Inconel Metal Guide [Property Comparison + Selection Tips]
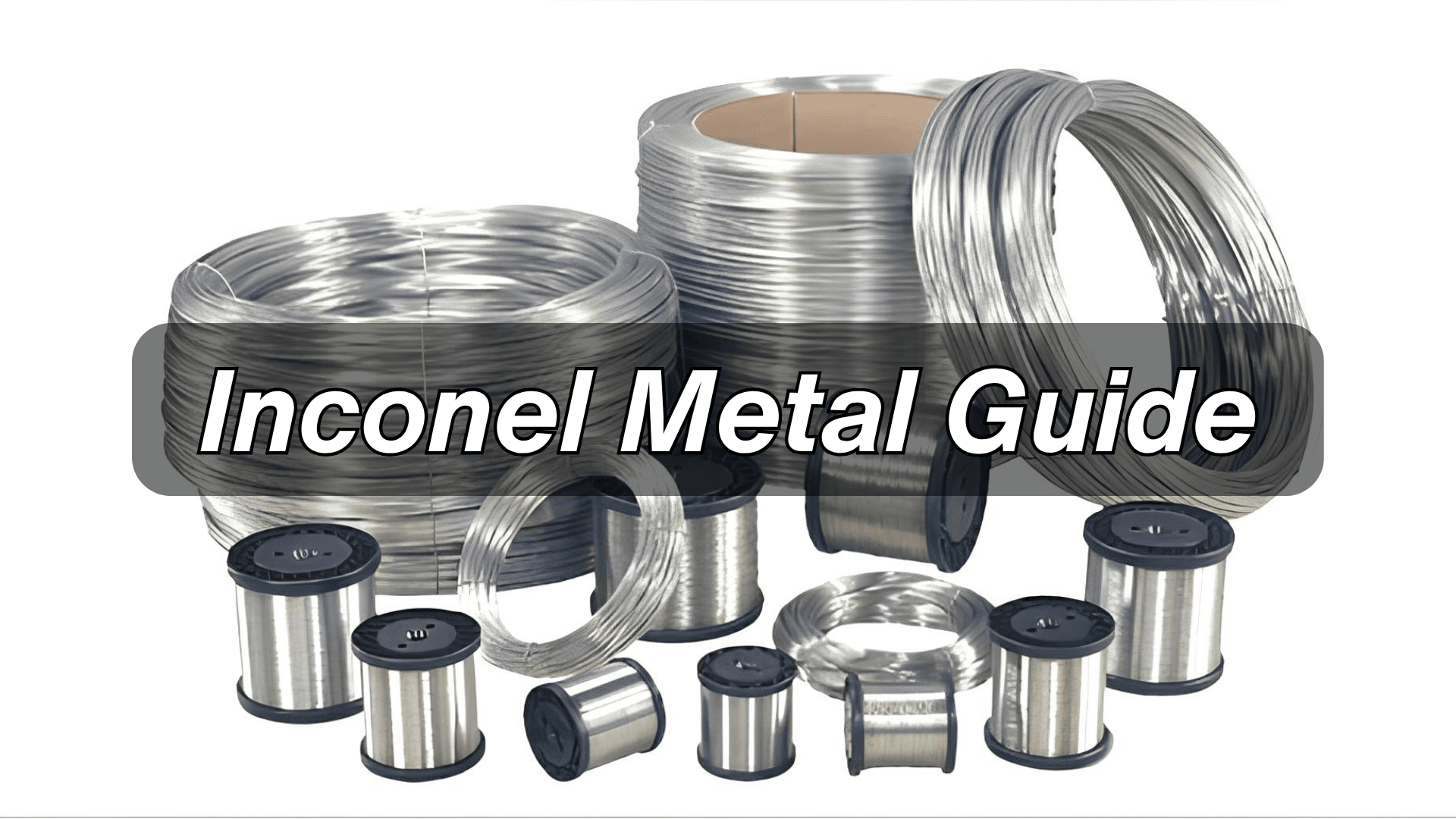
Discover the origin of Inconel, its common types, unique advantages and applications and learn how to choose the most suitable Inconel type for your projects.
Introduction
In extreme environments, material performance can make or break a project. Among the many high-performance alloys, Inconel stands out as a key material in aerospace, energy, and chemical industries due to its exceptional resistance to heat, corrosion, and mechanical stress.
This article explores what Inconel is, its types, key advantages, and real-world applications. You’ll also find a comparison of common grades like Inconel 625, 718 to help you choose the right alloy.
What is Inconel ?
Industries like aerospace, jet engines, nuclear power, and offshore drilling demand materials that can withstand extreme heat and harsh environments. Ordinary metals often oxidize, corrode, or lose strength under such conditions.
To solve this, INCO developed Inconel—a family of alloys that offer exceptional heat and corrosion resistance while maintaining high strength, even in the most demanding applications.
