Guide to Copper 3D Printing[+Cost Calculator]
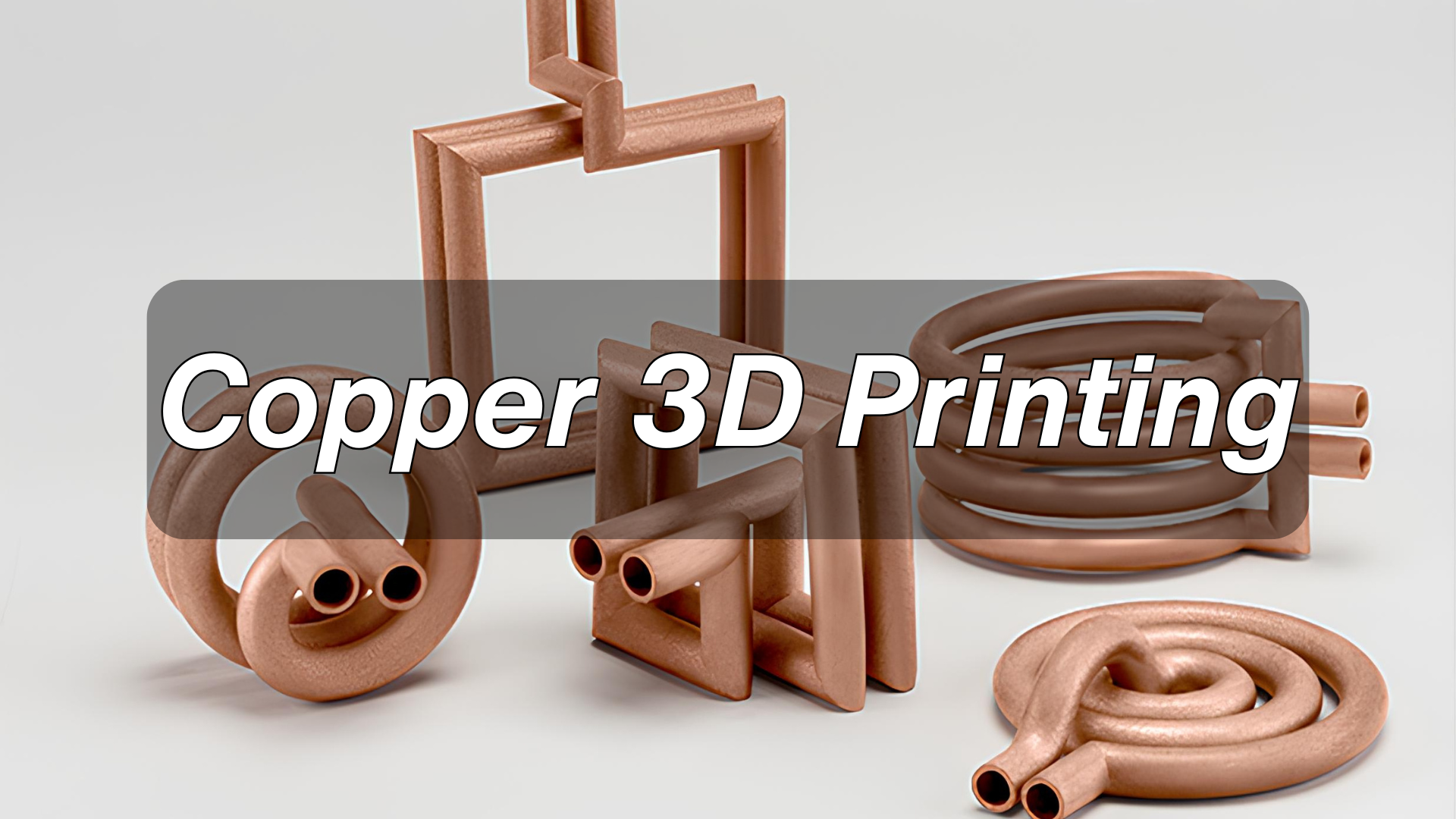
Explore the advantages of copper 3D printing and learn about its common alloys, printing technologies, and applications in various industries.
