3D Printing Replacement Parts: A Cost-Effective Solution [+ Real Cases]
![3D Printed Replacement Parts A Cost-Effective Solution [+ Real Cases]](https://ufc-dtc-cms.oss-accelerate.aliyuncs.com/blog/20250103/164734_frgr33epx.png)
Discover how 3D printed replacement parts are changing repairs. Faster, cost-effective, and customizable solutions for all your maintenance needs.
Introduction
From prototyping to mass production, 3D printing technology is reshaping how industries approach production, repair, and customization.
In this blog, we'll explore how 3D printed replacement parts are becoming a game-changer for small manufacturers and and repair professionals, offering advantages like speed, cost-efficiency, and customization.
At Unionfab, we are committed to providing these innovative solutions to help you streamline your processes, saving both time and money.
Why Choose 3D Printed Replacement Parts?
The Problem
Challenges in traditional manufacturing: cost, lead time, availability, downtime.
When a part breaks, the typical solution is to order a replacement from a manufacturer or supplier. However, this process can be time-consuming, expensive, and in some cases, the part may no longer be available.
For hobbyists, DIY enthusiasts, and small-scale manufacturers, waiting for replacement parts to arrive can lead to costly delays and extended downtime.
The Solution
3D printing offers a perfect solution to these common challenges by enabling users to print their own replacement parts on demand.
Speed: Transitioning from design to delivery in just a few days minimizes downtime and speeds up problem resolution.
Flexibility: Supports intricate designs and customization to optimize part performance for specific applications.
Material Variety: Offers a wide range of engineering plastics, metals, and other materials to meet diverse functional requirements.
No Minimum Order Quantity: Ideal for low-volume needs, eliminating the burden of excess inventory and associated storage costs.
