Additive vs. Subtractive Manufacturing: A General Comparison
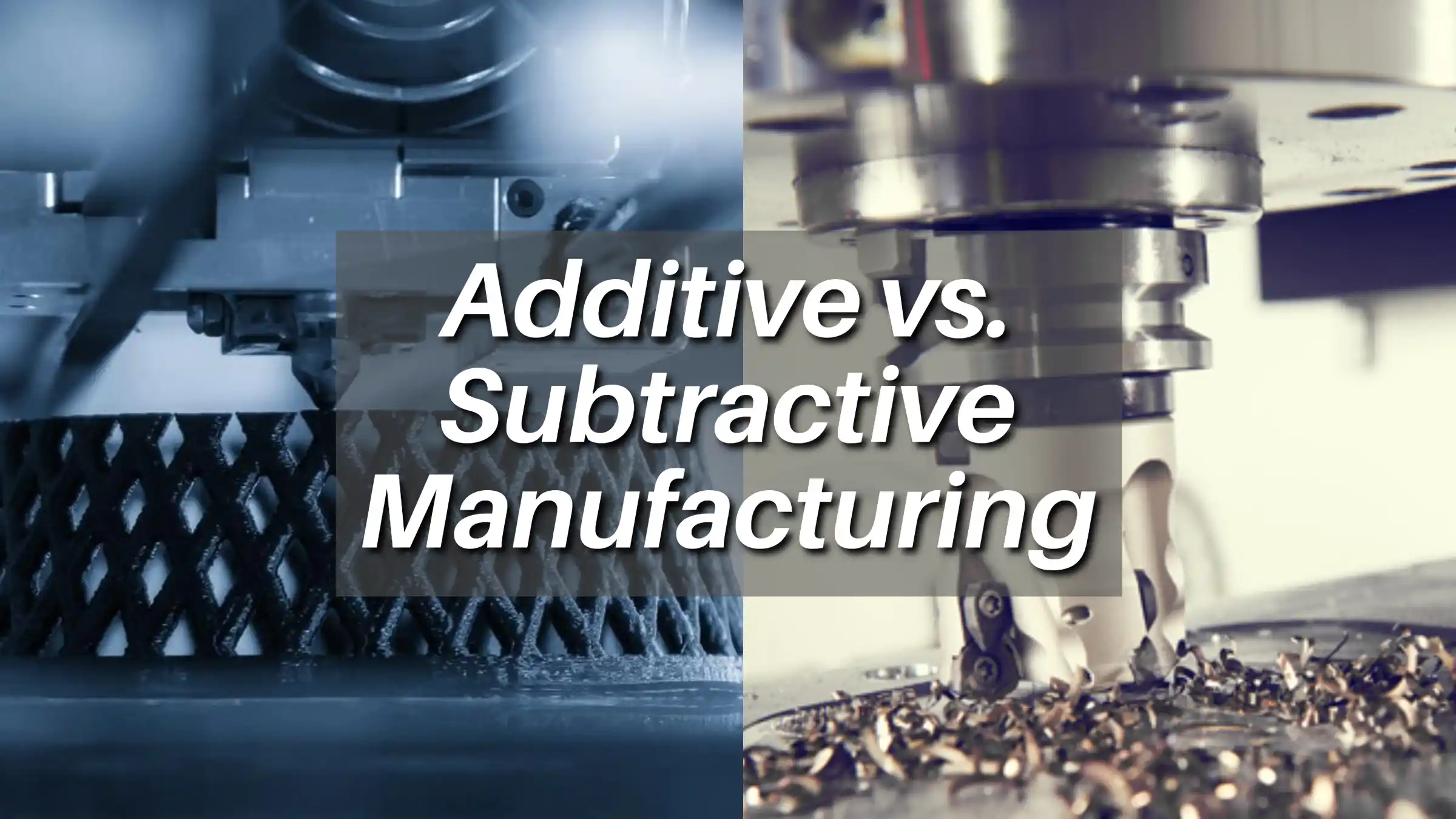
In this in-depth analysis, we explore the fundamental differences and applications of additive and subtractive manufacturing.
Introduction
Manufacturing methods have evolved, with additive manufacturing (AM) building objects layer by layer and subtractive manufacturing (SM) removing material from a solid block. Understanding their differences is crucial across industries for factors like design complexity and cost-effectiveness.
This guide compares AM and SM, exploring their principles, technologies, advantages, and applications, aiming to help readers make informed decisions and optimize production processes.
Understanding Additive Manufacturing
Definition and Principles
Additive manufacturing (AM), or 3D printing, creates objects by sequentially adding material layer by layer, guided by a digital 3D model.
This technique enables the production of complex geometries and intricate details that are difficult or impossible to achieve with traditional manufacturing, which typically involves subtracting material from a solid block.
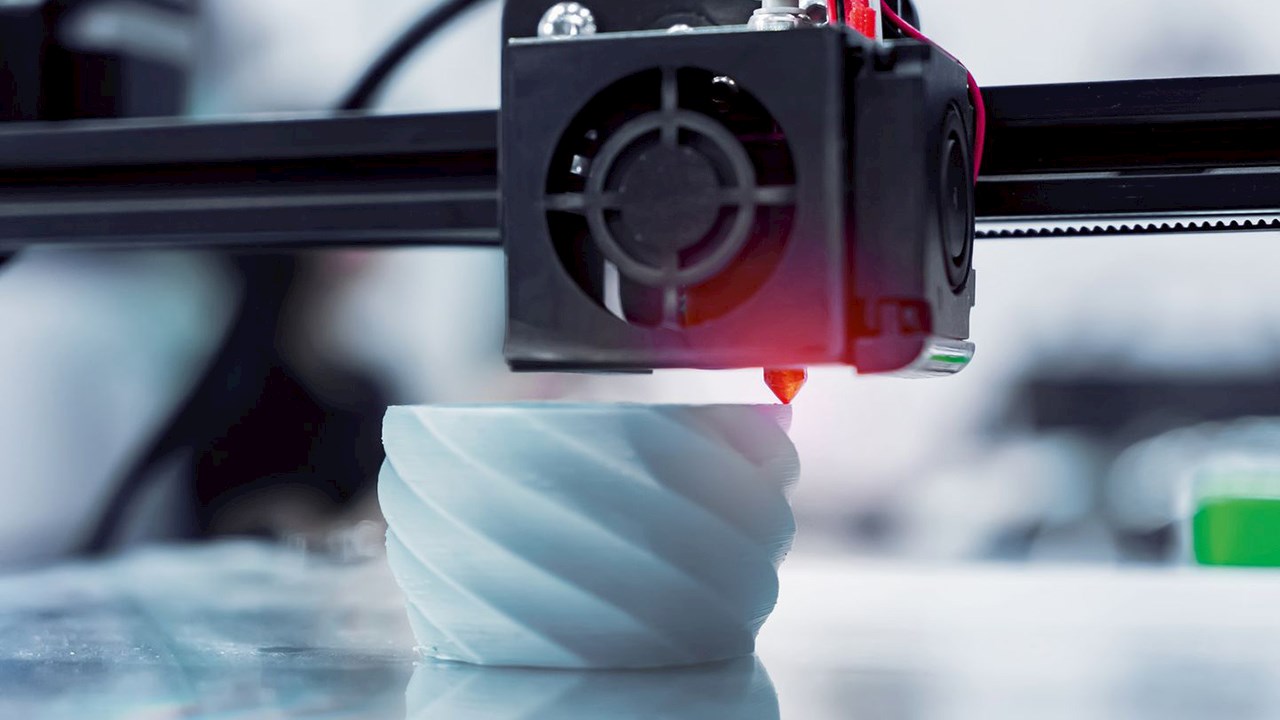
Source: new.abb.com
Historical Development
Additive manufacturing originated in the 1980s with stereolithography (SLA) by Charles Hull.