Introduction
Copper and its alloys, known for their excellent conductivity, corrosion resistance, and mechanical properties, are essential in fields like electronics, power transmission, aerospace, and medical devices.
However, traditional methods struggle to efficiently produce complex copper parts. 3D printing, with its layer-by-layer approach, provides a new way to precisely shape copper, especially for high-performance, customized components.
Advantages of Copper Over Other Metals Used in 3D Printing
Copper stands out as a unique material in additive manufacturing due to its unmatched combination of properties, making it irreplaceable in specific high-performance applications. Below is a detailed comparison of copper’s advantages over other commonly 3D-printed metals.
Unique Advantages of Copper
Unparalleled Thermal and Electrical Conductivity
Electrical: 100% *IACS (vs. 3–5% for steel, 30–40% for aluminum).
Thermal: 400 W/m·K (10× steel, 3× aluminum), ideal for heat exchangers and electronics.
Antimicrobial Properties
Kills >99% bacteria/viruses on contact( a feature absent in steel, titanium, or aluminum). Critical for medical tools and high-touch surfaces.
Corrosion Resistance in Specific Environments
Copper alloys (e.g., CuNi, CuSn) excels in humid, high-temperature, and chemically aggressive environments, making it ideal for marine equipment and chemical pipelines. For example, 3D-printed copper alloy valves last twice as long as stainless steel in acidic media.
*IACS: International Annealed Copper Standard (conductivity relative to pure copper).
Comparison of Key Properties
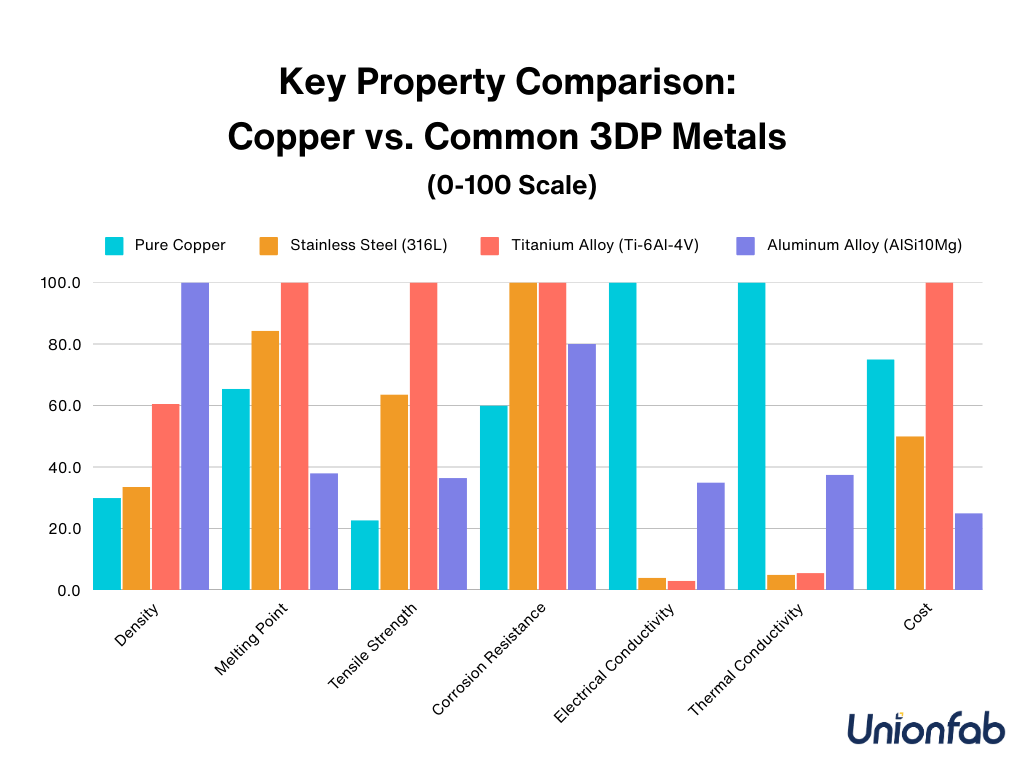
As we can see from the table above, while copper excels in conductivity and thermal management, it has lower strength compared to steel or titanium and higher density than aluminum. Engineers must prioritize:
Conductivity/thermal needs: Choose copper.
