New Trends of Ultem 3D Printing in 2024
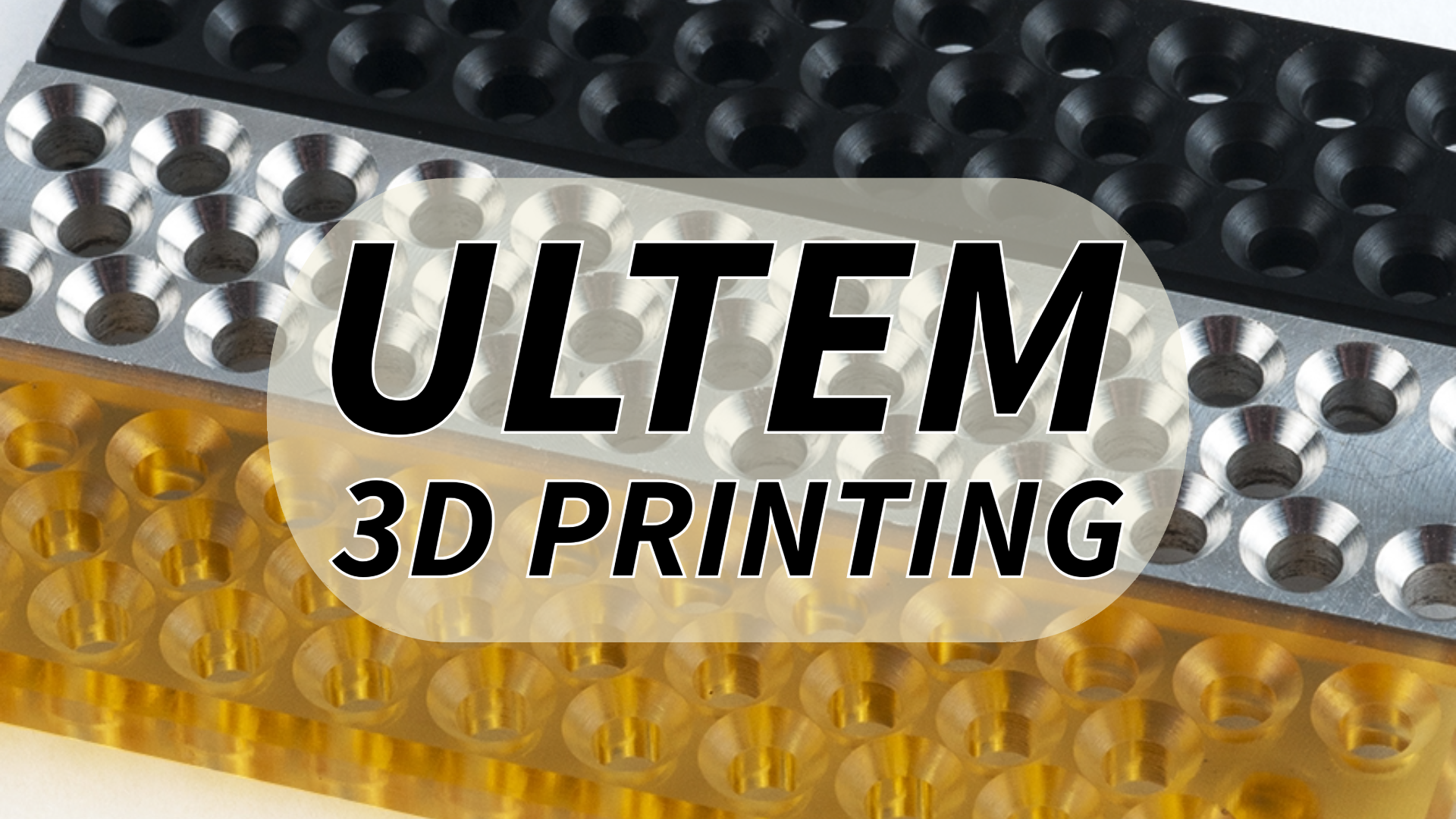
Discover the basics of Ultem 3d printing and its new trends of multi-material 3d printing in 2024.
