3003 Aluminum vs 6061 Aluminum
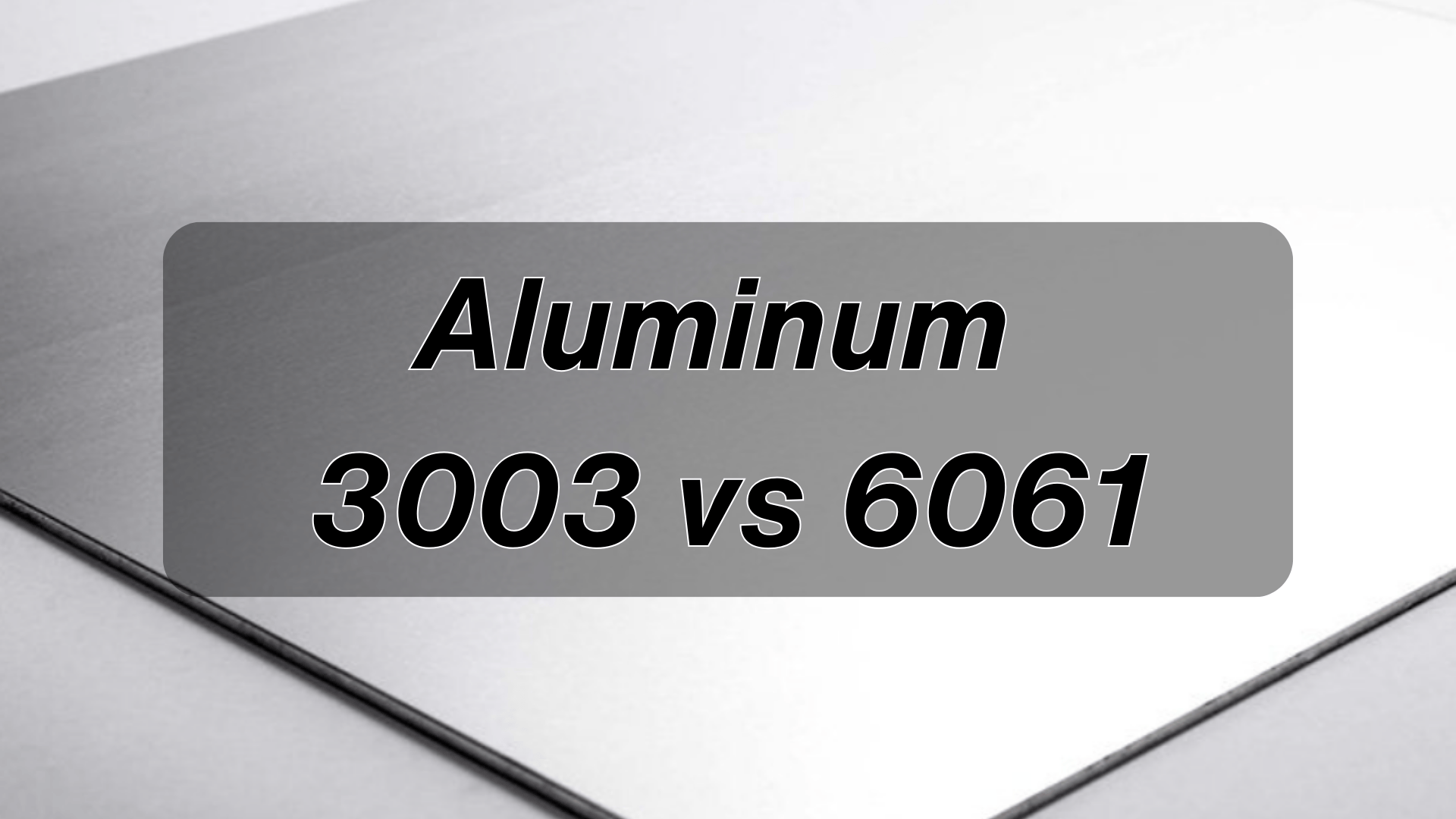
This article compares the main properties and applications of 3003 aluminum and 6061 aluminum in detail to help you make a wise choice.
