ASA vs ABS vs PETG vs PLA [+ Property Comparison]
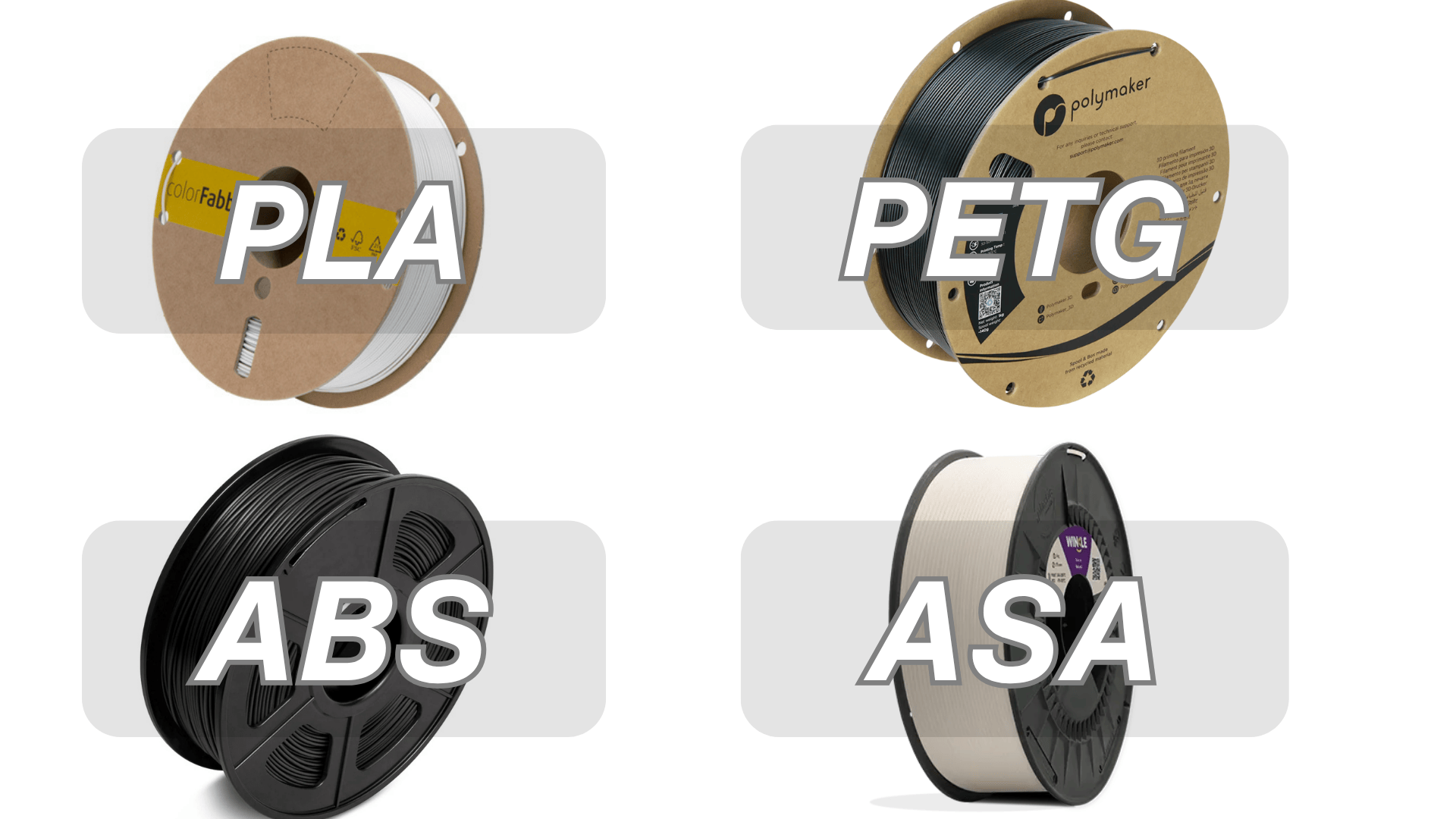
Compare ASA, ABS, PETG, and PLA. Discover their strengths, applications, and how to choose the right filament for 3d printing.
