Guide to Nylon 3D Printing [Cost Calculator+Success Story]
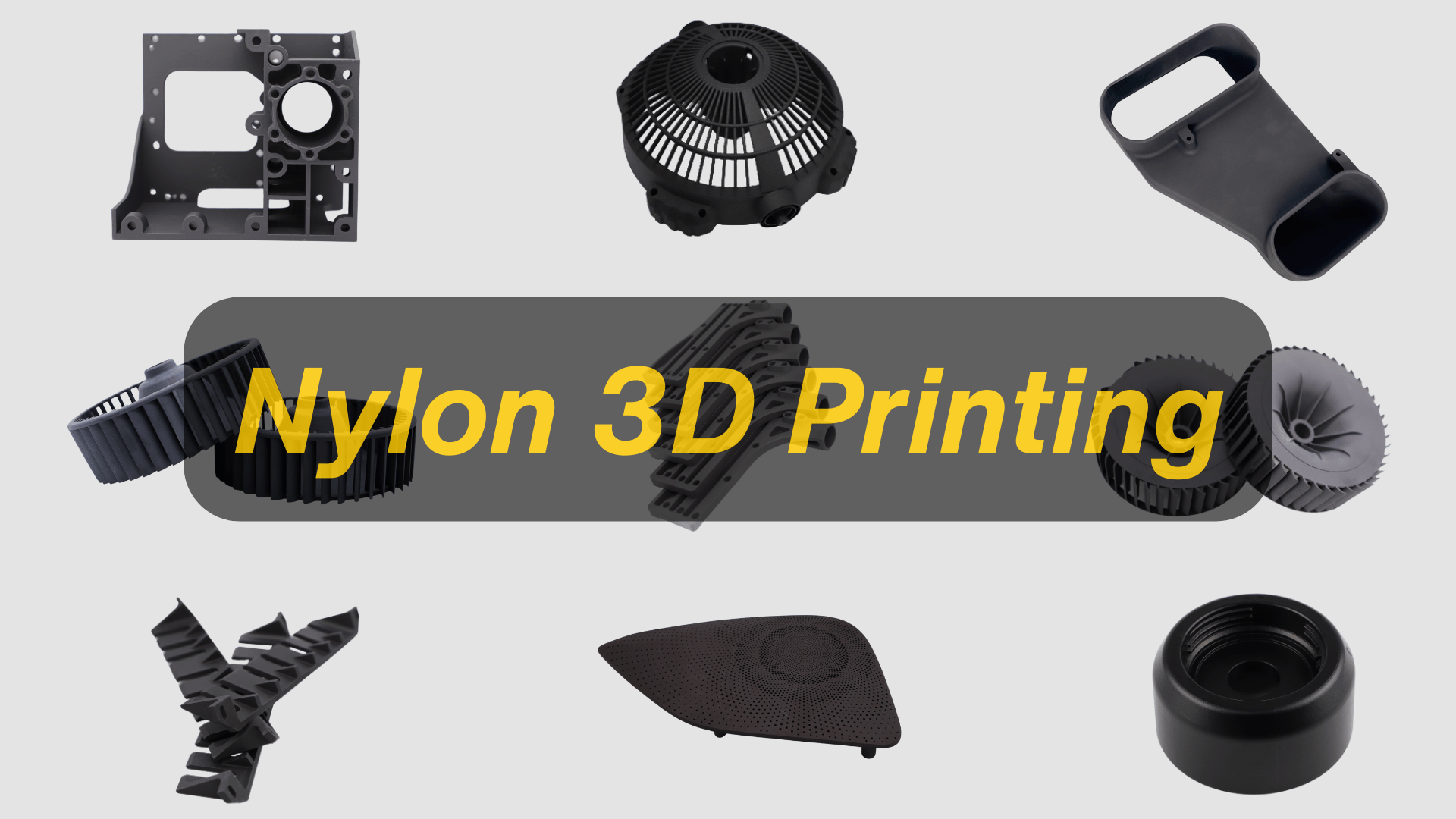
Pin down what is nylon 3d printing and learn from Unionfab’s success story to better your own printing.
Introduction
Nylon, or Polyamide (PA) is the go-to material for functional 3D-printed parts, offering strength, flexibility, and unmatched wear resistance.
From automotive components to medical devices, it thrives in demanding environments where plastics like PLA or PETG fall short. But here’s the catch: achieving high-quality nylon parts requires industrial-grade equipment and expertise. So, how do you get flawless nylon parts without buying a printer?
The answer: Professional outsourcing.
Nylon vs. ABS vs. PLA vs. TPU vs. PETG
The table below presents how Nylon outperforms other common 3D printing materials and why Nylon is the only option for parts that need to survive real-world stress, heat, or friction.
Property | Nylon | ABS | PLA | TPU | PETG |
---|---|---|---|---|---|
Wear Resistance | ⭐⭐⭐⭐⭐ | ⭐⭐ | ⭐ | ⭐⭐⭐ | ⭐⭐ |
Heat Resistance | ⭐⭐⭐⭐ | ⭐⭐ | ⭐ | ⭐ | ⭐⭐ |
Impact Strength | ⭐⭐⭐⭐ | ⭐⭐⭐ | ⭐ | ⭐⭐ | ⭐⭐ |
Chemical Resistance | ⭐⭐⭐⭐ | ⭐⭐ | ⭐ | ⭐⭐ | ⭐⭐ |
Structural Strength | ⭐⭐⭐⭐⭐ | ⭐⭐⭐ | ⭐⭐ | ⭐ | ⭐⭐⭐ |
Flexibility | ⭐⭐⭐⭐ | ⭐⭐ | ⭐ | ⭐⭐⭐⭐⭐ | ⭐⭐ |
Best For | Functional parts | Basic prototypes | Decorative models | Soft, stretchable parts | Transparent/outdoor parts |
Weakness | Requires drying, higher cost | Poor UV/weather resistance | Low durability, brittle | Low structural strength | Poor wear/heat resistance |
Why Nylon Wins?
