Guide to Polycarbonate 3D Printing [+Free Cost Calculator]
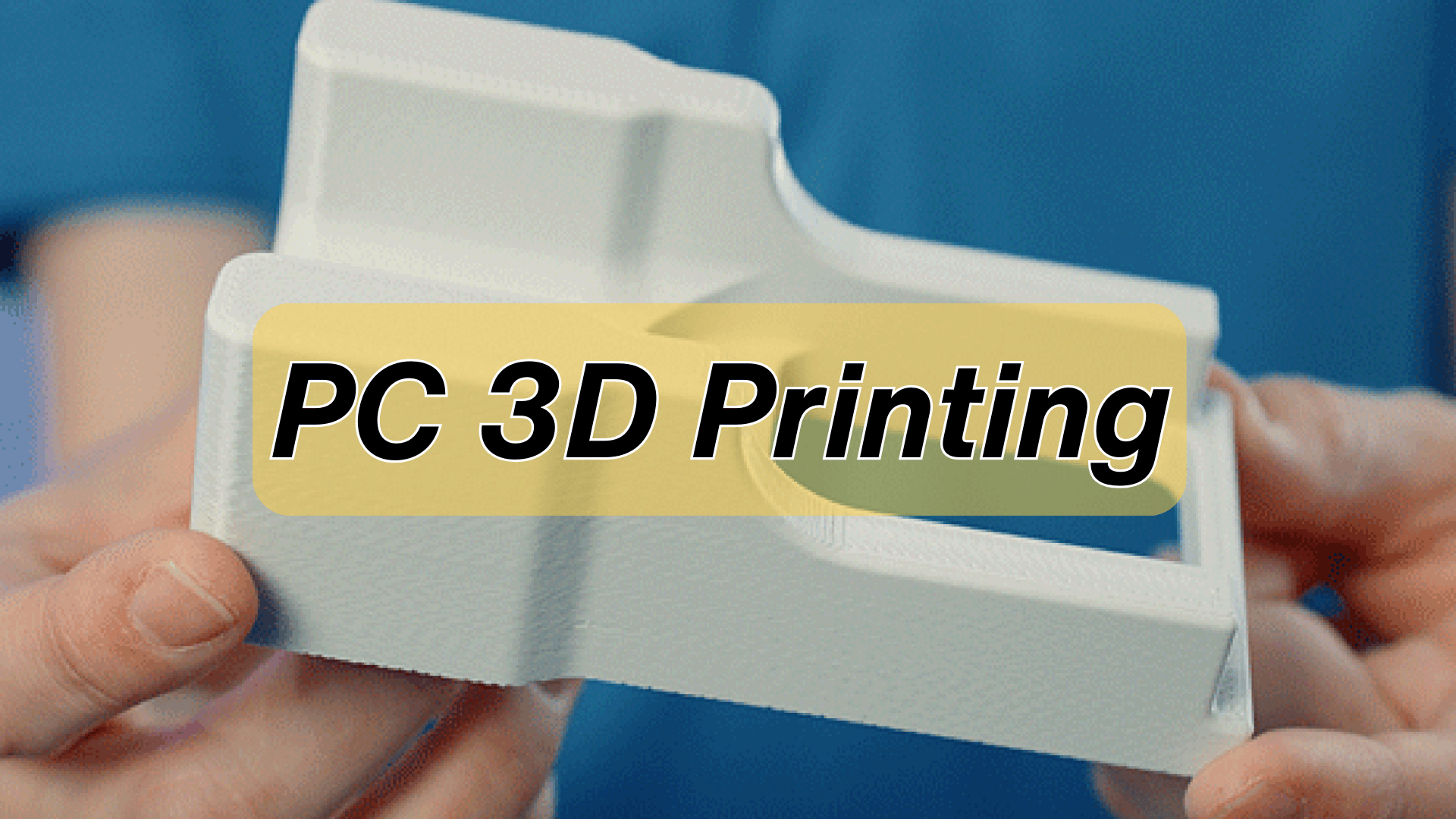
Discover why PC plastics are modified for 3D printing and why FDM is the dominant technology.
