Resin vs. Plastic [+Key Differences Explained]
![Resin vs. Plastic[+Key Differences Explained]](https://ufc-dtc-cms.oss-accelerate.aliyuncs.com/blog/20250516/104048_p6kf0rmrw.png)
Compare resin and plastic by properties, processing, and uses. Learn differences, pros, cons, and which fits your project.
Introduction
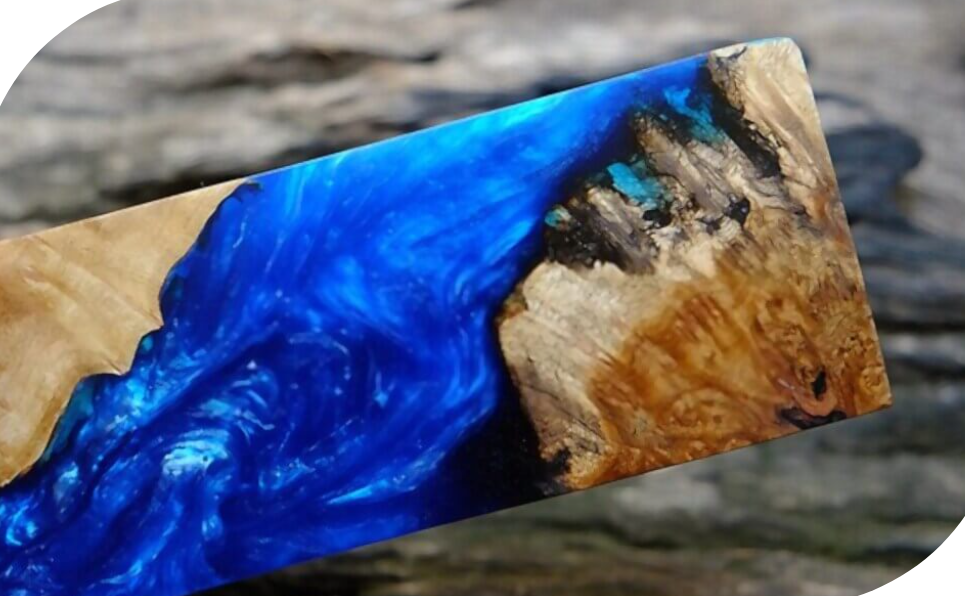
Resin and plastic are two terms often used interchangeably, but they refer to different forms of polymers with distinct properties and applications.
Understanding their differences-and how they relate-can help in choosing the right material for manufacturing, design, and especially 3D printing.
What Is Resin?
Resin is typically a viscous substance that hardens into a solid material through chemical reactions such as curing or polymerization. It can be natural or synthetic, and it's widely used in adhesives, coatings, and 3D printing-particularly where fine detail and smooth finishes are required.
What Is Plastic?
Plastic refers to a broad category of solid synthetic materials made from polymers. Plastics are usually thermoplastics (meltable and moldable) or thermosets (hardened permanently once set). They are used in everything from packaging to automotive parts due to their versatility and durability.
Relationship Between Resin and Plastic
In essence, resin is the raw form or precursor of plastic. Plastics are typically made by refining and polymerizing resins.
So, while all plastics start as resins, not all resins are processed into plastic. They are chemically related but differ in form, usage, and handling.
