Guide to UAV 3D Printing [+Design & Material Advice]
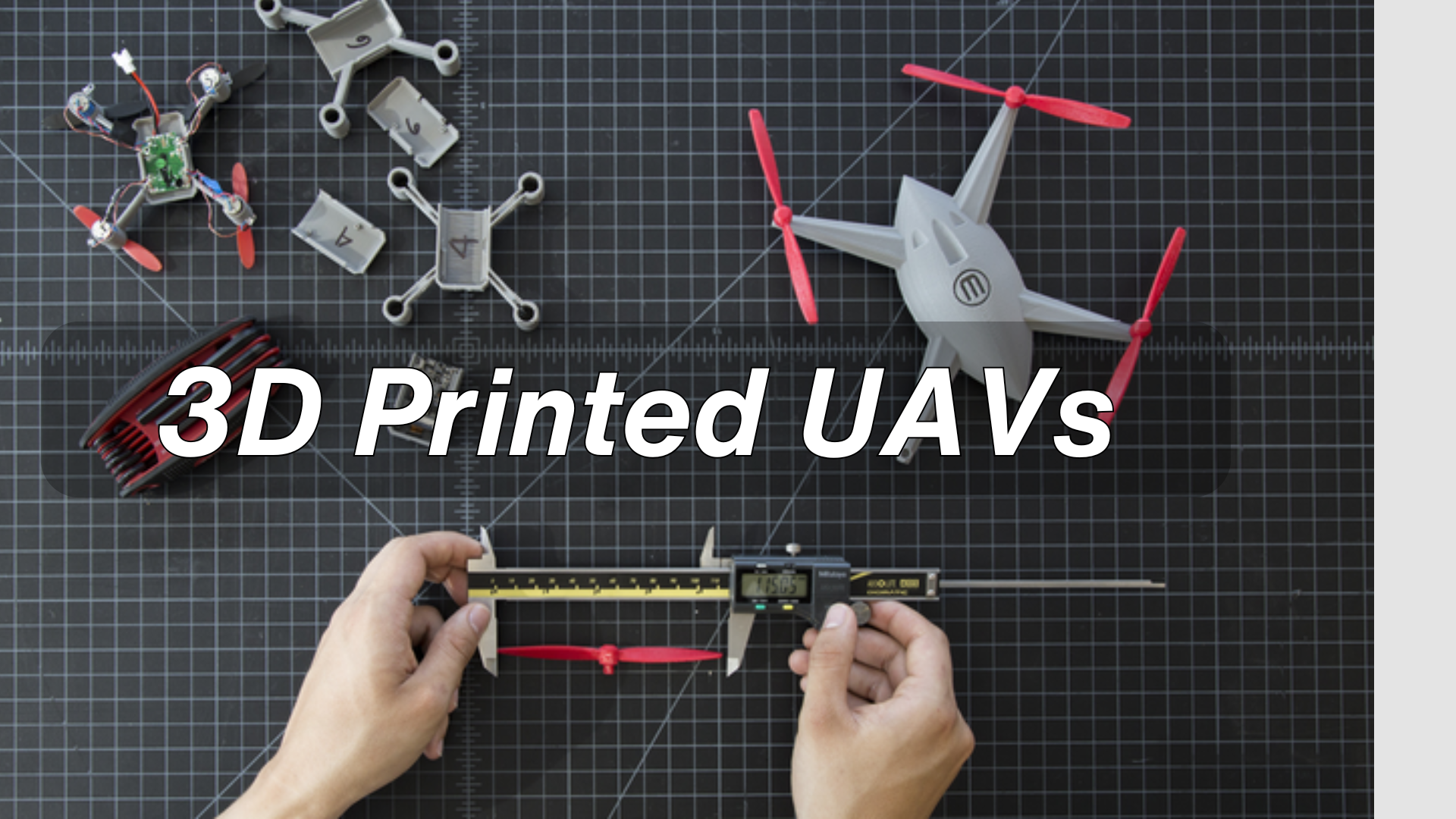
Discover how additive manufacturing is transforming UAV design with faster prototyping, lightweight materials, and enhanced customization for next-generation drones.
Introduction
3D printing is no longer confined to the prototyping lab—it’s now actively reshaping how UAVs (Unmanned Aerial Vehicles) are designed, built, and deployed.