SLA uses UV light to cure photopolymer resin into solid layers, leading to the development of various AM technologies.
Today, AM is widely employed in aerospace, automotive, healthcare, and consumer goods for rapid prototyping and functional part production.
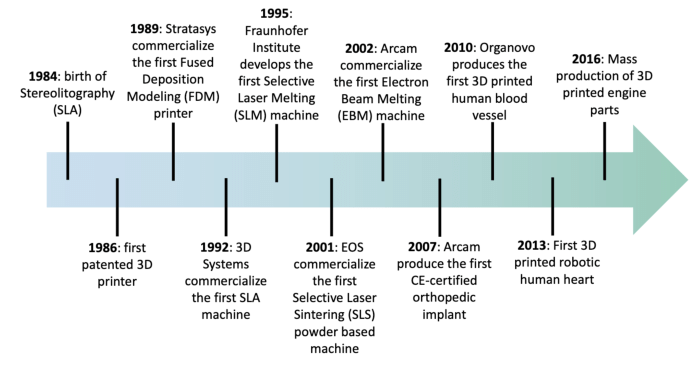
Source: researchgate.net
Key Technologies and Processes
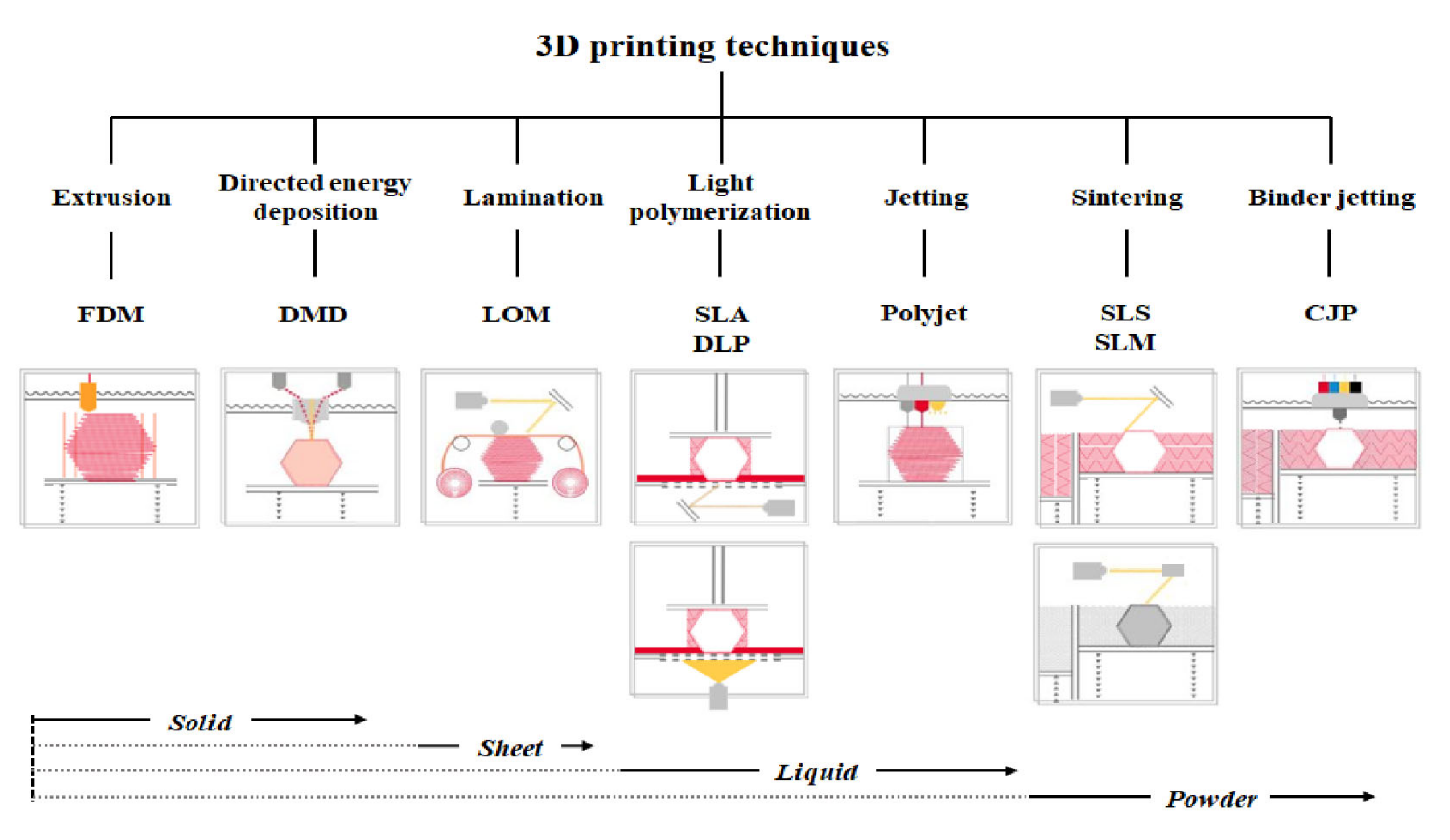
Source: mdpi.com
Powder Bed Fusion (PBF)
Powder Bed Fusion (PBF) encompasses various additive manufacturing technologies, including Selective Laser Melting (SLM) also called Direct Metal Laser Sintering (DMLS).
In PBF processes, a laser or electron beam selectively fuses powdered material to create solid objects layer by layer.
It is used in industries like aerospace and medical implants for high-strength components with intricate geometries.
