Mastering Horizontal Milling: Everything You Need to Know
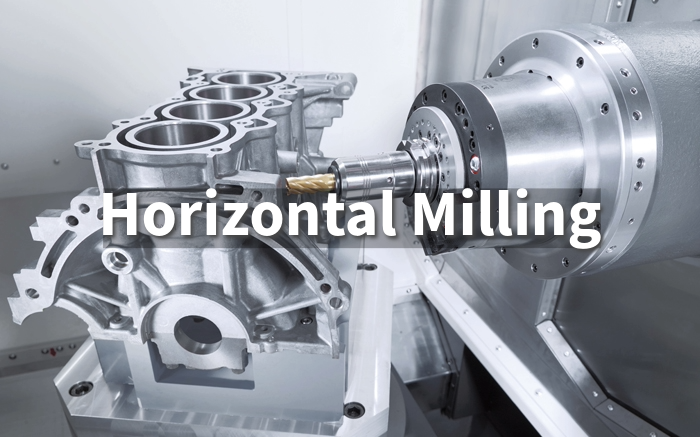
Discover how horizontal milling can enhance efficiency and precision in CNC projects, and learn when it's the perfect fit for your machining needs.
Introduction to Horizontal Milling
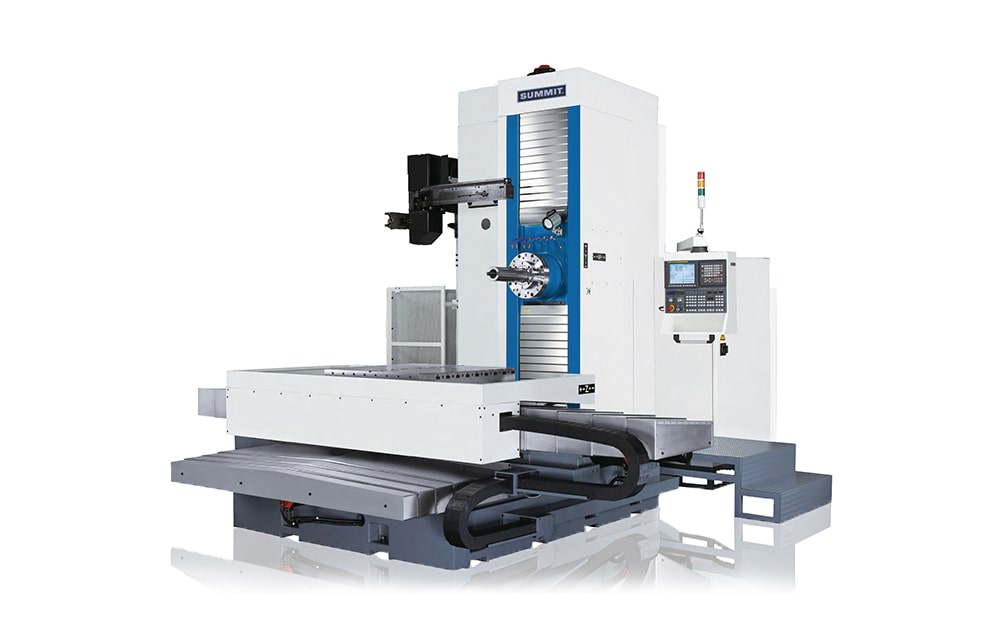
Source: summitmt.com
What is Horizontal Milling?
Horizontal milling is a type of machining that shapes materials like metal and plastic. It uses a machine with a cutting tool that is positioned horizontally. The cutting tool spins and removes material from the piece to create the desired shape or surface.
How is Horizontal Milling Different from Vertical Milling?
In horizontal milling, the cutting tool is placed parallel to the ground. This is different from vertical milling, where the cutting tool is positioned upright, like a drill. The horizontal position makes it easier to cut along the sides of the material, which is great for deep cuts and heavy materials. Vertical milling is better for working on flat surfaces and doing lighter, more detailed work, while horizontal milling is used for larger projects that need more power.
How Horizontal Milling Works
How Horizontal Milling Machines Operate
Horizontal milling machines use a spinning cutting tool to shape the material. The tool is mounted on a horizontal spindle, allowing it to move along the workpiece horizontally. The workpiece is held in place on a worktable, which can move in different directions (left-right, forward-backward) to help make precise cuts.
Key Parts of Horizontal Milling Machines
Horizontal Spindle: This part holds and spins the cutting tool. It is positioned horizontally, which gives horizontal milling its name.