Strength-to-weight ratio: Opt for titanium or aluminum.
Cost-sensitive projects: Use steel or aluminum.
Why Pure Copper is So Challenging to 3D Print?
Pure copper poses significant challenges in 3D printing due to its unique physical and chemical properties, which complicate common additive manufacturing processes like Selective Laser Melting (SLM) and Electron Beam Melting (EBM). The primary difficulties include:
High Thermal Conductivity
Copper rapidly dissipates heat away from the laser/energy beam focal point, making it hard to maintain a stable melt pool. This leads to inconsistent layer bonding, porosity, and incomplete fusion, requiring precise energy management to avoid defects.
High Reflectivity
Pure copper reflects infrared lasers (commonly used in SLM) rather than absorbing them, necessitating higher laser power or alternative wavelengths (e.g., green lasers). This increases costs and complexity, as green laser systems are less common and more expensive.
Oxidation Sensitivity
Copper oxidizes at high temperatures, forming oxides that degrade electrical/thermal conductivity and mechanical properties. Printing must occur in inert atmospheres (e.g., argon or nitrogen), but even trace oxygen can cause contamination.
Therefore, due to the challenges above, copper now used in 3d printing are mainly various copper alloys, which can addresses these inherent challenges while retaining its advantageous properties (e.g., high thermal and electrical conductivity).
Common Types of Copper Alloys Used in 3D Printing
Below are the mainstream copper alloys used in additive manufacturing.
Alloy Name | Composition | Key Properties | Cost | Typical Applications |
---|---|---|---|---|
Cu + 0.5–1.2% Cr + 0.03–0.3% Zr | High strength, | $$ | Rocket combustion chambers, nuclear fusion components, electronic heat sinks | |
CuNiSi | Cu + 2–4% Ni + 0.5–1.5% Si | High thermal resistance, fatigue resistance, moderate conductivity (~50% IACS) | $$$ | Mold inserts, automotive engine components |
CuSn | Cu + 5–15% Sn | Excellent wear/corrosion resistance, good fluidity, high strength (conductivity ~15% IACS) | $$ | Bearings, gears, artistic castings |
CuAl | Cu + 5–11% Al (optional Fe/Ni) | High strength, seawater corrosion resistance, high-temperature oxidation resistance (conductivity 7–15% IACS) | $$ | Marine components, chemical valves |
Cu-Al₂O₃ | Cu + 0.3–1.2% Al₂O₃ nanoparticles | Ultra-high strength (near steel), resistance to high-temperature softening (>800°C), retained conductivity (60–90% IACS) | $$$$ | Fusion reactor first walls, high-energy laser heat exchangers |
CuFe | Cu + 10–30% Fe | High wear resistance, low cost (conductivity 20–40% IACS) | $ | Tooling fixtures, industrial wear-resistant parts |
In Summary,
Cost: CuFe< CuCrZr, CuSn, CuAl< CuNiSi< CuNiSi
Cost-effective choice: CuFe (wear-resistant) or CuAl (corrosion-resistant).
Balanced performance & cost: CuCrZr (conductivity + high temperature) or CuAl (overall corrosion resistance).
Ultimate performance (cost not a concern): Cu-Al₂O₃ (ultra-high temperature) or CuNiSi (fatigue resistance).