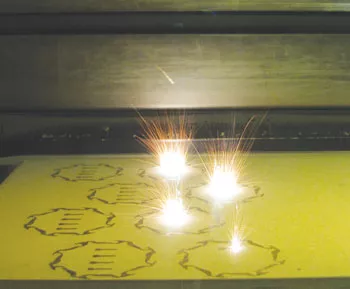
Source: canadianmetalworking.com
Stereolithography (SLA)
SLA uses a UV laser to cure liquid resin into solid layers, producing highly detailed and smooth parts.
It is used for prototypes, patterns, and high-precision parts in industries such as jewelry, dentistry, and engineering.
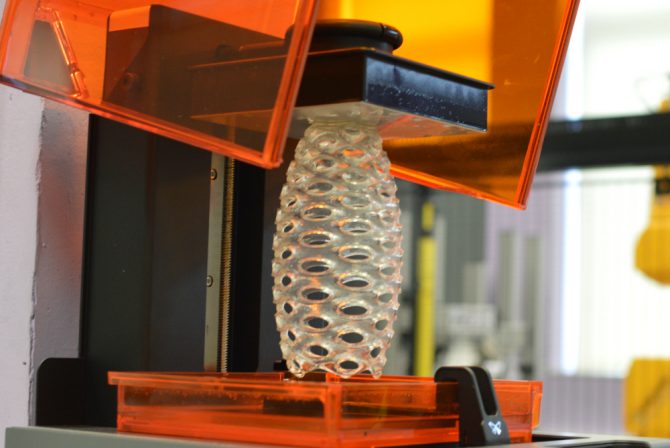
Source: re-fream.eu
Fused Deposition Modeling (FDM)
FDM extrudes thermoplastic filament through a heated nozzle, depositing material layer by layer.
It is widely accessible and used by hobbyists and professionals for prototyping, tooling, and small-scale production.
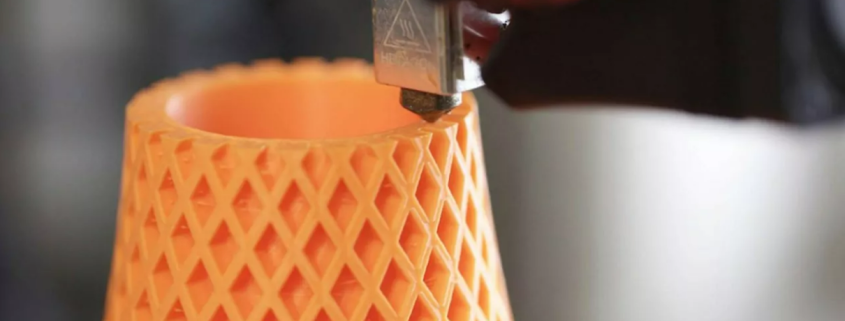
Source: rjcmold.com
Selective Laser Sintering (SLS)
SLS uses a laser to sinter powdered materials, such as plastics, ceramics, or metals, into a solid form layer by layer.
It is suitable for producing functional prototypes and end-use parts.
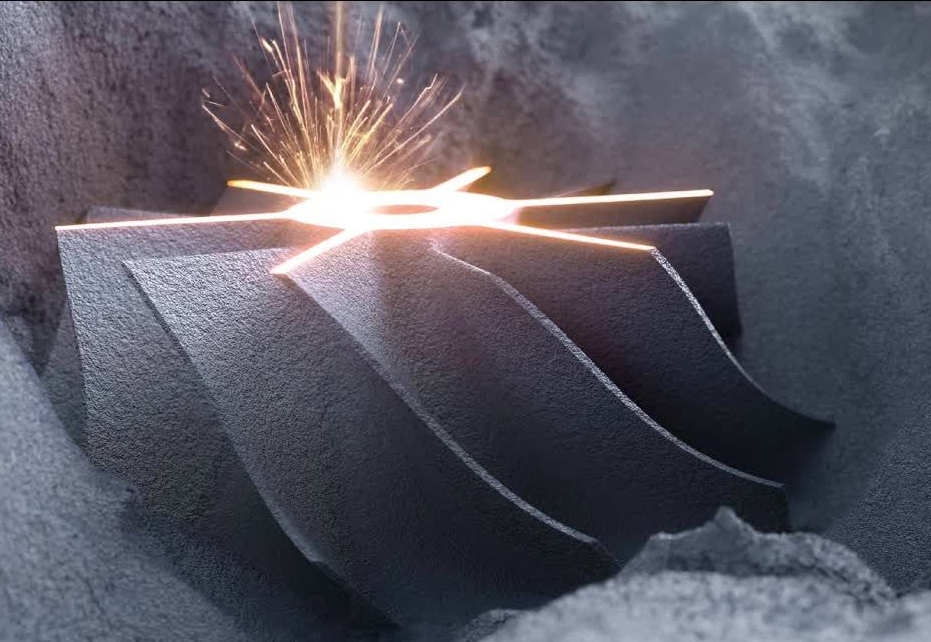
Source: rjcmold.com
Binder Jetting
In binder jetting, a liquid binding agent is selectively deposited onto a powder bed, bonding the powder together to create a solid part.
It is utilized for producing metal, sand, and ceramic parts with complex geometries.