Overview: Getting to Know ASA, ABS, PETG, and PLA
In the world of thermoplastics, ASA, ABS, PETG, and PLA are among the most popular materials used for both 3D printing and traditional manufacturing. Each has unique characteristics that make it suitable for different applications, performance needs, and environments.
● ASA (Acrylonitrile Styrene Acrylate)
Known for its excellent UV and weather resistance, ASA is ideal for outdoor applications where durability and color stability are important.
● ABS (Acrylonitrile Butadiene Styrene)
A versatile and tough plastic, ABS offers strong impact resistance and heat tolerance, making it widely used in automotive parts and consumer products.
● PETG (Polyethylene Terephthalate Glycol)
PETG combines good strength, flexibility, and chemical resistance with ease of printing, making it a favorite for functional prototypes and clear or food-safe parts.
● PLA (Polylactic Acid)
Derived from renewable resources, PLA is prized for its ease of use, low printing temperature, and biodegradability, commonly used for visual prototypes and educational projects.
Together, these materials provide a broad toolkit for manufacturing needs, balancing strength, durability, printability, and environmental considerations.
Material Characteristics Breakdown and Comparison
When choosing a thermoplastic for manufacturing or product development, it’s important to understand the differences between common materials like PLA, ABS, PETG, and ASA. Each plastic has unique traits that make it suitable for everything from everyday products to tough, outdoor parts.
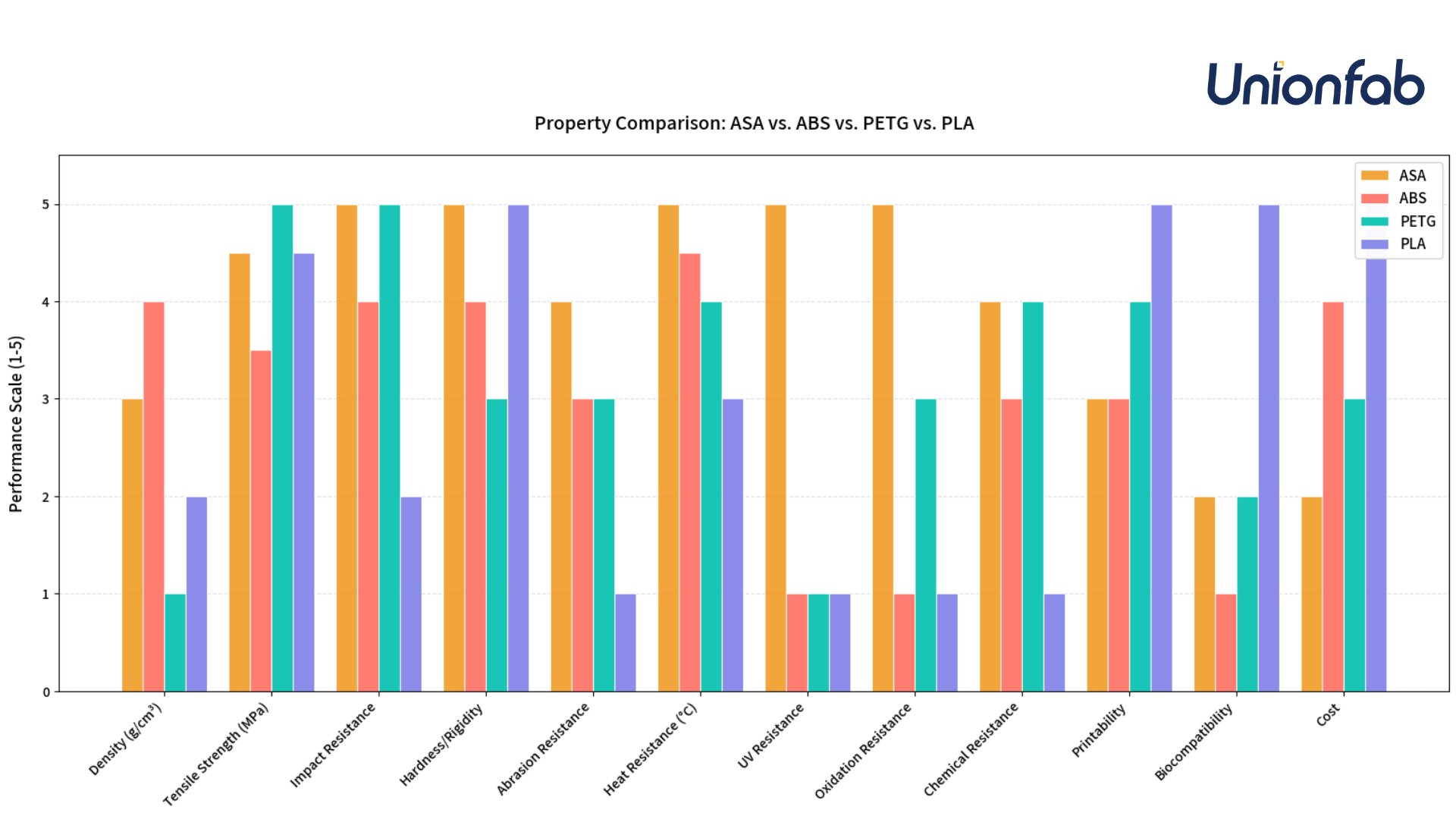
By comparing their core performance traits, one can better assess their suitability for various end-use environments and production methods.
