Guide to SLS Nylon[Property + Service Provider Comparison]
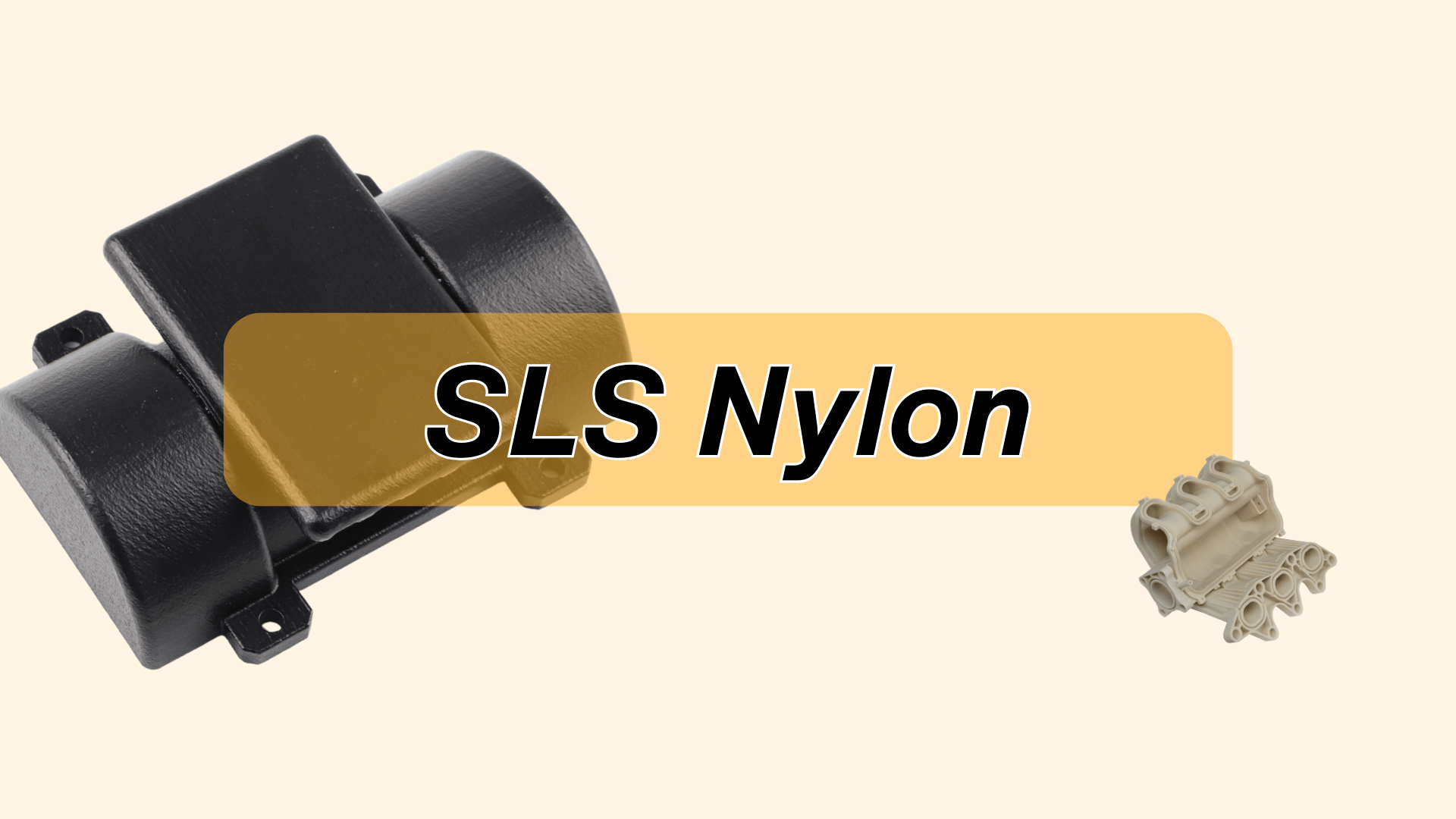
Unlock the full potential of SLS nylon—compare materials, master design tips, explore real-world uses, and get a fast quote from Unionfab!