Introduction
Aluminum 3003, due to its excellent corrosion resistance and formability, is often used for kitchen utensils
and HVAC systems. While, Aluminum 6061, with its higher strength and heat treatability, is the go-to choice for structural applications like aerospace components and automotive parts.
This article compares the chemical composition, physical properties, mechanical properties, and applications of 3003 and 6061 aluminum to help you make an informed choice.
Alloy Overview
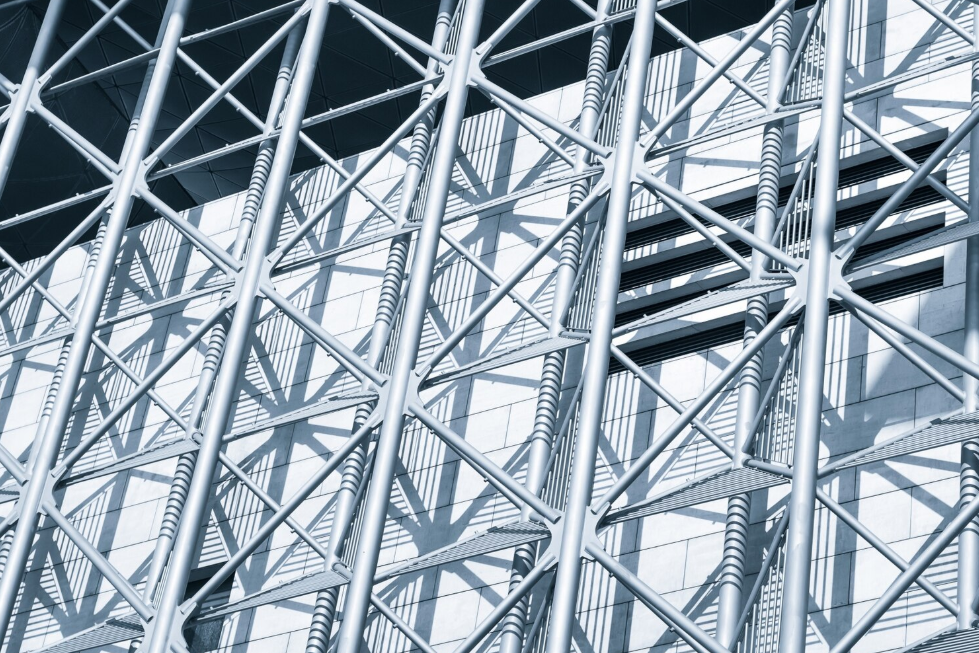
Aluminum alloys 3003 and 6061 each have distinct properties that make them suitable for different applications.
Below is a detailed overview of their compositions, key properties, and common uses:
3003 Aluminum
Composition: Primarily composed of 96.8% to 99% aluminum, with manganese as the main alloying element at 1.0% to 1.5%. It also contains small amounts of iron, silicon, copper, and zinc.
Key Properties:
Corrosion Resistance: Excellent due to its manganese content, making it resistant to moisture and chemicals.
Formability: Highly formable, supporting processes like bending, spinning, and deep drawing.
Weldability: Easily weldable using common arc welding methods.
Strength: Moderate strength, with ultimate tensile strength ranging from 110 MPa in the O condition to 152 MPa in the H14 temper.
Common Uses: Widely used in food and beverage containers, roofing, cooking utensils, and storage tanks due to its corrosion resistance and formability.
6061 Aluminum
Composition: Contains magnesium (0.8–1.2%) and silicon (0.4–0.8%) as primary alloying elements, along with small amounts of copper, chromium, and iron.
Key Properties:
Strength: Higher strength compared to 3003, with ultimate tensile strength up to 315 MPa in the T6 temper.
Heat Treatability: Can be heat-treated to improve mechanical properties.
Machinability: Excellent machinability, making it ideal for CNC machining and precision components.
Corrosion Resistance: Good corrosion resistance, especially in marine and industrial environments.
Common Uses: Commonly used in aerospace components, automotive parts, bicycle frames, and structural applications due to its high strength and machinability.
