Tempering and Hardening Steel [+Expert Tips]
![Tempering and Hardening Steel [+Expert Tips]](https://ufc-dtc-cms.oss-accelerate.aliyuncs.com/blog/20250721/220752_j804omv6q.png)
Learn how hardened and tempered steel improves strength, wear resistance, and dimensional stability for CNC machined and metal 3D printed parts.
Introduction
Hardening and tempering are key heat treatment processes used to improve the strength and durability of metals. Hardening increases hardness through rapid cooling, while tempering reduces brittleness by reheating the hardened metal to a lower temperature.
Among various metals, steel is the most commonly treated using hardening and tempering, thanks to its unique structural transformations under heat.
This article focuses on how hardening and tempering are applied to steel, explores the factors that influence the process, and explains why these treatments are essential for CNC machining and metal 3D printing.
What Is Steel Hardening and Tempering?
Steel hardening and tempering are two closely linked heat treatment processes that significantly improve the mechanical properties of steel, particularly its hardness, strength, and toughness.
1. What Is Steel Hardening?
Steel hardening is a heat treatment process used to increase the hardness and strength of steel.
In practice, this is usually achieved through quenching—a process where the steel is heated to a high temperature and then rapidly cooled in water, oil, or air.
Note:
Quenching is the process
Hardening is the resulting effect—a measurable increase in hardness and strength
2. Why Tempering Is Needed
While quenching makes steel harder, it also makes it brittle. Brittle steel may crack or fail under impact or stress.
That’s where tempering comes in. This improves the steel’s toughness and makes it more suitable for real-world applications such as tools, gears, and machine parts.
3. The Balance of Strength and Toughness
When combined, hardening and tempering help steel achieve an ideal balance between:
Hardness and wear resistance (from quenching)
Toughness and durability (from tempering)
This combination creates a balance between strength and toughness—critical for steel components that must endure both wear and impact.
Steel Hardening and Tempering Process Explained
Steel Hardening Process
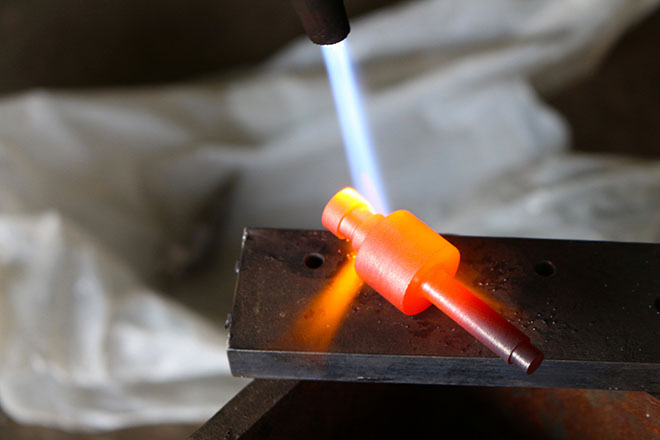
Source: MIHEU.COM
1. Heating
The steel is heated to a high temperature, usually between 800°C and 900°C, where its structure transforms into austenite.
2. Rapid Cooling (Quenching)
The hot steel is then quickly cooled in a medium such as water, oil, or air, depending on the steel type. This rapid cooling causes the formation of martensite, a very hard but brittle structure.
3. Result
The steel becomes significantly harder and stronger, but also more brittle, making it unsuitable for most applications without further treatment.
Steel Tempering Process
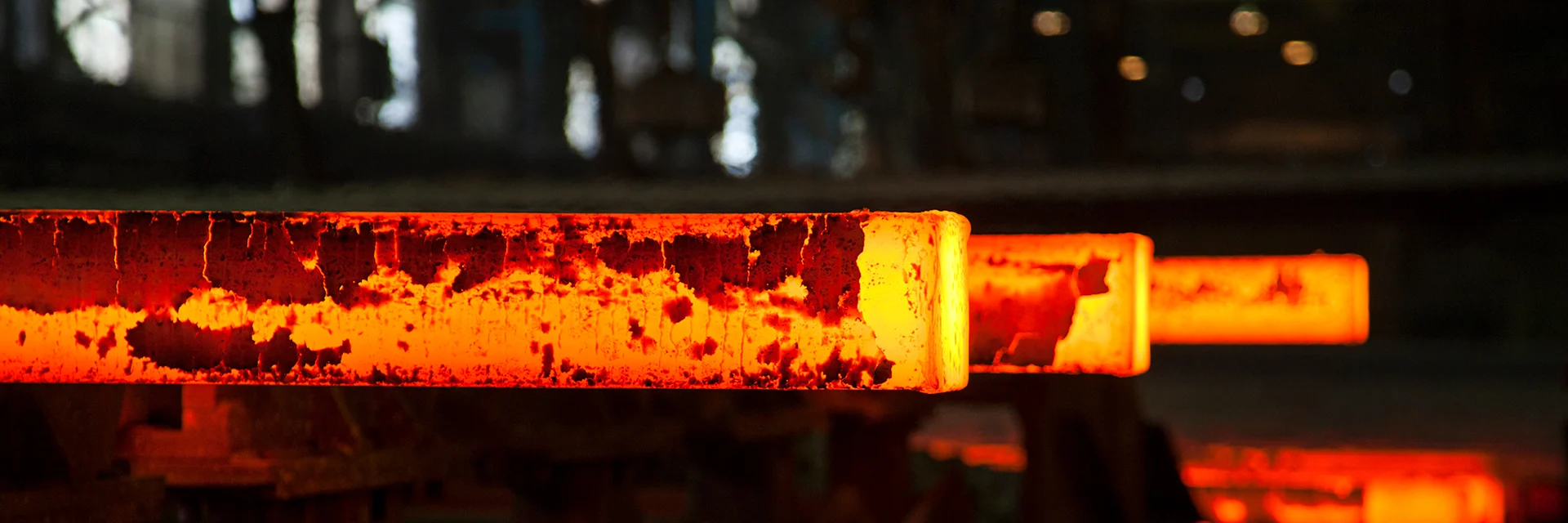
Source: Mead Metals
1. Reheating
The quenched steel is reheated to 150°C–650°C, depending on the desired mechanical properties. This reduces brittleness while maintaining hardness.