Why Choose SLS Nylon?
Selective Laser Sintering (SLS) Nylon is one of the most powerful and versatile 3D printing solutions available today. It combines the design freedom of additive manufacturing with the strength, durability, and precision required for real-world applications.
Whether you’re developing prototypes, functional end-use parts, or custom low-volume production runs, SLS Nylon offers a unique balance of performance, scalability, and cost-efficiency.
Key Benefits at a Glance
Complex Geometry Without Supports
SLS enables the creation of intricate, interlocking, and internal structures that would be impossible or expensive with traditional manufacturing. No support structures are needed, reducing post-processing time.
Durability & Mechanical Strength
Nylon materials used in SLS are known for their toughness, high impact resistance, and long-term dimensional stability, making them ideal for functional prototypes and industrial-grade components.
Scalable for Prototypes & Production
SLS Nylon is equally effective for single-part prototyping and small to medium production batches. Its repeatability and powder reuse make it cost-effective as you scale up.
Superior Surface Quality and Detail
Compared to FDM or SLA, SLS parts have a more uniform finish, especially when combined with post-processing techniques like vapor smoothing or dyeing.
Material Efficiency & Sustainability
Unfused nylon powder can be recycled and reused for subsequent prints, which minimizes waste and reduces material costs over time.
Is SLS Nylon Right for You?
SLS Nylon is the right choice if you need:
Functional prototypes that behave like final parts
End-use components with strong mechanical properties
High design freedom and part complexity
Reduced time-to-market for product development
A cost-effective alternative to injection molding for low-volume production
If you’re exploring how to bring stronger, smarter, and faster parts to life, SLS Nylon is your next step forward.
What Is SLS Nylon 3D Printing?
Selective Laser Sintering (SLS) Nylon 3D printing is an advanced additive manufacturing process that builds strong, functional plastic parts by fusing nylon powder layer by layer using a high-powered laser. Unlike other 3D printing methods, SLS does not require support structures, making it ideal for complex geometries and dense part nesting.
How SLS Works — In Simple Terms
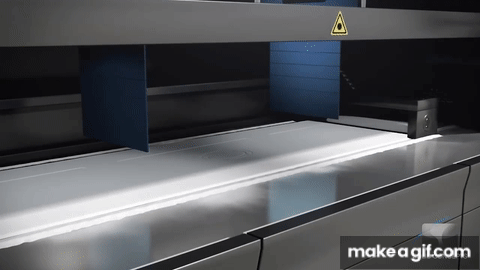
A thin layer of nylon powder is spread across the build platform.
A laser selectively sinters the powder in the shape of the current layer.
The platform lowers, and a new layer of powder is spread.
The process repeats until the full part is built.
The part is removed from the powder bed, cleaned, and post-processed if necessary.
For more details about SLS 3d printing process, read our previous article: Guide to SLS 3D Printing.
Why Nylon Is Ideal for SLS
Nylon (polyamide) is the most widely used material in SLS printing due to its excellent balance of strength, flexibility, and thermal stability. It is:
Lightweight yet strong
Resistant to wear, impact, and chemicals
Ideal for snap-fit components and load-bearing parts
Available in multiple formulations (e.g., PA12, PA11, glass-filled variants)
Whether you’re creating a prototype, a mechanical component, or a batch of functional end-use products, SLS Nylon delivers industrial-grade performance with minimal design compromise.
Materials Overview: Which Nylon to Choose?
SLS 3D printing supports a range of nylon materials, each designed to meet different mechanical, thermal, and aesthetic requirements.
Technically, Nylon 6, 66, 11, 12 and Glass-filled(GF) Nylon(Bead & Fiber) can all be applied in sls 3d printing. However, some of them are less commonly-used.
Nylon 6 (PA6): High melting point and shrinkage make it prone to warping and hard to print reliably.
Nylon 66 (PA66): Narrow processing window and strict temperature control make it difficult to use in SLS.
PA12 GF (Glass-Fiber Reinforced): Low powder reusability and high machine wear limit its use in long-term production.
Therefore, we will focus on the more common ones in the following.
PA12 (Nylon 12) The most widely used material in SLS 3D printing.