Explore how our 3D printing services can help you overcome these challenges—contact us today for a consultation.
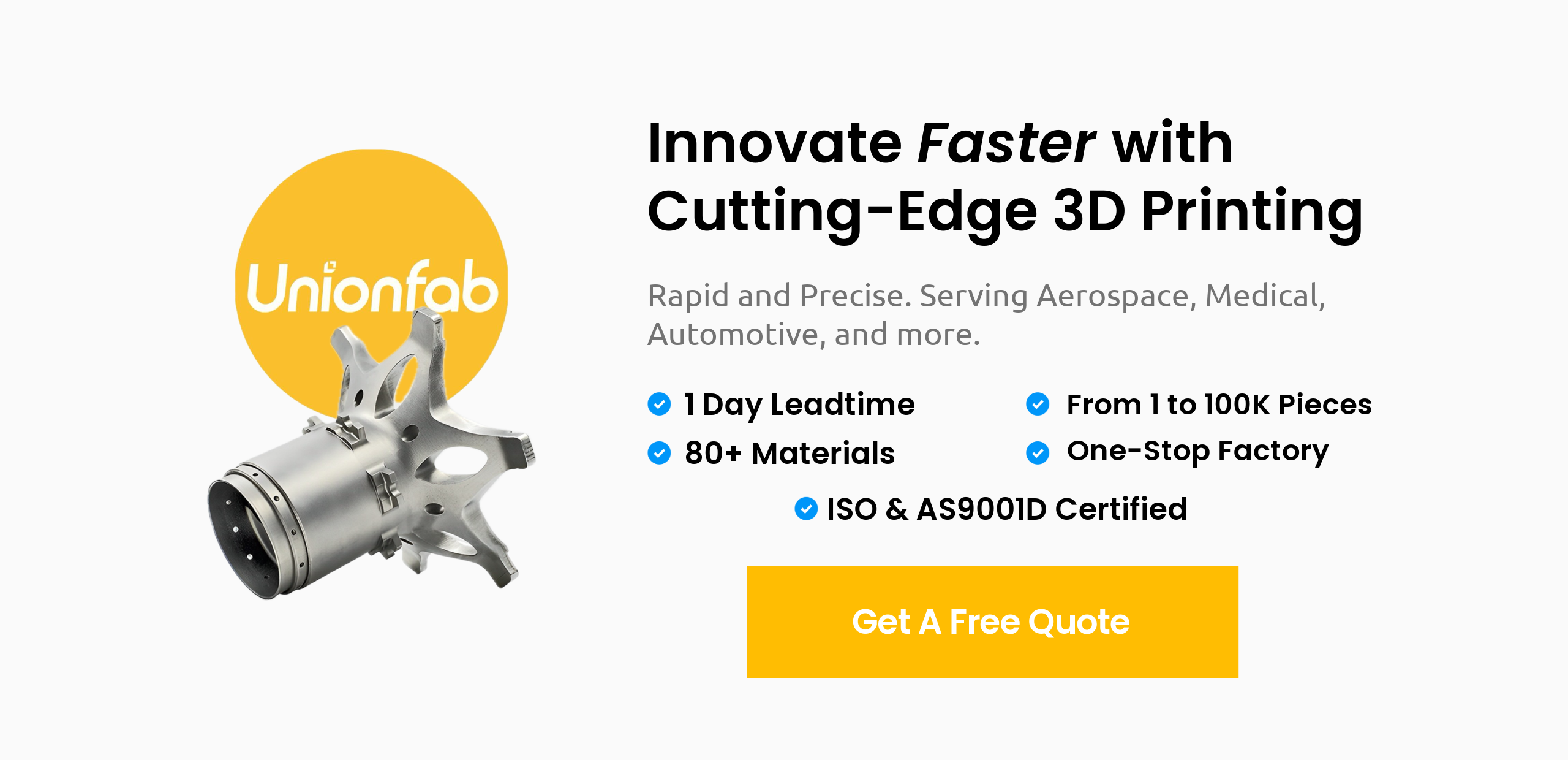
3D Printing vs. Traditional Manufacturing
For replacement part production, 3D printing offers distinct benefits, particularly in the context of low-volume, customized, and complex part requirements:
Criteria | 3D Printing | Traditional Manufacturing |
---|---|---|
Cost | Lower for small batches, no tooling costs | High setup costs (tooling, molds, fixtures) |
Time | Faster production times for small batches | Longer setup time, especially for low-volume production |
Flexibility | Highly flexible for complex geometries, design iterations | Limited flexibility, requires redesign for part modifications |
Suitability for Customization | Excellent for customized or unique designs | More cost-effective for standard designs and high-volume parts |
Material Variety | Wide range of materials, including specialized and composite materials | Limited to traditional materials like metals and plastics |
Production Speed | Rapid prototyping, quick turnaround for small quantities | Slower for small batches due to setup and production processes |
Tooling Requirements | No need for molds or tooling | Significant tooling investment required (molds, dies) |
Use Cases: How We Help Clients Overcome Challenges
Case Study 1: Custom Turbocharger Prototype
Challenge:
Customization is key in the automotive industry, especially for specialty or performance-focused applications. An automotive client required a highly precise turbocharger replacement part for a car engine. Due to the geometries (featuring intricate hollow, curved pipes) and time constraints, traditional manufacturing methods for prototyping were impractical.
The goal was to quickly create a prototype that could also serve as the master model for molding the final part.
