Hot Runner Injection Molding: Efficiency & Quality Benefits
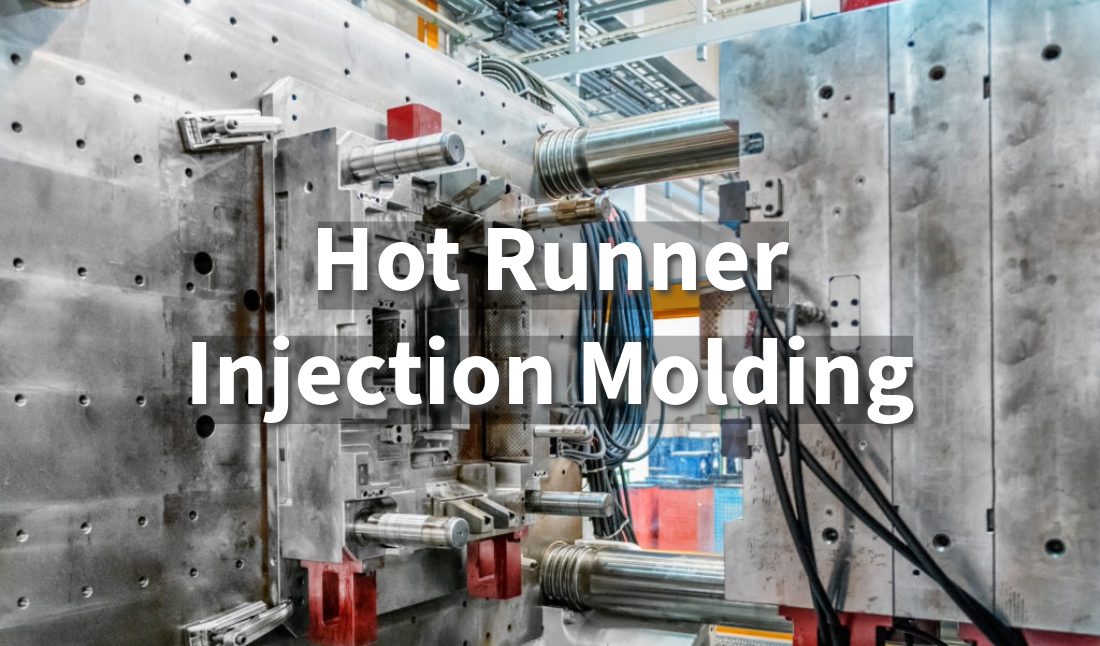
A complete guide to hot runner injection molding: discover its benefits, applications, and why it’s the top choice for high-quality, high-volume production.
Introduction to Hot Runner Injection Molding
Brief Overview of Injection Molding
Injection molding is a process used to make many identical parts by injecting melted material into a mold. It is commonly used to make plastic parts. In this process, plastic pellets are melted, pushed into a mold, and then cooled until they harden into the shape of the mold.
Hot Runner Systems vs. Cold Runner Systems
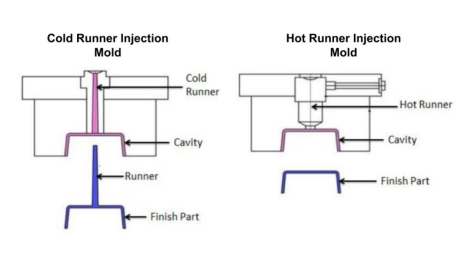
Source: polyshot.com
In injection molding, there are two main types of runner systems: hot runner systems and cold runner systems. A "runner" is the pathway that directs the melted plastic into the mold. The main difference between hot and cold runner systems is how they handle the flow of plastic.
Cold Runner Systems
In a cold runner system, the plastic moves through channels that are not heated. This means that after the part is formed, the leftover plastic in the channels also cools and hardens. This leftover plastic can be recycled, but it requires extra steps like grinding, which can lead to more waste.
Hot Runner Systems
A hot runner system, on the other hand, uses heated channels to keep the plastic melted until it reaches the mold. Because the plastic stays melted, there is no leftover solid plastic in the runner, which helps reduce waste. Hot runner systems are more complicated and expensive to set up, but they offer benefits like faster production, less waste, and better quality parts.