Excellent dimensional stability and durability
High resistance to impact, chemicals, and moisture
Ideal for functional prototypes, housings, fixtures, and end-use parts
Smooth surface finish and consistent accuracy
✅ Best for: General-purpose use, mechanical parts, consumer products
PA11 (Nylon 11) A bio-based alternative to PA12, offering more flexibility.
Higher elongation at break than PA12
Greater resistance to fatigue and impact
Derived from castor oil (renewable)
More ductile and suited for parts that bend or flex
✅ Best for: Flexible components, snap fits, prosthetics, sports gear
PA12 GB (Glass-Bead-Filled Nylon 12)
Reinforced with glass beads for improved stiffness and thermal resistance.
Enhanced rigidity and heat deflection
Lower elongation, but higher dimensional accuracy
Rougher surface finish (can be improved with post-processing)
✅ Best for: Structural parts, jigs & fixtures, high-load components
Common SLS Materials Comparison: PA12 vs. PA11 vs. PA12 GB vs. TPU
In addition to the types of nylon mentioned above, which are commonly used materials for SLS, TPU is also one of the commonly used materials for SLS.
Therefore, we have included TPU in the comparison table below as well.
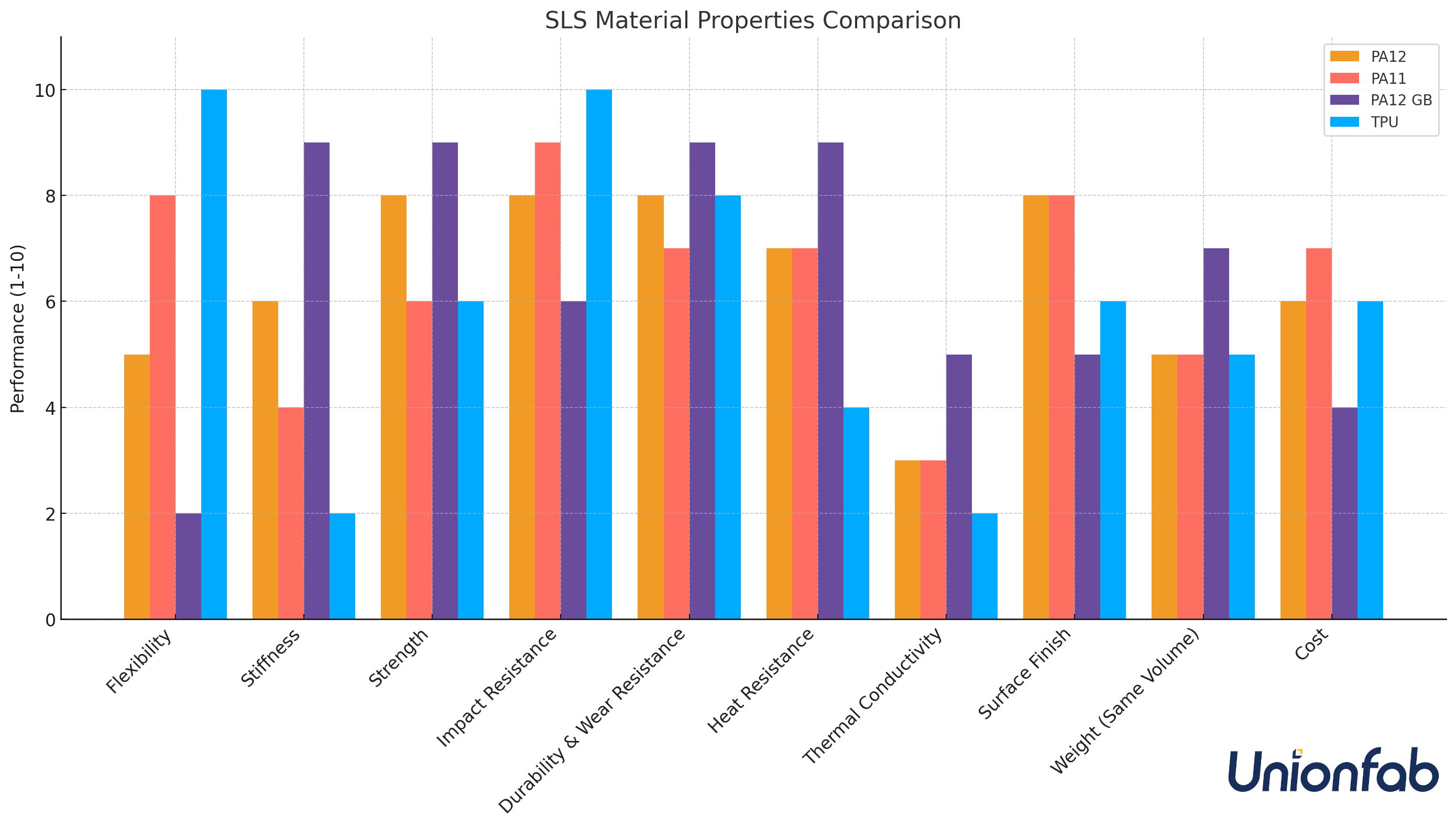