Origin of the Name “Inconel”
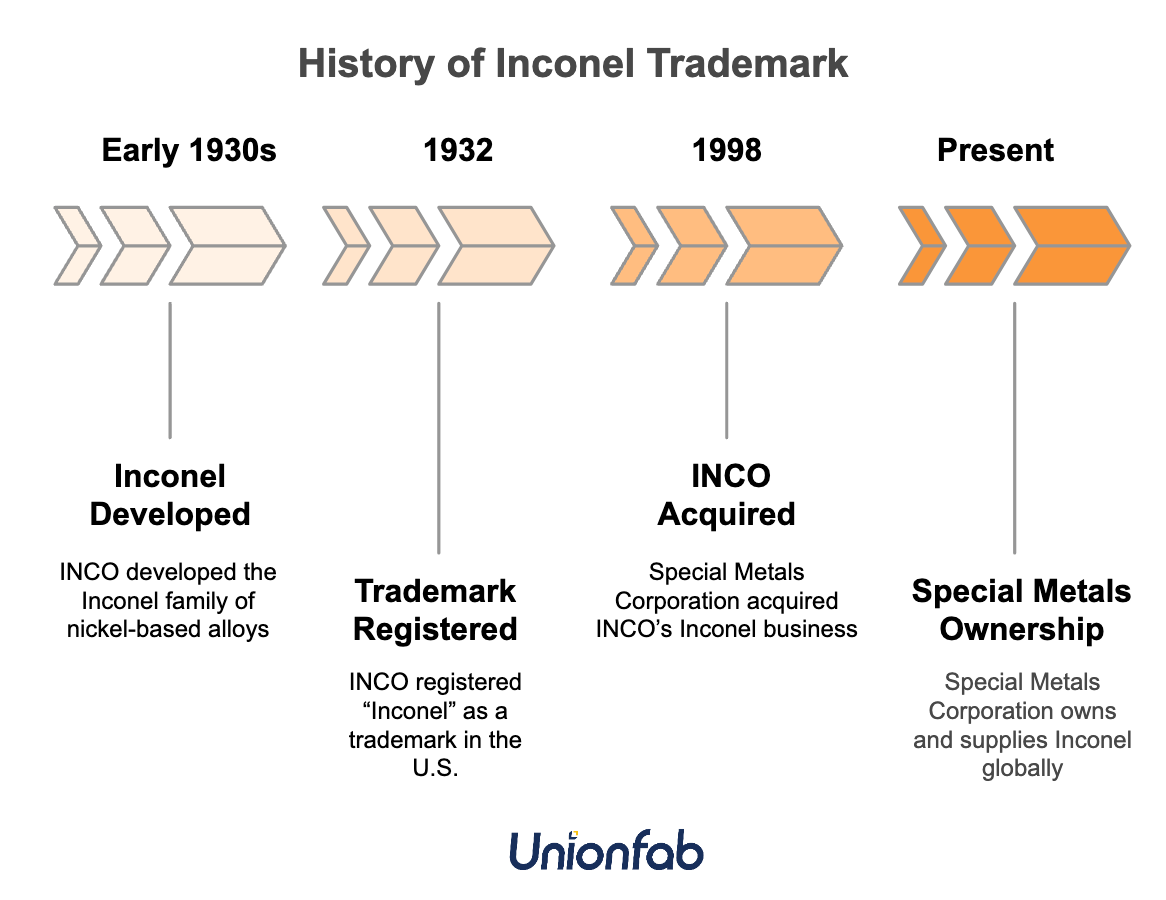
“Inconel” is not just a general material name—it’s actually a registered trademark. It was originally developed in the 1930s by the International Nickel Company (INCO).
The “Inco” part comes from the company name.
The “-nel” suffix indicates it’s a nickel-based alloy.
Put together, “Inconel” simply means: a nickel-based alloy developed by INCO.
Although the International Nickel Company was eventually acquired by other firms, the Inconel® brand name was retained. Today, the trademark is owned by Special Metals Corporation, which continues to manufacture and supply Inconel alloys globally.
Inconel Chemical Composition
Inconel is not a single alloy, but a family of nickel-chromium-based superalloys. While the exact chemical composition varies depending on the grade (such as Inconel 625 or Inconel 718), all Inconel alloys share a high percentage of nickel as their base, usually around 50–70%. This gives them excellent resistance to heat, corrosion, and oxidation.
Here’s a general overview of the key elements commonly found in Inconel alloys:
Element | Function |
---|---|
Nickel (Ni) | Main base metal; ensures high temperature and corrosion resistance |
Chromium (Cr) | Adds oxidation and corrosion resistance, especially in hot environments |
Iron (Fe) | Present in small amounts; contributes to mechanical strength and workability |
Molybdenum (Mo) | Enhances resistance to pitting and crevice corrosion |
Niobium (Nb) or Columbium | Strengthens the alloy through precipitation hardening (especially in Inconel 718) |
Titanium (Ti) | Improves high-temperature strength and phase stability |
Aluminum (Al) | Promotes oxidation resistance and strengthens the alloy matrix |
Each Inconel grade is engineered for a specific set of performance demands — from marine applications to aerospace turbine components — and its composition is finely tuned to match.
Pros and Cons of Inconel
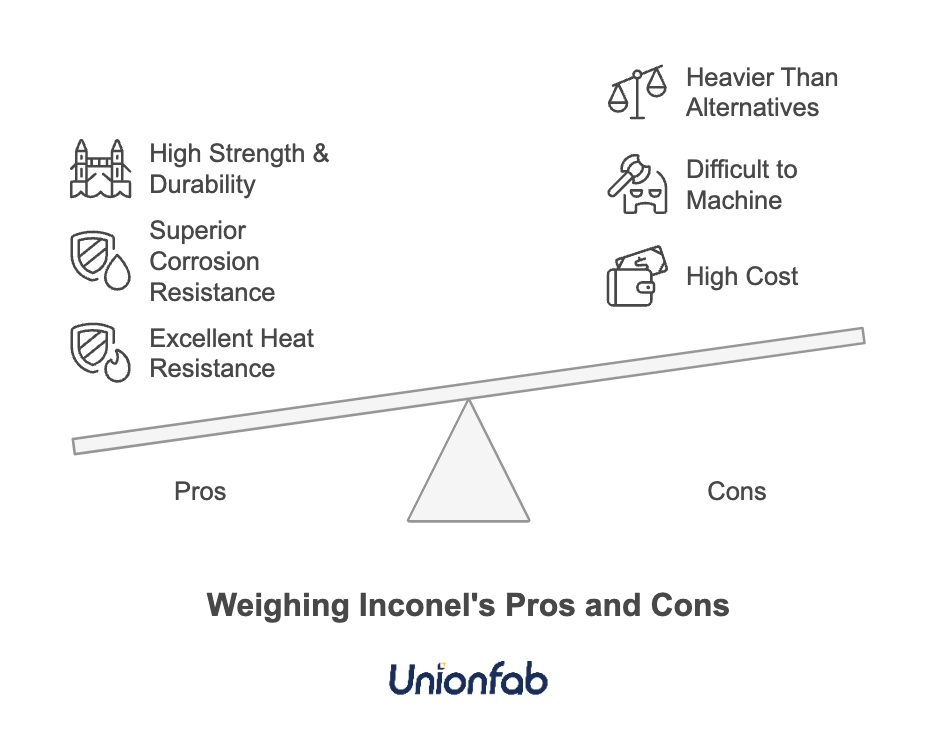
Pros:
Excellent Heat Resistance Maintains mechanical strength and stability at extremely high temperatures.