The table below shows how different tempering temperatures affect the mechanical properties of steel and lists typical applications for each range.
Tempering Temperature | Effect on Properties | Typical Applications |
---|---|---|
Low (150°C–300°C) | High hardness, lower toughness | Cutting tools, dies, springs |
Medium (300°C–500°C) | Balanced strength and toughness | Gears, shafts, structural parts |
High (500°C–650°C) | Lower hardness, improved ductility and toughness | Structural steels, pressure vessels |
2. Soaking and Cooling
The steel is held at the target temperature for a specific time, then allowed to cool in air.
3. Result
This reduces internal stresses and improves toughness, while maintaining much of the gained hardness.
What Influences the Process?
Steel Type Matters
Different types of steel respond differently to steel hardening and tempering based on their carbon content, alloying elements, and heat treatment compatibility.
Choosing the right steel grade is essential to achieving the desired combination of hardness, strength, and toughness.
Below is a comparison of how common engineering steels behave during the hardening process:
Steel Type | Hardenability | Quenching Sensitivity | Notes |
---|---|---|---|
1045 (Medium Carbon Steel) | Moderate | Moderate | Suitable for shafts, gears, and general mechanical parts |
4140 (Alloy Steel) | High | Low | Excellent toughness and strength, widely used in CNC applications |
H13 (Hot Work Tool Steel) | Very High | Requires controlled quenching | Ideal for hot work tooling, dies, and molds |
D2 (High Carbon, High Chromium Tool Steel) | Very High | High | Provides exceptional wear resistance, used in cutting tools |
1045 can be surface-hardened but does not achieve deep hardness due to its moderate carbon content.
4140 responds well to quenching and achieves high strength with good dimensional stability.
H13 and D2 require carefully controlled hardening cycles—often in vacuum or salt baths—to avoid cracking and decarburization.
The tempering behavior of steel is equally critical for performance:
Steel Type | Tempering Stability | Max Recommended Tempering Temp | Typical Applications |
---|---|---|---|
1045 | Moderate | ~300°C | Low-stress parts, general machinery |
4140 | Good | ~500°C | High-load components like axles, bolts |
H13 | Excellent | ~600°C | Dies, extrusion tooling, injection molds |
D2 | Good | ~500°C | Punches, shear blades, forming dies |
H13 retains hardness at elevated temperatures, making it ideal for tooling exposed to heat and pressure.
4140 offers an excellent balance of strength and toughness post-tempering, making it versatile for structural and dynamic parts.
D2, while extremely hard, must be tempered carefully to prevent brittleness and maintain dimensional control.
In summary, steel type selection significantly influences how effective the hardening and tempering process will be.
Unionfab offers engineering support to help you choose and process the right material for your CNC or 3D printed part applications. Feel free to contact us.
Why It Matters for CNC and 3D Printing
In CNC Machining
● Tool Durability: Cutting tools, dies, and fixtures often require hardened steel to resist wear and maintain precision during extended use.
● Dimensional Stability: Tempered steel helps prevent warping and cracking during high-speed cutting or under mechanical stress.
● Final Part Properties: Many CNC-machined components—like shafts, gears, and mechanical arms—rely on heat-treated steel for strength, impact resistance, and long-term reliability.
In 3D Printing (Metal AM)
● Post-Processing Requirement: In metal additive manufacturing (such as SLM or DED), printed steel parts are often in a non-ideal microstructure and require post-print heat treatment to achieve desired hardness and toughness.
● Stress Relief and Performance: Hardening and tempering can reduce residual stresses from the printing process and improve fatigue resistance and mechanical stability.
● Functional End-Use Parts: For load-bearing or wear-prone 3D printed steel components, proper heat treatment ensures that the parts can match or exceed the performance of traditionally manufactured ones.
Achieve High Precision and Performance with Unionfab
At Unionfab, we specialize in both CNC machining and metal 3D printing, delivering high-performance steel parts tailored to your exact needs.
Whether you require hardened and tempered components for durability, or post-processed 3D printed steel parts with optimized mechanical properties, our team ensures every part meets industry standards for strength, hardness, and reliability.
Contact us today to get expert support on material selection, heat treatment options, and manufacturing solutions that bring your designs to life. For customers who haven’t cooperated with us before, you will get 10% discount for you first order.
FAQs
What is the purpose of tempering after hardening?
Tempering reduces brittleness and increases toughness by reheating the hardened steel.
Can all steels be hardened and tempered?
No. Only steels with enough carbon and specific alloy content respond well to heat treatment.
Do 3D printed metal parts need heat treatment?
Yes. Heat treatment like hardening and tempering of steel reduces stress and improves strength in metal-printed parts.
Is steel heat treatment offered separately by Unionfab?
Yes. We offer heat treatment as a standalone or integrated service with CNC and 3D printing.
Which file formats does Unionfab accept for orders?
We accept STL, STEP, IGES, and more. Upload your part and receive expert support within 24 hours.
Can stainless steel be hardened and tempered?
Some types of stainless steel, especially martensitic grades, can be hardened and tempered. Austenitic stainless steels generally cannot due to their low carbon content.
What is the difference between hardening and tempering steel?
Hardening increases steel's hardness through rapid cooling after heating. Tempering follows hardening and reduces brittleness by reheating to a lower temperature, improving toughness and stability.