Property | PA12 | PA11 | PA12 GB | TPU |
---|---|---|---|---|
Flexibility | ⭐️⭐️⭐️ | ⭐️⭐️⭐️⭐️½ | ⭐️ | ⭐️⭐️⭐️⭐️⭐️ |
Stiffness | ⭐️⭐️⭐️ | ⭐️⭐️ | ⭐️⭐️⭐️⭐️½ | ⭐️ |
Strength | ⭐️⭐️⭐️⭐️ | ⭐️⭐️⭐️ | ⭐️⭐️⭐️⭐️½ | ⭐️⭐️⭐️ |
Impact Resistance | ⭐️⭐️⭐️⭐️ | ⭐️⭐️⭐️⭐️½ | ⭐️⭐️⭐️ | ⭐️⭐️⭐️⭐️⭐️ |
Durability & Wear Resistance | ⭐️⭐️⭐️⭐️ | ⭐️⭐️⭐️½ | ⭐️⭐️⭐️⭐️½ | ⭐️⭐️⭐️⭐️ |
Heat Resistance | ⭐️⭐️⭐️½ | ⭐️⭐️⭐️½ | ⭐️⭐️⭐️⭐️½ | ⭐️⭐️ |
Thermal Conductivity | ⭐️⭐️ | ⭐️⭐️ | ⭐️⭐️½ | ⭐️ |
Surface Finish | ⭐️⭐️⭐️⭐️ | ⭐️⭐️⭐️⭐️ | ⭐️⭐️⭐️ | ⭐️⭐️⭐️ |
Weight (Same Volume) | ⭐️⭐️⭐️ | ⭐️⭐️⭐️ | ⭐️⭐️⭐️⭐️ | ⭐️⭐️⭐️ |
Cost | ⭐️⭐️⭐️ | ⭐️⭐️⭐️½ | ⭐️⭐️ | ⭐️⭐️⭐️ |
Biocompatible | ✅ Yes | ✅ Yes | ❌ No | ✅ Yes |
Renewable Source | ❌ No | ✅ Yes | ❌ No | ❌ No |
For more property details of the materials above, you can download the data sheets: PA11, PA12, PA12 GB, TPU.
How to Choose the Right Nylon
Ask yourself:
Does your part need to bend or flex? → PA11 or TPU
Is strength and dimensional stability critical? → PA12 or PA12 GB
Will the part face high loads or heat? → PA12 GB
Are you aiming for a sustainable material? → PA11
Do you need an all-purpose option? → PA12
If you’re still unsure, our material experts can help evaluate your requirements and suggest the most suitable solution.