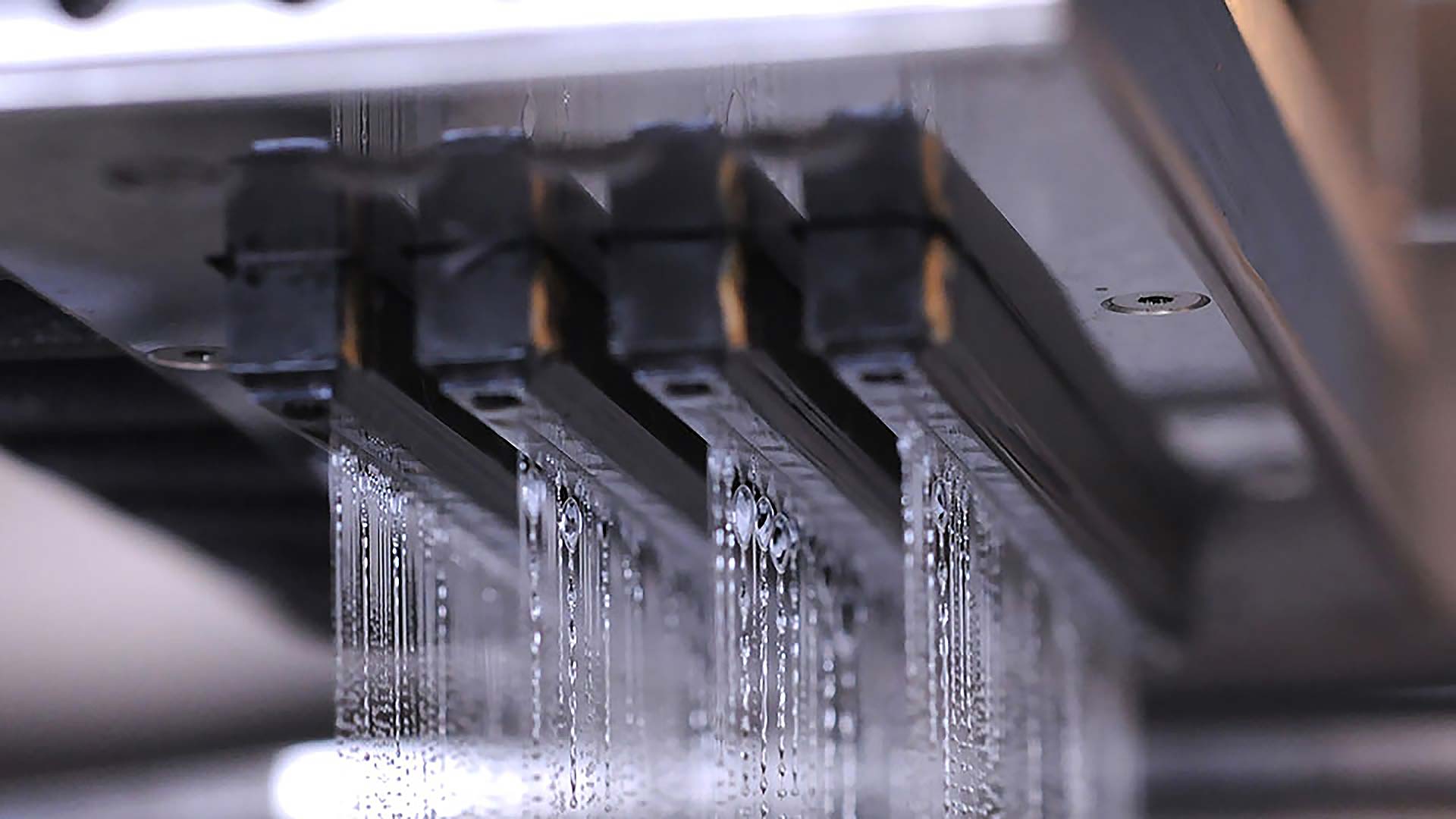
Source: exone.com
Other Advanced Additive Manufacturing Technologies:
Digital Light Processing (DLP): Similar to SLA, DLP uses a digital light projector to cure liquid resin into solid layers, offering high-resolution prints at faster speeds.
Multi Jet Fusion (MJF): MJF technology uses fusing agents and detailing agents applied by inkjet print heads to selectively fuse nylon powder, producing strong, precise, and functional parts.
PolyJet: PolyJet technology jets and cures droplets of liquid photopolymer onto a build tray, layer by layer, enabling the creation of parts with smooth surfaces and fine details.
Each of these technologies offers unique advantages and applications, contributing to the advancement and versatility of additive manufacturing in various industries.
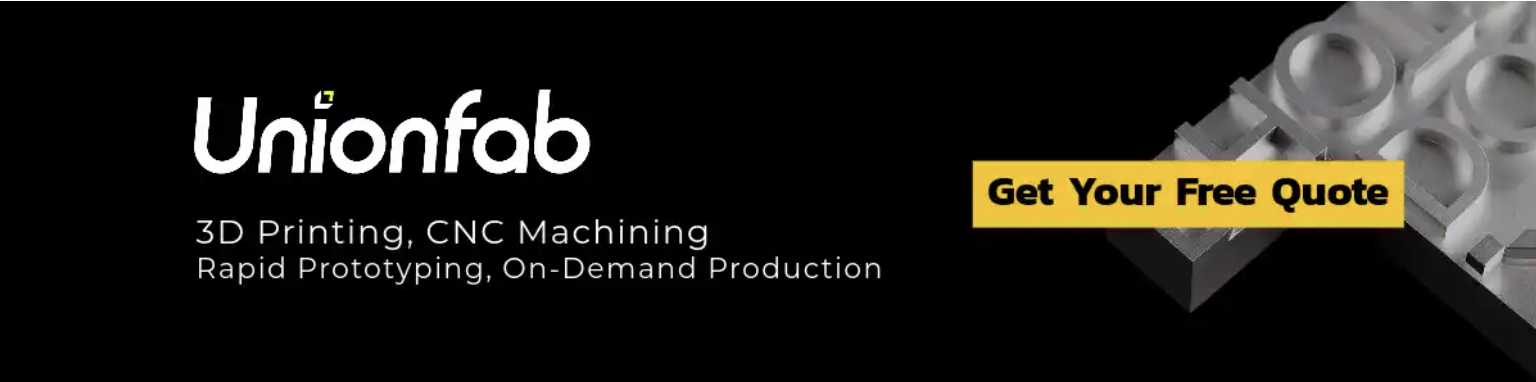
Materials Used in Additive Manufacturing
Additive manufacturing employs a diverse array of materials, each selected for its unique properties and suitability for specific applications. The primary categories of materials used in this technology include:
Resins
UV-curable resins are used in stereolithography (SLA) and digital light processing (DLP) printers to produce high-resolution, smooth-surfaced parts for applications like dental models and intricate jewelry.
Standard Resin (White), Rigid Resin (White), Casting Resin, and Rubber-like Resin are among the types of resins commonly utilized in these additive manufacturing processes, each offering specific properties suited for different applications.
Metals
Titanium (TC4): Valued for its high strength-to-weight ratio, corrosion resistance, and biocompatibility, titanium is frequently used in aerospace, medical implants, and high-performance engineering applications.
Stainless Steel: Renowned for its strength, durability, and corrosion resistance, stainless steel finds applications across industries including tooling, automotive, and aerospace, with variants like Stainless Steel 316L and Stainless Steel 17-4PH offering specific advantages.
Aluminum (Alsi10Mg): Known for its lightweight and excellent thermal conductivity, aluminum is used in applications ranging from aerospace components to automotive parts.
Polymers
ABS (Acrylonitrile Butadiene Styrene): Known for its strength and durability, ABS is commonly used in desktop 3D printers for prototyping and end-use parts.
PLA (Polylactic Acid): This biodegradable polymer is favored for its ease of use, lower printing temperature, and environmental friendliness, making it popular in consumer-level 3D printing.
Nylon (Polyamide): Valued for its flexibility, durability, and resistance to abrasion, nylon is used for creating functional prototypes, gears, and other mechanical components. This includes variants like MJF Nylon 12 and SLS Nylon 11.
PC (Polycarbonate): Known for its high impact resistance and strength, polycarbonate is used in applications requiring durability and thermal stability.