Superior Corrosion Resistance Resists oxidation, rust, and chemical attack—even in seawater, acidic, or high-pressure environments.
High Strength & Durability Performs reliably under extreme mechanical stress and thermal cycling.
Great for Harsh Environments Ideal for aerospace, nuclear, chemical processing, and marine applications.
Cons:
High Cost Significantly more expensive than stainless steel or other common alloys.
Difficult to Machine Its strength and toughness make it challenging to cut, shape, or weld without specialized tools or techniques.
Heavier Than Some Alternatives Inconel is denser than materials like titanium, which can be a drawback in weight-sensitive applications.
Inconel Metal Types, Properties and Comparison
Inconel grades are generally classified by their strengthening mechanism and alloy composition:
Solid Solution Strengthened Alloys: Enhanced through the uniform distribution of alloying elements (e.g., Inconel 600, 625)
Precipitation Hardened Alloys: Strengthened by heat treatments that form fine, hard particles within the structure (e.g., Inconel 718, X-750)
According to Special Metals website, there are 20 INCONEL® nickel-based alloys available, including INCONEL® Alloys 600, 601, 617, 625, 625LCF, 686, 690, 693, 718, 718SPF, 725, 740H, X-750, 751, 783, N06230, C-276, HX, 22, and G-3.
To help you quickly understand the differences and applications of these grades, we’ve provided a simple comparison of their compositions and key features.
Alloy Grade | Strengthening Method | Key Alloying Elements | Brief Description |
---|---|---|---|
600 | Solid solution | Ni-based (>72% Ni), ~15% Cr, low Fe | One of the earliest Inconel alloys; good corrosion and heat resistance. |
601 | Solid solution | +Al (>1.0%) for oxidation resistance, ~22% Cr | Improved version of 600; enhanced oxidation resistance. |
617 | Solid solution | High Cr, Mo, Co; strengthening by Al, Ti | High-temp alloy for gas turbines and petrochemical use. |
625 | Solid solution | High Mo (9%), high Ni, moderate Cr | Versatile corrosion- and strength-resistant alloy. |
625LCF | Solid solution (LCF-optimized) | Same as 625; purer and more uniform microstructure | Fatigue-optimized version of 625 for flexible components. |
686 | Solid solution | Very high Mo (>20%), +W | Extremely corrosion-resistant for harsh chemical environments. |
690 | Solid solution | ~30% Cr | Excellent stress corrosion resistance; used in nuclear systems. |
693 | Solid solution | High Cr + 2.5–4.0% Al | Superior resistance to metal dust corrosion; for hydrogen service. |
718 | Precipitation hardened | +Nb, Ti, Al; γ’’ (Ni₃Nb) as strengthening phase | Most common PH alloy; used in aerospace and power sectors. |
718SPF | Precipitation + Superplastic forming | Same as 718; grain refined for superplasticity | For complex sheet metal forming at high temperature. |
725 | Precipitation hardened | Similar to 625; +Ti/Nb for aging strengthening | High strength + corrosion resistance; for oilfield connectors. |
740H | Precipitation hardened | High Ni, Cr, Co; +Ti, Al, Nb forms γ’ | Advanced high-temp alloy for USC boiler tubes. |
X-750 | Precipitation hardened | +Ti/Al; forms γ’ (Ni₃(Al,Ti)) | γ’-strengthened alloy for springs and turbines. |
751 | Precipitation hardened | Ti/Al; improved machinability over X-750 | X-750 variant with better workability. |
783 | Precipitation hardened | Ni-Co base, low expansion; +Al, Ti forms γ’ | Low expansion; used in aircraft engine structures. |
N06230 | Solid solution | Ni-Cr base, +W, Mo | Excellent oxidation and creep resistance; aerospace applications. |
C-276 | Solid solution | High Mo, Cr, W; Ni-based | Exceptional corrosion resistance; used in chemical and pollution control. |
HX | Solid solution | Ni-Cr-Fe base; +Mo, Co | High strength and thermal stability; for furnaces and turbines. |
22 | Solid solution | Ni-Cr-Mo-W | Resists a wide range of corrosive media. |
G-3 | Solid solution | Ni-Cr-Fe base; +Mo, Cu | Balanced resistance to oxidizing and reducing environments. |
Inconel 625 vs 718 vs 600 vs X-750 vs C-276
Among all the grades above, several alloys are widely used. We’ve summarized their key performance advantages and typical applications to help you choose the most suitable INCONEL alloy for your projects.
