Material Jetting 3D Printing: All You Need to Know [+ Comparsion table]
![Material Jetting 3D Printing [+Comparsion table]](https://ufc-dtc-cms.oss-accelerate.aliyuncs.com/blog/20250508/171436_avhsevi5t.png)
Material jetting is a professional-grade 3D printing technology known for its high accuracy, smooth surfaces, and multi-material capabilities. In this article, we’ll provide a clear and complete overview of material jetting, how it works, what it’s used for, and how it compares to other additive and subtractive methods such as CNC machining.
What is Material Jetting?
Material jetting is an additive manufacturing process that works by jetting tiny droplets of photopolymer materials onto a build platform. These droplets are immediately cured using ultraviolet (UV) light, layer by layer, to build a 3D object. It’s similar to 2D inkjet printing but extended into three dimensions.
Unlike other 3D printing technologies, material jetting offers extremely high resolution and the ability to print in multiple materials and colors within a single part.
Curious about whether material jetting is right for your prototype? Try our free project review — Talk to a Unionfab specialist now!
How Does Material Jetting Work?
Droplet Deposition: The printer jets microscopic drops of liquid material from multiple nozzles.
Layer-by-Layer Curing: Each layer is hardened instantly by UV light before the next one is added.
Support Structures: Temporary support material is printed at the same time and removed after printing.
This process enables fine details and complex geometries, ideal for applications where precision and visual quality are critical.
Key Advantages of Material Jetting 3D Printing
Feature | Benefit |
---|---|
High Resolution | Up to 16-micron layer thickness for highly detailed parts |
Excellent Surface Finish | Smooth surfaces with minimal post-processing |
Multi-Material Capability | Combine rigid, flexible, and transparent materials in one print |
Full Color Options | Ideal for presentation models and realistic prototypes |
Accuracy | Dimensional tolerances close to CNC standards |
Compared to other 3D printing methods, material jetting 3D printers offer superior detail and surface quality.
Printer Types and Print Settings
Material jetting printers are designed for industrial and professional applications where resolution and surface finish are top priorities. The two most common printer technologies are:
PolyJet (e.g., Stratasys): This system uses multiple print heads to jet several materials at once. PolyJet printers support full-color printing and allow blending of materials with different mechanical properties. These are ideal for functional prototypes, concept models, and anatomical simulations.
MultiJet Printing (MJP, e.g., 3D Systems): MJP printers typically use a wax-based support structure and are especially valued in the production of high-accuracy casting patterns for jewelry and dentistry. They offer excellent detail and repeatability.
Typical print settings include:
Layer height: Ranges from 16 to 32 microns, enabling extremely fine surface texture
Resolution: Up to 600 x 600 dpi or higher, depending on the model
Build volume: Typically up to 500 x 400 x 200 mm, though varies by system
Printing speed: Generally moderate; print times vary depending on resolution and part geometry
Material jetting printers also feature enclosed build environments to maintain material consistency and curing conditions.
Common Applications of Material Jetting
An artistic demonstration of PolyJet 3D printing: multi-material, high-resolution structures simulating organic overgrowth on an engine block.
