A Complete Guide to Inconel 718 [+ Datasheet]
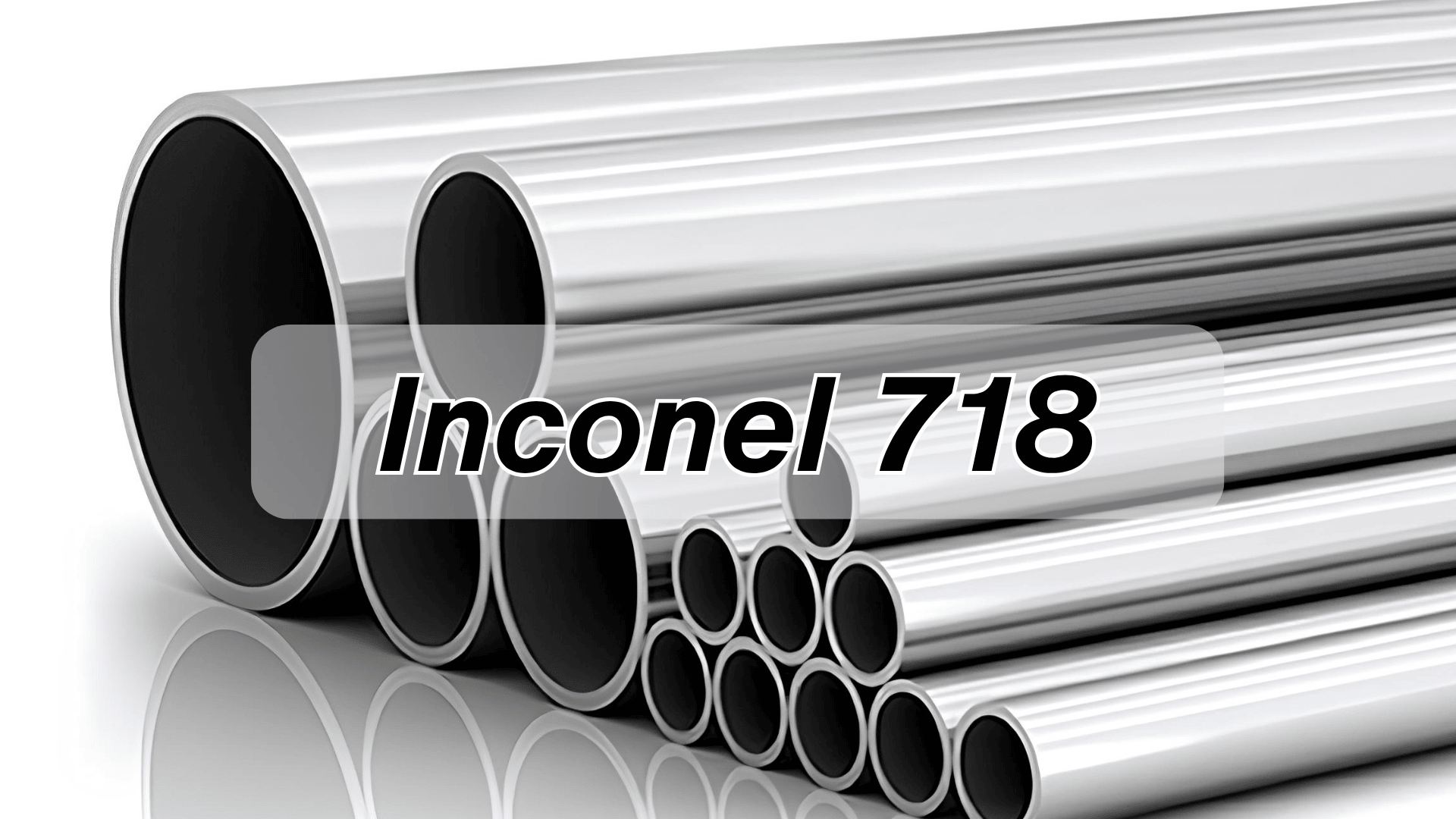
Explore the properties, manufacturing methods and uses of Inconel 718 with datasheet insights—perfect for engineers and 3D printing professionals!
What is Inconel 718?
Inconel 718 is a high-performance, nickel-based superalloy designed for strength, corrosion resistance, and stability at high temperatures.
It is precipitation-hardenable, meaning it gains strength through a heat treatment process, and is known for its excellent fatigue resistance, creep resistance, and weldability. These properties make it ideal for use in demanding industries such as aerospace, energy, and oil & gas.