Introduction
When designing high-strength, heat-resistant functional prototypes or end-use parts, traditional 3D printing materials like PLA or ABS often fall short. PLA lacks durability, while ABS, though tougher, struggles in high-temperature environments.
This is where polycarbonate (PC) shines—a material known for its exceptional strength, impact resistance, and thermal stability.
PC Plastic: Pros & Cons
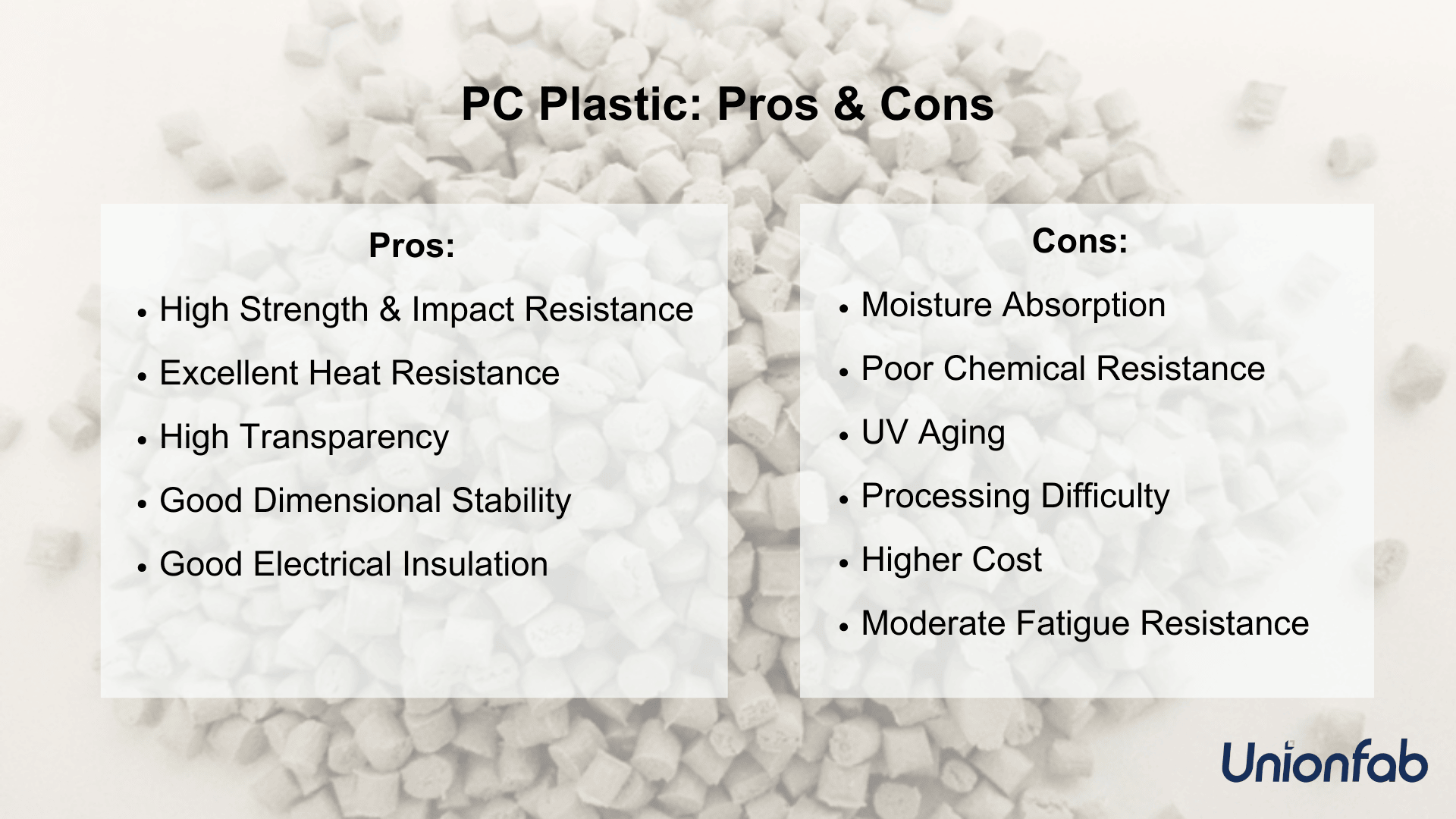
Pros:
The most significant advantages of PC (Polycarbonate) include:
High Strength and Impact Resistance: PC is more durable than many plastics like ABS, making it ideal for safety equipment, automotive parts, and other high-strength applications.
