Guide to 3D Printing Robot Parts [+Cost Calculator]
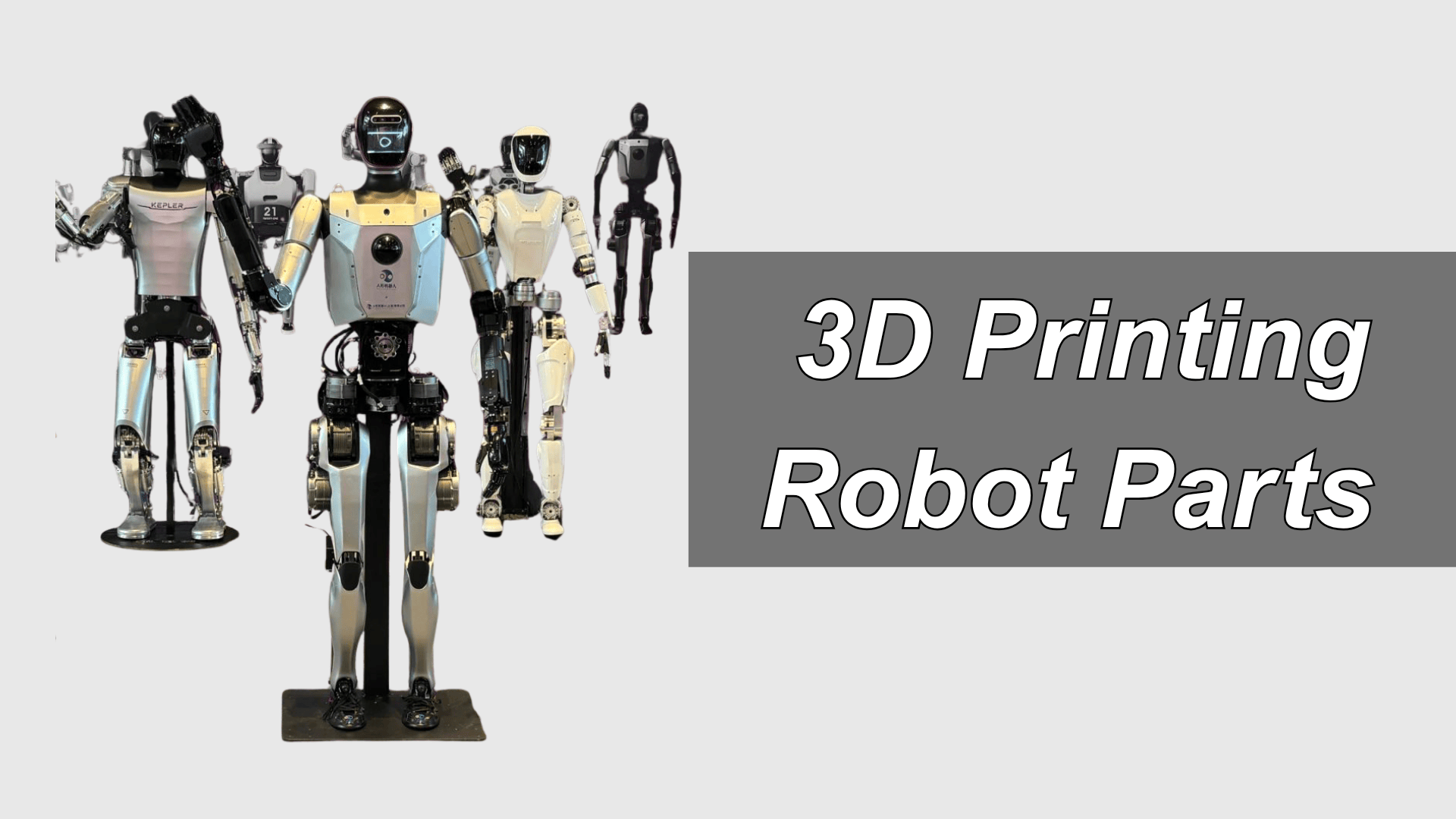
Discover how 3D printing accelerates robot manufacturing with the right materials, design tips, and cost-saving strategies. Learn what parts to print and why.
Introduction
Robotics is evolving rapidly—from service bots and industrial arms to humanoid assistants and automated warehouses. Greater complexity brings tighter timelines, lower tooling budgets, and a need for flexible design. 3D printing meets these demands by delivering quick prototypes, low-volume runs, and intricate custom parts.
In this article, we’ll cover the top technologies and materials used for 3D printed robot parts, highlight which components are best suited for additive manufacturing, and provide practical design and cost-reduction tips based on real-world applications.
