Guide to Golf 3D Printing [+Cost Calculator]
![Guide to Golf 3D Printing [+Cost Calculator]](https://ufc-dtc-cms.oss-accelerate.aliyuncs.com/blog/20250713/233017_ugt5ydr2m.png)
Enhance your game with custom 3D printed clubheads. Unionfab helps you achieve lightweight, high-performance golf gear tailored to your swing.
Introduction
3D printing is transforming industries worldwide, and the golf sector is no exception. Leading golf brands are using 3D printing to create custom clubheads, shafts, grips, and accessories. This technology offers greater precision, faster prototyping, and customization that traditional manufacturing can't achieve.
As 3D printing enables golf manufacturers to create more tailored, high-performance equipment, it offers golfers the opportunity to optimize their gear based on individual needs. Now, let's explore how 3D printing is reshaping the design of golf equipment.
Golf Club Components
A golf club consists of several key components, each essential for performance:
● Clubhead:
The most critical part of the club, striking the ball and influencing its trajectory, speed, and distance. 3D printing enables the creation of clubheads with custom shapes and internal structures to improve control and distance.
● Shaft:
Connects the clubhead to the grip and plays a key role in swing control, flexibility, and feel. 3D printing allows for custom shafts that can be tailored for specific weight and flexibility.
● Grip:
The part the golfer holds, providing comfort and stability. 3D printing lets you customize grips to fit hand size and offer the needed control for optimal performance.
● Hosel:
The part that connects the shaft to the clubhead. It affects alignment and loft, and 3D printing allows for a more precise fit, improving balance and performance.
Among these, the clubhead is the most commonly 3D printed part, offering manufacturers and golfers the ability to create custom designs that enhance performance, aerodynamics, and appearance.
Traditional vs. 3D Printed Golf Clubheads
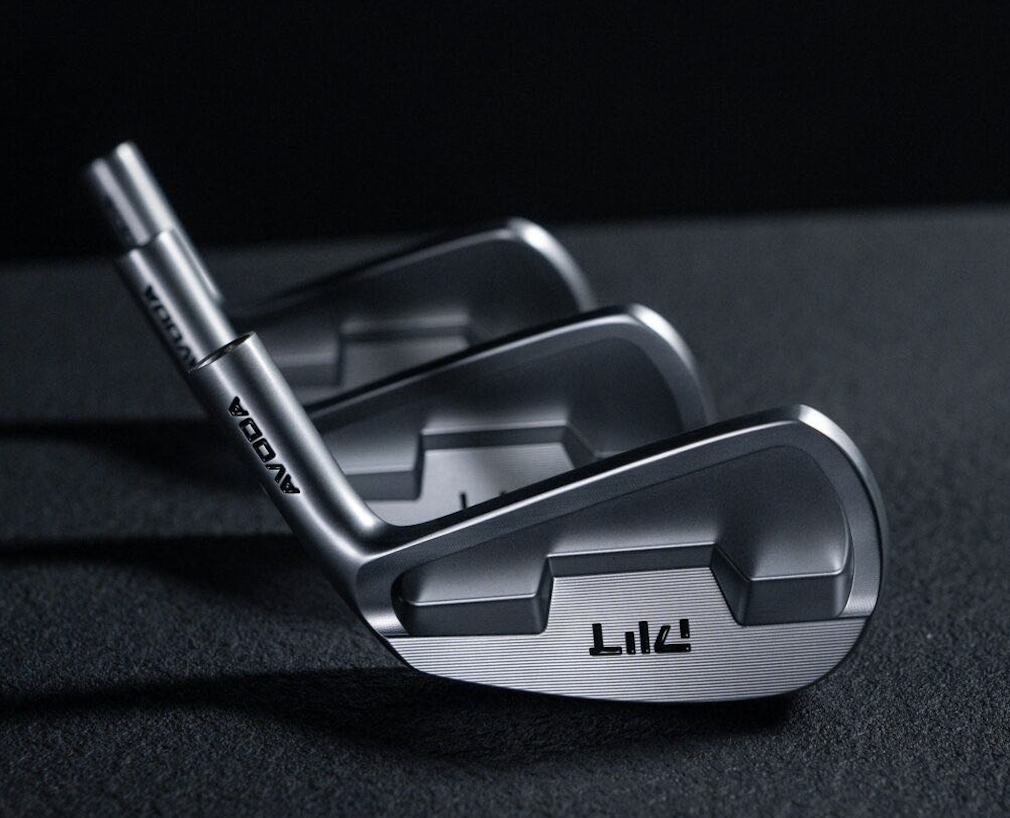
Source: 3dprintingindustry.com
When it comes to manufacturing golf clubheads, there are notable differences between traditional manufacturing methods and 3D printing. The two approaches differ in terms of design flexibility, production speed, material options, and cost efficiency. Below is a comparison that highlights these key distinctions:
Aspect | Traditional Manufacturing | 3D Printing |
---|---|---|
Design Flexibility | Limited by the constraints of molds, casting, and forging. Complex shapes are difficult or costly to achieve. | Allows for complex geometries and detailed internal structures that can optimize performance. |
Customization | Customization is possible, but often requires significant investment in specialized molds or tooling. | Enables highly personalized designs with ease, allowing golfers to tailor clubheads to their unique preferences. |