Property | ASA | ABS | PETG | PLA |
---|---|---|---|---|
Density (g/cm³) | ~1.07 | ~1.04 | ~1.27 | ~1.24 |
Tensile Strength (MPa) | ~50–55 | ~40–50 | ~50–60 | ~45–60 |
Impact Resistance | High | Medium-High | High | Low-Medium |
Hardness / Rigidity | High (Shore D ~70) | Medium-High | Medium | High, but brittle |
Abrasion Resistance | Good | Moderate | Moderate | Poor |
Heat Resistance (°C) | ~90–100 | ~85–100 | ~75–85 | ~60 |
UV Resistance | Excellent | Poor | Poor | Poor |
Oxidation / Aging Resistance | High | Low | Medium | Low |
Chemical / Corrosion Resistance | Good | Moderate | Good | Low |
Printability | Moderate (needs enclosure) | Moderate (needs enclosure) | Easy | Very Easy |
Biocompatibility | Limited | No | Limited | Yes (food-safe grades) |
Cost | Medium-High | Low-Medium | Medium | Low |
Summary
Each material has specific strengths that make it ideal for certain scenarios:
● PLA is the easiest to print and eco-friendly, making it perfect for beginners, prototypes, and aesthetic models. However, it's weak against heat, UV, and chemicals.
● PETG balances strength and ease of use. It’s a strong, chemical-resistant option for mechanical parts but lacks UV resistance.
● ABS is tougher than PLA and better suited for functional prototypes, though it demands higher temperatures and a controlled print environment.
● ASA stands out for outdoor use thanks to its excellent UV and weather resistance. It offers a strong, durable alternative to ABS with better environmental stability.
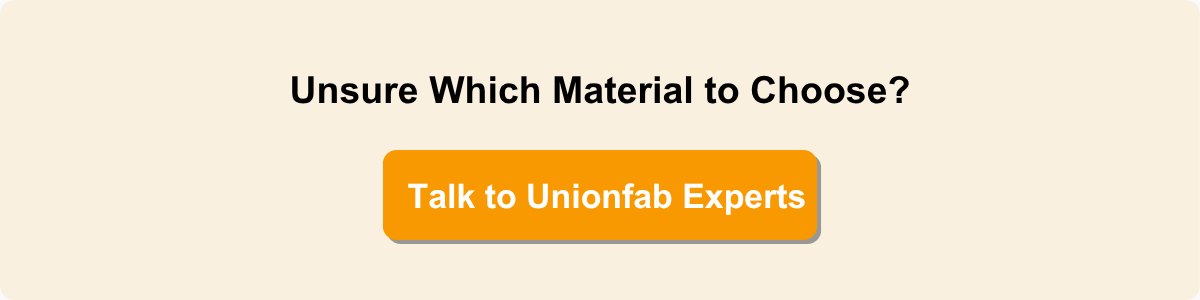
Primary Manufacturing Methods of ASA, ABS, PETG, and PLA
ASA, ABS, PETG, and PLA are popular thermoplastics used in both 3D printing and traditional manufacturing. When making final products—not just prototypes—it’s important to choose the right method based on quantity, performance, and cost.
These materials are mainly shaped using two methods: 3D printing and molding (including injection and extrusion molding).