Summary
Aluminum 3003 is an excellent choice for applications requiring good corrosion resistance and formability at a lower cost, making it ideal for general-purpose uses. On the other hand, Aluminum 6061 is preferred for its higher strength, heat treatability, and machinability, despite its higher cost.
Advantages and Disadvantages
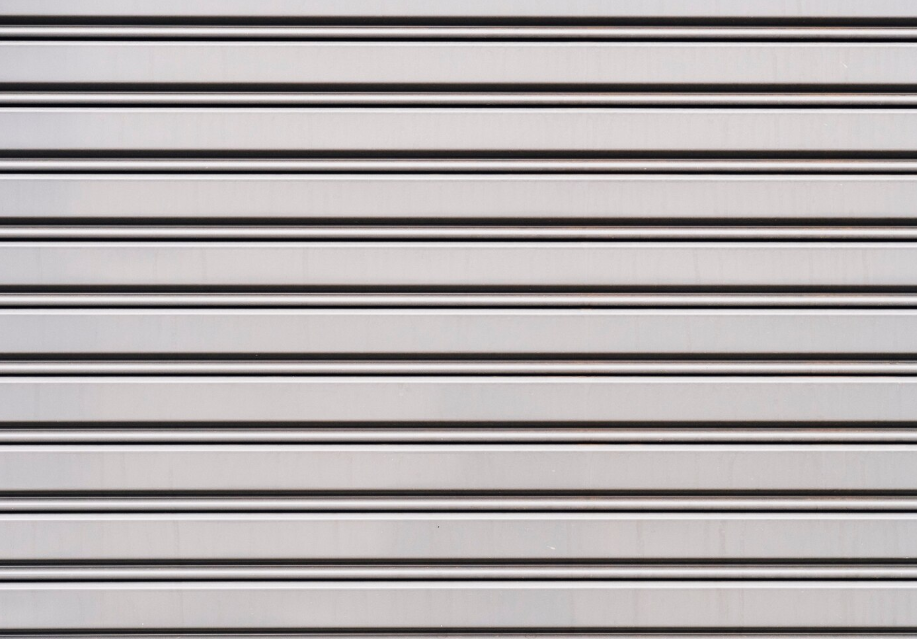
When it comes to selecting the right aluminum alloy for your project, understanding the advantages and disadvantages of different alloys is crucial. Aluminum 3003 and 6061 are two popular choices, each with distinct properties that make them suitable for various applications.
Below is a detailed comparison of their pros and cons.
Aluminum 3003
Pros:
Excellent corrosion resistance makes it ideal for environments exposed to moisture and chemicals.
Good formability allows it to be easily shaped into complex forms without special tools.
Excellent weldability with common arc welding methods, requiring no preheating.
Moderate strength sufficient for general-purpose applications, with cold working enhancing its strength.
Cost-effective due to simple processing without the need for heat treatment.
Cons:
Lower strength limits its use in high load-bearing structural applications.
Cannot be strengthened through heat treatment, relying instead on cold working.
Prone to peeling corrosion in cold-worked conditions, affecting appearance and performance.
Lower fatigue resistance makes it unsuitable for applications with repeated stress cycles.
Aluminum 6061
Pros:
High strength, especially in the T6 temper, ideal for structural components in various industries.
Excellent machinability for precision parts with tight tolerances and complex geometries.
Good weldability with methods like TIG and MIG, though post-weld heat treatment is recommended.
Heat treatable to enhance mechanical properties, providing greater strength and hardness.
Moderate corrosion resistance, improvable with surface treatments like anodizing.
Cons:
Higher cost due to alloying elements and heat treatment requirements.
Post-weld heat treatment adds complexity to the manufacturing process.
Often requires surface treatments to optimize corrosion resistance, increasing cost and processing time.
Lower formability compared to 3003, making it more challenging to shape into complex forms.
Summary
The choice between Aluminum 3003 and 6061 hinges on your project's needs. Opt for 3003 if cost, corrosion resistance, and formability are key, and high strength isn't required. Choose 6061 for higher strength and precision machining, accepting higher costs and complexity.
Consider factors like strength, corrosion resistance, machinability, and cost to make the best decision.