Alloy Grade | Key Performance Advantage | Typical Applications | Reason for Widespread Use |
---|---|---|---|
625 | Excellent corrosion resistance (chlorides, acids); max temp ~980 °C | Chemical processing, marine, aerospace, flue systems | High strength, corrosion resistance, weldable, versatile |
718 | High yield strength (up to 1035 MPa); works up to ~650 °C | Jet engines, gas turbines, nuclear parts | Strength + weldability; reliable for structural use |
600 | Oxidation resistance up to ~1175 °C | Heat-treating, nuclear, chemical exchangers | Stable in high-temp + corrosive environments |
X-750 | High-temperature elasticity, good to ~815 °C | Turbine springs, nuclear parts, fasteners | Strong and elastic at high temperatures |
C-276 | Outstanding corrosion resistance (acids, mixed media); up to ~1040 °C | Acid handling, chemical plants, pollution control | Survives extreme corrosion; often no alternatives |
For the detailed properties of all inconel metals, you can refer to the Special Metals nickel-alloy handbook or download the related data sheets from their product page.
Inconel vs. Titanium vs. Stainless Steel
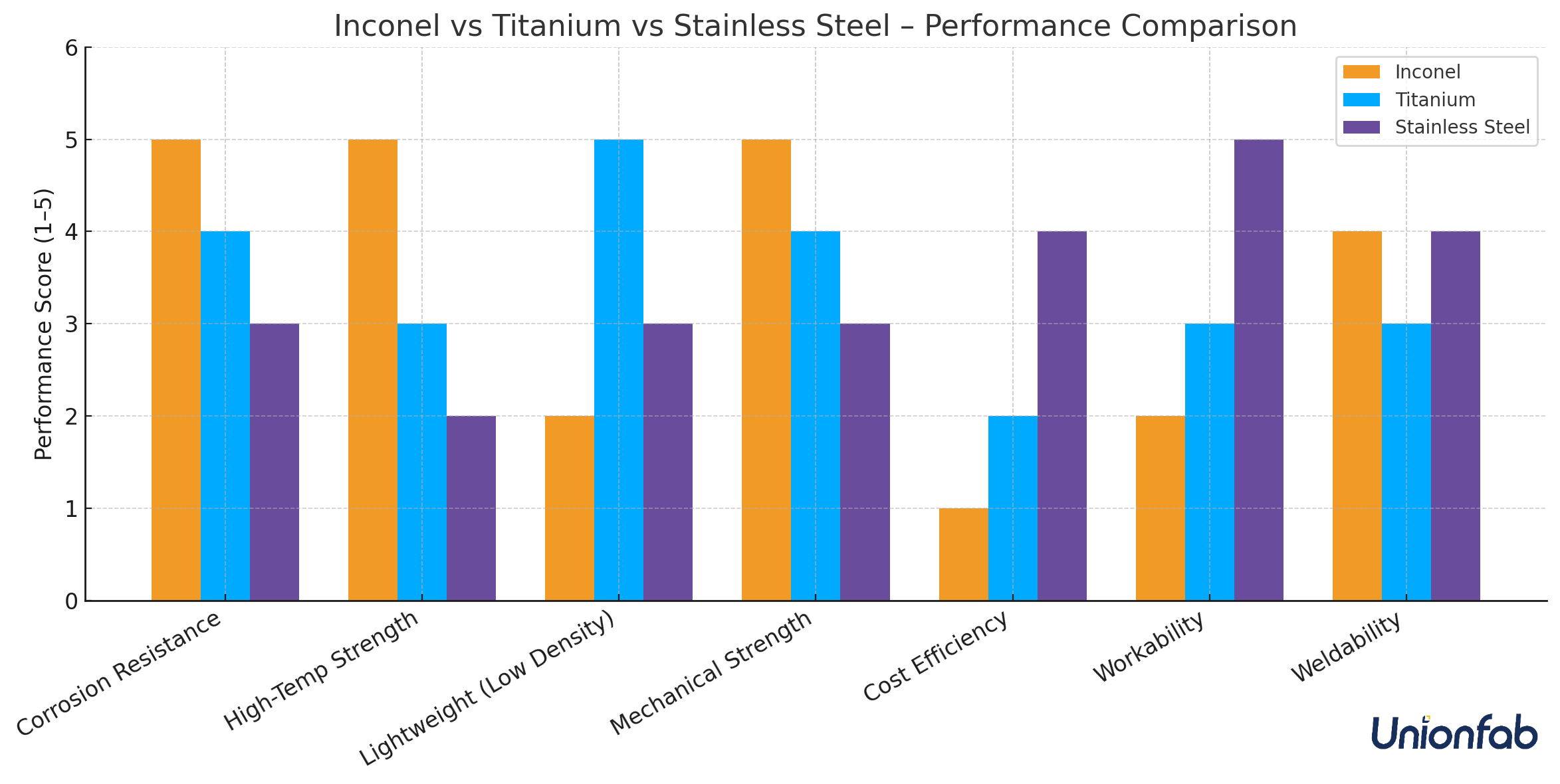
When selecting materials for high-performance applications, especially in aerospace, chemical processing, marine, and energy industries, Inconel, Titanium, and Stainless Steel are often considered. Each offers distinct advantages depending on the environment and performance requirements.