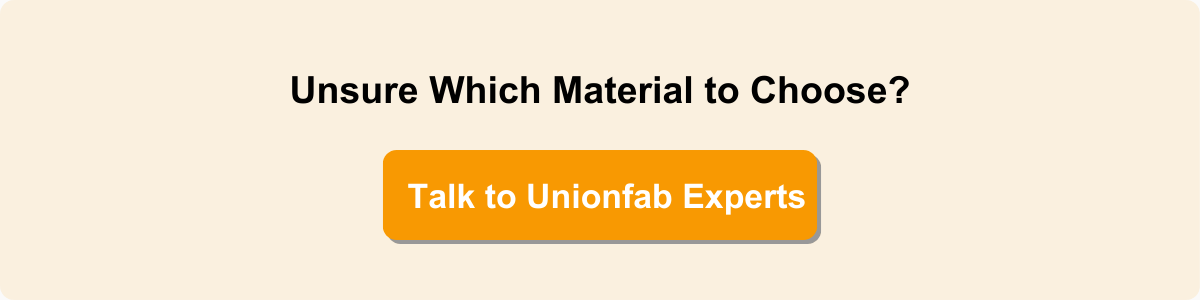
How much does sls nylon 3d printing cost?
Most 3D printing services determine pricing using this basic formula: Total Printing Cost = Material Unit Price × Weight of Material Used
Keep in mind that this calculation only reflects the base printing cost. The final cost of your order may also include post-processing charges, shipping, taxes, and packaging fees.
For a complete breakdown, check out our earlier post: How much does it cost to 3D print something?
Already have a 3D model? Try our online cost calculator to get a fast estimate for your project.
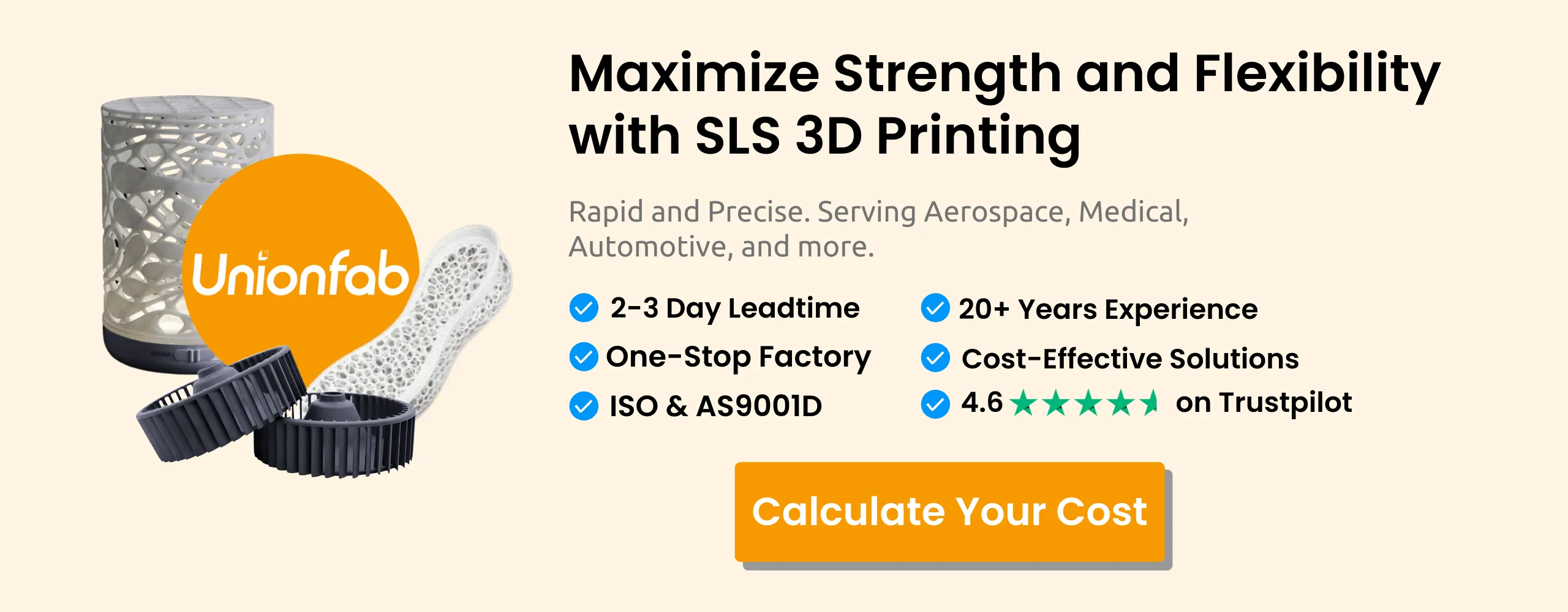
Design Guidelines for SLS Nylon 3D Printing
Recommended Design Specifications
Feature | Recommended Specification | Notes / Reason |
---|---|---|
Wall Thickness | - PA12: ≥ 0.8 mm | Material-specific wall thickness: |
Hole Size | ≥ 1.5 mm | Refers to general functional holes (e.g., screw holes, mounting holes). Smaller holes may fuse or trap powder. |
Escape Holes | ≥ 3.5 mm diameter (preferably 2+ holes for larger cavities) | Specifically designed for removing unsintered powder from hollow structures. Essential for weight reduction and post-processing efficiency. |
Feature Size | ≥ 0.8 mm | Applies to pins, ridges, and other fine elements. |
Embossed Details | Embossing height ≥ 1.0 mm | To ensure raised features like pins or ribs are visible and printable. |
Engraved Details | Engraving depth ≥ 1.0 mm | Shallow engravings may get lost or blurred during printing. |
Text | Font height ≥ 2.0 mm (size 14) | Improves legibility on all surfaces; serif or small fonts may lose definition. |
Tolerances | ± 0.3 mm or ± 0.3% | Depends on part size and geometry; tighter tolerances require careful design. |
Fillets / Radii | Internal corners should use fillets ≥ 0.5 mm | Reduces stress concentrations and improves part strength. |
Moving Assemblies | ≥ 0.7 mm Clearance between moving parts | Prevents fusing between interlocked or nested components during sintering |
Interlocking Parts | ≥ 0.5 mm Clearance | Ensures parts remain functional after printing and powder removal. |
Unsupported Overhangs | Avoid angles > 45° without support or reorientation | May cause deformation or surface defects despite SLS not needing support. |
Part Nesting | ≥ 2.0 mm Spacing between adjacent parts | Ensures airflow and consistent powder flow; too close may cause thermal bonding or poor surface quality. |
Maximum Part Size | Limited by printer build volume (e.g., 300 × 300 × 300 mm) | Larger parts should be split in design and joined after printing using mechanical or adhesive methods. |
Minimum Channel Size | ≥ 2.0 mm diameter | Applies to internal cavities or fluid paths; smaller channels may clog or trap powder that’s hard to remove. |
Additional Design Guidelines
Except for the recommended specifications above, below are additional design guidelines that go beyond numerical standards but are equally critical for optimizing your SLS 3D printing results.
Design Aspect | Guideline | Reason |
---|---|---|
