Analysis and insights on the application of copper alloys in 3D printing and other manufacturing industries
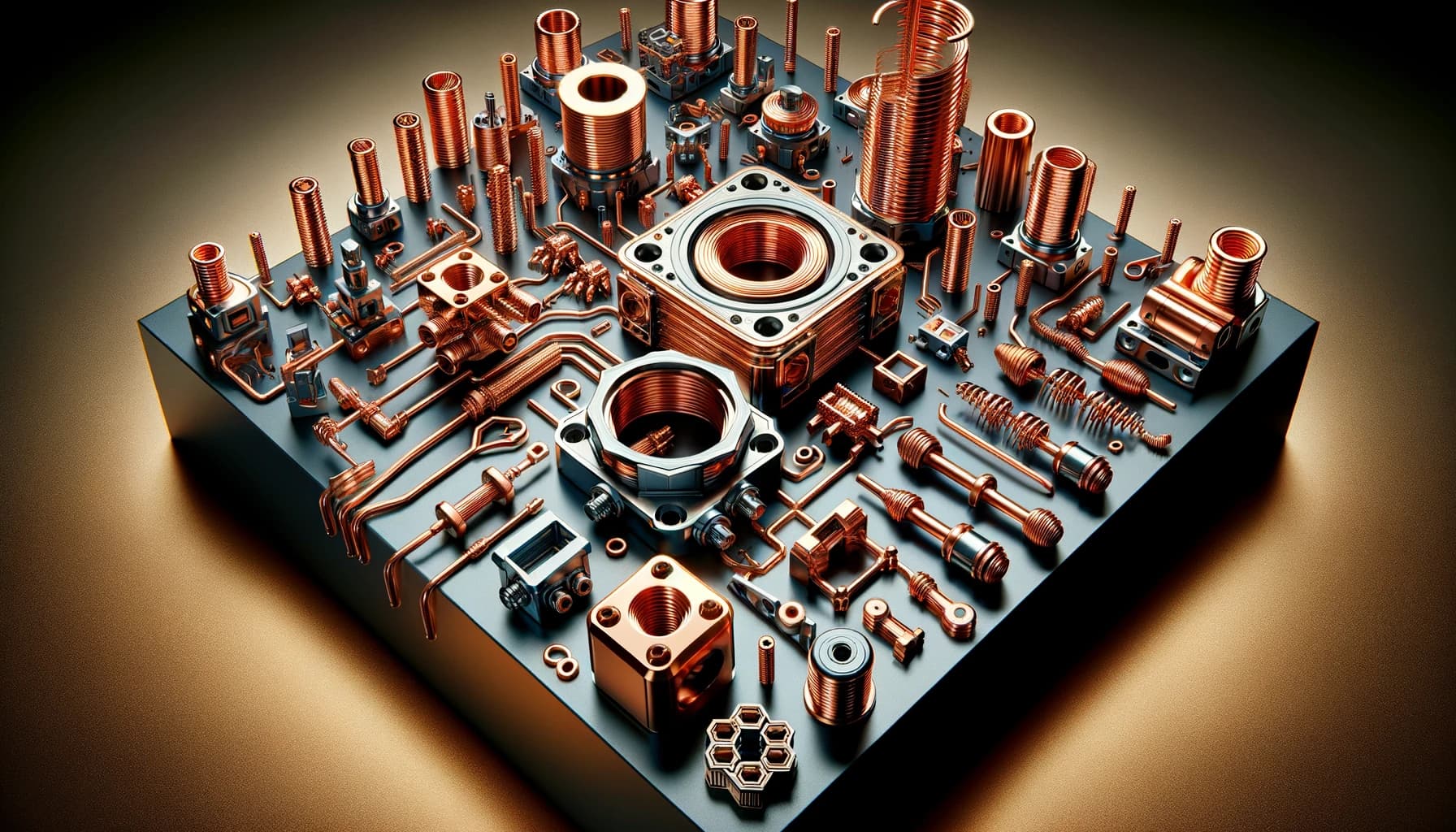
Copper alloys created by combining copper with one or more other metals, offer enhanced properties for a wide range of applications. This article delves into the world of copper alloys, exploring their types, characteristics, origins, applications, strengths, and limitations.
What are Copper Alloys?
Copper alloys are formed when copper is mixed with other elements to improve its natural properties. The addition of other metals such as tin, zinc, nickel, and aluminum enhances copper's strength, corrosion resistance, and hardness, making it more suitable for specific applications.