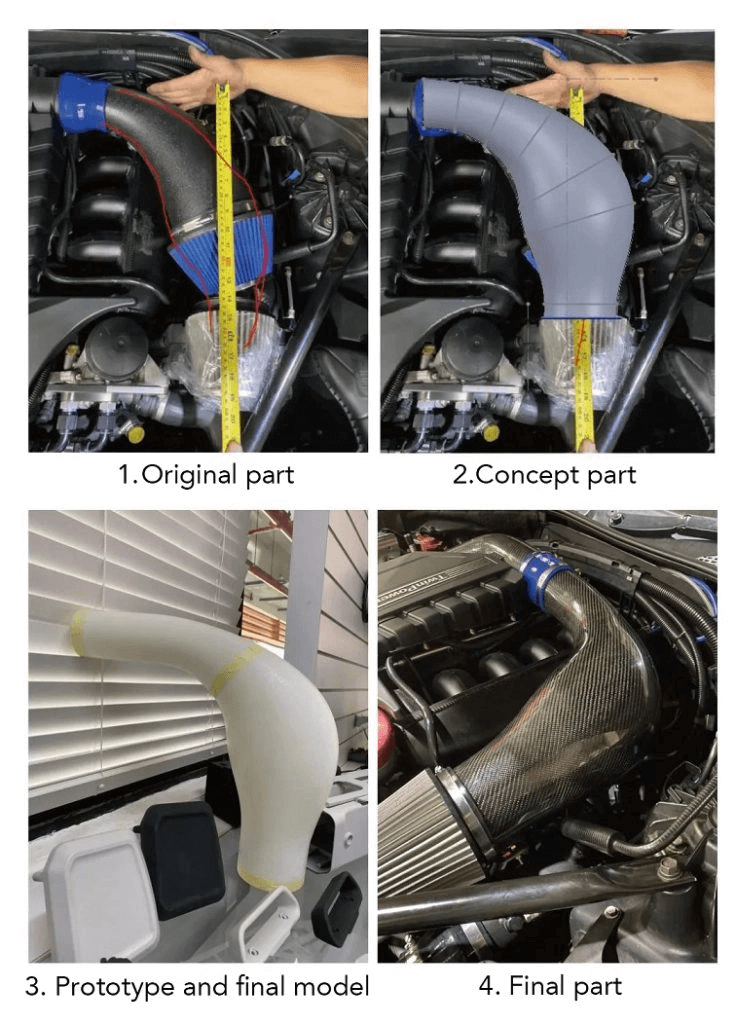
Source: Unionfab
Using SLA (Stereolithography) 3D printing, we produced a detailed turbocharger prototype that met the client's stringent requirements. The SLA process enabled the creation of a smooth, dimensionally accurate model suitable for subsequent molding of carbon fiber final parts.
Within days, the client received a high-quality turbocharger prototype that facilitated the molding process. This streamlined approach cut weeks from the production timeline and significantly reduced costs
Case Study 2: Small-Batch Nylon Parts
Challenge:
A manufacturing company needed a small batch of replacement parts for an assembly line that had broken down. Downtime can be costly in industries relying on continuous operation.
Our Solution:
Using our advanced MJF (Multi Jet Fusion) 3D printing technology, we provide higher productivity and lower cost-per-part, making it the ideal choice for producing small-batch, high-quality industrial components. MJF allows us to quickly produce replacement parts with exceptional mechanical properties, while maintaining cost-effectiveness—a perfect solution for industries requiring low-volume production and fast prototyping.
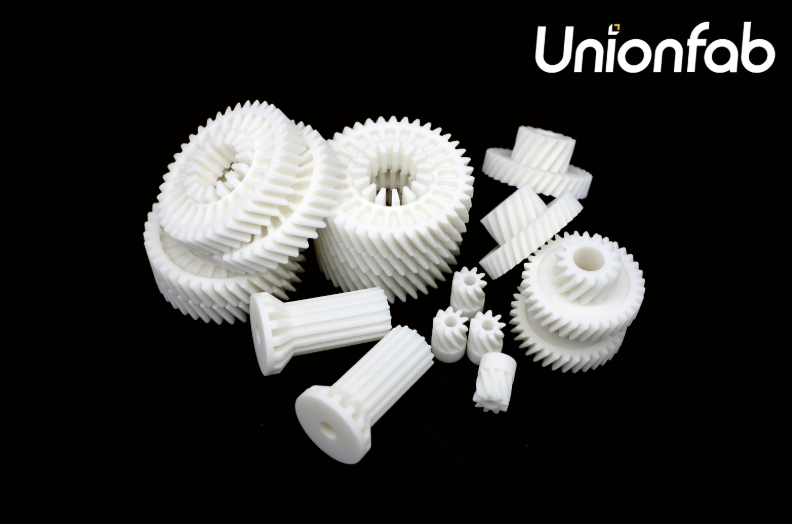
Source: Unionfab
To further enhance the final part quality, we employ PostPro3D chemical vapor smoothing technology, which significantly improves the surface finish and mechanical properties of the printed parts.