Composites
Composites combine two or more materials to achieve enhanced properties.
For example, carbon fiber-reinforced nylon offer exceptional strength and stiffness while remaining lightweight, making them ideal for automotive, aerospace, and sporting goods.
Others
Ceramics: Ceramics, including Silica utilized in investment casting molds and for producing high-precision, high-strength parts, and Alumina (Aluminum Oxide), renowned for its hardness and high-temperature resistance, employed in wear-resistant components and electronic substrates.
Wax: Used primarily in investment casting, wax patterns are created through additive manufacturing to produce highly detailed and complex molds for metal casting.
Sand: Used in binder jetting processes to create sand molds and cores for metal casting, allowing for complex geometries and quick turnaround times.
Each of these materials brings distinct advantages to additive manufacturing, enabling the creation of complex, customized, and high-performance components across a wide range of industries.
Advantages and disadvantages of Additive Manufacturing
Advantages of Additive Manufacturing
Flexibility in Design: Additive manufacturing allows for intricate geometries and complex structures, fostering innovation and optimized product design.
Reduced Waste: By building layer by layer, additive manufacturing minimizes material wastage compared to subtractive methods, contributing to sustainability efforts and cost savings.
Customization Capabilities: It enables the creation of customized parts tailored to individual needs, particularly valuable in fields like healthcare for patient-specific solutions.
Rapid Prototyping: Additive manufacturing accelerates the prototyping process, facilitating faster product development cycles and reducing time-to-market for new innovations.
Disadvantages of Additive Manufacturing
Material Limitations: While offering a range of materials, additive manufacturing options may still be limited compared to traditional methods, affecting suitability for certain applications.
Surface Finish and Tolerances: Achieving desired surface finishes and dimensional tolerances may require post-processing, adding time and cost to production.
Production Speed for Large Volumes: Additive manufacturing is generally slower for large-scale production runs compared to traditional methods, potentially limiting its efficiency in mass production scenarios.
Cost Considerations: Initial setup costs and per-part expenses can be high, prompting careful evaluation of cost-effectiveness for specific applications and production volumes.
Understanding Subtractive Manufacturing
Definition and Principles
Subtractive manufacturing is a process where material is removed from a solid block, or workpiece, to create the desired shape.
This is done using various cutting, grinding, and drilling tools. The process is guided by digital or manual instructions to achieve precise dimensions and geometries.
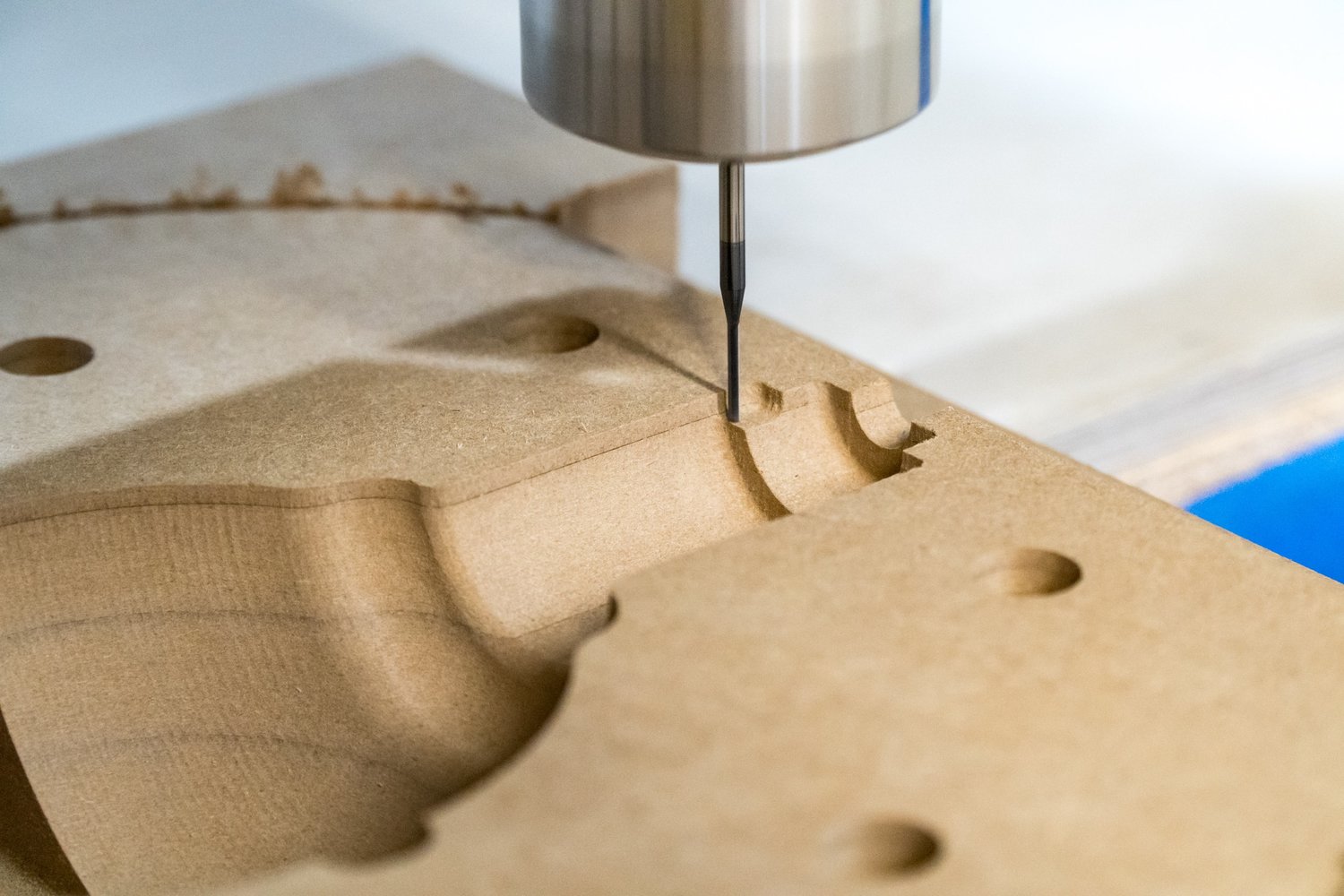
Source: architizer.com
Historical Development
Subtractive manufacturing has roots in ancient crafting techniques, but it significantly advanced during the Industrial Revolution with the development of machine tools.
The introduction of Computer Numerical Control (CNC) in the mid-20th century revolutionized the field, allowing for higher precision and automation.
Key Technologies and Processes
Milling
Milling involves rotating multi-point cutting tools to remove material from a workpiece, producing flat or contoured surfaces.
It is versatile and widely used for creating complex parts with various shapes and sizes.