Beyond the material recommendations above, our customer orders also reveal a clear trend. CuCrZr stands out as the most popular choice, thanks to its excellent conductivity, high-temperature stability, and cost-effectiveness.
Want to learn more about CuCrZr 3D printing? Contact our experts today! Plus, first-time customers at Unionfab can enjoy an exclusive 10% discount—sign up now!
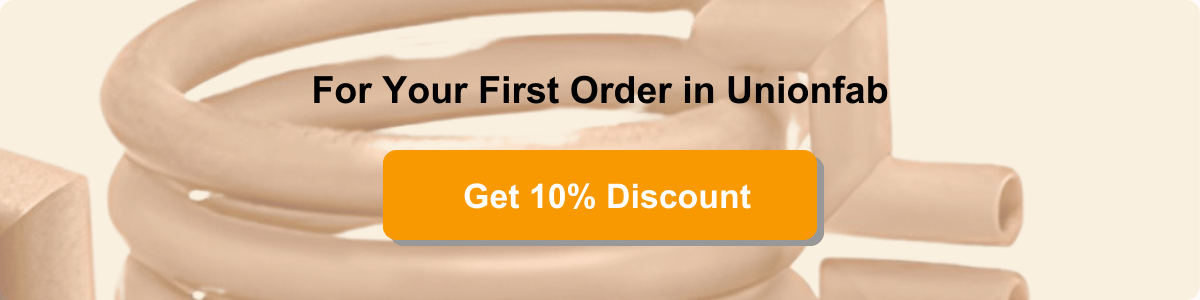
Copper 3D Printing Technologies
Technology | Speed | Cost | Printing Quality | Key Advantages | Best For |
---|---|---|---|---|---|
SLM | Slow | Very High ($$$$) | High (near-full density, smooth surfaces) | High precision, dense parts, excellent conductivity | Complex heat exchangers, RF components |
EBM | Fast | High ($$$) | Moderate (requires post-machining) | Fast, high-purity prints, handles large builds | Large aerospace parts, thermal systems |
Very Fast | Low ($) | Moderate (porous, post-processing needed) | Fast, low cost, scalable for batches | Decorative items, prototypes | |
DED | Medium | Medium ($$) | Low (layered appearance) | Repairs/adds material, high deposition rates | Repairing tools, hybrid manufacturing |
Material Extrusion | Medium | Lowest ($) | Low (layered, <10% IACS conductivity) | Desktop-friendly, ultra-low cost | Non-functional models, education |
Key Takeaways
Speed: Binder Jetting > EBM > DED > Material Extrusion > SLM.
Cost: SLM/EBM > DED > Binder Jetting > Material Extrusion.
Quality: SLM > EBM > Binder Jetting > DED > Material Extrusion.
How to Choose The Most Suitable Technology?
Prioritize Speed + Low Cost?
Binder Jetting or Material Extrusion (for non-functional parts).
Need Maximum Quality/Conductivity?
SLM (for critical components) or EBM (for large parts).
Repair/Modify Existing Parts?
DED (e.g., welding electrode tips).
Prioritize Scale and Speed? Prototypes:
SLM or Material Extrusion; Mass production: Binder Jetting.
New Trends in Copper 3D Printing
Copper 3D printing is rapidly evolving to overcome historical challenges and expand its applications. By 2030, copper 3D printing is projected to grow at 18% CAGR. Here are the latest advancements shaping the industry:
Green Laser Adoption
Traditional infrared lasers struggle with copper’s high reflectivity (~95% IR reflection). Green lasers (515 nm wavelength) improve energy absorption by 3–5×, enabling faster printing and higher density.
Scaling for Mass Production Binder Jetting Breakthroughs
Binder jet-printed copper parts now achieve ~70% IACS after sintering + infiltration (vs. 50% in 2020).
Multi-Material Printing
Multi-Material Printing integrates copper with materials like stainless steel, ceramics, or polymers to create functionally graded designs, overcoming single-material limitations.
