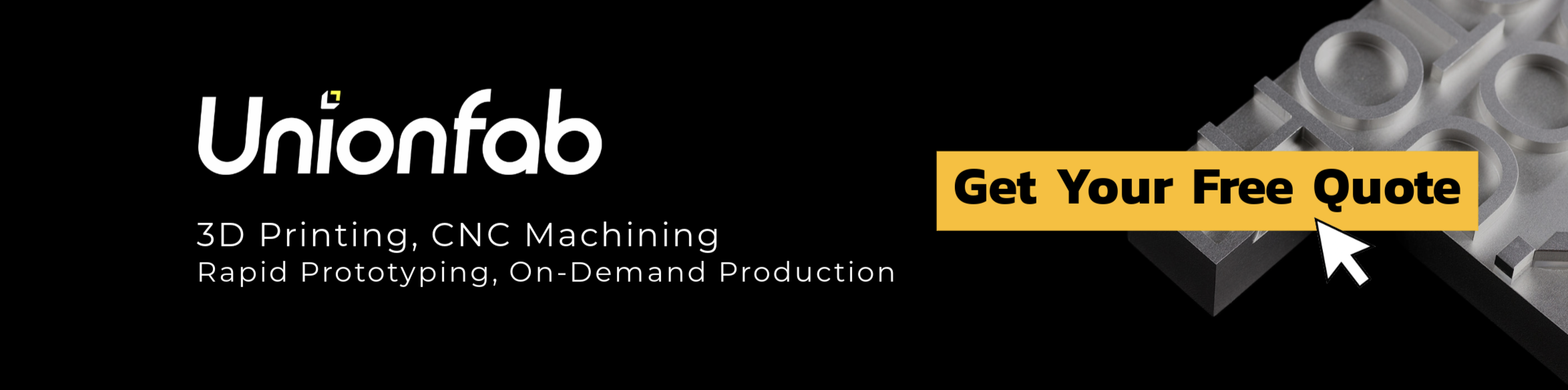
Common Applications of Vertical Milling
Industries that Rely on Vertical Milling
Vertical milling is used in industries like automotive, aerospace, and manufacturing. These industries need precise, high-quality parts, making vertical milling a popular choice for creating complex components.
Types of Parts and Products Typically Produced
Vertical milling is used to make parts like engine components, brackets, mold tools, and custom fixtures. It is great for making detailed features, drilling holes, and cutting grooves or profiles in different materials, like metals and plastics.
Advantages of Vertical Milling
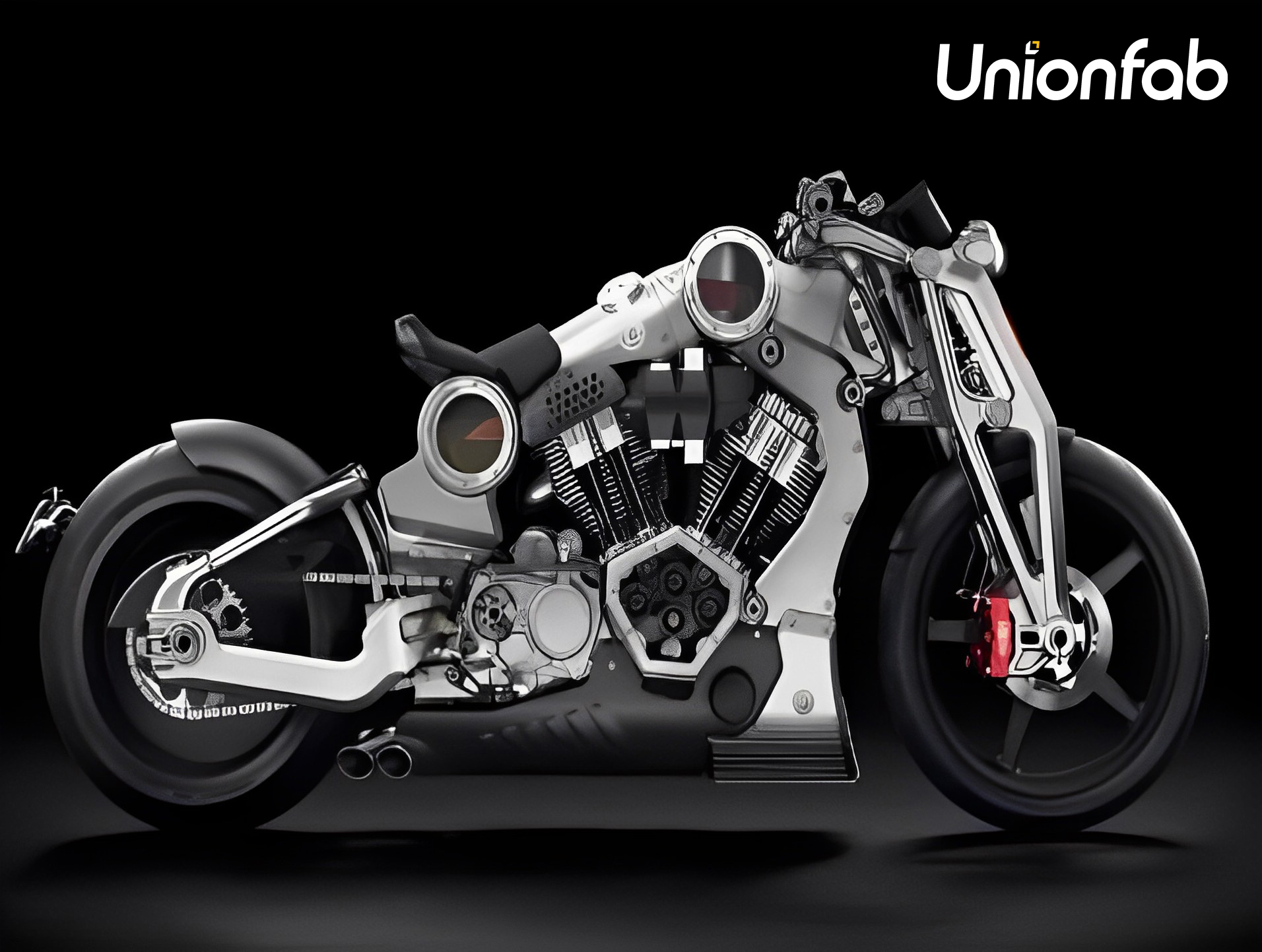
Source: Unionfab
High Precision and Detail Control: Vertical milling machines offer high accuracy, making them perfect for creating detailed and complex parts.