Unbeatable Combo: Only nylon balances strength, flexibility, and heat/chemical resistance.
Real-World Edge: Survives harsh conditions (e.g., engine heat, factory friction) where ABS/PLA fail.
Design Freedom: Print snap-fit joints, thin walls(>0.8mm), or load-bearing parts without breakage risks.
How to Select the Right Material: Nylon 6 vs. 66 vs. 11 vs. 12 vs. Glass-filled vs. Carbon-filled
The common nylon materials used in 3d printing include pure Nylon materials (Nylon 6, Nylon 66, Nylon 11 & Nylon 12) and composite Nylon materials ( Glass-filled Nylon & Carbon-filled Nylon).
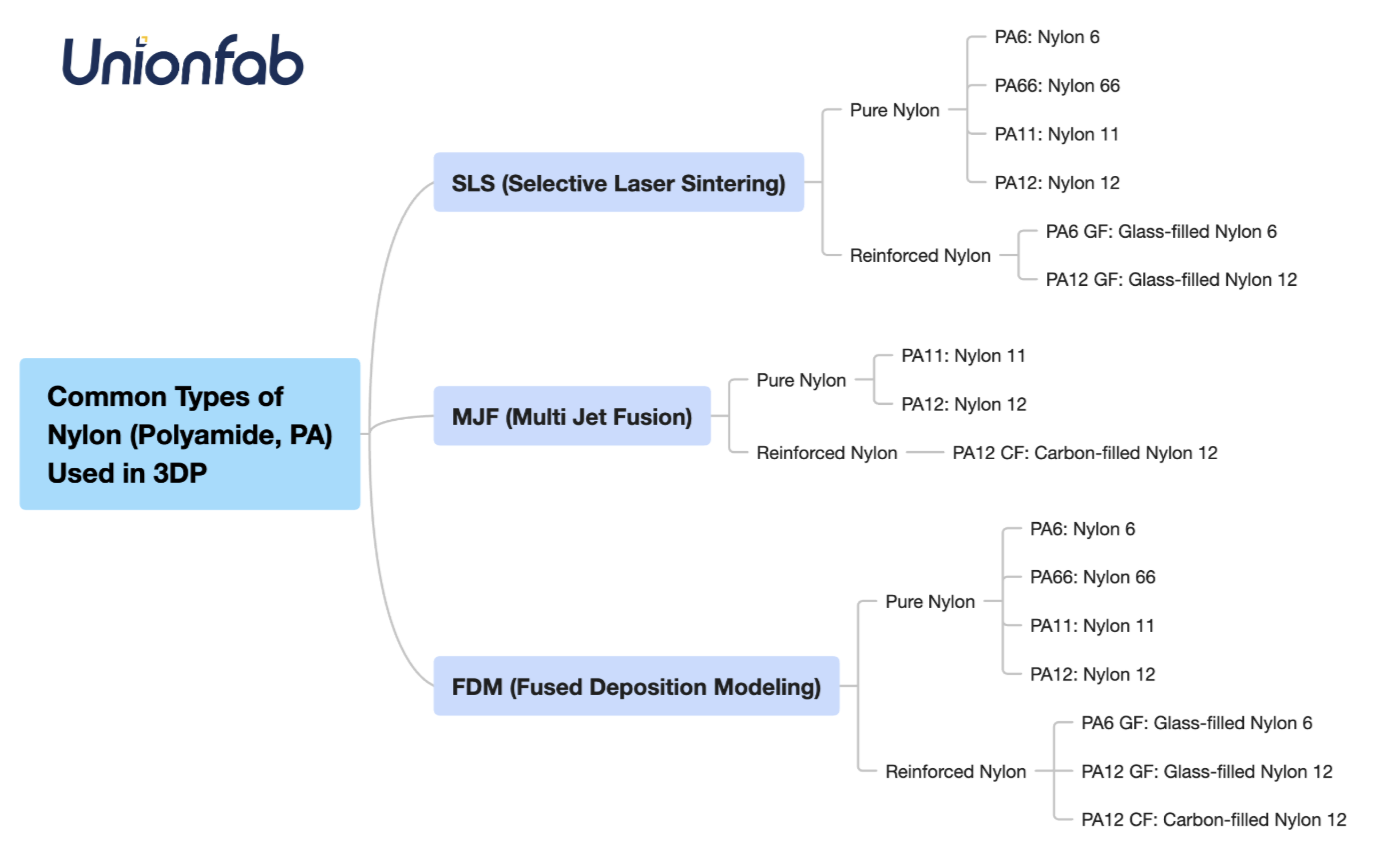
Nylon 6, Nylon 66, Nylon 11 & Nylon 12
Pure Nylon are made from different monomers through different polymerization processes and therefore named after the number of carbon atoms the monomer contains.
For example, Nylon 6, or PA 6, is made from a 6-carbon atom monomer, caprolactam. Their different chemical composition directly impact their properties, applications, and production costs.
Why Add Glass or Carbon to Nylon?
Glass fibers or beads are added to nylon to increase its strength, rigidity, and dimensional stability. Glass fibers are inexpensive and provide a good balance between performance and cost.
Carbon fibers are added to nylon to improve strength, stiffness, and thermal conductivity. Carbon fibers offer even higher performance than glass fibers, but at a higher cost.
Comparison Table
Here we have compared the 6 common Nylon materials used in 3d printing.