Types of Resins Classified by Curing Method
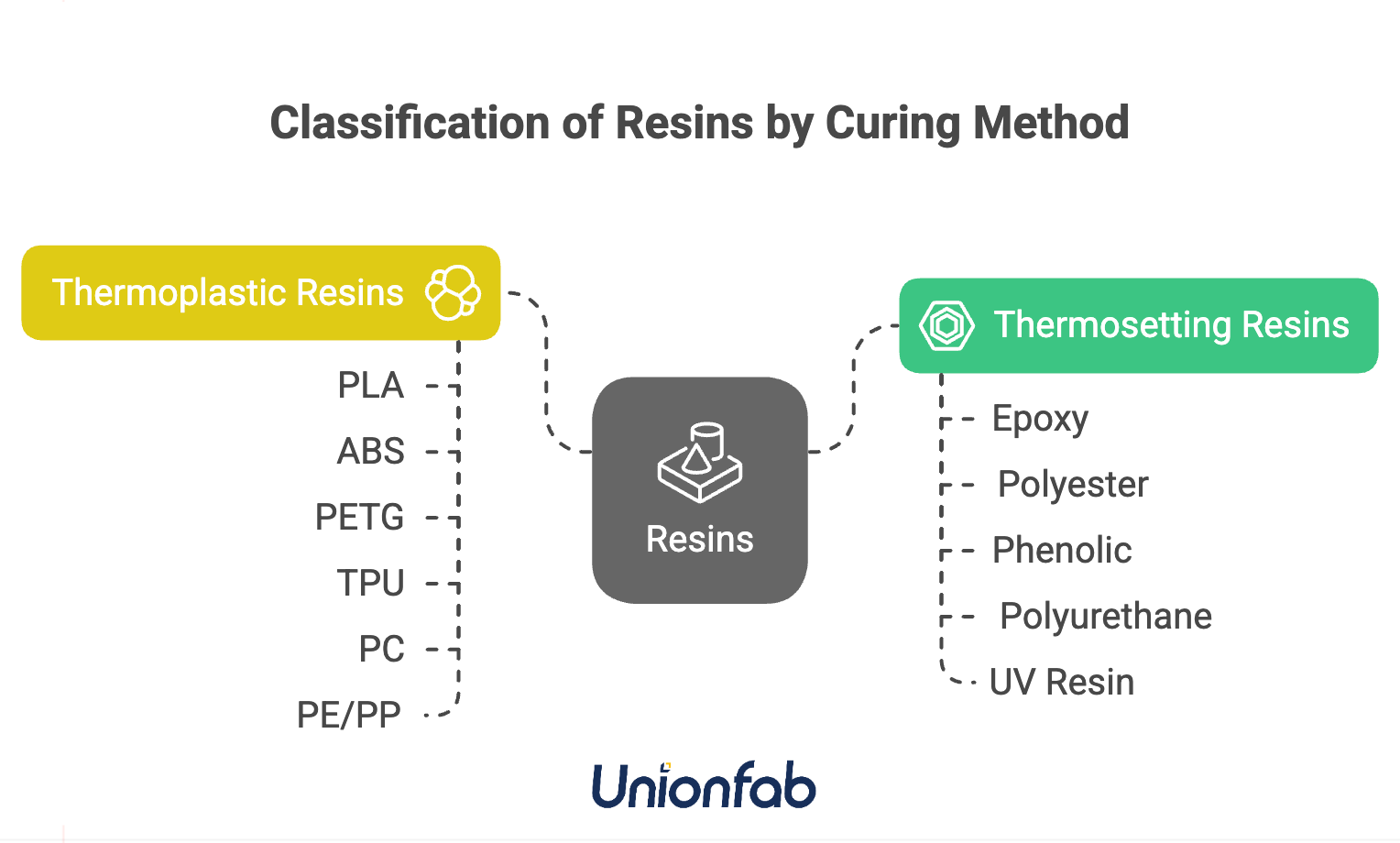
Resins can be broadly categorized based on how they cure or harden. This classification affects their behavior, performance, and suitability for different applications.
Below are the two main types-thermosetting and thermoplastic resins-each with distinct properties, processing methods, and uses.
1. Thermosetting Resins
Cannot be re-melted or reshaped once cured.
Undergo a chemical reaction when heated or combined with a curing agent, forming a three-dimensional cross-linked structure.
Characteristics: High hardness, excellent heat resistance, resistant to melting or deformation.
Applications: Electronic encapsulation, composite materials, structural adhesives, high-performance 3D printing materials, etc.
Common Thermosetting Resins: Epoxy, Polyester, Phenolic, Polyurethane, UV Resin
2. Thermoplastic Resins / Plastics
Can be repeatedly softened, melted, and reshaped upon heating; solidify upon cooling.
Do not undergo an irreversible chemical change-only physical transformation.
Characteristics: Recyclable, reprocessable, good toughness.