Result:
This combination of MJF and PostPro3D enables us to deliver smooth, durable, and high-performance components that meet the stringent demands of the industrial client.
Case Study 2: Durable Stainless Steel Automotive Parts
Challenge:
One of our clients in the automotive sector needed a high-strength, corrosion-resistant component for their vehicle manufacturing process. Traditional manufacturing methods were too costly and time-consuming for the small quantity required.
Our Solution:
The part required exceptional hardness and toughness, which made Stainless Steel 17-4 PH an ideal choice.
A key example of the power of 3D printing in automotive applications involves Stainless Steel 17-4 PH—a highly durable material ideal for demanding industrial applications, including automotive parts.
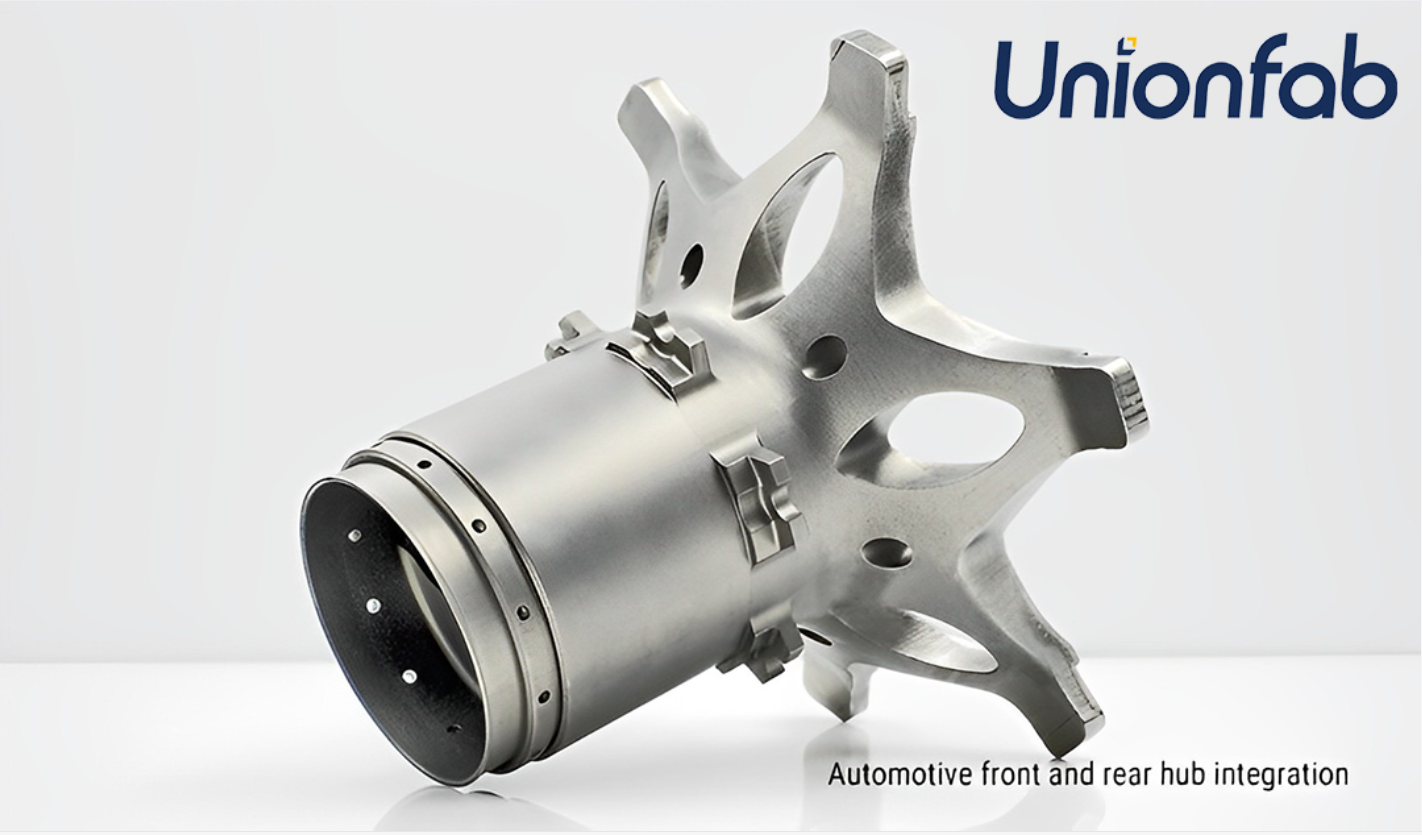
Source: Unionfab
Using SLM (Selective Laser Melting) 3D printing technology, we were able to produce the custom part quickly and with superior precision.