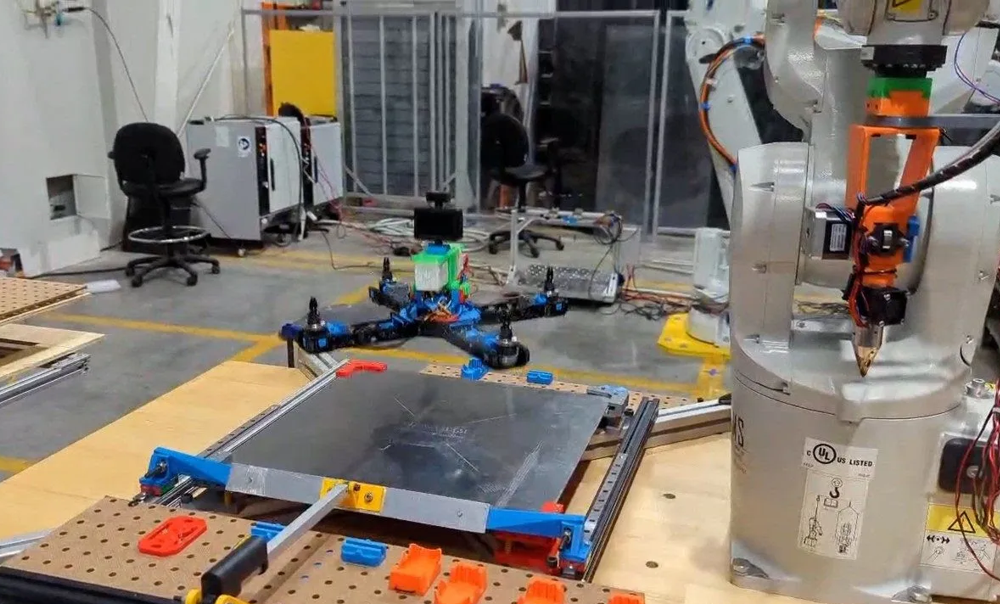
Source: suasnews.com
Across aerospace, defense, logistics, and agriculture, leading organizations are already embracing additive manufacturing to create high-performance drone components.
GE Aviation developed propulsion module prototypes with improved thermal performance using 3D printing.
Stratasys enabled drone manufacturers to reduce weight and simplify assembly by printing modular structures in lightweight thermoplastics.
NASA and the European Space Agency have leveraged 3D printing for planetary simulation UAVs, benefiting from enhanced design freedom and part consolidation.
This article explores how UAV components benefit from 3D printing, which materials and processes are best suited, and how to integrate additive manufacturing into your drone development workflow.Traditional UAV Manufacturing vs. UVA 3D Printing
Traditional manufacturing methods—such as CNC machining, injection molding, and vacuum casting—have long been used in UAV production.
However, as drone designs become more complex and mission-specific, these methods reveal several limitations:
Limitations of Traditional UAV Manufacturing:
● High Upfront Costs: Tooling for injection molding or casting requires significant initial investment, which is difficult to justify for low-volume or iterative UAV designs.
● Long Lead Times: Producing custom parts or prototypes can take weeks, slowing down development cycles and delaying field testing.
● Design Constraints: Subtractive and mold-based methods restrict geometric freedom, limiting weight optimization, part consolidation, and aerostructural performance.
● Assembly Complexity: Traditional manufacturing often necessitates multi-part assemblies due to manufacturing constraints, increasing points of failure and manual labor requirements.
Advantages of 3D Printing for UAVs:
3D printing offers a radically different approach that removes many of the bottlenecks of traditional processes. It empowers UAV teams to iterate faster, design more freely, and reduce time-to-flight.
● No Tooling Required: Eliminate mold and fixture costs; ideal for low-to-medium production or custom drone builds.
● Rapid Iteration: Print and test new airframe components or payload mounts in hours—not weeks.
● Complex Geometries: Create lightweight, internal lattice structures or aerodynamic shapes that are impossible to CNC or mold.
● Part Consolidation: Combine multiple components into one, reducing weight, fasteners, and assembly labor.
● On-Demand Fabrication: Manufacture parts locally and just-in-time, reducing inventory and logistics delays.
● Material Versatility: Use high-performance polymers and composites tailored for stiffness, temperature resistance, or impact durability.