Part Orientation | Orient parts to optimize mechanical strength and surface quality. | Affects stress distribution and aesthetics due to anisotropy. |
Avoid Fully Sealed Cavities | Always allow powder escape via holes or openings. | Prevents unsintered powder entrapment. |
Accessible Internal Geometry | Avoid narrow or deep internal areas that are hard to clean. | Helps effective post-processing and powder removal. |
Stress Minimization | Avoid sharp internal corners; fillet where possible. | Reduces potential stress fractures. |
Avoid Thin Overhangs & Tabs | Reorient or thicken long unsupported features. | Prevents warping or breakage even without supports. |
Label Placement | Place embossed features (logos, text) on flat, low-wear areas. | Enhances durability and readability after handling. |
Applications of SLS Nylon 3D Printing
1. Functional Prototypes
SLS is widely used for rapid prototyping of mechanical parts that require real-world testing. Nylon’s toughness and thermal resistance make it ideal for producing parts that need to snap-fit, flex, or undergo mechanical stress. Use cases include:
Automotive enclosures and brackets
Consumer product housings
Aerospace component mockups
Mechanical test parts for form, fit, and function
2. End-Use Production Parts
Thanks to the high strength-to-weight ratio and lack of support structures required, SLS is increasingly adopted for small- to mid-volume production of functional components. Common applications:
Custom brackets, clips, and fixtures
Lightweight housings and covers
Spare or replacement parts
Tooling components for manufacturing environments
3. Medical and Orthopedic Devices
PA11, a bio-based and biocompatible material, is often chosen for medical-grade applications. SLS allows for customized geometries tailored to individual patients. Notable examples:
Orthotic braces and prosthetic sockets
Surgical guides and templates
Wearable health devices with ergonomic fit
4. Footwear and Sports Equipment
TPU and PA11 are popular in the sportswear industry due to their flexibility and impact resistance. Examples include:
Custom midsoles and shoe components
Protective gear components
Lightweight performance parts for bicycles or helmets
5. Jigs, Fixtures, and Manufacturing Aids
In industrial settings, SLS nylon parts are used to produce robust, heat-resistant jigs and fixtures that support complex assembly or inspection processes. Applications:
Assembly guides
Positioning tools
Robot end-effectors
Custom inserts or alignment tools
6. Ducting and Fluid Management Systems
The design freedom of SLS makes it easy to produce complex internal channels and non-linear geometries often used in ductwork or fluid routing. Common components:
Air ducts and manifolds
Coolant channels
Custom pipe fittings for aerospace and automotive
Choosing A Suitable SLS 3D Printing Service Provider
Now, desktop SLS technology is not yet mature, and product quality may not be guaranteed. Industrial SLS machines are expensive, with entry-level models costing up to $30,000. If the equipment is underused, you could face significant financial loss.