Cutters: These are the rotating tools that remove material from the workpiece. They come in different shapes and sizes, depending on the type of cut needed.
Worktable: The workpiece is held on the worktable, which can move in different directions to position the material under the cutting tool correctly.
Advantages of Horizontal Milling
Higher Efficiency for Certain Operations
Horizontal milling machines are very efficient for cutting along the sides of a workpiece. The horizontal position allows for faster and stronger cutting, which makes the process quicker and more productive.
Handling Heavier Cuts
Horizontal milling is perfect for removing a lot of material and for larger projects. The horizontal spindle can hold bigger cutters, making it good for heavy cuts and tougher materials.
Good for Batch Production
Horizontal milling machines are often used in settings where many parts need to be made quickly. They are great for consistent, high-volume production.
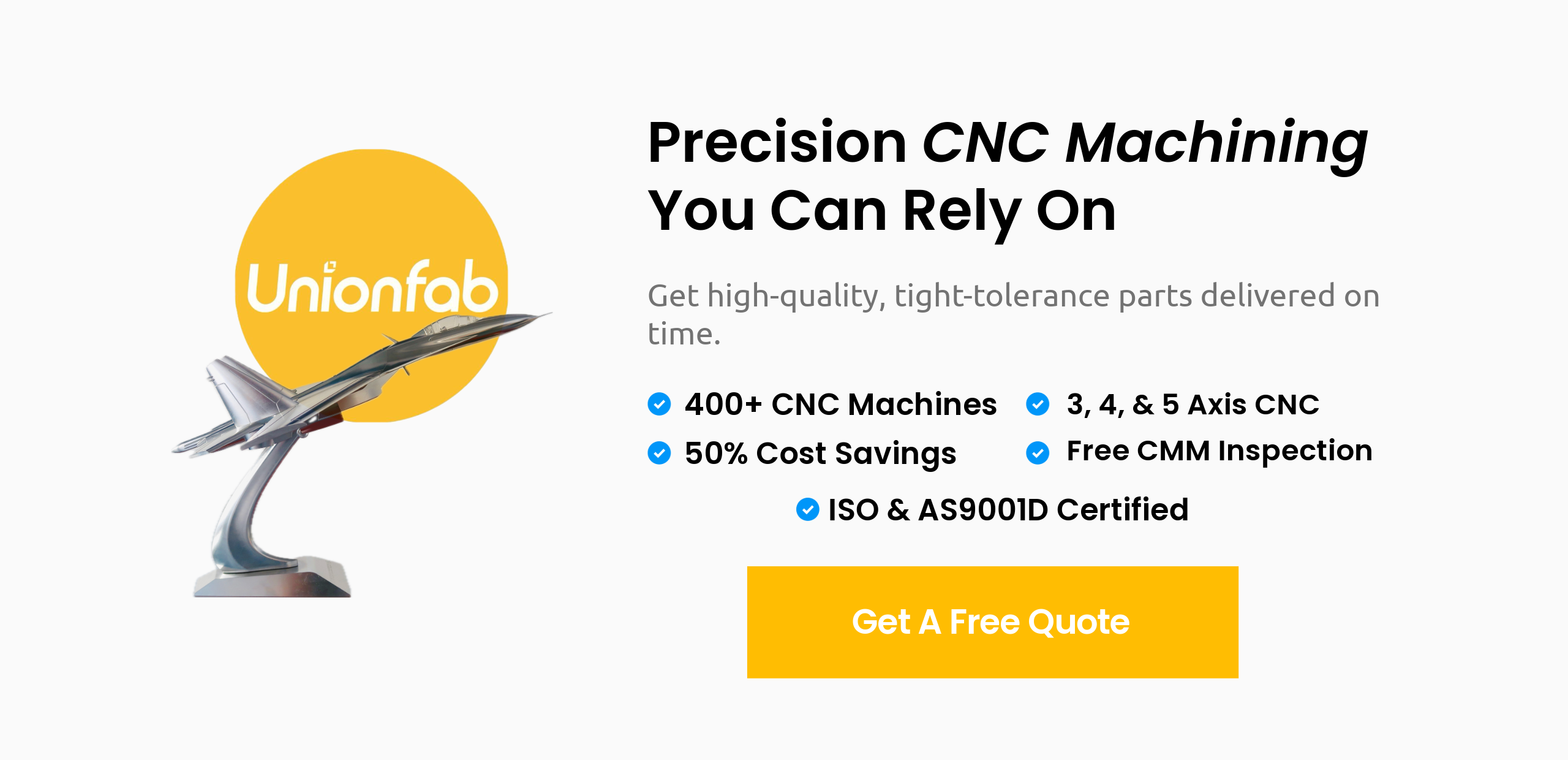
Applications of Horizontal Milling
Projects and Industries That Use Horizontal Milling
Horizontal milling is often used in industries that need to remove a lot of material or handle tough projects. It is commonly used in the automotive, aerospace, and heavy equipment industries. These industries need parts that require deep cuts, slots, or multiple pieces to be cut accurately and efficiently.