Real-world Cases of 3D Printing in Robot Manufacturing
As 3D printing becomes more accessible and industrial-grade materials continue to improve, many leading institutions and companies are applying additive manufacturing to push the boundaries of robot design, functionality, and cost-efficiency.
Below are several real-world examples that illustrate how 3D printing is transforming robot manufacturing:
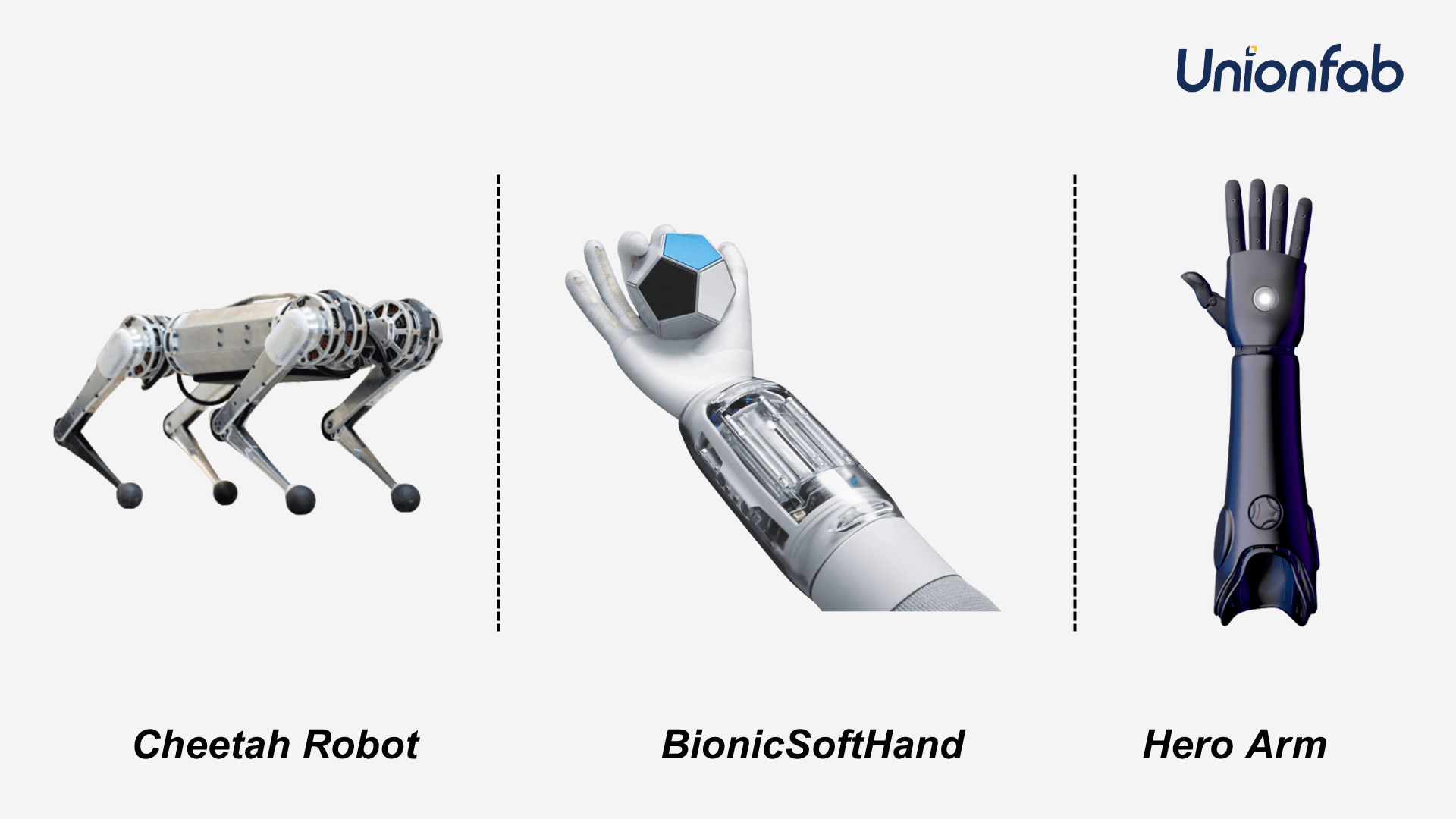
Dimension | MIT – Mini Cheetah Robot | Festo – BionicSoftHand & BionicSoftArm | Open Bionics – Hero Arm |
---|---|---|---|
Application Focus | Structural lightweighting and rapid prototyping | Soft robotics and biomimetic actuation | Mass customization and low-cost wearable robotics |
3D Printing Technology | SLS (Selective Laser Sintering) | FDM with flexible TPU | SLA (Stereolithography) |
Parts 3D Printed | Mechanical legs, connecting joints, outer shell | Soft joints, pneumatic fingers, integrated shells and air channels | Customized outer shells, fingers, internal mechanical components |
Benefits and Outcomes | • Weight: only 9 kg, speed up to 3 m/s | • Safe for human-robot interaction | • 1/10 the cost of traditional prosthetics |
In summary,
MIT – Mini Cheetah Robot
This case highlights how 3D printing enables complex geometry and topological optimization that would be difficult or impossible with traditional methods. It also dramatically shortened the development cycle from weeks to just a few days, making it a model example of academic and engineering agility in mobile robotics.