Therefore, if you want to use SLS nylon 3D printing for final products or functional prototypes, choosing the right 3D printing service provider is a more cost-effective option.
To assist you in finding the right service provider, we’ve prepared the comparison table below.
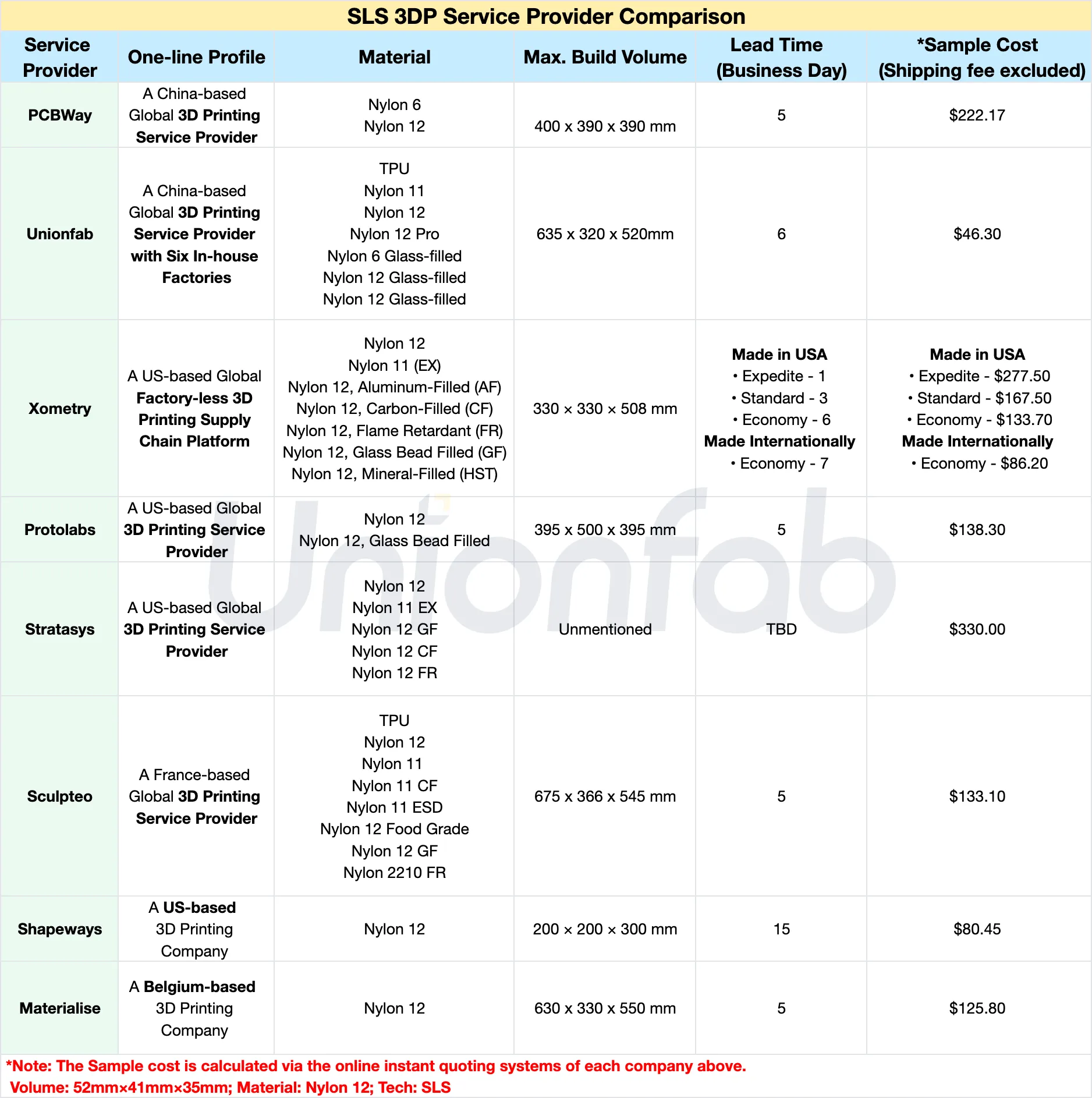
Recommendation:
If cost is a key factor, Unionfab provides the most affordable service.
If you need larger parts, Unionfab, Sculpteo and Materialise are all good options.
If specialized materials are required, Xometry and may be worth considering despite the higher cost.