Cost and Efficiency Comparison
Compared with CNC machining and vacuum casting, 3D printing offers clear economic advantages for UAV prototyping and small-batch production. See the infographic below for a visual breakdown of cost-efficiency across manufacturing methods.
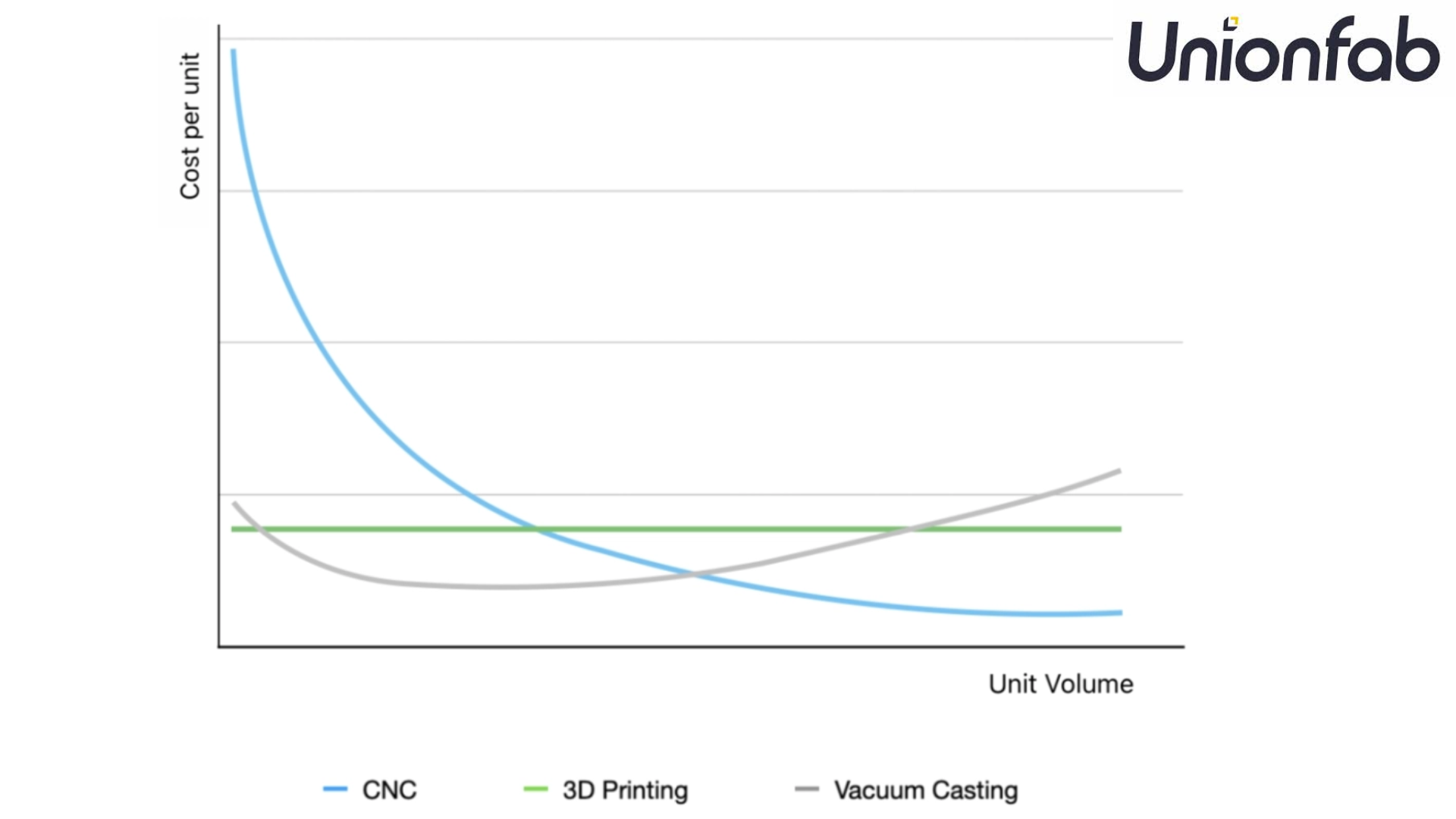
Source: Unionfab
Lower Unit Cost at Low Volumes: Traditional methods only become cost-effective at high production runs. 3D printing excels in low to mid volumes with minimal setup cost.
Faster Production Time: Avoid weeks of lead time for tooling and machining—print functional UAV parts within 24–48 hours.