It enables unified manufacturing of components that combine thermal management, electrical conductivity, and structural strength in one build, eliminating assembly steps and boosting efficiency.
If you’re interested in copper 3d printing and willing to employ this technology to bring your prints to life, please feel free to contact us. Or use our online free cost calculator below to figure out how much will your print cost.
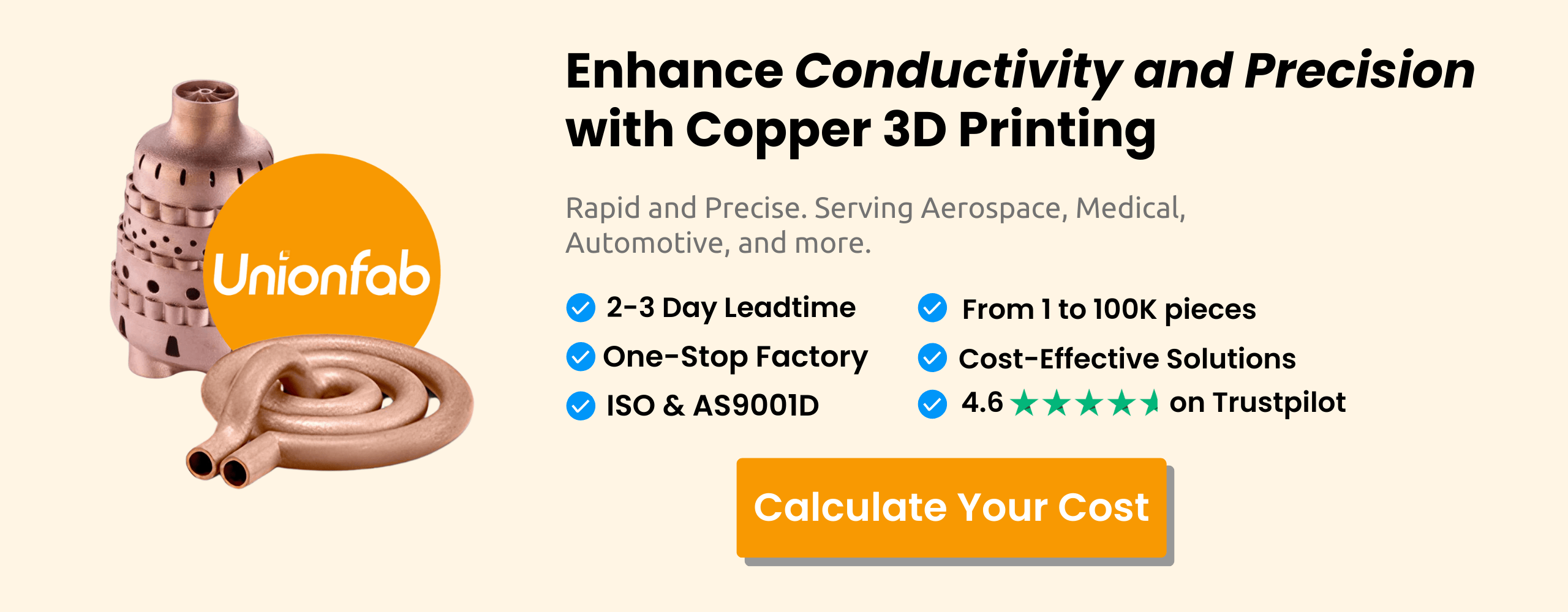
Unionfab’s Copper 3D Printing Service
The followings are the details of Unionfab’s copper 3d printing services.