1. 3D Printing (Additive Manufacturing)
All four materials—ASA, ABS, PETG, and PLA—are widely used in Fused Deposition Modeling (FDM), a popular 3D printing method that builds parts layer by layer using thermoplastic filament.
● PLA is especially favored for its ease of use, low printing temperature, and excellent surface finish.
● PETG offers a good balance of strength and printability, with better durability than PLA.
● ABS is strong and impact-resistant, but more challenging to print due to warping and fumes.
● ASA is similar to ABS but adds excellent UV and weather resistance, making it ideal for outdoor parts.
Use case: Rapid prototyping, custom one-off parts, low-volume functional parts.
2. Molding (Subtractive and High-Volume Manufacturing)
a. Injection Molding
Injection molding is a high-precision, high-volume process where molten plastic is injected into a mold cavity.
● ABS is one of the most widely used materials in injection molding due to its balance of toughness, machinability, and cost-effectiveness.
● ASA is preferred when outdoor durability and UV resistance are required, such as for automotive parts.
● PETG is used when clarity or chemical resistance is needed, especially in packaging or medical applications.
● PLA, while less common in injection molding due to its thermal limitations, is used in biodegradable products and compostable packaging.
Use case: Mass production of durable, repeatable parts with tight tolerances.
b. Extrusion Molding
Extrusion involves pushing molten plastic through a die to create continuous profiles such as pipes, sheets, and films.
● PETG is often extruded into clear sheets for packaging and signage.
● ABS is used in profiles and panels, offering toughness and ease of thermoforming.
● ASA is ideal for extruded outdoor applications like trims and signage due to its weather resistance.
● PLA can be extruded into films and sheets, especially for compostable products, though it is more brittle than other plastics.
Use case: Continuous production of semi-finished products like sheets, rods, tubes, and films.
Conclusion
When choosing the best manufacturing method for ASA, ABS, PETG, or PLA parts, consider your production volume, part performance, and cost.
● For rapid prototyping, custom designs, or low-volume runs, 3D printing offers flexibility and ease of iteration, with PLA and PETG being easiest to print, and ASA or ABS used when durability or weather resistance is needed.
● For high-volume, consistent-quality parts, injection molding is ideal—ABS and ASA excel for durable applications, while PETG suits clear or chemical-resistant parts, and PLA fits biodegradable needs.
● Extrusion molding is best for continuous profiles like sheets or films, where PETG, ABS, and ASA are preferred for their toughness and weatherability.
Selecting the right combination ensures efficient production and optimal part performance.
How to print with ASA, PLA, ABS, and PETG
Successfully printing with ASA, PLA, ABS, and PETG requires understanding each material’s unique properties and the best practices tailored to them. Factors such as the printing environment, temperature settings, bed adhesion methods, and fine-tuning can greatly influence the final print quality.
This part highlights key considerations and practical tips to help you achieve consistent and reliable results with these popular 3D printing filaments.
Workspace Considerations:
● ASA & ABS
Best printed in enclosed printers to maintain stable temperatures and reduce warping. Good ventilation is necessary to manage fumes.
● PLA & PETG
More tolerant of open environments; good airflow helps PLA cool properly, while PETG benefits from moderate cooling.
Optimal Extrusion and Bed Temperatures:
● PLA: Extrude at 190–220°C; bed at 50–60°C.
● ABS: Extrude at 230–260°C; bed at 90–110°C.
● ASA: Similar to ABS, extrusion at 240–260°C; bed at 90–110°C.
● PETG: Extrude at 230–250°C; bed at 70–80°C.
Bed Surface and Adhesion Strategies:
● PLA: Blue painter’s tape, PEI sheets, or glue stick for reliable adhesion.
● ABS & ASA: Use ABS slurry, Kapton tape, or textured PEI sheets for better grip.
● PETG: PEI sheets or glass beds with a light glue stick layer prevent excessive sticking.
Tuning and Calibration Tips:
● ASA & ABS: Use slower print speeds, minimal cooling fans, and ensure precise bed leveling to avoid warping and cracking.
● PLA: Print faster with active cooling fans for crisp detail.
● PETG: Balance fan speed and print speed carefully to reduce stringing and improve layer bonding.