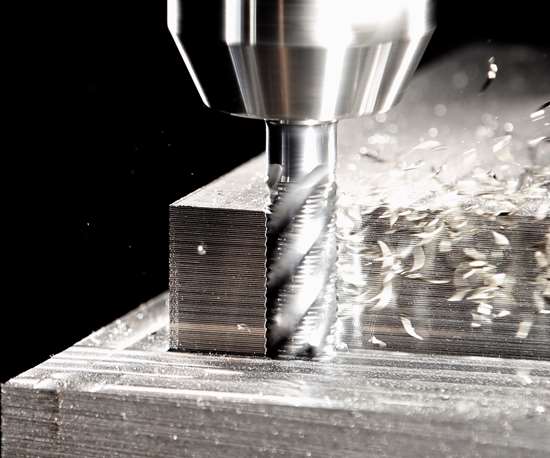
Source: productionmachining.com
Turning
Turning uses a single-point cutting tool to remove material from a rotating workpiece, typically producing cylindrical shapes.
It is essential for manufacturing components like shafts, bolts, and other symmetrical parts.
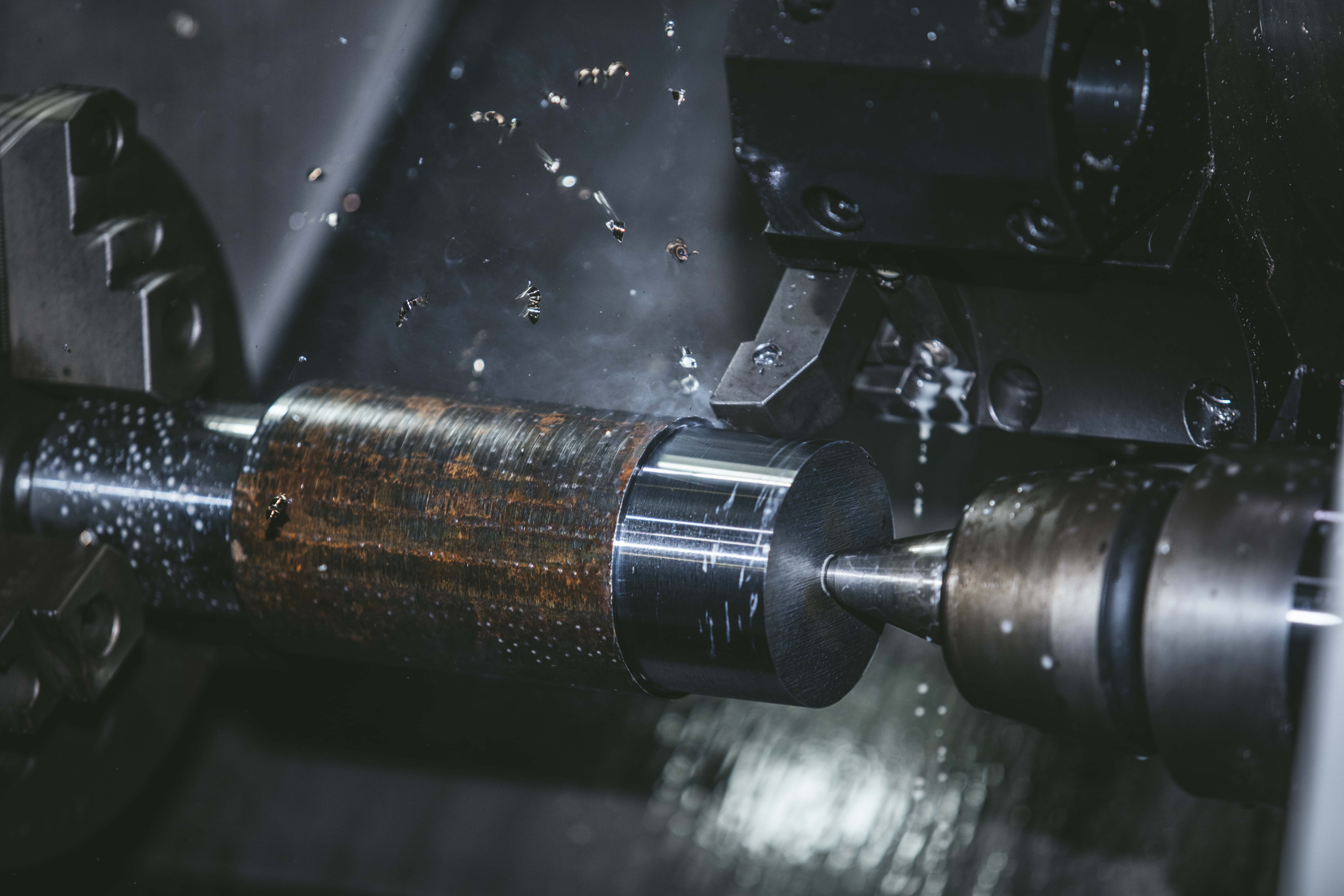
Source: pepmfg.us
Drilling
Drilling involves creating round holes in a workpiece using a rotating drill bit. It is a fundamental process for making holes of various diameters and depths in a wide range of materials.
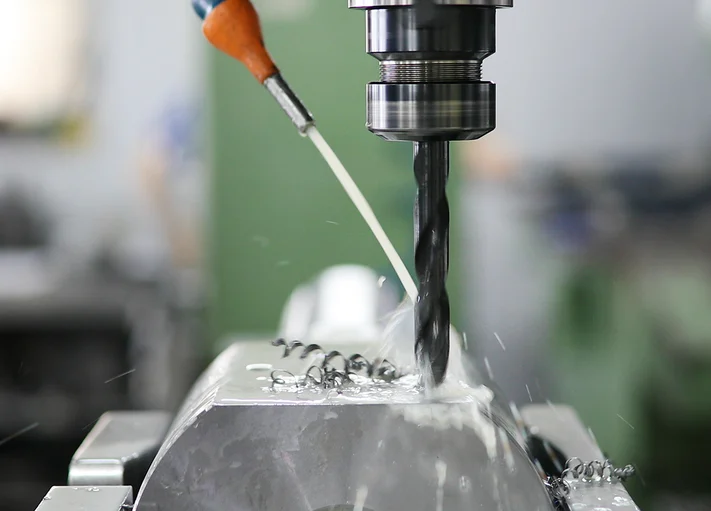
Source: blog.eaglegroupmanufacturers.com
CNC machining employs computer-controlled machines to perform milling, turning, drilling, and other subtractive processes with high precision. This technology enhances efficiency, repeatability, and accuracy in manufacturing complex parts, ensuring consistent quality and tight tolerances.
Additionally, CNC machining is versatile, capable of working with a wide range of materials, including metals, plastics, and composites, making it indispensable in industries such as aerospace, automotive, and medical device manufacturing.