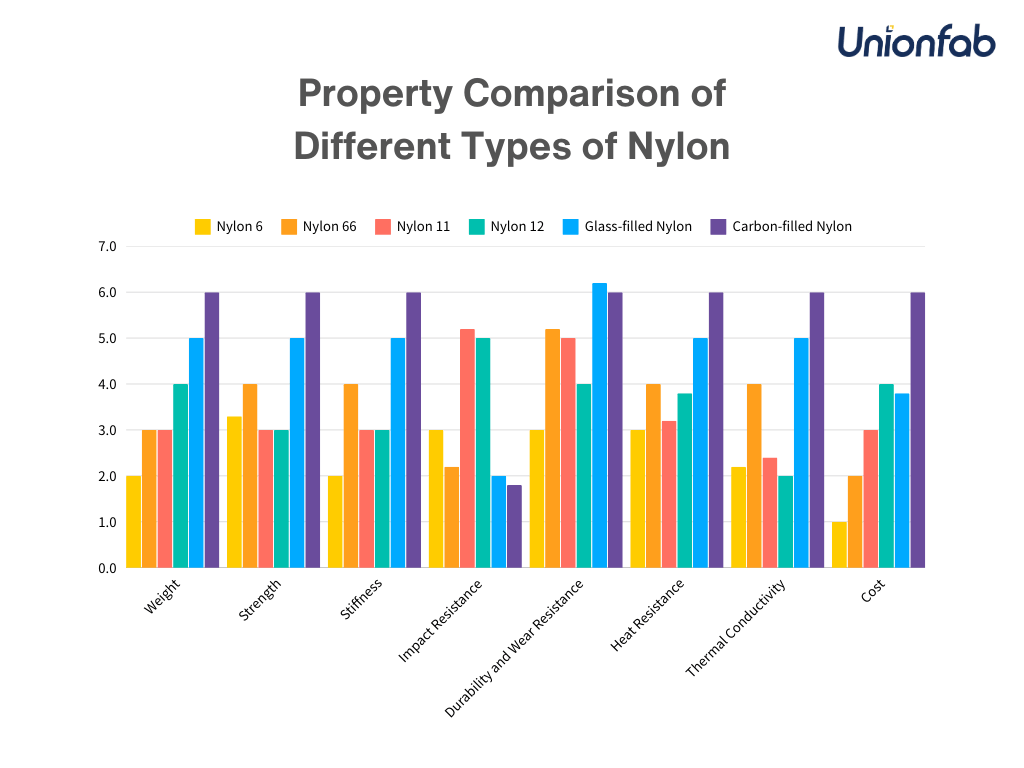
Property | Nylon 6 | Nylon 66 | Nylon 11 | Nylon 12 | Glass-filled Nylon | Carbon-filled Nylon |
---|---|---|---|---|---|---|
Weight | ⭐️⭐️ | ⭐️⭐️⭐️ | ⭐️⭐️⭐️ | ⭐️⭐️⭐️⭐️ | ⭐️⭐️⭐️⭐️⭐️ | ⭐️⭐️⭐️⭐️⭐️⭐️ |
Strength | ⭐️⭐️⭐️ | ⭐️⭐️⭐️⭐️ | ⭐️⭐️⭐️ | ⭐️⭐️⭐️ | Significantly higher | Higher than Glass-filled Nylon (100~180 MPa) |
Stiffness | ⭐️⭐️ | ⭐️⭐️⭐️⭐️ | ⭐️⭐️⭐️ | ⭐️⭐️⭐️ | ⭐️⭐️⭐️⭐️⭐️ | ⭐️⭐️⭐️⭐️⭐️⭐️ |
Impact | ⭐️⭐️⭐️ | ⭐️⭐️ | ⭐️⭐️⭐️⭐️⭐️ | ⭐️⭐️⭐️⭐️⭐️ | ⭐️⭐️ | ⭐️⭐️ |
Durability and Wear Resistance | ⭐️⭐️⭐️ | ⭐️⭐️⭐️⭐️⭐️ | ⭐️⭐️⭐️⭐️⭐️ | ⭐️⭐️⭐️⭐️ | ⭐️⭐️⭐️⭐️⭐️⭐️ | ⭐️⭐️⭐️⭐️⭐️⭐️ |
Heat Resistance | ⭐️⭐️⭐️ | ⭐️⭐️⭐️⭐️ | ⭐️⭐️⭐️ | ⭐️⭐️⭐️⭐️ | ⭐️⭐️⭐️⭐️⭐️ | ⭐️⭐️⭐️⭐️⭐️⭐️ |
Thermal Conductivity | ⭐️⭐️ | ⭐️⭐️⭐️⭐️ | ⭐️⭐️ | ⭐️⭐️ | ⭐️⭐️⭐️⭐️⭐️ | ⭐️⭐️⭐️⭐️⭐️⭐️ |
Cost | $ | $$ | $$$ | $$$$ | $$$$ | $$$$$$ |