Reduced Waste: Additive manufacturing uses only the material needed, unlike CNC which subtracts from a solid block, leading to material savings.
For detailed comparison between 3d printing and traditional methods, read our article before: 3D Printing vs. CNC vs. Vacuum Casting: the Ultimate Comparison
What UAV Components Are Suitable for 3D Printing?
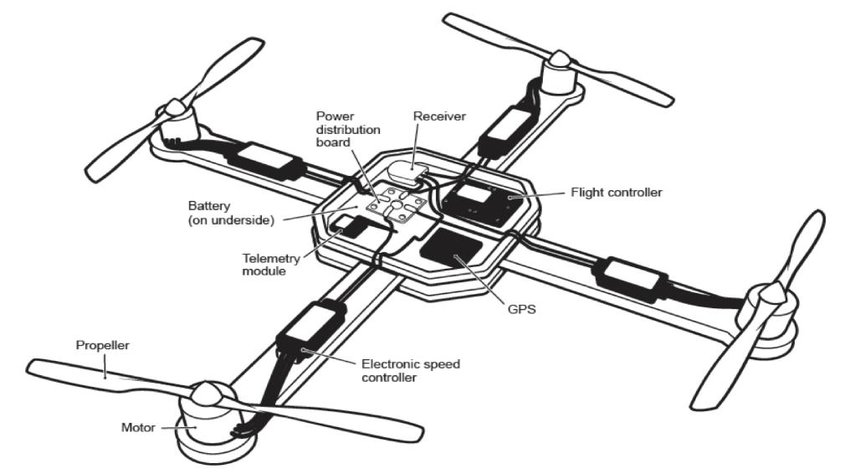
Source: ResearchGate.com
3D printing is not just limited to prototyping—it’s increasingly used to manufacture fully functional UAV parts.
Below is a breakdown of drone components that are well-suited to additive manufacturing, along with common materials and printing processes used.
Structural Components
● Airframe
Highly suitable for 3D printing. Materials: carbon-fiber reinforced nylon (FDM), TPU, SLS nylon.
Features: Lightweight and durable; can integrate stiffeners directly into the frame.
● Wings and Stabilizers
Suitable Materials: PLA, PA, PETG, carbon-fiber composites.
Features: Aerodynamically optimized structures with reduced part count.
● Motor Mounts and Arms
Suitable Materials: PA-CF, PETG, ABS.
Features: High impact resistance, good mechanical strength.
● Battery Bay / Equipment Housing
Suitable Materials: SLA resins, FDM plastics, SLS nylon.
Features: Fast swappable, fully customizable compartments.
Functional Elements
● Propeller Guards
Suitable Materials: TPU, ABS.
Features: Flexible and protective, can be printed to fit specific propeller dimensions.
● Mounting Brackets and Connectors
Suitable Materials: Tough Resin, PA12.
Features: Rapidly produced to reduce dependency on fasteners.
● Gearboxes / Mechanical Linkages
Suitable Materials: SLA Tough Resin, FDM PA.
Features: High-precision components for small-scale motion.
● Gimbal Mounts
Suitable Materials: SLA high-strength resin, PETG.
Features: Shock-absorbing and small in size for camera integration.
Enclosure & Protection
● Flight Controller Case
Suitable for 3D printing.
Common materials: SLA high-resolution resin (for fine detail and tight tolerances), FDM PETG (for general-purpose enclosures).
Features: Offers excellent heat resistance and dimensional precision. Ideal for protecting PCBs and supporting thermal management in compact layouts.
● GPS Modules / RF Radomes
Suitable for 3D printing.
Common materials: SLA standard resin, PETG, or PA12 depending on transparency and thickness needs.
Features: Customizable in thickness and geometry to accommodate signal transparency and module shape. Often used for antenna protection without interference.
● Complete UAV Shells
Suitable for 3D printing.
Common materials: PETG, carbon-fiber reinforced nylon (FDM), or SLS PA12.
Features: Ideal for low-volume production or rapid prototyping of full drone bodies. Balances weight and durability, supports quick iteration on shell designs.UAV 3D Printing: Technologies & Materials
Choosing the right 3D printing process and material is essential for ensuring performance, weight, and reliability in UAV components. Each additive manufacturing technology offers unique advantages depending on part function and mission demands.