Festo – BionicSoftHand
Traditional manufacturing struggles to produce complex, flexible structures. This case shows how 3D printing makes it possible to build safe, lightweight, biomimetic systems that can collaborate with humans. Festo’s work is a global benchmark in soft robotics innovation.
Open Bionics – Hero Arm
This project demonstrates how 3D printing can unlock affordable, scalable, and highly personalized robot products. The Hero Arm reduced production costs by up to 90% and enabled delivery within days—turning high-tech prosthetics into an accessible consumer product.
What 3D Printing Enables in Robotics
Drawing from the previous case studies, it's clear that 3D printing is not just a tool for making parts—it's a strategic enabler of faster, more flexible, and more innovative robot development.
The following points highlight how additive manufacturing empowers robotics teams by combining technical capabilities with practical advantages:
Faster Development
Turn digital designs into physical parts in days. Quickly test fit, function, and form without waiting for tooling.
Greater Design Freedom
Print complex shapes, internal channels, and lightweight structures that are hard or impossible to machine.
No Tooling Required
Skip molds and jigs. Ideal for low-volume production and custom builds with minimal upfront cost.
Lightweight, Strong Parts
Create optimized structures that reduce weight without sacrificing strength—key for mobile and wearable robots.
Easy Customization
Adapt robots to different users, tasks, or environments with quick design changes and no added tooling cost.
Integrated Functions
Combine multiple parts—like frames, cable paths, or actuators—into single, printable components to simplify assembly.
Robot Components Ideal for 3D Printing
The following four categories highlight common parts produced and the benefits of using additive manufacturing for each.
1. Structural Components
Common Parts 3D Printed:
Robot frames and skeletons
Outer housings and covers
Mechanical arms and support brackets
Benefits of 3D Printing:
Enables lightweight structural design through topology optimization and hollow features
Allows complex shapes that are difficult or impossible with traditional machining
Shortens prototyping and iteration cycles for structural layouts
Reduces material waste and improves design freedom
2. Customized End Effectors / Grippers
Common Parts 3D Printed:
Suction cups, clamps, and soft grippers
Tool holders and robot wrist adapters
End-of-arm tooling for special objects
Benefits of 3D Printing:
Enables fast and low-cost customization for non-standard or fragile objects
Supports frequent task changes with minimal delay
Avoids the need for tooling or machining
Ideal for small-batch, task-specific applications
3. Soft Robotics & Bionic Components
Common Parts 3D Printed:
Pneumatic actuators and soft fingers
Bionic joints and flexible linkages
Soft muscle structures and air channels
Benefits of 3D Printing:
Facilitates biomimetic movement and high flexibility
Enables safe interaction with humans and sensitive environments
Combines function and form in a single printed part, reducing assembly
Expands design space for wearable and assistive robotics
4. Integrated Functional Parts
Common Parts 3D Printed:
Structural components with built-in cable channels or cooling ducts
Mounting brackets with embedded threads
Panels with vibration dampening or snap-fit joints
Benefits of 3D Printing:
Reduces part count by combining multiple functions into one component
Simplifies assembly and maintenance
Improves system reliability and compactness
Supports design of modular or mobile platforms with fewer constraints
Comparison of 3D Printing Technologies Suitable for Robot Manufacturing
Here, we have compared common 3d printing technologies used in robot manufacturing to help you choose the most suitable one for your project.