Common Materials Used in Horizontal Milling
Horizontal milling can work with many materials, including steel, cast iron, brass, and other metals that need heavy material removal. It can also be used to shape plastics and composite materials, making it useful for different manufacturing needs.
Horizontal Milling vs. Vertical Milling
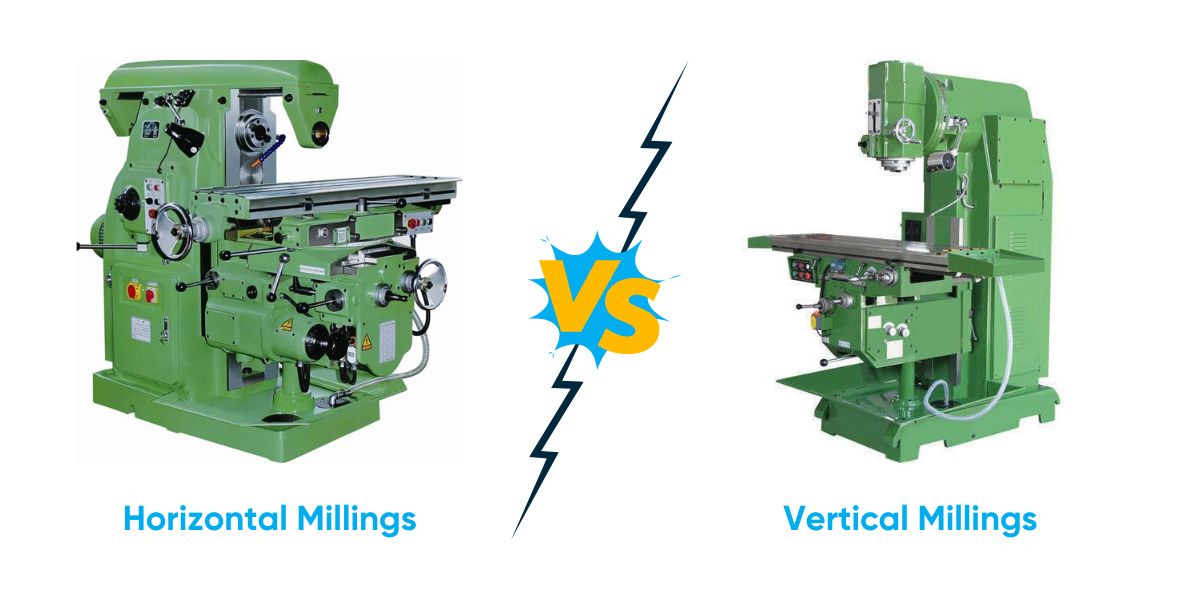
Source: bhansalitechno.com
Comparing Horizontal and Vertical Milling
Horizontal milling and vertical milling are two common ways to shape materials. In horizontal milling, the cutting tool is mounted on a horizontal spindle, which is better for heavier, more aggressive cutting. Vertical milling uses a vertical spindle, which is better for detailed and precise work. Horizontal milling is best for removing large amounts of material, while vertical milling is better for working on flat surfaces and smaller, detailed cuts.
Pros and Cons of Each Type
Horizontal Milling:
Pros: Better for side cutting, can handle heavy cuts, good for batch production, and great for deep slots and grooves.
Cons: Usually bigger and more expensive, needs more space, and can be harder to set up compared to vertical milling.
Vertical Milling:
Pros: Easier to set up and use, good for detailed work, takes up less space, and usually costs less than horizontal milling machines.
Cons: Not as good for heavy material removal, and can't handle deep slots or tough materials as well as horizontal milling.
Choosing the Right Milling Technique
How to Decide Between Horizontal and Vertical Milling
When deciding between horizontal and vertical milling, think about the type of material, the size and shape of the workpiece, and the type of cuts you need. If the project needs heavy material removal, deep cuts, or high-volume production, horizontal milling is probably the better choice. If the project needs precise work on flat surfaces or detailed cuts, vertical milling might be more suitable.