Excellent Heat Resistance: With a glass transition temperature (Tg) of about 145°C, PC maintains good mechanical properties in high-temperature environments.
High Transparency: PC has light transmittance of up to 88%-90%, making it ideal for optical applications such as glasses and lampshades.
Good Dimensional Stability: PC resists deformation under temperature changes or stress, making it suitable for high-precision components.
Good Electrical Insulation: PC’s excellent electrical insulating properties make it suitable for electronic components and enclosures.
Cons:
Although PC (Polycarbonate) offers superior performance, it also has some drawbacks, primarily including:
Moisture Absorption: PC absorbs moisture, which can affect dimensional accuracy and mechanical performance.
Solution: Dry PC material (e.g., at 80-100°C for several hours) before use.Poor Chemical Resistance: PC is vulnerable to acids, alkalis, and solvents (like alcohol, acetone, and benzene), which can cause stress cracking or degradation.
Solution: Avoid strong solvents or use coatings for better chemical resistance.UV Aging: Prolonged UV exposure can cause PC to yellow and become brittle, affecting its appearance and performance.
Solution: Use PC-UV enhanced versions or apply UV protective coatings.Processing Difficulty: PC has a high melting point (around 270-300°C), which can cause warping during FDM 3D printing and make shrinkage harder to control in SLS.
Solution: Use high-temperature printers or choose PC-ABS or PC-Blend for easier processing.Higher Cost: PC costs more than ABS or PLA, increasing both material and processing expenses.
Solution: Choose a cost-effective PC variant like PC-ABS, PC-Blend, or other modified materials.Moderate Fatigue Resistance: PC may lose strength with cyclic loading, leading to stress cracking over time.
Solution: Use reinforced PC (e.g., glass fiber reinforced PC) for improved durability.
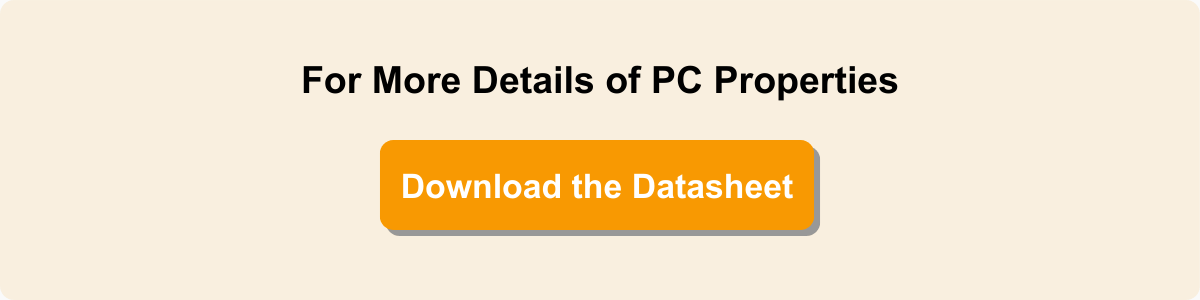
PC vs. ABS vs. PMMA vs. Nylon vs. PEEK vs. PP
PC (Polycarbonate) is often compared with other engineering plastics or high-strength thermoplastic materials, including the following:
PC vs. ABS (Impact Resistance vs. Machinability)
PC: Higher strength, impact resistance, and heat resistance (>120°C), but harder to process and prone to warping during printing.
ABS: Good mechanical properties, moderate heat resistance (80-100°C), easy to process, cost-effective, ideal for automotive and home appliance housings.
✅ Choose PC: For high-strength, high-temperature applications (e.g., industrial parts)
✅ Choose ABS: For cost-effective, easy processing (e.g., electronic enclosures)
PC vs. PMMA (Acrylic) (Impact Resistance vs. Transparency)
PC: High impact strength, shatter-resistant, good heat resistance (>120°C), but lower transparency.
PMMA: Higher transparency (similar to glass), but more brittle and much less impact-resistant than PC.