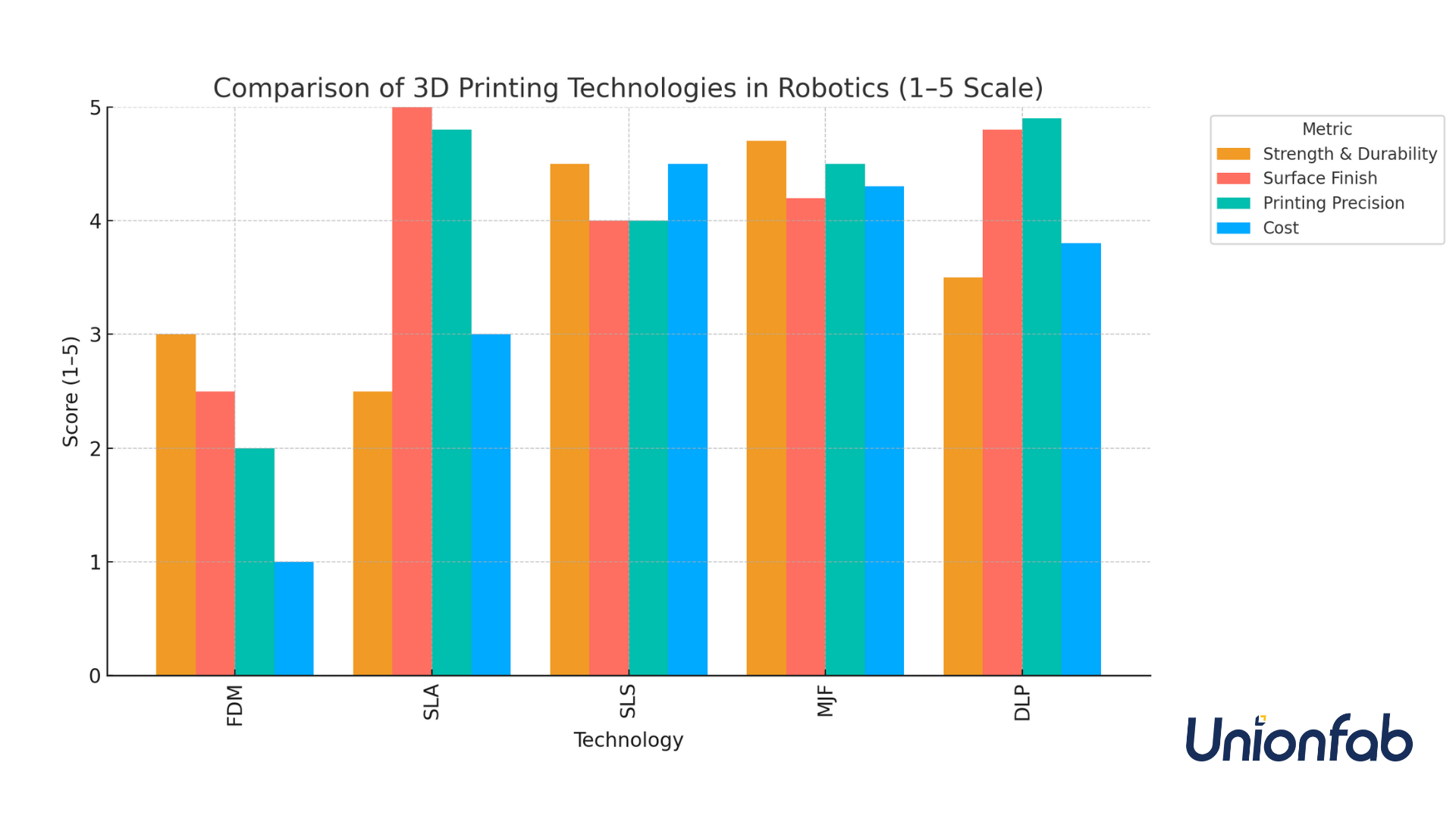
Technology | Materials | Strength & Durability | Surface Finish | Printing Precision | Cost | Typical Applications |
---|---|---|---|---|---|---|
Thermoplastics (e.g. PLA, ABS, PETG, TPU) | Moderate (can be reinforced with CF) | Moderate (visible layer lines) | ±0.2–0.5 mm | Low | Structural frames, brackets, tooling fixtures, soft grippers (TPU) | |
Photopolymer resin | Moderate (brittle in some cases) | High (very smooth) | ±0.05–0.1 mm | Medium | Bionic parts, detailed mechanical components, prosthetics shells | |
Nylon (PA12, PA11), composites | High (strong, tough, functional) | Matte & uniform | ±0.1–0.2 mm | High | Load-bearing parts, housings, functional end-use parts | |
Nylon (PA12), TPU | High (better isotropic strength than SLS) | Smooth & uniform (gray tone) | ±0.1 mm | High | Functional prototypes, integrated parts with internal channels | |
DLP (Digital Light Processing) | Engineering-grade resins | Moderate to high (depending on resin) | High (smooth surface) | ±0.05 mm | Medium–High | Small functional parts, connectors, detailed custom grippers |
Selection Tips (Quick Summary):
Choose FDM when budget is limited, part size is large, high precision is not required, or flexible materials like TPU are needed.
Choose SLA/DLP when high resolution, smooth surface finish, or fine details are critical—ideal for small, aesthetic, or bionic components.
Choose SLS/MJF for strong, functional parts with complex geometries and no need for support structures—suitable for end-use or load-bearing components in robots.
Still unsure which tech to choose? Talk to Unionfab experts.