| Automotive: Engine components &interior parts | Automotive: Engine covers, gears | Automotive: Pneumatic tubing, flexible pipes | Automotive: | Automotive: Engine parts, transmission housings | Aerospace: Structural components for aircraft, heat shields |
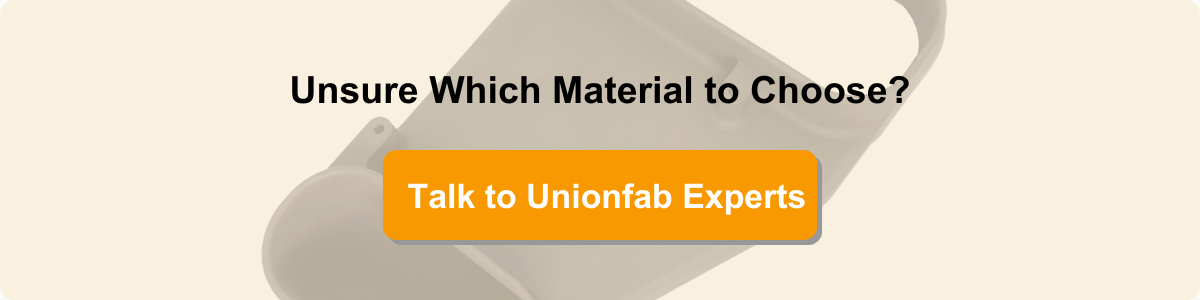
How to Choose the Right Technology: SLS vs. MJF vs. FDM
SLS(Selective Laser Sintering)
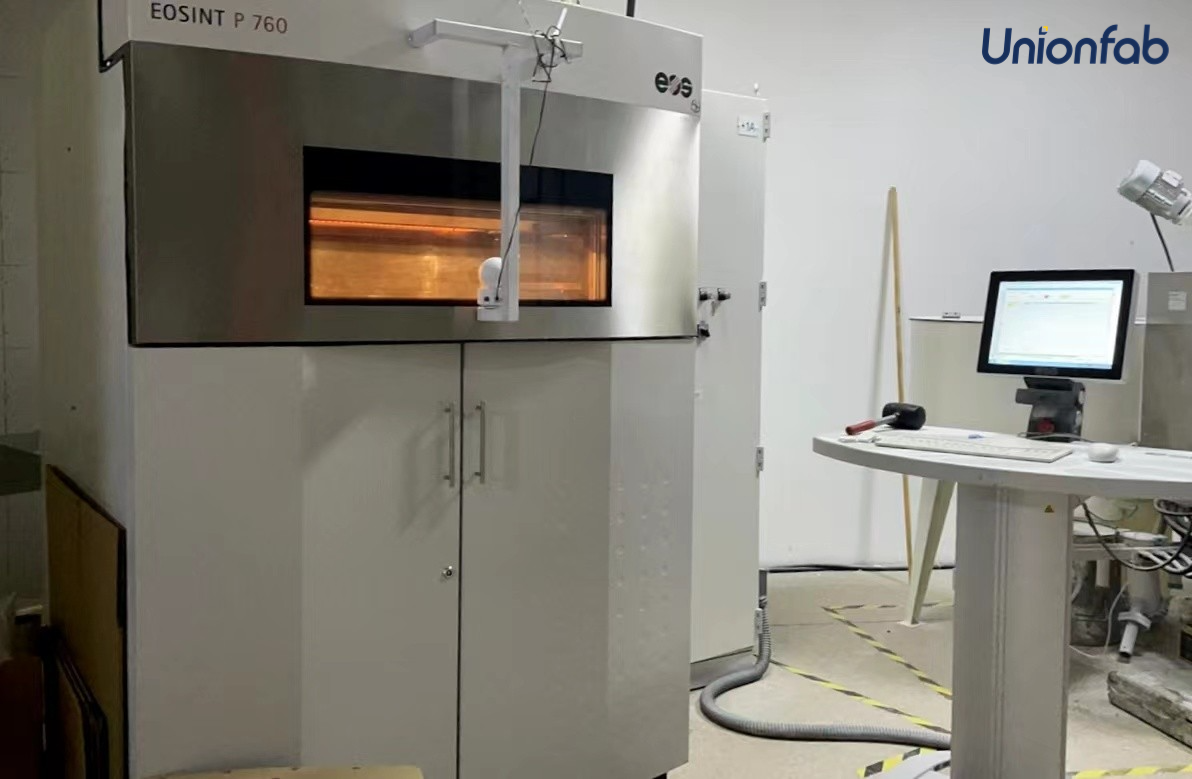
How it works: A laser selectively melts powdered material (plastic or metal) layer by layer.
Result: The material hardens as it cools, building up the object.
MJF(Multi Jet Fusion)
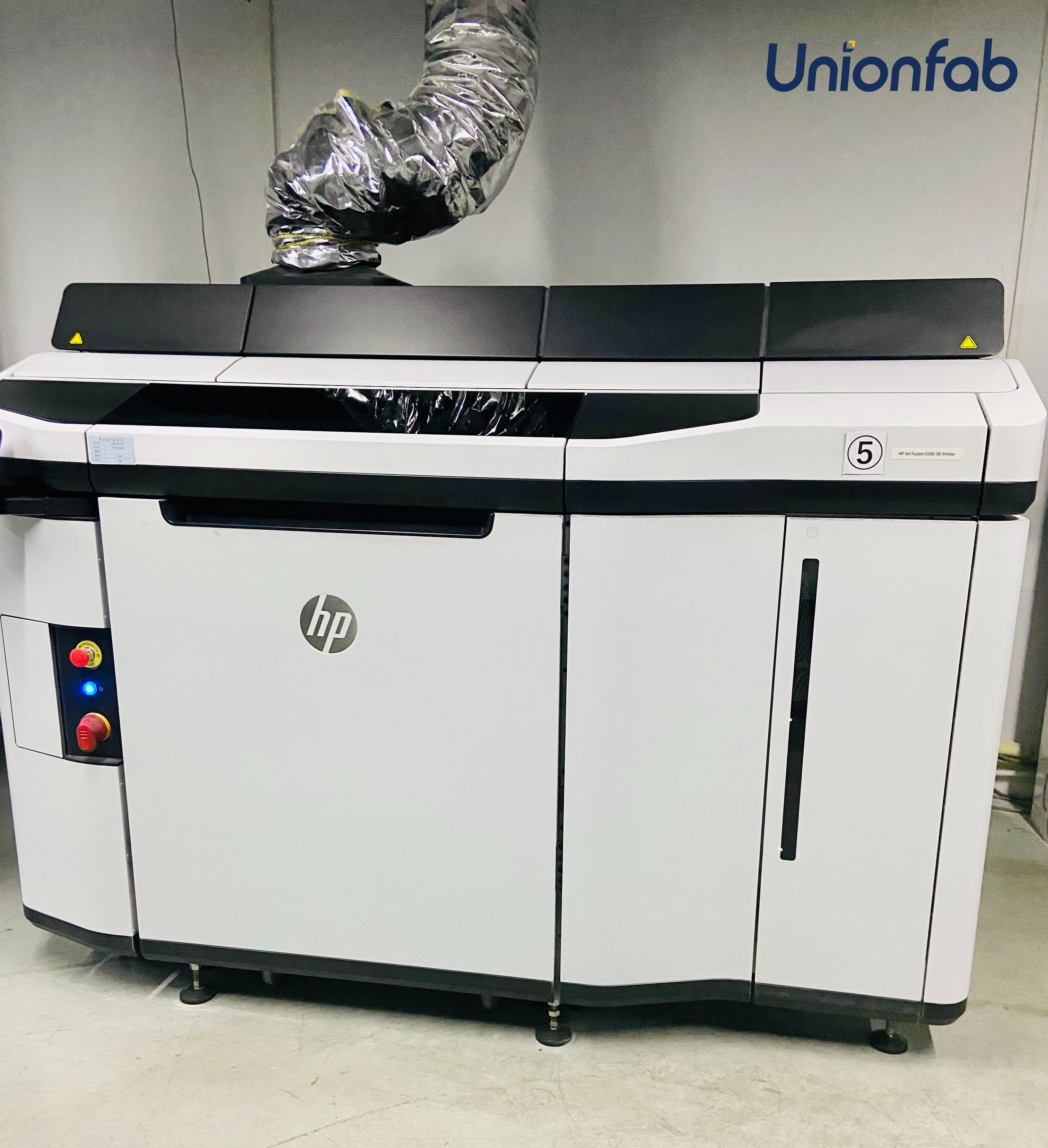
How it works: Inkjet print heads spray a binding agent onto powdered material. Then, infrared light fuses the material together.
Result: Creates strong, detailed parts quickly.
FDM(Fused Deposition Modeling)
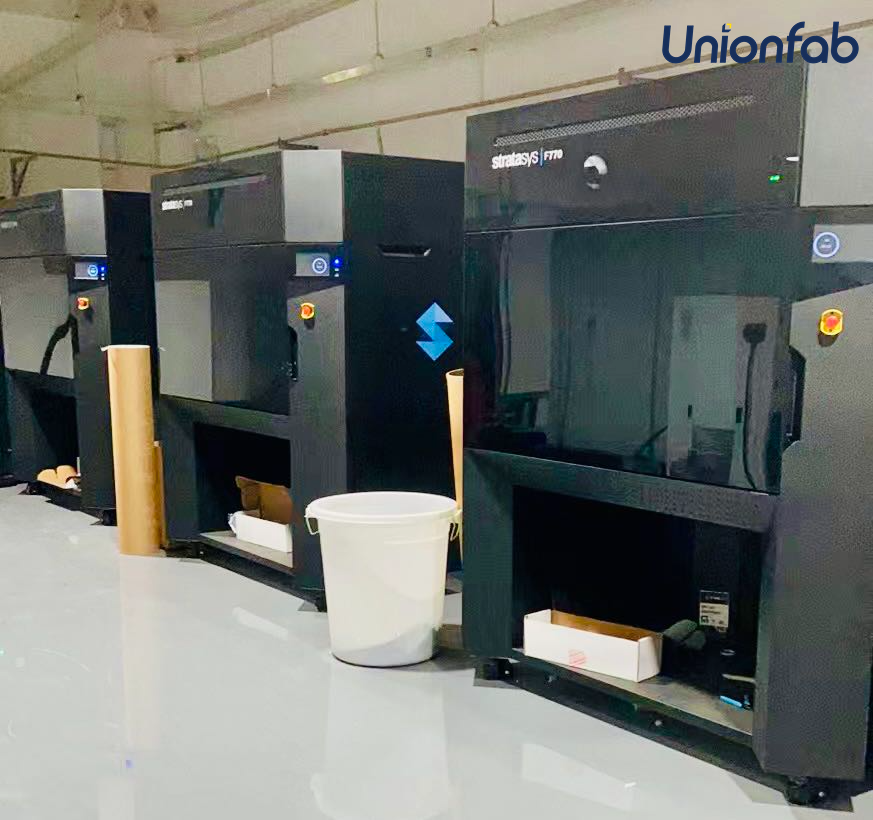
How it works: Plastic filament is heated and extruded layer by layer to form the object.
Result: The material cools and solidifies as each layer is added.
Comparison Table
Aspect | SLS | MJF | FDM |
---|---|---|---|
Materials | Nylon 6, 66, 11, 12 | MJF Nylon 12 Glass Bead | PLA |
Cost | $$$ | $$ | $ |
Surface Finish | ⭐⭐⭐⭐ | ⭐⭐⭐⭐⭐ | ⭐⭐ |
Dimensional Accuracy | ⭐⭐⭐⭐ | ⭐⭐⭐⭐⭐ | ⭐⭐ |
Post-Processing | Requires cleaning and sometimes support removal | Minimal, often no post-processing required | Requires sanding, smoothing, or painting |
Speed | ⭐⭐ | ⭐⭐⭐⭐⭐ | ⭐⭐ |
Applications | Functional prototypes, aerospace, automotive | Functional parts, quick production runs, consumer goods | Prototyping, small runs, budget-friendly projects |
In summary:
If you're working on high-performance, complex prototypes, go with SLS.
If you need fast, high-quality production with an emphasis on precision, MJF is the way to go.
For budget-conscious projects, FDM is a great choice, especially when you don’t need the top-tier performance of the other two technologies.