Production Speed | Typically slower, as it requires the creation of molds, tooling, and extended production runs. | Faster production, with the ability to produce prototypes or final products in a matter of days. |
Material Options | Limited to traditional metals like steel, aluminum, or titanium, which may not offer the best balance of performance. | Offers a broader range of materials, including custom alloys and composite materials, to improve performance. |
Cost Efficiency | High initial costs for molds and tooling. Larger production runs can help reduce per-unit costs. | Cost-effective for low-volume, customized production, with less material waste. |
Precision | Traditional methods like casting may result in variations due to mold imperfections. | High precision and accuracy, ensuring that every part is made to exact specifications with minimal tolerances. |
Weight Optimization | Achieving optimal weight distribution can be difficult and costly. | 3D printing allows for precise control of weight distribution, which can enhance performance and feel. |
Common 3D Printing Technologies for Golf Clubheads
The technology behind 3D printed golf clubheads involves advanced processes that allow for precise, complex structures.
One of the most widely used technologies for manufacturing golf clubheads is Selective Laser Melting (SLM). This metal 3D printing process is perfect for creating robust, high-performance clubheads.
Process of Selective Laser Melting (SLM)
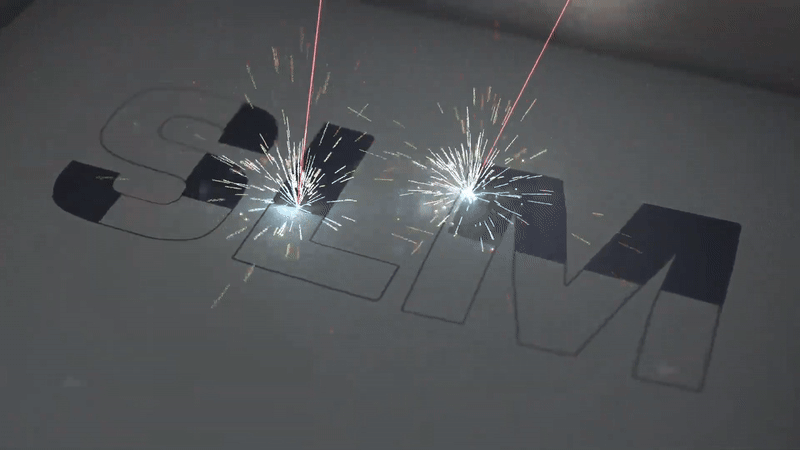
Powder Bed Preparation
A fine metal powder, such as stainless steel or titanium, is spread evenly across the build platform, creating the base layer for the print.
Laser Sintering
A high-powered laser scans the metal powder, melting it in precise areas based on the 3D model. The laser selectively melts and fuses the powder layer by layer to form the desired shape.
Layering
Once the first layer is complete, the platform lowers slightly, and a new layer of metal powder is spread over the previous layer. The laser then melts this new layer, continuing the process until the part is fully formed.
Cooling and Solidifying
After each layer is melted, it cools and solidifies, allowing the metal structure to maintain its shape. The process repeats until the entire part is created.
Post-Processing
Once the print is complete, the part is carefully removed from the build platform. Additional post-processing steps like cleaning, heat treatment, and finishing may be done to enhance the material properties and surface quality.
SLM is highly effective for producing metal golf clubheads, as it creates parts with excellent mechanical properties, making it ideal for the rigorous demands of golf.
For a deeper understanding of SLM 3D printing, check out our detailed article: Guide to SLM 3D Printing.
If you're curious about the cost of 3d printing your model with a specific metal, feel free to try our free online cost calculator.
