POM Material: A Versatile Engineering Plastic
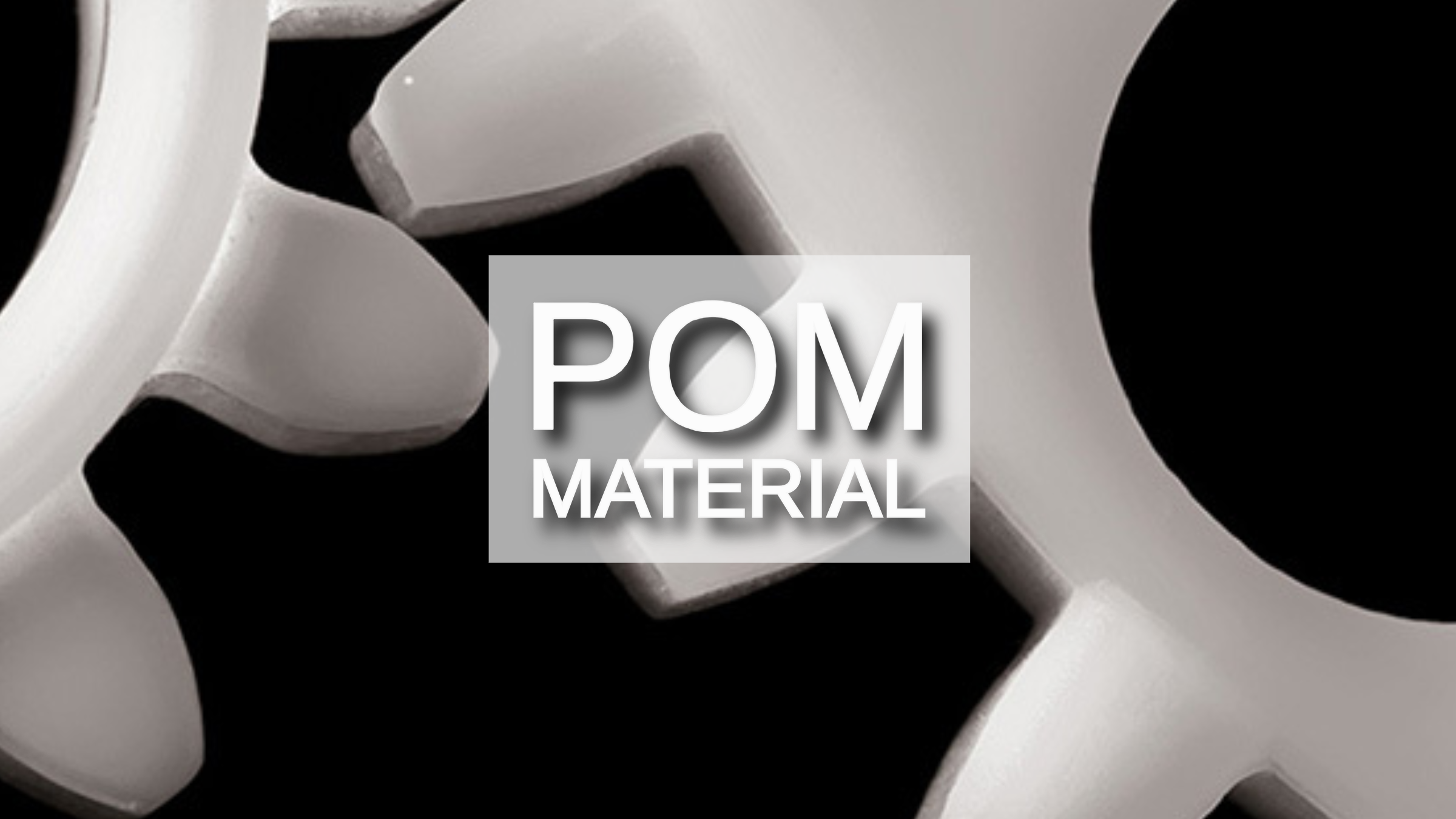
This guide explores POM material’s properties & uses in industries like automotive & consumer goods, revealing its significance for manufacturers.