How to Choose the Right Material for Robot Parts
Selecting the right material is critical to ensuring that 3D printed robot components meet performance, safety, and durability requirements. The ideal material depends on the function of the part, the working environment, and the mechanical stresses involved.
Key Factors to Consider:
Mechanical Requirements
Consider strength, stiffness, flexibility, and impact resistance. Load-bearing frames require rigid and tough materials, while grippers or joints may need flexible or shock-absorbing ones.
Thermal and Chemical Resistance
For robots operating in high-temperature or chemically exposed environments, choose materials that can withstand heat, UV, or corrosion—such as Nylon, PEEK, or reinforced composites.
Surface Quality and Accuracy
Aesthetic or functional interfaces may require high-resolution and smooth finishes, in which case resins (SLA/DLP) or MJF materials are ideal.
Weight Optimization
Lightweight materials like PA12 or carbon fiber–reinforced filaments help reduce total robot mass, improving speed and energy efficiency.
Biocompatibility or Wearability
For medical or wearable robots, ensure materials are skin-safe, non-toxic, and comfortable—such as soft TPU or medical-grade resins.
Common 3D Printing Materials for Robotics:
Material | Properties | Typical Use Cases |
---|---|---|
PLA / PETG (FDM) | Easy to print, low cost, moderate strength | Prototypes, housings, non-structural parts |
ABS / ASA (FDM) | Durable, impact-resistant, slightly heat-tolerant | Mechanical brackets, enclosures, internal mounts |
TPU (SLS) | Flexible, elastic, abrasion-resistant | Grippers, soft joints, wearable padding |
Nylon PA12 (SLS / MJF) | High strength, lightweight, chemical-resistant | Structural frames, gears, robotic arms |
Carbon Fiber Composites | Very strong, stiff, lightweight | Load-bearing arms, drone parts, high-stress joints |
Resins(SLA / DLP) | High detail, smooth finish, brittle (some types) | Bionic shells, cosmetic parts, detailed end-effectors |
Final Tip: No single material fits all use cases
Start by defining your part’s function, environment, and required properties;
Then choose the material that balances performance and cost.
For hybrid needs, consider multi-material printing or combining printed parts with off-the-shelf components.
How Much Does 3D Printing Robot Parts Cost?
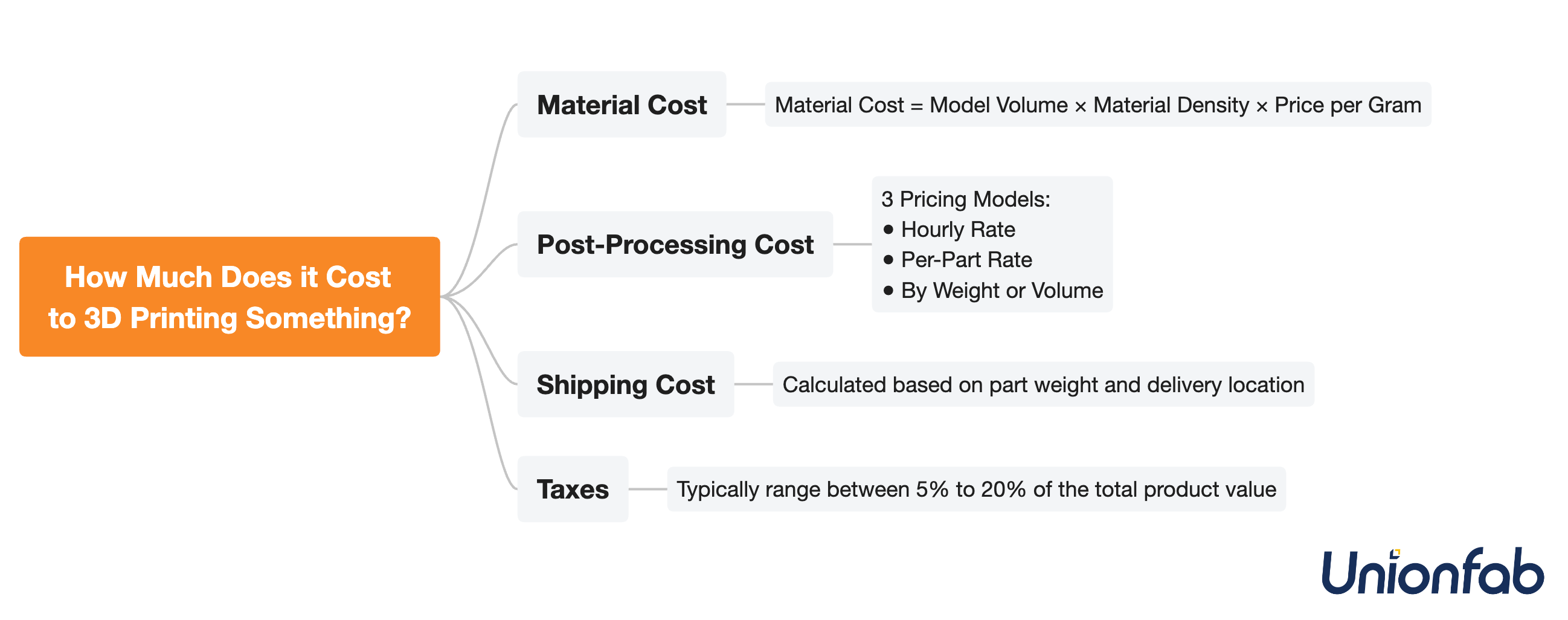
The total cost of 3D printing typically includes several key elements: material cost, post-processing, shipping, and taxes. Here's how each component is generally determined:
Material Cost
This is usually calculated using the following formula:
Material Cost = Model Volume × Material Density × Price per Gram
In most cases, the quoted price per gram already includes both raw material and printing service fees.