TL;DR: Scroll down to the end to pin down the new trend of multi-material Ultem 3D printing and discover how the sandwich ULTEM-PC-ULTEM composite, could be a cost-effective alternative to pure ULTEM 9085.
Introduction
Ultem 3D printing is becoming popular in industries that need strong, heat-resistant materials. Known for its durability and toughness, Ultem is widely used in aerospace, automotive, and medical fields, where regular plastics can’t handle the stress.
This article will explain what Ultem is, compare different types, explore 3D printing technologies that work with Ultem, and share key printing tips. We’ll also look at the pros, cons, and common uses of Ultem 3D printing, along with new trends in the field.
What is Ultem?
Ultem, the branded name for polyetherimide (*PEI), is a high-performance plastic that has been a staple in manufacturing for over 35 years.
Originally developed by General Electric’s Plastics Division (now SABIC) in the early 1980s, Ultem is known for its strength, durability, and exceptional resistance to heat and chemicals. Its ability to maintain mechanical integrity at high temperatures makes it an ideal material for demanding applications in industries like aerospace, automotive, and medical, where conventional plastics may fall short.
(*To get to know the relationship between ULTEM and PEI, you can refer to the article: What is Ultem?)
Grades and Properties of Ultem
After understanding what ULTEM is, let’s first take a look at a concise table summarizing its key properties. The table highlights Ultem’s core characteristics in areas such as thermal stability, mechanical strength, and chemical resistance, helping to explain why it is widely used in demanding industrial applications.
Property | Description |
---|---|
Color | Black; Natural amber; Brown |
Thermal Stability | High glass transition temperature (~217°C). |
Mechanical Strength | Strong tensile strength and stiffness. |
Flame Retardancy | Excellent flame resistance with low smoke and toxicity. |
Chemical Resistance | Resists many harsh chemicals and hydrolysis. |
Electrical Insulation | Great dielectric strength and stability across frequencies. |
Dimensional Stability | Maintains shape and size under stress and temperature changes. |
Applications | Used in aerospace, automotive, medical devices, and 3D printing. |
The Ultem family of resins includes a variety of grades designed for different applications. Here, we will present the properties of the most well-known and commonly-used 4 types: Ultem™ 1000, Ultem™ 9085, Ultem™ 1010, Ultem™ 2200.
Property | ULTEM™ 1000 | ULTEM™ 1010 | ULTEM™ 2200 | |
---|---|---|---|---|
Glass Transition Temperature (°C) | 217°C | 186°C | 216°C | 217°C |
*Tensile Strength (MPa) | 110 MPa | 90 MPa | 100 MPa | 170 MPa |
* Flexural Modulus (GPa) | 3.3 GPa | 2.15 GPa | 3.2 GPa | 5.5 GPa |
Flame Retardancy | Standard | Aerospace-grade | Food/medical grade | Glass-filled |
Advantage | Good all-around performance | Excellent (low) flame, smoke, and toxicity (FST) properties | Sterilizable and biocompatible | High stiffness and dimensional stability |
Chemical Resistance | Good resistance to most chemicals | Resistant to hydrolysis and harsh chemicals | Resistant to sterilization chemicals | Improved chemical resistance due to glass fiber |
Electrical Insulation | Excellent dielectric strength | Good insulation over a wide frequency range | Stable electrical properties | High dielectric strength |
Dimensional Stability | Stable even under thermal stress | Good dimensional stability in challenging environments | Retains stability in varying temperatures | Enhanced stability with low thermal expansion |
Applications | General-purpose, electrical components | Aerospace, transportation | Food processing, medical devices, industrial applications | High-strength components, automotive |
Properties of Ultem™ 1000, Ultem™ 9085, Ultem™ 1010, Ultem™ 2200
*Note: The two values can vary depending on testing conditions, material orientation, and processing methods.