Key Performance Comparison
When selecting between 3003 and 6061 aluminum, it's crucial to understand their differing mechanical and physical properties, which make each alloy suitable for distinct applications.
Below is a detailed comparison of their key performance metrics:
Property | 3003 Aluminum | 6061 Aluminum |
---|---|---|
Tensile Strength | 120–160 MPa | 290 MPa (T651 temper) |
Yield Strength | ≥85 MPa | 240 MPa (T651 temper) |
Hardness | HB30–40 | HB95–110 |
Corrosion Resistance | Excellent (naturally resistant) | Moderate (requires surface treatment) |
Weldability | Excellent (no preheating needed) | Good (post-weld heat treatment recommended) |
Cost | Lower (due to simple processing) | Higher (heat treatment and alloying costs) |
Typical Thickness | Sheets (0.2–6.35 mm) | Sheets, extrusions, and forgings |
In summary
3003 aluminum is ideal for general-purpose applications needing good corrosion resistance and formability at a lower cost.
Conversely, 6061 aluminum is better for automotive and aerospace applications requiring higher strength and machinability, despite its higher cost and need for post-weld heat treatment.
Applications by Industry
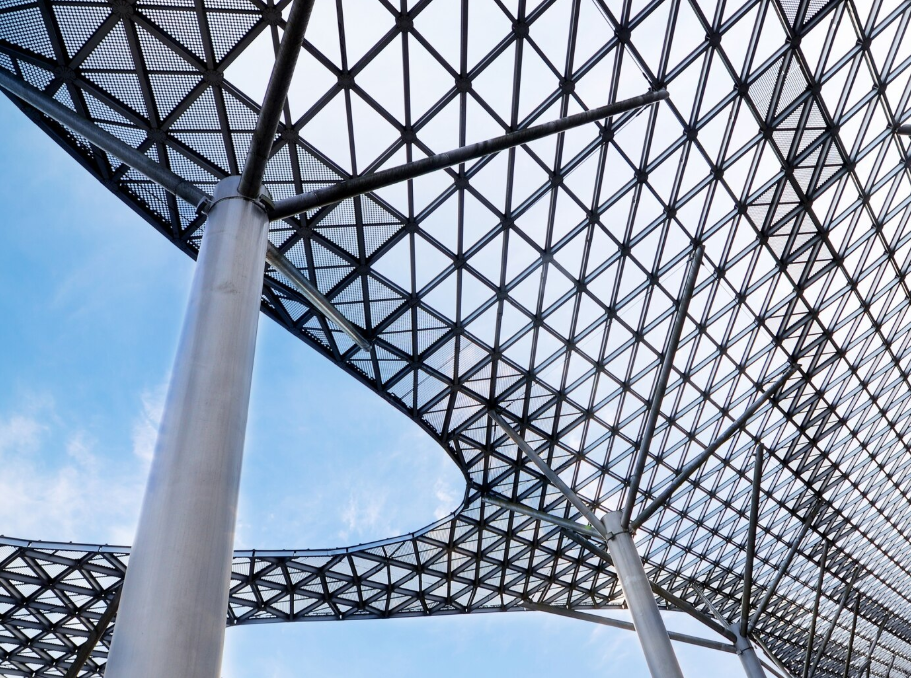
Aluminum alloys 3003 and 6061 find extensive applications across various industries due to their distinct properties.
Below is a detailed look at how each alloy is utilized:
Aerospace
3003 Aluminum: Due to its good formability and corrosion resistance, 3003 aluminum is used in non-structural components like fuel tanks and oil ducts.
6061 Aluminum: With higher strength and good machinability, it's widely used in aircraft wings, fuselage frames, and other crucial structural parts.
Automotive
3003 Aluminum: Its excellent corrosion resistance and formability make it suitable for fuel tanks, radiators, and interior components.
6061 Aluminum: Used in car frames, wheels, and engine components due to its high strength - to - weight ratio, contributing to improved fuel efficiency and performance.
Construction
3003 Aluminum: Commonly used for roofing, siding, and decorative panels due to its corrosion resistance and ease of forming.
6061 Aluminum: Utilized in structural components like beams and columns, as well as windows and doors, leveraging its higher strength.