Development of Inconel 718
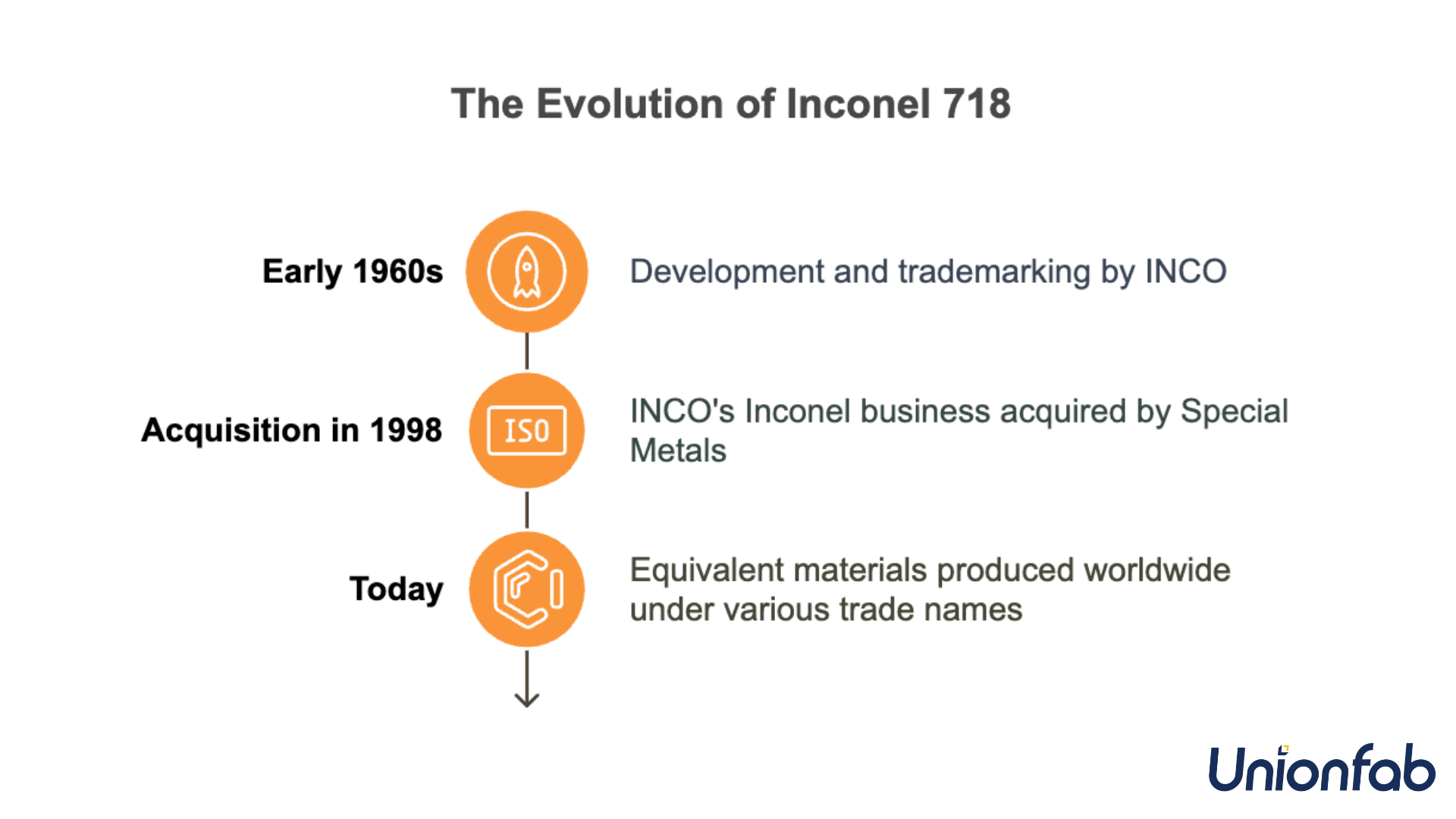
Inconel 718 was originally developed and trademarked by INCO (International Nickel Company) in the early 1960s to meet the demand for a high-strength, corrosion-resistant alloy for aerospace applications.
INCO’s Inconel business was later acquired by Special Metals, which now owns and maintains the INCONEL® trademark.
Today, Inconel 718 remains a registered trademark of Special Metals, but equivalent materials are produced globally under different trade names. Common equivalents include ATI 718, Haynes 718, Nicrofer® 5219 Nb (VDM Metals), Carpenter 718, and GH4169 (China).