✅ Choose PC: For impact-resistant, transparent parts (e.g., bulletproof glass, helmets)
✅ Choose PMMA: For optical applications (e.g., display boxes, light covers)
PC vs. Nylon (PA) (Rigidity vs. Flexibility)
PC: Higher rigidity, impact-resistant, but less flexible.
Nylon: More flexible, excellent wear resistance, but absorbs moisture and has poor dimensional stability.
✅ Choose PC: For high-strength, impact-resistant structural parts (e.g., electronic housings)
✅ Choose Nylon: For high-wear parts (e.g., gears, pulleys)
PC vs. PEEK (High-Temperature High-Performance Materials)
PC: Good heat resistance (Tg ≈ 145°C), lower cost.
PEEK: Excellent heat resistance (Tg ≈ 250°C), superior mechanical properties, but very expensive.
✅ Choose PC: For general high-temperature applications (e.g., automotive parts)
✅ Choose PEEK: For extreme environments (e.g., aerospace, medical implants)
PC vs. PP (Polypropylene) (Strength vs. Chemical Resistance)
PC: Higher strength, better rigidity, but poorer chemical resistance.
PP: Strong chemical resistance, good toughness, but lower rigidity.
✅ Choose PC: For high-strength applications (e.g., electronic enclosures)
✅ Choose PP: For chemical corrosion resistance (e.g., chemical containers) ⠀
Summary:
PC vs. ABS → PC is stronger and more heat-resistant, while ABS is easier to process and cheaper.
PC vs. PMMA → PC is more impact-resistant, while PMMA has higher transparency.
PC vs. Nylon → PC is more rigid, while Nylon is more flexible and wear-resistant.
PC vs. PEEK → PC is more affordable, while PEEK excels in extreme high-temperature scenarios.
PC vs. PP → PC is structurally stronger, while PP offers better chemical resistance.
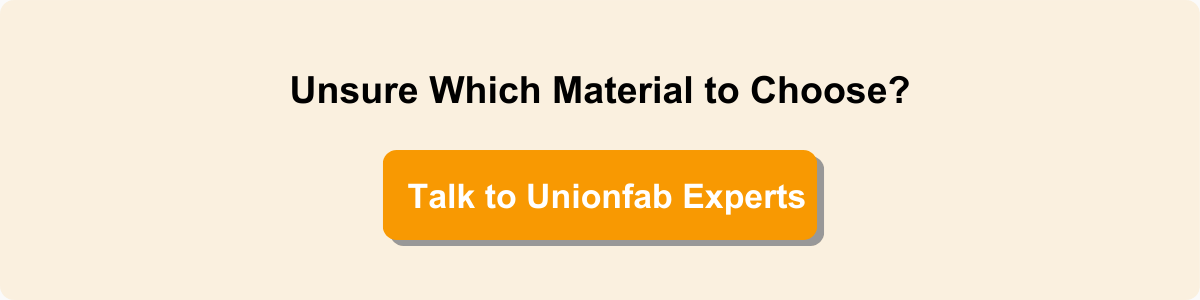
Common PC Types Used in 3D Printing
Notably, unmodified PC is expensive and challenging to 3D print due to its high moisture absorption, elevated melting point, significant shrinkage, and tendency to warp and delaminate. As a result, its application in 3D printing is limited. Currently, most PC materials used in 3D printing are modified variants, primarily including the following types:
1. PC-ABS
The most commonly used PC composite, combining PC’s heat resistance with ABS’s printability.