Hot runner systems are known for being efficient and producing high-quality parts, which makes them a popular choice for large production runs.
How Hot Runner Injection Molding Works
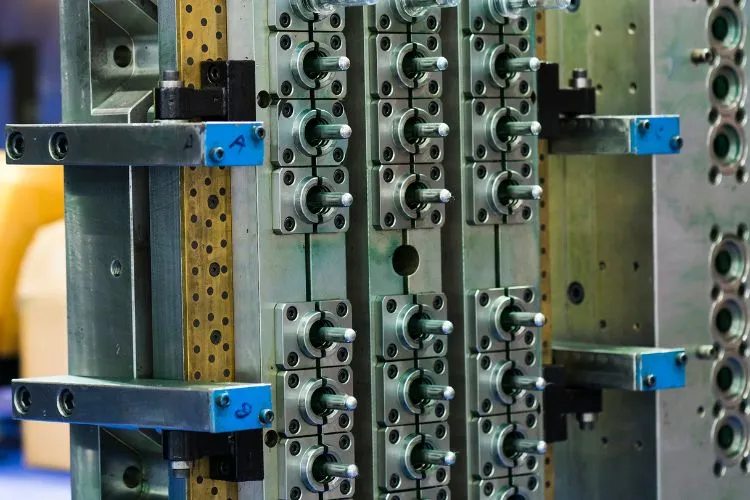
Source: kemalmfg.com
Key Components
Hot runner systems have a few key parts, including the manifold and nozzles. The manifold distributes the melted plastic to different parts of the mold, while the nozzles deliver the plastic into the mold cavities. These parts are kept hot to make sure the plastic stays melted.
How Plastic Flows in a Hot Runner System
In a hot runner system, the plastic is kept in a liquid state as it moves through the manifold and nozzles. The melted plastic flows directly into the mold cavities without cooling in the runner, which makes the molding process more consistent and efficient.
Role of Temperature Control
Temperature control is very important in hot runner systems. Keeping the right temperature ensures that the plastic stays melted and flows smoothly into the mold. Good temperature control also helps prevent problems like plastic breaking down or the parts having poor quality.
Advantages of Hot Runner Injection Molding
Reduced Cycle Time
Hot runner systems help make the injection molding process faster. Since the plastic stays melted, there is no need to wait for it to cool and be removed from the runner, which speeds up production.
Improved Part Consistency and Quality
Hot runner systems give better control over the flow of melted plastic, which results in more consistent parts with fewer defects. This helps make higher-quality products.
Lower Material Waste and Environmental Benefits
Since there is no leftover solid plastic in the runner, hot runner systems create less waste. This saves money and also has environmental benefits by reducing plastic waste.
Enhanced Production Speed for High-Volume Runs
Hot runner systems are great for large production runs because they allow for faster production and more efficient use of materials. This makes them a popular choice for manufacturers who need to make a lot of parts quickly.
Applications of Hot Runner Systems
Industries and Products Where Hot Runners Are Preferred
Hot runner systems are used in industries that need to produce a large number of parts with consistent quality, like the automotive, packaging, and consumer goods industries. Products like car parts, plastic bottles, and household items are often made using hot runner injection molding because it is fast and precise.
Types of Plastic Materials Used
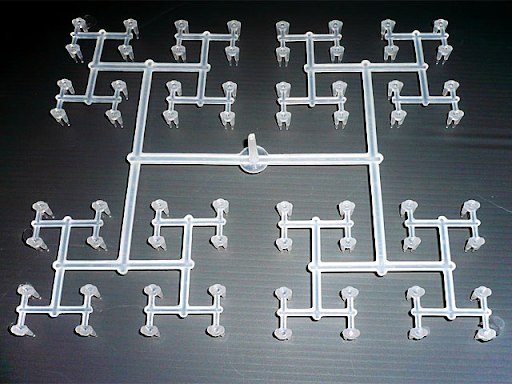
Source: rexplastics.com
Hot runner systems can work with many types of plastic, including common thermoplastics like polypropylene (PP), polyethylene (PE), polystyrene (PS), and acrylonitrile butadiene styrene (ABS). These plastics work well in hot runner systems because they can stay melted without breaking down, which helps make high-quality products.