Material jetting is widely used across industries for both visual and functional prototypes:
Medical: Dental models, anatomical parts, and surgical guides
Consumer Products: Realistic product prototypes for marketing or testing
Aerospace & Automotive: Small detailed components and testing models
Jewelry & Art: Wax casting patterns and design validation models
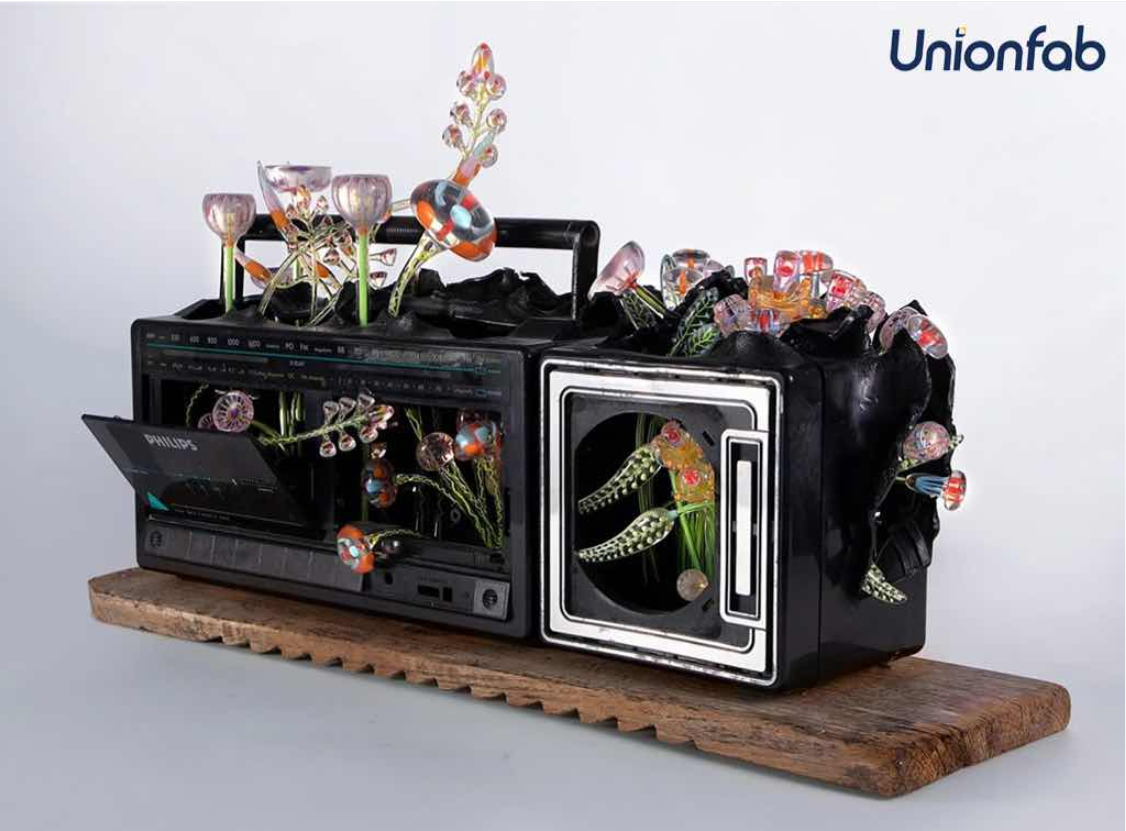
Source: Unionfab
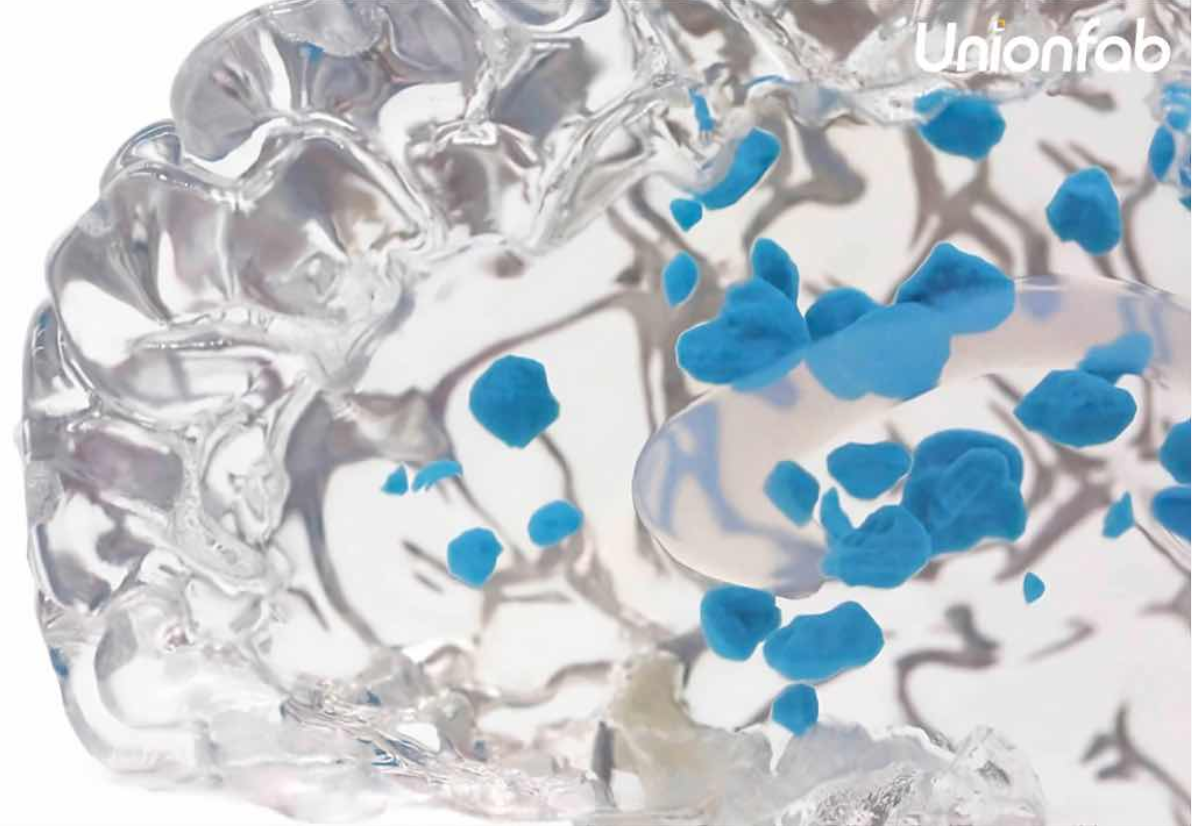
Source: Unionfab
Thanks to its ability to produce precise and smooth parts, 3D printing with material jetting is particularly valuable for design review and presentation.
Materials Used in Material Jetting
Material jetting uses mainly photopolymers and wax-like materials, depending on the application:
Rigid Photopolymers: Suitable for general-purpose prototypes
Rubber-like Materials: Useful for flexible components
Casting Wax: Common in jewelry and investment casting workflows
Full-Color Photopolymers: Used in realistic models and educational displays
Material formulations vary by printer manufacturer and are often optimized for specific tasks such as high-temperature resistance, biocompatibility, or transparency. Most photopolymer parts are not UV-stable over time, so indoor applications are preferred.
Limitations of Material Jetting
Despite its precision, material jetting comes with several limitations that are important to consider:
Material Fragility: The cured photopolymers are often brittle compared to thermoplastics or metals. While suitable for visual prototypes, they lack the strength required for mechanical or load-bearing applications.
Limited Functional Use: Material jetting is not ideal for producing functional end-use parts that require durability, temperature resistance, or chemical resistance. Degradation may occur over time with exposure to UV light or moisture.
Cost of Ownership: Both the hardware and consumables (resins, support materials) are relatively expensive. Additionally, the support removal process may require specialized equipment.
Size Constraints: Most machines are designed for small to medium-sized parts. Printing large parts requires splitting the model and assembling afterward, which can affect part integrity or aesthetics.
For best results, material jetting should be reserved for parts where precision, appearance, and fine detail are more important than structural performance.
Material Jetting vs Other 3D Printing Technologies
Technology | Resolution | Surface Finish | Multi-Material | Best Use Cases |
---|---|---|---|---|
Material Jetting | Very high | Excellent | Yes | Prototypes, visual models |
Low | Rougher | No | Basic prototypes, functional parts | |
High | Smooth | Limited | Dental, figurines, fine parts | |
Medium | Slightly Rougher | No | Functional prototypes, mechanical parts |
For projects needing visual quality and fine features, material jetting 3D printing is the clear winner.
Material Jetting or CNC Machining
While material jetting and CNC machining are different in nature (additive vs subtractive), they are often considered together during early-stage prototyping and small-batch production.