Common Thermoplastic Plastics: PLA, ABS, PETG, TPU, PC, PE/PP
Resin vs. Plastic: Pros and Cons
When choosing between resin and plastic, it’s helpful to understand their strengths and trade-offs. Both are common in manufacturing and 3D printing, but they differ in detail, strength, cost, and ease of use.
The table below compares their main pros and cons to help you choose the right material for your project.
Feature | Resin | Plastic |
---|---|---|
Detail | High resolution, smooth finish | Moderate resolution, layered finish |
Strength | Brittle, but some tough resins exist | Strong, impact-resistant |
Cost | More expensive | Generally cheaper |
Ease of Use | Requires careful handling | Easier and safer to work with |
Post-processing | Requires cleaning and curing | Minimal finishing required |
Resin offers high detail and smooth finishes but requires more care and post-processing. Plastic is generally more durable, affordable, and user-friendly. Choosing the right material depends on your specific priorities—whether it's fine detail or ease of use and strength.
Resin vs. Plastic in Processing Methods
Resin and plastic are processed in different ways, which affects how they’re used in manufacturing. Thermosetting resins and thermoplastics each work best with certain methods like casting or molding.
The table below shows how each material fits with common processing techniques.
Processing Method | Resin (Thermosetting) | Plastic (Thermoplastic) |
---|---|---|
Casting (Mold Pouring) | ✅ Common method—used in applications like epoxy potting and handcrafted resin art. | ⚠ Rarely used due to high melting points and poor flow characteristics. |
3D Printing | ✅ SLA / DLP / LCD technologies use liquid photopolymer resins that cure under UV light. | ✅ FDM / SLS technologies use thermoplastic filaments or powders melted and layered. |
Injection Molding | ❌ Not suitable—once cured, thermosetting resins cannot be re-melted or reshaped. | ✅ One of the most common methods for mass-producing plastic parts. |
Lamination / Composite Molding | ✅ Widely used with fiberglass or carbon fiber reinforcement (e.g., epoxy resins). | ⚠ Less commonly used for structural composites. |
Spraying / Coating | ✅ Liquid resins such as polyurethane and acrylics are used as coatings and finishes. | ⚠ Rarely used unless modified; thermoplastics are not ideal for spraying. |
Thermoforming / Blow Molding / Heat Pressing | ❌ Not applicable to cured resins. | ✅ Commonly used for forming plastic bottles, packaging, and casings from PET, PP, etc. |
Machining (Cutting / Turning) | ❌ Brittle after curing, not suitable for traditional machining—prone to dust and cracking. | ✅ Machinable—materials like nylon and ABS blocks are regularly cut or milled. |
Resins are great for detailed work like casting and coatings, while plastics are better for large-scale methods like injection molding and machining. Your choice depends on the process, quantity, and final use of the product.
Summary
Resins (thermosetting) are excellent for casting, composite reinforcement, and coatings, but are unsuitable for re-melting or traditional machining once cured. Their strength lies in high precision and chemical resistance, making them ideal for custom parts and high-performance applications like 3D printing (SLA/DLP).
Plastics (thermoplastics), on the other hand, dominate mass production and mechanical shaping. They are highly versatile and can be injected, extruded, thermoformed, or even machined, making them essential for consumer goods and functional components—particularly in FDM/SLS 3D printing.