Features:
Lower printing temperature (~250°C), making it easier to print than pure PC
High impact resistance, better than both ABS and pure PC
Moderate heat resistance (110-125°C), suitable for most industrial applications
Good surface quality, requiring minimal post-processing ⠀
Applications:
Automotive parts: dashboards, ventilation components, electronic housings
Electronic enclosures: durable and heat-resistant
Industrial prototypes: strong enough for functional testing
2. PC-CF (Carbon Fiber-Reinforced PC)
High strength and lightweight, ideal for load-bearing parts
Features:
Increased stiffness, making it more rigid and resistant to deformation
Higher heat resistance (120-140°C), suitable for high-temperature environments
Lower warping, as carbon fibers reduce thermal expansion and improve dimensional stability
Rougher surface, reduced toughness, suitable for structural parts but less for impact resistance
Applications:
Drones & aerospace components: lightweight and high-strength
Automotive engine bay parts: heat-resistant and durable
Mechanical jigs and fixtures: stiff and dimensionally stable
3. PC-GF (Glass Fiber-Reinforced PC)
Higher heat resistance than PC-CF, extremely rigid but slightly heavier
Features:
Highest heat resistance (130-150°C), ideal for high-temperature environments
Excellent dimensional stability, suitable for precision components
More impact-resistant than PC-CF but slightly more brittle than PC-ABS ⠀
Applications:
Electrical enclosures: heat-resistant and insulating
High-temperature mechanical parts: engine covers, industrial machine components
Chemical-resistant parts: laboratory equipment
4. PC-PBT (Polybutylene Terephthalate)
Resistant to chemicals, ideal for harsh environments
Features:
Better chemical resistance than pure PC, making it suitable for exposure to oils, solvents, and chemicals
Higher heat resistance than PC-ABS (120-140°C)
Good toughness and impact resistance, but slightly harder to print ⠀
Applications:
Chemical equipment casings
Automotive fuel system components
Weather-resistant industrial parts
5. PC-FR (Flame-Retardant PC)
Designed for electrical and aerospace industries with high safety standards
Features:
Contains flame retardants and meets UL94 V-0 standards (self-extinguishing)
Maintains mechanical strength and heat resistance close to pure PC
Commonly used in electrical and aerospace applications ⠀
Applications:
Battery enclosures, circuit board mounts
Aerospace components
Fire-resistant safety equipment
FDM — Preferred Technology for PC 3D Printing
PC materials are compatible with both FDM and SLS 3D printing technologies. However, due to PC powder’s high melting point, poor flowability, and strong moisture absorption, SLS printing is technically demanding and costly, restricting its widespread use.
In contrast, PC excels in FDM printing, making FDM the preferred method for polycarbonate (PC) 3D printing.
Why is FDM the Mainstream PC 3D Printing Technology?
FDM has become the dominant choice for PC 3D printing due to several key advantages:
1. High-Temperature Compatibility
PC requires a high extrusion temperature (260–310°C), which FDM printers can handle with heated nozzles and heated beds (100–120°C). This minimizes warping and ensures strong layer adhesion. ⠀
2. Preservation of Mechanical Properties
Slow printing speeds (20–50 mm/s) and optimized layer thickness (0.1–0.3 mm) help retain PC’s high impact resistance, strength, and heat resistance (110–130°C), making it ideal for engineering applications. ⠀
3. Versatility with Modified PC Materials
FDM supports reinforced PC materials (e.g., glass fiber or carbon fiber-enhanced PC), enabling lightweight, high-rigidity applications that are challenging for SLS to process. ⠀
4. Greater Process Control & Reliability
FDM reduces moisture absorption and warping risks through enclosed print chambers, pre-print drying (80–100°C), and improved bed adhesion (PEI/glass fiber sheets), ensuring higher success rates compared to SLS.
How FDM 3D Printing Works?
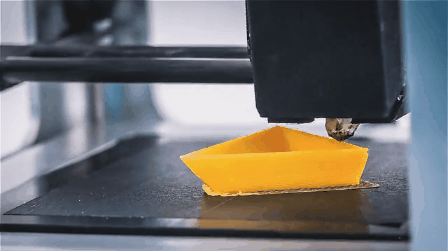
FDM builds objects layer by layer using melted thermoplastic filament. The key steps include:
Melting & Extrusion
The filament is heated and extruded as a viscous fluid.
Layer-by-Layer Deposition
The nozzle follows a G-code path, precisely depositing material onto the print bed.
Cooling & Solidification
The material cools and hardens immediately, forming a solid structure. ⠀
Post-processing can be applied as needed to enhance the final product.
Desktop VS. Industrial-grade FDM 3D Printing for PC
Print Accuracy
Desktop: Lower accuracy (0.1-0.3mm), noticeable layer lines and defects, especially for large or complex parts.