Consumer Goods
3003 Aluminum: Found in kitchenware like pots and pans, leveraging its corrosion resistance and thermal conductivity.
6061 Aluminum: Used in electronics like laptop casings and smartphone frames due to its good machinability and aesthetics.
Industrial
3003 Aluminum: Used in low - stress components like storage tanks and conveyor systems due to its corrosion resistance and formability.
6061 Aluminum: Applied in machinery parts and structural components where higher strength and machinability are required. Also used in SLM 3D-printed tools/fixtures with complex geometries.
Conclusion
In conclusion, 3003 aluminum is ideal for general-purpose applications where corrosion resistance and formability are important. 6061 aluminum is better suited for structural and high-performance applications due to its higher strength and machinability.
Choosing the Right Alloy
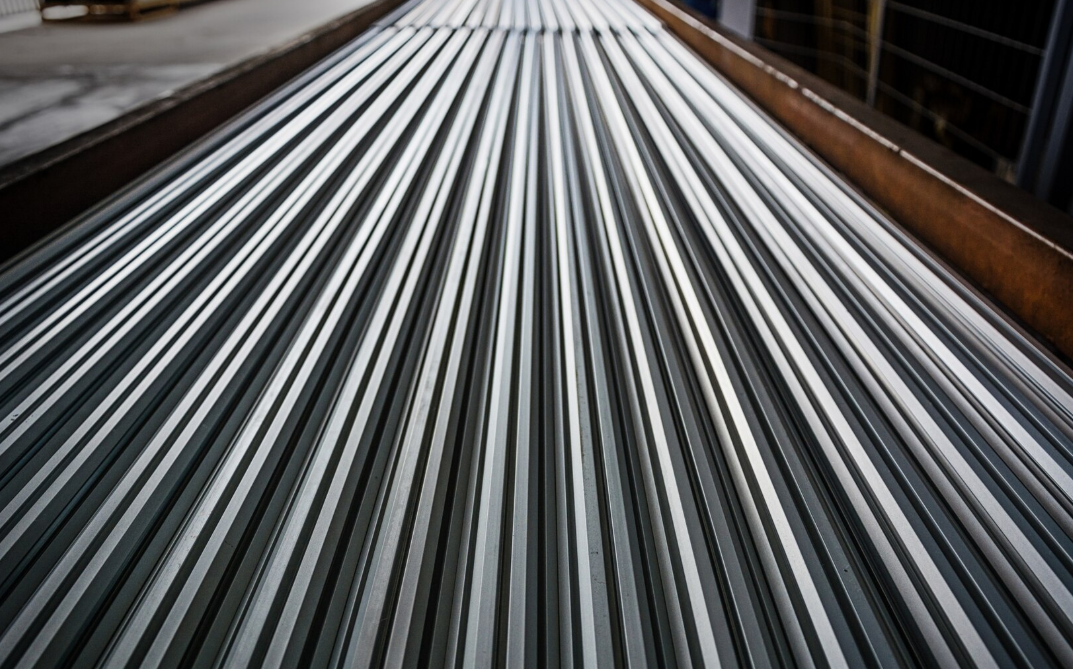
Selecting the appropriate aluminum alloy is crucial for the success of your project due to the varying properties and performance characteristics of each alloy.
Opt for 3003 Aluminum when:
Your project requires excellent corrosion resistance, especially in moist or chemically corrosive environments.
Good formability and weldability are essential for processes like bending, spinning, and arc welding.
Lower cost and simpler processing are priorities.
Applications include general-purpose uses like food and beverage containers, roofing materials, and low-stress industrial components.
Opt for 6061 Aluminum when:
Higher strength and a good strength-to-weight ratio are needed for structural support and performance - critical components.
Precision machining is required, leveraging its excellent machinability for accurate manufacturing.
Heat treatability is necessary to enhance mechanical properties.
Uses involve automotive parts, aerospace components, and high-precision consumer electronics.
Conclusion
The choice between 3003 and 6061 aluminum should be guided by your project's specific demands.
3003 aluminum is ideal for general-purpose applications with a focus on cost-effectiveness and corrosion resistance, while 6061 aluminum is better suited for high-strength, precision-machining needs despite its higher cost and more complex processing requirements.