Comparison Area | Material Jetting | CNC Machining |
---|---|---|
Process | Adds material layer by layer | Removes material from a block |
Tolerance | ±0.1 mm (excellent for printing) | ±0.01 mm (ideal for engineering) |
Materials | Photopolymers, waxes | Metals, plastics, composites |
Strength | Good for visual or light-use parts | Best for mechanical strength |
Speed for Small Runs | Fast | Moderate to fast |
Need both CNC and 3D printing for your prototype?
Unionfab offers hybrid workflows and consolidated shipping — talk to us about combining services efficiently. Get a tailored quote!
At Unionfab, we often recommend material jetting for early prototypes or client-facing models, and CNC for functional components or when using metals.
Post-Processing in Material Jetting
Post-processing is a critical step to ensure the quality and functionality of printed parts. The typical steps include:
Support Removal: Support structures are made from a different material than the main print and are usually removed with water jets, ultrasonic baths, or melting (in the case of wax). The process is non-invasive and preserves fine features.
UV Curing: Some parts may require additional UV curing to fully harden the outer layers, especially if the build was interrupted or materials require secondary exposure.
Surface Cleaning & Finishing: Parts are washed and optionally polished or sanded. In many cases, no sanding is needed due to the already smooth finish.
Optional Coatings: Depending on use, coatings can be applied for color enhancement, wear resistance, or surface protection.
Casting Preparation: For wax patterns, investment casting procedures follow, including shell building and burnout steps.
Because material jetting prints parts with a high-quality surface straight out of the machine, post-processing is typically faster and less labor-intensive than other technologies.
Need PolyJet 3D Printing Services?
At Unionfab, we offer professional-grade PolyJet 3D printing services alongside CNC machining and other advanced manufacturing options.
Our PolyJet technology enables high-resolution, multi-material, and full-color prototyping suitable for a wide range of design and engineering applications. and other advanced manufacturing options. Whether you need one prototype or a small batch of highly detailed models, our engineers are here to help.
Unionfab: Your Partner in Polyjet and High-Precision 3D Printing
Get instant quotes and design feedback
Combine 3D printing with CNC for hybrid workflows
Fast lead times and global shipping
Contact us today to learn more about how material jetting can support your next project!
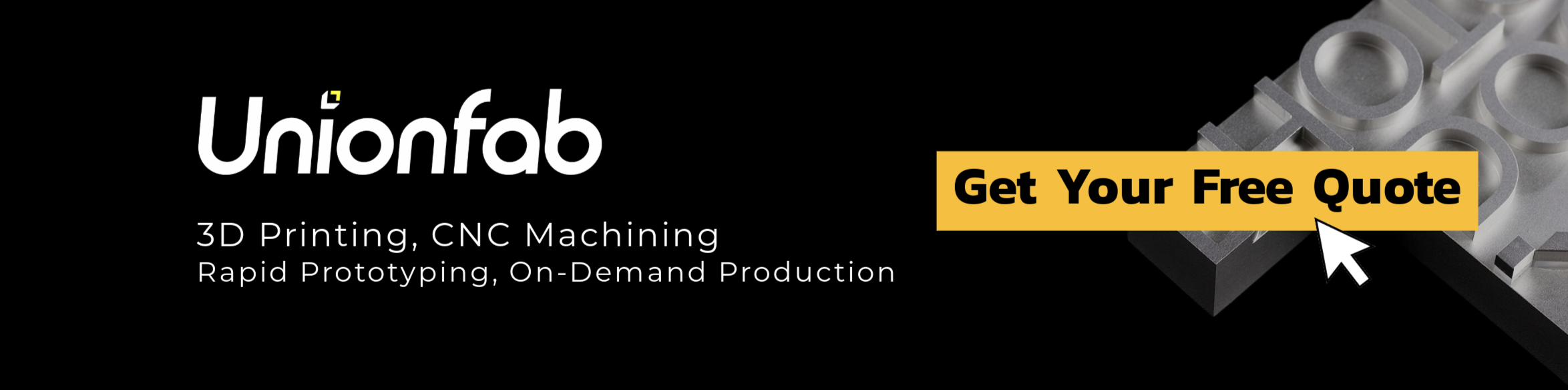