Inconel 718 Composition
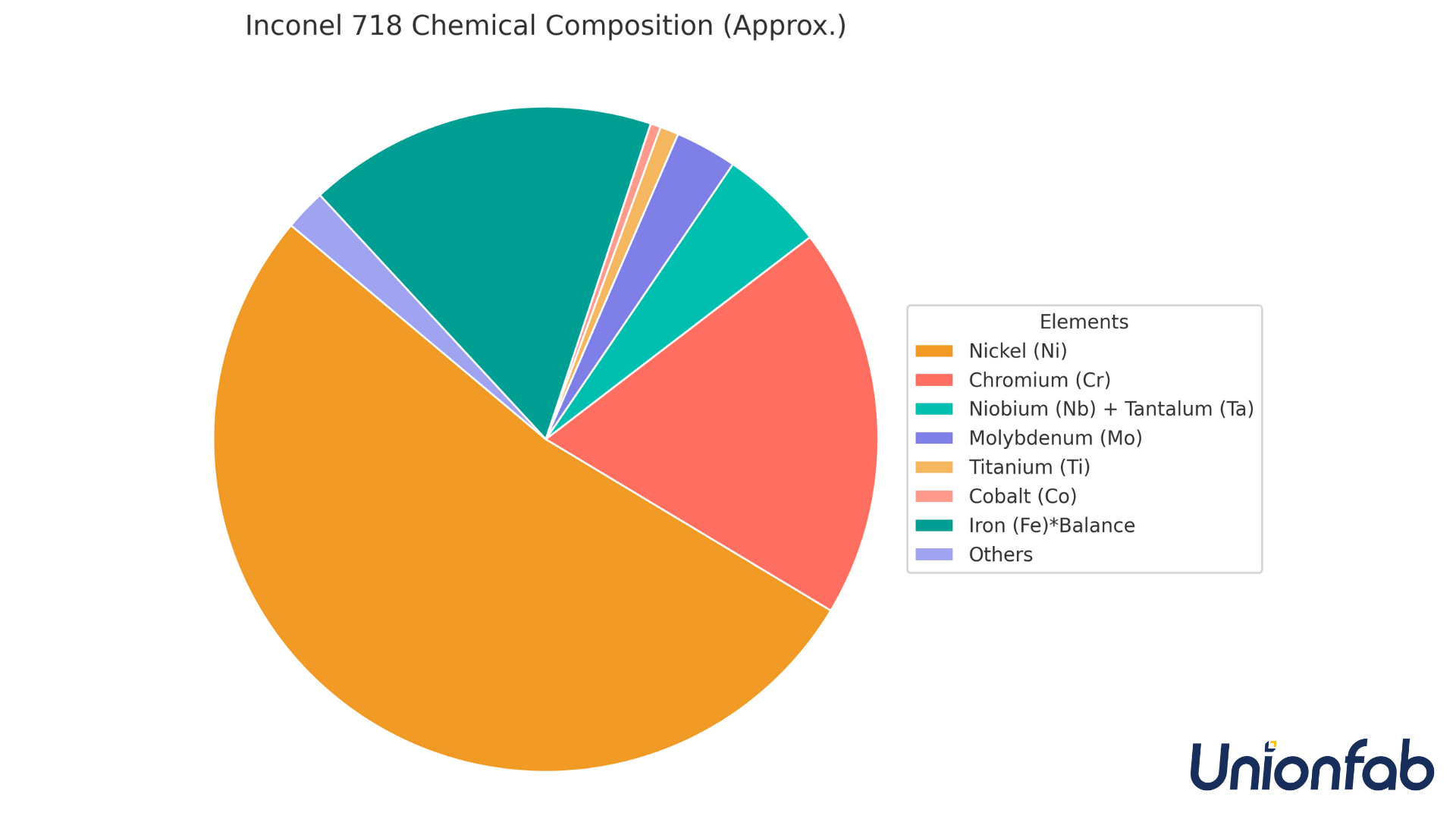
The excellent performance of Inconel 718 in extreme conditions comes from a carefully designed chemical composition that allows it to stay strong at high temperatures and resist wear.
The table below shows the typical elements it contains and how each one helps it work.
Element | Content (wt.%) | Function / Role |
---|---|---|
Nickel (Ni) | 50–55% | Base metal; provides corrosion resistance and strength |
Chromium (Cr) | 17–21% | Enhances oxidation and corrosion resistance |
Iron (Fe) | *Balance | Matrix element; adds structural integrity |
Niobium (Nb) + Tantalum (Ta) | 4.75–5.50% | Precipitation hardening (strengthening phase) |
Molybdenum (Mo) | 2.80–3.30% | Improves high-temperature strength |
Titanium (Ti) | 0.65–1.15% | Aids in precipitation hardening |
Aluminum (Al) | 0.20–0.80% | Strengthens alloy with Ti |
Cobalt (Co) | ≤ 1.0% (typical) | Optional; may improve hot strength |
Manganese (Mn) | ≤ 0.35% | Deoxidizer; improves hot working properties |
Silicon (Si) | ≤ 0.35% | Improves oxidation resistance |
Carbon (C) | ≤ 0.08% | Increases strength, but must be limited |
Sulfur (S) | ≤ 0.015% | Impurity; must be minimized |
Phosphorus (P) | ≤ 0.015% | Impurity; must be minimized |
Boron (B) | ≤ 0.006% | Enhances grain boundary strength |
Copper (Cu) | ≤ 0.30% | Usually residual |
*Balance: the remaining amount to reach 100%, after all other specified elements.