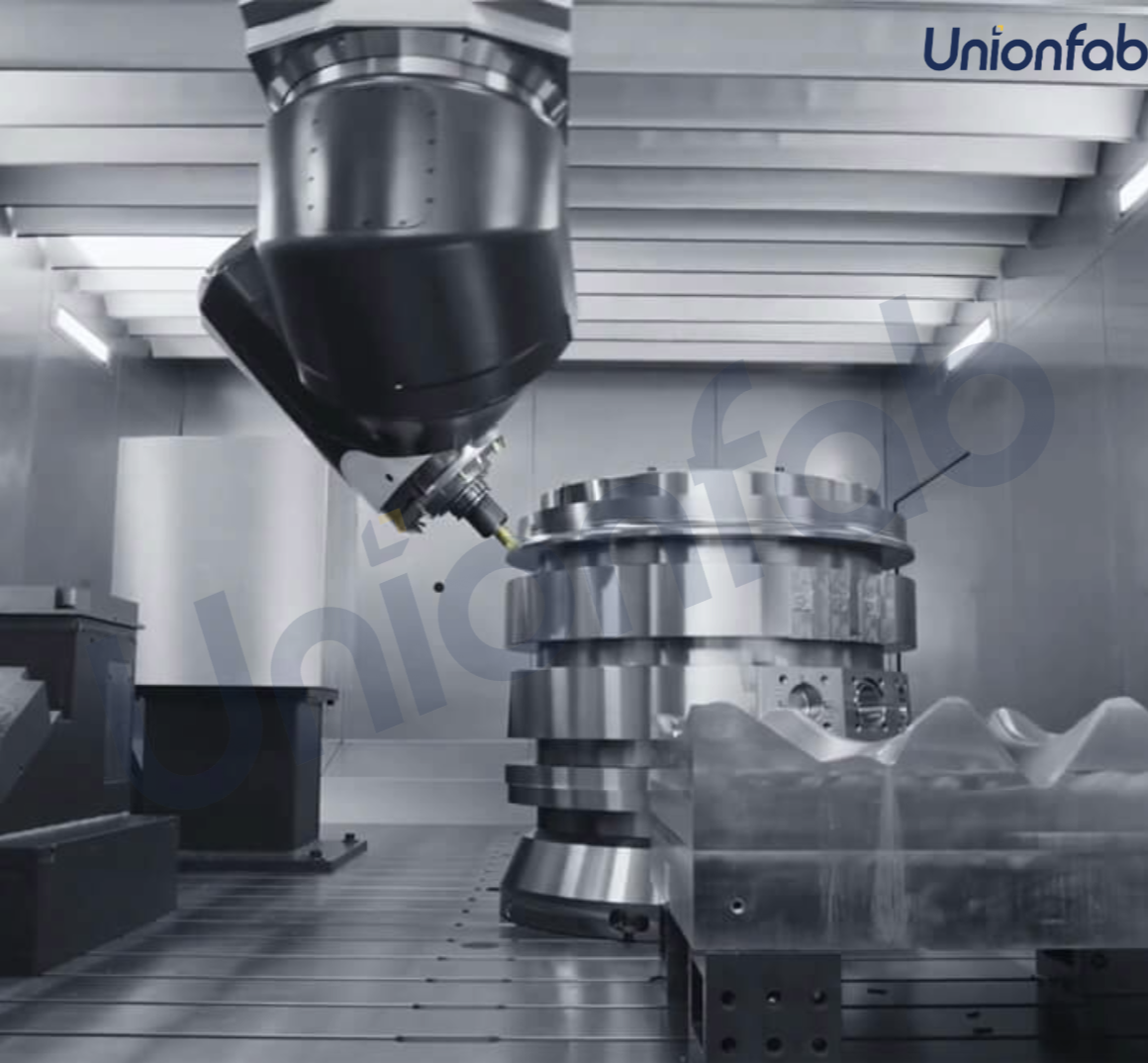
Materials Used in Subtractive Manufacturing
Subtractive manufacturing can work with a wide range of materials, including metals (steel, aluminum, titanium), plastics, wood, and composites.
Metals: Steel is used for its strength and durability in automotive, construction, and machinery; aluminum for its lightweight and corrosion resistance in aerospace, automotive, and electronics; and titanium for its high strength-to-weight ratio and biocompatibility in aerospace, medical implants, and high-performance engineering.
Plastics: Acrylics, ABS, and Polycarbonate are used in a variety of applications from prototyping to production parts in industries such as consumer goods, medical devices, and automotive.
Wood: Various types of wood are used in furniture making, architectural models, and custom woodworking projects, with hardwood and softwood selections depending on the required strength and aesthetic qualities.
Composites: Composites, such as Carbon Fiber Reinforced Polymers (CFRP) and Glass Fiber Reinforced Polymers (GFRP), are widely used in various industries for their exceptional strength-to-weight ratios and versatility.
The choice of material depends on the desired properties of the final product and the capabilities of the cutting tools.
Advantages and disadvantages of Subtractive Manufacturing
Advantages of Subtractive Manufacturing
Precision and Accuracy: Subtractive manufacturing, notably CNC machining, ensures tight tolerances and high-quality finished parts.
Material Versatility: Subtractive manufacturing works with a wide range of materials, offering flexibility based on application needs.
Superior Surface Finish: Subtractive techniques often yield better surface finishes than some additive methods, ideal for applications requiring smooth surfaces or tight tolerances.
Established Technology: With decades of development, subtractive manufacturing benefits from a skilled workforce proficient in operating CNC machines, ensuring reliable production processes.
Disadvantages of Subtractive Manufacturing
Material Waste: Subtractive processes generate significant material waste, increasing costs and posing environmental concerns if not managed properly.
Tooling Complexity and Cost: Specialized tooling required for subtractive manufacturing, such as cutting tools and fixtures, can be costly to purchase and maintain. Setup and calibration add further time and expense.
Design Limitations: While precise, subtractive methods may struggle with complex geometries and internal features compared to additive techniques, restricting design options, especially for intricate shapes.
Comparative Analysis: Additive vs Subtractive Manufacturing
Aspect | Additive Manufacturing (AM) | Subtractive Manufacturing (SM) |
---|---|---|
Process | Layer-by-layer construction | Carving from solid blocks |
Digital design & printer prep | Precise workpiece setup & CNC programming | |
Economics | Lower initial investment | Higher initial investment |
Cost per unit favors smaller batches | Cost-effective for larger production runs | |
Environmental Impact | Minimizes material waste | Generates substantial waste |
Enhances sustainability through recycling | Poses challenges for disposal & recycling | |
Performance | Flexibility for prototypes & complex designs | Slower speed for high-volume production |
Suitable for intricate geometries & customization | Efficiency & precision in mass production |
Comparison Table: Additive vs Subtractive Manufacturing

Source: researchgate.net
Process Comparison
In additive manufacturing (AM), objects are built layer by layer from a digital model, streamlining setup with digital design and printer preparation.