Introduction
POM material is a semi-crystalline thermoplastic, boasting high mechanical strength, dimensional stability, and low friction, ideal for various applications including gears and precision parts.
Its cost-effectiveness, versatility, and functional performance make it indispensable in manufacturing, offering reliable functionality and design flexibility across industries from automotive to medical devices.
What is POM Material
Definition and Composition
POM, or polyacetal, is a semi-crystalline engineering thermoplastic derived from formaldehyde (CH2O)n. Its molecular structure includes a carbon atom bonded to two -OR groups, giving it both crystalline and amorphous regions.
This unique composition contributes to its notable properties, including good dimensional stability.
Types of POM Material
POM-H (Homopolymer): This is the standard POM variety, known for its well-balanced mechanical properties, good chemical resistance, and natural white color.
POM-C (Copolymer): This type offers even higher chemical resistance and improved long-term dimensional stability compared to POM-H. However, it has slightly lower mechanical strength.
Improving POM Material with Additives
Additionally, POM can be modified with various additives like:
Glass fibers: Enhance stiffness and dimensional stability
Lubricants: Improve wear resistance and sliding properties
Flame retardants: Increase fire resistance
These modifications result in a wider range of POM materials suitable for specific applications.
Properties of POM Material
TL;DR: The following chart provides a summary of the content for an easy read.
Category | Property | Description |
---|---|---|
Mechanical | Strength and Durability | High |
Impact Resistance | Good | |
Friction | Low coefficient | |
Wear Characteristics | Excellent | |
Thermal | Melting Point | High |
Temperature Resistance | Good | |
Thermal Expansion | Low coefficient | |
Chemical | Resistance to Chemicals and Solvents | Good |
Hydrolysis Resistance | Good | |
Electrical | Dielectric Strength | Good |
Insulating Properties | High |
Mechanical properties
POM is strong, durable, and tough, capable of withstanding stress without deforming. It offers decent impact resistance
,especially in cold conditions, and excels in low-friction and high wear scenarios, perfect for parts requiring durability in moving contacts.
Thermal properties
With a high melting point and consistent performance at temperatures up to 100°C, POM maintains its shape and
strength when exposed to heat. Its low thermal expansion rate ensures size stability despite temperature changes.
Chemical properties
Resistant to many chemicals including alcohols and hydrocarbons, POM is not compatible with strong acids and bases. It stands up well against hydrolysis, remaining stable in hot and humid conditions.
Electrical properties
POM has strong dielectric properties, effectively preventing electrical leaks, positioned well as an electrical insulator with high resistance to electrical conductivity.
Applications of POM Material
Automotive Industry
Interior Components: POM’s strength and abrasion resistance make it ideal for instrument panels, bushings, seat adjusters, armrests, door handles, and knobs.
Fuel System Parts: POM's toughness and chemical resistance suit fuel lines, rails, pump housings, valves, and sensor components.