Maximize Strength and Flexibility with Unionfab SLS Nylon 3D Printing Service
With over 20 years of experience, a fleet of 1,000+ industrial 3D printers, and six state-of-the-art facilities, Unionfab—certified to ISO 9001, ISO 13485, and AS 9001D standards—delivers reliable, high-quality, and cost-efficient 3D printing solutions.
To help you explore our SLS 3D printing capabilities, we’ve created a VR factory tour. Click the GIF below to begin your virtual visit!
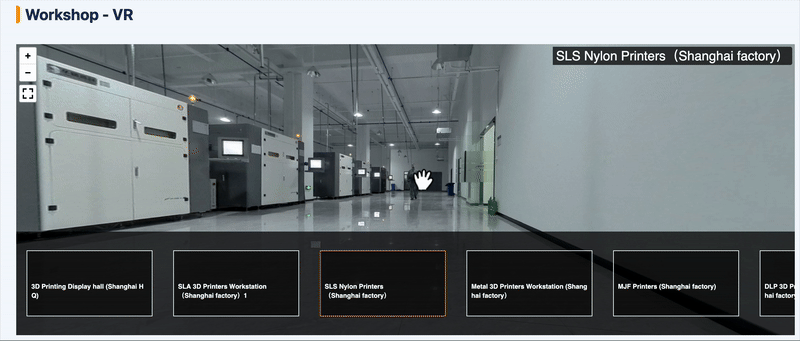
If you haven’t used Unionfab’s 3d printing service before, sign up to get 10% discount for your first order.
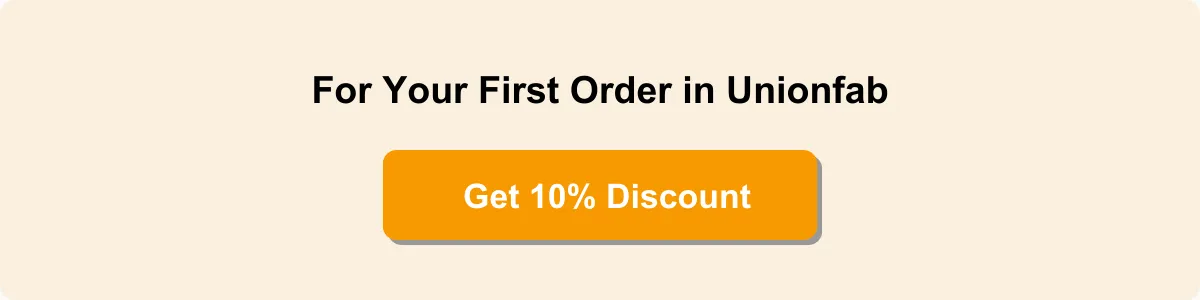