Inconel 718 Properties
Inconel 718 is known for its excellent balance of mechanical strength, heat resistance, and corrosion performance. The table below highlights its typical properties across key performance areas.
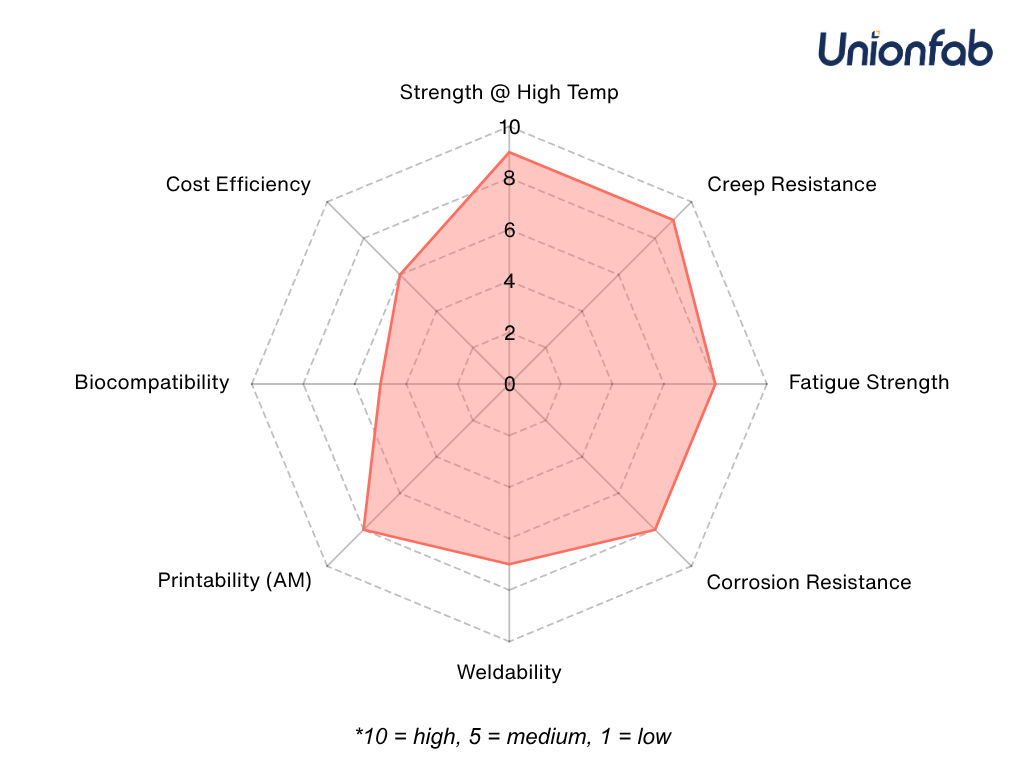
Property | Typical Value / Range | Description |
---|---|---|
Density | ~8.19 g/cm³ | relatively heavy but structurally strong; important for structural and weight-sensitive applications. |
High-Temperature Strength | Tensile: ~1240 MPa (at room temp) | Maintains excellent mechanical strength even at elevated temperatures. |
Creep Resistance | Stress rupture life: >1000 hrs at 650 °C / 690 MPa | Resists deformation under long-term high heat and load. |
Fatigue Resistance | ~450 MPa (10⁷ cycles at RT) | High fatigue strength makes it suitable for rotating and vibrating parts. |
Corrosion & Oxidation Resistance | Oxidation resistance up to ~980 °C | Excellent chemical stability in harsh conditions. |
Weldability | Good – suitable for TIG, laser welding | Better weldability than many nickel-based alloys. |
Printability (Additive Manufacturing) | High – especially in PBF & DED | Supports complex geometries with good dimensional stability. |
Biocompatibility | Moderate – ISO 10993 compliant (for non-implants) | Safe for short-term body contact; not for permanent implants. |
Cost | ~$50–100/kg (raw powder or bar stock) | More affordable than some high-end superalloys, but pricier than steels. |
Key Takeaways:
High strength even at high temperatures (up to 700 °C)
Excellent creep and fatigue resistance for long-term durability
Outstanding corrosion & oxidation resistance, ideal for harsh environments