Property/ Material | Inconel | Titanium | Stainless Steel |
---|---|---|---|
Base Composition | Nickel-based alloy | Pure Ti or Ti alloy (e.g., Ti-6Al-4V) | Iron-based with Cr (≥10.5%), Ni, Mo, etc. |
Corrosion Resistance | Excellent in extreme environments (acids, seawater, high-temp oxidizers) | Excellent in seawater and biological environments | Good in mild to moderate corrosive environments |
High-Temperature Strength | Outstanding, maintains strength > 1000 °C | Limited to ~600 °C | Varies by grade; typically up to ~750 °C |
Weight/Density | High (~8.4 g/cm³) | Low (~4.5 g/cm³) | Medium (~7.9 g/cm³) |
Mechanical Strength | Very high, especially in PH grades like Inconel 718 | Good strength-to-weight ratio | Good, but may weaken at elevated temps |
Cost | Very high | High | Moderate to low |
Workability/Machining | Difficult, requires special tooling | Fair, can be challenging | Generally good |
Weldability | Generally good (varies by grade) | Moderate to good (some alloys crack-sensitive) | Good |
When to Use Each Material
Inconel: Best for extreme heat and corrosion, such as in jet engines, gas turbines, chemical reactors, and exhaust systems.
Titanium: Ideal when weight savings and corrosion resistance are critical, especially in aerospace, marine, and medical implants.
Stainless Steel: A cost-effective choice for structural applications, food processing, and moderate-temperature equipment.
Primary Manufacturing Methods of Inconel Metals
Due to their exceptional strength, corrosion resistance, and heat tolerance, Inconel alloys are widely used in demanding industries—but they also require specific manufacturing methods. The following are the primary manufacturing processes that can independently produce Inconel parts from raw material.
Evaluation Criteria | Hot Forming(Forging / Rolling) | Machining(CNC Milling, Turning) | Welding(Fabrication) | Additive Manufacturing(SLM, EBM, DED) |
---|---|---|---|---|
Manufacturing Process | High-temperature deformation | Material removal via cutting | Joining of plates or tubes | Layer-by-layer part building from powder |
Typical Applications | Flanges, rings, tubes, preforms | Precision parts, flanges, shafts | Pressure vessels, ducts, supports | Complex and lightweight aerospace components |
Processing Difficulty & Notes | Requires thermal control; post-machining needed | Work hardens easily; needs rigid setup and cooling | Heat-affected zones; cracking control needed | Slow; expensive; post-heat treatment often required |
Recommended Use Case | Pre-shaping high-strength or large parts | Precision machining or final finishing | Structural assembly or fluid-tight joints | Complex geometries or performance-critical parts |
Compatible Inconel Grades | 625, 718, 713, 706 | Most grades (esp. 625, 718) | 625, 718, 600, 690 | 625, 718 |
Cost | ⭐️⭐️⭐️ | ⭐️⭐️⭐️⭐️ | ⭐️⭐️ | ⭐️⭐️⭐️⭐️⭐️ |
Summary & Selection Guidance
Hot Forming is ideal for producing large, strong preforms when high-volume or heavy-duty components are needed.
Machining offers the best precision and is essential for tight-tolerance parts or final shaping after forging.
Welding is preferred for assembling Inconel sheets or tubes into complex structures like pressure vessels or ducts.
Additive Manufacturing is best suited for low-volume, high-value components with complex geometries that are difficult to achieve by traditional methods.
Inconel 3D Printing (Additive Manufacturing)
Among the four primary manufacturing methods for Inconel metals, CNC machining remains the most widely used due to its precision, versatility, and compatibility with nearly all Inconel grades. However, the method that is currently gaining the most attention is 3D printing —because it allows manufacturers to create complex, lightweight Inconel parts that traditional methods can’t easily produce.
Why are Inconel 625 and 718 sought-after in 3D printing?
Among all the Inconel grades, Inconel 625 and 718 are the most widely-used and popular in 3D printing because they offer an ideal balance of material performance, printability, and industry demand. Here are the details:
Aspect | Inconel 625 | Inconel 718 |
---|---|---|
Key Material Strength | Excellent corrosion resistance | High strength, creep and fatigue resistance |
Printability | Very stable, low cracking risk, well-validated | Good printability, well-supported by SLM/EBM/DED |
Process Maturity | Proven parameters across AM platforms | Widely adopted in industry, standard post-treatment available |
Engineering Acceptance | Suitable for structural parts with basic post-processing | Compatible with aerospace standards after aging treatment |
In short,
Inconel 625 meets the demand for lightweight, corrosion-resistant parts in custom 3D printing.
Inconel 718 enables 3D printing of high-strength, high-temperature structural components.
For more details about Inconel 3d printing, you can refer to the article: https://www.unionfab.com/blog/2024/11/inconel-3d-printing
And if you’re looking for Inconel 3D printing services, consider Unionfab — China’s largest 3D printing manufacturer. We offer 3D printing materials with performance comparable to Inconel 625 and 718, but at 3–5 times lower cost. Feel free to contact us if you’re interested.