Industrial: Higher accuracy (0.05mm or smaller), smooth surface, fine details, stable printing with fewer defects. ⠀
Material Properties
Desktop: Printing PC can cause warping, shrinking, and rough surfaces, with poor mechanical properties, especially without a closed chamber.
Industrial: Precise temperature control and a closed environment ensure better performance of PC materials, offering improved strength and heat resistance. ⠀
Print Size
Desktop: Smaller print size (200x200x200mm), large parts need to be printed in sections.
Industrial: Larger print sizes, ideal for large parts and prototypes.(Unionfab’s largest build volume: 1000* 610 * 610mm) ⠀
Print Stability
Desktop: Less stable printing process, prone to clogging or failure, requiring frequent adjustments and maintenance.
Industrial: Stable, automated printing with professional temperature control and a closed environment, ensuring consistent high-quality results. ⠀
Printing Costs
Desktop: Low equipment and material costs but higher maintenance and waste.
Industrial: Higher equipment cost, suitable for mass production and high-precision needs, with lower waste and higher efficiency. ⠀
End-Product Usability
Desktop: PC parts printed are generally not suitable as end products due to rough surfaces and unstable properties, best for prototypes or non-structural applications.
Industrial: PC parts printed are suitable as end products, offering better surface quality, mechanical properties, and heat resistance, ideal for industrial applications
In summary,
Desktop FDM printers are suitable for individuals, hobbyists, or small studios. They can print PC materials, but their print accuracy, material properties, and stability are inferior to industrial-grade equipment.