Good weldability and high printability, suitable for additive manufacturing
Biocompatible for short-term body contact (non-implant use)
For detailed property data about Inconel 718, you can download the data sheet from Special Metal: https://www.specialmetals.com/documents/technical-bulletins/inconel/inconel-alloy-718.pdf
Inconel 625 vs. Inconel 718 vs. Haynes 282
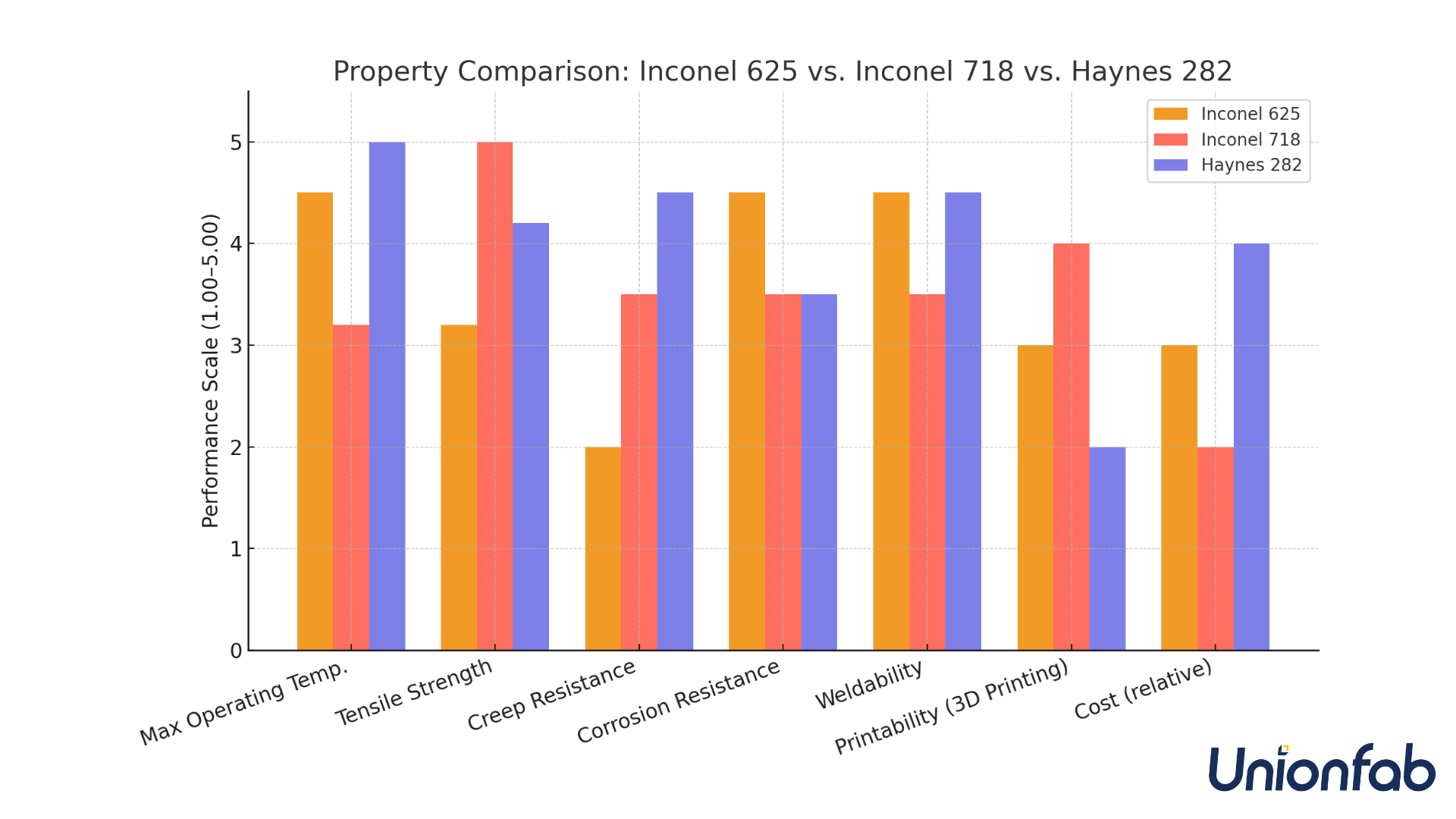
On top of Inconel 718, Inconel 625 and Haynes 282 are two other widely used nickel-based superalloys, each designed for demanding environments but optimized for different performance needs.
The following comparison highlights their key properties, helping you choose the right material for specific high-temperature or corrosive applications.
Property / Feature | Inconel 625 | Inconel 718 | Haynes 282 |
---|---|---|---|
Main Strength | Excellent corrosion resistance | High strength + good corrosion resistance | High-temperature strength + stability |
Strengthening Mechanism | Solid solution | Precipitation hardening (Nb/Ti) | Precipitation hardening (γ′ phase) |
Max Operating Temp. | ~980 °C | ~700 °C | ~1050 °C |
Tensile Strength | ~827 MPa | ~1240 MPa (RT) | ~930 MPa (RT); >800 MPa at 870 °C |
Creep Resistance | ⭐️⭐️ | ⭐️⭐️⭐️ | ⭐️⭐️⭐️⭐️ (Excellent up to 1050 °C) |
Corrosion Resistance | ⭐️⭐️⭐️⭐️ | ⭐️⭐️⭐️ | ⭐️⭐️⭐️ |
Weldability | ⭐️⭐️⭐️⭐️ | ⭐️⭐️⭐️ | ⭐️⭐️⭐️⭐️ |
Printability (3D Printing) | ⭐️⭐️⭐️ | ⭐️⭐️⭐️⭐️ | ⭐️ |
Cost (relative) | ⭐️⭐️⭐️ | ⭐️⭐️ | ⭐️⭐️⭐️⭐️ |
Typical Applications | Marine, chemical processing, aerospace | Aerospace, power, nuclear, tooling | Gas turbines, hot section aerospace parts |
How to Choose?