Post-Processing Cost
Post-processing expenses vary depending on the part’s size, geometry, material, and finishing requirements. Common pricing models include:
Hourly Rate – Used for complex tasks like surface finishing or machining.
Per-Part Rate – Applied to simpler operations, such as support removal or basic cleaning.
By Weight or Volume – Typically used for energy-intensive steps like heat treatment.
Shipping and Taxes
Additional costs may arise from logistics and regional tax policies.
Shipping is often calculated based on part weight and delivery location.
Taxes depend on local laws and are usually charged as a percentage of the total cost.
For further details on 3d printing cost, you can refer to our previous article: How Much Does It Cost to 3D Print Something (2024)?
If you already have a 3d model and want to calculate its printing cost, feel free to try our online free cost calculator below.
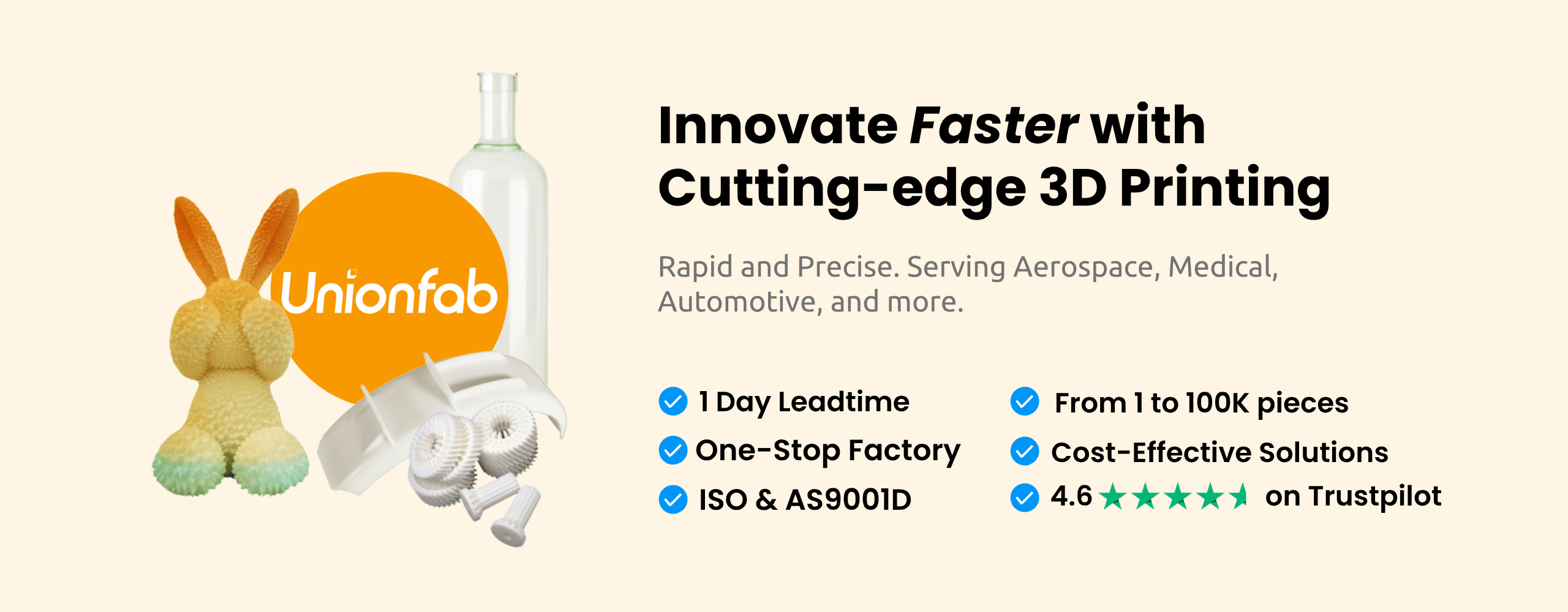
Cost- Saving Design Tips for 3D Printed Robot Parts
Well-designed 3D printed parts can help reduce the final printing cost. Here are some design tips to help you achieve this.