Contrastingly, subtractive manufacturing (SM) involves carving shapes from solid blocks, necessitating precise workpiece setup and CNC machine programming.
Scalability Comparison
In terms of scalability, additive manufacturing (AM) provides remarkable flexibility, particularly for prototyping and intricate designs. However, its efficiency diminishes when it comes to high-volume production due to its inherently slower speed.
On the other hand, subtractive manufacturing (SM) shines in mass production scenarios, especially after the initial setup is complete. Once the machinery is calibrated and ready to go, SM processes can churn out large quantities of simpler parts with remarkable efficiency and precision.
Economic Comparison
Initial Investment: AM generally requires a lower initial investment, especially for desktop 3D printers, compared to the significant investment needed for high-precision CNC machines and setup in subtractive manufacturing (SM).
Cost Efficiency: AM is more cost-effective for small batch production and prototyping due to its material efficiency and minimal tooling requirements. In contrast, SM becomes more economical for larger production runs as setup costs are spread over many units.
Material and Production Costs: While AM materials can be expensive and the process slower, it minimizes waste and allows for high customization. SM, on the other hand, uses cheaper materials but generates more waste and offers faster production speeds, making it ideal for large-scale manufacturing.
Environmental Impact
Additive Manufacturing (AM) AM minimizes waste by using only necessary materials, enhancing sustainability through recycling possibilities.
It enables precise material usage, reducing environmental footprints associated with excess material production and disposal.
Subtractive Manufacturing (SM) - Including CNC Machining In contrast, SM, especially CNC machining, generates substantial waste through material removal, posing challenges for disposal and recycling efforts.
This excess material production contributes to environmental concerns such as increased energy consumption and pollution.
CNC machining exacerbates these challenges due to its reliance on material removal processes, emphasizing the environmental benefits of additive manufacturing methods like 3D printing.
Additive vs Subtractive Manufacturing: Applications
Industries Using Additive Manufacturing
Aerospace
Applications: Aerospace companies use additive manufacturing to produce lightweight components, complex geometries, and custom parts that would be difficult or impossible to create with traditional manufacturing methods. Examples include engine components, turbine blades, and lightweight structural parts.
Benefits: Significant weight reduction, which is crucial for fuel efficiency, and the ability to rapidly prototype and test new designs.
Medical and Dental
Applications: In the medical field, additive manufacturing is used for custom implants, prosthetics, surgical guides, and dental crowns. It allows for patient-specific solutions that are tailored to individual anatomy.
Benefits: Customization to patient needs, rapid production of prototypes, and the ability to produce complex structures like porous implants that promote tissue integration.
Automotive
Applications: The automotive industry uses additive manufacturing for prototyping, tooling, and the production of complex parts like custom brackets and fixtures. It is also used in the production of end-use parts for high-performance and luxury vehicles.
Benefits: Rapid prototyping, reduced lead times, cost-effective low-volume production, and the ability to create lightweight structures.
Consumer Goods
Applications: Additive manufacturing is increasingly used to produce consumer products such as custom jewelry, eyewear, footwear, and home decor items. It allows for mass customization and on-demand production.
Benefits: Customization, design flexibility, and the ability to quickly bring new products to market.
Industries Using Subtractive Manufacturing
Aerospace
Applications: The aerospace industry relies on subtractive manufacturing for producing critical, high-precision components such as turbine blades, engine parts, and structural elements. These parts often require tight tolerances and superior surface finishes.
Benefits: High precision, superior material properties, and excellent surface finish, which are essential for safety-critical aerospace components.
Automotive
Applications: Subtractive manufacturing is used in the automotive industry for producing engine blocks, transmission components, and other high-precision metal parts. It is also used for creating molds and dies for plastic injection molding.
Benefits: Precision, repeatability, and the ability to work with a wide range of materials, including metals and alloys.
Defense
Applications: In the defense sector, subtractive manufacturing is used to produce high-strength components for weapons systems, military vehicles, and aircraft. Components such as gun barrels, armor plating, and missile parts often require the precision and material integrity that subtractive methods provide.
Benefits: The ability to produce high-strength, high-precision parts necessary for defense applications, along with superior reliability and durability.
Heavy Equipment
Applications: Subtractive manufacturing is used to produce large, robust components for heavy machinery and equipment used in construction, mining, and agriculture. Examples include hydraulic components, engine parts, and structural frames.
Benefits: Durability, ability to handle large-scale parts, and the capability to work with very hard materials that can withstand harsh operating conditions.
Future Trends and Innovations
Technological Advancements
Additive Manufacturing (AM) Advancements in multi-material printing and increased printer speed and build volume are making AM more versatile and efficient.
Improved post-processing techniques enhance the surface finish and mechanical properties of AM parts, expanding their application range.
Subtractive Manufacturing (SM) Innovations in high-speed machining and adaptive control systems optimize material removal and performance.
Cutting-edge developments in cutting tools and coatings enable SM to handle advanced materials more effectively.
Integration of Additive and Subtractive Methods
Hybrid machines that combine additive and subtractive capabilities offer greater manufacturing flexibility.
Integrating both methods optimizes workflows, reduces lead times, and improves part quality.
Emerging Materials and Processes
New advanced polymers, composites, and metal alloys are being developed to enhance the performance and reliability of AM parts.
Functional gradients within parts are being created to meet specific performance needs.
The Future of Manufacturing
The future of manufacturing involves integrated design and manufacturing processes for rapid, efficient production.
Smart manufacturing systems utilizing IoT, AI, and machine learning will optimize production, while sustainability efforts will focus on material recycling and energy efficiency.
Conclusion
In summary, additive and subtractive manufacturing offer unique benefits, with additive excelling in customization and rapid prototyping, while subtractive ensures precision and efficiency for high-volume production.
As manufacturing evolves, integrating both methods and adopting new technologies will be essential for maximizing efficiency and sustainability.
Thus, a strategic approach is crucial for leveraging these advancements and staying competitive in the ever-changing manufacturing landscape.
Streamlining Manufacturing: Unionfab's Comprehensive Solutions
Unionfab, a leading company in the realm of 3D Printing, is committed to delivering top-notch 3D printing solutions to meet the diverse needs of our clients.
With our expertise in additive manufacturing (AM) and computer numerical CNC Machining, we ensure optimal efficiency and precision in the production process.
Contact us today for further information on how we can assist you in achieving your manufacturing goals.