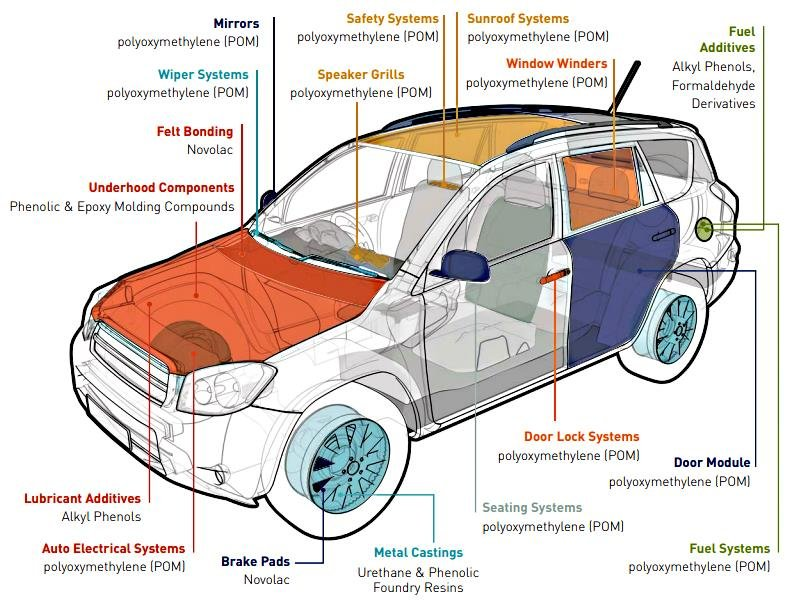
Source: researchgate.net
Consumer goods
Handles and Knobs: POM’s durability and resistance to deformation suit doorknobs, cabinet hardware, appliance knobs, levers, and tool handles.
Zippers and Fasteners: Its low friction and resilience make POM ideal for zipper sliders, teeth, coil springs, and snaps.
Engineering Applications
Gears and Bearings: POM’s stability and low friction fit gears, low-load bearings, and bushings.
Valve Components: Its chemical resistance suits valve seats, seals, bodies, and housings in various engineering applications.
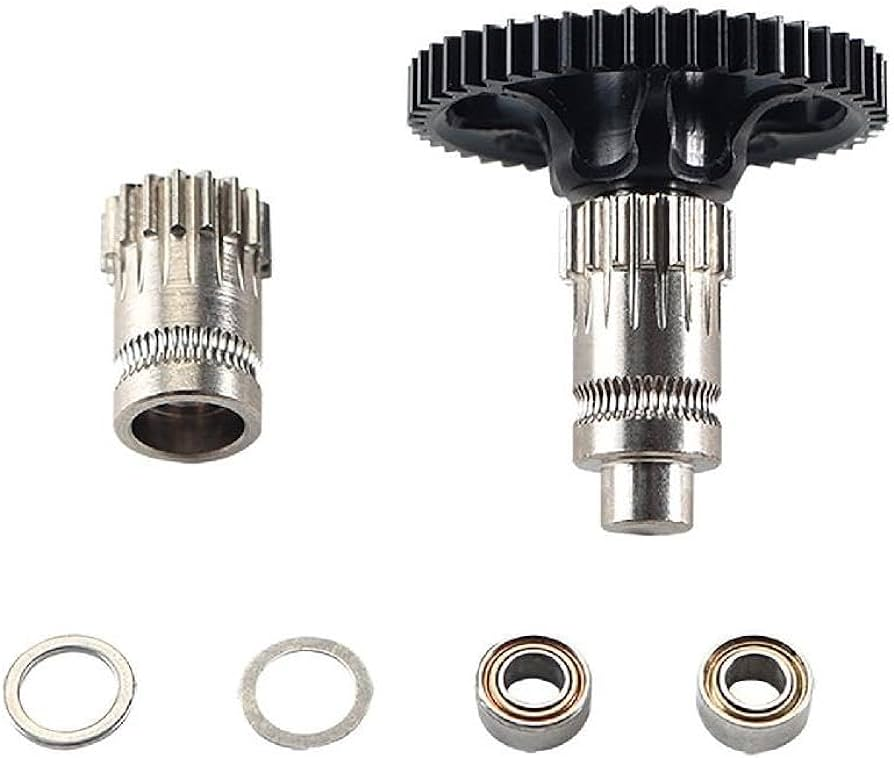
Source: amazon.com
Medical Devices
Surgical Instruments: POM’s biocompatibility and sterilizability suit handles and housings for surgical instruments.
Dental Applications: Its resistance to sterilization makes POM suitable for disposable dental tools and orthodontic retainers.