Optimize Your Design
Simplify Geometry: Reducing overly complex shapes can cut down on print time and material use, helping lower overall cost.
Use Lightweight Structures: Swap out solid parts for hollow or lattice designs to reduce material while maintaining strength.
Combine Components: Merge separate parts into a single print to save on assembly and manufacturing time.
Reduce Model Volume
Scale Down When Appropriate: Smaller parts use less material and print faster. If full size isn’t necessary, consider scaling the model.
Use Thinner Walls and Lower Infill: Minimize wall thickness and infill density to lower material usage and printing time, while ensuring the part still meets mechanical and functional requirements.
Optimize Post-Processing
Keep Finishes Functional: Select surface finishes that meet performance needs without adding unnecessary complexity or cost.
Group Similar Parts: Batch parts with similar finishing requirements to reduce setup time and post-processing expenses.
For customers who haven’t used our services before, you can get 10% discount for your first order!
Success Story --- 3D Printed Humanoid Robot Parts by Unionfab
At the World Artificial Intelligence Conference 2024 (WAIC), Unionfab supported the development of a full-sized humanoid robot by producing several mission-critical components using industrial-grade 3D printing.
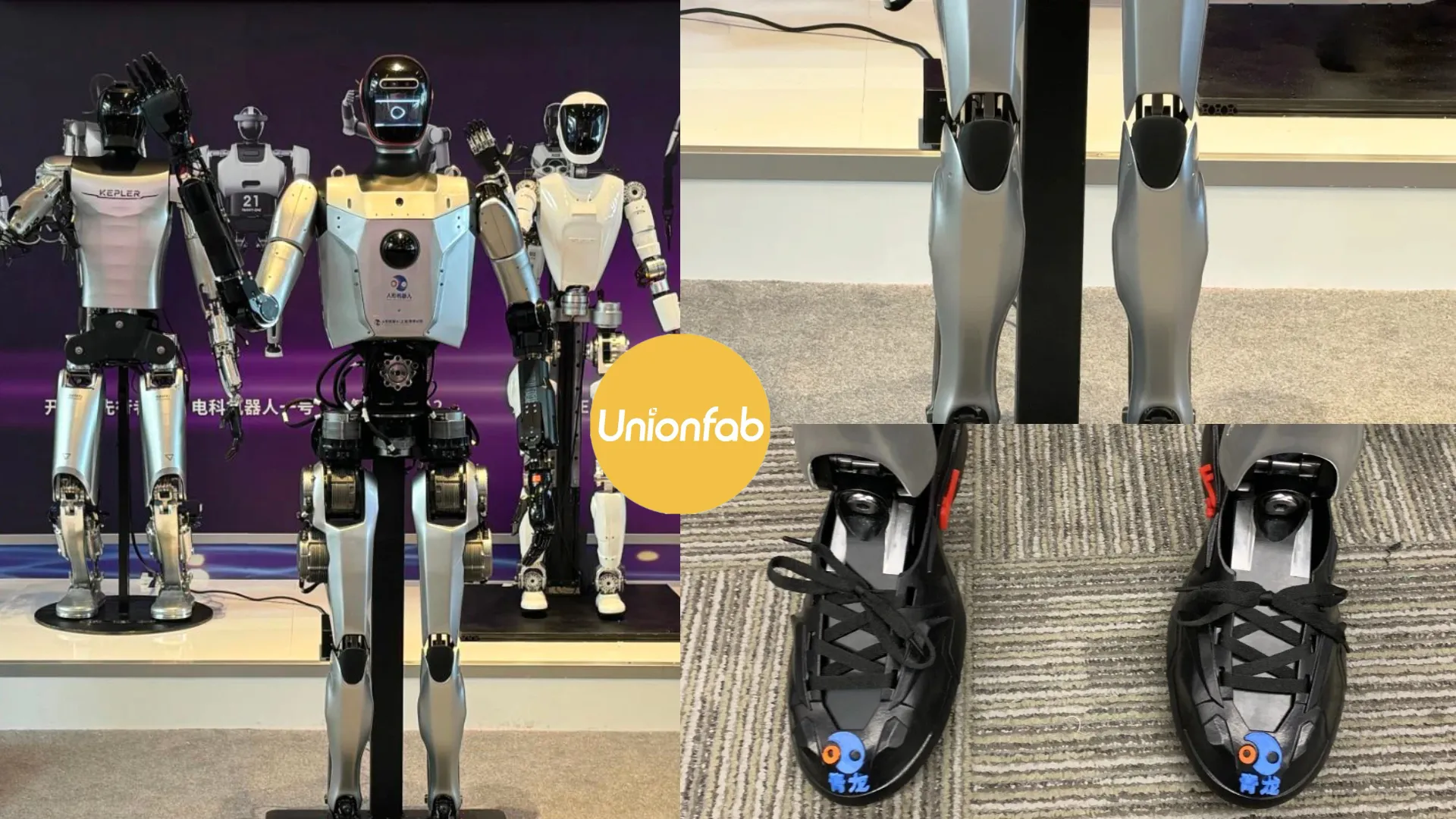
Client Background
Humanoid Robots (Shanghai) Co., Ltd., a humanoid robotics company based in China, aimed to debut its first humanoid robot at the World Artificial Intelligence Conference 2024 (WAIC 2024).