Technology | SLM/DMLS |
---|---|
Equipment | SLM/DMLS: BLT; SLM; EOS; EXONE |
Materials | CuCrZr |
Max Part Size | 280x280x350mm |
Layer Thickness | 50-100 μm |
Tolerance | ±0.2 mm |
Min. Wall Thickness | 0.3 mm–0.5 mm for fine features (in SLM) |
Minimum Feature Size | 0.5 mm |
Minimum Clearance Between Parts | 0.2mm |
Minimum Size of Details | 1mm |
Minimum height and width details | Embossed: 0.5mm |
Minimum height and width | 1mm |
Enlargement ratio | 1/1 |
Pass Rate | 99.5% |
Lead Time | As fast as 4-5 days |
On-time Delivery Rate | 98% |
Certification | ISO 9001, ISO 13485, and AS 9001D |
Post Processing
![]() | ![]() |
---|---|
![]() | ![]() |
Customer Feedback
See Unionfab’s customer review from Trustpilot:
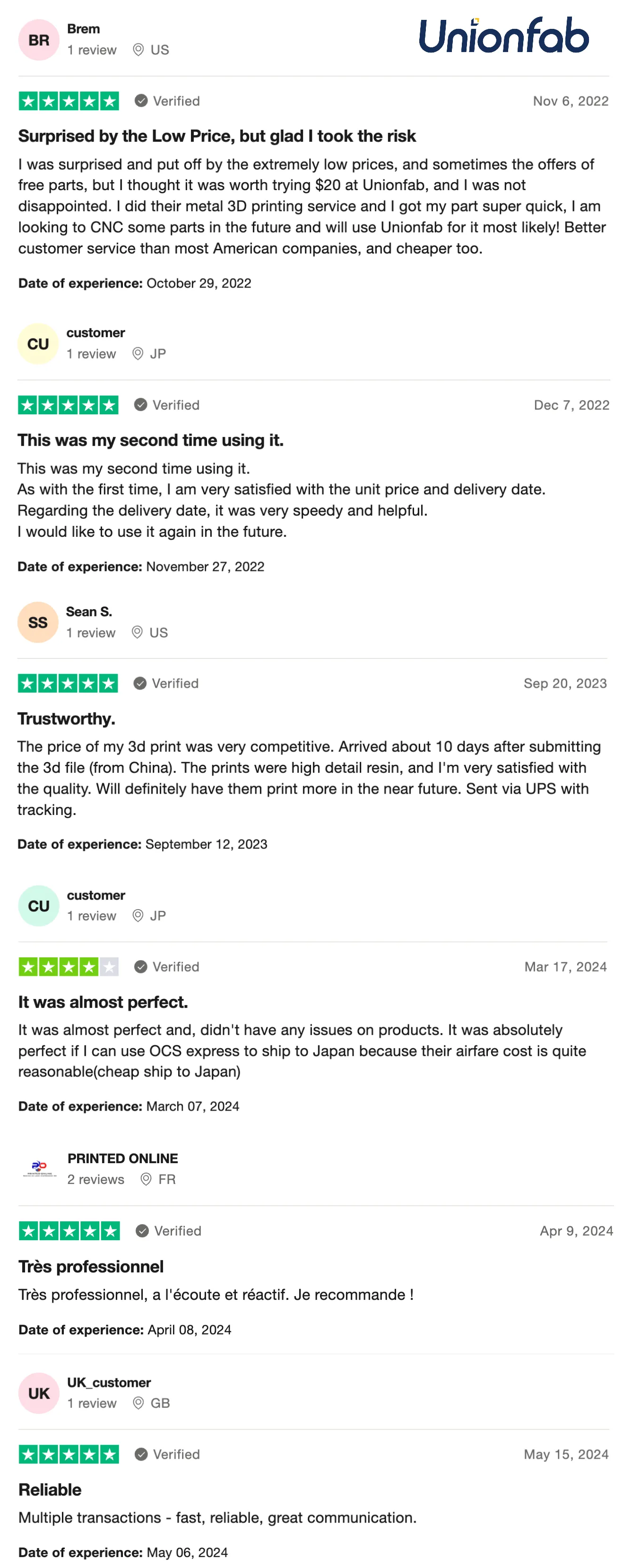