Result:
This technology allowed us to deliver a fully functional, high-performance end-use replacement part that met the client's exact specifications—ensuring it performed optimally in its application.
At Unionfab, we take pride in delivering exceptional results to our clients, with an impressive 99.95% customer satisfaction rate. We strive to meet and exceed expectations by providing fast, reliable, and cost-effective replacement solutions for our customers.
Find out more: https://www.unionfab.com/why-unionfab
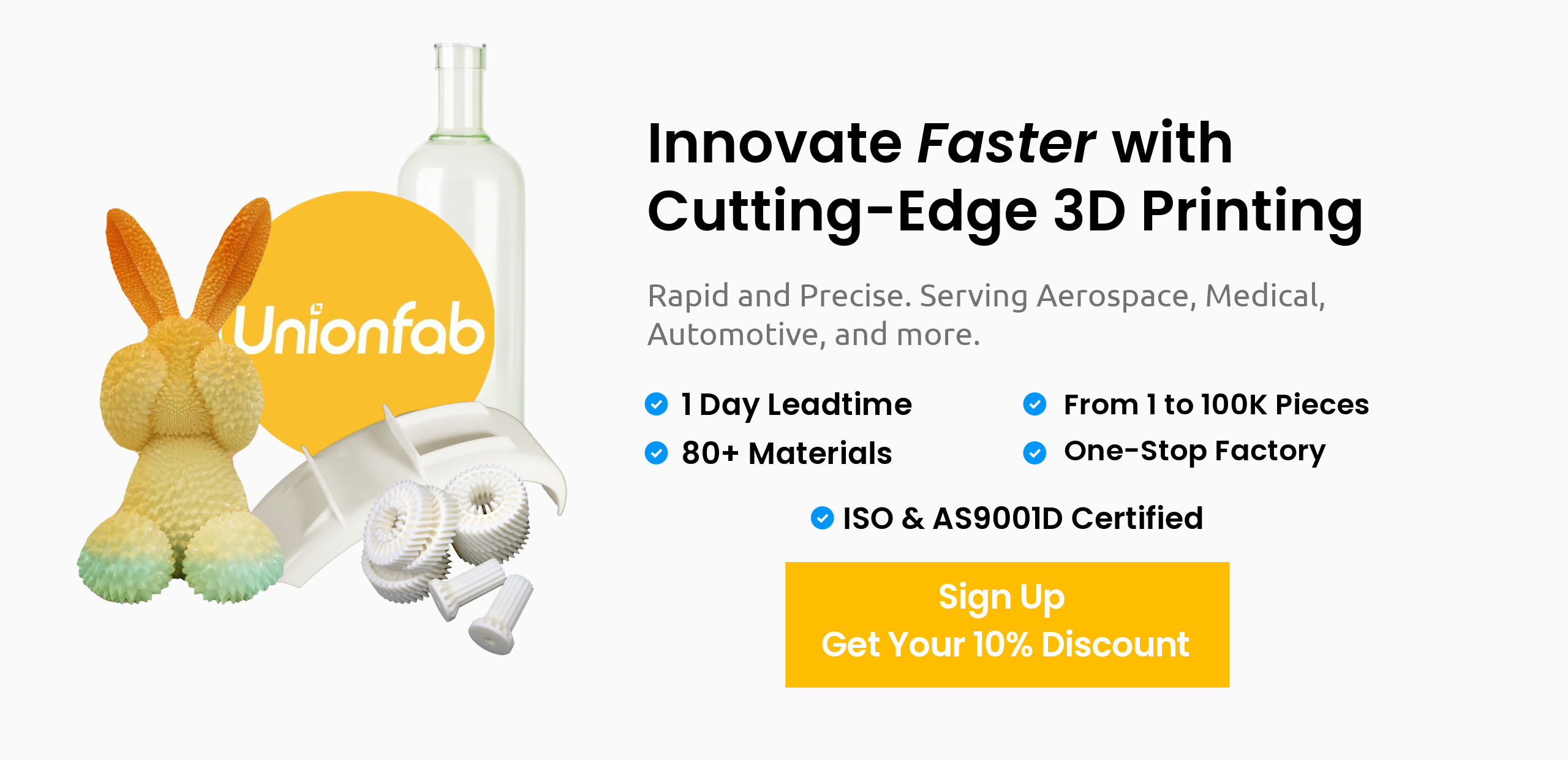
Conclusion
3D printed replacement parts are revolutionizing industries by offering on-demand, customizable, and cost-effective solutions.
Whether you're a DIY enthusiast, a small manufacturer, or a repair professional, 3D printing provides unparalleled flexibility and speed in producing replacement parts that meet your exact needs.