Common 3D Printing Technologies for UAVs
● FDM (Fused Deposition Modeling)
Best for: Large airframe prototypes, jigs, low-cost structural parts
Materials: PLA, ABS, PETG, Carbon fiber-filled nylon
Pros: Affordable, easy to use, fast prototyping
Cons: Lower resolution and strength compared to other methods
Best for: Aerodynamic fairings, sensor housings, fluid-smooth aerodynamic parts
Materials: Standard resins, engineering resins, high-temp resins
Pros: Exceptional surface finish and detail accuracy
Cons: Brittle compared to thermoplastics; limited structural strength
● SLS (Selective Laser Sintering)
Best for: Functional brackets, clips, structural connectors
Materials: Nylon (PA11, PA12), glass-filled or carbon-filled nylons
Pros: High strength, no support structures needed, good thermal resistance
Cons: Rough surface finish without post-processing
● SLM / DMLS (Metal 3D Printing)
Best for: Load-bearing components, motor mounts, landing gear, heat sinks
Materials: Aluminum, Titanium, Inconel, Stainless Steel
Pros: High strength-to-weight ratio, aerospace-grade performance
Cons: High cost; requires post-processing and design adaptation
Choosing the Right Material
The intended function of the UAV part should guide your material choice:
● Lightweight Non-Structural Parts: FDM with carbon fiber-reinforced filament or SLS nylon
● High-Precision Housings: SLA with engineering resin
● Functional Prototypes / Mechanical Connectors: SLS Nylon PA12 or PA11
● Critical Load-Bearing Components: SLM with Aluminum or Titanium alloys
Still unsure about which material or technology fits your UAV design?
Talk to Unionfab experts to get tailored recommendations and technical support.
Design Tips for UAV 3D Printing
To get the best results from UAV 3D printing, consider the following practical tips during the design stage:
1. Design for Additive: Avoid shapes that require unnecessary support structures. Optimize for self-supporting angles where possible.
2. Lightweighting with Lattices: Use gyroid or honeycomb infill patterns to reduce weight without sacrificing strength.
3. Consolidate Parts: Merge multiple components into a single 3D-printed part to reduce fasteners, failure points, and assembly time.
4. Wall Thickness Optimization: Maintain consistent wall thickness for better structural integrity and predictable print outcomes.
5. Orientation Matters: Orient parts during printing to minimize stress and support usage, and to improve mechanical performance along intended load directions.
6. Account for Post-Processing: Design with space for sanding, coating, or mechanical finishes, especially in high-precision or client-facing components.
By applying these principles, engineers can fully leverage 3D printing to create lightweight, robust, and production-ready UAV parts.
Cost Reduction Tips for UAV 3D Printing
While 3D printing offers inherent efficiency gains, thoughtful design and process choices can further cut costs:
● Reduce Support Volume: Orient and design parts to minimize the need for supports, which lowers material use and post-processing time.
● Split and Stack: Large UAV frames can be split into smaller printable sections and stacked intelligently to maximize build space.
● Use Material Strategically: Print prototypes with lower-cost materials, then switch to engineering or metal materials for the final iteration.
● Batch Similar Parts: Group similar UAV components in a single build job to improve throughput and machine utilization.
● Avoid Overengineering: Match material and print resolution to the part’s actual functional needs—don’t overspecify when it’s not necessary.
Want to estimate the cost of your 3D model instantly?
Upload your file to Unionfab’s free online cost calculator and explore material options, lead times, and pricing.
Try Unionfab’s Cost Calculator below – Get real-time estimates for your UAV parts.