Inconel 625: Best for corrosion resistance, especially in aggressive environments. Not as strong as 718/282.
Inconel 718: Best strength-to-cost ratio, widely used in aerospace and AM (additive manufacturing).
Haynes 282: Best for sustained high-temperature performance, designed for next-gen turbines.
If you’d like to learn more about nickel-based alloys, feel free to read our previous article:
Monel vs. Inconel vs. Incoloy vs. Hastelloy
Inconel vs. Titanium vs. Stainless Steel
Primary Manufacturing Methods of Inconel 718
Inconel 718 can be processed through a variety of manufacturing methods, each suited to different part geometries, performance requirements, and production volumes.
Below are the most common approaches and the typical material forms they use:
1. Conventional Machining (Subtractive Manufacturing)
Material form: Bar stock, billet, or forging
Used when precision is critical and production volumes are moderate to low.
Requires high-performance tools due to Inconel 718’s work-hardening and toughness.
Common for aerospace fasteners, components with tight tolerances, and repair parts.
2. Forging + Heat Treatment
Material form: Ingot, billet
Suitable for high-strength, high-integrity components like turbine disks and structural parts.
Involves hot forging followed by solution treatment and aging to develop desired properties.
Offers superior grain structure and fatigue resistance.
3. Powder Metallurgy (PM) + HIP (Hot Isostatic Pressing)
Material form: Inconel 718 powder
Produces near-net-shape or net-shape parts with excellent microstructural control.
Often combined with HIP to achieve full density and mechanical strength.
Used in aerospace, nuclear, and medical sectors for high-performance applications.
4. Additive Manufacturing (3D Printing)
Material form: Pre-alloyed powder (typically gas atomized)
Technologies: Laser Powder Bed Fusion (LPBF), Directed Energy Deposition (DED)
Enables the production of complex geometries with minimal waste.
Increasingly used in aerospace, tooling, and customized medical parts.
5. Casting (Vacuum or Investment Casting)
Material form: Ingot or melt
Suitable for producing large or complex components in medium to large batches.
Requires precise control to avoid segregation and cracking.
Common in turbine casings and pump bodies.
Inconel 718 3D Printing
Inconel 718 is one of the most widely used superalloys in metal additive manufacturing due to its excellent strength, corrosion resistance, and suitability for complex geometries. It is especially well-suited for high-value aerospace, energy, and tooling applications that demand both performance and geometric freedom.