To meet the demands of tight timelines and high production quality, the company partnered with Unionfab to utilize 3D printing for manufacturing critical robotic parts.
Challenge
Developing the robot required components that met stringent performance and reliability standards:
Lightweight – Materials needed to minimize inertia and enhance movement responsiveness.
Heat and Wear Resistance – Parts had to endure frequent thermal changes, vibrations, and fatigue stress.
High Rigidity – Structural integrity was essential for high-speed walking and resistance to mechanical impact.
Solution
Advanced Material Selection
Unionfab chose high-strength nylon for its durability, thermal resistance, and rigidity. For flexible components, TPU was used due to its elasticity and resilience. These materials provided the balance of lightweight performance and reliability required for dynamic movement.
Precision SLS 3D Printing
Using SLS (Selective Laser Sintering) technology, Unionfab produced complex structures for the robot’s leg shells (nylon) and flexible shoes (TPU), ensuring accurate dimensions and robust mechanical performance.
Functional & Aesthetic Integration
The nylon leg shells received a painted finish for a refined mechanical look. The TPU shoes were designed for optimal grip and stability, contributing to smooth and reliable motion.
Result
The partnership delivered strong results in both function and form:
Improved Functionality – The 3D-printed parts enhanced airflow, agility, and mechanical performance.
Durable and Lightweight – Nylon offered structural strength while keeping the robot’s weight low.
Rapid Delivery – Unionfab met tight deadlines, ensuring timely delivery for WAIC 2024.
Eco-Friendly Production – Additive manufacturing minimized material waste, supporting sustainable manufacturing goals.
Build Better Robots with Unionfab
Unionfab offers expert 3D printing services tailored to different robot manufacturing needs. With advanced materials, multi-technology support, and fast lead times, we help robotics teams turn complex ideas into high-performance parts.
Ready to bring your robotic designs to life? Contact US to get a free quote or technical consultation.
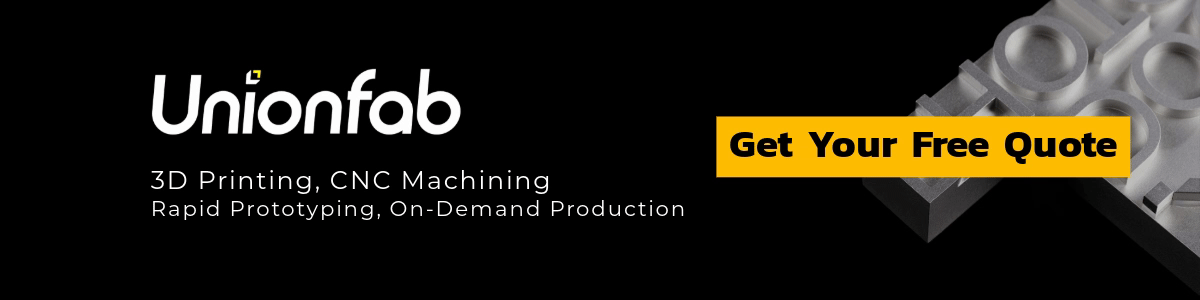
FAQs
Q1: Are 3D printed parts strong enough for robots?
Yes, when printed with industrial materials like PA12, carbon-fiber nylon, or metal, parts can handle real loads and conditions.
Q2: Can I use 3D printed parts in final products or just for prototyping?
Definitely. Many end-use robot parts today are 3D printed, especially for custom and low-volume production.
Q3: What’s the best 3D printing technology for robot frames?
MJF and SLS offer high strength and precision—ideal for structural components.
Q4: How fast can I get parts printed?
Unionfab delivers most robot components in 2–5 business days depending on volume and material.
Q5: Can 3D printing replace CNC or injection molding?
Yes, particularly for complex, low-volume, or customized parts where traditional tooling is costly or slow.