Projects That Are Best for Horizontal Milling
Horizontal milling is great for projects that need heavy cutting and high-volume production. It is often used for deep slots, grooves, or side cuts, as well as for harder or thicker materials. Industries like automotive, aerospace, and heavy equipment manufacturing benefit from the power and efficiency of horizontal milling machines.
Best Practices for Horizontal Milling
Tips to Get the Best Results
Choose the Right Tool: Use the correct cutter for the material and the type of cut. This helps improve efficiency and extends the tool's life.
Set Proper Feed Rate and Speed: Adjust the feed rate and spindle speed based on the material and cutter. Using the right settings will improve the quality of the cuts and reduce machine wear.
Secure the Workpiece Properly: Make sure the workpiece is firmly held in place on the worktable. Proper clamping helps avoid mistakes and keeps things safe.
Regular Maintenance: Keep the machine in good shape by doing regular maintenance checks. Lubricate moving parts and replace worn components to keep it running smoothly.
Use Coolant: Apply coolant to the cutting area to reduce heat and friction. This helps improve the surface finish and prevents damage to both the cutter and the workpiece.
Safety Tips
Wear Protective Gear: Always wear safety goggles, gloves, and protective clothing when using a milling machine to protect yourself from flying debris.
Keep Hands Away: Never put your hands near the spinning cutter or moving parts. Use the right tools for adjustments or removing chips.
Use Machine Guards: Make sure all guards are in place before using the machine. Guards help prevent accidental contact with moving parts.
Know the Emergency Stop: Be familiar with where the emergency stop button is. If anything goes wrong, use it to quickly stop the machine.
Manage Chips Safely: Use a brush or vacuum to remove chips from the work area. Avoid using your hands to prevent injuries from sharp edges.
Conclusion
Horizontal milling is a powerful way to shape materials, especially for heavy-duty jobs and removing large amounts of material. With its horizontal spindle, it works well for industries like automotive, aerospace, and heavy equipment manufacturing. Horizontal milling is perfect for projects that need deep cuts, grooves, and batch production, making it an important tool in many manufacturing processes.
If your project needs heavy material removal, deep cuts, or high-volume production, horizontal milling might be the right choice. It offers power, precision, and efficiency that can make a big difference in manufacturing projects.
Get Precision Milling Solutions Today with Unionfab
At Unionfab, we offer high-quality horizontal milling services to help you achieve precision and efficiency in your projects. Whether you need expert consultation or ready-to-use CNC products, our experienced team is here to assist.
Contact us today to explore how our advanced milling capabilities can meet your specific needs and drive your project success.
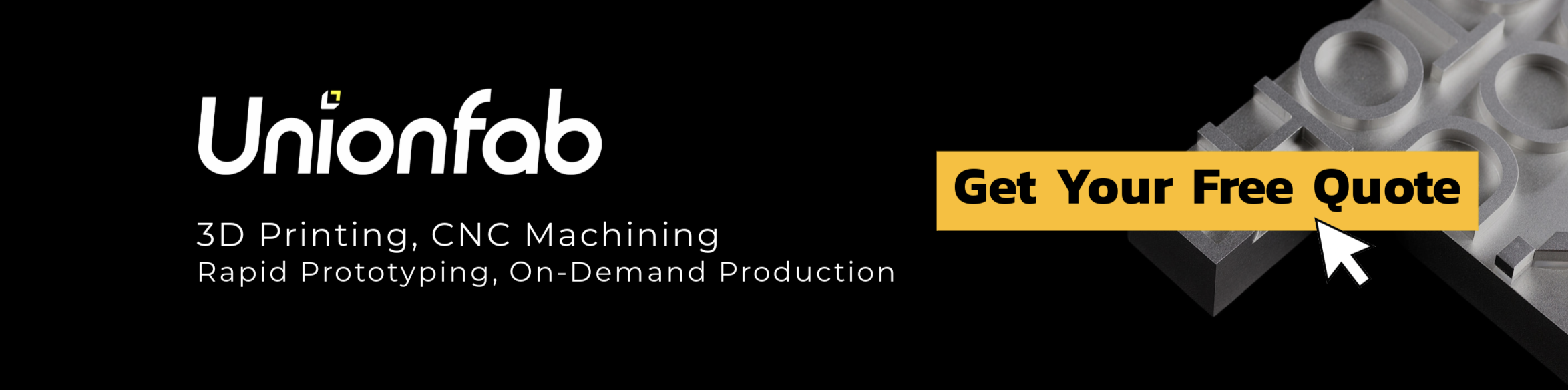