If you're looking to replace parts quickly, efficiently, and affordably, 3D printing is the solution you need.
Get Started with 3D Printed Replacement Parts
At Unionfab, we are here to help you harness the power of 3D printing for all your replacement part needs. Whether you're designing custom parts for a new project or need an immediate solution for a repair, we offer a range of services, including:
On-Demand Printing: Quickly produce parts to fit your exact specifications.
Consultation: Reach out to our experts to learn how 3D printing can improve your business.
Let us help you innovate and reduce downtime with fast, reliable, and cost-effective solutions!
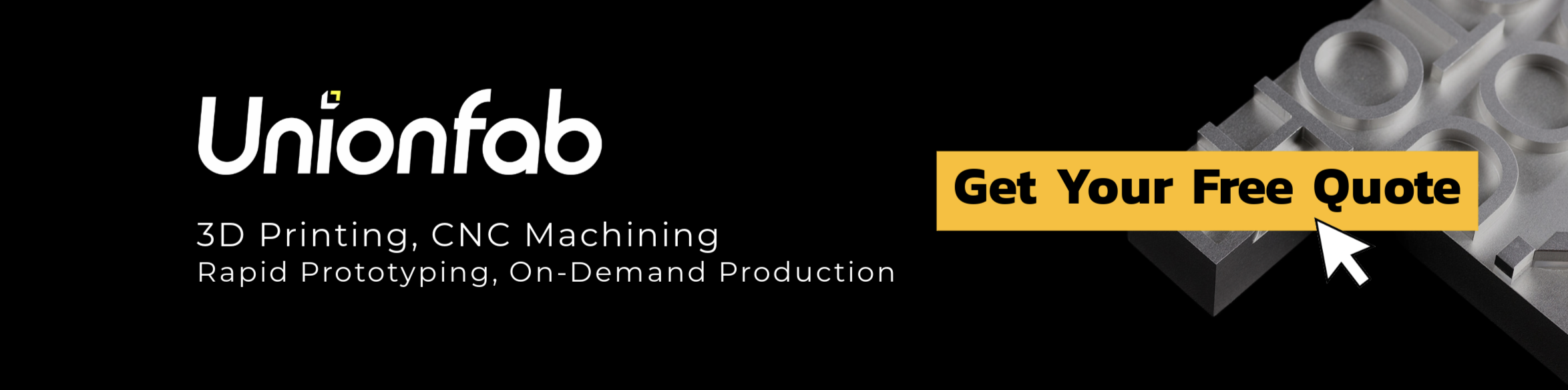