Processes Applicable in Ultem 3D Printing
Fused Deposition Modeling (FDM)
FDM is one of the most common methods for 3D printing Ultem. FDM printers use a heated nozzle to melt Ultem filament and build up layers to form a part. Since Ultem has a high melting point, FDM printers used for Ultem require high-temperature nozzles (over 350°C) and heated build chambers to prevent warping.
Selective Laser Sintering (SLS)
SLS is another method suitable for Ultem powder. This process uses a laser to fuse Ultem particles together layer by layer. SLS allows for detailed and strong parts but requires precise temperature control due to Ultem’s heat sensitivity.
Ready to bring your ideas to life with Ultem 3D printing? Unionfab provides professional-grade 3D printing services designed to meet your unique needs. Click the banner below for an instant quote and enjoy our exclusive 10% discount for new customers !
ULTEM Printing Parameters?
Parameter | Details |
---|---|
Extruder Temperature | 350°C to 390°C; ensures material melts evenly and reduces weak layers |
Bed Temperature | 140°C to 160°C; prevents warping and improves adhesion of the first layer |
Chamber Temperature | 70°C to 80°C; maintains consistent temperature to reduce stress and warping |
Layer Height | 0.1mm to 0.3mm; allows detailed resolution and maintains strength, with higher layer heights printing faster but rougher |
Print Speed | 20–40 mm/s; slower speeds ensure better adhesion and part strength |
Cooling | Minimal cooling; avoids sudden temperature drops to prevent warping or cracking |
Tips for Ultem 3D Printing
Ultem is a challenging yet rewarding material for 3D printing. To achieve the best results, here are practical tips along with the reasoning behind each:
1. Prepare Your Printer
High Temperatures: Ultem requires a heated bed (200°C+) and a nozzle capable of 350°C–450°C due to its high melting point, ensuring proper extrusion and adhesion.
Enclosed Chamber: A heated build chamber helps maintain consistent temperatures, preventing warping and layer separation caused by uneven cooling.
2. Adjust Print Settings
Adhesion: Use high-temperature adhesives or Ultem-specific build surfaces to secure the print and prevent lifting during the process.
Layer Height and Speed: Opt for smaller layer heights (0.1–0.2 mm) and moderate speeds to improve detail and ensure strong layer bonding.
Cooling: Turn off cooling fans to avoid sudden temperature drops, which can cause cracks or warping in Ultem prints.
3. Dry the Filament
Moisture Control: Ultem is hygroscopic, meaning it absorbs moisture from the air. Wet filament can cause bubbling, poor layer adhesion, and defects. Dry it at 120°C for 4–6 hours before printing for smooth results.
4. Minimize Warping and Shrinkage
Support Structures: Add a brim or raft to stabilize the model and enhance adhesion, especially for larger prints that are prone to warping.
Design Adjustments: Incorporate fillets and chamfers to distribute stress evenly, reducing the chances of warping during cooling.
5. Post-Processing
Annealing: Gradually heat the finished part to just below Ultem’s glass transition temperature (~180°C) and cool it slowly. This process improves dimensional stability and enhances mechanical properties.
Surface Finishing: For polished results, use sandpaper or chemical smoothing agents designed for Ultem.
6. Select the Right Grade
Application-Specific Grades: Choose Ultem 9085 for aerospace and automotive applications due to its flame-retardant properties, or Ultem 1010 for medical and food-safe uses. The right grade ensures performance and compliance with application standards.
Advantages and Disadvantages of Ultem 3D Printing
Ultem 3D printing offers unique benefits that make it ideal for high-performance applications, but it also comes with challenges. Here’s a balanced view:
Advantages
High Strength and Durability
Ultem is one of the strongest thermoplastics used in 3D printing, providing excellent mechanical properties suitable for demanding environments. It is deal for aerospace, automotive, and industrial applications requiring long-lasting parts.