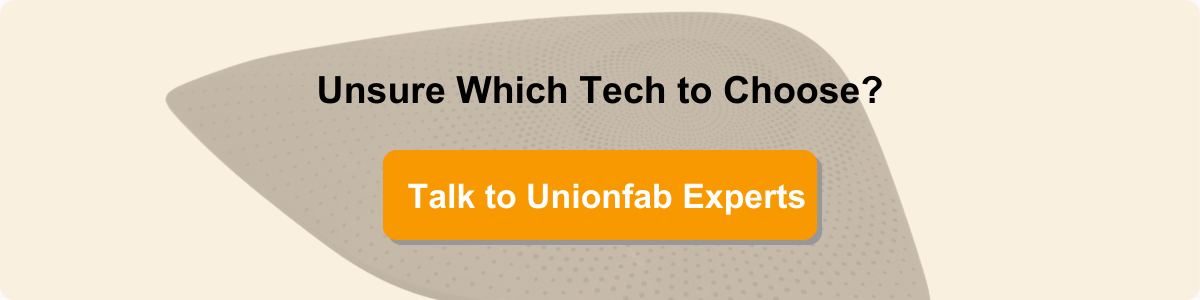
Cost-saving Design Tips
Hollow Designs with Structural Integrity
Remove internal material (walls ≥2mm thick) to reduce material usage while ensuring durability.
Scale Down & Simplify Geometry
Adjust non-critical dimensions and avoid unnecessary details to lower material volume and print time.
Optimize Infill & Orientation
Use low infill (10-20%) for non-structural parts and align critical features parallel to the build plate to save material and improve speed.
Batch Print & Arrange Efficiently
Print multiple models simultaneously and place them closely on the build plate to maximize machine efficiency.
Smooth Edges & Avoid Shallow Angles
Round sharp corners (fillet) to prevent material overflow and ensure angles >45° to reduce post-processing.
Design Inner Cavity Properly
Min. inner cavity dimension: 5mm; Max. depth: 100mm. Complex dead corners and sharp turns should be avoided to reduce powder residue and minimize material usage, thereby lowering printing costs.
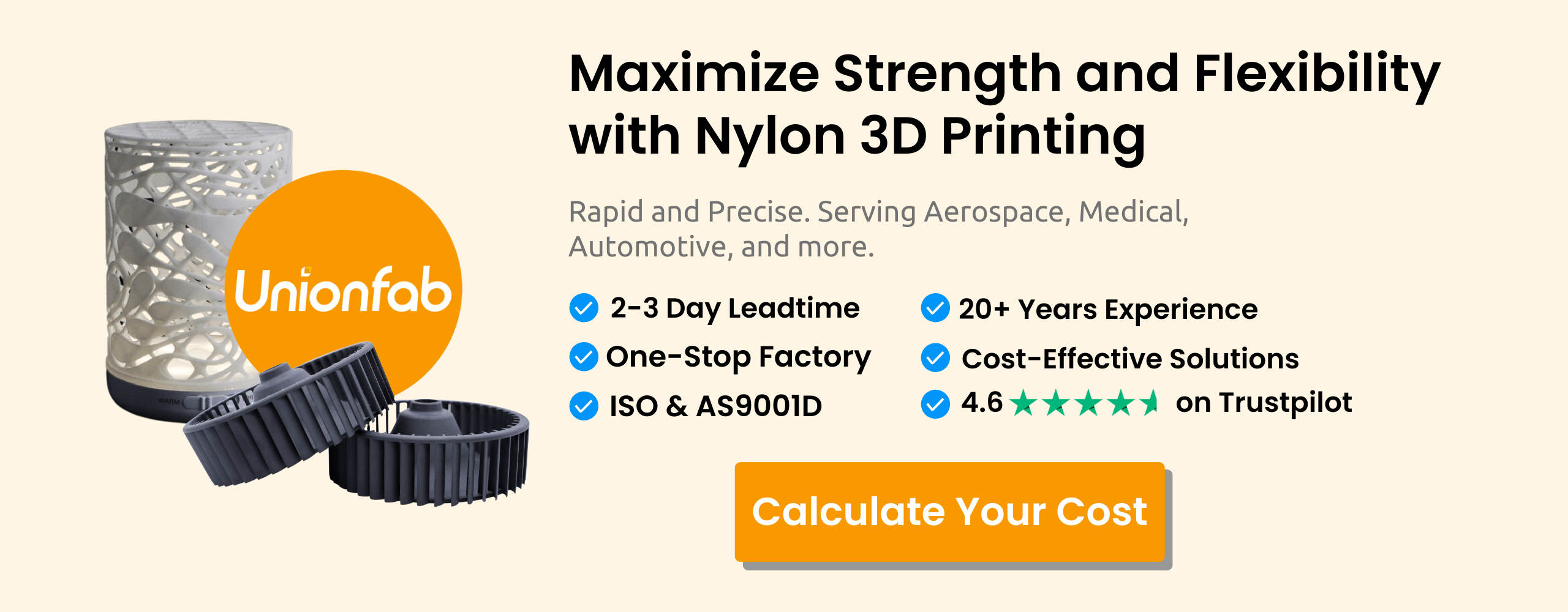
Why Outsourcing? The Hidden Costs of Self-printing
1. Initial Investment and Equipment Depreciation
Equipment Purchase: Industrial-grade nylon 3D printers (e.g., Stratasys Fortus series) are costly, over $200,000 per machine, and require additional post-processing equipment.
Facility Upgrades: Specialized space is needed for temperature and ventilation control (nylon printing can release fine dust and gases), adding infrastructure costs.
Advantage of Outsourcing: Service providers have already absorbed equipment depreciation costs, and customers only pay for printing services as needed, avoiding capital investment. ⠀
2. Material Costs and Waste
Material Procurement Premium: Nylon powder (e.g., PA12) costs around $70/kg, much higher than injection-molding nylon pellets ($2-5/kg). Specialty materials (e.g., carbon-filled nylon) cost even more.