Finishing and Detailing Techniques
Finishing is an important step that turns 3D prints into smooth, usable parts. Materials like ASA, ABS, PETG, and PLA each need different methods for support removal, surface smoothing, and coloring. Heat treatment and annealing can also improve strength and durability.
Understanding the best practices for each material ensures high-quality results and maximizes the potential of your prints.
Support Cleanup and Removal
After printing, removing supports cleanly is crucial for a smooth finish. For ASA, ABS, PETG, and PLA, supports can be carefully clipped or snapped off with pliers or cutters.
Using soluble supports (like PVA with dual extrusion printers) can simplify cleanup for complex geometries. Sanding the contact points where supports attached helps achieve a seamless surface.
Surface Smoothing Methods
Each material responds differently to smoothing techniques:
● ABS and ASA: Can be vapor-smoothed using acetone or specialized solvents to achieve glossy, smooth surfaces by melting the outer layer.
● PLA: Generally not suitable for vapor smoothing; instead, sanding and applying filler primers work best.
● PETG: Can be lightly sanded but tends to be more scratch-resistant; careful polishing or filler application is recommended.
Painting, Dyeing, and Color Finishing
Painting can enhance aesthetics and add protective layers:
● PLA and ABS: Accept a wide range of paints (acrylics, spray paints) after proper surface preparation (sanding and priming).
● ASA: Paints adhere well, especially after acetone smoothing, making it ideal for outdoor or durable color finishes.
● PETG: Requires surface cleaning and priming for best paint adhesion; dyeing is less common but possible with specialized methods.
Heat Treatment and Annealing Guidelines
Annealing improves strength and heat resistance by heating printed parts below their melting point:
● PLA: Annealing can significantly increase thermal stability but may cause dimensional changes or warping.
● ABS and ASA: Respond well to annealing with minimal deformation, improving toughness.
● PETG: Less commonly annealed due to its already good heat resistance; careful temperature control is needed to avoid distortion.
Summary:
To achieve the best finish for your 3D prints, match your post-processing approach to the material. Use soluble supports for complex prints and sand contact areas for cleaner results.
Surface Smoothing:
ABS & ASA: Vapor smoothing works best.
PLA & PETG: Sanding and priming are more effective.
Painting:
Always prep surfaces before painting (especially PETG).
Strength & Heat Resistance:
Consider annealing to improve durability.
Pro Tip:
Test on sample prints first to avoid damaging the final part.
Use Cases of ASA, PLA, ABS, and PETG in 3D Printing
While ASA, PLA, ABS, and PETG are widely used in various manufacturing processes such as injection molding, their behavior and suitability can differ significantly when used in 3D printing, particularly FDM (Fused Deposition Modeling). The unique thermal and mechanical constraints of FDM require careful material selection based on application type, printability, and post-processing needs.
Below are the primary application types where these materials excel specifically in 3D printing contexts:
1. Aesthetic and Concept Models
Ideal for: Visual Prototypes, Display Models, Figurines, Architectural Models
● PLA is the go-to material here thanks to its excellent surface finish, wide color availability, and ease of use.
● PETG and ASA may also be used if slight durability or weather-resistance is needed for outdoor displays.
● ABS is less common in this category due to warping and surface quality challenges without post-processing.
2. Functional Prototyping
Ideal for: Fit Testing, Mechanical Interfaces, Design Iterations
● ABS and PETG are widely used for their good mechanical properties and dimensional stability.
● ASA is preferred when UV or weather exposure is part of the testing conditions.
● PLA is occasionally used for non-functional prototypes where strength is not critical.
3. End-Use Custom Parts
Ideal for: Tooling Aids, Mounts and Brackets, Housing Enclosures, Low-Volume Production
● PETG and ASA offer strength and durability with better chemical and environmental resistance, making them suitable for low-run, customized functional parts.
● ABS remains popular due to its balance between strength and cost, especially for indoor parts.
● PLA is typically avoided for long-term or load-bearing parts due to its brittleness and low heat resistance.
4. Outdoor and Weather-Exposed Applications
Ideal for: Outdoor Fixtures, Signage, Protective Covers, Garden Tools
● ASA is the top choice due to its outstanding UV resistance, weather durability, and color retention over time.
● PETG can be a secondary option but may degrade faster under UV exposure.