Types, Composition, and Characteristics
Brass (Copper-Zinc Alloys)
Known for its acoustic properties, brass is widely used in musical instruments, decorative items, and plumbing fixtures. It typically contains 55-95% copper and 5-45% zinc, with lead added to improve machinability.
Bronze (Copper-Tin Alloys)
This group is distinguished by its excellent wear resistance and strength, making it ideal for bearings, bushings, and marine applications. Bronze usually contains copper (up to 88%) and tin, with phosphorus, aluminum, or silicon for specific properties.
Cupronickel (Copper-Nickel Alloys)
With high resistance to corrosion in seawater, cupronickel is perfect for marine hardware, desalination plants, and coinage. It typically comprises 60-90% copper and 10-40% nickel.
Origin, Applications, Strengths, and Limitations
Copper alloys are produced worldwide, with major producers located in Chile, China, Peru, and the United States. Their applications span across various industries:
Electrical and Electronics
Due to their excellent electrical conductivity, copper alloys are used in wires, connectors, and switches.
Marine
The corrosion resistance of cupronickel makes it suitable for ship hulls and offshore platforms.
Construction
Brass fittings and bronze sculptures are common in construction and decorative applications.
The strengths of copper alloys include their superior electrical and thermal conductivity, corrosion resistance, and aesthetic appeal. However, their limitations include susceptibility to stress corrosion cracking (for certain alloys) and higher costs compared to other metals.
Highest Working Temperatures
Copper alloys can operate at varying maximum temperatures depending on their composition:
Brass
Up to 450°C (842°F), beyond which zinc begins to vaporize.
Bronze
Can withstand up to 600-700°C (1112-1292°F) in certain compositions.
Cupronickel
Up to 500°C (932°F), maintaining strength and corrosion resistance.
Differences and Use Cases of Copper Alloys
Brass is preferred for decorative items, musical instruments, and fittings due to its acoustic properties and ease of machining.
Bronze is chosen for applications requiring wear resistance and strength, such as bearings and sculptures.
Cupronickel is ideal for marine environments, offering durability against seawater corrosion.
Visual Exploration of Copper Alloys
To complement this overview, let's generate three images that capture the beauty and utility of copper alloys in various applications:
Brass musical instruments, showcasing the alloy's luster and acoustic properties.
Bronze sculptures, highlighting the material's durability and aesthetic appeal.
Cupronickel marine hardware, demonstrating the alloy's resistance to seawater corrosion.
These visuals will illustrate the diverse applications and properties of copper alloys, enhancing our appreciation for this versatile group of materials. Let's create the images.
The Use of Copper Alloys in 3D Printing
Copper alloys are increasingly significant in the 3D printing industry, known for their excellent thermal and electrical conductivity, making them ideal for a wide range of applications, including electronics, heat exchangers, and aerospace components. The unique properties of copper alloys, such as high thermal conductivity, corrosion resistance, and mechanical strength, offer valuable benefits in 3D printed parts.
Advantages of Copper Alloys in 3D Printing
High Thermal Conductivity
Copper's high thermal conductivity is essential for components like heat sinks and exchangers, facilitating efficient heat dissipation.
Electrical Conductivity
Ideal for electrical applications, copper alloys are used in producing connectors, coils, and other conductive components.
Corrosion Resistance
Copper alloys resist various corrosive environments, making them suitable for marine and chemical processing applications.
Mechanical Strength
When alloyed, copper maintains significant strength, offering durability and longevity for functional parts.
Challenges and Solutions
While copper's high thermal conductivity presents advantages, it also poses challenges for 3D printing, including rapid heat dissipation that can affect the print quality. Advanced 3D printing techniques, such as Laser Powder Bed Fusion (LPBF) and Direct Energy Deposition (DED), have been adapted to manage these challenges effectively. Printers equipped with high-power lasers or adjusted energy densities ensure consistent melting and solidification of copper alloys.
Applications of Copper Alloys in 3D Printing
Copper alloys are utilized in various sectors, including:
Electronics
For creating conductive pathways and components.
Automotive
In manufacturing heat exchangers and electrical components.
Aerospace
For lightweight, thermally efficient parts.
Energy
In components for renewable energy sources, benefiting from copper's conductivity.
The versatility and efficiency of copper alloys in 3D printing continue to expand their applications, driving innovations in design and manufacturing processes.
Unionfab's Experitse
To learn more about Manufacturing processes, Contact a Unionfab representative.
Unionfab provides a wide range of manufacturing capabilities for all of your prototyping and production needs. Resquest a free and instant quote.