Material Waste: While unused nylon powder can be partially recycled, repeated use reduces strength, resulting in 20-30% waste.
Inventory Management: Multiple materials need to be stored for different needs, and due to nylon’s moisture sensitivity, proper storage conditions are required.
Advantage of Outsourcing: Service providers reduce material costs through bulk purchasing and optimize powder recycling processes, minimizing material waste for customers. ⠀
3. Operating and Maintenance Costs
Equipment Maintenance: Core components like lasers and heating modules require regular replacement, with annual maintenance costs reaching 10-15% of the equipment price.
Consumables: Parts like the blade and resin filter in SLS processes wear out quickly, with monthly consumable costs around $500–1,000.
Energy Costs: Industrial-grade 3D printers typically consume 3-10kW, and electricity costs for continuous printing can account for 20% of total costs in some regions (e.g., Europe).
Advantage of Outsourcing: Service providers handle equipment maintenance and consumable replacement, and customers only pay for usage as needed. ⠀
4. Labor and Technical Training
Specialized Operator: Hiring skilled operators is necessary. Training takes 3-6 months, from basic operation to troubleshooting complex issues.
Cross-department Collaboration Costs: Design, engineering, and production departments must collaborate to optimize models, increasing internal communication costs.
Advantage of Outsourcing: Service providers offer a one-stop solution, reducing internal coordination costs. ⠀
5. Hidden Opportunity Costs
Idle Capacity: Non-continuous production leads to low equipment utilization (usually <50%), reducing capital efficiency.
Loss of Agility: In-house printing requires advance scheduling, making it difficult to respond quickly to urgent orders.
Advantage of Outsourcing: Service providers combine orders from multiple clients, achieving equipment utilization over 85%, and customers only share fixed costs. ⠀
6. Quality Control and Risk
Failure Rate Costs: Complex nylon parts have a failure rate of 5-15%, resulting in material and time losses.
Compliance Risks: Industries like medical need certifications such as ISO 13485, and establishing an in-house quality system can be costly.
Advantage of Outsourcing: Service providers absorb defective parts losses and have industry certifications, so customers don’t need to invest more.
Unionfab’s Nylon 3D Printing Service and Success Story
With 20+ years of expertise, 1,000+ industrial 3D printers, and 6 cutting-edge factories, Unionfab, certified with ISO 9001, ISO 13485, and AS 9001D, is committed to delivering high-quality, cost-effective 3D printing services.
The followings are the details of our stainless steel 3d printing service.
SLS | MJF | |
---|---|---|
Equipment | EOS; Farsoon | HP |
Materials | Nylon 12(White, Black) | MJF Nylon 12(Raw Gery) |
Max Part Size | 635 x 320 x 520mm | 380 x 380 x 280mm |
Layer Thickness | 0.1016 mm | 0.08 mm |
Tolerance | ±0.3% | ±0.3% |
Min. Feature Size | / | 0.5 mm |
Min. Wall Thickness | 0.762 mm | 0.508 mm |
Min. Reference Unit Price of Materials | Nylon 12(White): | MJF Nylon 12(Raw Gray): |
Pass Rate | 99.5% | 99.5% |
On-time Delivery Rate |
|
|
*The actual unit price is subject to real-time inquiry.
If you haven’t used Unionfab’s 3d printing service before, sign up to get 10% discount for your first order.
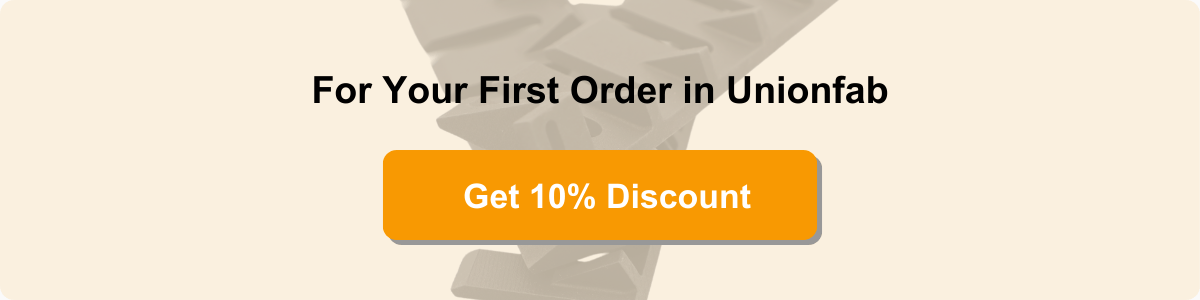
Post-Processing of Nylon
The 5 commonly used post-processing techniques for nylon by customers are: Paint glossy; Paint Matte; Dye Black; Sand Blasting; Vapor Smoothing; Color Paint.