Selecting the optimal aluminum alloy is crucial for your project's success. At Unionfab, we leverage cutting-edge aluminum alloys to bring your designs to life.
We offer key services such as CNC machining and precision finishing, ensuring your products surpass quality and performance standards.
Contact us today to learn how Unionfab can deliver tailored solutions and exceptional results.
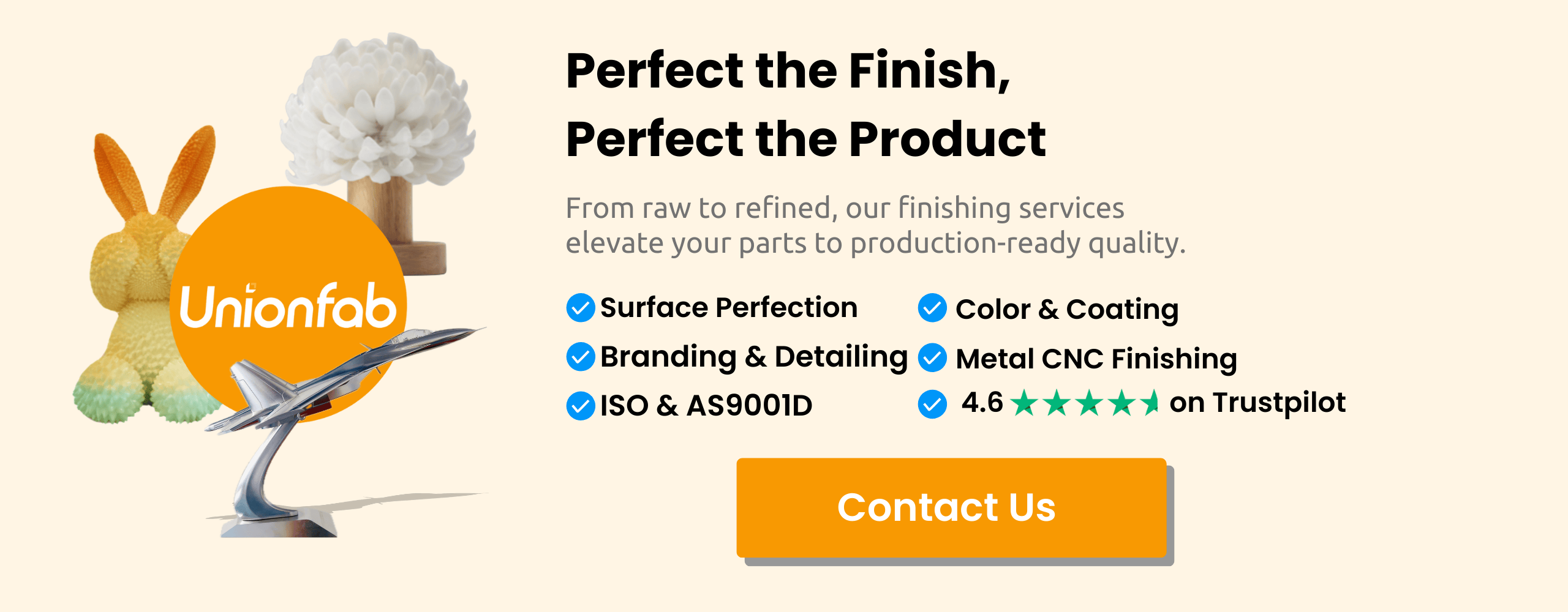
FAQs
What is the alternative to 3003 aluminum?
5052 Aluminum: A good alternative to 3003, offering higher strength and excellent corrosion resistance, especially in marine environments.
What is the strongest type of aluminum?
7075 Aluminum: Known for its exceptional strength-to-weight ratio, often compared to steel in terms of strength. Widely used in aerospace and high-performance applications.
What aluminum is stronger than 6061?
7075 Aluminum: Significantly stronger than 6061, with higher yield and tensile strengths. Suitable for high-stress applications like aircraft parts.
2024 Aluminum: Offers higher yield strength than 6061 and is commonly used in aircraft structures.