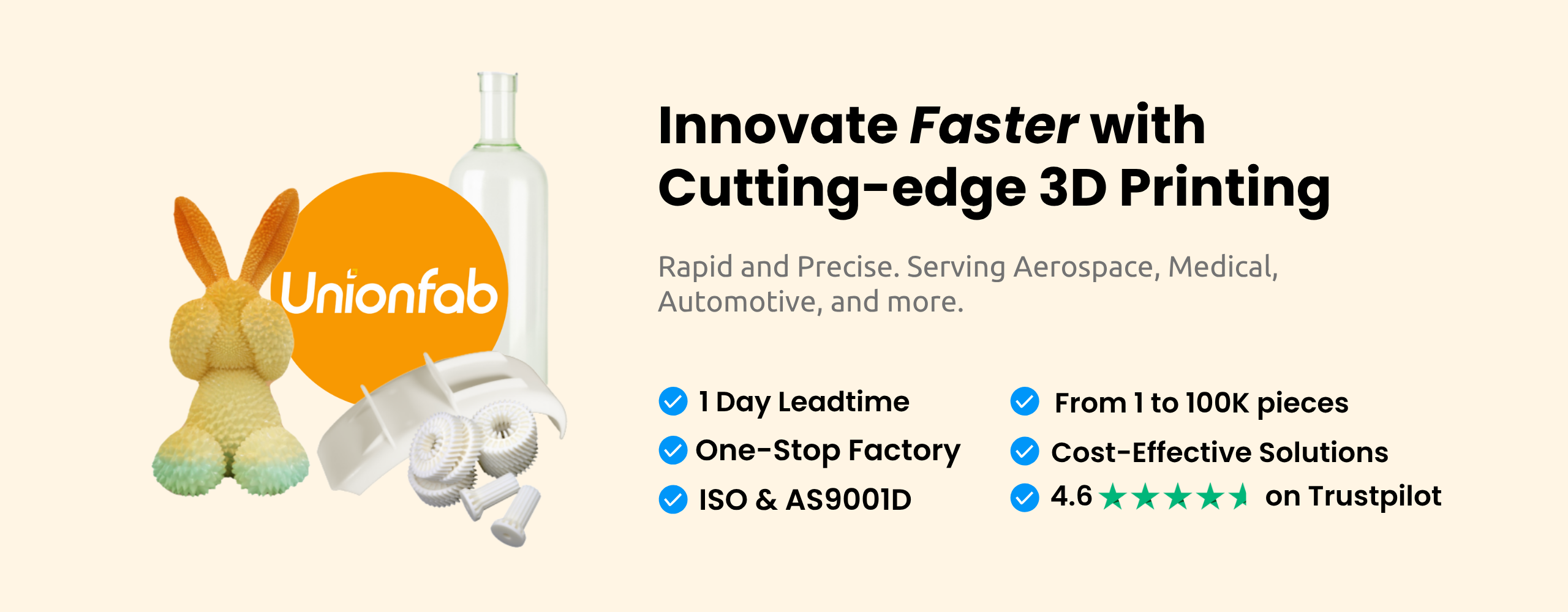
Industry-specific Applications of Inconel Metals
Inconel alloys are widely used in industries where heat, pressure, and corrosion resistance are critical. Below is an overview of key application areas, with typical alloy grades used in each.
Aerospace and Aviation
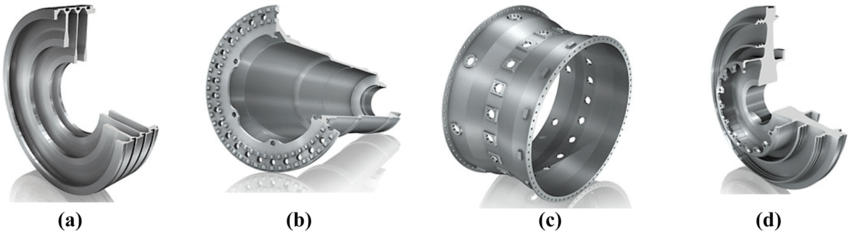
Source: researchgate.net
Applications: Inconel exhaust valve & pipe, turbine blades, engine components, heat shields etc.
Common Alloys: Inconel 718, Inconel X-750, Inconel 625
Why Inconel?: High strength and oxidation resistance at extreme temperatures
Energy and Power Generation
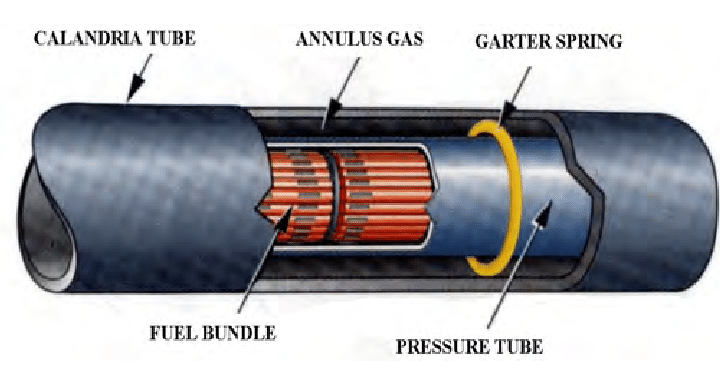
Source: researchgate.net
Applications: Gas turbines, boiler tubes, steam lines, reactor parts etc.
Common Alloys: Inconel 617, Inconel 625, Inconel 718, Inconel 740H
Why Inconel?: Creep resistance, thermal stability, and corrosion resistance
Chemical and Petrochemical Processing
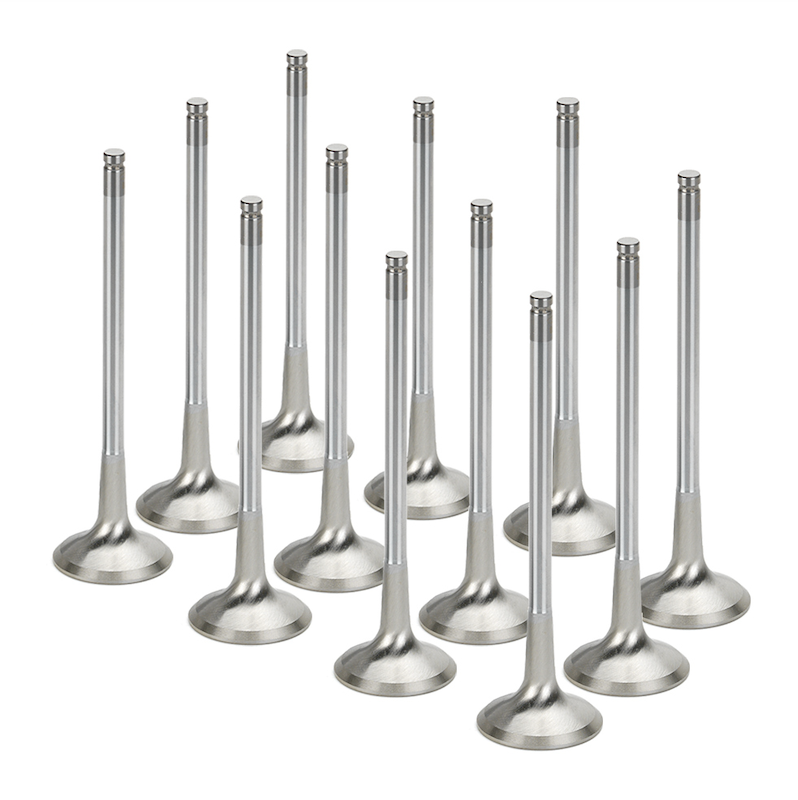
Source: supertechperformance.com
Applications: Reactors, pressure vessels, valves, heat exchangers etc.