PBF vs. DED for Inconel 718
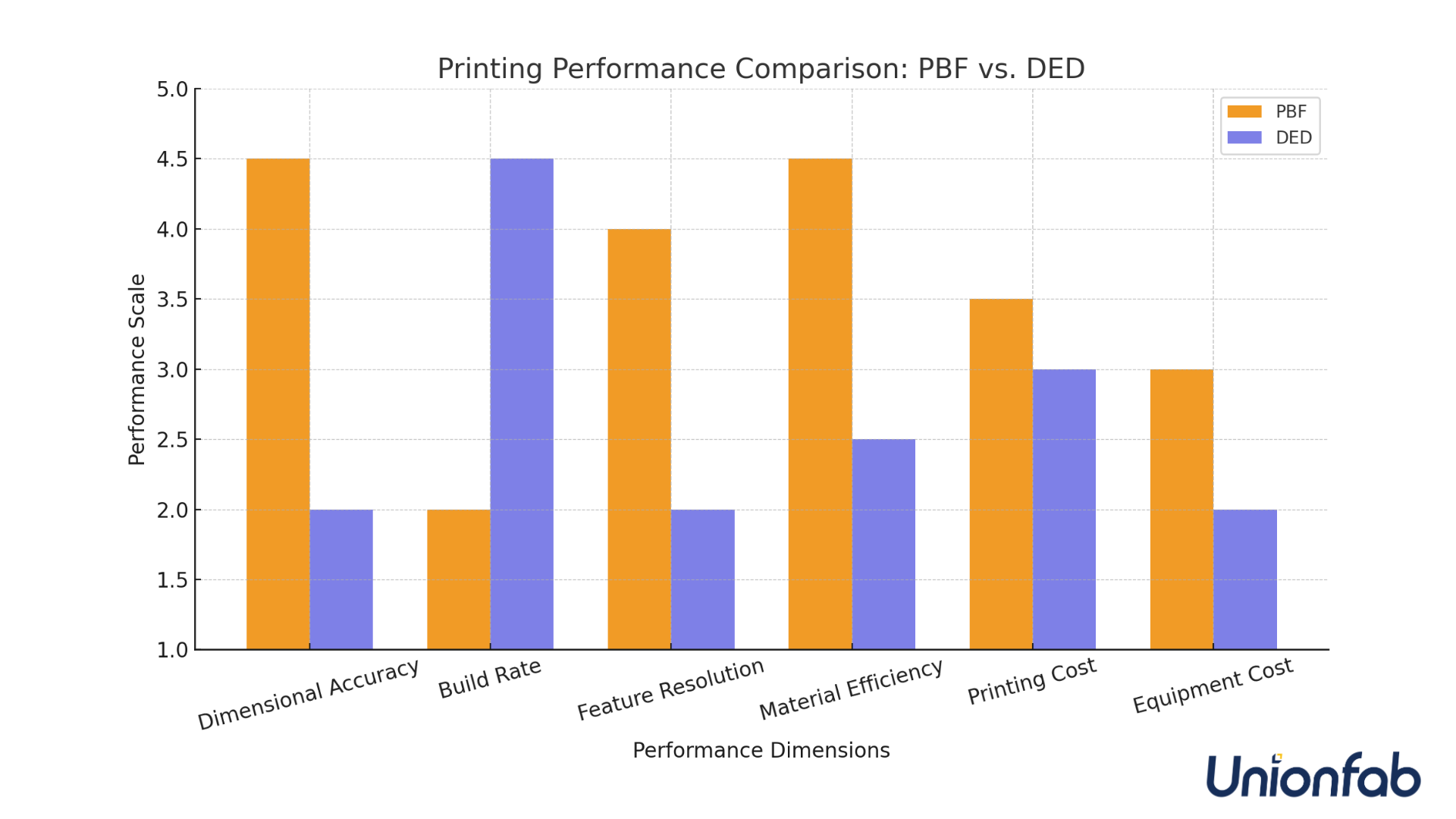
PBF and DED are the two common 3d printing processes applicable for Inconel 718. To better understand how they performs, we have made a comparison table to highlight their differences in different dimensions.
Feature | PBF (Powder Bed Fusion) | DED (Directed Energy Deposition) |
---|---|---|
Widely-applied Techniques | SLM, DMLS | LENS |
Material Form | Pre-alloyed powder | Powder or wire |
Dimensional Accuracy | ⭐⭐⭐⭐ (High precision) | ⭐⭐ (Moderate) |
Build Rate | ⭐⭐ (Slow) | ⭐⭐⭐⭐ (Fast) |
Feature Resolution | ⭐⭐⭐⭐ (Good for fine details) | ⭐⭐ (Coarse features) |
Post-Processing Needs | Requires support removal and heat treatment | Requires machining and heat treatment |
Material Efficiency | ⭐⭐⭐⭐ (High; unused powder recyclable) | ⭐⭐ (Lower; more overspray/waste) |
Printing Cost | ⭐⭐ (Powder is costly but efficient) | ⭐⭐⭐ (Wire may be cheaper, but waste and complexity increase cost) |
Equipment Cost | ⭐⭐⭐ (Moderate) | ⭐⭐ (Can vary; often higher for industrial systems) |
Best Suited For | Intricate geometries, small-to-medium parts | Large parts, repair, or adding material to existing components |
Typical Applications | Aerospace engine components, medical implants | Turbine blade repair, structural aerospace components |
Key Considerations in 3D Printing Inconel 718
Printability: Inconel 718 shows very good printability, especially in PBF, due to its favorable thermal and metallurgical behavior.
Post-Processing: Requires stress relief, hot isostatic pressing (HIP), and aging heat treatment to achieve full mechanical properties.
Microstructure Control: Careful process parameter tuning is needed to avoid defects like cracking or porosity, especially in thicker sections.
Advantages of Using Inconel 718 in Additive Manufacturing
Enables design freedom for complex cooling channels, lightweight structures, and topologically optimized parts.
Allows for rapid prototyping and part customization in aerospace and energy industries.
Reduces material waste compared to subtractive manufacturing of expensive superalloys.
For more details about inconel 3d printing, read our previous article: Guide to inconel 3d printing.
If you have Inconel 3D printing needs but are unsure which material or technique to choose, feel free to contact Unionfab. Compared to our Western counterparts, our Inconel-equivalent materials are 3 to 5 times more affordable, and 3D printing costs can be up to 70% lower.