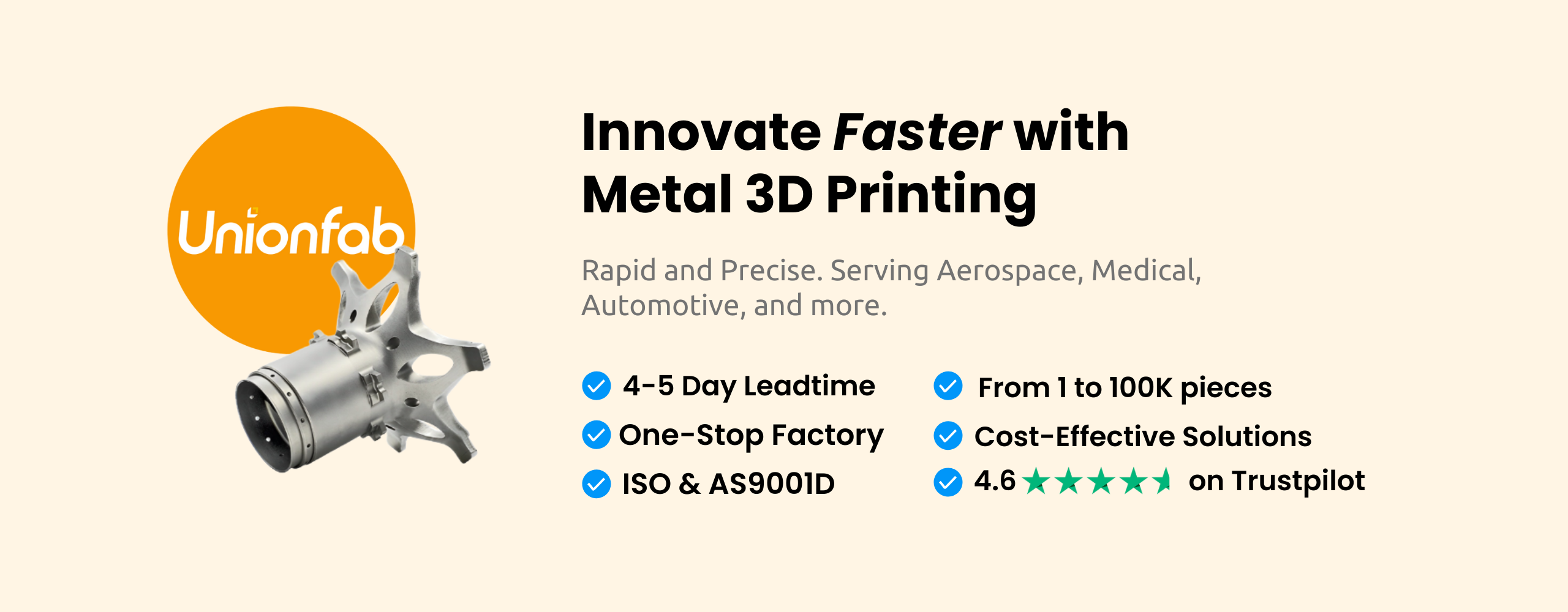
Materials for 3D Printed Clubheads
The material selected for 3D printing a golf clubhead significantly impacts its performance. The most common materials used for manufacturing golf clubheads include stainless steel, aluminum alloys, and titanium.
Below is a comparison table of these materials based on important performance attributes for golf clubs, including durability, weight, strength, cost, and impact resistance—all critical factors in producing a high-performance clubhead.