Thermal Resistance
With a heat deflection temperature of up to 217°C, Ultem parts can withstand high temperatures, making it suitable for high-heat applications like engine components.
Chemical Resistance
Ultem resists a wide range of chemicals, including oils, solvents, and acids, ensuring durability in harsh environments.
Flame Retardancy
Grades like Ultem 9085 are inherently flame-retardant, self-extinguishing, and meet stringent safety standards (e.g., FAR 25.853 in aerospace).
Dimensional Stability
Its low thermal expansion and high stiffness allow for precision parts that maintain their shape under stress or heat.
Customizable Properties
Available in multiple grades (e.g., 1010 and 9085), Ultem can be tailored for applications needing biocompatibility, food safety, or extreme strength.
Compatibility with Complex Designs
3D printing with Ultem enables the creation of lightweight, intricate designs, including lattice structures, that are challenging for traditional manufacturing.
Disadvantages
High Printing Costs
Ultem filament is expensive compared to standard materials, and its high-temperature requirements mean you need advanced 3D printers, increasing setup costs.
Complex Printing Requirements
Requires a heated bed, high-temperature nozzle, and an enclosed chamber. Printing mistakes can lead to wasted material and time.
Moisture Sensitivity
Ultem is hygroscopic, and even small amounts of absorbed moisture can cause defects like bubbling and weak layers, necessitating careful storage and drying.
Warping and Shrinkage
Despite its stability, Ultem is prone to warping during printing, especially for large parts, requiring additional design considerations and post-processing.
Limited Color Options
Ultem is primarily available in natural (amber) or black, which might limit aesthetic applications without post-processing or painting.
Slow Printing Speed
Due to its high melting point and the need for precise settings, printing Ultem parts can be time-intensive.
Post-Processing Challenges
Machining or smoothing Ultem parts can be difficult due to its toughness, requiring specialized tools for finishing.
Typical Applications of Ultem 3D Printing
Aerospace and Aviation
Structural Components: Ultem is used for lightweight, strong parts like brackets, panels, and ducts that meet stringent flame retardancy and safety standards.
Insulation Materials: Ideal for high-temperature electrical components due to its excellent dielectric properties.
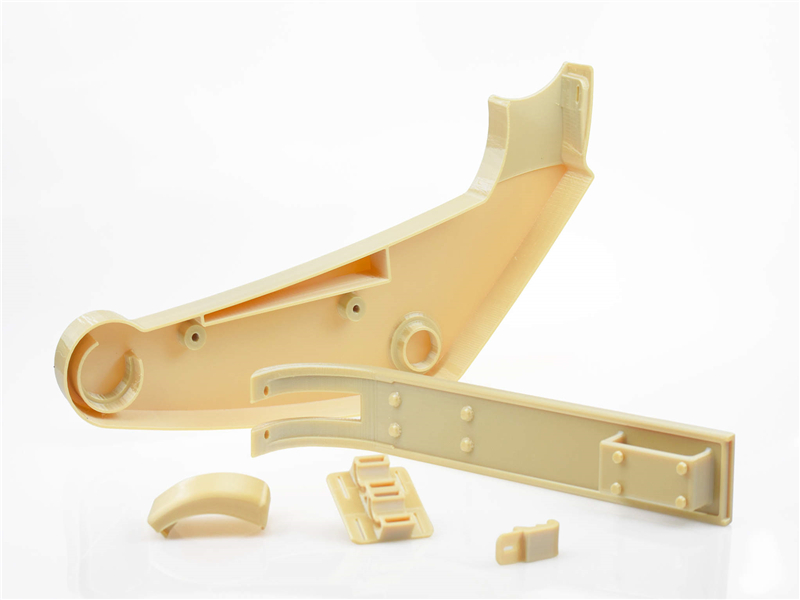
Source: Stratasys.com
Automotive Industry
Engine Parts: Ultem withstands high heat and chemical exposure, making it suitable for under-the-hood components like housings and manifolds.