Ease of Setup and Operation: These machines are easy to set up and operate. The operator has a clear view of the workpiece, which makes alignment and adjustments simpler.
Cost-Effectiveness in Various Applications: Vertical milling machines are versatile and can do many operations like drilling, cutting, and tapping, which makes them cost-effective for a wide range of tasks.
Limitations of Vertical Milling
Height Limitations: Vertical milling machines have limits on how tall the workpiece can be, which restricts the size of parts that can be made.
Material Removal Rate: They generally remove material slower than horizontal milling machines, making them less efficient for large-scale work.
Comparing Vertical and Horizontal Milling
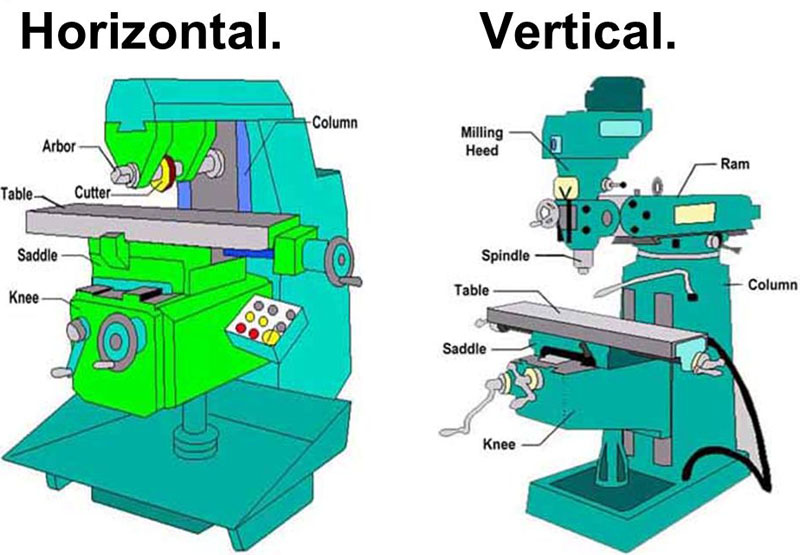
Source: sansmachining.com
Key Differences
Spindle Orientation: Vertical milling has a vertical spindle, while horizontal milling has a horizontal one. This affects how the tool interacts with the workpiece and the types of operations possible.
Material Removal Rate: Horizontal milling can remove material faster because it can use multiple tools at once, while vertical milling is slower but more precise.
Visibility and Ease of Use: Vertical milling allows better visibility of the workpiece, making it easier for operators, while horizontal milling is better for handling heavier, larger parts but takes more time to set up.
Situations Where One is Preferred Over the Other
Vertical Milling: Best for detailed, complex parts that need high precision and operations that need frequent adjustments.
Horizontal Milling: Ideal for larger parts that need heavy material removal and for projects where speed is important.
Tips for Effective Vertical Milling
Choosing the Right Tools
Choosing the right cutting tools is important for successful vertical milling. Tools like end mills, face mills, and drills are commonly used. The choice depends on the material and the type of cut needed. High-speed steel (HSS) or carbide tools are popular for their strength and efficiency.
Speed, Feed, and Depth Considerations
Setting the correct speed (RPM), feed rate, and depth of cut is important for good results and to make the tools last longer. The speed should match the type of material being cut, while the feed rate determines how quickly the tool moves through the material. The depth of cut should be adjusted based on the hardness of the material and how sturdy the machine setup is.
Maintenance and Troubleshooting Tips
Regular maintenance is important for keeping a vertical milling machine working well. This includes lubricating moving parts, checking the spindle, and making sure the table is clean. Troubleshooting problems like tool chatter, poor surface finish, or misalignment can be done by checking if the tool is sharp, adjusting feed rates, and making sure the machine is calibrated correctly.
Conclusion
Vertical milling is a flexible machining process that offers high precision, easy setup, and cost-effectiveness. It is widely used to create detailed parts, making it an essential tool for manufacturing tasks that need accuracy and flexibility.
Experience Precision with Unionfab’s CNC Milling Services
With over 20 years of manufacturing expertise and ISO 9001:2015 certification, Unionfab delivers precision engineering across multiple technologies:
✓ Molding
✓ Professional Casting Services
Whether you need CNC milling, rapid prototyping, or complex casting, our team of expert engineers is ready to optimize your project from prototype to production.
Get an instant quote today and experience Unionfab’s manufacturing excellence!
Contact Unionfab — Where Innovation Meets Precision.