![]() | ![]() |
---|---|
![]() | ![]() |
![]() | ![]() |
Success Story: Unionfab’s Advanced 3D Printing Solutions for Humanoid Robots at WAIC 2024
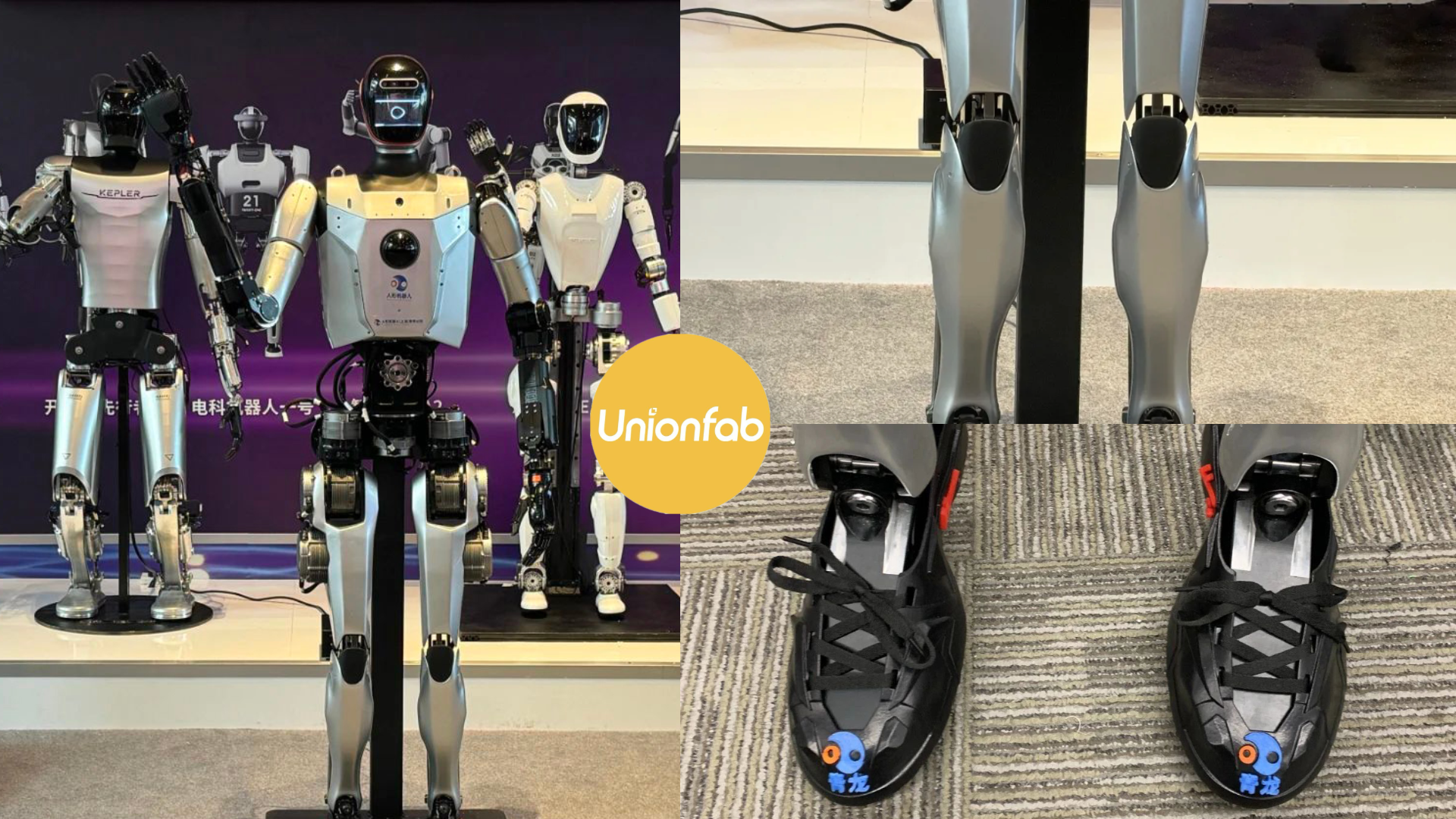
Client Background
Humanoid Robots (Shanghai) Co., Ltd., a China-based humanoid robot developer, planned to unveil its first humanoid robot at the World Artificial Intelligence Conference 2024 (WAIC 2024). To ensure rapid turnaround time (TAT) and high-quality production, they partnered with Unionfab to leverage 3D printing technology for manufacturing key robot components.
Challenge
The humanoid robot required several high-performance components that met strict durability and functionality standards:
Lightweight: Reduce inertia and improve movement response speed by using light materials.
Heat and Wear Resistance: Materials must withstand temperature fluctuations, vibrations, and long-term fatigue loads.
High Rigidity: Ensure structural stability during fast walking and resistance to interference.
Solution
Material Selection: High-performance Nylon was selected for its strength, durability, and heat resistance. And TPU was selected due to its outstanding flexibility and Elasticity. Both materials allowed the robot to function in demanding environments while maintaining lightweight characteristics.
Precise 3D Printing: Using advanced SLS (Selective Laser Sintering) 3D printing technology, Unionfab created intricate geometries for the robot’s leg shell (Nylon) and shoes (TPU), ensuring an exact fit and excellent durability.
Aesthetic & Functional Design: The leg shell was given a painted finish, enhancing the robot’s sleek mechanical appearance. Additionally, flexible shoes were designed to provide stable and efficient movement, vital for the robot's mobility.
Result
The collaboration produced outstanding results for both the robot's performance and aesthetic appeal.
Enhanced Performance: The 3D-printed components optimized airflow, improved mobility, and ensured the robot’s ability to deliver an outstanding performance.
Durability & Weight Reduction: The use of high-performance nylon ensured robust strength while reducing the overall weight of the robot.
Fast Turnaround: Unionfab was able to produce and deliver the parts within a short timeframe, helping the project meet the tight deadlines for the WAIC2024 exhibition.
Sustainability: The 3D printing process minimized material waste, aligning with sustainability objectives and offering an eco-friendly solution.
FAQ
Is Nylon good for 3D printing?
Yes, nylon is good for 3D printing. It is strong, durable, and flexible, making it suitable for many applications.
Is Nylon stronger than PLA?
Yes, nylon is generally stronger and more durable than PLA. It has better impact resistance and flexibility.
Is 3D printed Nylon brittle?
No, 3D printed nylon is not brittle. It is flexible and tough, but it can become more brittle if not printed or stored properly.
What is the difference between TPU and Nylon?
TPU is a flexible, rubber-like material, while nylon is stronger and more rigid. TPU is ideal for flexible parts, whereas nylon is better for durable and tough components.
What is the difference between thermoplastic and nylon?
Nylon is a type of thermoplastic. Thermoplastics are materials that can be melted and reformed, and nylon is one of the most common thermoplastics used in 3D printing.