Prototyping: Its mechanical properties and ease of customization allow for prototyping parts that perform like production-grade materials.
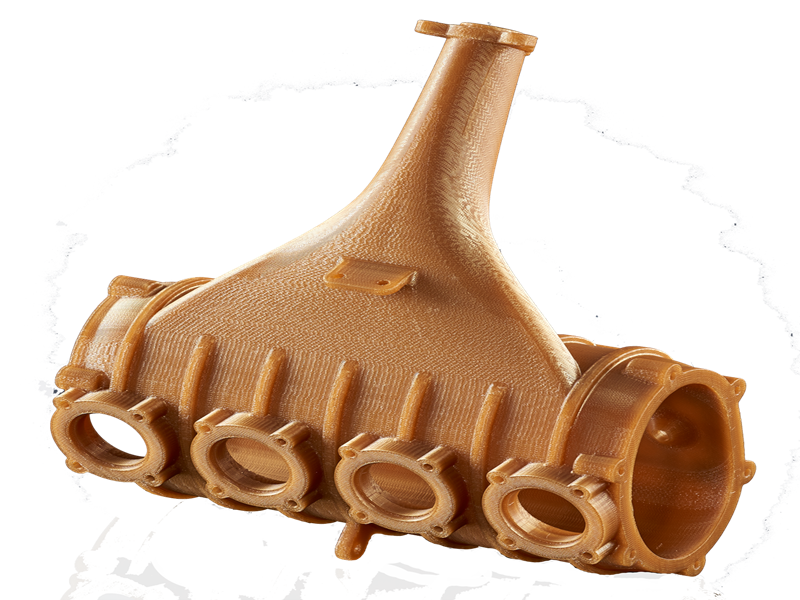
Source: Stratasys.com
Medical and Healthcare
Surgical Tools and Guides: Biocompatible and sterilizable, ideal for reusable surgical instruments and guides.
Dental Devices: Custom-fit prosthetics and orthodontic aligners are a practical application due to Ultem’s precision and safety.
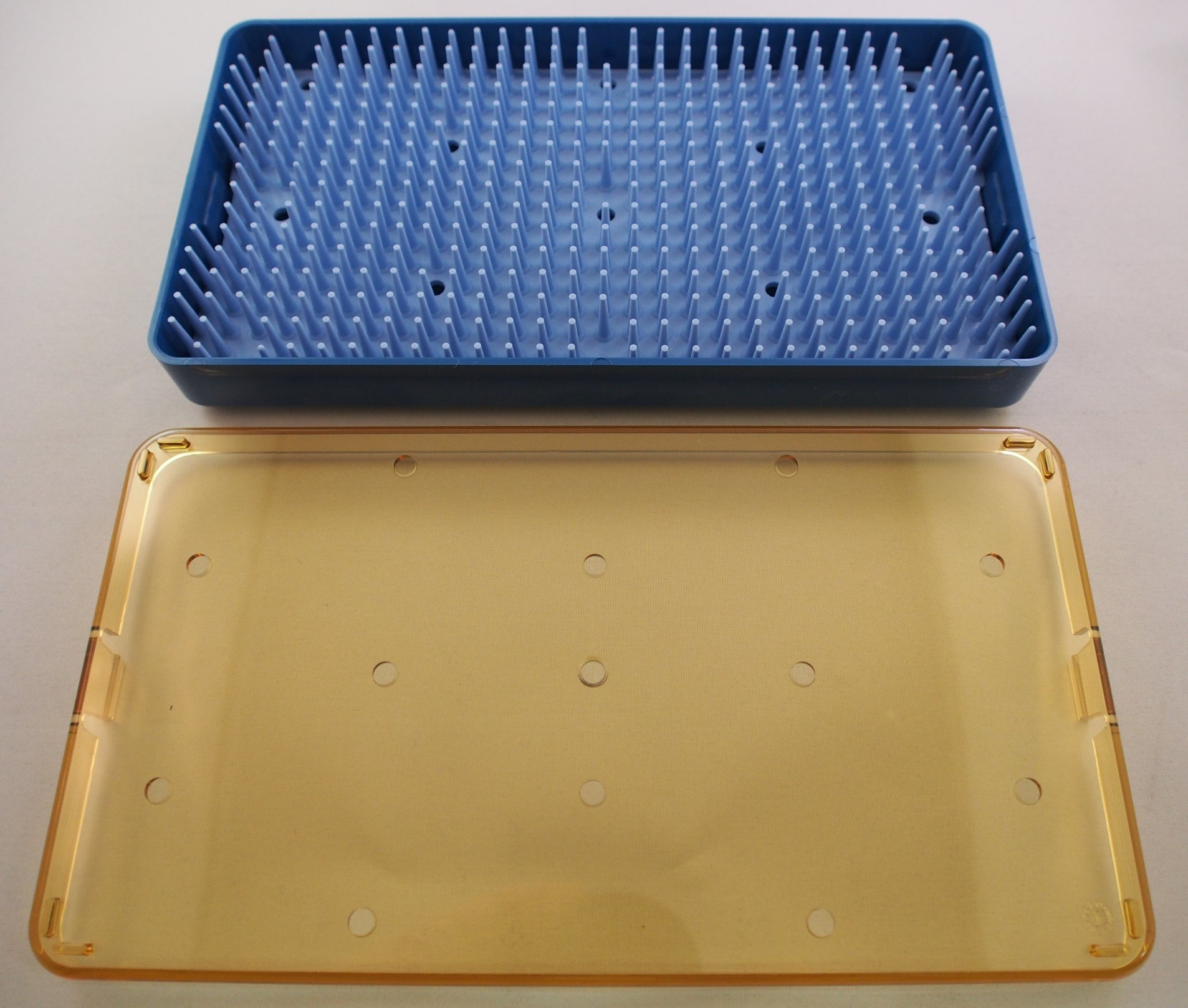
Source: strongvisiontech.com
Electronics and Electrical Equipment
Housings and Enclosures: Protects sensitive electronic components in environments with heat and mechanical stress.
Insulators: Strong dielectric properties make it suitable for insulation in electrical systems.

Source: sabic.com
New Trend of Ultem 3D Printing
Research in 2024
A recent study in the journal Materials introduced a new ULTEM 9085-based sandwich composite, ULTEM-PC-ULTEM. This composite uses ULTEM 9085 for the strong non-flammable outer layers and polycarbonate (PC) for the cheaper core (as shown in the picture below).
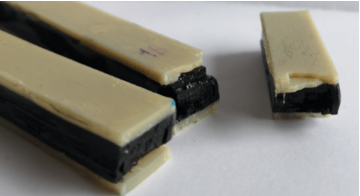
Source: https://www.mdpi.com/1996-1944/17/21/5341
It combines high strength with lower costs, offering a cost-effective solution without compromising on the essential mechanical integrity needed for demanding engineering applications.
Here is an excerpt from the abstract of the paper.
The composite consisted of outer layers made of ULTEM 9085 and a core made of polycarbonate. Each layer was 3D-printed using the fused filament fabrication (FFF) technology, which enables nearly unlimited design flexibility.
The geometry of the test specimens corresponds to the ISO 527-4 standard. Tensile and three-point bending tests were conducted. The structure was modeled in a simplified manner using averaged stiffness values, and with the classical laminate theory (CLT). The models were calibrated through tensile and bending tests on ULTEM and polycarbonate prints. The simulation results were compared with experimental data, demonstrating good accuracy.
As for the details of the mechanical property comparison between the two, 2 testings: tensile test and three-point bending test in the paper speak for themselves. The followings are the results.