Resin vs Plastic in 3D Priting
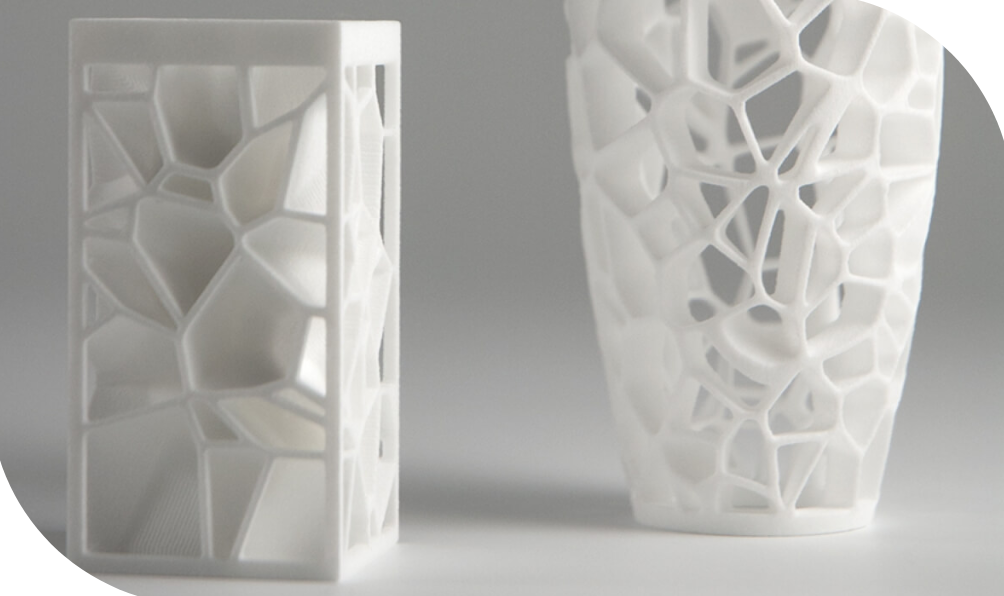
Resin and plastic materials offer distinct advantages in 3D printing. Resin printing excels in detail and surface quality, making it ideal for artistic models and prototypes, while plastic printing is better suited for durable, functional parts.
The following comparison of common resins and plastics highlights their key properties to assist in selecting the most suitable material for a project.
Common Resins in 3D Printing:
● Standard Resin – Ideal for visual models, prototypes, and figurines; provides high detail and smooth finishes but can be brittle.
● Tough Resin – Designed to simulate ABS; significantly improved impact resistance and durability, suitable for functional prototypes.
● Flexible Resin – Mimics rubber or silicone textures; used for parts requiring bendability or cushioning.
● Dental/Castable Resin – High precision; specialized for dental applications, jewelry casting, and mold making.
Common Plastics in 3D Printing:
● PLA (Polylactic Acid) – Easy to use, environmentally friendly, low warping; ideal for beginners and aesthetic models.
● ABS (Acrylonitrile Butadiene Styrene) – Strong and impact-resistant; suitable for functional and mechanical parts but requires controlled environment due to warping and fumes.
● PETG (Polyethylene Terephthalate Glycol) – Combines the strength of ABS and ease of PLA; good chemical resistance and flexibility.
● TPU (Thermoplastic Polyurethane) – Soft and flexible; excellent for wearable items, seals, and components requiring elasticity.
Property Comparison of Materials
Material choice greatly affects 3D print quality and function. Resins and plastics each offer different levels of detail, strength, and flexibility.
The table below compares popular materials to help match them to specific uses—from fine models to durable parts.
Property | Standard Resin | Tough Resin | Flexible Resin | Dental/Castable Resin | PLA | ABS | PETG | TPU |
---|---|---|---|---|---|---|---|---|
Resolution | Very high | Very high | High | Very high | Moderate | Moderate | Moderate | Moderate |
Surface Finish | Smooth | Smooth | Smooth | Smooth | Layered | Layered | Layered | Slightly layered |
Strength | Brittle | Tough and impact-resistant | Flexible, low structural strength | Moderate (depending on resin type) | Rigid but weak | Strong and durable | Strong with slight flexibility | Elastic, impact-resistant |
Flexibility | Low | Medium | High | Low | Low | Medium | Medium | Very high |
Best For | Figurines, display prototypes | Functional prototypes, tools | Wearables, grips, flexible joints | Dental molds, jewelry patterns | Aesthetic models, toys | Mechanical, automotive, enclosures | Functional parts, containers | Phone cases, hinges, shock absorbers |
Summary
● Resin-based 3D printing (SLA/DLP) excels in visual precision, making it ideal for high-detail models like miniatures, dental molds, and jewelry prototypes.
● Plastic-based 3D printing (FDM/FFF) prioritizes durability and function, making it more suitable for mechanical parts, enclosures, and daily-use components.
● For applications that require strength and flexibility, Tough Resin, ABS, PETG, and TPU are excellent choices.
● Beginners and eco-conscious users often prefer PLA for its ease of use and biodegradable nature.