Choosing Between Hot Runner and Cold Runner Systems
Cost Considerations
Hot runner systems usually cost more to set up than cold runner systems because they are more complex and need precise temperature control. However, the reduction in waste and faster production times can lead to savings in the long run, especially for large production runs.
Complexity and Maintenance Differences
Hot runner systems are more complex and need regular maintenance to keep them working well. The need for precise temperature control and extra parts makes maintenance harder compared to cold runner systems, which are simpler and easier to maintain.
When to Use Each System Based on Project Needs
Hot runner systems are best for large production runs where efficiency, less waste, and high quality are important. Cold runner systems are better for smaller production runs, simple parts, or projects where keeping setup costs low is important.
Challenges and Limitations
Potential Issues like Color Changes and Maintenance Needs
One challenge with hot runner systems is changing colors. Since the plastic stays melted in the hot runner channels, changing colors can lead to contamination if not done correctly. Hot runner systems also need regular maintenance to make sure all parts are working well and to avoid issues like leaks or clogs.
Solutions and Maintenance Best Practices
To avoid color contamination, it is important to thoroughly clean the system when switching colors. Regular maintenance, like checking parts such as the manifold and nozzles, can help prevent common issues like wear, clogs, or leaks. Keeping temperature controls properly calibrated is also key to making sure the system works well and the plastic does not degrade.
Conclusion
Hot runner injection molding has many advantages, including faster production, more consistent and higher quality parts, less material waste, and faster production speeds for large runs. These benefits make hot runner systems a great choice for manufacturers looking to be more efficient and reduce waste.
Optimize Your Production with Unionfab
Ready to enhance efficiency and quality in your injection molding projects? Unionfab offers cutting-edge hot runner injection molding solutions tailored to your manufacturing needs.
Get in touch with our experts today to see how we can optimize your production for high-volume, consistent output. Contact Unionfab now to discuss your project.
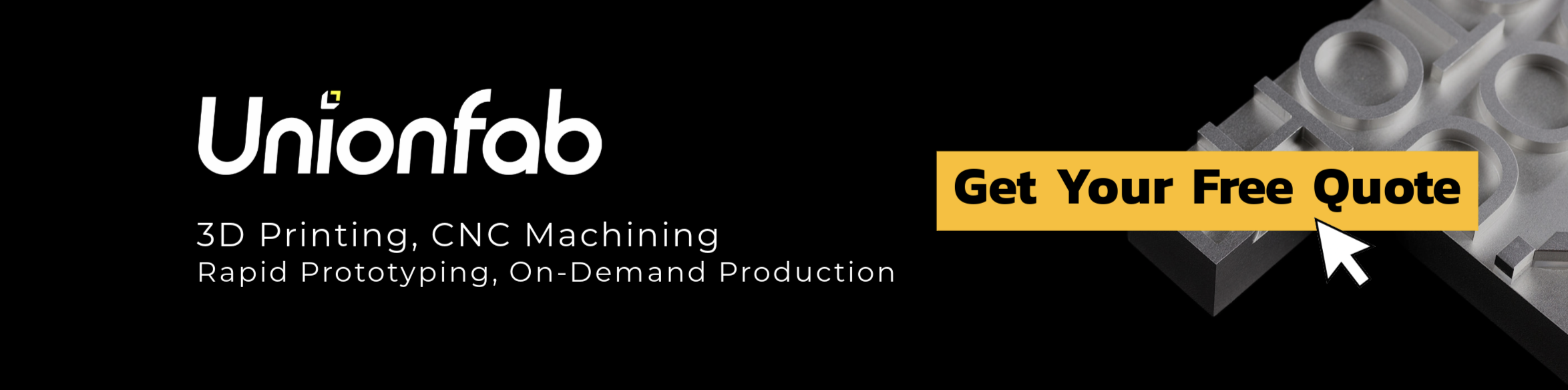