Common Alloys: Inconel 625, Inconel 600, Inconel 686, Inconel 22
Why Inconel?: Excellent resistance to acids, solvents, and corrosive media
Marine and Offshore
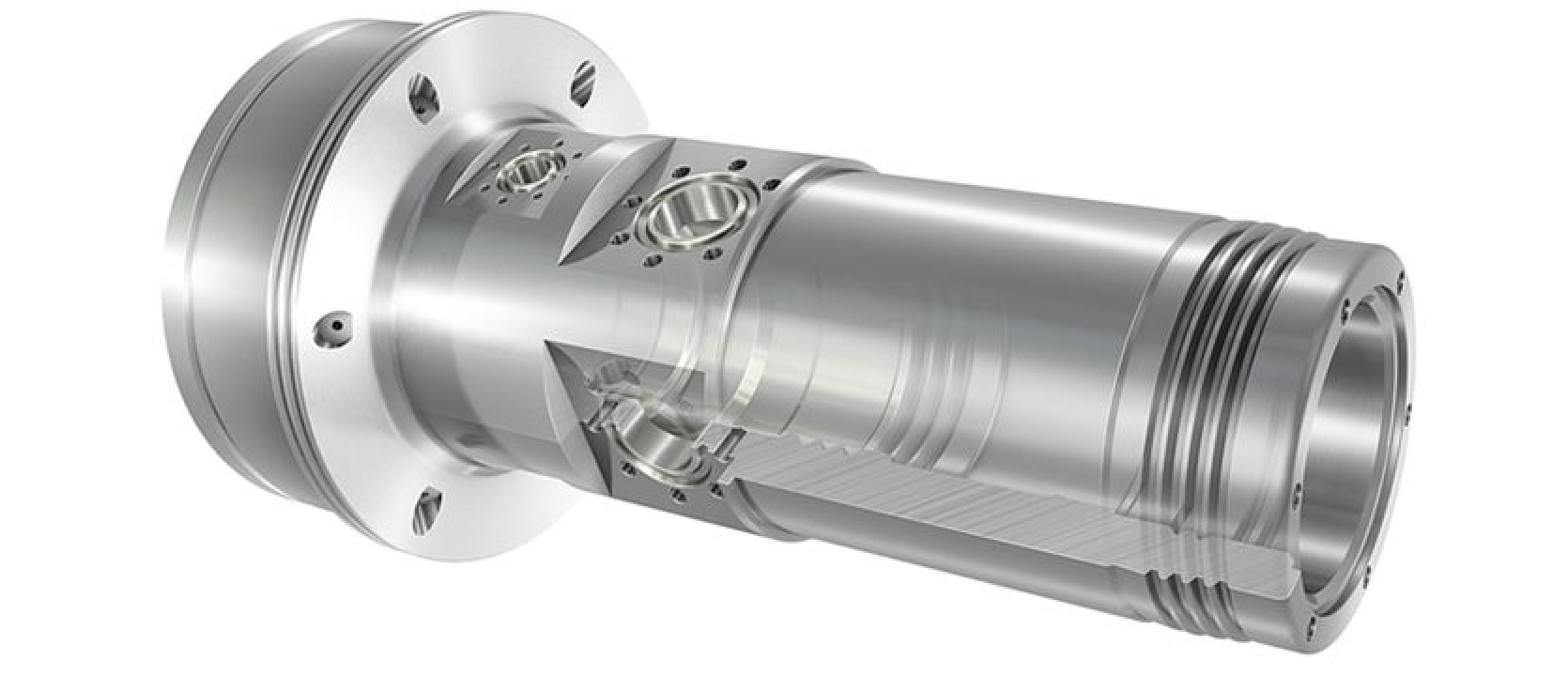
Source: sandvik.coromant.com
Applications: Inconel fasteners, subsea components, seawater piping, pumps, etc.