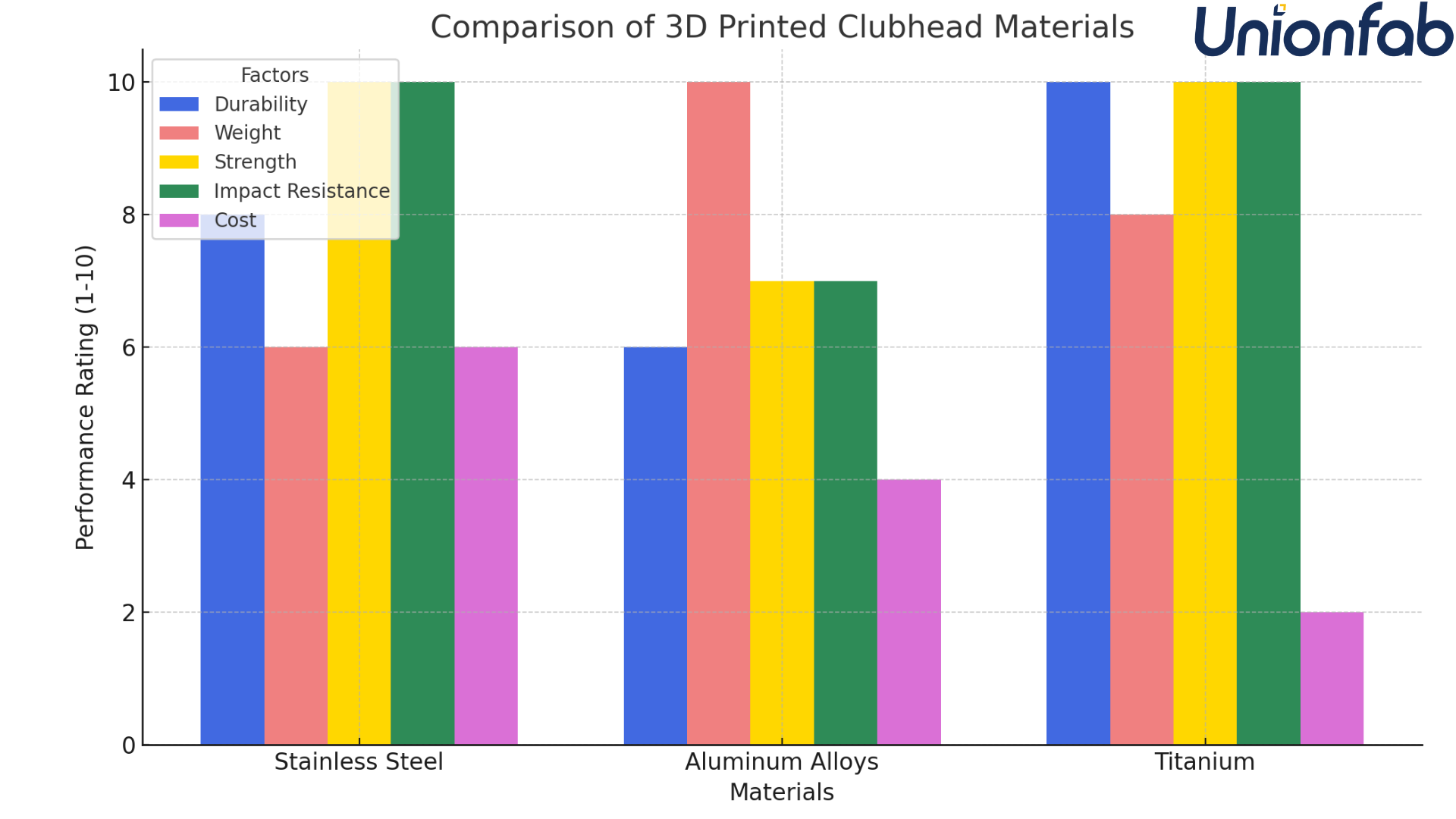
Material | Durability | Weight | Strength | Impact Resistance | Cost | Ideal For |
---|---|---|---|---|---|---|
High | Medium | High | High | $$ | Durable, long-lasting, ideal for most golfers | |
Medium | Low (lighter) | Medium | Medium | $ | Lightweight, best for higher swing speeds | |
Very High | Low | Very High | Very High | $$$ | High-end, professional clubs, strength-to-weight ratio |
Key Performance Dimensions Explained:
Durability: The material's ability to withstand repeated impacts during gameplay. Stainless steel and titanium are durable, ensuring the clubhead lasts longer with consistent use.
Weight: Lighter materials like aluminum alloys and titanium help increase swing speed and control, while heavier materials like stainless steel offer better stability, though they can feel heavier.
Strength: The material’s ability to handle high forces during contact. Titanium provides the best strength-to-weight ratio, ideal for high-performance clubs.
Impact Resistance: How well the material absorbs force during ball contact without breaking or deforming. Titanium leads in impact resistance, with aluminum alloys and stainless steel also performing well.
Cost: Stainless steel is affordable, making it a common choice. Aluminum alloys are cost-effective for lighter clubheads, while titanium is more expensive and used in premium equipment.
How Much Does It Cost to 3D Print a Golf Club Head?
The cost of 3D printing a golf club head typically involves four major components: material cost, post-processing, logistics, and taxes. Here’s how each factor is usually calculated:
Material Cost
Material cost is calculated based on part volume, material density, and price per gram. Most service providers quote a price that already includes both the raw material and the printing cost.Formula:
Material Cost = Model Volume × Density × Price per Gram
Example:
Model Volume: 10 cm³
Material: 316L Stainless Steel
Density: 7.9 g/cm³
Unit Price: $0.40/g
Estimated Cost: $31.60
(Note: This is a sample estimate. Larger production quantities often lead to lower per-unit costs.)