● PLA and ABS are not recommended unless treated or coated post-printing.
5. Educational and Learning Projects
Ideal for: STEM Projects, 3D Printing Training, DIY Kits
● PLA dominates in education due to its low cost, safety (biocompatibility and no toxic fumes), and ease of printing.
● PETG is used for more advanced learners who require stronger, slightly more durable prints.
● ABS and ASA are less common due to the need for controlled printing environments and potential fumes.
6. Functional Assemblies and Moving Mechanisms
Ideal for: Hinges, Gears, Snap-fit Components, Prototypes with Assembly Features
● ABS offers great performance in parts requiring friction fits and mechanical stress.
● PETG provides flexibility and durability, useful for snaps and light bearings.
● ASA is a strong contender when outdoor mechanical parts are involved.
● PLA can be used for low-stress mechanisms but is prone to wear and fracture.
Summary
Each of the four materials—ASA, PLA, ABS, and PETG—has its strengths and limitations in the context of 3D printing.
PLA excels in aesthetic applications and education due to its ease of use and safety.
ABS and PETG are go-to choices for functional parts and assemblies that require mechanical performance and durability.
ASA stands out in outdoor and UV-exposed applications thanks to its superior weather resistance.
Decision Factors for Filament Selection
Choosing the right filament goes beyond comparing technical specs—it requires balancing performance requirements, equipment capabilities, and cost considerations.
PLA, ABS, PETG, and ASA each bring distinct strengths and trade-offs, so aligning material choice with your specific needs will ensure successful prints and efficient workflows.
Evaluating Application Needs
Start by defining what the printed part needs to achieve. Consider the following questions:
Will the part be load-bearing or structural? → PETG, ABS, and ASA offer greater strength and durability than PLA.
Is the part for indoor or outdoor use? → ASA excels in UV and weather resistance, while PLA and ABS degrade faster without protective coatings.
Does the part require fine detail or a smooth finish? → PLA provides excellent detail out of the box, while ABS and ASA benefit from post-processing like vapor smoothing.
Is biodegradability or environmental safety a concern? → PLA is compostable and made from renewable resources, ideal for eco-conscious applications.
Choosing based on the part's functional, aesthetic, and environmental demands helps narrow down the most appropriate material.
Printer Compatibility and Limitations
Not all printers handle all materials equally. Assess your printer’s features before committing to a filament:
Enclosure: Needed for ABS and ASA to prevent warping from temperature fluctuations.
Heated Bed: Essential for ABS, ASA, and PETG to improve adhesion and prevent curling.
Ventilation or Filtration: Important for ABS and ASA, which emit fumes during printing.
Extruder Temperature Range: Your hotend must reach the higher temperatures required by ABS, ASA, and PETG (typically over 230°C).
Build Surface: Consider compatibility with your material—for example, PEI works well with PETG and PLA, but ABS might need slurry or tape.
Matching filament to your printer's capabilities avoids print failures and reduces unnecessary troubleshooting.
Cost-Effectiveness and Material Efficiency
Beyond the price per spool, consider the total value a filament brings to your application:
PLA is the most affordable and easiest to print, making it ideal for prototypes and educational use.
ABS is cost-effective for functional parts but requires a controlled environment and more post-processing.
PETG offers a good strength-to-price ratio and minimal warping, making it efficient for functional parts without enclosure requirements.
ASA is generally more expensive, but its weather resistance can offset costs in outdoor or high-durability applications.
Evaluate not just material price, but waste, print success rate, and post-processing needs when calculating total cost.
Final Thought (Summary)
PLA: Best for easy, fast prototypes.
PETG: Good for strong, functional parts.
ABS: Ideal when strength and machinability matter.
ASA: Great for high-performance outdoor use.
Check your printer’s compatibility before choosing a material.
Consider overall material efficiency, not just initial cost, for sustainable printing.
Expand Your Printing Potential with Unionfab
Ready to take your prints to the next level? Unlock the full capabilities of industrial-grade FDM 3D printing with Unionfab.
Unionfab is China's largest 3D printing manufacturing company, specializing in rapid prototyping and on-demand production. We boast four key strengths: experience, certification, shipping, and cost.
Experience: With 100 3D printers and 20+ years' experience in 3D printing.