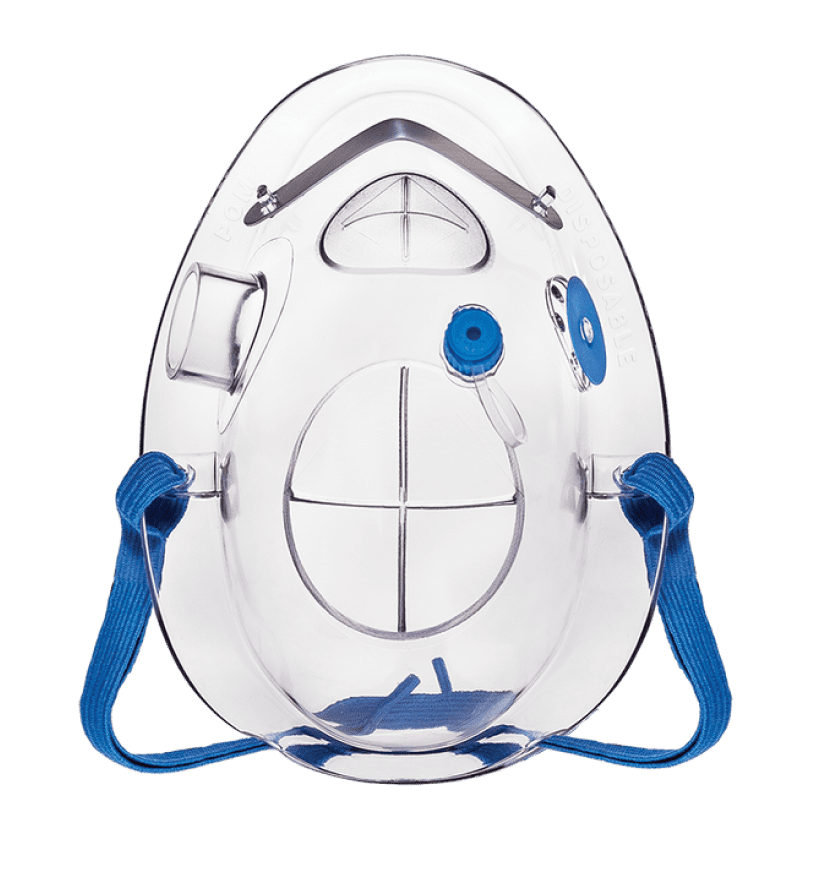
Source: proceduraloxygenmask.com
Advantages and Disadvantages of POM Material
Advantages of POM Material
High mechanical strength: POM is a tough and rigid plastic, making it suitable for parts that need to bear significant loads without deforming.
Excellent dimensional stability: POM retains its shape well even under varying temperatures and moisture conditions. This makes it ideal for precision parts.
Low coefficient of friction: POM has a slippery surface, reducing friction and wear in moving parts. This makes it useful for gears, bearings, and rollers.
Ease of machining and fabrication: POM can be easily machined using conventional tools and techniques. It can also be welded, threaded, and polished.
Disadvantages of POM Material
Poor chemical resistance: POM can be degraded by strong acids, bases, and solvents. This limits its use in environments with harsh chemicals.
High moisture absorption: While not as high as some nylons, POM can absorb moisture over time, which can affect its dimensional stability and mechanical properties.
Limited UV resistance: POM can degrade when exposed to ultraviolet light for extended periods. This makes it less suitable for outdoor applications.
Flammability: POM is flammable and will burn if exposed to an ignition source. It may not be suitable for applications with fire safety requirements.
Brittle at low temperatures: POM can become brittle and more susceptible to cracking at low temperatures.
Difficult to paint and bond: POM's low surface energy makes it challenging to make paints and adhesives adhere well. Special surface treatments may be required.
POM Material: Limitations and Considerations
Limitations Due to Water Absorption
Water absorption in POM leads to dimensional changes and weakened mechanical properties, requiring alternative materials for high-load or outdoor applications to ensure long-term performance.