Post-Processing Cost
The cost of finishing the printed part varies depending on its size, complexity, material, and finishing method. Common pricing models include:
● Hourly Rate: For complex treatments like machining or polishing
● Per Part: Used for simpler tasks such as cleaning or basic surface smoothing
● By Weight or Volume: Applied to intensive processes like heat treatment or annealing
Logistics & Taxes
Shipping charges depend on the weight of the part and the delivery location, while tax rates vary by region and are usually calculated as a percentage of the total service fee.
For more detailed insight into each cost factor, visit the full article:
👉 How Much Does It Cost to 3D Print Something ?
Top 3D Printed Golf Accessories You Should Try
Below is a table comparing some of the top 3D printed golf accessories, highlighting their applicable 3D printing technologies, common 3D printing materials, and recommended 3D models:
Accessory | Applicable 3D Printing Technologies | Common 3D Printing Materials | Recommended 3D Model |
---|---|---|---|
3D Printed Golf Balls | SLM, FDM | PLA, TPU, Resin | Customizable designs for spin control, texture patterns, or internal structures for performance enhancement ![]() Source: cgtrader.com |
3D Printed Golf Ball Holder | FDM, SLA, SLS | PLA, ABS, Nylon | Design for size and shape fitting, with added personal style ![]() |
3D Printed Golf Ball Marker | SLA, FDM | PLA, Resin, ABS | Simple or customized designs with logos, names, or patterns ![]() |
3D Printed Golf Tees | FDM, SLS | PLA, ABS, Nylon, Eco-friendly materials | Adjustable heights, unique designs, eco-friendly options ![]() |
Explanation of Each Accessory:
1. 3D Printed Golf Balls:
3D printing allows for the creation of golf balls with customized textures, patterns, and internal structures. Players can enhance spin control, distance, and feel, making it easier to design a ball that suits their playing style.
3D Printed Golf Ball Holder:
These holders can be custom-designed to fit perfectly into your golf bag, keeping your golf balls organized and easy to access. Personalize them with your own designs, colors, or logos for a unique touch.
3D Printed Golf Ball Marker:
3D printing lets you design custom ball markers with logos, messages, or patterns. Whether you want something simple or more personalized, the possibilities for customization are endless.
3D Printed Golf Tees:
Golfers can now create tees that fit their exact needs, whether that involves adjusting height, shape, or material. 3D printing also offers eco-friendly material options for those looking to make environmentally conscious choices.
Design Tips for 3D Printed Golf Equipment
Use these practical design tips to maximize the performance of your 3D printed golf equipment:
● Optimize Clubhead Weight:
Adjust the weight distribution in the clubhead to improve control. For example, place more weight towards the rear or perimeter to increase stability and forgiveness on off-center hits.
● Improve Aerodynamics:
Design smooth, low-profile clubheads to reduce drag. Use flow channels or dimples to help the clubhead cut through the air more efficiently, increasing swing speed and distance.
● Select the Right Material:
For lightweight components, use titanium alloys. For stronger parts like the clubhead face or hosel, use stainless steel or tungsten to enhance durability and performance.
● Optimize Shaft Flex:
Adjust the shaft’s internal structure (like varying wall thickness) to match a golfer’s swing speed. You can add honeycomb structures to fine-tune flexibility for better control or power.
● Reinforce Stress Points:
Strengthen high-stress areas, especially where the clubhead meets the hosel, using durable materials like titanium or steel composites to ensure long-lasting performance.
These tips help you design 3D printed golf equipment that performs at its best, with precise control and durability.
Partner with Unionfab for 3D Printed Golf Equipment
Unionfab is at the forefront of providing high-quality 3D printing services tailored to the golf industry. Whether you're looking for custom-designed clubheads or personalized accessories, we offer innovative solutions that can enhance your game.
Contact us today to see how 3D printing can revolutionize your golf equipment! For new customers, you will get 10% discount for your first order.
FAQs
1. Are 3D printed golf clubs durable?
Yes, 3D printed clubs made from metals like stainless steel and titanium are highly durable and designed to withstand the rigors of the game.
2. How long does it take to 3D print a golf clubhead?
3D printing provides a faster turnaround time compared to traditional methods. A golf clubhead prototype can typically be printed in just a few days.
3. Can 3D printing improve the performance of golf accessories?
Absolutely. 3D printing allows for customization of golf accessories such as tees, markers, and holders, offering improved functionality and a more personalized touch.