Quality Assurance: Certified to the strict ISO 9001 quality management standards.
Fast Shipping: Air shipments in 3-5 days via DHL Express and FedEx.
Competitive Pricing: Up to 70% cheaper than European and American competitors without compromising on quality.
If you are looking for 3d printing service and want to estimate the cost of your project, feel free to use our online free cost calculator for an instant quote.
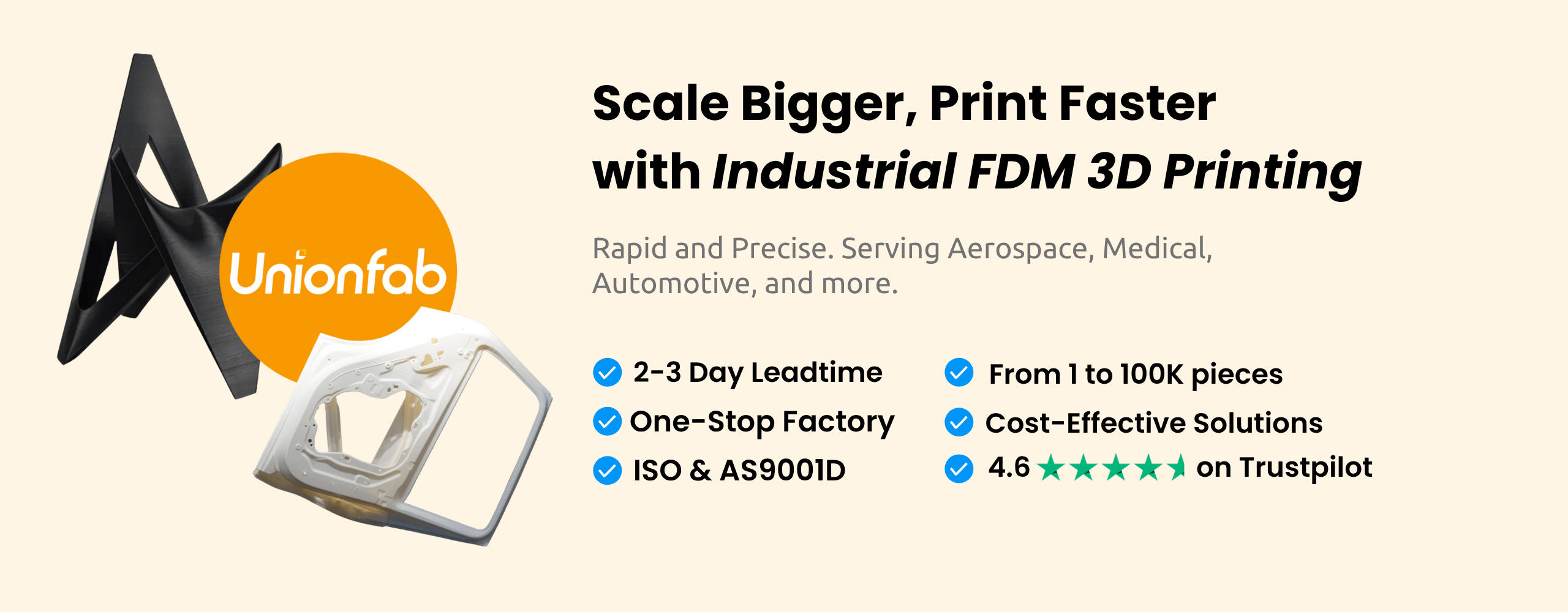
FAQs
What is the disadvantage of ASA filament?
ASA offers excellent UV and weather resistance, but its drawbacks include a higher tendency to warp compared to PLA or PETG, requiring a fully enclosed printer for best results. It also emits fumes during printing, necessitating proper ventilation, and is more difficult to post-process than PLA.
Does ASA need a hardened nozzle?
No, ASA does not require a hardened nozzle. It is not abrasive like carbon fiber- or glass-filled filaments. A standard brass nozzle is sufficient for printing pure ASA filament.
Does ASA absorb moisture?
Yes, ASA is moderately hygroscopic, meaning it can absorb moisture from the air over time. While not as moisture-sensitive as materials like nylon, drying ASA before printing is recommended if it's been exposed to humid environments to avoid issues like popping, bubbling, or poor layer adhesion.