Environmental Considerations
Exposure to chemicals or fluctuations in humidity and temperature affects water absorption in POM, potentially degrading the material.
Design Considerations
Maintaining uniform part thickness is vital for preserving dimensional stability and mechanical properties in POM. Surface treatments and alternative materials like PEEK can further mitigate water absorption issues, improving reliability.
POM Material Compared to other materials
POM Compared to Metals
Properties | POM | Metals |
---|---|---|
Weight | Lightweight | Heavier |
Corrosion Resistance | Excellent | Variable |
Friction | Low | Higher, may need lubricants |
Strength | Stiff, less strong than metals | Very high |
Thermal Conductivity | Low | High |
POM outperforms metals in several aspects: it’s lightweight, corrosion-resistant, and exhibits low friction properties.
Nonetheless, it falls short in terms of strength and thermal conductivity when compared to metals.
POM Compared to Other Plastics
Properties | POM | Other Plastics |
---|---|---|
Stiffness | Higher | Variable |
Friction | Low | May be higher |
Chemical Resistance | Good | Ranges widely |
Impact Strength | Good (esp. low temps) | Some plastics higher |
Temperature Resistance | Moderate | Some plastics higher |
POM exhibits distinct characteristics compared to other plastics. It boasts higher stiffness, ensuring precise part dimensions, and low friction for smooth movement. Additionally, POM offers good chemical resistance, making it suitable for harsh environments.
However, it falls short in impact strength when compared to some plastics, especially at low temperatures, and has limited temperature resistance, making it less ideal for high-temperature applications.
POM Compared to Engineering Polymers
Properties | POM | Engineering Polymers |
---|---|---|
Cost | Affordable | Typically higher |
Machinability | Easy | Can vary |
Stability | Excellent | Varies, some exceptional |
Temp Resistance | Moderate | Generally higher |
Chemical Resistance | Moderate | Often superior |
Strength (High Temperatures) | Lower | Usually remains strong |
POM stands out in comparison to engineering polymers. It offers advantages such as affordability, easy machinability, and excellent dimensional stability.
However, it has limitations including lower temperature resistance, limited chemical resistance, and reduced strength at elevated temperatures compared to engineering polymers.
Conclusion
Polyoxymethylene (POM), a versatile engineering plastic, offers high strength, stability, and ease of production. Its low friction and cost-effectiveness make it ideal for various components. However, limitations such as poor chemical resistance and brittleness in cold temperatures must be considered.
Despite these drawbacks, POM remains significant due to its balanced properties, finding use in gears, bearings, and other applications across industries, providing a competitive edge in cost-sensitive production environments.
Discover High-Performance Materials at Unionfab
Unionfab, a top-tier 3D printing company in the industry, offers a range of materials beyond POM, including high-performing PLA, PEEK, and Stratasys ULTEM™ 9085, allowing you to select the optimal solution.
Whether opting for 3D printing or traditional manufacturing techniques like CNC machining or vacuum casting, Unionfab seamlessly integrates your chosen material into the production process.
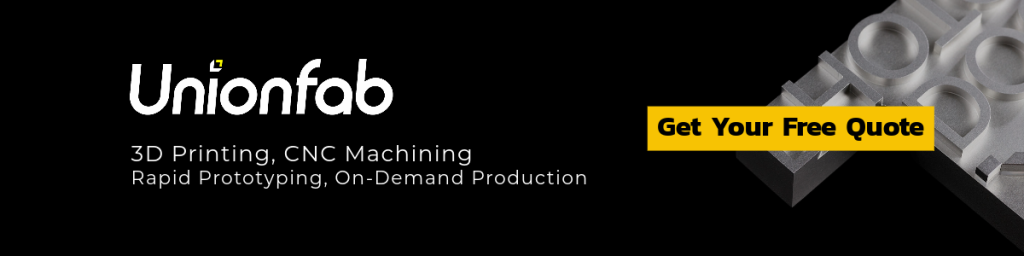