Tensile test:

Source: https://www.mdpi.com/1996-1944/17/21/5341
Three-point bending test:

Source: https://www.mdpi.com/1996-1944/17/21/5341
In a word, according to the paper, the 3D-printed ULTEM-PC-ULTEM composite exhibits favorable mechanical properties, making it a promising material for cost-effective engineering applications.
The full text of the paper can be found at MDPI.
Research in 2018
In fact, as early as 2018, scholars conducted similar experiments, studying the performance of mixtures of standard PEI with PC and PETG as modifiers, and comparing these mixtures to Ultem 9085.
The study found:
Adding PC or PETG to pure PEI can decrease the viscosity of the blends, especially in the high-frequency range, thereby improving their melt flowability and processing performance. In particular, when 10 wt% of PC is added, the viscosity behavior of the blends is similar to that of Ultem 9085. The results of the rheological analyses in the paper are shown as follows.
Isothermal Rheology at 350 ◦C for PEI/PC Blends with Different Content of PC
Source: https://www.researchgate.net/publication/323138722For PC content up to 40 wt % (especially less than 20 wt %), the PEI/PC blends showed equal or higher tensile properties compared to Ultem 9085 sample. The results of the mechanical testings are as follows.
Effect of modifier content for PEI/PC (black) and PEI/PETG (red) blends compared to
Ultem 9085 (blue) on tensile modulus (a) and tensile strength (b)
Source: https://www.researchgate.net/publication/323138722
You can find the full paper at Researchgate.
So, based on the above research, it is evident that multi-material 3D printing is one of the future trends in ULTEM 3D printing.
ULTEM is a high-performance material, but its cost is relatively high. Through multi-material printing, ULTEM can be used for critical parts (such as outer layers or load-bearing sections), while more economical materials (such as polycarbonate PC or PETG) are utilized for less demanding areas.
This combination retains ULTEM’s exceptional properties, such as high strength, heat resistance, and chemical stability, while significantly reducing overall material costs, greatly promoting its wider adoption in complex engineering applications.

Conclusion
Ultem 3D printing is more than just a manufacturing option—it represents a shift toward smarter, more efficient material use in high-demand industries. Its ability to combine strength, heat resistance, and chemical durability makes it invaluable for complex designs and applications.
As innovations like multi-material 3D printing continue to evolve, the opportunities for integrating Ultem into more cost-effective and functional solutions are expanding. This not only reduces production barriers but also paves the way for creative and sustainable engineering breakthroughs.
FAQs
What temperature is Ultem 3D printing?
Ultem 3D printing requires high temperatures:
Extruder Temperature: 350°C to 390°C (depending on the grade).
Bed Temperature: 140°C to 160°C to ensure proper adhesion.
Chamber Temperature: 70°C to 80°C to maintain consistent environmental conditions and prevent warping.
What is the strength of Ultem 3D printed?
Ultem 3D-printed parts exhibit high mechanical strength:
Tensile Strength: Typically ranges from 90 MPa (Ultem 9085) to 110 MPa (Ultem 1000).
Flexural Modulus: 2.15 GPa (Ultem 9085) to 5.5 GPa (Ultem 2200, glass-filled). These properties make it suitable for demanding engineering applications.
What are the types of ULTEM 3D printing filaments ?
Ultem 3D printing filaments are high-performance thermoplastics used in Fused Deposition Modeling (FDM). Common grades include:
Ultem 9085: Known for flame retardancy, low smoke, and toxicity, ideal for aerospace and transportation.
Ultem 1010: Biocompatible and food-safe, often used in medical and food processing applications.
Filament Diameter: Typically available in 1.75 mm and 2.85 mm sizes
How much does Ultem 3d printing cost ?
The cost of Ultem 3D printing depends on the filament price and the printer's specifications:
Filament Cost: Ultem filament is relatively expensive, ranging from $200 to $500 per kilogram (depending on the grade).
Printing Costs: High-temperature printers required for Ultem can cost anywhere from $10,000 to $50,000.