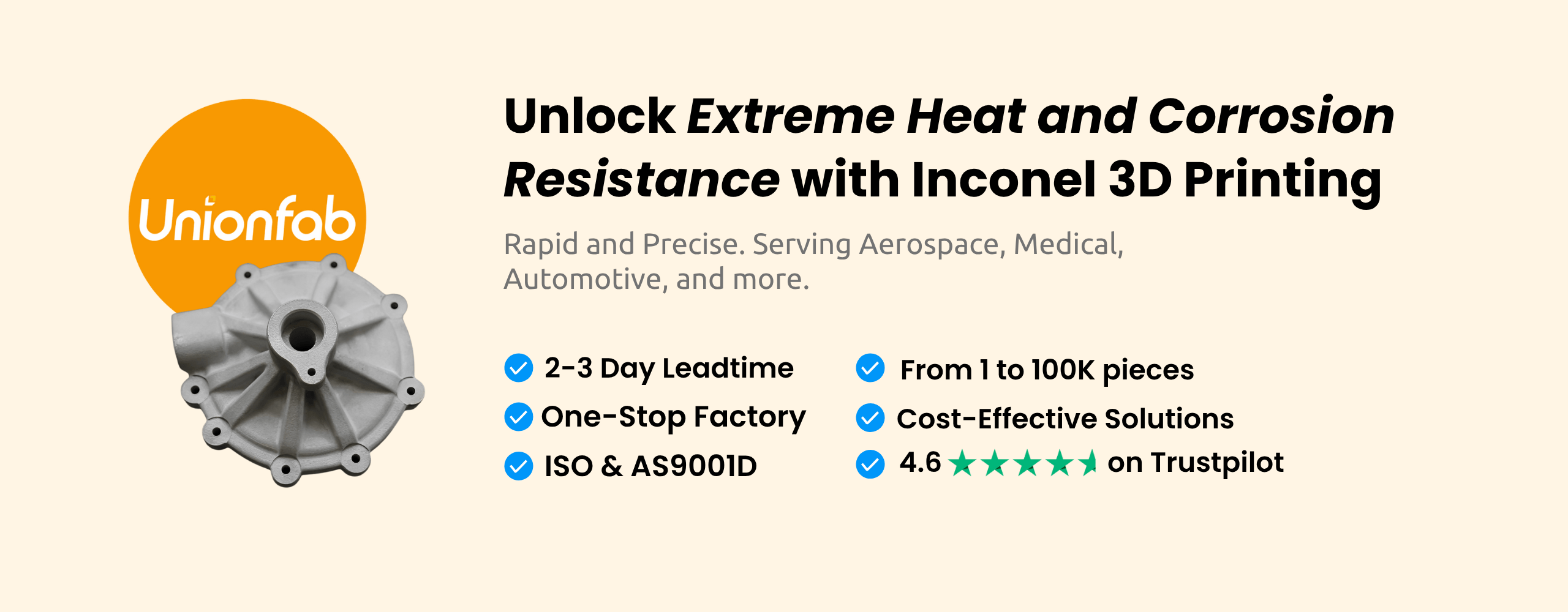
Typical Applications of Inconel 718
Thanks to its unique combination of high-temperature strength, corrosion resistance, and excellent weldability, Inconel 718 has become a go-to superalloy for a wide range of demanding applications.
Below is a breakdown of its typical uses categorized by functional role:
1. Load-Bearing Components
Inconel 718 offers exceptional fatigue strength and tensile properties, making it ideal for structural applications where mechanical loads are critical.
Example parts: turbine disks, shafts, fasteners, structural connectors.
2. Heat-Resistant Parts
With a maximum operating temperature exceeding 700°C and good creep resistance, Inconel 718 excels in thermally intensive environments.
Example parts: combustion chamber components, exhaust ducts, thermal shields.
3. Corrosion-Resistant Structures
With a maximum operating temperature exceeding 700°C and good creep resistance, Inconel 718 excels in thermally intensive environments.
Example parts: combustion chamber components, exhaust ducts, thermal shields.
4. Sealing & Fastening Components
The alloy’s strength and stability under both thermal and mechanical stress make it suitable for precision fastening and sealing solutions.
Example parts: bolts, washers, flanges, pressure seals.
5. Repair or Additive Overlays
Inconel 718 is also used in directed energy deposition (DED) and laser cladding for repairing high-value components or enhancing surface durability.
Example parts: turbine blade tip rebuilds, wear-resistant overlays, aerospace component refurbishments.
FAQs:
What is 718 in Inconel?
It refers to the specific alloy designation. Inconel 718 is a nickel-based superalloy known for its high strength, corrosion resistance, and excellent performance at high temperatures.
Is Inconel better than Titanium?
It depends on the application. Inconel performs better at high temperatures and in corrosive environments, while titanium is lighter and offers excellent strength-to-weight ratio and biocompatibility.
Is Inconel 718 better than Stainless Steel?
It depends on the application. Inconel performs better at high temperatures and in corrosive environments, while titanium is lighter and offers excellent strength-to-weight ratio and biocompatibility.
What is the difference between Inconel 625 and 718?
Inconel 625 is strengthened by solid solution hardening, offering superior corrosion resistance. Inconel 718 is precipitation-hardened, making it stronger and better for high-stress, high-temperature applications.
What is Inconel 718 price per kg?
Prices vary, but typically range from $80 to $150 per kg depending on form (powder, bar, etc.), quantity, and supplier.