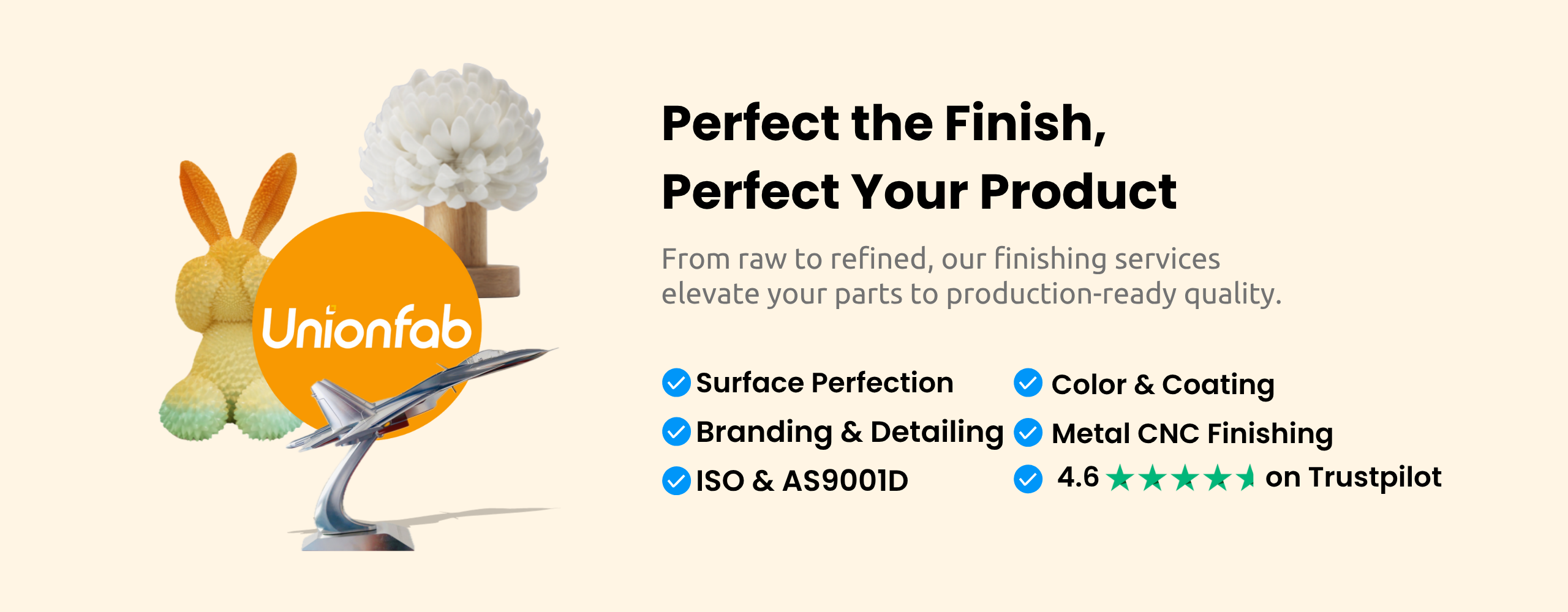
Industry Trends & Future Outlook
3D printed UAV adoption is growing across defense, logistics, and agriculture. Drones increasingly require custom, modular, and lightweight builds—tasks perfectly suited for 3D printing.
Materials and printer resolution are improving rapidly, bringing printed parts closer to the performance of traditional components. Flame-retardant, ESD-safe, and aerospace-grade materials are now printable at scale.
AI-assisted generative design and simulation tools now pair with additive workflows. These technologies allow engineers to generate structurally optimal, print-ready designs faster than ever.
Conclusion
3D printing is unlocking the future of UAV development. From prototyping to production-ready parts, additive manufacturing enables faster innovation, greater design flexibility, and improved drone performance.
Whether you’re building surveillance drones, mapping UAVs, or agricultural flyers, additive manufacturing offers a smarter path to the sky.Partner with Unionfab for UAV 3D Printing & Development
Unionfab is your trusted partner for 3D printed UAV components. We provide:
● UAV-focused design-for-additive reviews
● Wide selection of industrial and aerospace-grade materials
● High-quality FDM, SLS, and SLA production
● Low-volume production with fast turnaround
Start your drone project today—get in touch with Unionfab to bring your UAV designs to life.
FAQs
Is a 3D printed UAV safe for flight? Yes. When designed and printed with engineering-grade materials, 3D printed UAV parts meet the structural and performance needs of real-world missions.
Which drone parts are best for 3D printing?
Airframes, brackets, covers, housings, ducts, and payload mounts are all ideal for additive manufacturing due to their geometry and customization needs.
Are 3D printed materials light enough for UAVs?
Absolutely. Materials like carbon-fiber nylon and TPU combine high strength with minimal weight—ideal for airborne applications.
Can 3D printing be used for production, not just prototyping?
Yes. Small-batch or low-volume production is one of additive manufacturing’s biggest advantages for UAV builders.
Does Unionfab support UAV design validation?
Yes. We provide CAD reviews, simulation analysis, and flight-readiness checks for drone components made with additive manufacturing.