Common Alloys: Inconel 625, Inconel 718, Inconel 725
Why Inconel?: Outstanding resistance to seawater corrosion and chloride stress cracking
Medical and Surgical Equipment(limited use)
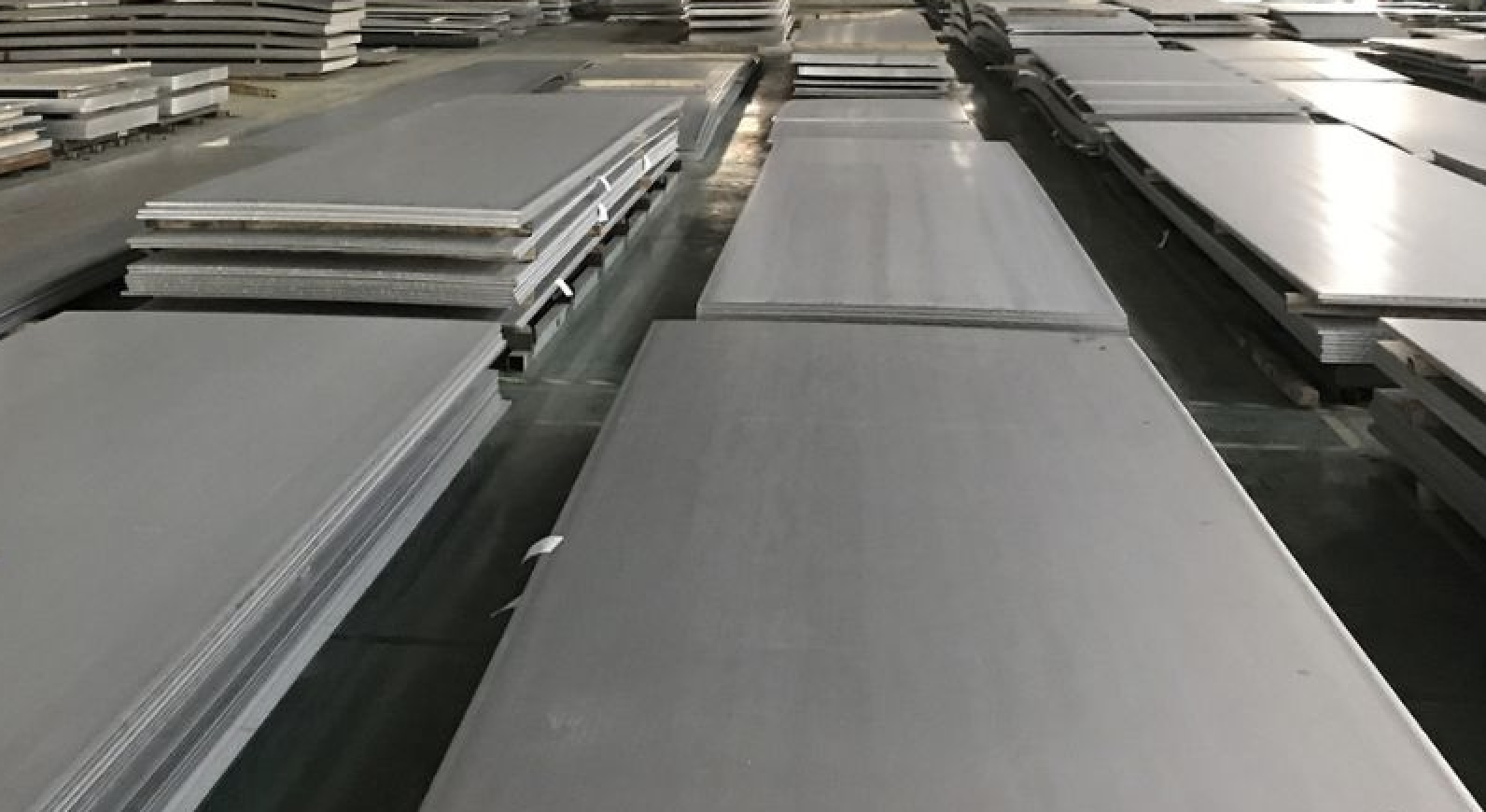
Source: bhansalioverseas.com
Applications: Surgical tools, orthopedic components, high-sterility devices etc.
Common Alloys: Inconel 625, Inconel 718 (in specialized applications)
Why Inconel?: Biocompatibility, strength, and sterilization resistance
FAQs
What is Inconel made of and how is Inconel made?
Inconel is a nickel-based alloy primarily composed of nickel (≥50%), chromium, and often molybdenum, niobium, or iron. It’s made through vacuum induction melting (VIM) or vacuum arc remelting (VAR) for high-purity applications.
What is Inconel used for?
Inconel is used in high-temperature, high-stress, and corrosive environments—such as jet engines, gas turbines, chemical reactors, heat exchangers, and nuclear power systems.
How hard is Inconel?
Depending on the grade and heat treatment, Inconel typically reaches a hardness of Rockwell C 30–45. Inconel 718, after aging, can exceed 40 HRC.
What is Inconel 718?
Inconel 718 is a precipitation-hardened nickel-chromium alloy known for high strength, corrosion resistance, and excellent weldability. It’s widely used in aerospace and energy industries.
Is Inconel magnetic?
No, Inconel is generally non-magnetic, especially in annealed condition.
How hard is Inconel?
Inconel typically has a hardness of Rockwell C 30–45, depending on the grade and heat treatment.
What is the Inconel price per pound? How much does Inconel cost?
Prices vary by grade and market, but Inconel typically costs $25–$50 per pound, significantly more than stainless steel or titanium due to raw material and processing costs.
What is Inconel used for?
Inconel is used in high-temperature and corrosive environments such as aerospace engines, gas turbines, chemical processing, and nuclear reactors.
Why is Inconel so expensive?
Inconel is expensive due to its high nickel content, complex alloying elements, difficult machining, and specialized production processes.
How to weld Inconel?
Inconel can be welded using TIG (GTAW) or MIG (GMAW) methods. Proper filler metals, controlled heat input, and post-weld heat treatment (if needed) are essential to prevent cracking.
Inconel vs Hastelloy
Inconel is optimized for high-temperature strength and oxidation resistance. Hastelloy (usually C-series) excels in chemical resistance, especially in strongly reducing environments. Inconel is preferred for heat; Hastelloy for corrosion.