Industrial FDM printers offer higher stability, accuracy, and material properties, making them ideal for mass production and high-performance industrial applications.
However, industrial FDM printers are often expensive, so outsourcing printing services can be a more cost-effective option.
If you are interested in outsourcing services and want to know how much your model will cost, feel free to use Unionfab’s online free cost calculator below.
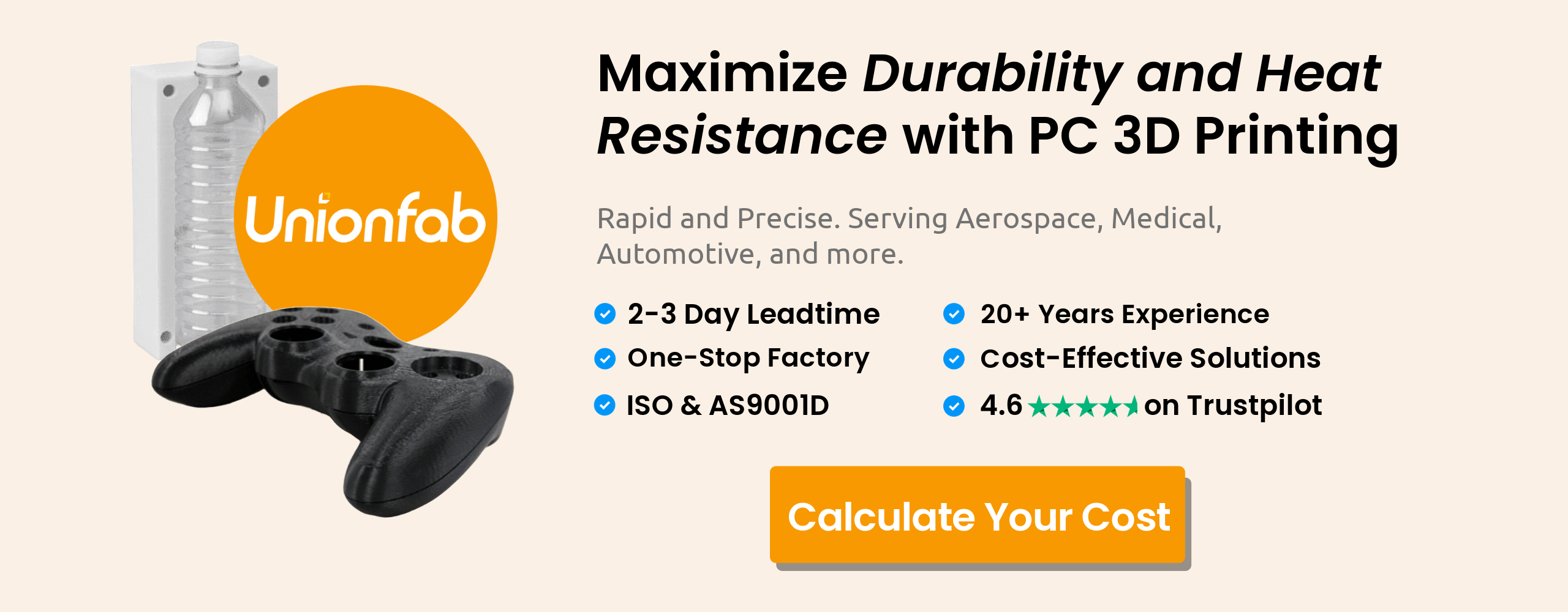
Unionfab’s PC 3D Printing Service
Technology: FDM
Materials: Modified PC; PC-FR (UL-94-V0)
Max Part Size: 1000 x 610 x 610mm
Layer Thickness: 0.178mm~0.508mm
Tolerance: 0.05mm
Min. Wall Thickness: >=1mm
Part Pass Rate: 99.5%
On-time Delivery Rate (DHL, FedEx etc.): 99%
Post Processing:
![]() | ![]() |
---|---|
![]() | ![]() |
If you haven’t used our 3d printing service before, sign up to get 10% discount for your first order.
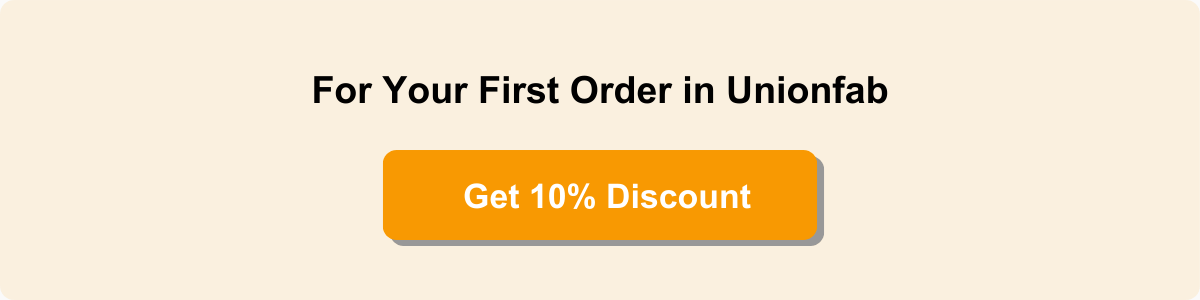
Unionfab’s Success Story of PC-FR 3D Printing
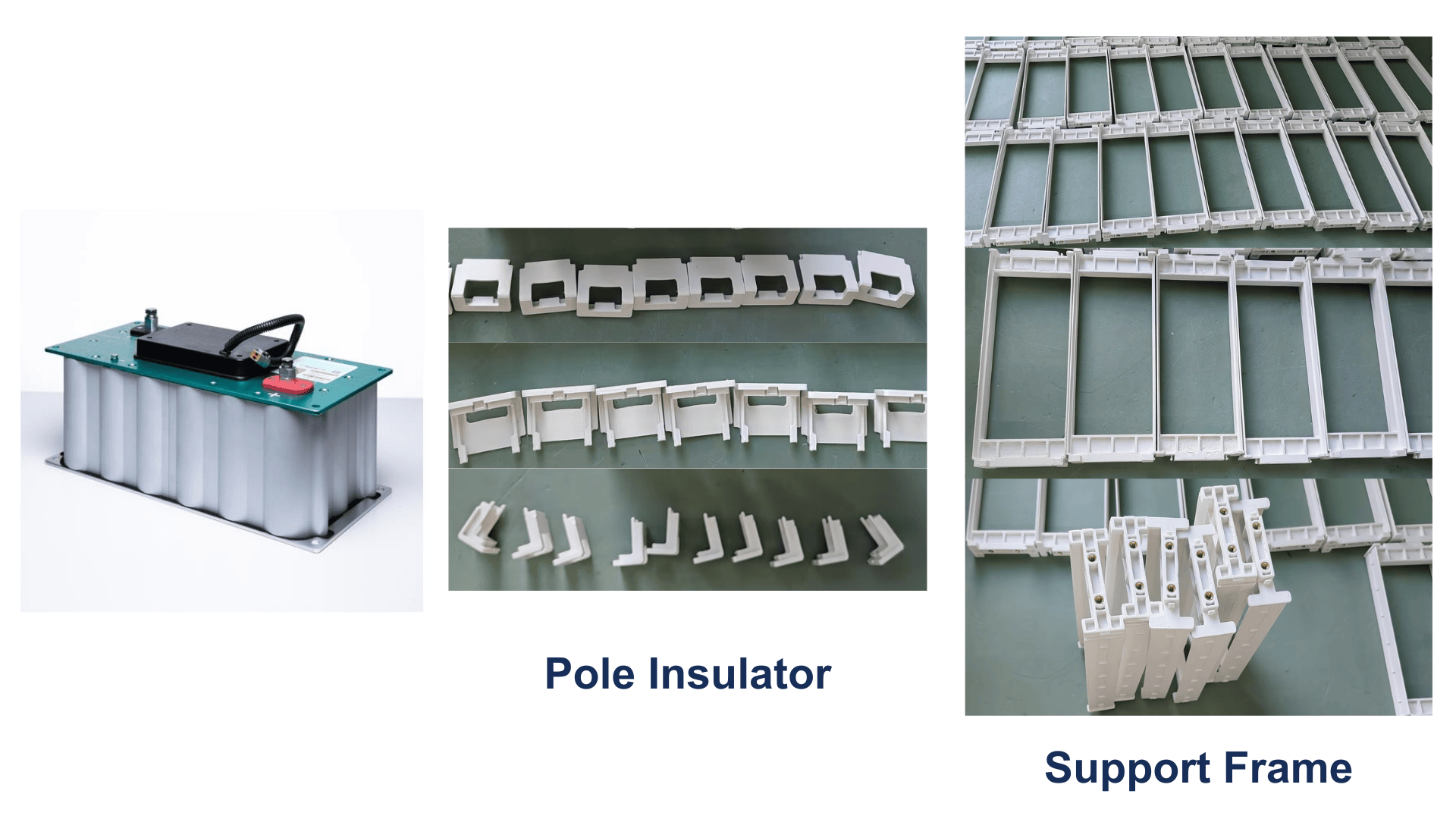
Client Background
The client is an innovative developer and producer of supercapacitors and double-layer capacitors, providing energy storage solutions for applications like vehicle start-up systems, electric buses, and subways. They chose to cooperate with Unionfab to produce some components for their new series of supercapacitors used in drones, electronic products, and more.
Challenge
High-performance materials were required to produce the components for their new supercapacitor system, specifically the pole insulator and the support frame. These components needed to meet stringent requirements for:
Electrical insulation to prevent leakage currents.
Mechanical strength to withstand high-pressure environments.
Flame-retardant properties to enhance safety under demanding conditions. The client sought a manufacturing solution that could achieve both precision and performance, while reducing production time and costs.
Solution
Unionfab leveraged Industrial FDM 3D printing technology to produce the key components. The solution involved:
Material Selection: PC-FR (UL-94-V0) was chosen for its ideal combination of electrical insulation, mechanical strength, and flame retardance, ensuring safety and durability.
FDM Technology: FDM technology was chosen for its high compatibility with PC-FR, ensuring its properties were fully maintained and maximizing its performance.
Result
The collaboration resulted in significant improvements for the client’s supercapacitor systems:
Enhanced Component Performance: The 3D-printed pole insulators and support frames met all required specifications for insulation, strength, and flame retardancy.
Efficiency and Cost Savings: The FDM 3D printing process significantly reduced manufacturing time by eliminating the need for costly molds and tooling required in traditional manufacturing, allowing the client to meet tight development schedules.
Sustainability: The 3D printing process minimized material waste, aligning with their sustainability goals.
Customer Feedback
The client’s technical team expressed great satisfaction with the collaboration. They praised Unionfab for delivering high-quality, precise parts on time and under budget. The use of PC-FR material and FDM technology exceeded their expectations, providing a robust and efficient solution for their new supercapacitor system.