Want Professional-Grade 3D Prints?
Whether you need fine-detail resin prints or durable plastic prototypes, Unionfab offers industrial-level 3D printing services using a wide range of materials and technologies.
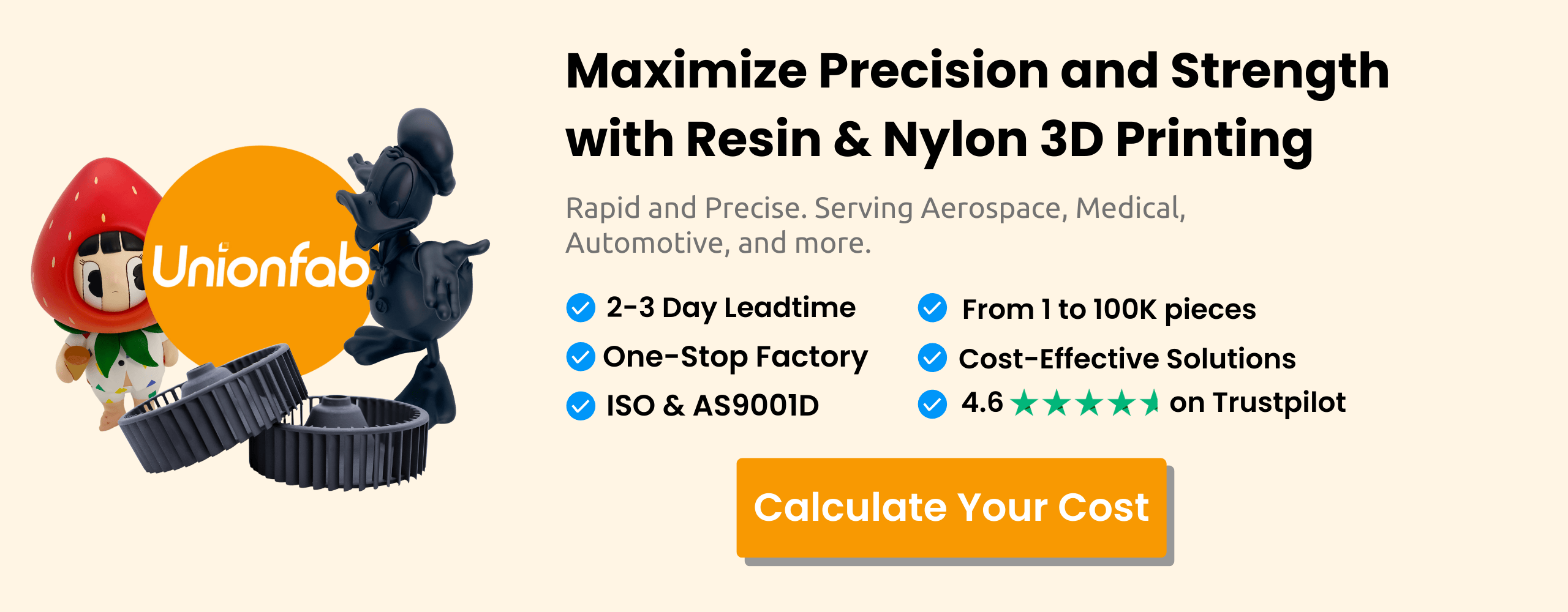
Conclusion
Resin and plastic both play vital roles in 3D printing and manufacturing. Resin stands out for precision and surface finish, while plastic is a go-to for functional strength and versatility. Choosing between the two depends on your project needs, budget, and application.
FAQs
Does resin last longer than plastic?
Resin can be more durable than certain plastics, especially when it is cured properly. However, its longevity depends on the type of resin and the environmental conditions it’s exposed to, such as UV light, temperature, and physical stress.
Does resin break easily?
Resin can be brittle and may break or crack under impact, but some tougher resins are designed to offer more durability and resistance to breakage. It’s important to choose the right resin based on the intended application.
Can resin melt plastic?
Resin itself does not melt plastic, but certain types of resins can bond or chemically react with plastics. The interaction depends on the specific types of resin and plastic used. However, resin curing temperatures are typically not high enough to melt most plastics.